mikrowrzeciono
-
- Lider FORUM (min. 2000)
- Posty w temacie: 24
- Posty: 2788
- Rejestracja: 15 sty 2006, 18:34
- Lokalizacja: Wrocław
To nawet nie takie dziwne skoro mówisz o 12 woltach. W końcu zasiliłeś go napięciem o ponad 60% wyższym od znamionowego(według listy którą zamieściłeś 7.2V). Proporcjonalnie wzrósł prąd a moc ponad 2.5 raza Na zdjęciu skrzynki prostownika nie zauważyłem kondensatora za mostkiem. Daj jakiś kondensator przynajmniej kilkaset mikrofaradów, włącz silnik, pokręć gałą sterującą PWM mierząc przy tym napięcie na wyjściu i wszystko się wyjaśni.
-
- ELITA FORUM (min. 1000)
- Posty w temacie: 7
- Posty: 1744
- Rejestracja: 03 sty 2007, 14:27
- Lokalizacja: Wiedeń
Ja da kondensator za mostkiem na silnik pójdzie większe napiecie. W tej chwili ma sinusoide o napieciu skutecznym 12V, po dodaniu kondensatora będzie miał napięcie stałe bliskie napięciu szczytowemu sinusoidy, coś koło 16diodas1 pisze:To nawet nie takie dziwne skoro mówisz o 12 woltach. W końcu zasiliłeś go napięciem o ponad 60% wyższym od znamionowego(według listy którą zamieściłeś 7.2V). Proporcjonalnie wzrósł prąd a moc ponad 2.5 raza Na zdjęciu skrzynki prostownika nie zauważyłem kondensatora za mostkiem. Daj jakiś kondensator przynajmniej kilkaset mikrofaradów, włącz silnik, pokręć gałą sterującą PWM mierząc przy tym napięcie na wyjściu i wszystko się wyjaśni.

To że moc wzrośnie 2.5 raza to też nie do końca prawda, silnik DC to nie rezystor, po przełożeniu większego napięcia obroty będą wzrastać aż napięcie samoindukcji zrównoważy przyrost napięcia zasilania. Przy odrobinie pecha silnik zostanie mechanicznie uszkodzony (w moim rozerwało komutator) zanim spalą sie uzwojenia.
Nie rozumiem tylko w czym problem skoro w obwodzie jest układ pwm? 16V nie przebije izolacji uzwojeń a regulator pwm ograniczy moc.
-
- Specjalista poziom 1 (min. 100)
- Posty w temacie: 3
- Posty: 168
- Rejestracja: 12 kwie 2013, 19:03
- Lokalizacja: Świdnica
faktycznie - kondensator być musi !
nawet w tysiącach µF
potem zmierz napięcie na kondensatorze (bez obciążenia),
jest to ważna informacja bo tym napięciem zasilasz silnik.
Jeśli silnik może pracować na 12V
i jeśli na kondensatorze będzie 12V to stabilizator na NE555 nie może być większy niż 9V
a nawet te 9V może okazać się za duże jeśli pod obciążeniem
napięcie będzie mocno siadać.
nawet w tysiącach µF
potem zmierz napięcie na kondensatorze (bez obciążenia),
jest to ważna informacja bo tym napięciem zasilasz silnik.
Jeśli silnik może pracować na 12V
i jeśli na kondensatorze będzie 12V to stabilizator na NE555 nie może być większy niż 9V
a nawet te 9V może okazać się za duże jeśli pod obciążeniem
napięcie będzie mocno siadać.
-
- Specjalista poziom 3 (min. 600)
- Posty w temacie: 1
- Posty: 843
- Rejestracja: 02 gru 2013, 19:21
- Lokalizacja: Częstochowa
Weź stabilizator 7809, do tego jakiś większy tranzystor + rezystor i masz stabilizator z max prądem zależącym tylko od zastosowanego tranzystora (czyli możesz go rozbudować do ilu A chcesz). Koniecznie kondensator za mostkiem! Przy 13.5A prądu pobieranego przez silnik przydałoby się dać chociaż 6800µF.
