Frezarka 1650/650/250
-
Autor tematu - Specjalista poziom 3 (min. 600)
- Posty w temacie: 143
- Posty: 663
- Rejestracja: 01 lut 2011, 00:31
- Lokalizacja: Bolechowice/Kraków
Wczoraj wyżarzylimy ramę razem z bramą. Postaram się to jak najlepiej opisać bo myślę, że może się to komu przydać.
Ogólnie jestem zadowolony z całego procesu, i myślę że spełnił swoje zadanie, ale
niestety w trakcie wyżarzania wyszło na jaw parę błędów które można było uniknąć a które zaraz opiszę.
Piec zrobilimy podobnie do tego planu który zamieściłem w tym wątku, różnił się
jednak paroma szczegółami.
Wloty powietrza były tylko po dwóch stronach, i zamiast wentylatorów do
wtłaczania powietrza użylimy spalinowych dmuchaw do liści.
Kominy były 3, również po dwóch stronach, z tym, że jeden komin był tak duży jak te dwa po przeciwległej stornie.
Komory w której była rama ostatecznie nie przysypaliśmy ziemią.
Pod konstrukcje podłożyliśmy kawałki dachówki żeby nie dotykała bezpośredni blachy.
Wełna mineralna nie dotykała konstrukcji frezarki tylko była parę cm nad nią, utrzymywana na stalowych prętach. Na zdjęciu widać jeden, ale potem wbiliśmy z 8 kolejnych.
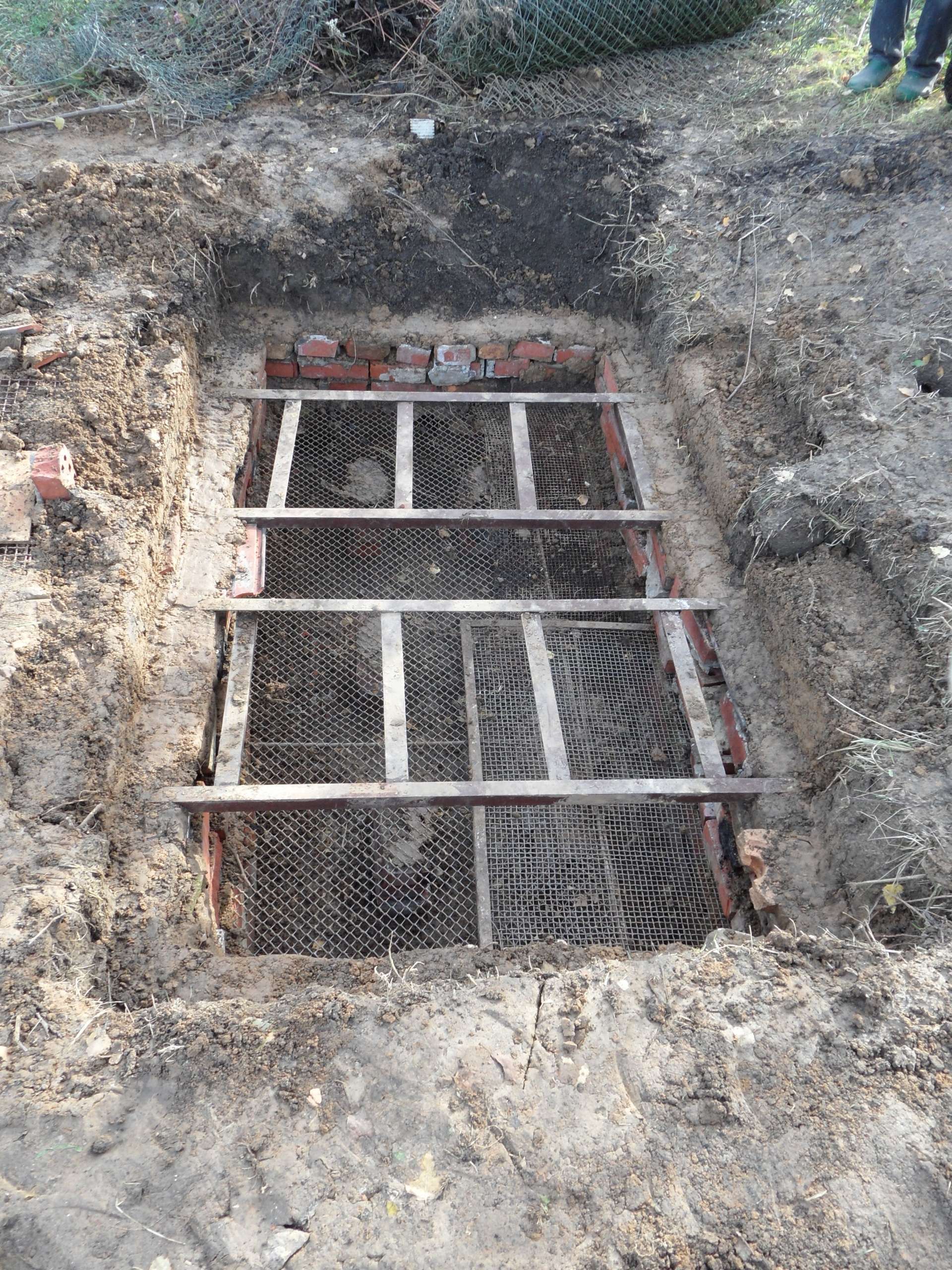
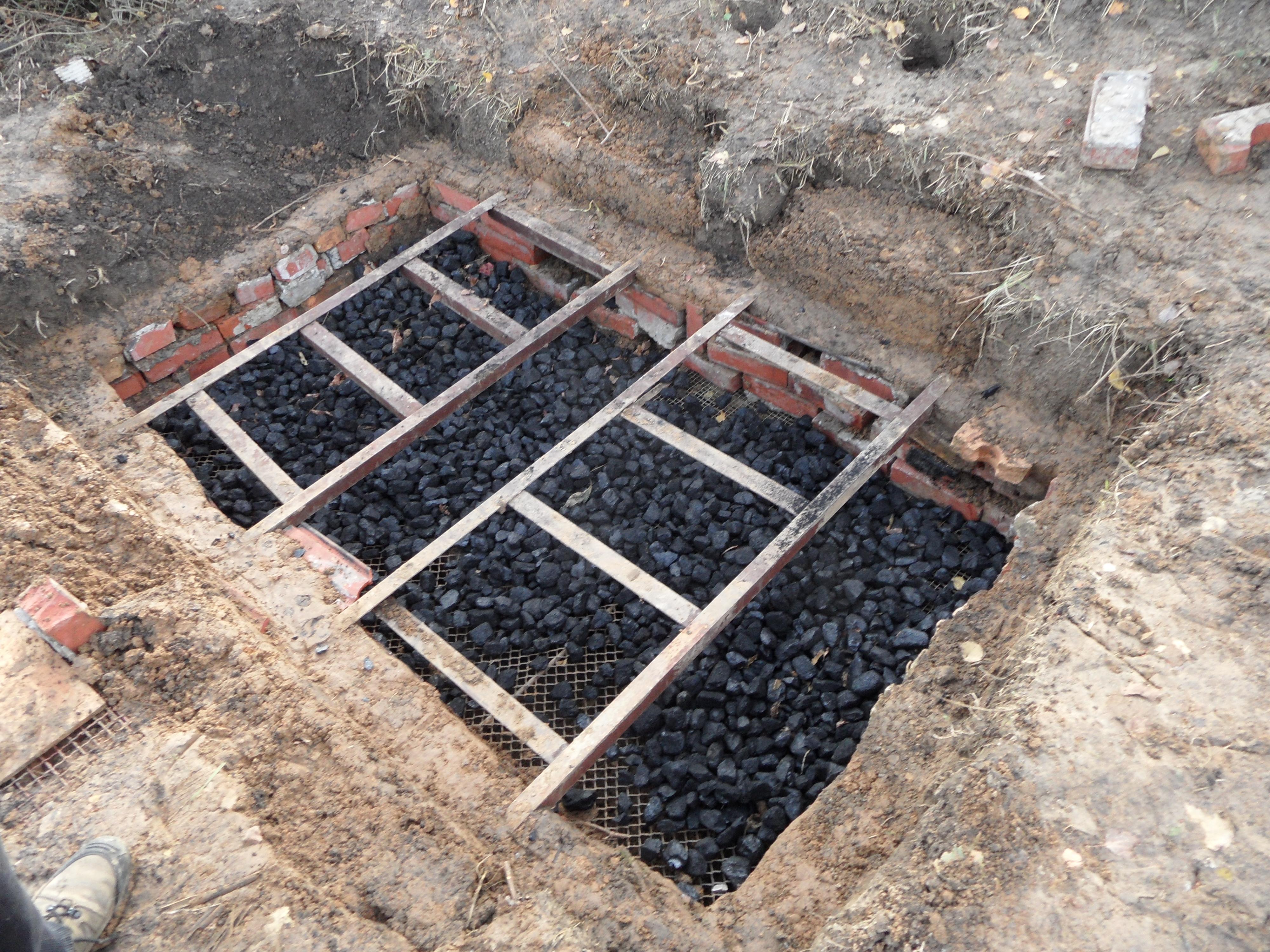
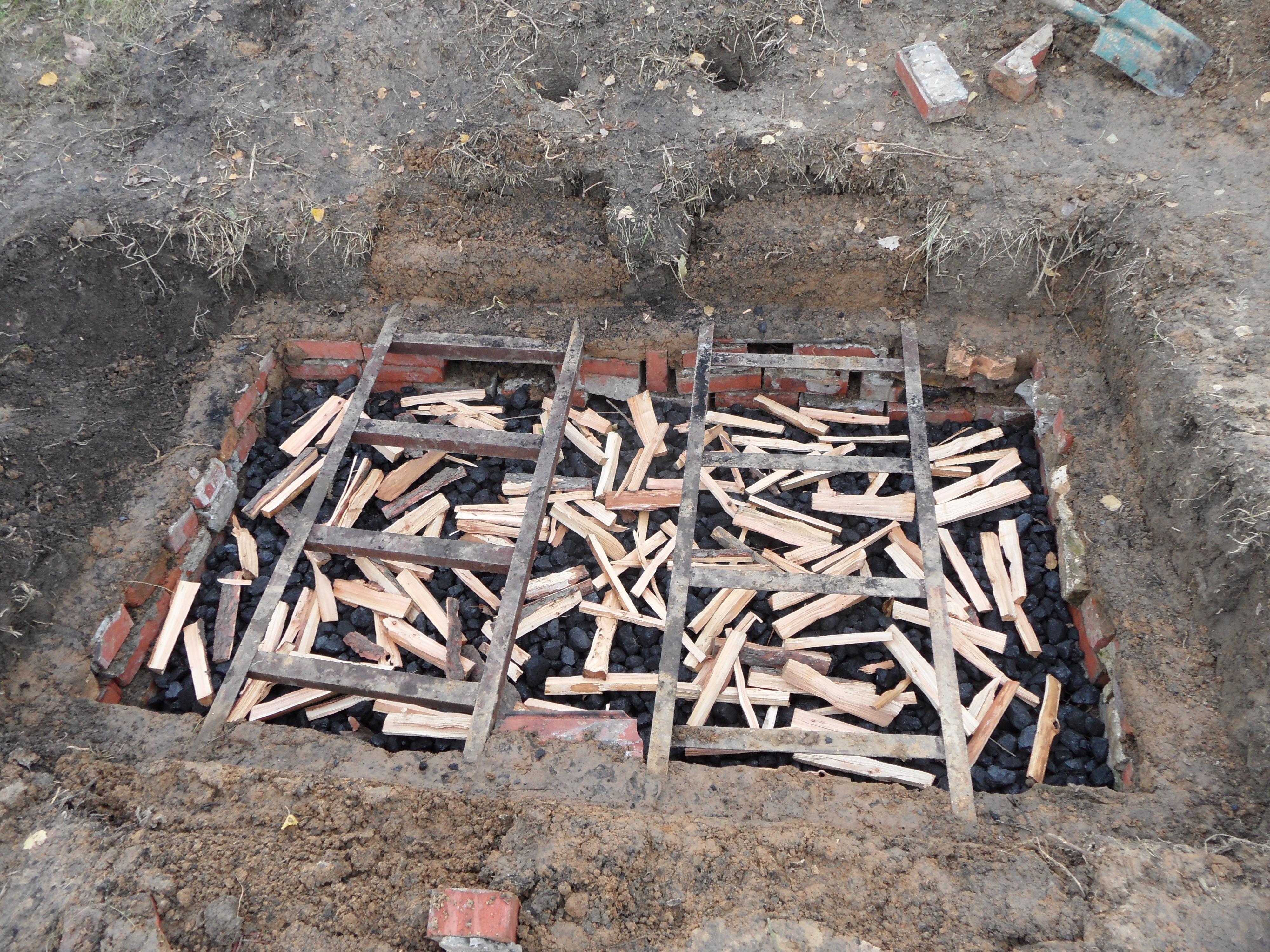
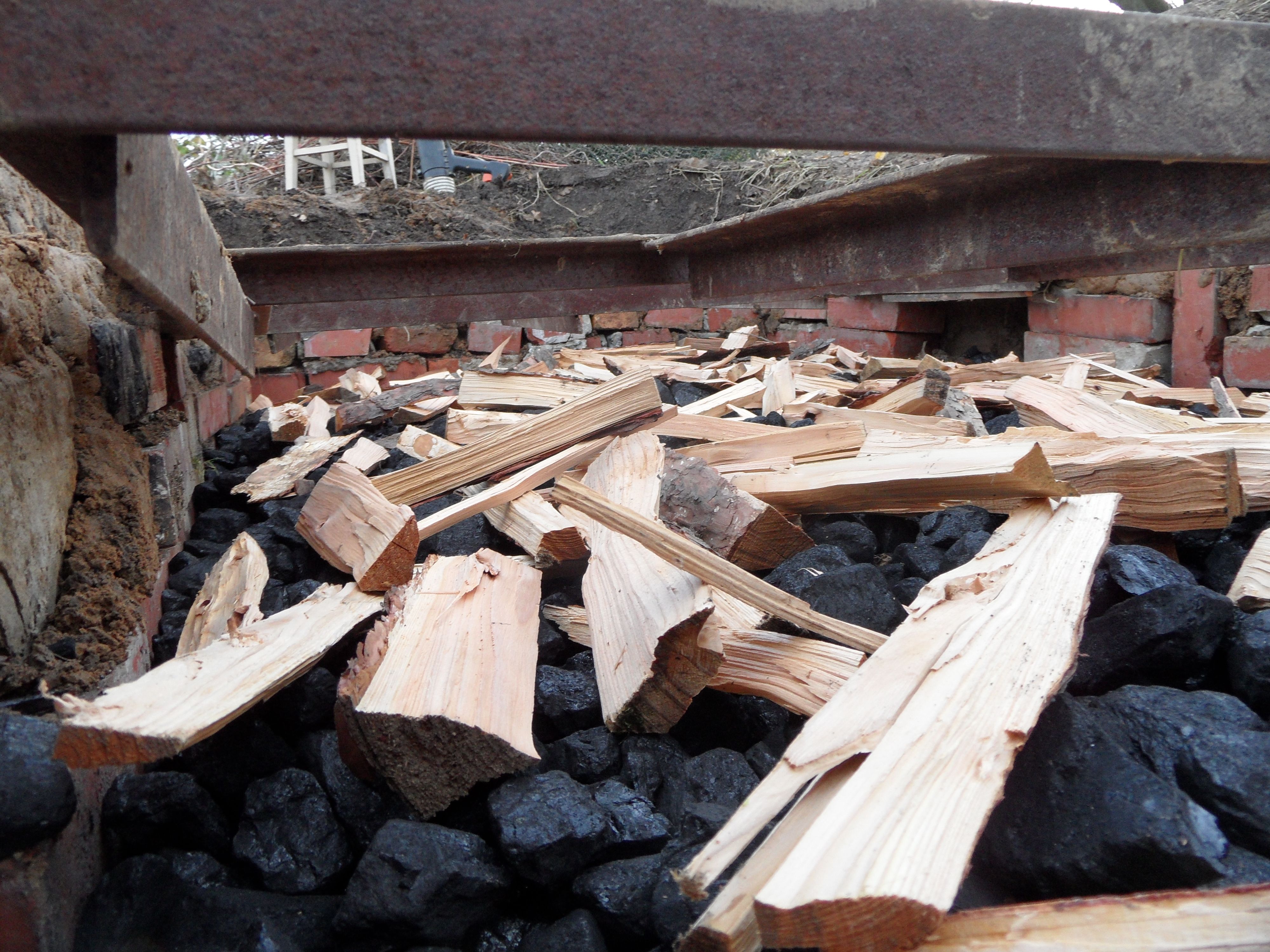
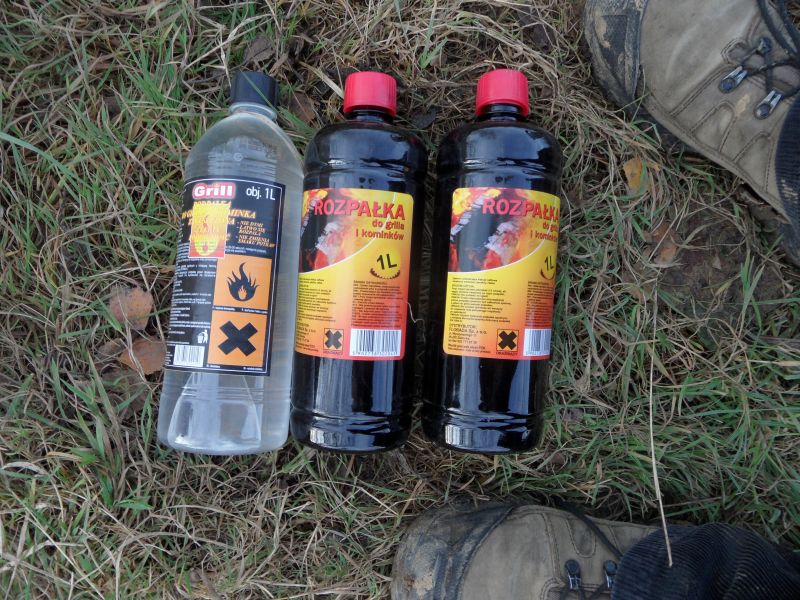
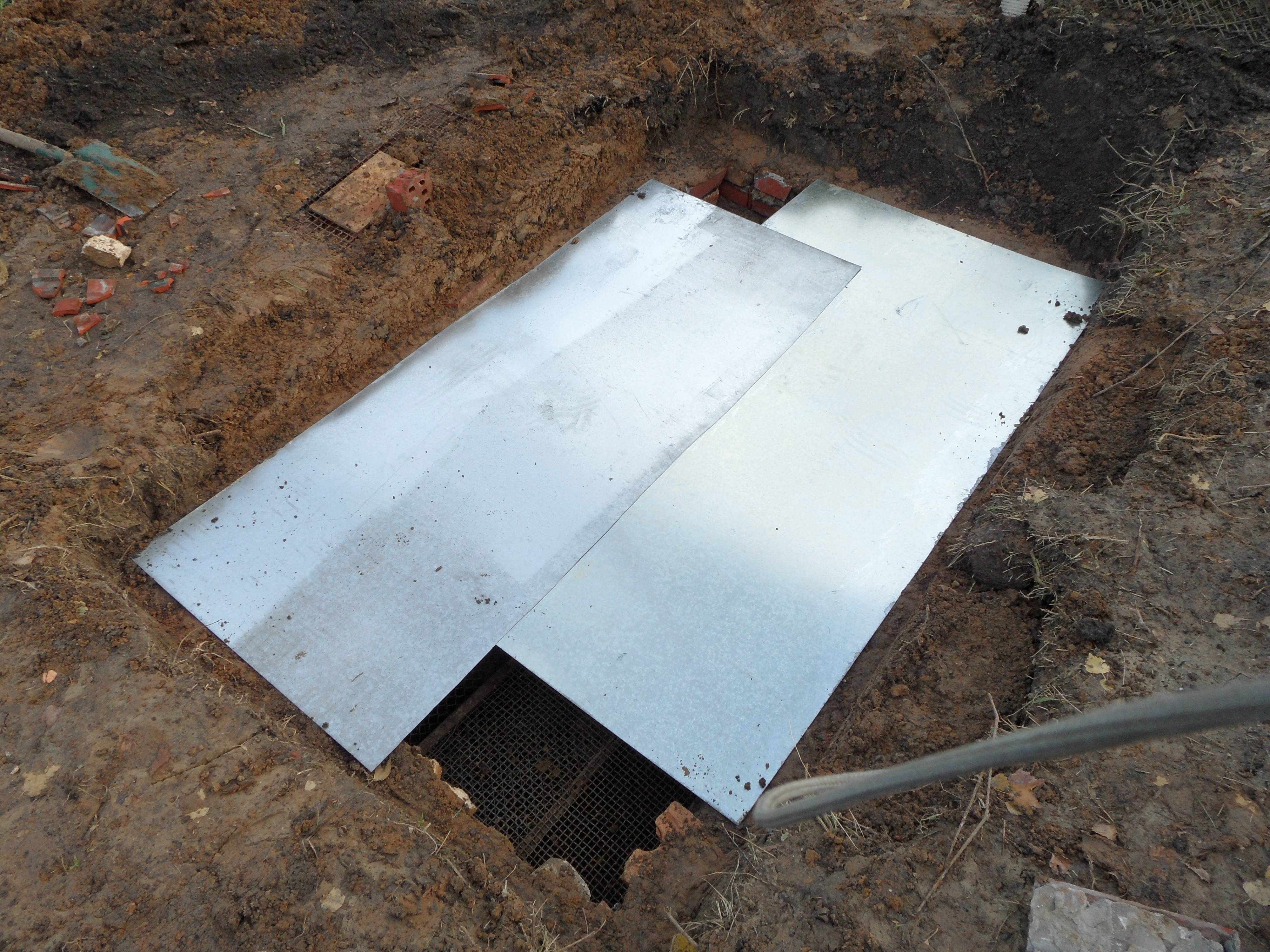
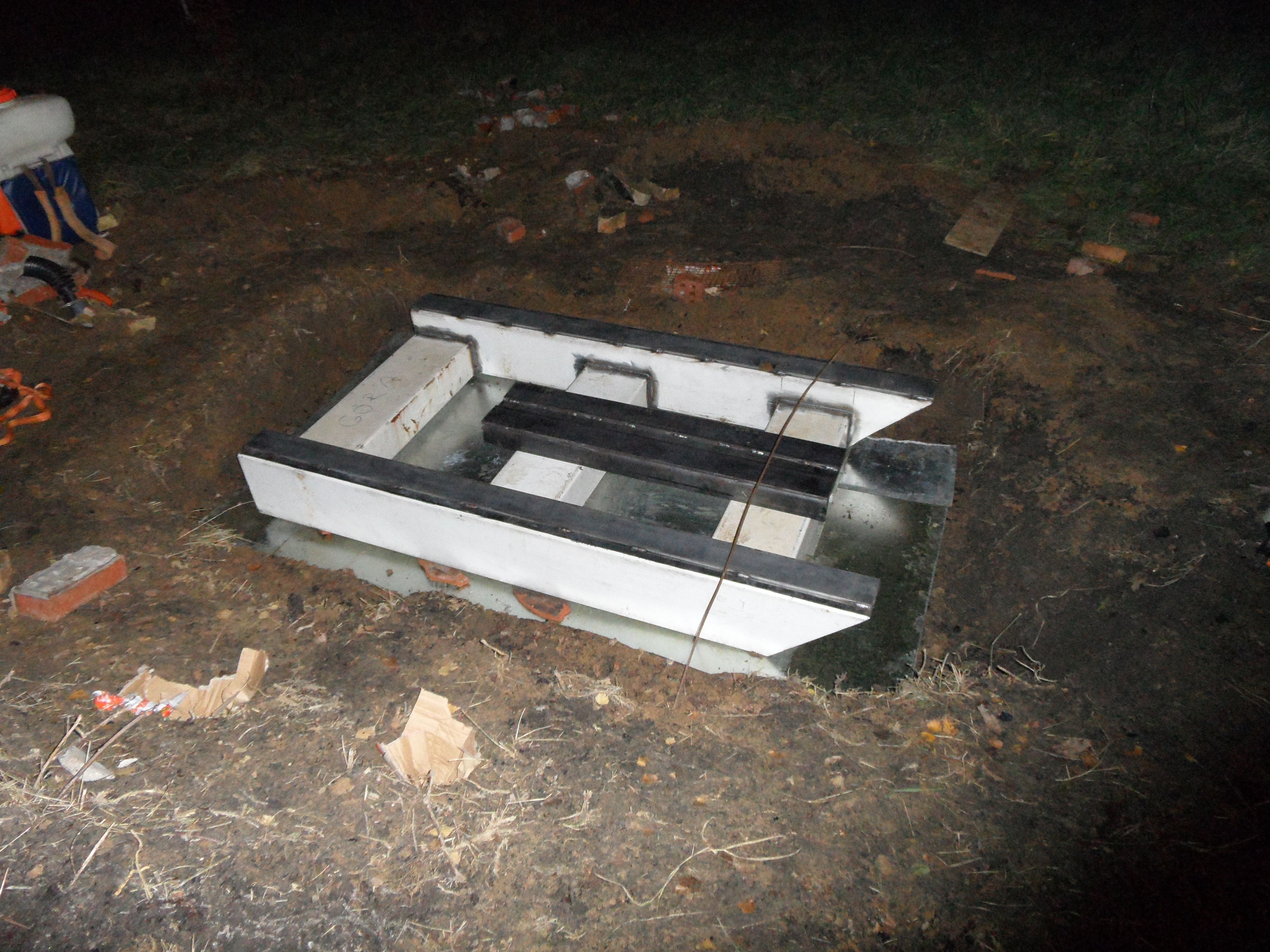

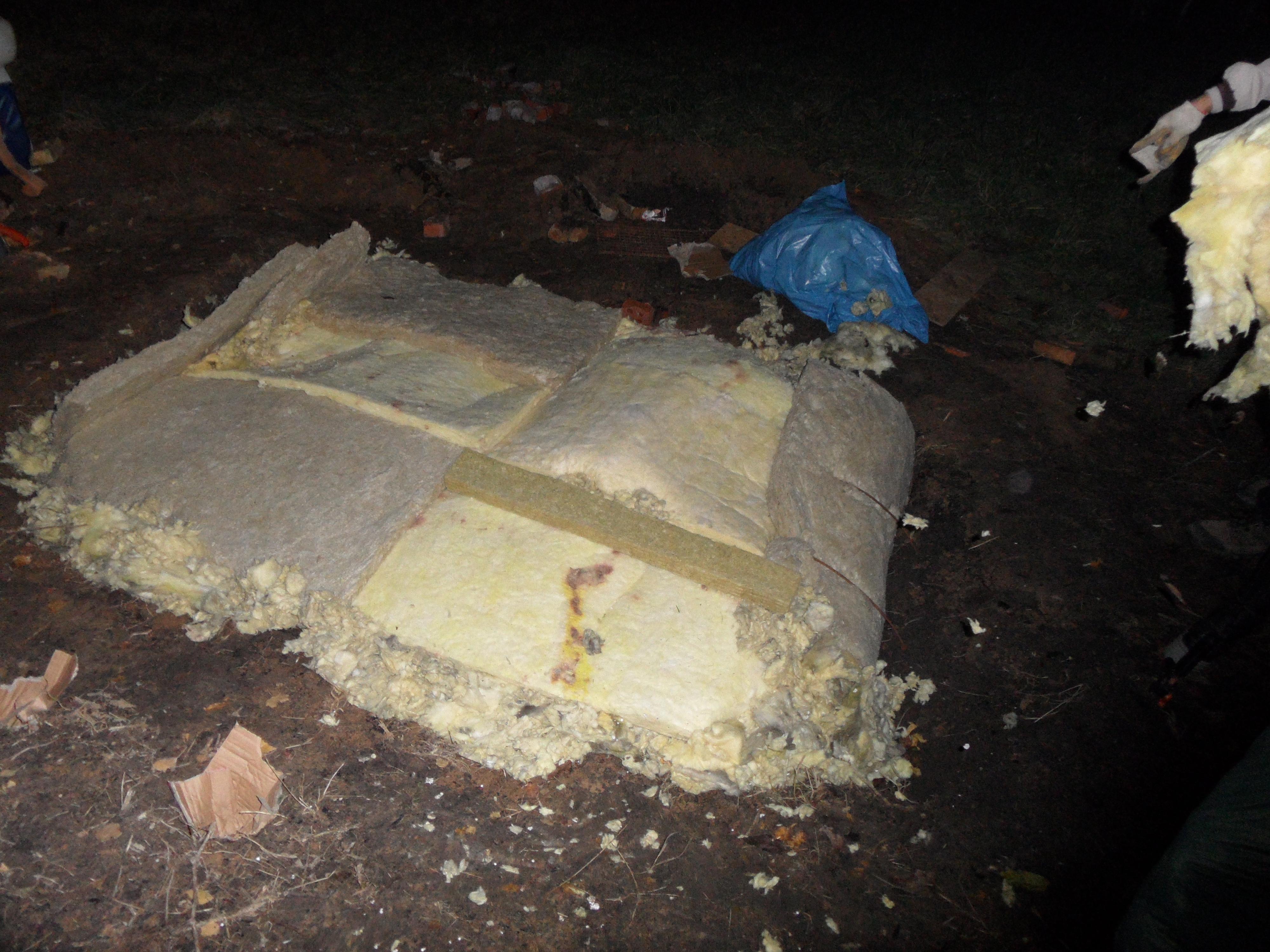
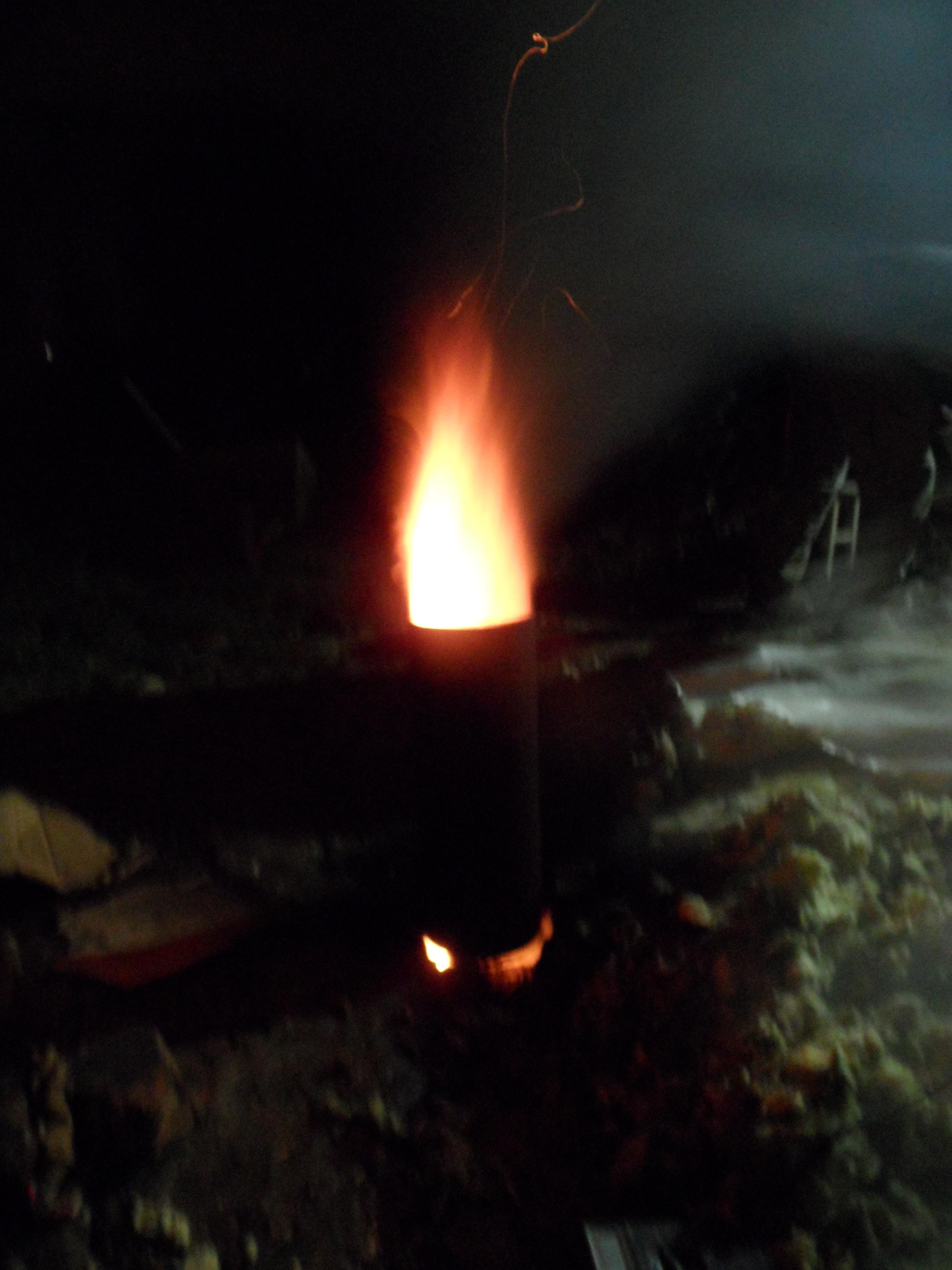
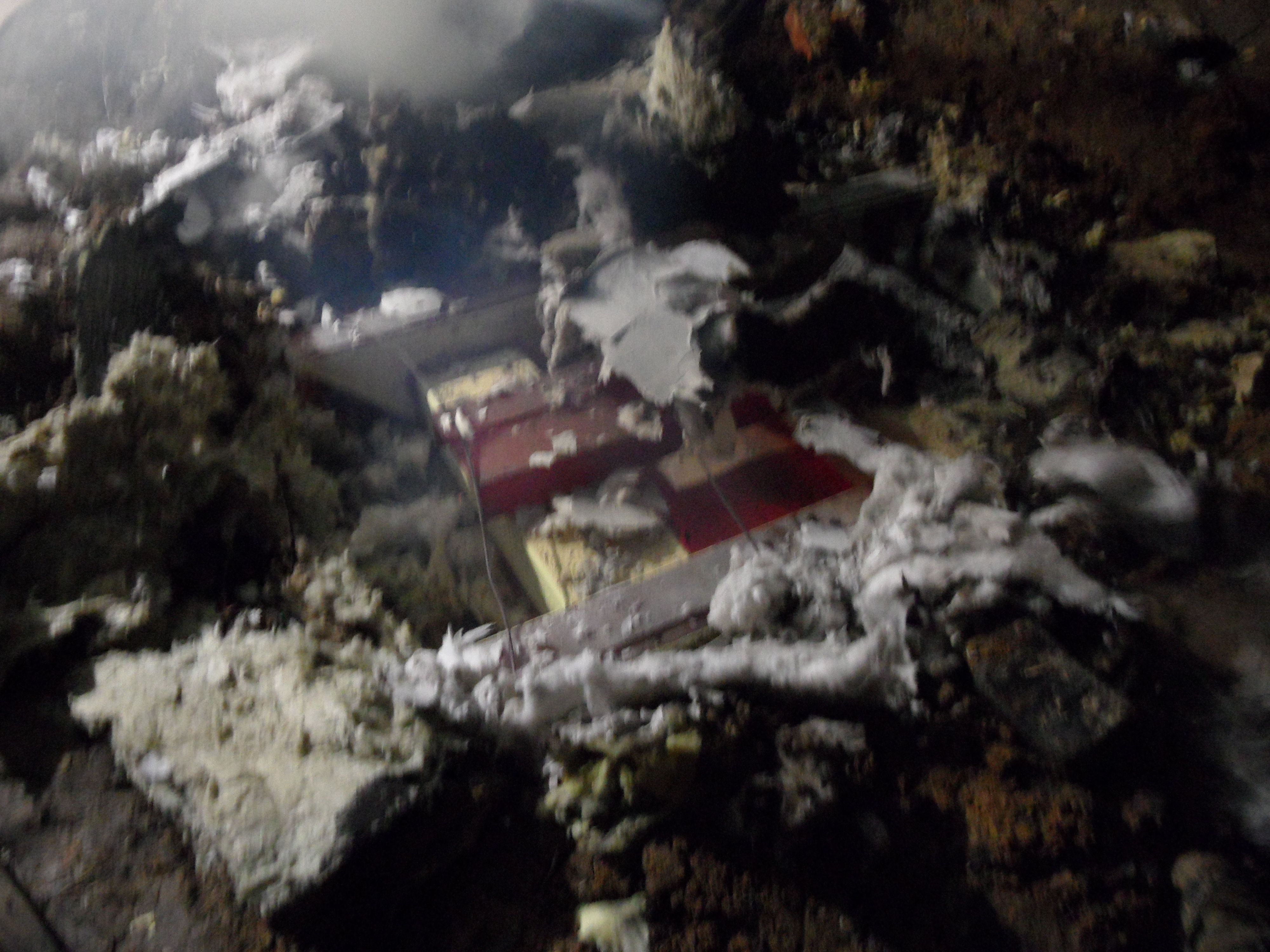
Na początku wszystko szło zgodnie z planem, zapaliliśmy węgiel bez problemu i szybko zaczęła się rozgrzewać komora z konstrukcją, po około 15-20 minutach było już w niej 300 stopni i cały czas rosła.
