W pewnym sensie tak. Teoretycznie powinien się pod działaniem sił skrawania i docisku na środku wyboczyć na zewnątrz, wtedy miałby kształt beczki a nie klepsydry, ale mógł być to także wynik niejednorodności twardości materiału(lub obu z dociskiem konikiem na raz). Jeśli twardość pręta z jakiegoś powodu na środku była minimalnie mniejsza, to mniejsze opory toczenia, a konkretnie składowa prostopadła do osi toczenia Fo mniej odpychała nóż, przez co skrawał głębiej.Metodą dedukcji doszedłem do tego że za hardo docisnąłem konika.
Czy moja teoria jest słuszna?
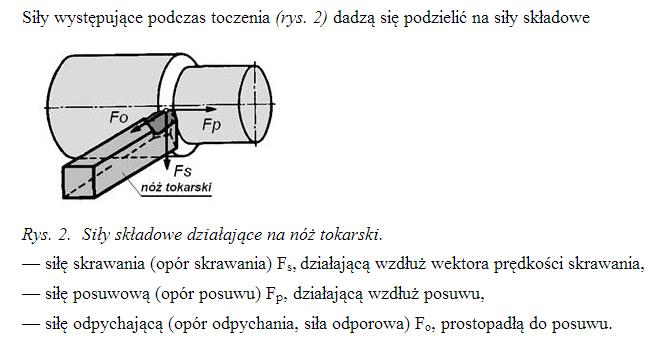
Większa twardość na końcach może też wynikać z tytułu cięcia pręta przecinarką z tarczą ścierną, tak rozgrzany do czerwoności materiał potrafi się miejscowo lekko utwardzić(choć nie zawsze tak jest).
Również zużycie maszyny czy powstanie narostu na nożu(ale po jego urwaniu się powstaje zazwyczaj minimalny zauważalny stopień) może w pewnych granicach wpływać na to co otrzymamy.
Ale dokładne zdiagnozowanie zjawiska bez adekwatnych badań, pomiarów jest tylko mniej lub bardziej trafną teorią...
Dodane 2 godziny 7 minuty 59 sekundy:
Dużo, ale nie zawsze to wina nakrętki, czy luzu jej zamocowania w korpusie. Czy jesteś pewien, że śruba nie ma luzu na łożyskowaniu (b na rys) w swoim gnieździe w korpusie lub oporze (ana rys.) ? Tzn. może się bezproduktywnie "wkręcać" w nakrętkę w ramach tego luzu, zanim opór w oprawie ją zatrzyma, i pociągnie nakrętkę z sankami.nagwintowaniem trochę polepszyla sytuację jednak nadal mam luz. Luz sięgający pełnego obrotu korby zanim sanki zareaguja.
Nie znam się ale według mnie to bardzo dużo.
Jeśli w TSA160 jest tak samo jak w TSA16 ,to śruba 116 przy odsuwaniu od operatora sanek poprzecznych zapiera się o korpus 100 kryzą w miejscu a, a jeśli przysuwamy do operatora to w miejscu b (139), i jeśli zbyt duży luz pozwala na ruchy śruby (niebieska strzałka) to poprawianie nakrętki 110 niewiele da.
