Stalowa Betty
-
- ELITA FORUM (min. 1000)
- Posty w temacie: 12
- Posty: 1714
- Rejestracja: 13 sty 2006, 16:41
- Lokalizacja: Stargard
- Kontakt:
ale będzie sprzęcior. Świetnie się zapowiada.
https://www.instagram.com/cncworkshop.pl/
Obróbka CNC - frezowanie & toczenie
Obróbka CNC - frezowanie & toczenie
-
- Specjalista poziom 2 (min. 300)
- Posty w temacie: 4
- Posty: 309
- Rejestracja: 19 sty 2014, 18:56
- Lokalizacja: Elbląg
-
Autor tematu - ELITA FORUM (min. 1000)
- Posty w temacie: 38
- Posty: 1361
- Rejestracja: 18 sie 2010, 10:58
- Lokalizacja: Okolice Łodzi
Witamy ponownie
Długo nie miałem czasu na dłubanie przy maszynie bo zawsze coś ważniejszego wypadało.
Ale coś drgnęło. Przycisnąłem trochę i są postępy.
Tak więc pokazuję co się ostatnio działo.
Wykombinowałem sobie ładne prowadniki przewodów firmy Tsubaki (wykopałem ze śmieci w Extremtechu). Nie miały one zakończeń do montażu więc sobie je pomierzyłem i wyfrezowałem w aluminium. Pasują bardzo ładnie. Teraz będzie je można zamontować bez druciarstwa.
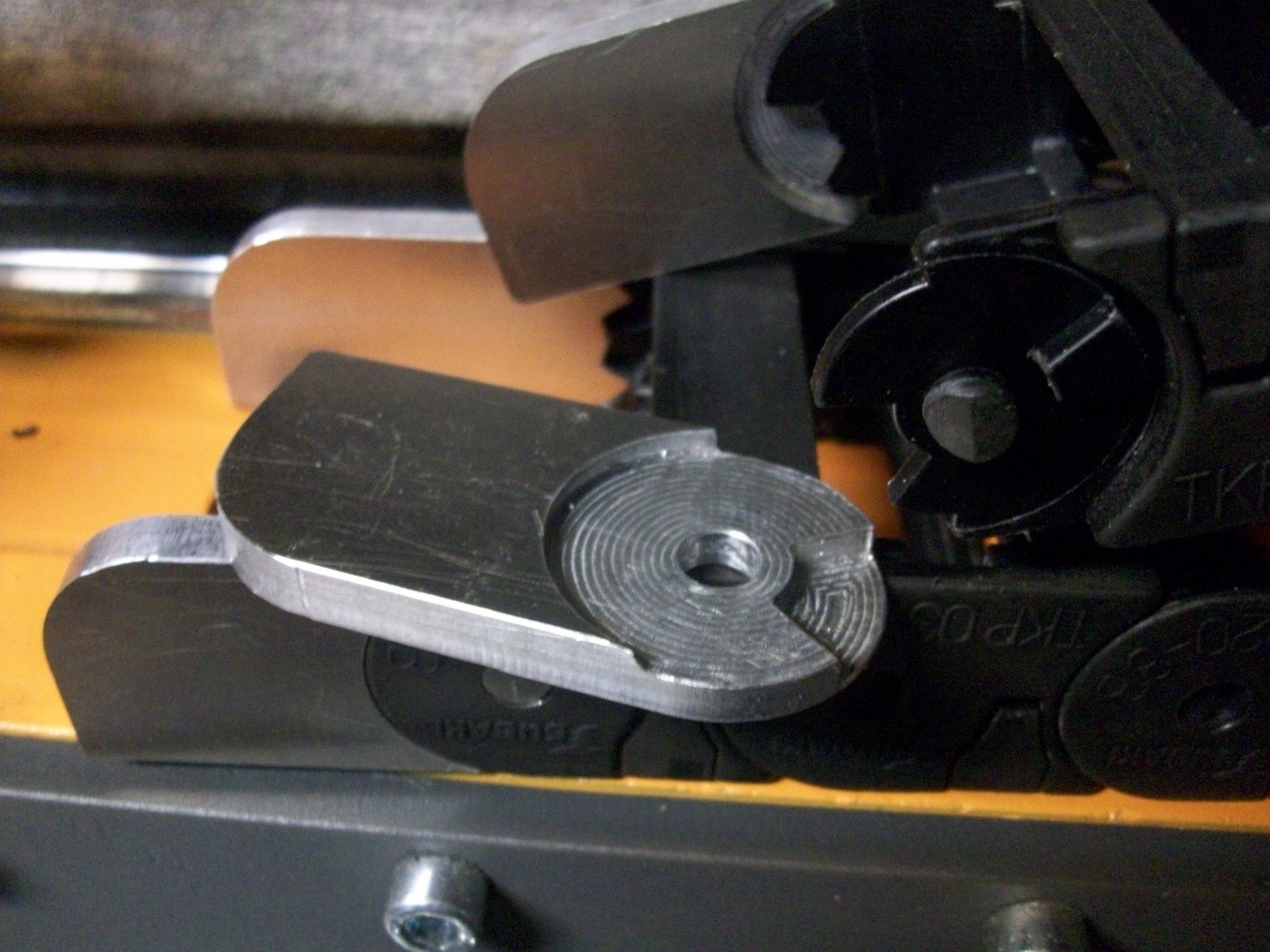
Zleciłem wypalenie 8-ki blachy na laserze abym mógł nią zamknąć ten żeliwny ceownik na bramie.
Blaszkę pomalowałem i przykręciłem. Pomalowałem tez krzyżak bo mi ktoś coś o rdzy wypominał ostatnio