Ponieważ z kominów zaczął wylatywać spory ogień, wyłączyliśmy jedną dmuchawę a drugą ustawiliśmy na najmniejsze obroty. Temperatura praktycznie stanęła na 300 stopniach (nieznacznie się podnosiła) więc po około 5 minutach włączyliśmy z powrotem drugą dmuchawę( na najniższych obrotach mocniej dmuchała niż ta pierwsza), i temperatura zaczęła szybko rosnąć.
Coraz więcej dymu przelatywało przez komorę spalania, dlatego stale dokładaliśmy strzępy waty mineralnej w miejsca gdzie najbardziej dymiło.
Po około 40 minutach osiągnęliśmy temperaturę 400 stopni, ale przewody od miernika elektrycznego jak i końcówka (ta która nie powinna oczywiście) termopary zaczęły się mocno grzać, tak że dalszy pomiar nie miał sensu.
Zdemontowaliśmy termoparę z trochę przy topionymi przewodami po około 45 minutach.
Płomienie coraz bardziej przelatywały przez szczeliny pomiędzy blachami i niszczyły wełnę.
Po około godzinie przez szczelinę która powstała w wyniku stopienia wełny widać było że blacha na której stoi konstrukcja jest czerwona, konstrukcja również. Szczelinę tą zatkaliśmy strzępami waty.
Po około 3h miejscami wełna tak się stopiła że widać już było konstrukcję która była czerwonawa, zdjęliśmy resztę tej izolacji.
Po 24h węgiel dalej się żarzy a konstrukcja ma około 60 stopni.
Największym błędem w konstrukcji pieca były szczeliny pomiędzy blachami, pomimo tego 2 duże blachy miały zakładkę około 30cm i całkiem dobrze do siebie przylegały to płomienie bez problemu przelatywały i bezpośrednio stapiały wełnę której po 3h tak mało zostało że zdjęliśmy jej resztki. Najlepiej by było zastosować jedna dużą blachę lub porządnie uszczelnić łączenia. Gdybyśmy tak zrobili to prawdopodobnie nie zniszczyła by się tak wełna i mogli byśmy cały czas mierzyć temperaturę.
Kolejnym błędem była ilość kominów, lepszym rozwiązaniem było by zrobienie ich około 6 (fi100). Duży komin był zbyt blisko pieca i przez to płomienie wylatując niszczyły trochę wełnę od zewnątrz, dlatego daliśmy stalowa rurę.
Dmuchawy do liści spokojnie mogłyby być zastąpione zwykłymi wentylatorami łazienkowymi bo żeby osiągnąć wysoką temperaturę nie trzeba było mocno dmuchać.
Warstwę węgla kamiennego jaką daliśmy miała około 13-15cm i wydawało nam się że jeśli chcemy otrzymać temperaturę koło 600 stopni nie wystarczy go na więcej niż pół godziny, jak się okazało to było aż za nadto. Bazując na kolorze żarzącej się stali wydaję mi się że osiągnęliśmy 600 stopni lub nawet więcej. Wełna mineralna podobno zaczyna się topić w temperaturze 700 stopni a nam się jej trochę stopiło