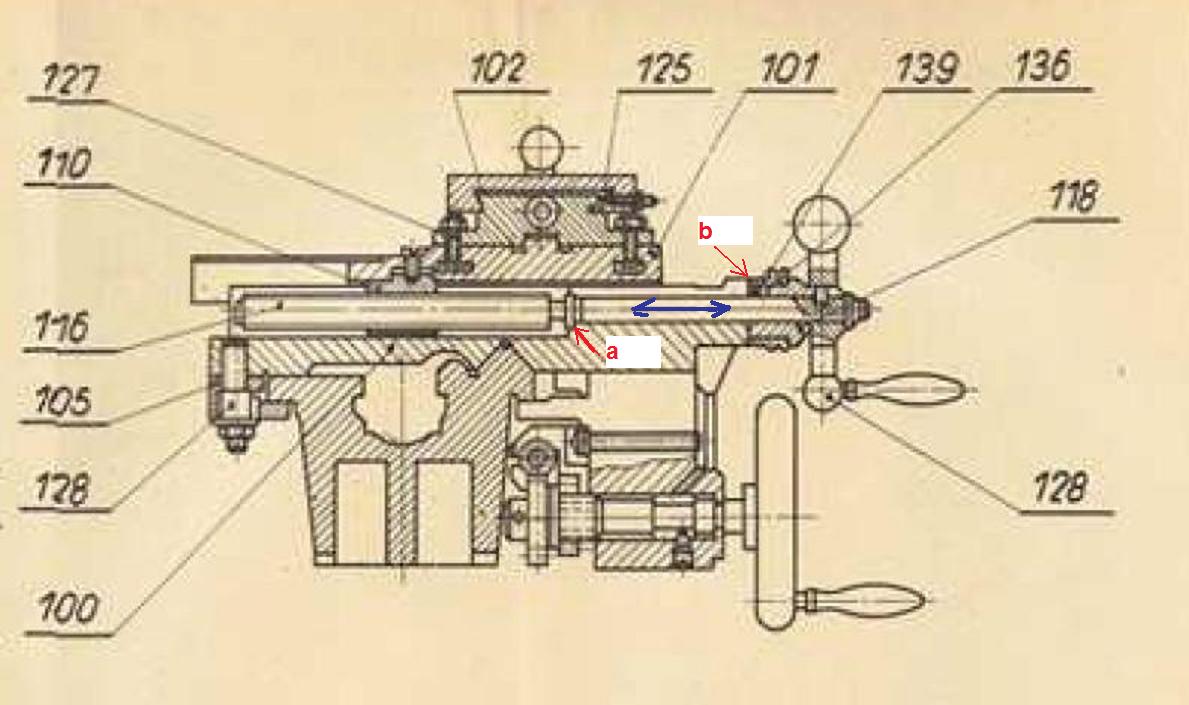
Zanim zabierzesz się za przeróbkę nakrętki Upewnij się czy tak nie jest, bo Twoja praca może okazać się niepotrzebna.
Jeśli możesz to unikaj takiego rozwiązania, bo gwint śruby/nakretki z czasem pod wpływem sił skrawania, drgań, udarów nabierze luzu i sytuacja się powtórzy. Po to jest ten występ by do tego nie doszło.Z racji że polutowac mosiądzu nie mam jak a i sam lut nie wiadomo czy wytrzyma to wymyśliłem pewne obejście.
Otóż chcę ten kawałek trzpienia stoczyć na równo.
Następnie ze śruby która pasuje bez luzu w otwór stoczyć i zagwintowac koniec aby pasował w sanki.
Moim zdaniem tym sposobem wyeliminuje luz nakrętki względem suportu.
Mam rację?
To już lepiej zamiast staczać czy lutować nałóż klej(np epoksydowy do metalu, nawet poxipol, czy inny gotowy lub epoksyd wymieszany z proszkiem brązu) i obrób po jego stwardnieniu. Pamiętaj by przed obróbką kleju sprawdzić i ewentualnie poprawić kształt gniazda w korpusie(może być uszkodzone, pozbijane, itp) w które wchodzi potem nakrętka, by potem po obróbce idealnie pasowały.
Będzie to lepsze rozwiązanie, bardziej trwałe, a w razie czego powtarzalne.
cdn...
Dodane 36 minuty 2 sekundy:
Chłodzenie zawsze się przyda, jakie by nie było.Z racji że nie chciałem wiercic i gwintowac jak i nie było za bardzo gdzie, to całość trzyma się na 4 magnesach neodymowych.
Minusem jest to że zbiera wszelki szmelc.
Choć gdy tak na to popatrzyłem to zastanawiam się nad zamontowaniem dużego magnesu przy wrzecionie aby zabierał wióry.
A dobrze Ci radzę zrezygnuj z magnesów, bo jak namagnesuje się od nich łoże czy uchwyt (jaK planujesz zastosować magnes koło niego) to stalowe mikroopiłki po obróbce czy ścieraniu trzymane szczątkowym polem magnetycznym do powierzchni ślizgowych łoża/suportu, powierzchni współpracujących ze sobą w uchwycie, nie mówiąc o tym że uchwyt będzie trzymał mniejsze wióry z np wytaczania zamiast je wyrzucać na zewnątrz, czy nawet "przylepione" do wrzeciona w łożyskowaniu, będą z czasem rysować i psuć te powierzchnie.
Lepiej w dłuższej perspektywie magnesy trzymać z dala od maszyny.