. Teraz wygląda ładnie i nie rdzewieje.

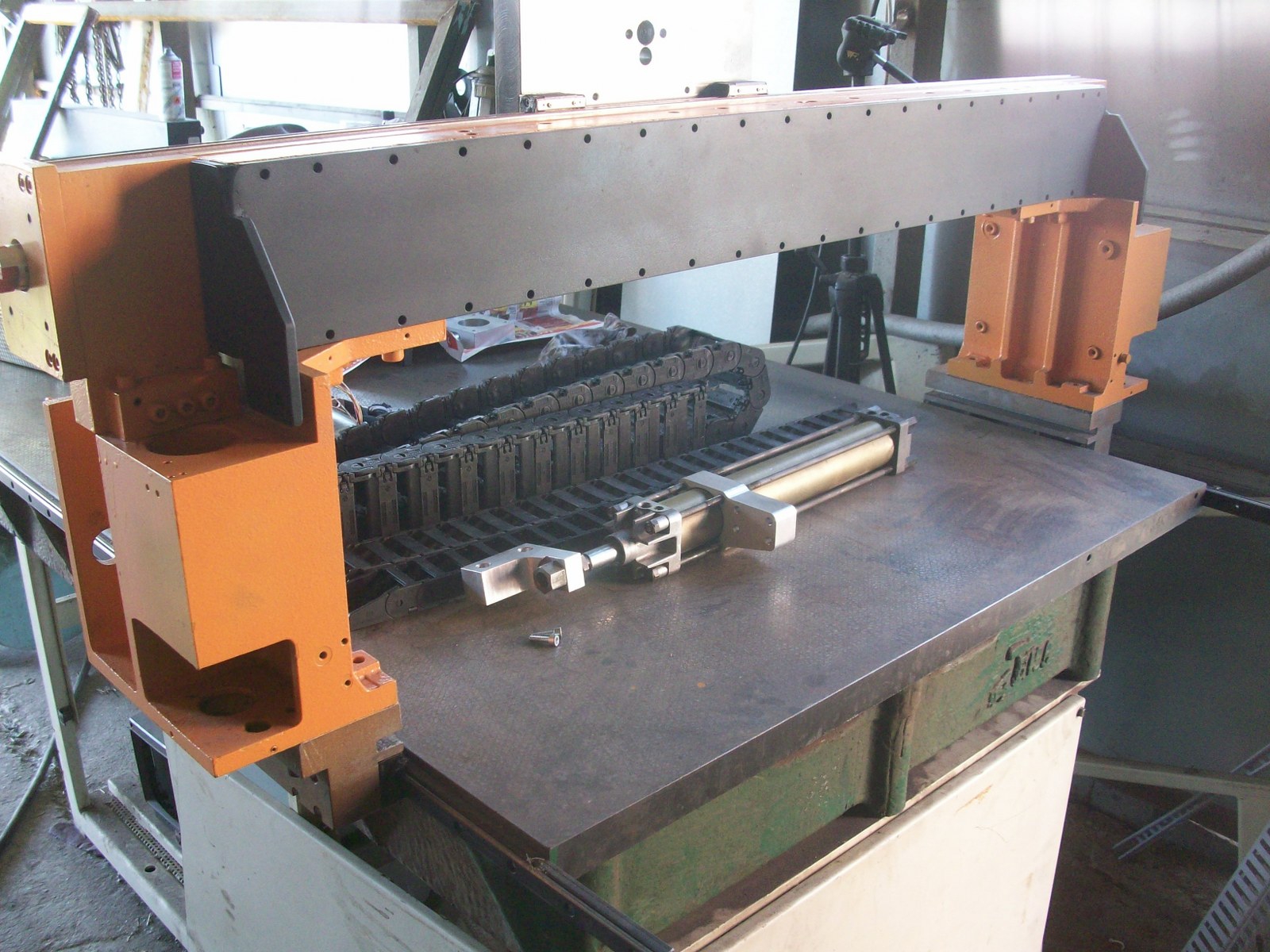
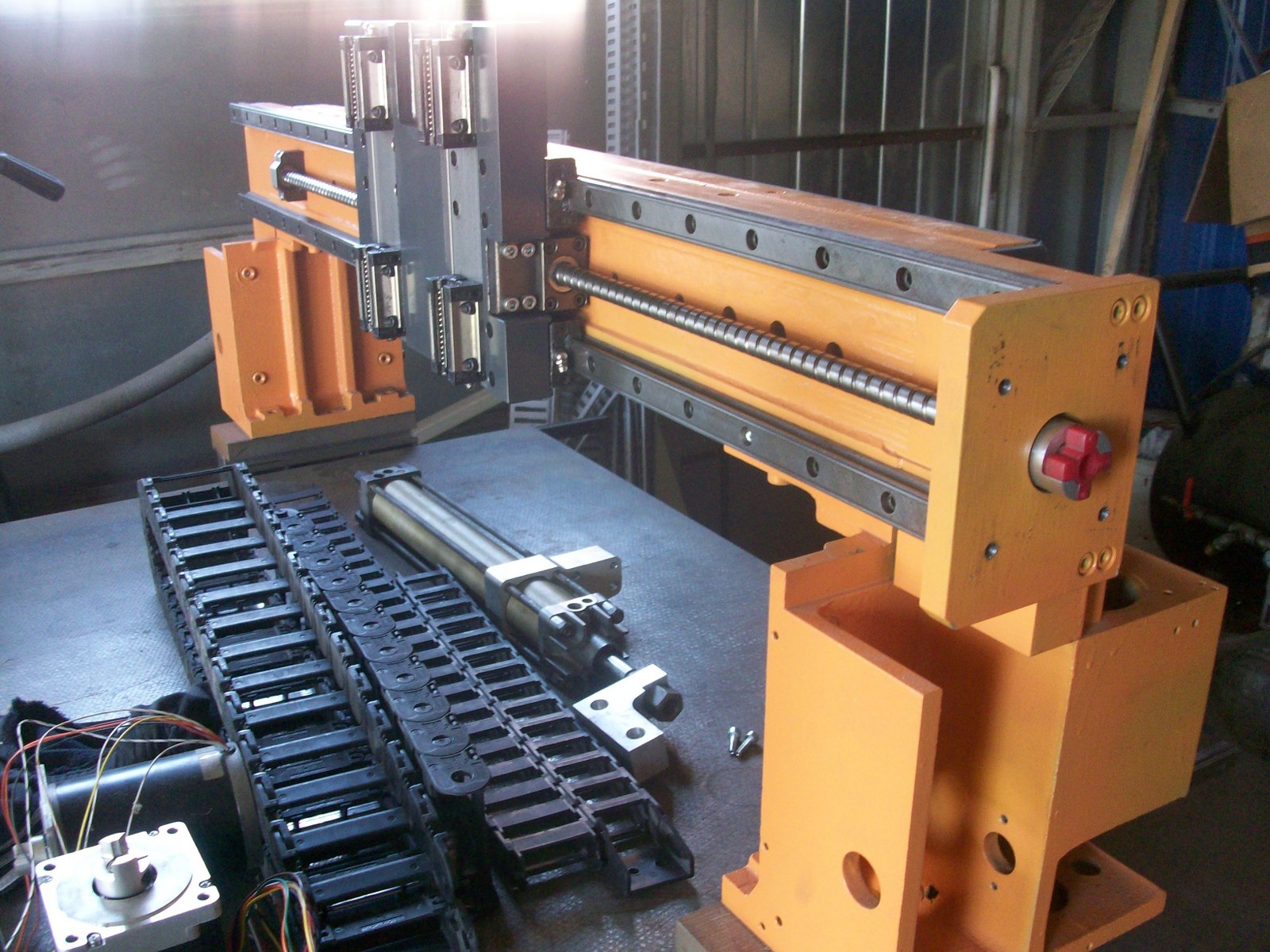
Kupiłem też kawał stali 145x145x60 (koszt 40 zł) z którego miał powstać uchwyt wrzeciona.
Zgrubne toczenie i frezowanie tego nie było łatwe i trwało kupę czasu.
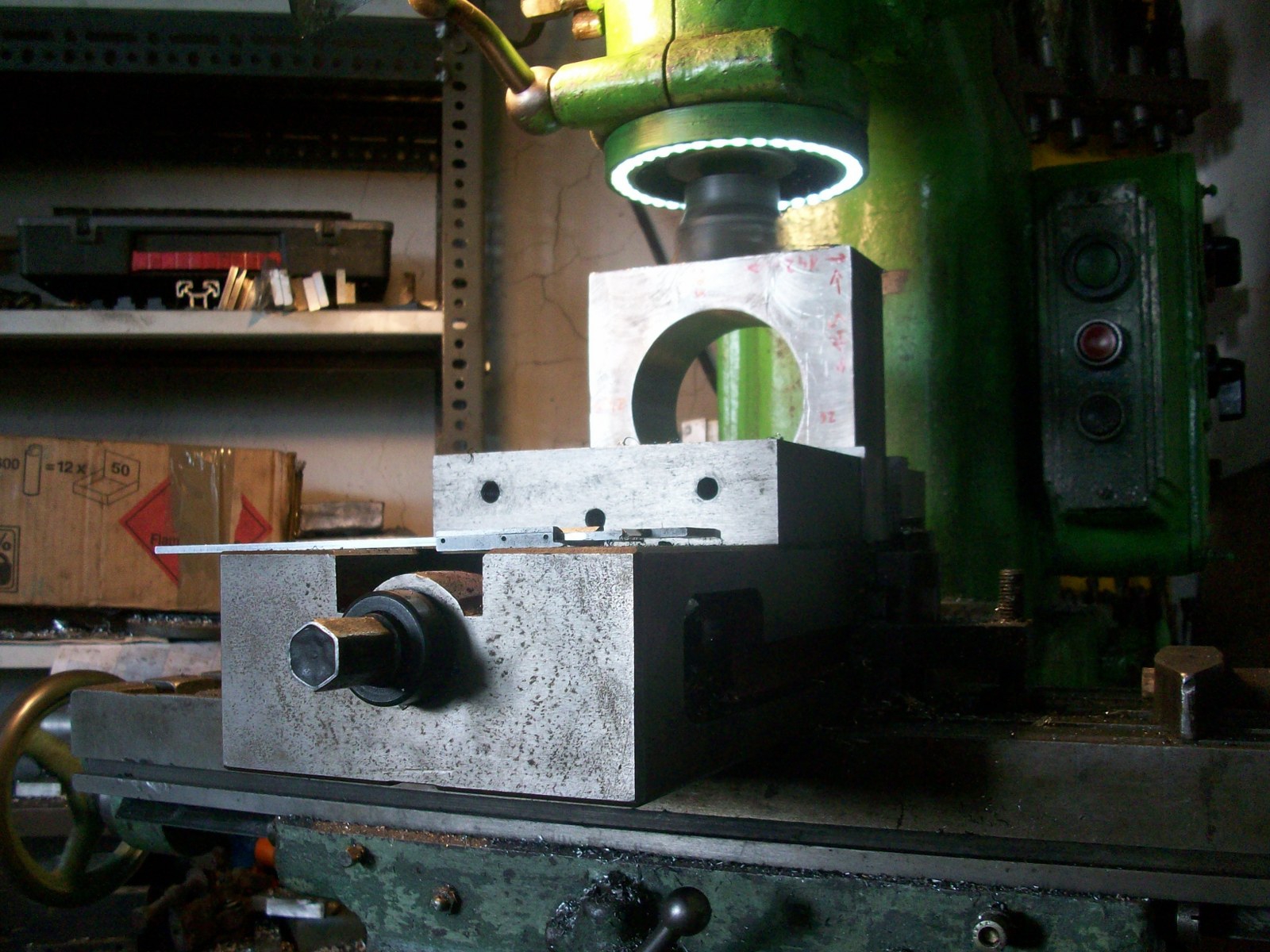
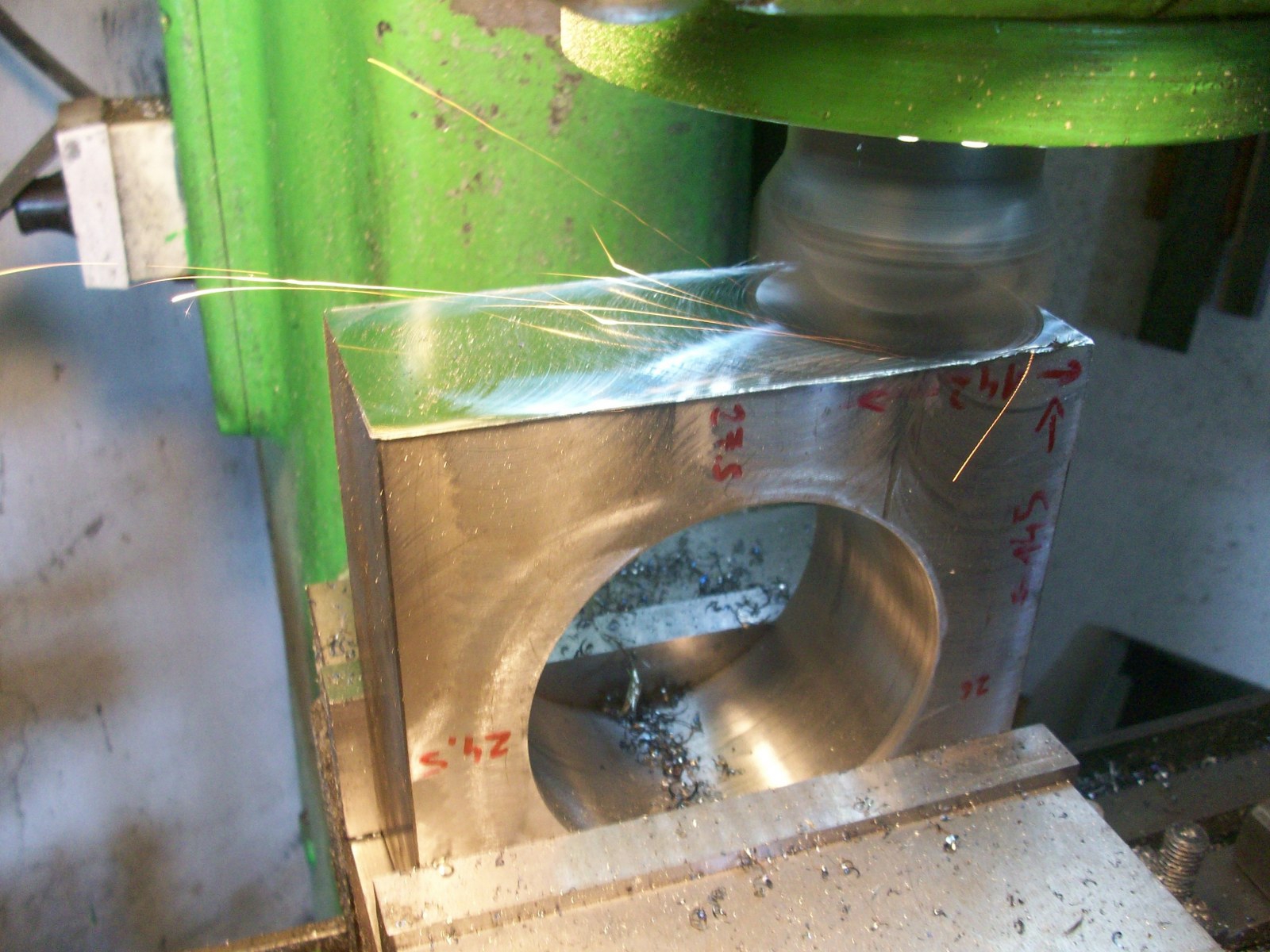
Wykończenie na wymiar otworu i czoła zostawiłem naszemu forumowemu koledze - Dudi1203.
Ma starszą ale dokładniejszą tokarkę niż moja i dużo precyzyjnych narzędzi pomiarowych więc zrobił mi to perfekcyjnie jak zawsze
. Najpierw wytoczył otwór z setka luzu na wrzeciono. Za chwilę splanował z tego samego mocowania powierzchnię czołową co dało nam pewność prostopadłości tych dwóch powierzchni. Mocowanie wrzeciona po wyjęciu z tokarki powędrowało na frezarkę i zamocowane zostało tą splanowaną powierzchnią do stołu pod kątem prostym i można było wyprowadzić płaszczyznę mocowania do płyty Z-ki oraz precyzyjnie powiercić otwory. Taką robotę lubimy tym bardziej że majster Dudi pozwala gapić się na jego sprawne ręce i podglądać jak powstają kolejne elementy do maszyny.
Zawsze wszystko cierpliwie tłumaczy i na każde pytanie odpowiada. Nie wiem skąd On ma tą całą wiedzę i umiejętności...
