Konkretnie płytkę z wątku laczenie-wejsc-roznych-typow-t119417.html
Postanowiłem zrobić to też ładnie, czyli dać złącza XH i otwory montażowe.
Najpierw KiCAD.
Obrys płytki zrobiłem w LibreCAD. Nie to żeby w KiCAD się nie dało, ale w LibreCAD robię coś często, a w KiCAD od wielkiego dzwonu, więc po prostu było mi łatwiej.
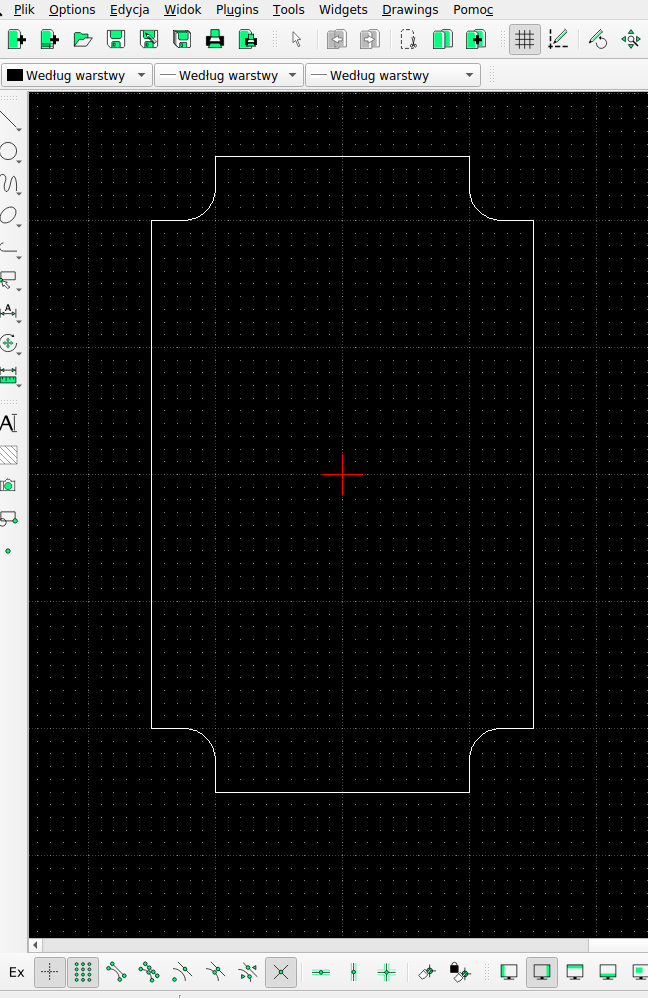
Przy imporcie dxf do KiCAD linia zamienia się w ścieżkę, ale można ustawić sobie jej grubość, ja dałem 1 mm, bo tak mi się podobało...
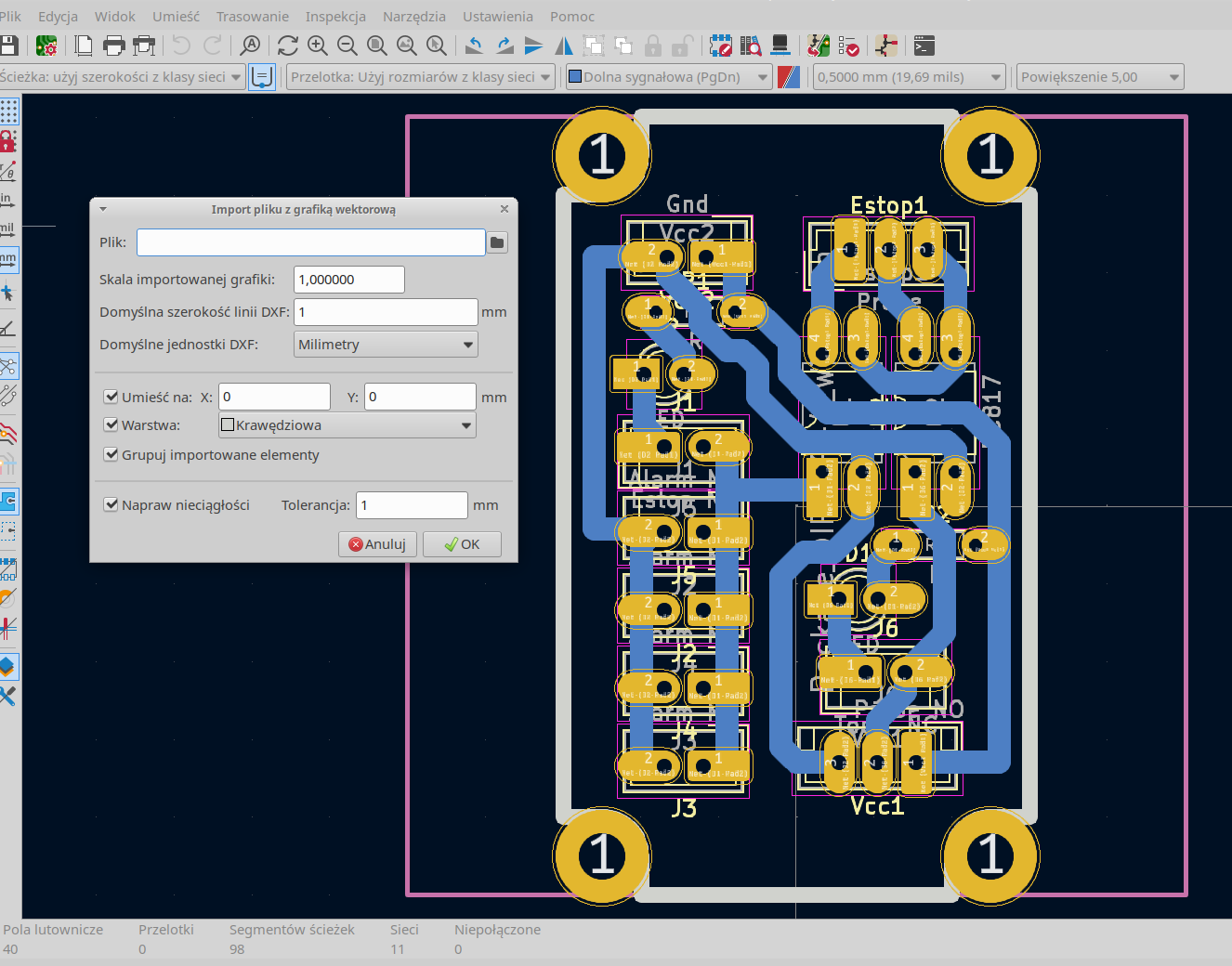
Na uwagę zasługują jeszcze otwory montażowe, do których zrobiłem sobie własną bibliotekę. I znowu nie to żeby KiCAD nie miał "mounting hole", bo ma, ale szlag mnie trafia kiedy muszę tego używać. Po prostu jest tam naćkane napisów, które do niczego mi nie są potrzebne, za to dość skutecznie utrudniają pracę. Także czasem warto sobie wyedytować najczęściej używane symbole i wypieprzyć ten nadmiar dobra...
O eksporcie gerberów i ich obróbce we FlatCAM pisać nie będę, bo tam wszystko robi się standardowo, zgodnie z instrukcją obsługi, tylko trzeba pamiętać o odbiciu płytki w lustrze i ustawieniu parametrów wiercenia, szczególnie głębokości i bezpiecznej wysokości.