Schemat mogę jutro naszkicować, jakby był potrzebny
Schemat mogę jutro naszkicować, jakby był potrzebny

-
Autor tematu - Lider FORUM (min. 2000)
- Posty w temacie: 44
- Posty: 2558
- Rejestracja: 04 paź 2007, 01:32
- Lokalizacja: Kraków
- Kontakt:
kondensatorek jest na płytce ale taki ze 450 mikro stricte do wygładzania pulsacji. na silniku nie pisze na ile wolt nominalnie, kupowałem nijako na 12 ale chyba jednak nie jest 
generalnie z układu jestem zadowolony, wszystko gra i buczy i nic się nie grzeje poza silnikiem.
muszę wypróbować ten drugi (fuji micro fm-43e) ale pod niego potrzebne mi inne kołnierze mocujące i trzpień silnik -prostnica na inna średnice osi (4mm). no i przede wszystkim czas żeby za to siąść.

generalnie z układu jestem zadowolony, wszystko gra i buczy i nic się nie grzeje poza silnikiem.
muszę wypróbować ten drugi (fuji micro fm-43e) ale pod niego potrzebne mi inne kołnierze mocujące i trzpień silnik -prostnica na inna średnice osi (4mm). no i przede wszystkim czas żeby za to siąść.
Nie otrzymasz koni wyścigowych krzyżując dwa osły
-
- Sympatyk forum poziom 2 (min. 50)
- Posty w temacie: 3
- Posty: 60
- Rejestracja: 21 gru 2010, 16:46
- Lokalizacja: Winnica
Aby nie rozpoczynać nowego, to podepnę się do tematu, bowiem moim "głównym hobby" jest modelarstwo, a "maszynka CNC" ma być dodatkiem ułatwiającym te działania
Frezowanie w sklejce, laminacie, a jak da radę to i aluminium...
Prosił bym o opinie o takim rozwiązaniu na tanie wrzeciono (silniki, regulatory i.t.p. posiadam z racji uprawianego hobby).
Silnik BLDC "w okolicach" 1500/2000W na przykład taki: NTM Prop Drive 50-50 580KV / 2000W wymienić w nim wał na Collet Chuck Holder 8mm Shank Dia. Straight Extension Rod C8 ER11A 100L Milling i zrobić z tego "wrzeciono" podobne do tego:
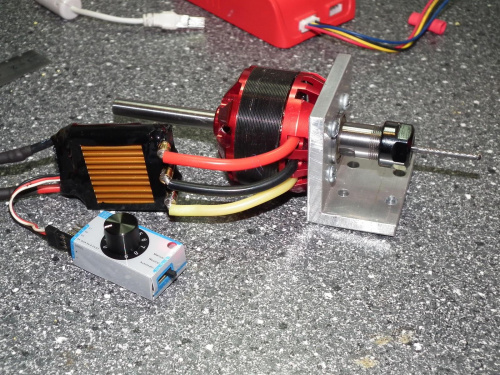

Prosił bym o opinie o takim rozwiązaniu na tanie wrzeciono (silniki, regulatory i.t.p. posiadam z racji uprawianego hobby).
Silnik BLDC "w okolicach" 1500/2000W na przykład taki: NTM Prop Drive 50-50 580KV / 2000W wymienić w nim wał na Collet Chuck Holder 8mm Shank Dia. Straight Extension Rod C8 ER11A 100L Milling i zrobić z tego "wrzeciono" podobne do tego:
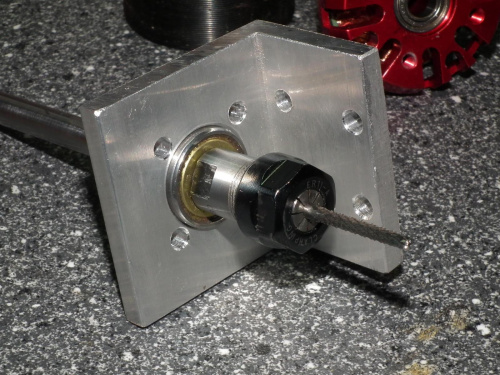
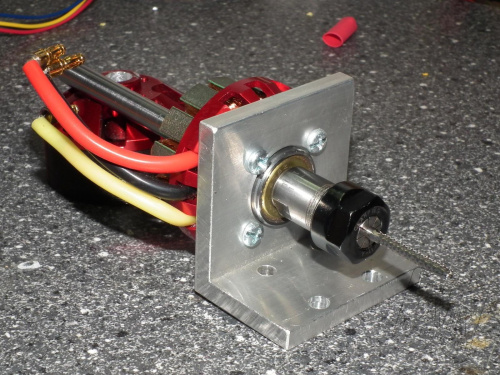
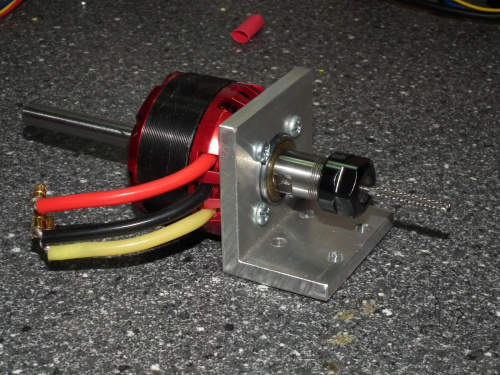
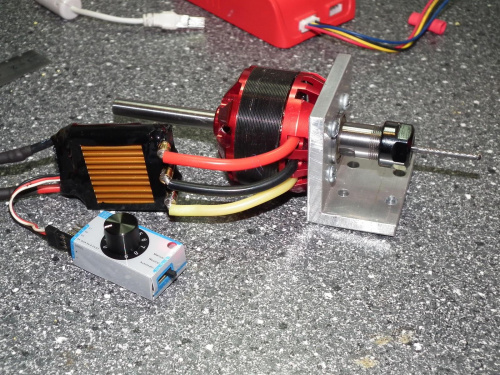
Pozdrawiam, Artur
-
- Lider FORUM (min. 2000)
- Posty w temacie: 3
- Posty: 11969
- Rejestracja: 17 mar 2009, 08:55
- Lokalizacja: Skępe
Witam kolegę, sama konstrukcja pod względem mechanicznym dość poprawna, choć można by się pokusić o:
- mniej prądożerny silnik (ten max 90A, przy Kv=580) z większym Kv, by zastosować przekładnię (planetarną, pasek zębaty itd. nawet wielostopniową), co zmniejszyłoby apetyt na ampery do poziomu akceptowalnego dla zastosowania (sporego jeszcze) zasilacza sieciowego, ale nie redukowało momentu obrotowego (przypomnę, że przekładnia 1/2 RPM zwiększa Mo x 4). Bo ten konkretny układ musi zasilać wydajny pakiet LiPo, czy LiFe, który na długo nie starcza, zwłaszcza kiedy opory skrawania powodują pobór A w granicach maximum.
(trzeba by dokładnie wyliczyć teoretyczny moment dla tego silnika, i porównać z układem z przekładnią)
A w układzie bez przekładni (j.w.na zdjęciu):
- dodatkowy, większy wirnik wentylatora na wałku powyżej silnika(w tunelu z silnikiem podobnie do EDF) dla bardziej wydajnego chłodzenia, zwłaszcza przy zredukowanych obrotach,
- dodatkowe podparcie łożyskiem wałka na jego końcu (ponad silnikiem i wentylatorem), bo co dwa punkty to nie jeden - składowa boczna siły działającej na narzędzie nie będzie obciążać łożysk silnika.
Czyli całość napędu ładnie zamknęła by się w rurze (z otworkami na dole dla poboru powietrza..)
To takie moje wariacje na temat..
- mniej prądożerny silnik (ten max 90A, przy Kv=580) z większym Kv, by zastosować przekładnię (planetarną, pasek zębaty itd. nawet wielostopniową), co zmniejszyłoby apetyt na ampery do poziomu akceptowalnego dla zastosowania (sporego jeszcze) zasilacza sieciowego, ale nie redukowało momentu obrotowego (przypomnę, że przekładnia 1/2 RPM zwiększa Mo x 4). Bo ten konkretny układ musi zasilać wydajny pakiet LiPo, czy LiFe, który na długo nie starcza, zwłaszcza kiedy opory skrawania powodują pobór A w granicach maximum.