Sprawdzałem dzisiaj czy nie pogięła się rama, ale wygląda że jest tak jak po spawaniu (patrzyłem tylko na równość długich profili bo czy się zwichrowała nie miałem jak sprawdzić)
Najgłupszą wpadką było nie przewiercenie profili łączących te długie, ponieważ były szczelnie zamknięte wytworzyło się tam niezłe ciśnienie i wyobliło je trochę. Nie wiem jak mogliśmy przeoczyć coś tak oczywistego
Jak macie jakieś pytania to śmiało.
Wszytko piszę z głowy więc mam nadzieję że niczego nie przekręciłem a czas się mniej więcej zgadza.
Ogólnie jestem zadowolony z całego procesu, i myślę że spełnił swoje zadanie, ale
niestety w trakcie wyżarzania wyszło na jaw parę błędów które można było uniknąć a które zaraz opiszę.
Piec zrobilimy podobnie do tego planu który zamieściłem w tym wątku, różnił się
jednak paroma szczegółami.
Wloty powietrza były tylko po dwóch stronach, i zamiast wentylatorów do
wtłaczania powietrza użylimy spalinowych dmuchaw do liści.
Kominy były 3, również po dwóch stronach, z tym, że jeden komin był tak duży jak te dwa po przeciwległej stornie.
Komory w której była rama ostatecznie nie przysypaliśmy ziemią.
Pod konstrukcje podłożyliśmy kawałki dachówki żeby nie dotykała bezpośredni blachy.
Wełna mineralna nie dotykała konstrukcji frezarki tylko była parę cm nad nią, utrzymywana na stalowych prętach. Na zdjęciu widać jeden, ale potem wbiliśmy z 8 kolejnych.
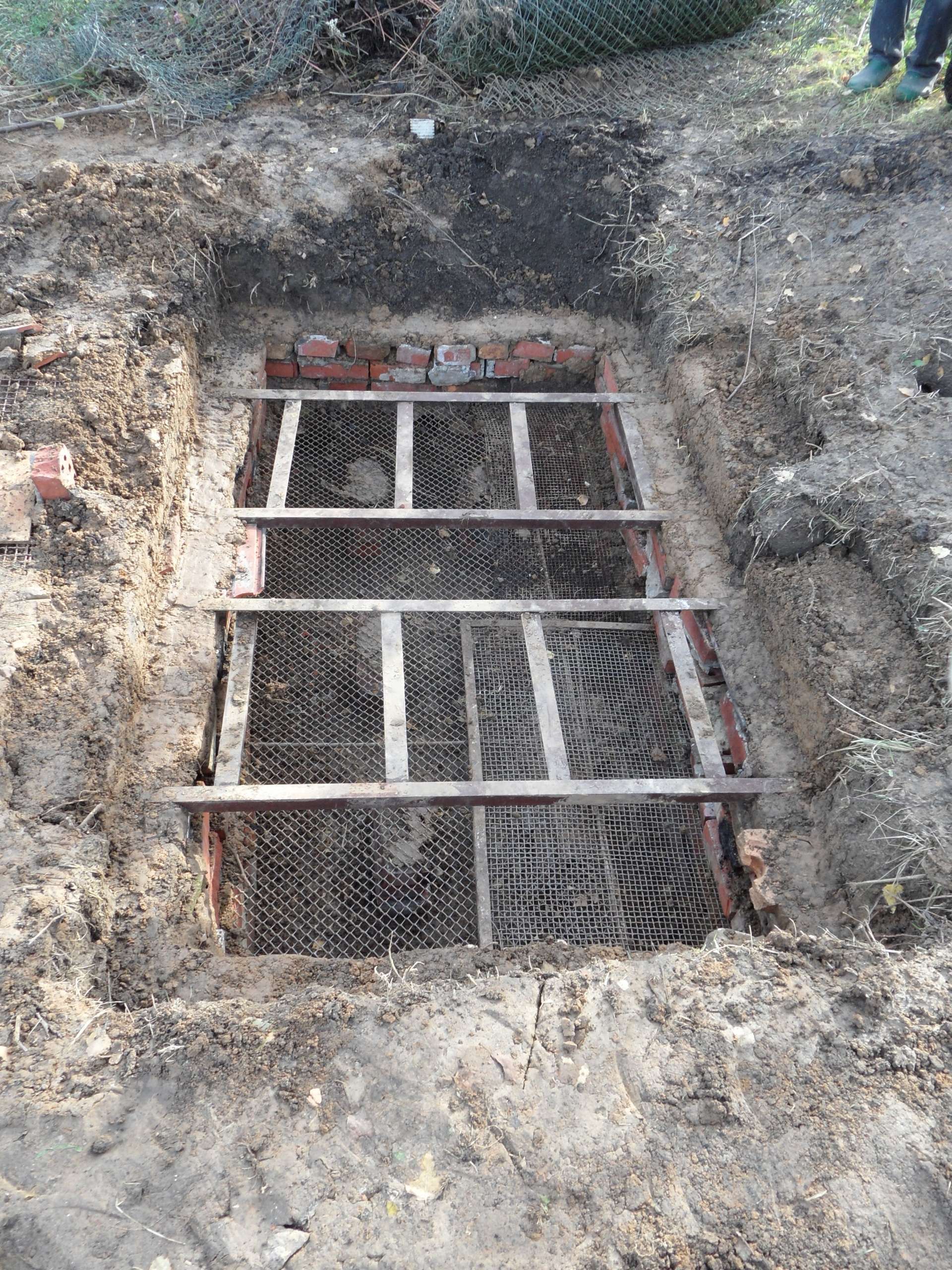
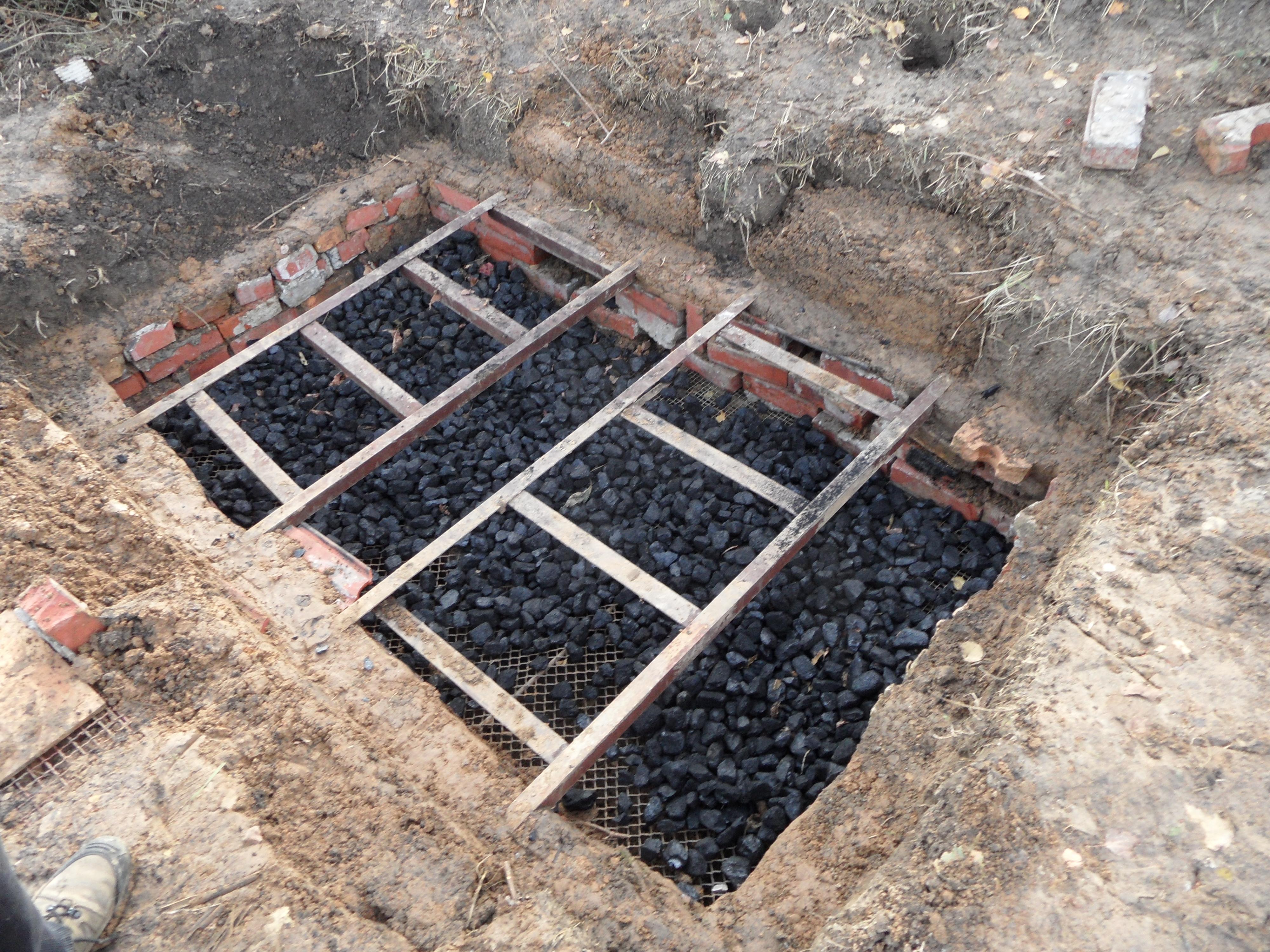
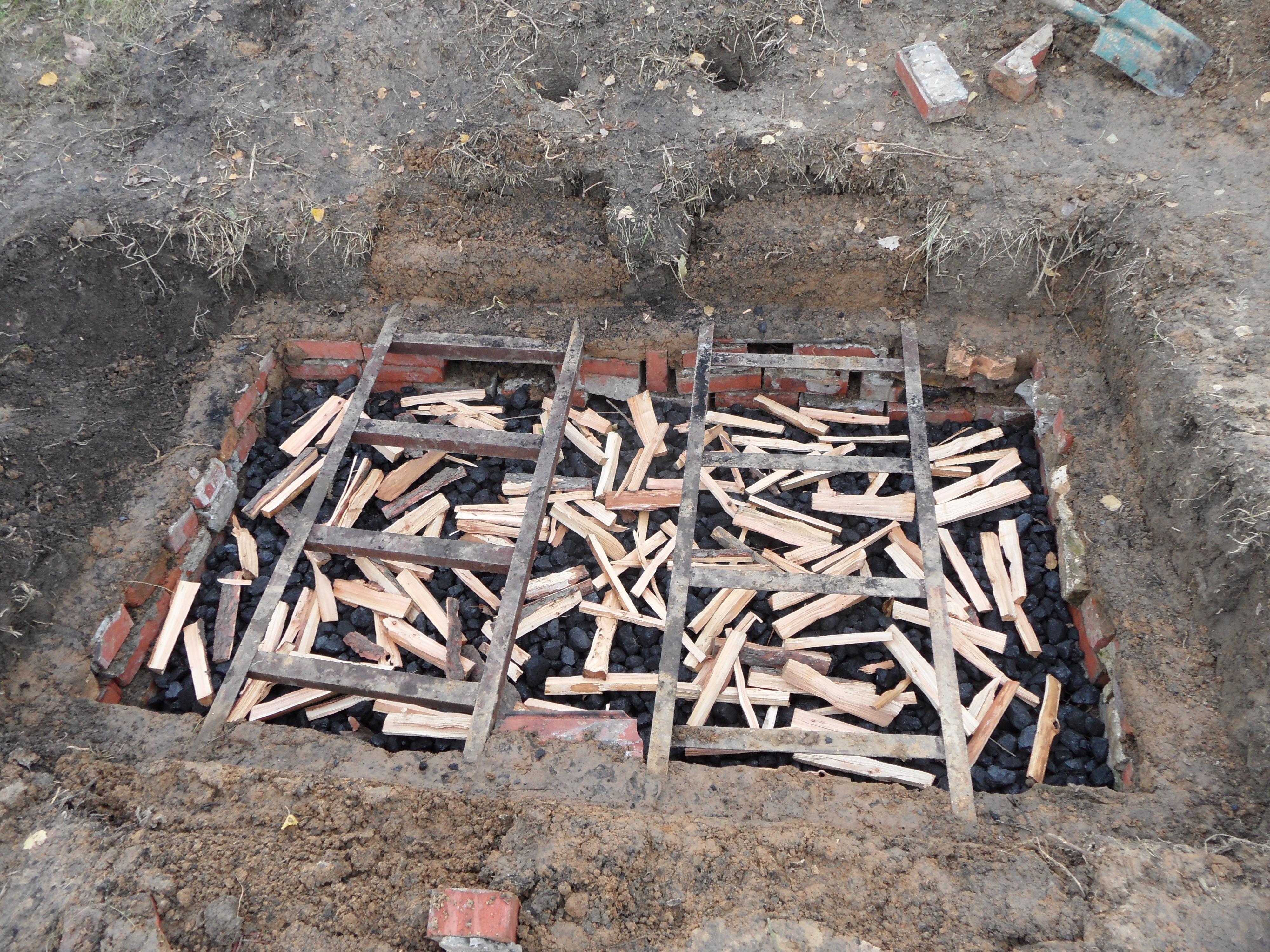
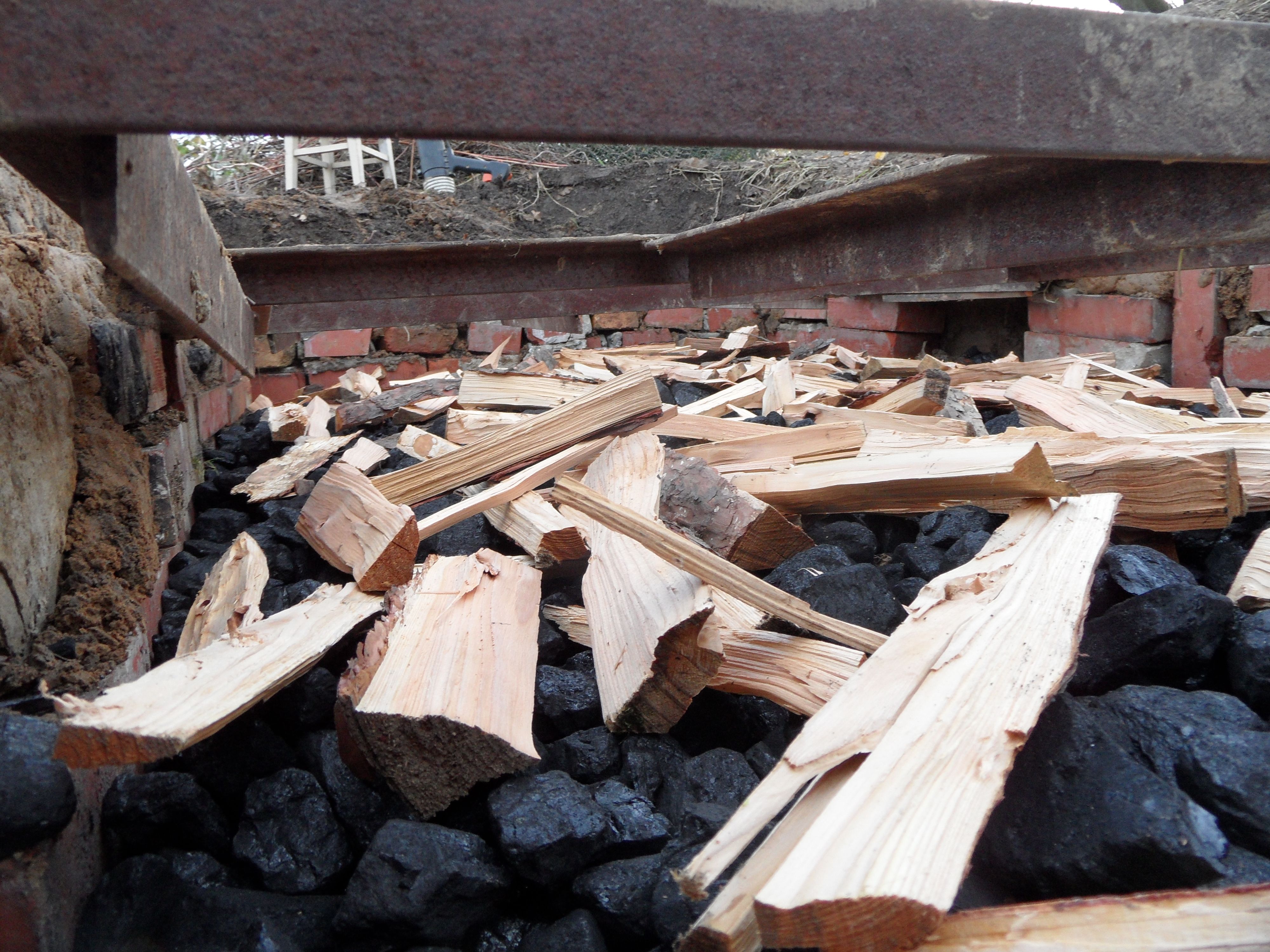
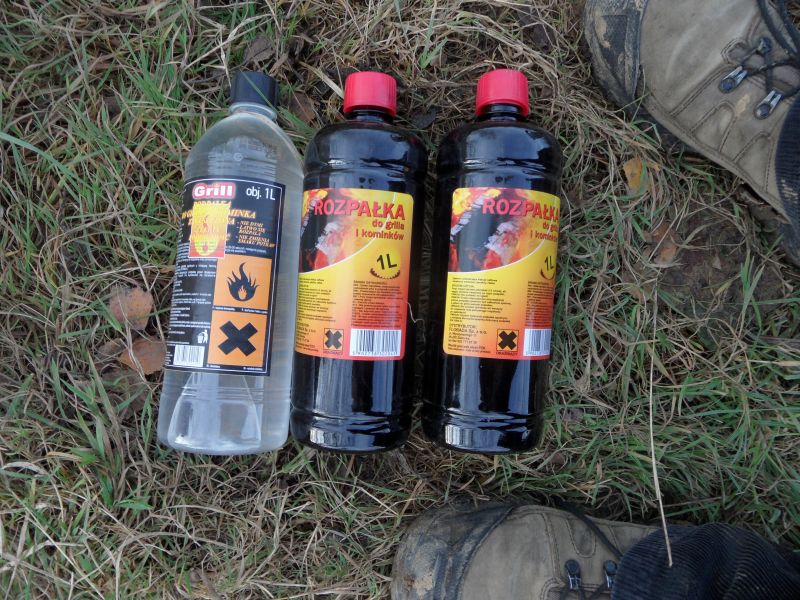
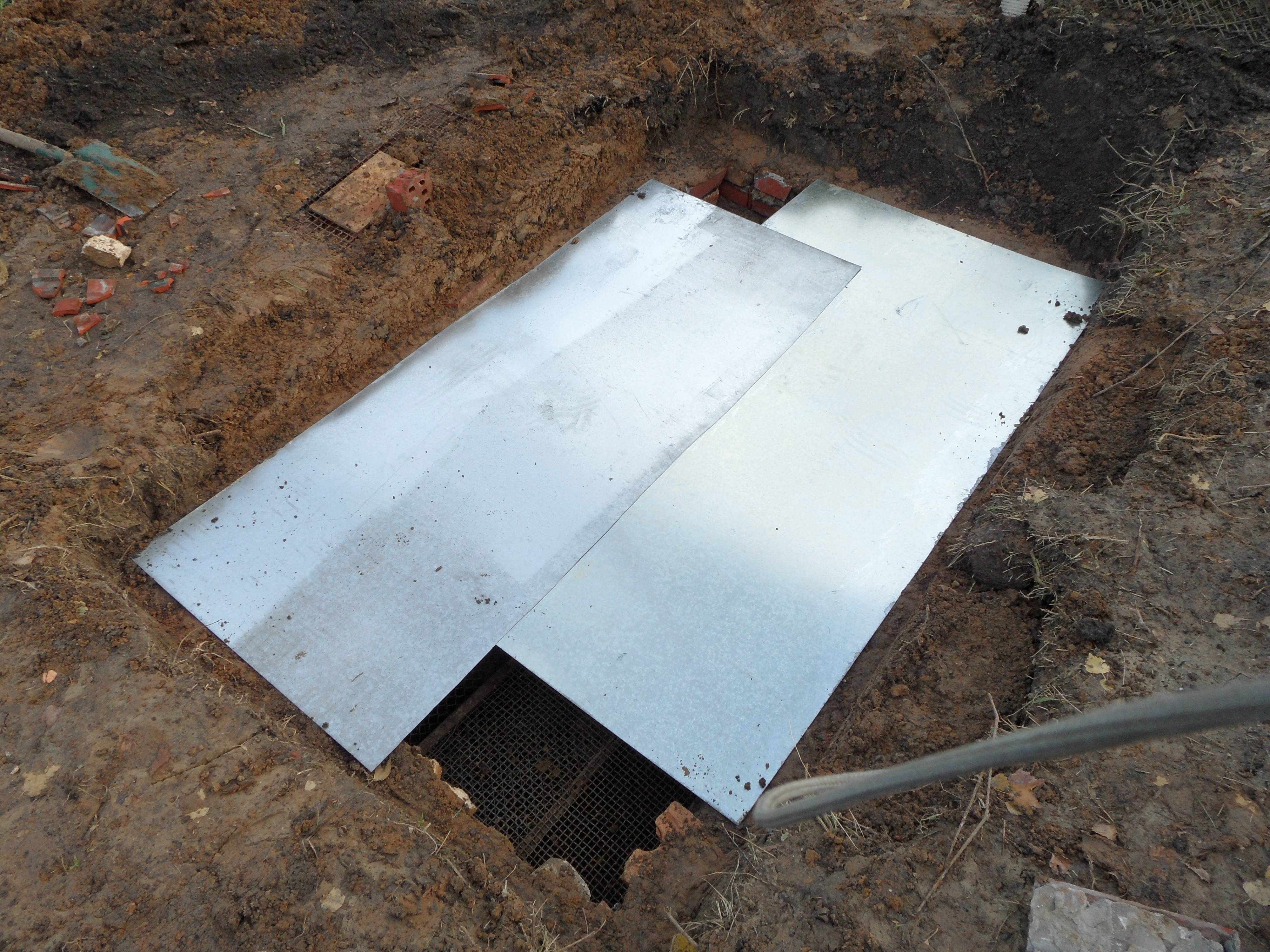
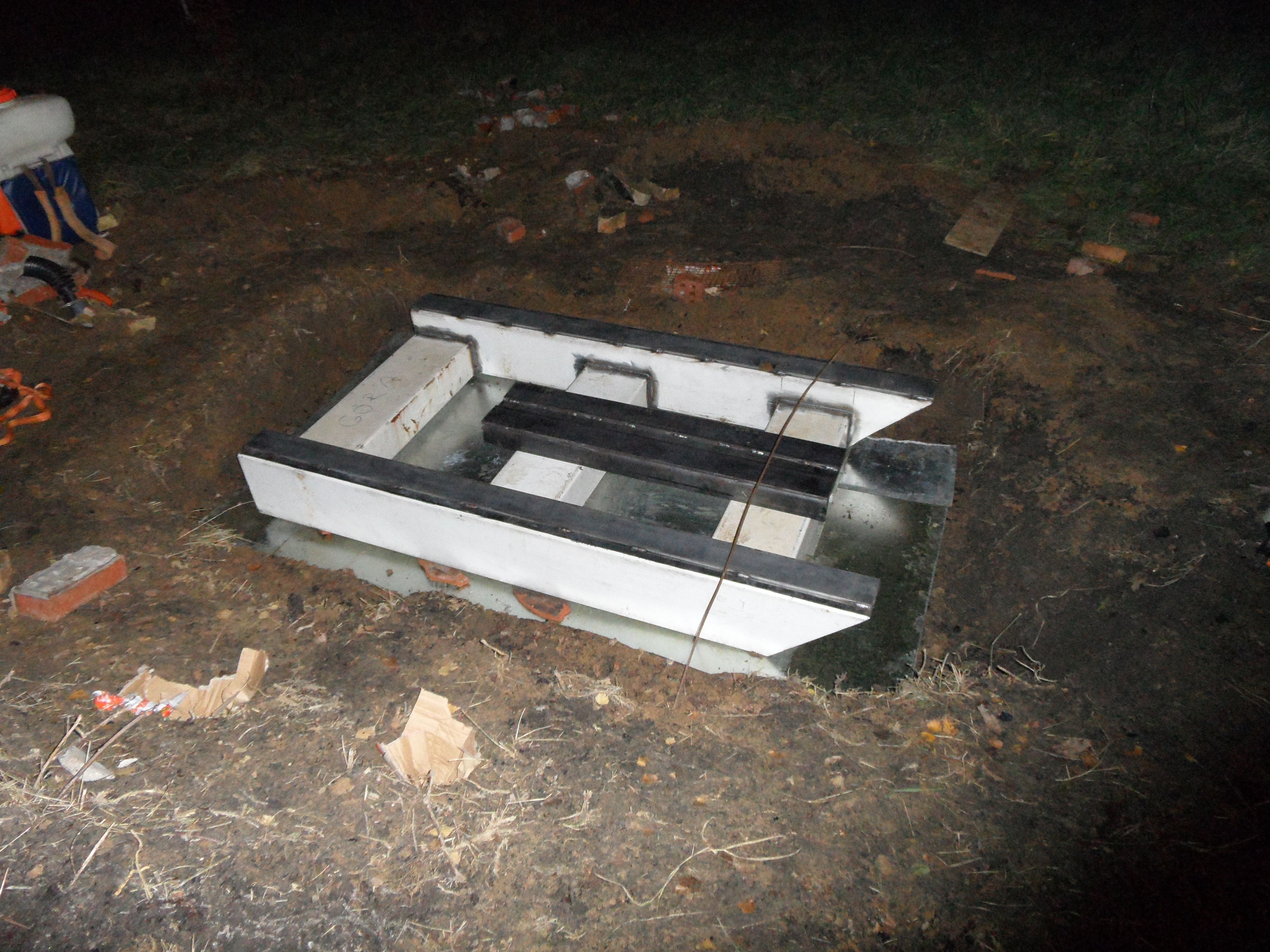

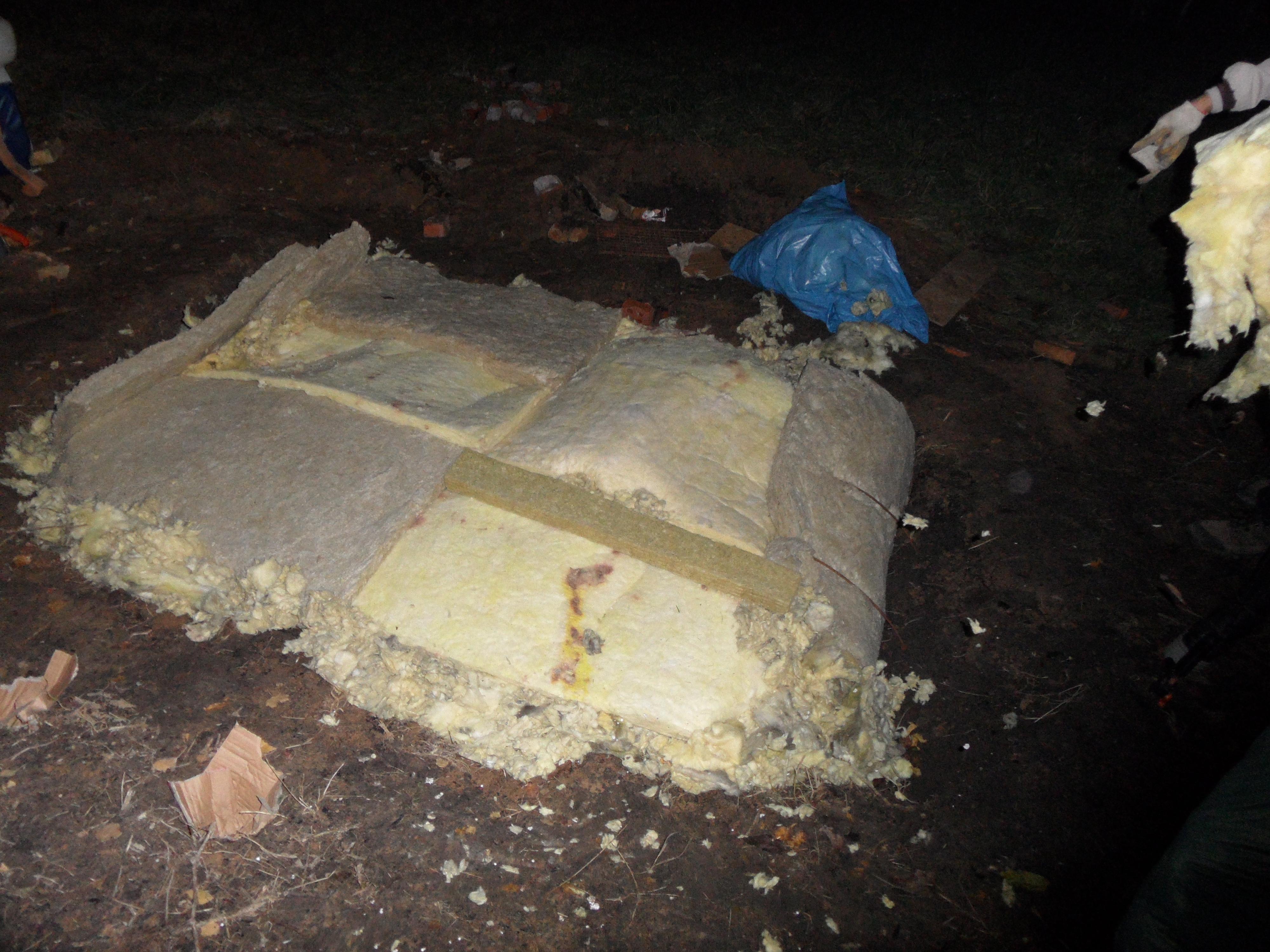
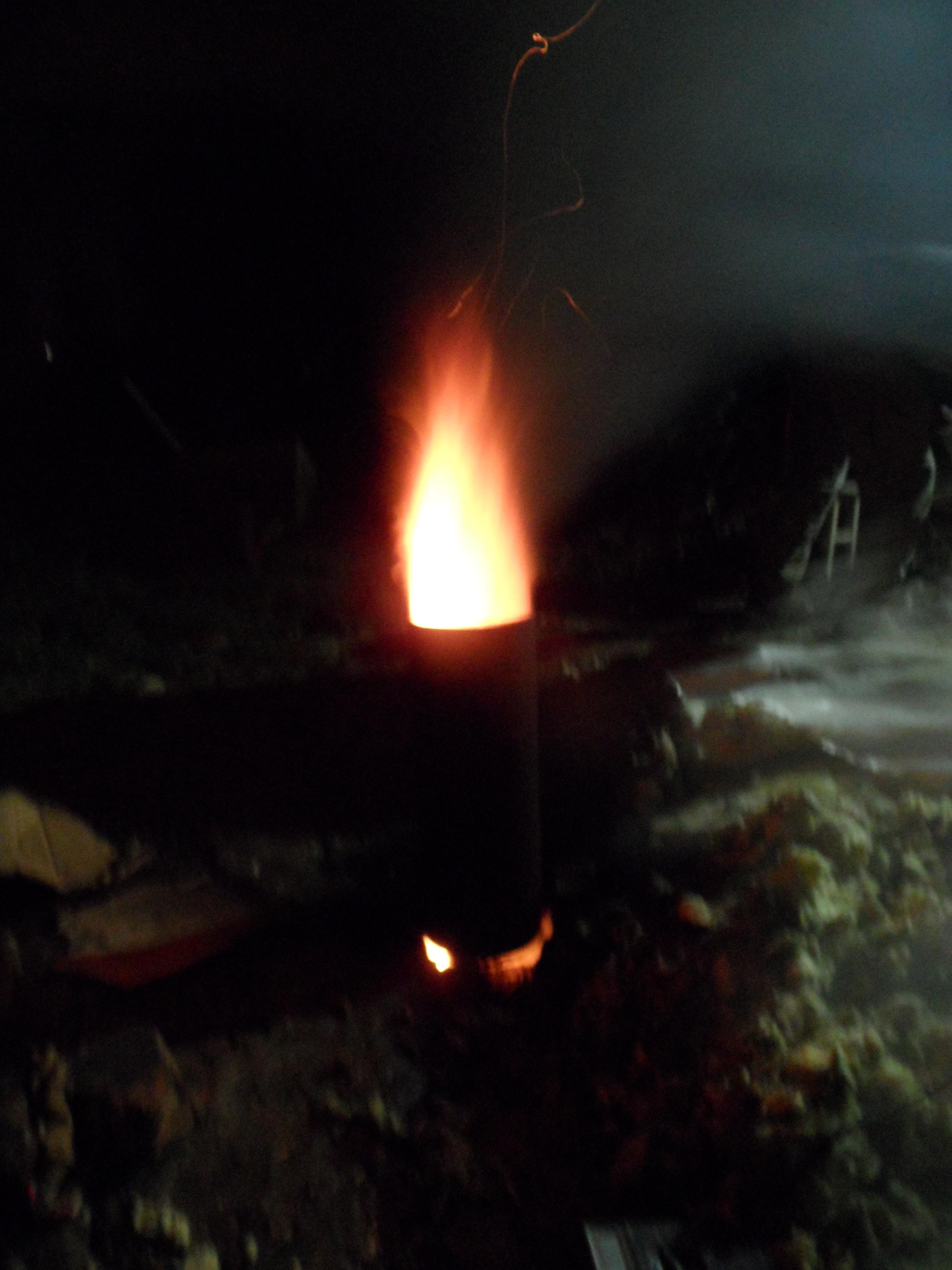
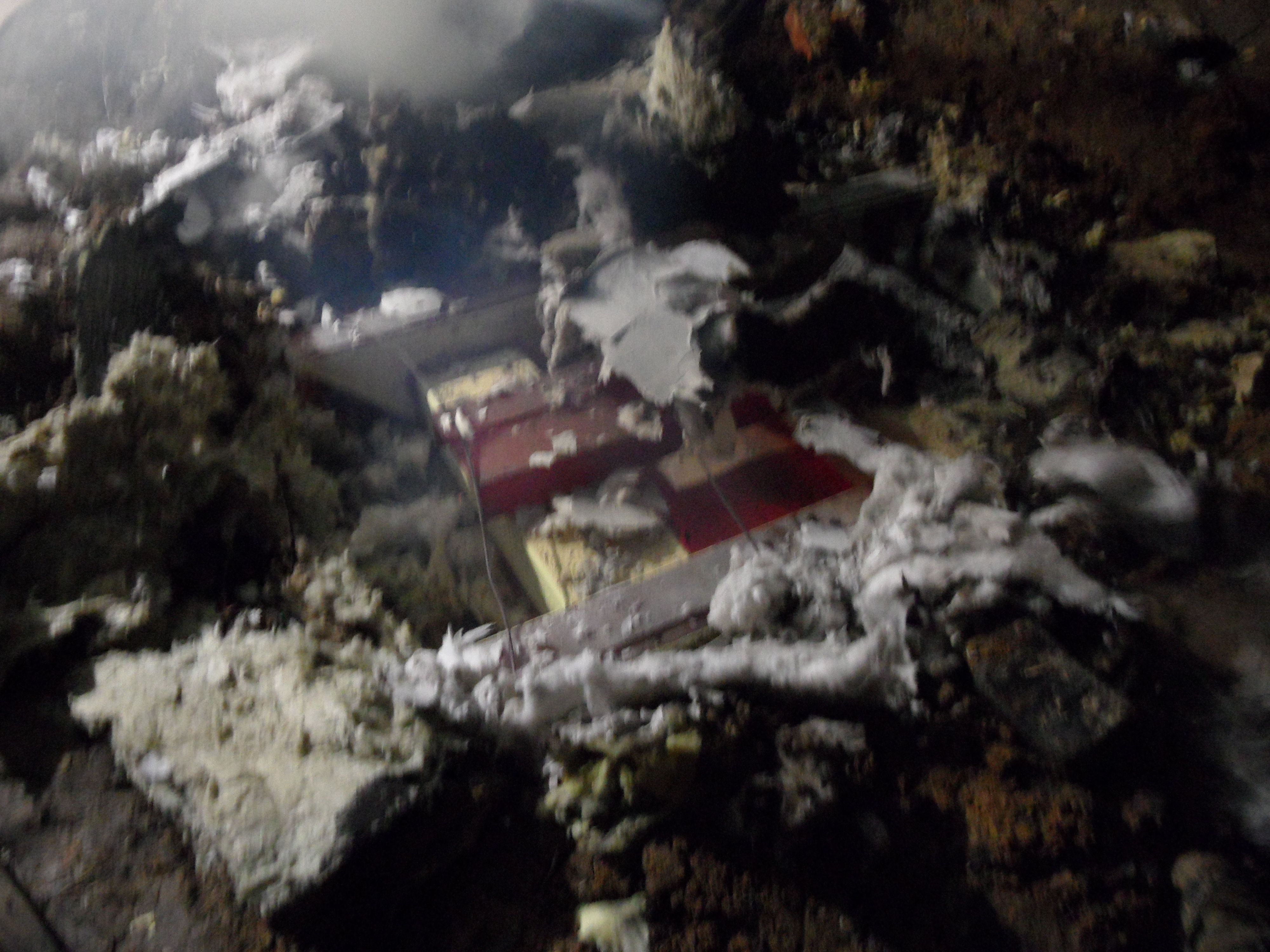
Na początku wszystko szło zgodnie z planem, zapaliliśmy węgiel bez problemu i szybko zaczęła się rozgrzewać komora z konstrukcją, po około 15-20 minutach było już w niej 300 stopni i cały czas rosła.
Ponieważ z kominów zaczął wylatywać spory ogień, wyłączyliśmy jedną dmuchawę a drugą ustawiliśmy na najmniejsze obroty. Temperatura praktycznie stanęła na 300 stopniach (nieznacznie się podnosiła) więc po około 5 minutach włączyliśmy z powrotem drugą dmuchawę( na najniższych obrotach mocniej dmuchała niż ta pierwsza), i temperatura zaczęła szybko rosnąć.
Coraz więcej dymu przelatywało przez komorę spalania, dlatego stale dokładaliśmy strzępy waty mineralnej w miejsca gdzie najbardziej dymiło.