Po zaimportowaniu g-kodu do EzCAD nie usuwałem ramki, tylko dodałem nową, co jest wyjątkowo proste - rysujemy gdziekolwiek prostokąt i w jego oknie właściwości wpisujemy wymiary i położenie 0,0. Teraz po zaznaczeniu wszystkiego robimy Hatch, który tym razem powinien zadziałać prawidłowo.
Obrazków tym razem wklejać nie będę, bo nie zrobiłem zrzutów ekranu, ale to naprawdę żadna strata.
Teraz kwestia sprzętu.
Przyszło mi do głowy, że we frezarce do PCB (CNC1310) mam stolik zrobiony z V-slota 2080, mam też 100 mm takiego profila kupionego przy okazji innego projektu, żeby dobić do darmowej wysyłki na Allegro. Tak więc pomyślałem, że dorobię z tego profila stolik do znakowarki i na obu maszynach będę tak samo montował płytki i ich oprzyrządowanie.
Z kolei przypomniałem sobie o aluminiowych profilach do ramek, których kiedyś używałem i wydały mi się idealne do zastosowania w tym projekcie. Idealne to może przesada, bo zasłaniają po 5 mm brzegu płytki, ale umożliwiają powtarzalne i pewne zamocowanie płytki.
Kupiłem profil A6Z i potrzebne do niego blaszki tutaj: https://www.ramyaluminiowe.pl/oferta/
Byłem tam osobiście i niestety nie wiem czy wyślą pocztą/kurierem, ale zawsze można zadzwonić i zapytać.