(trzeba by dokładnie wyliczyć teoretyczny moment dla tego silnika, i porównać z układem z przekładnią)
A w układzie bez przekładni (j.w.na zdjęciu):
- dodatkowy, większy wirnik wentylatora na wałku powyżej silnika(w tunelu z silnikiem podobnie do EDF) dla bardziej wydajnego chłodzenia, zwłaszcza przy zredukowanych obrotach,
- dodatkowe podparcie łożyskiem wałka na jego końcu (ponad silnikiem i wentylatorem), bo co dwa punkty to nie jeden - składowa boczna siły działającej na narzędzie nie będzie obciążać łożysk silnika.
Czyli całość napędu ładnie zamknęła by się w rurze (z otworkami na dole dla poboru powietrza..)
To takie moje wariacje na temat..
pozdrawiam,
Roman
Roman
-
- Sympatyk forum poziom 2 (min. 50)
- Posty w temacie: 3
- Posty: 60
- Rejestracja: 21 gru 2010, 16:46
- Lokalizacja: Winnica
W tej konstrukcji jest zastosowane dodatkowe łożysko:
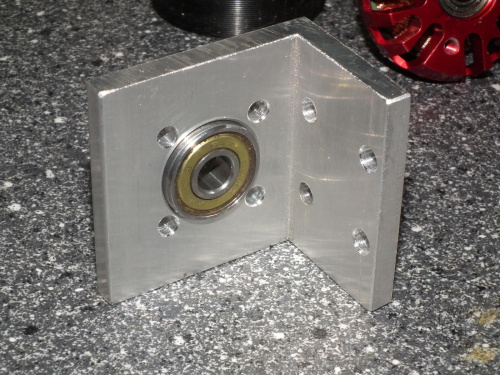
Co do przekładni, to właśnie tego chciałem uniknąć z racji ograniczenia wielkości "wrzeciona". Ma to być do małej, biurkowej frezarki o polu roboczym 200x300mm. Zasilenie linkowanego wcześniej silnika z napięcia 20V da mi na narzędziu 11600rpm (oczywiście w pełni regulowane), tylko pytanie jak z mocą
To znaczy na jakie materiały będę mógł sobie "pozwolić"...
Kolejna sprawa to chłodzenie. Wiem jak potrafią się grzać te silniki, bo kilkanaście ich posiadam i użytkuję w modelach RC
Pomysł z zabudowaniem go w rurę i wykorzystanie dłuższej osi do montażu wiatraczka jest jak najbardziej do zrealizowania. Tym bardziej, że ograniczy to przedostawanie się "opiłków wszelakich" do silnika 
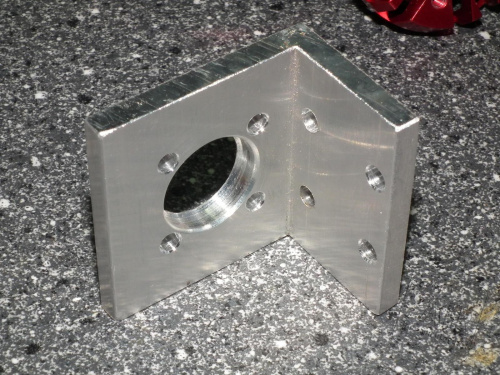
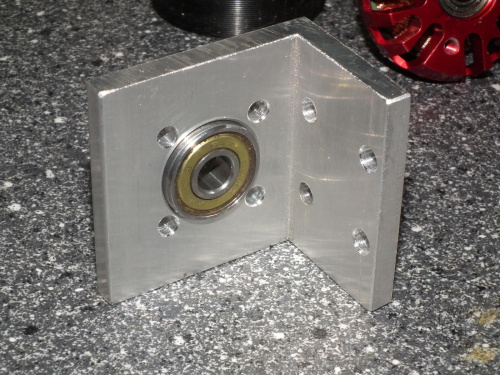
Co do przekładni, to właśnie tego chciałem uniknąć z racji ograniczenia wielkości "wrzeciona". Ma to być do małej, biurkowej frezarki o polu roboczym 200x300mm. Zasilenie linkowanego wcześniej silnika z napięcia 20V da mi na narzędziu 11600rpm (oczywiście w pełni regulowane), tylko pytanie jak z mocą

Kolejna sprawa to chłodzenie. Wiem jak potrafią się grzać te silniki, bo kilkanaście ich posiadam i użytkuję w modelach RC


Pozdrawiam, Artur