Po około 40 minutach osiągnęliśmy temperaturę 400 stopni, ale przewody od miernika elektrycznego jak i końcówka (ta która nie powinna oczywiście) termopary zaczęły się mocno grzać, tak że dalszy pomiar nie miał sensu.
Zdemontowaliśmy termoparę z trochę przy topionymi przewodami po około 45 minutach.
Płomienie coraz bardziej przelatywały przez szczeliny pomiędzy blachami i niszczyły wełnę.
Po około godzinie przez szczelinę która powstała w wyniku stopienia wełny widać było że blacha na której stoi konstrukcja jest czerwona, konstrukcja również. Szczelinę tą zatkaliśmy strzępami waty.
Po około 3h miejscami wełna tak się stopiła że widać już było konstrukcję która była czerwonawa, zdjęliśmy resztę tej izolacji.
Po 24h węgiel dalej się żarzy a konstrukcja ma około 60 stopni.
Największym błędem w konstrukcji pieca były szczeliny pomiędzy blachami, pomimo tego 2 duże blachy miały zakładkę około 30cm i całkiem dobrze do siebie przylegały to płomienie bez problemu przelatywały i bezpośrednio stapiały wełnę której po 3h tak mało zostało że zdjęliśmy jej resztki. Najlepiej by było zastosować jedna dużą blachę lub porządnie uszczelnić łączenia. Gdybyśmy tak zrobili to prawdopodobnie nie zniszczyła by się tak wełna i mogli byśmy cały czas mierzyć temperaturę.
Kolejnym błędem była ilość kominów, lepszym rozwiązaniem było by zrobienie ich około 6 (fi100). Duży komin był zbyt blisko pieca i przez to płomienie wylatując niszczyły trochę wełnę od zewnątrz, dlatego daliśmy stalowa rurę.
Dmuchawy do liści spokojnie mogłyby być zastąpione zwykłymi wentylatorami łazienkowymi bo żeby osiągnąć wysoką temperaturę nie trzeba było mocno dmuchać.
Warstwę węgla kamiennego jaką daliśmy miała około 13-15cm i wydawało nam się że jeśli chcemy otrzymać temperaturę koło 600 stopni nie wystarczy go na więcej niż pół godziny, jak się okazało to było aż za nadto. Bazując na kolorze żarzącej się stali wydaję mi się że osiągnęliśmy 600 stopni lub nawet więcej. Wełna mineralna podobno zaczyna się topić w temperaturze 700 stopni a nam się jej trochę stopiło

Sprawdzałem dzisiaj czy nie pogięła się rama, ale wygląda że jest tak jak po spawaniu (patrzyłem tylko na równość długich profili bo czy się zwichrowała nie miałem jak sprawdzić)
Najgłupszą wpadką było nie przewiercenie profili łączących te długie, ponieważ były szczelnie zamknięte wytworzyło się tam niezłe ciśnienie i wyobliło je trochę. Nie wiem jak mogliśmy przeoczyć coś tak oczywistego

Jak macie jakieś pytania to śmiało.
Wszytko piszę z głowy więc mam nadzieję że niczego nie przekręciłem a czas się mniej więcej zgadza.