Ewentualnie można kupić podobną gotową ramkę na Allegro i ją pociąć, ale to zły pomysł, bo trzeba będzie sobie dorobić te sprężyste blaszki odpowiedzialne za zmykanie profila. (Tych co będą raczej nie da się wyjąć tak żeby ich użyć ponownie, a poza tym będzie ich potrzeba więcej, na laserze dałem po dwie, ale na frezarce po cztery.). Górne elementy są celowo dłuższe, żeby łatwiej było otwierać.
Tak to wygląda:
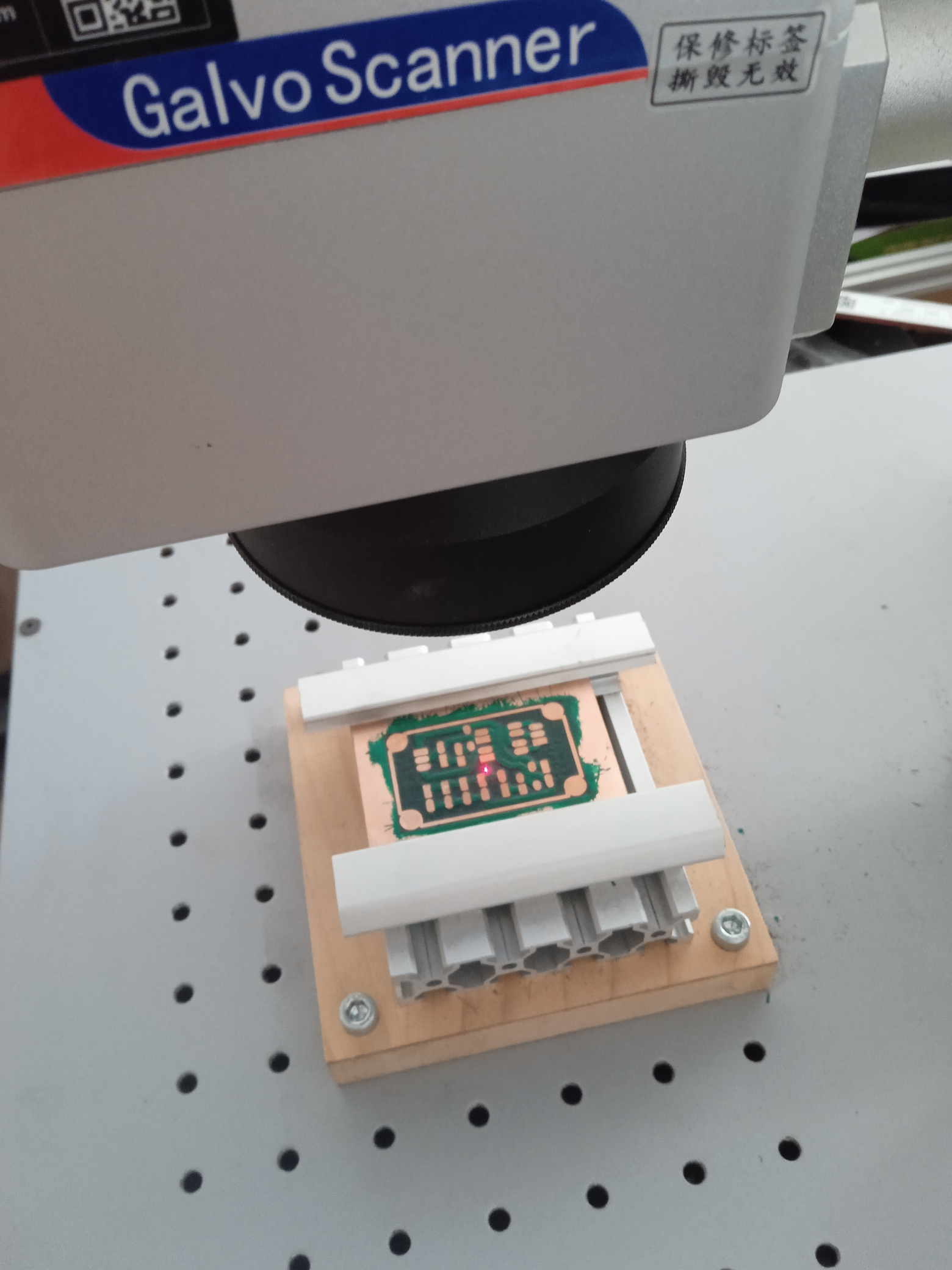
