Witam. Należąca do mnie ZX7016 osiągnęła gotowość operacyjną.
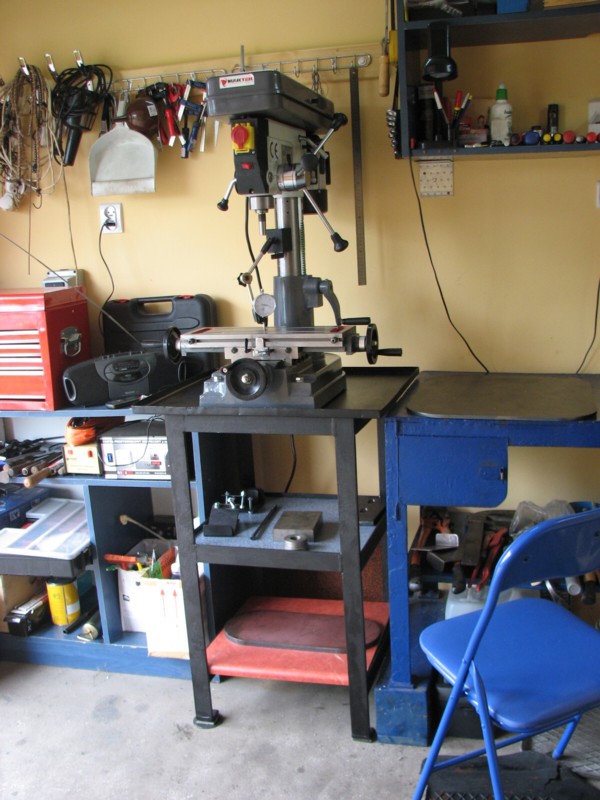
Ale po kolei.
Najpierw wykonałem podstawę - postument pod maszynę widoczną na foto.
Jest to konstrukcja spawana z kątowników 50x50x5 i płaskownika 50x10. Pod nóżkami zastosowałem gumy z przenośnika taśmowego o grubości 10mm. Całość wypoziomowana.
Jako blat zastosowałem blachę stalową o grubości 8mm (taką samą jak ta leżąca na warsztacie). Na blacie zamocowałem wannę (tacę) na wióry. Wykonałem ją z blachy 1,5mm, boki są zaginane i zespawane szczelnie. Półki pod spodem wykonane z płyty do blatów kuchennych o grubości 40mm. Masa podstawy:
-konstrukcja 35 kg
-blat z blachy 8mm 15 kg
-półki 8 kg
-balast w postaci owalnej blaszki widocznej na dolnej półce 10 kg
Razem masa podstawy 68 kg - to dobrze robi na stabilność i eliminację drgań.
W poprzednich postach napisałem, że stół krzyżowy mojej maszyny wymaga niestety poprawek, wykazały to pomiary po zmontowaniu. Stan fabrycznie wykonanych prowadnic był delikatnie mówiąc nie do przyjęcia... Zdecydowałem się na poprawki przy pomocy obróbki mechanicznej w pewnym dobrym zakładzie ślusarskim.
Pracę rozpoczęto od początku czyli od podstawy. Przyjmując za płaszczyznę bazową powierzchnię na której stoi obejma kolumny:
przy pomocy szlifierki magnesowej sprawdzono równoległość nóżek podstawy do tej powierzchni. Następnie biorąc jako powierzchnie bazowe te pewne teraz nóżki na frezarce pionowej przy pomocy odpowiednio dobranego, zeszlifowanego i podgiętego fly cuttera,
wykonano powierzchnię prowadnic na podstawie. Foto tych prowadnic przed obróbką:
i po obróbce:
Dalej prace objęły dolną część stolika. Fabrycznie oddane prowadnice tego elementu wyglądały tak, jakby ktoś po nieudanej obróbce dopracował je szlifierką kątową:
Na nich stolik jeździ po prowadnicach podstawy. Naprawa wyglądała w ten sposób, że jako powierzchnia bazowa posłużyły przeciwległe płaszczyzny, które były w niezłym stanie
i na szlifierce magnesowej doprowadzono płaszczyzny do porządku. Została tylko mała plamka, która była zbyt głęboka i nie było sensu brać tak głęboko:
Mając dopracowane te płaszczyzny sprawdzono kontrolnie te przeciwległe na magnesówce, ale nie było wiele do zbierania, nieco zabielono:
Kolejnym detalem podlegającym obróbce była górna część stołu. Na wstępie splanowano na szlifierce magnesowej powierzchnię roboczą stołu. Mając górę stołu idealnie sprawdzoną, potraktowano ją jako bazową i położono na stole frezarki do poprawek prowadnic jeżdżących w osi X. Ich powierzchnia nie była najtragiczniejsza, ale jej prostości nie byłem po pomiarach pewien:
Po przejechaniu ich na frezarce przy pomocy fly cuttera wyglądają tak i są z pewnością równoległe do płaszczyzny roboczej stolika:
Na tym zakończono obróbkę mechaniczną. Pisałem też wcześniej, że mój stolik pod koniec swojego ruchu po osi X w lewo ciężko idzie. Przyczyną okazały się niewielkie nierówności na prowadnicy bocznej górnego stolika, po której jeździ listwa kasująca luzy. Zlokalizowałem je po montażu i przejeździe przy pomocy farby z pisaka spirytusowego:
Aby zniwelować tę niedoskonałość zastosowałem dotarcie papierem ściernym 150 nałożonym na pilnik o kształcie nożowym (powierzchnię sąsiedniej prowadnicy zabezpieczyłem kilkoma warstwami taśmy izolacyjnej:
Lepiej może byłoby docierać elementem o element (prowadnicą dolnego stolika z papierem ściernym o górny, ale nie miałem już ochoty ponownie go rozbierać.
Nie muszę chyba dodawać, ale jednak napiszę, że efektem tych wszystkich prac jest dokładna praca stolika. Po wykasowaniu luzów w każdym miejscu i w każdej osi stół chodzi w setce, może nawet poniżej jednej setki. Oczywiście jak luzy są wykasowane, czyli śruby dość mocno skręcone, korbki chodzą ciężkawo, i nie da się ich kręcić jednym palcem