-
Autor tematu - Specjalista poziom 3 (min. 600)
- Posty w temacie: 143
- Posty: 663
- Rejestracja: 01 lut 2011, 00:31
- Lokalizacja: Bolechowice/Kraków
Brama już czeka na zawiezienie do jakiegoś frezera/zakładu
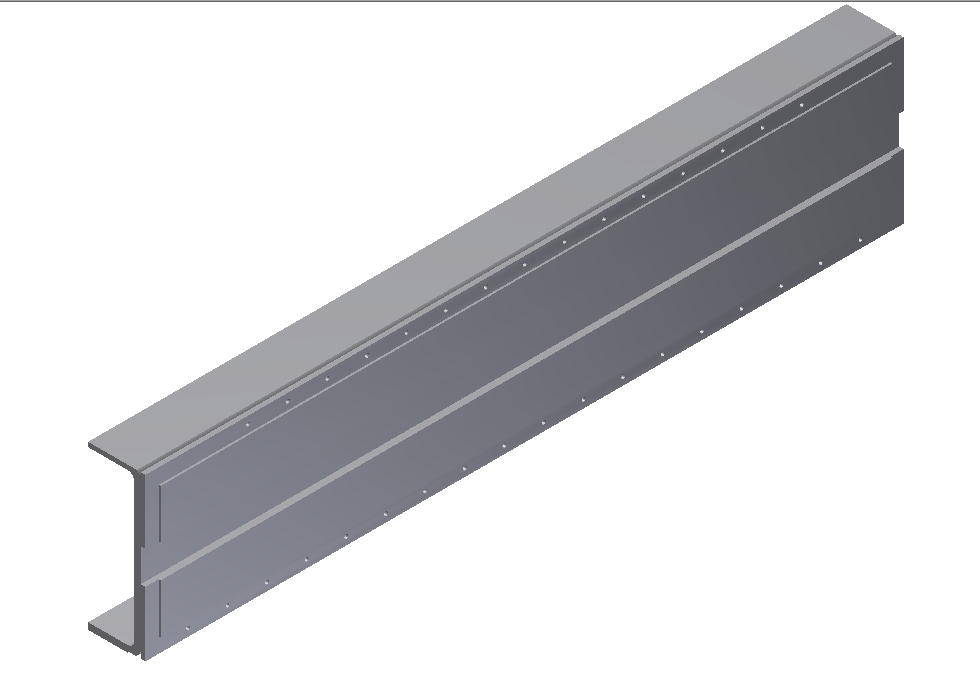
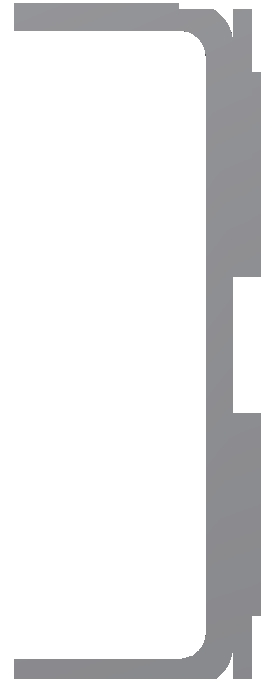
Dzisiaj przyszedł pocztą blok z łożyskami linowymi Star który mam zamiar przerobić na blok pod zwykłe łożyska. Zdjęcie zrobiłem żeby porównać
ile więcej "mięsa" jest w porządnych blokach niż w chińskich, obydwie te obudowy są pod łożyska liniowe 30 (otwór 47mm)
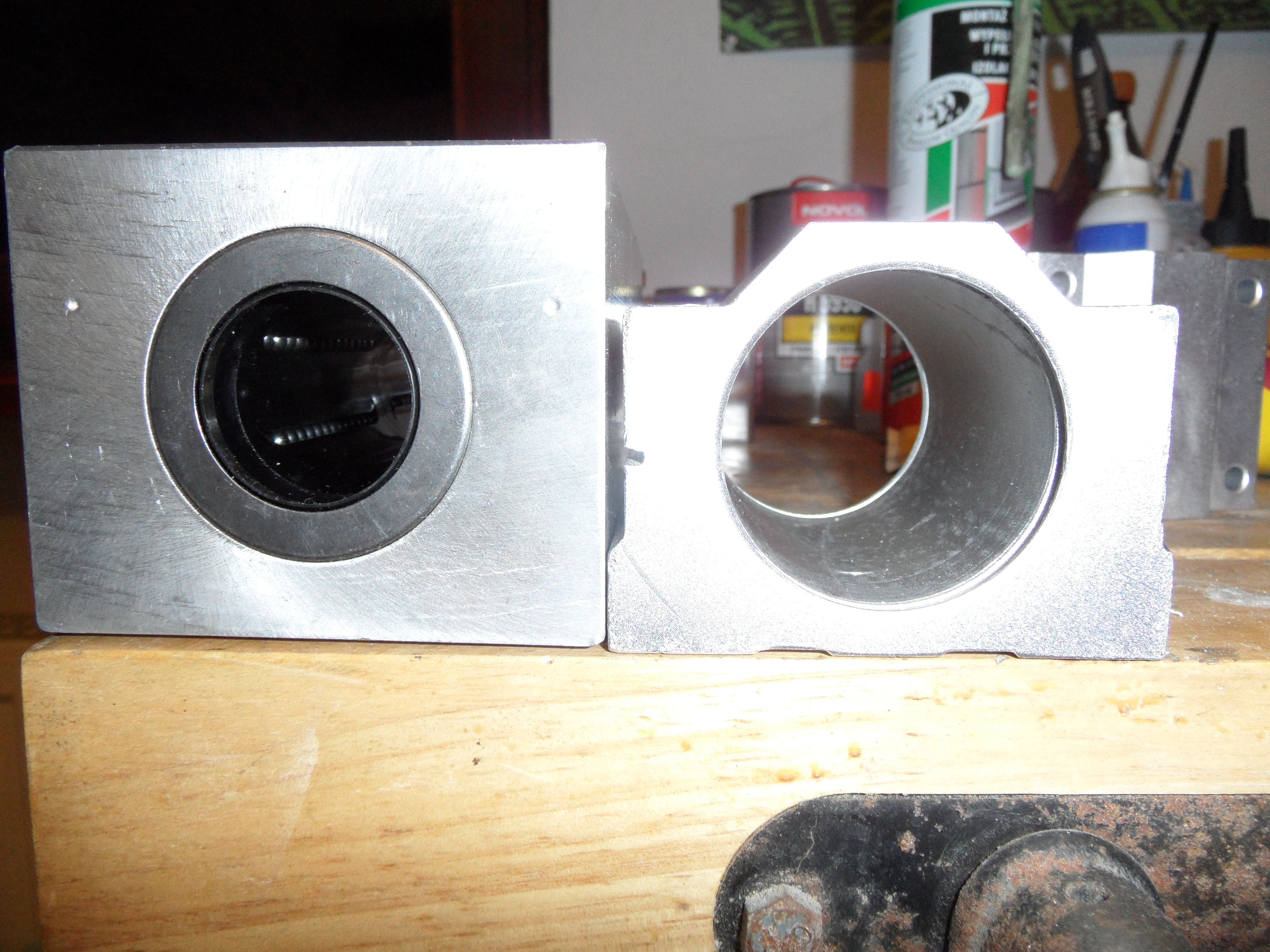
Co do sterowania to będę próbował zrobić 4 sterowniki
http://www.max-mod-shop.com/index.php?o ... 3Ayapsc10v
Jak się uda to maszynka będzie śmigać na serwach
Udało mi się uruchomić jeden silnik krokowy (na samym początku wątku jest pokazany)
używając tej szafki elektronicznej, kręci się ale ma problemy ze startami, ciężko mu też zacząć się kręcić i jak się zatrzyma i znowu ruszy to potrafi zmienić kierunek obrotów,
nie wiem co jest na rzeczy ale podejrzewam że go po prostu źle podpiąłem, nieźle się zdziwiłem że w ogóle zaczął się kręcić
Niestety przyszła zima i mam problem, chciałem zrobić wylewkę pod prowadnice z żywicy, ale są już ujemne temperatury i raczej się nie uda, będę musiał poczekać
z tym aż do wiosny
chyba że jest jakaś dobra żywica która dobrze wiąże nawet przy niskich temperaturach, zna ktoś taką ?
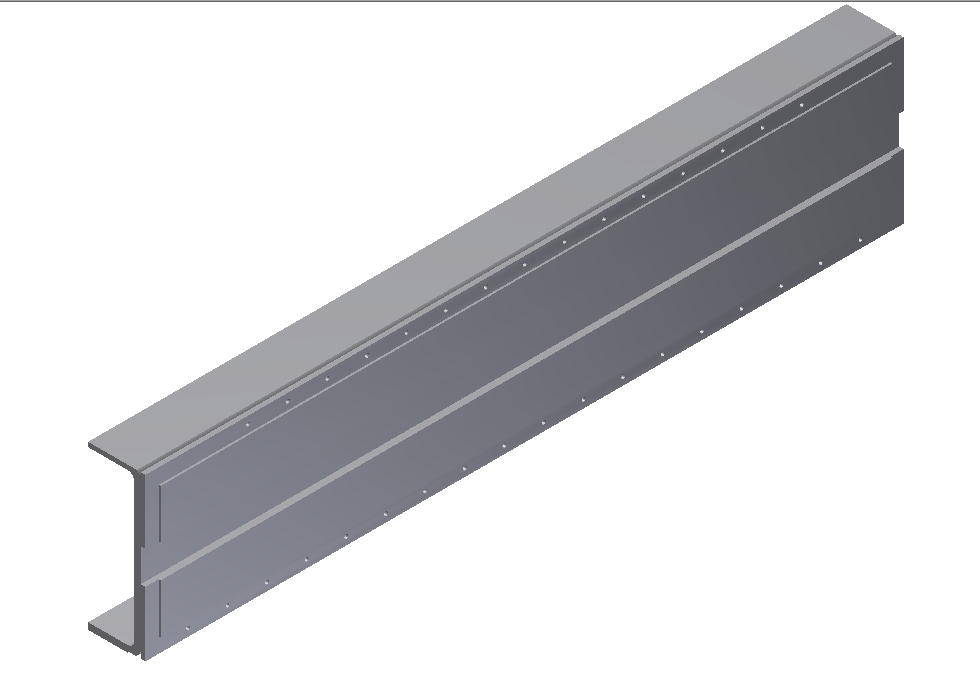
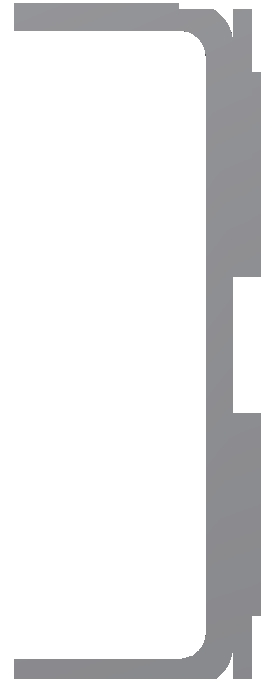
Dzisiaj przyszedł pocztą blok z łożyskami linowymi Star który mam zamiar przerobić na blok pod zwykłe łożyska. Zdjęcie zrobiłem żeby porównać
ile więcej "mięsa" jest w porządnych blokach niż w chińskich, obydwie te obudowy są pod łożyska liniowe 30 (otwór 47mm)
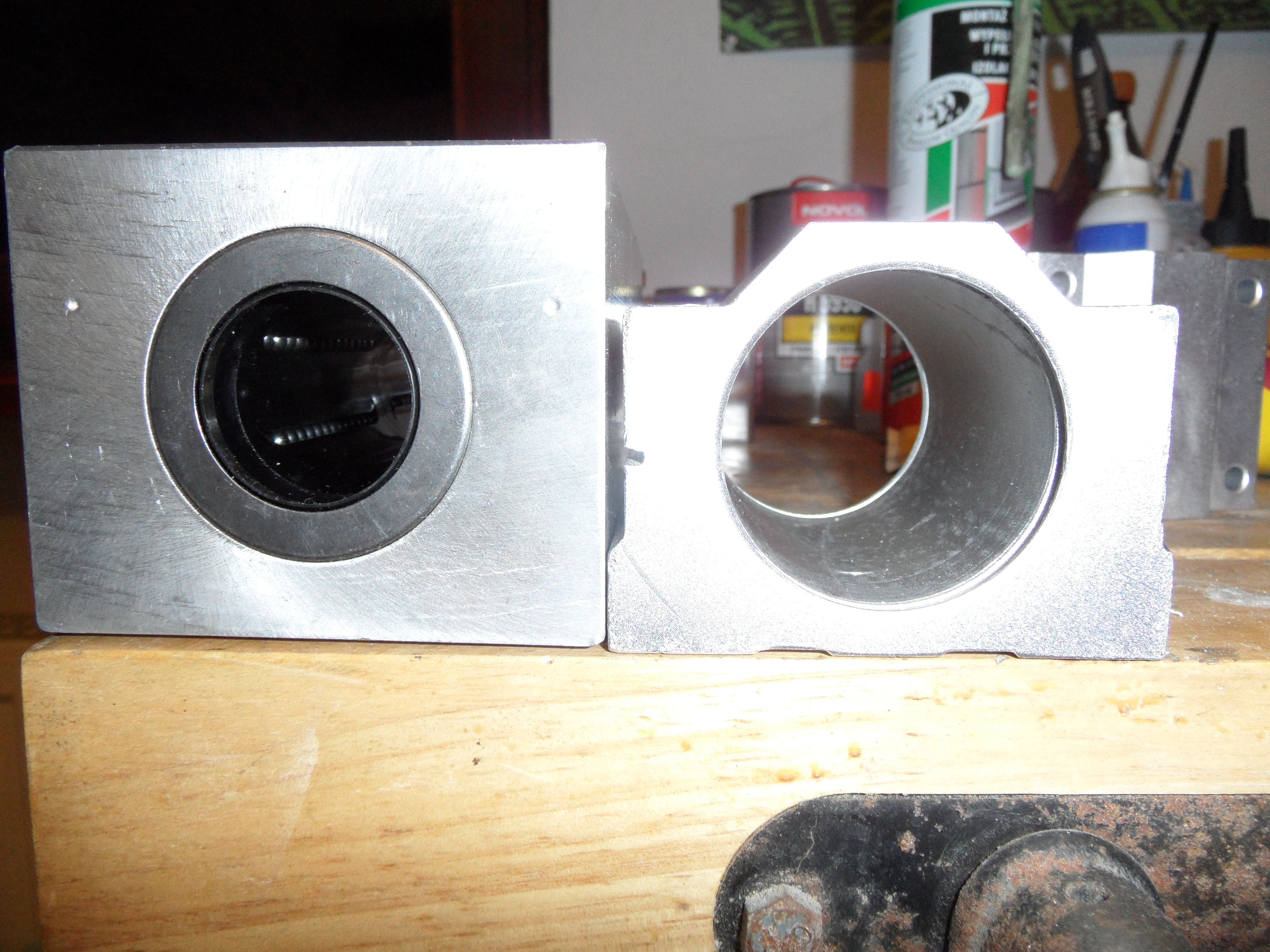
Co do sterowania to będę próbował zrobić 4 sterowniki
http://www.max-mod-shop.com/index.php?o ... 3Ayapsc10v
Jak się uda to maszynka będzie śmigać na serwach

Udało mi się uruchomić jeden silnik krokowy (na samym początku wątku jest pokazany)
używając tej szafki elektronicznej, kręci się ale ma problemy ze startami, ciężko mu też zacząć się kręcić i jak się zatrzyma i znowu ruszy to potrafi zmienić kierunek obrotów,
nie wiem co jest na rzeczy ale podejrzewam że go po prostu źle podpiąłem, nieźle się zdziwiłem że w ogóle zaczął się kręcić

Niestety przyszła zima i mam problem, chciałem zrobić wylewkę pod prowadnice z żywicy, ale są już ujemne temperatury i raczej się nie uda, będę musiał poczekać
z tym aż do wiosny

Ostatnio zmieniony 09 gru 2012, 18:25 przez Malaxis, łącznie zmieniany 1 raz.