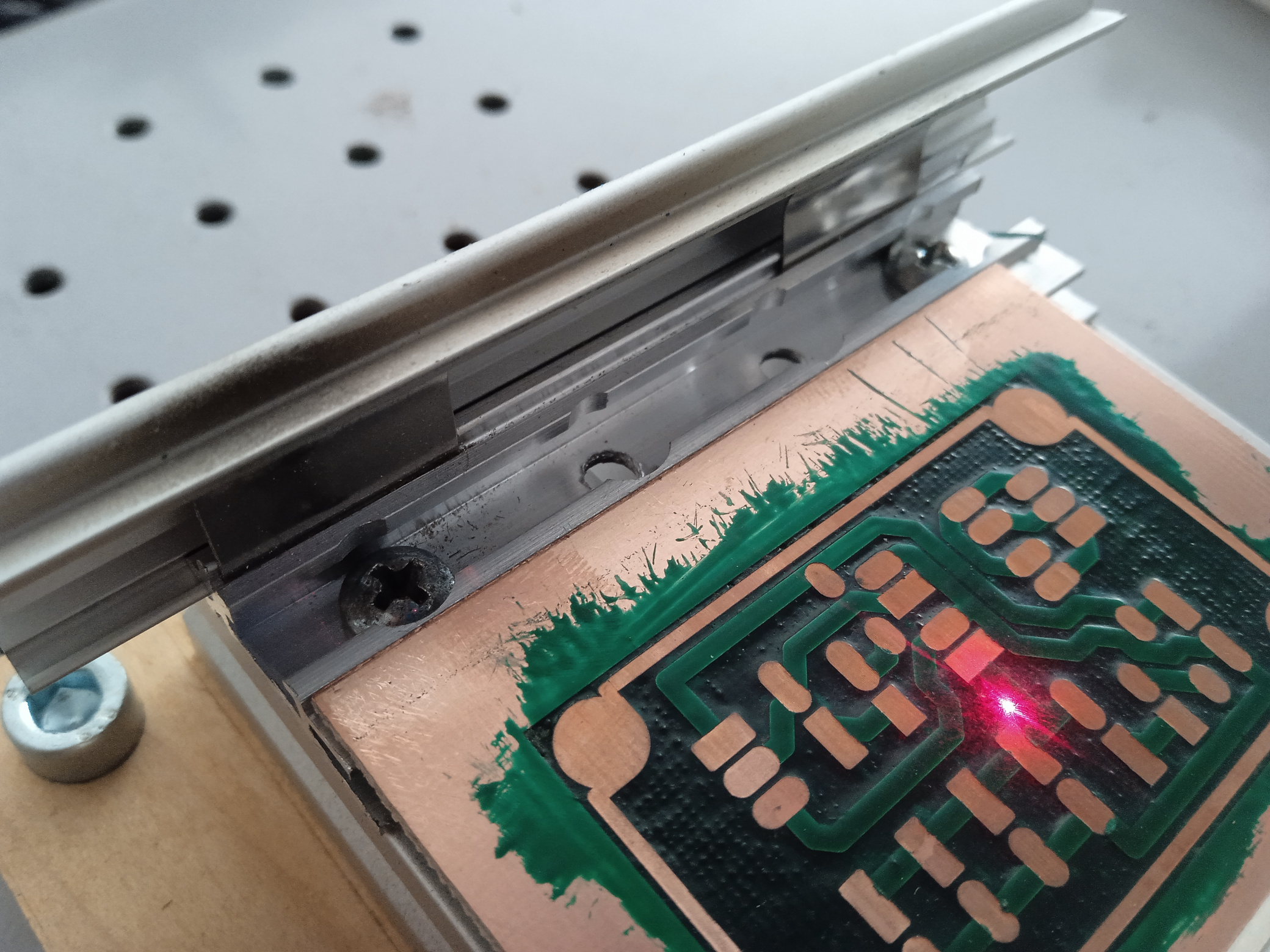
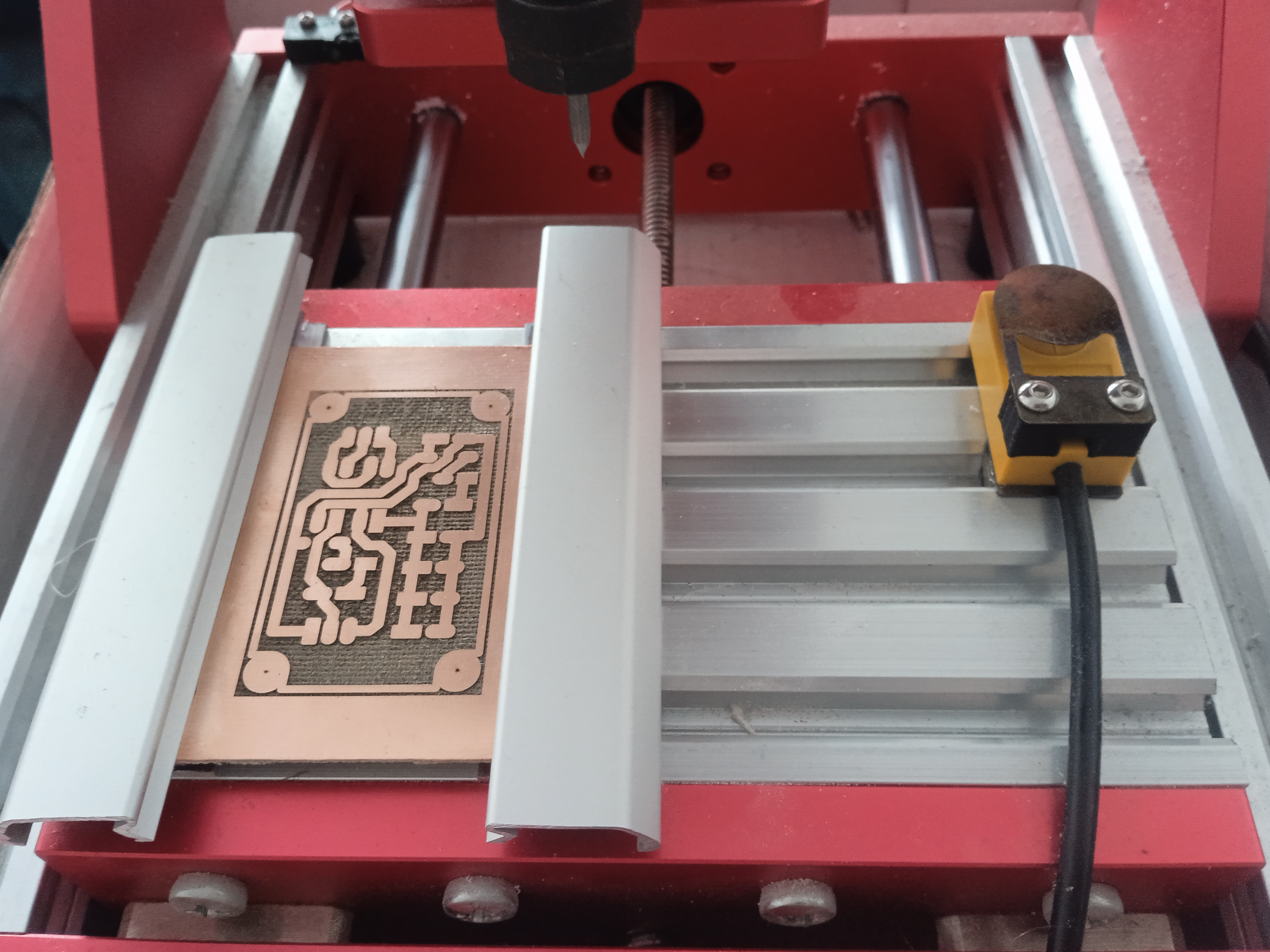
Tutaj mały offtopic.
To co widać po prawej stronie stołu frezarki, to czujnik wysokości narzędzia, wykonany z taniego chińskiego czujnika indukcyjnego, wydruku 3d (to czarne) i sprężystej stalowej blaszki 0,3mm, wyciętej na znakowarce fiber.
Tutaj nawet nie chodziło o to, żeby to kosztowało 5 PLN, ile o to, że żaden fabryczny czujnik tam się nie zmieści.
W każdym razie działa bez zarzutu, współpracując z klasycznym kontrolerem GRBL na Atmega 328P. W tej maszynie taki kontroler jest w zupełności wystarczający i nie mam motywacji wymieniać go na nic nowocześniejszego.
GRBL nie obsługuje kodu M6, ale używany przeze mnie bCNC może ten kod przechwytywać i wykonywać wymianę narzędzia z jego pomiarem. Działa to dokładnie tak, jak powinno i tutaj nie będę pisał na ten temat więcej.