-
- Specjalista poziom 3 (min. 600)
- Posty w temacie: 22
- Posty: 613
- Rejestracja: 22 lis 2006, 15:41
- Lokalizacja: Bochnia/Kraków
-
Autor tematu - Specjalista poziom 3 (min. 600)
- Posty w temacie: 143
- Posty: 663
- Rejestracja: 01 lut 2011, 00:31
- Lokalizacja: Bolechowice/Kraków
Mam problem, nie wiem jak wyjąć łożyska liniowe z obudowy nie niszcząc ich
Z jednej strony uszczelniacz jest 6mm od łożyska więc gdyby udało się go wyjąć to mógłbym
spróbować wybić łożyska jakimś kawałkiem drewna. Wygląda to tak:
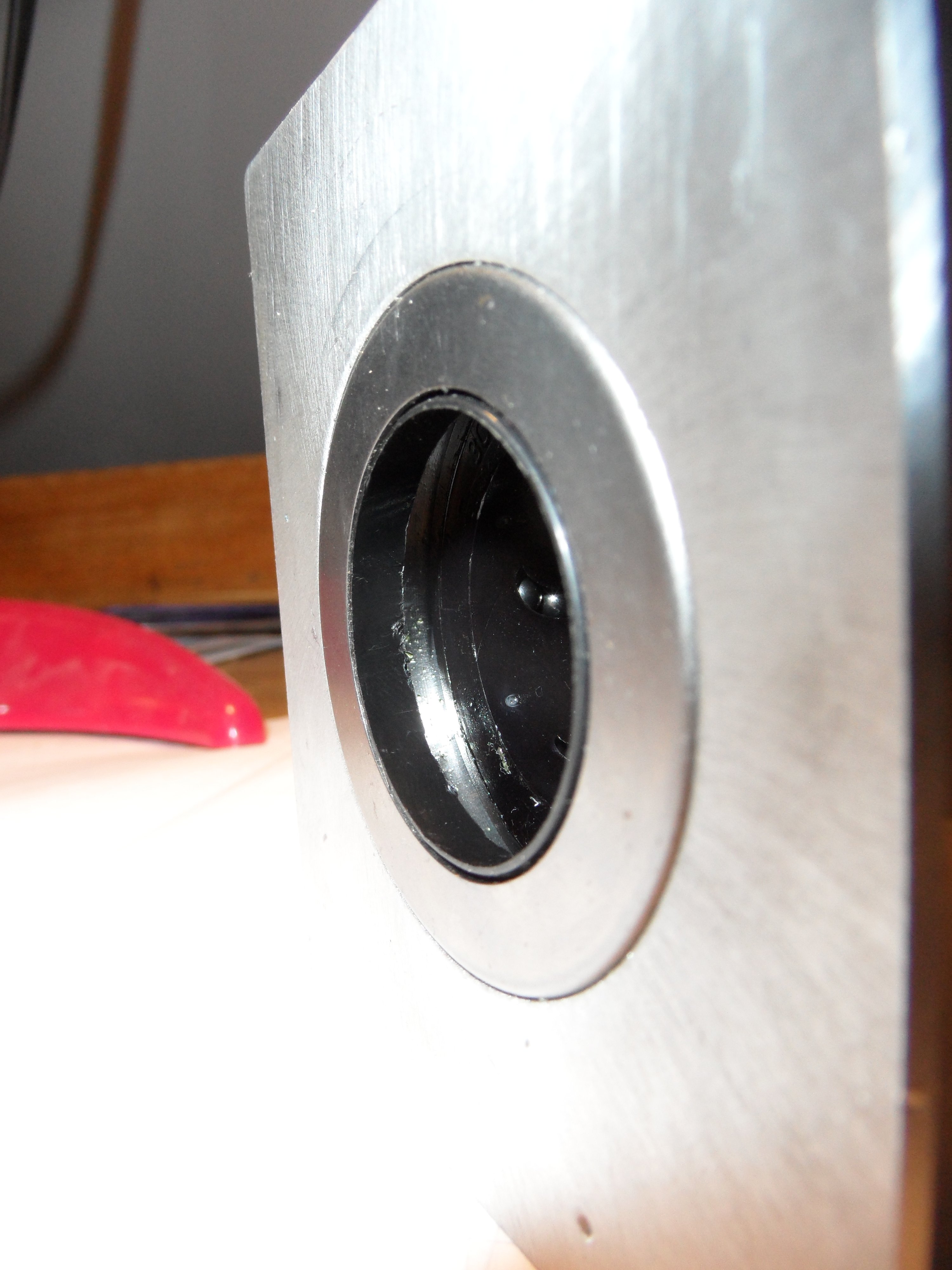
Myślałem żeby ten uszczelniać wyjąć za pomocą przyrządu do ściągania łożysk, ale ten który posiadam ma za grube końcówki.
Może miał ktoś podobny problem i wie jak najlepiej się za to zabrać ?

Z jednej strony uszczelniacz jest 6mm od łożyska więc gdyby udało się go wyjąć to mógłbym
spróbować wybić łożyska jakimś kawałkiem drewna. Wygląda to tak:
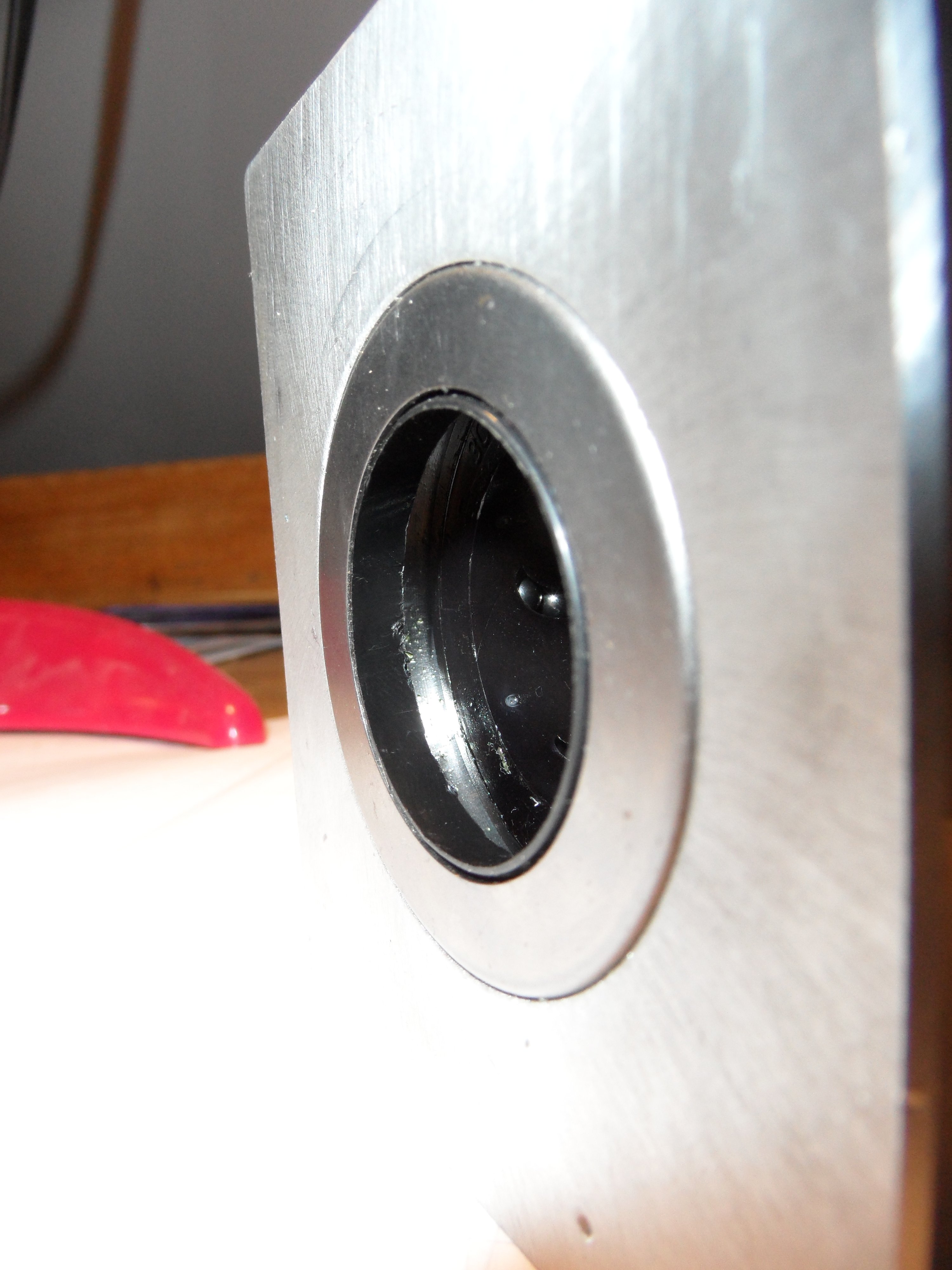
Myślałem żeby ten uszczelniać wyjąć za pomocą przyrządu do ściągania łożysk, ale ten który posiadam ma za grube końcówki.
Może miał ktoś podobny problem i wie jak najlepiej się za to zabrać ?
-
Autor tematu - Specjalista poziom 3 (min. 600)
- Posty w temacie: 143
- Posty: 663
- Rejestracja: 01 lut 2011, 00:31
- Lokalizacja: Bolechowice/Kraków
Łożyska wyjęte. Gdzie w Krakowie przetną mi taki blok na pile taśmowej ?
nie mogę w google znaleźć żadnych firm/warsztatów które chwalą się usługami
cięcia na pile taśmowej. Najlepiej jak by był jakiś w okolicach Bronowic, ale
jako że nie mogę znaleźć w ogóle to za każdą wskazówkę lokalizacji będę bardzo wdzięczny.
nie mogę w google znaleźć żadnych firm/warsztatów które chwalą się usługami
cięcia na pile taśmowej. Najlepiej jak by był jakiś w okolicach Bronowic, ale
jako że nie mogę znaleźć w ogóle to za każdą wskazówkę lokalizacji będę bardzo wdzięczny.
-
Autor tematu - Specjalista poziom 3 (min. 600)
- Posty w temacie: 143
- Posty: 663
- Rejestracja: 01 lut 2011, 00:31
- Lokalizacja: Bolechowice/Kraków
Mam kolejne pytanie, nie miał by ktoś pomysłu jak ściągnąć koło pasowe z wału silnika?
Koło jest aluminiowe, może się zniszczyć przy zdejmowaniu bo i tak wygląda na zużyte.
Może jakimiś chemikaliami co aluminium niszczą a stal nie?
Myślałem że odkręcę robaczka i śrubokrętem podważę od tyłu i je wsunę, ale strasznie ciężko siedzi.
Nie mam kompletnie pomysłu jak się za to zabrać żeby nie uszkodzić wału silnika.
Co do postępów z pracami, to mam już wytoczone tulejki do nakrętek obrotowych, muszę w nich wykonać otwory do zamocowania do nakrętki kulowej, nagwintować oraz zrobić płytkę która będzie od zewnątrz powstrzymywała łożyska od wypadnięcia. Zdecydowałem się użyć do przeniesienia napędu paski HTD 3M o szerokości 15mm za radą techników od sponsora, polecam.
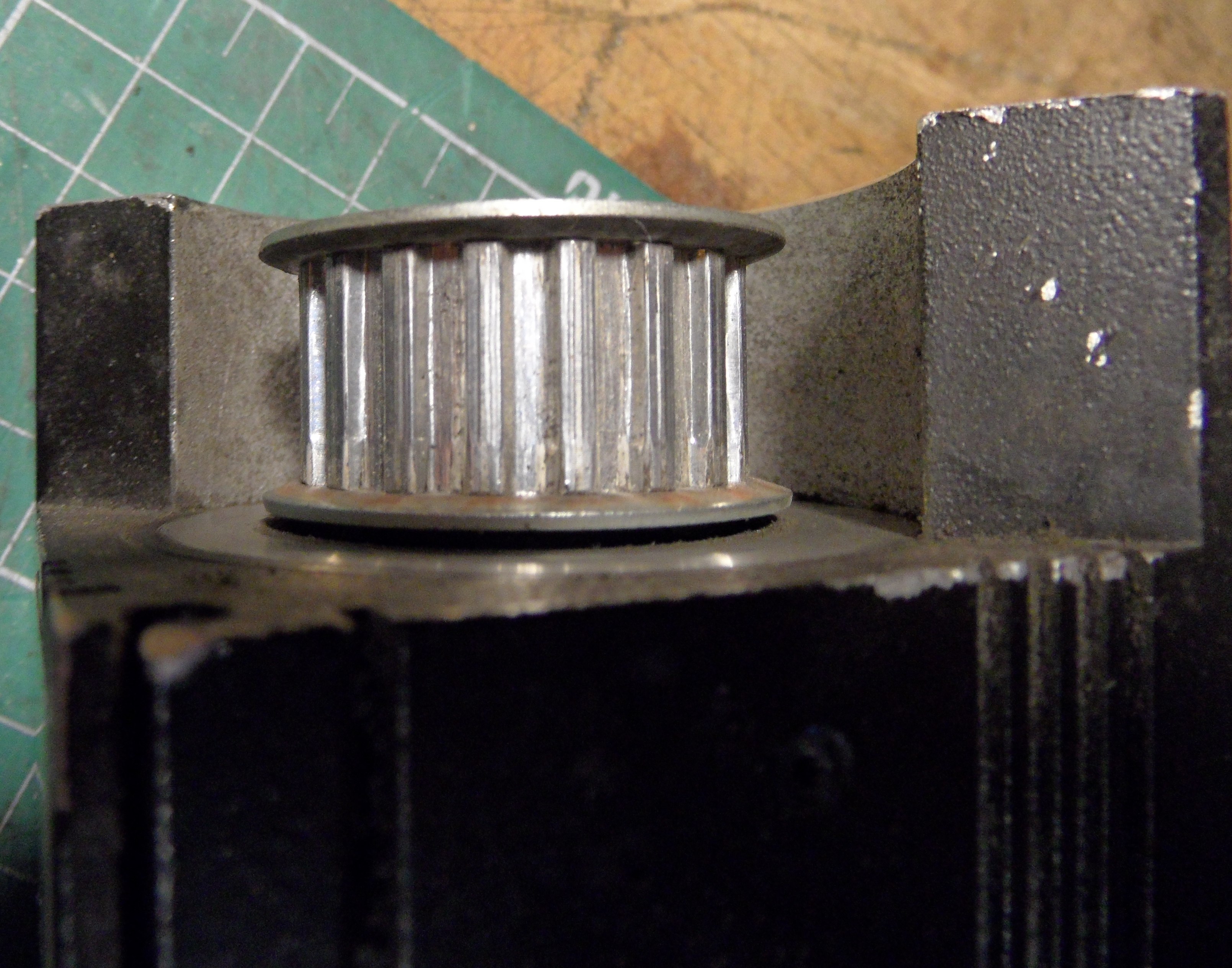
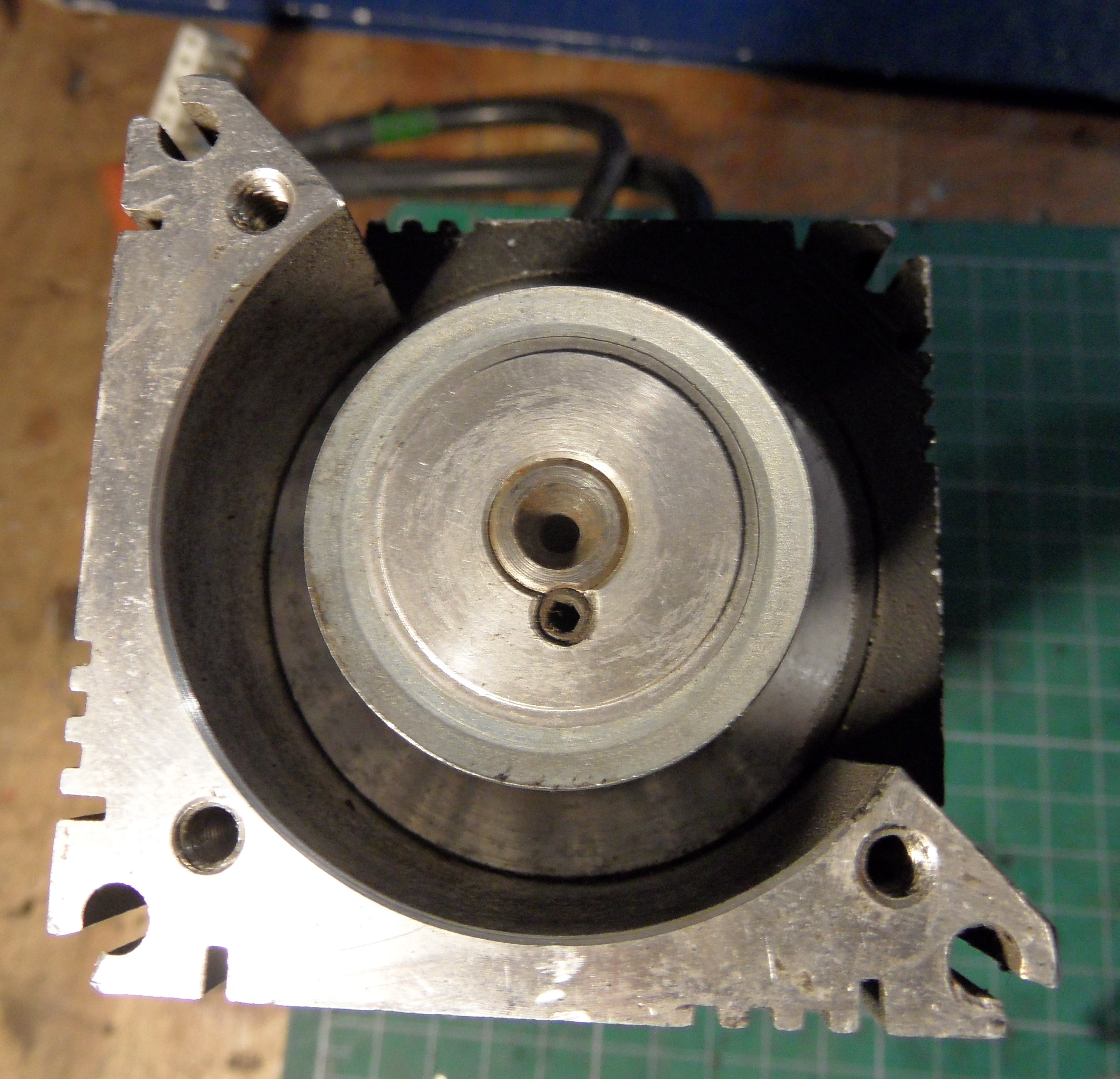
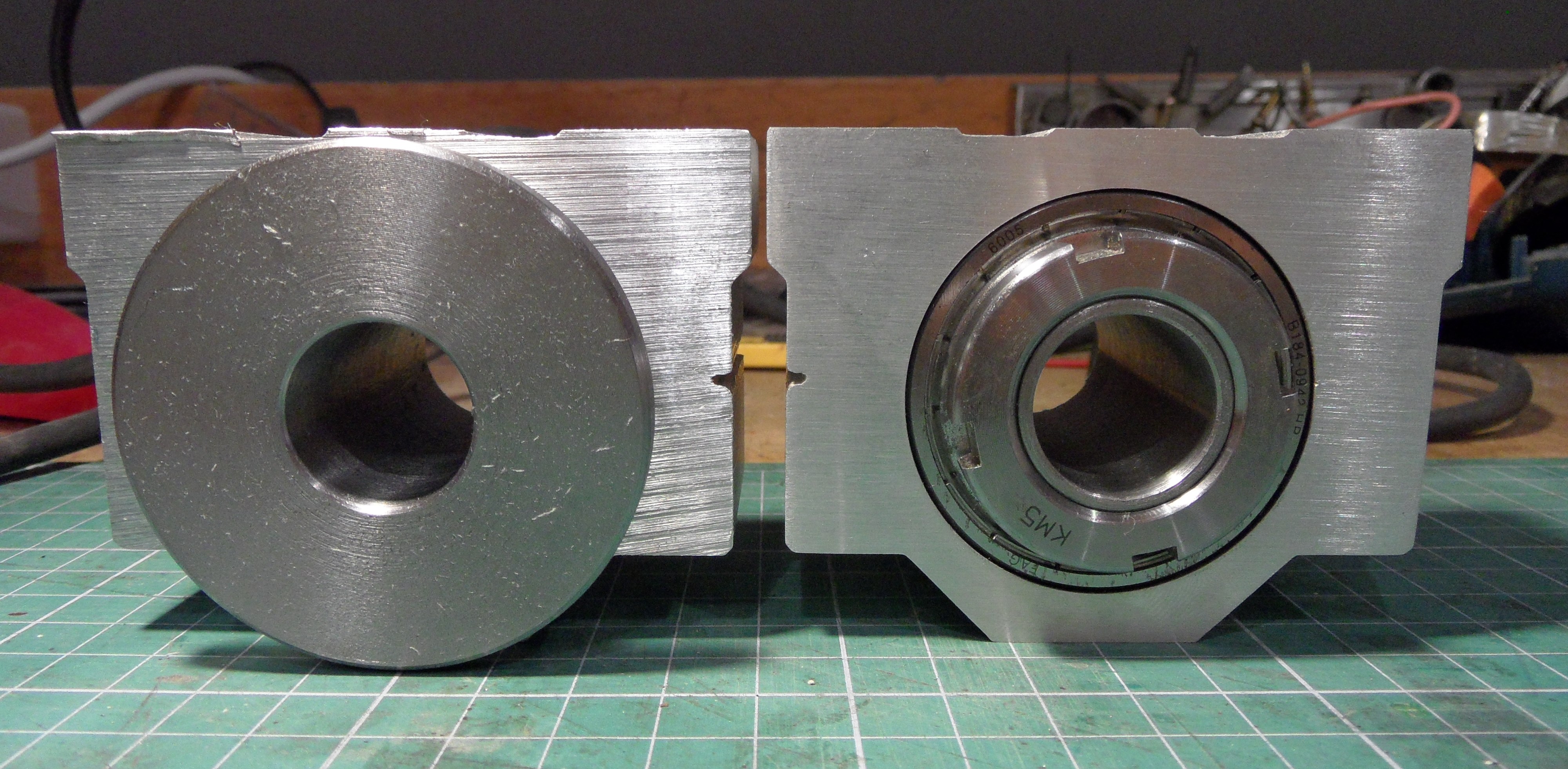
Koło jest aluminiowe, może się zniszczyć przy zdejmowaniu bo i tak wygląda na zużyte.
Może jakimiś chemikaliami co aluminium niszczą a stal nie?
Myślałem że odkręcę robaczka i śrubokrętem podważę od tyłu i je wsunę, ale strasznie ciężko siedzi.
Nie mam kompletnie pomysłu jak się za to zabrać żeby nie uszkodzić wału silnika.
Co do postępów z pracami, to mam już wytoczone tulejki do nakrętek obrotowych, muszę w nich wykonać otwory do zamocowania do nakrętki kulowej, nagwintować oraz zrobić płytkę która będzie od zewnątrz powstrzymywała łożyska od wypadnięcia. Zdecydowałem się użyć do przeniesienia napędu paski HTD 3M o szerokości 15mm za radą techników od sponsora, polecam.
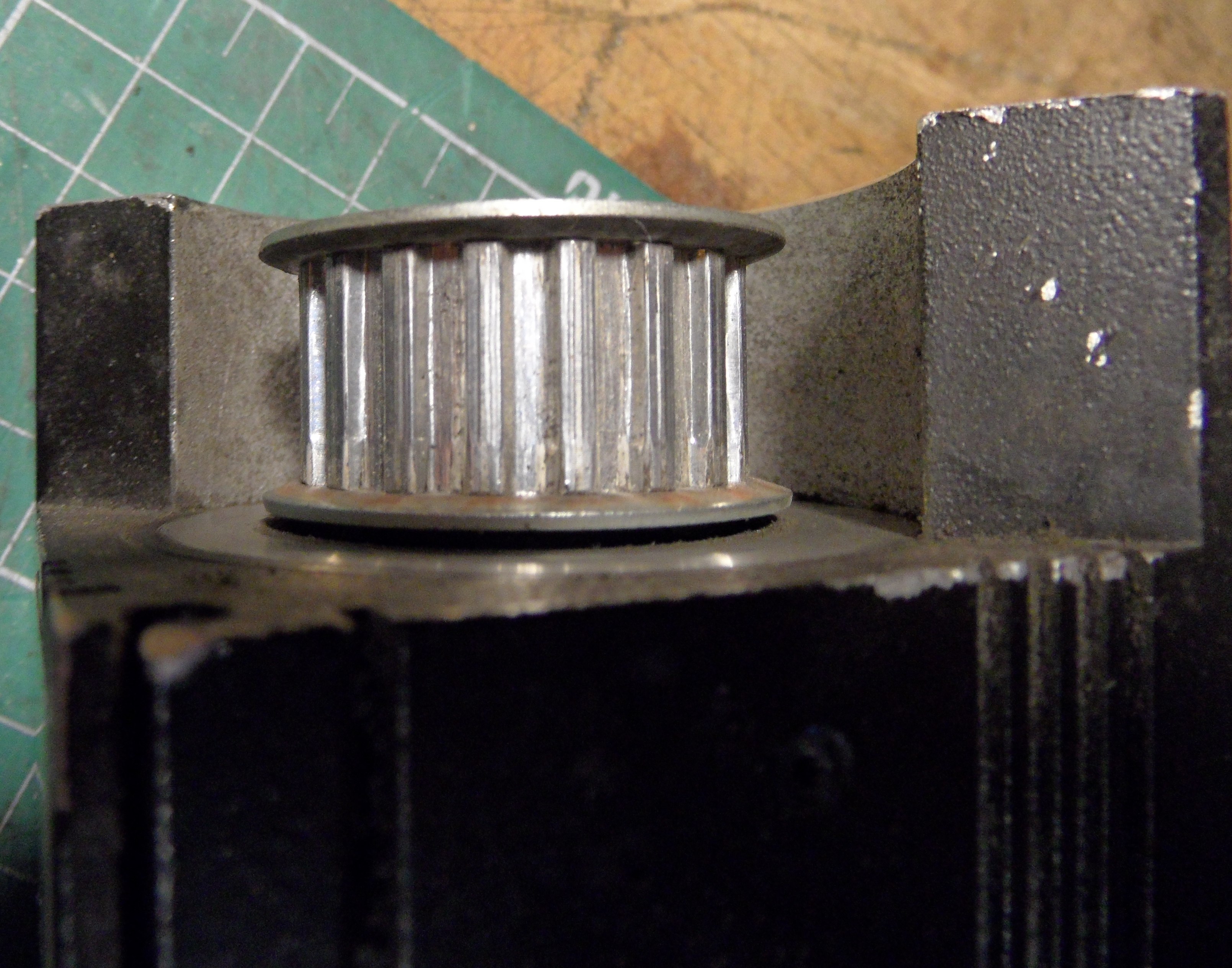
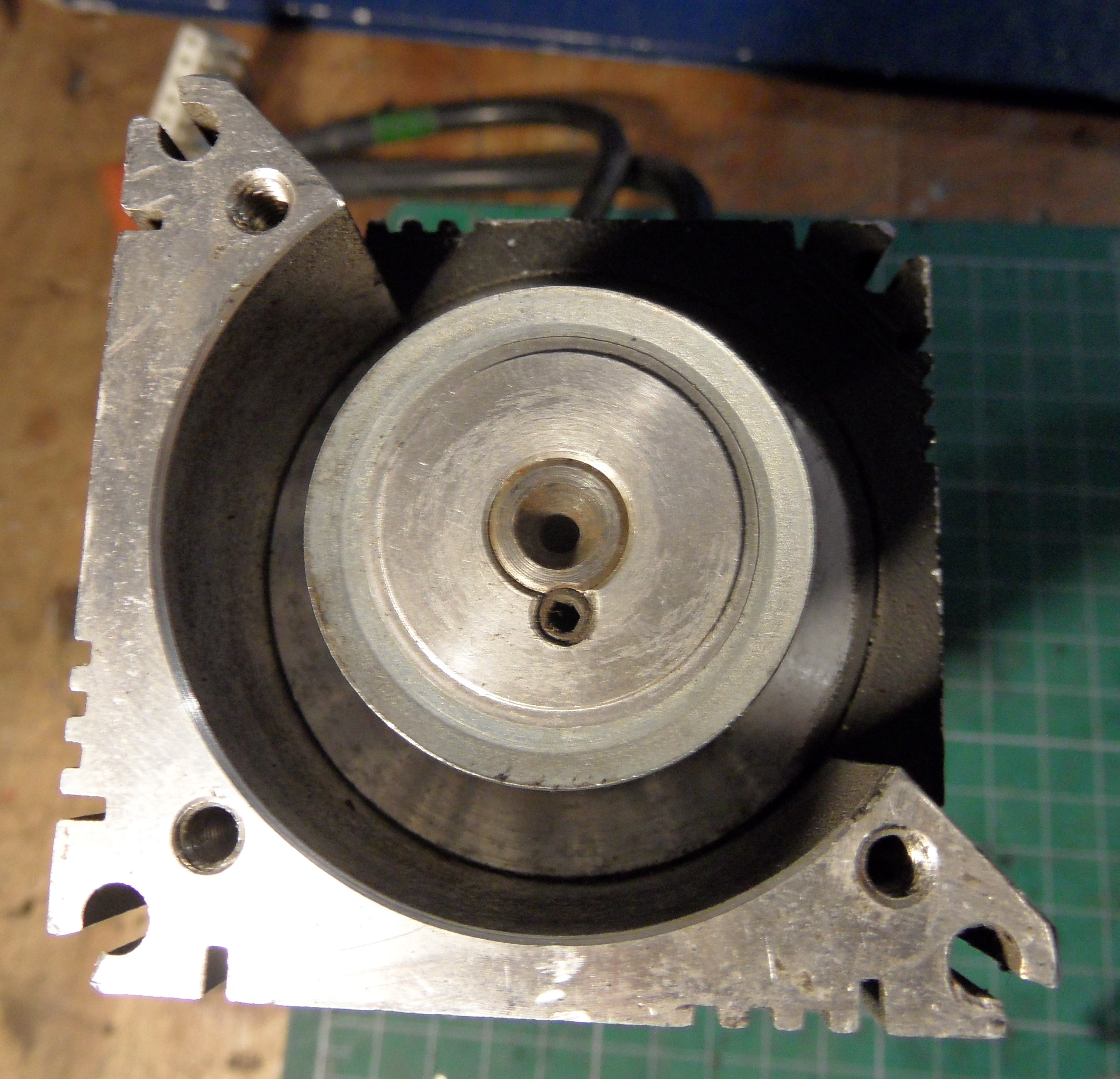
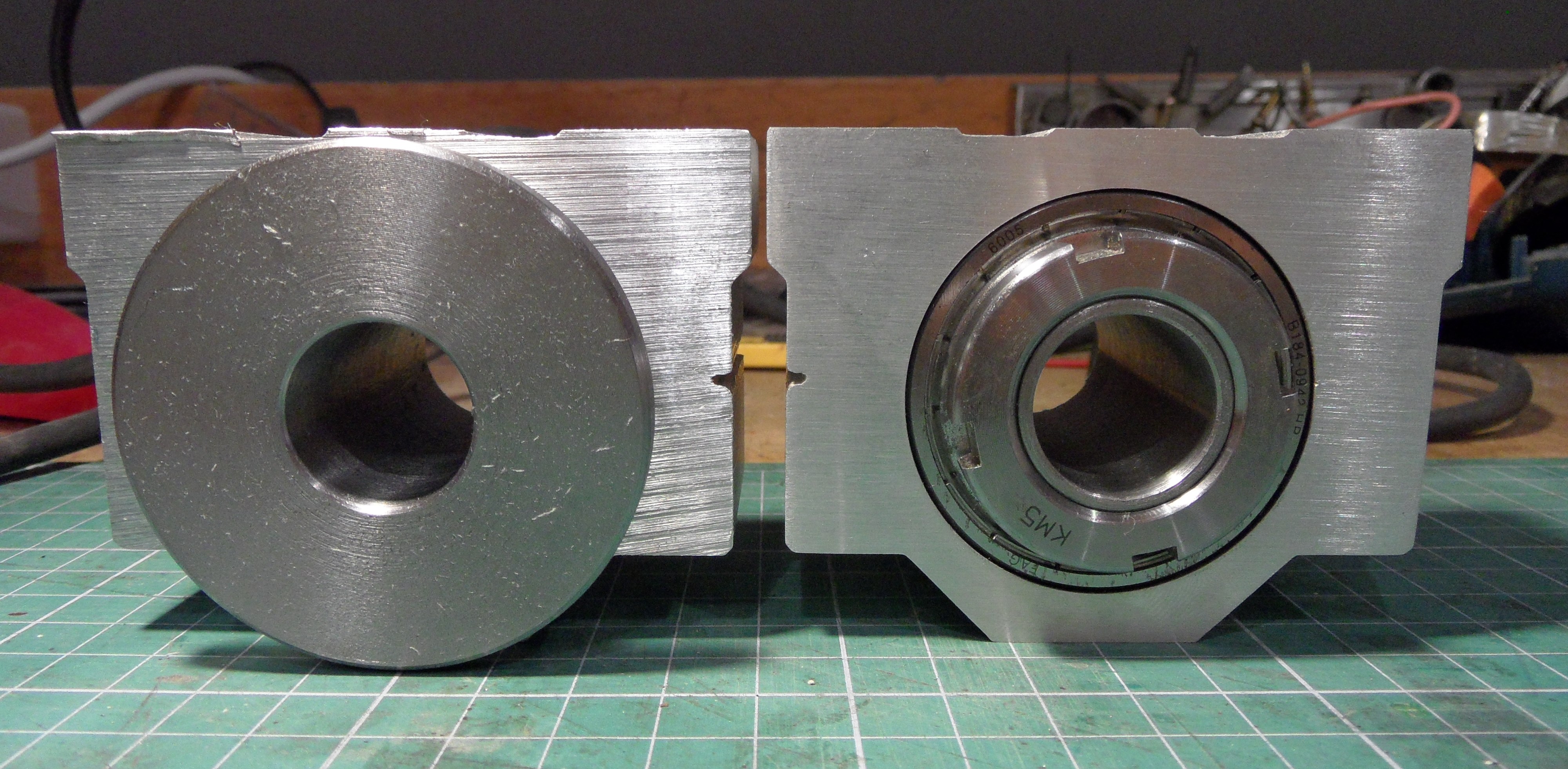