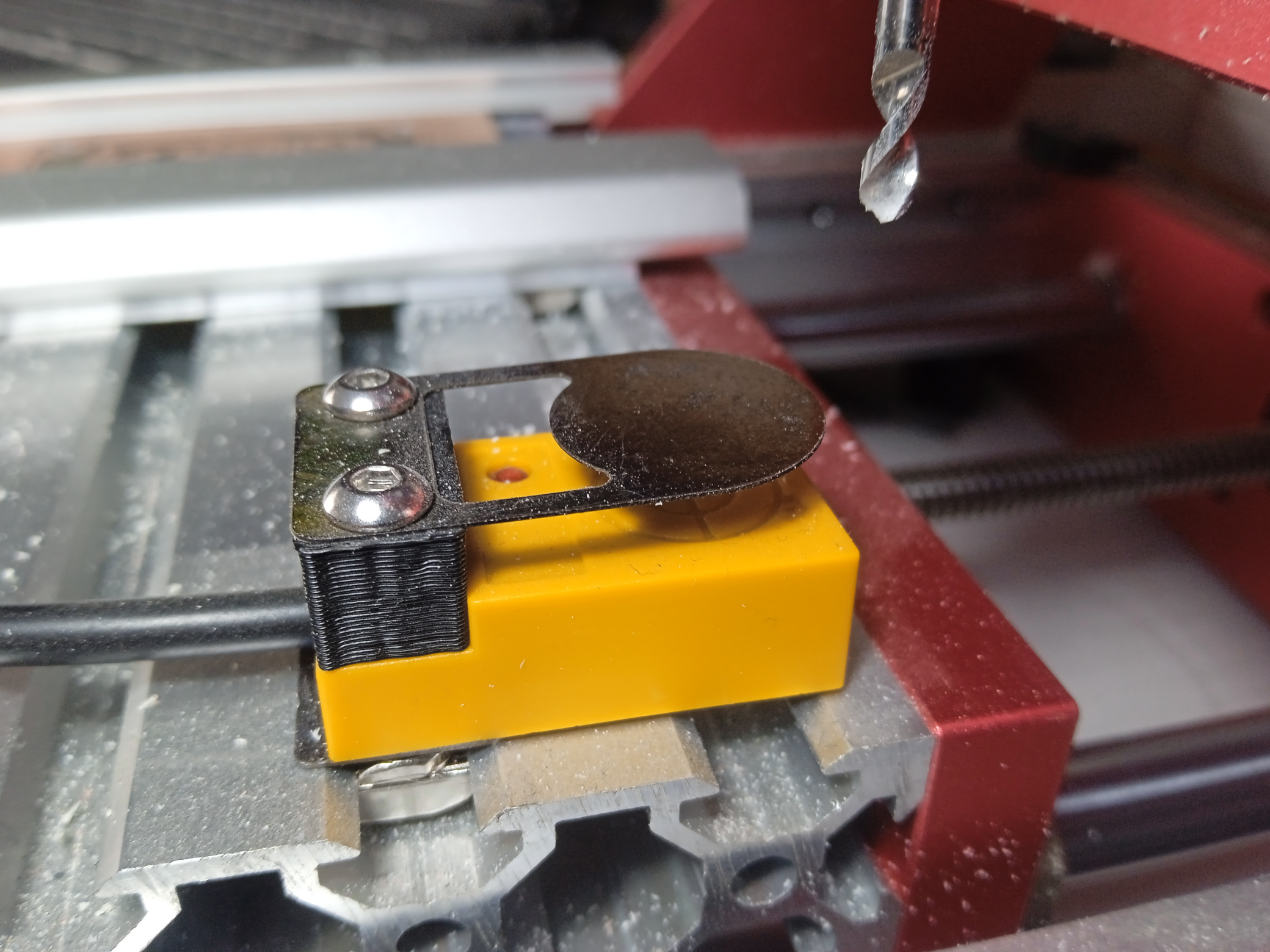
Wracamy do wykonania PCB.
Postanowiłem wykonać dwie płytki, jedną z soldermaską, a drugą bez.
Wcześniej zmarnowałem kilka płytek na dobranie parametrów lasera. Szczegółów opisywać nie będę, bo to zależy od mocy lasera, użytej soczewki i konkretnej płytki (lepiej zakupić większą ilość i jechać na tym samym towarze), ale tak ogólnie, to nie należy się śpieszyć. Da się płytkę wypalić bardzo szybko, ale wypalić jest tu właściwym określeniem, bo będzie przypalony plastik, a ścieżki będą odchodzić od płytki. Lepiej jest dobrać mniej agresywne parametry i poświęcić więcej czasu. Ale w drugą stronę też nie należy przesadzać, bo to przecież lśniący metal i słaby promień będzie odbijać. Pierwsze próby na zbyt małej mocy dawały taki efekt, że fragmenty płytki były nieruszone, ale tam gdzie laserowi udało się miedź zmatowić, to już się wypalała za każdym kolejnym przejściem...
Warto jeszcze zauważyć, że łatwo poznać co laser pali. Miedź barwi płomień na zielono-niebiesko, a węgiel na czerwono, więc po kolorze wiadomo, czy miedź została już przebita, czy jeszcze nie...
A jak skwierczy i dymi, to znaczy że pali plastik a ekspozycja jest stanowczo zbyt duża i trzeba zejść z mocy albo podnieść prędkość.
Z PCB, kiedy już znalazłem dobre parametry nie było większych problemów, za to z soldermaską już tak. Nie wiem, może jakąś tandetną kupiłem, a może taka właśnie powinna być, ale miejscami odklejała mi się od miedzi i wstawała (tylko tam gdzie była palona, obok nie). Efekt był taki, że miejscami miedź była już odsłonięta, a miejscami pod "dachem", którego laser nie chciał palić, bo najwyraźniej było to powyżej fokusa... No nie to żeby uniemożliwiało to wykonanie płytki, ale trzeba było pomóc laserowi mechanicznie...
Potem przyszedł czas na wiercenie.
Tą płytkę bez soldermaski ustawiłem dokładnie i wyszło całkiem dobrze, ale tą z soldermaską na szybko i otwory się przesunęły względem ścieżek (lewy dolny róg jest na swoim miejscu, ale płytka się względem niego obróciła). Na szczęście przesunięcie zmieściło się w dopuszczalnej tolerancji i płytka się nadaje do użycia. W każdym razie to był mój błąd. a nie problemy z technologią...
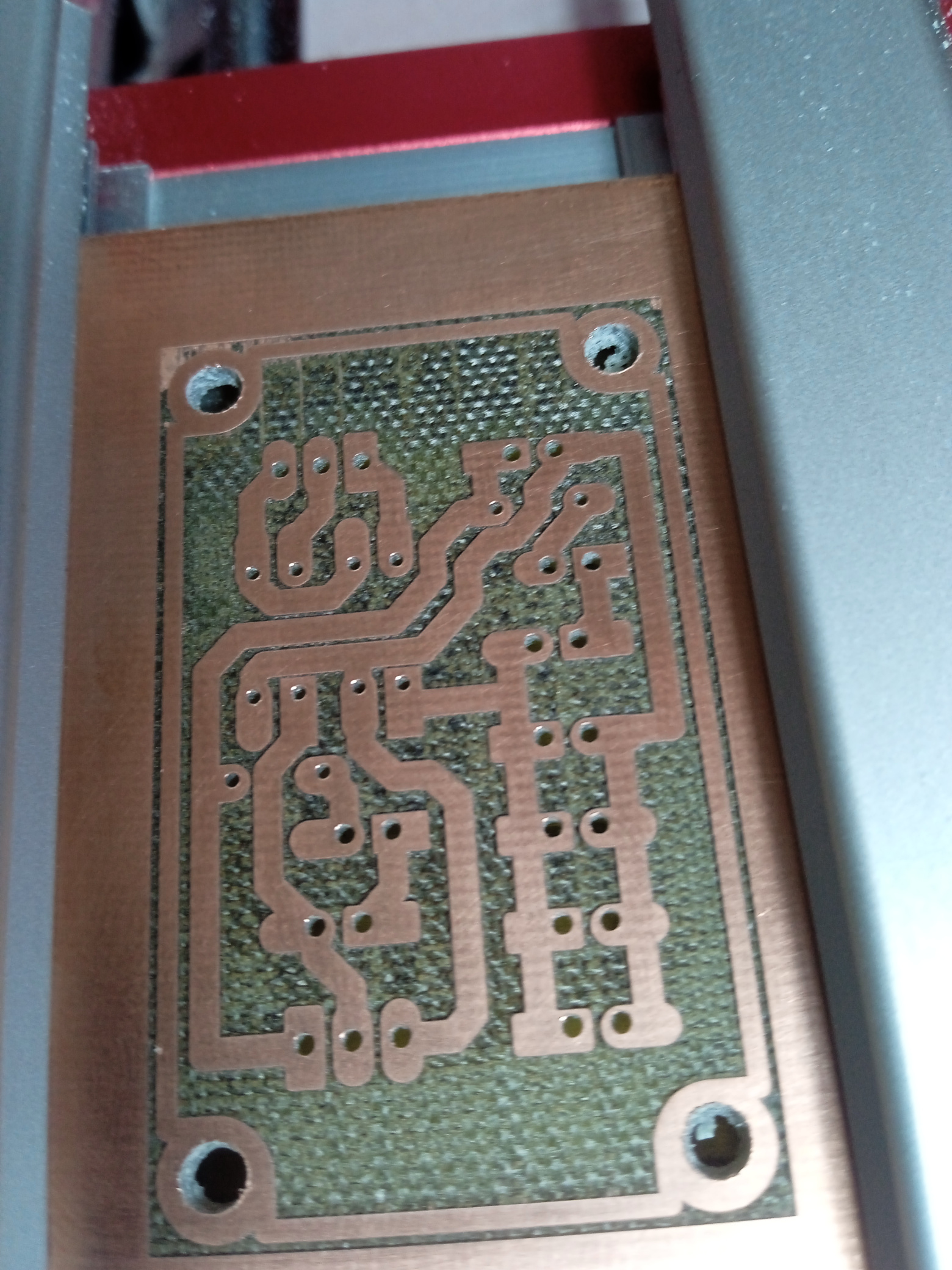
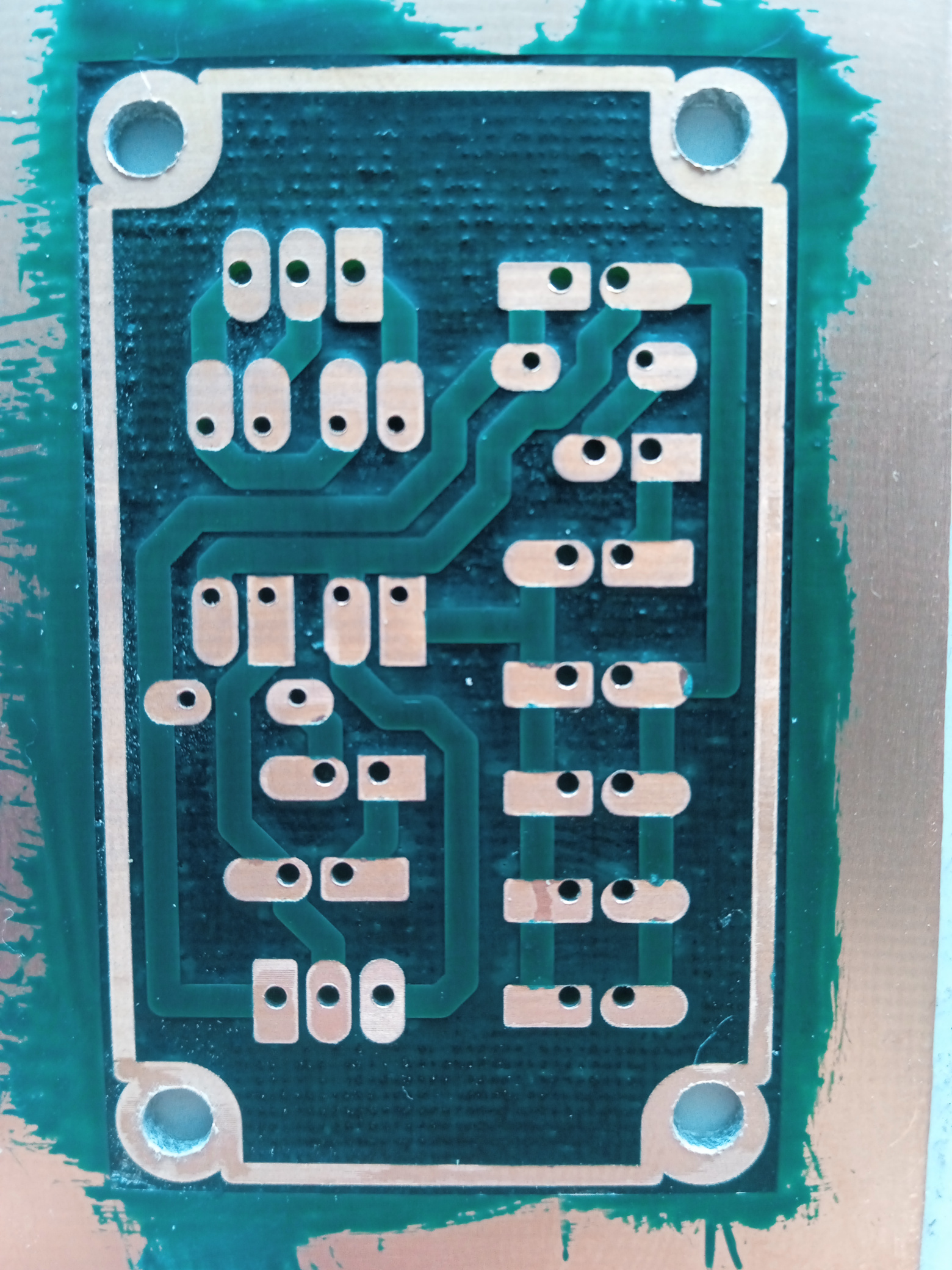