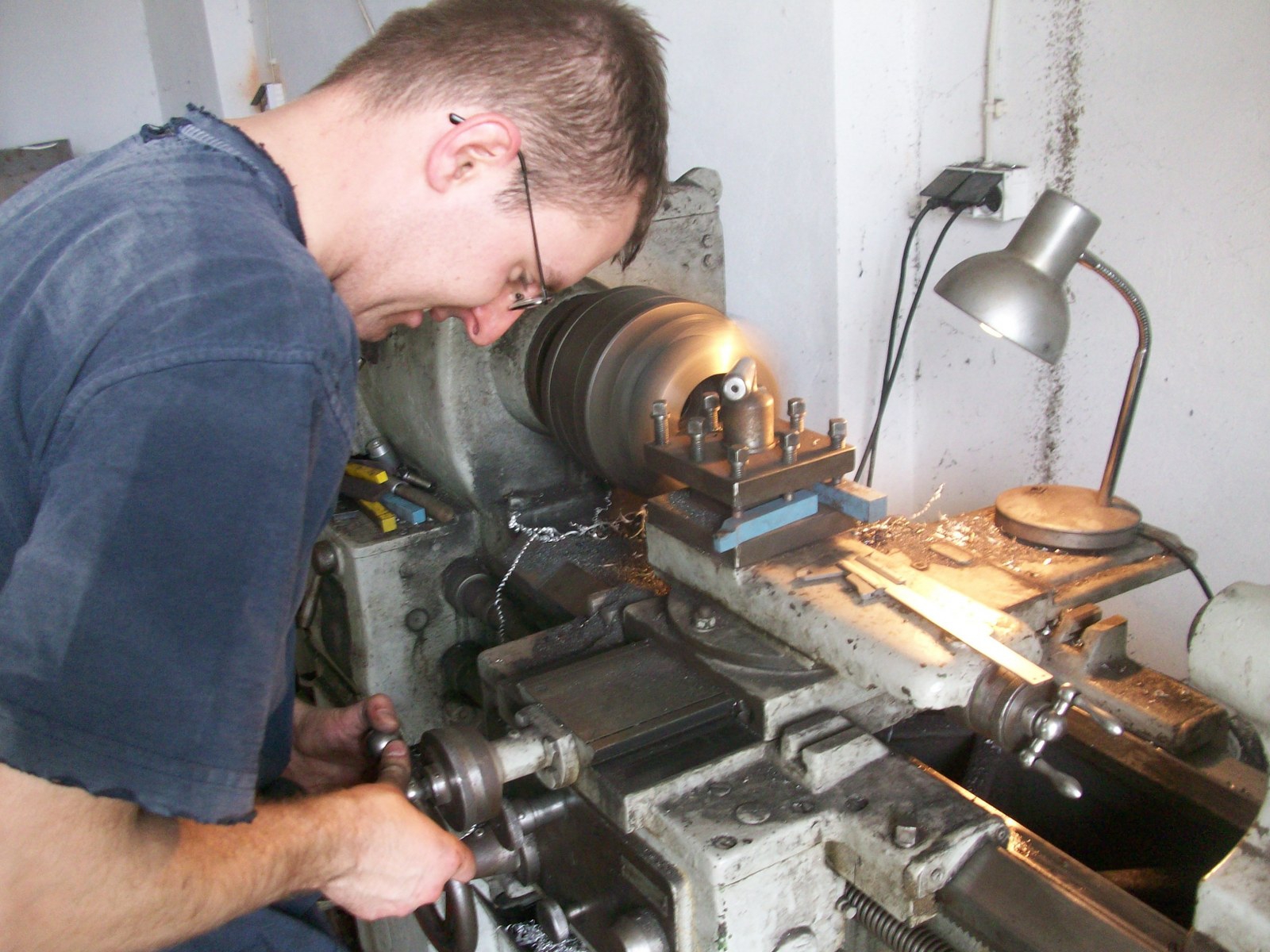
Na frezarkę powędrowała tez płyta osi Z w której zostały wykonane otwory do przykręcenia mocowania wrzeciona. Zażyczyłem sobie 8 otworów w rozstawie 38x100mm. Dzięki tylu otworom mam możliwość podnieść wrzeciono o oczko wyżej lub niżej co może się przydać w krytycznych sytuacjach jak na przykład wiercenie długim wiertłem w wysokim przedmiocie.
O precyzyjne prostopadłe ustawienie wrzeciona zadba rowek z klinem. Klin (8mm szerokości) jest ciasno osadzony w mocowaniu wrzeciona i spasowany suwliwie w rowku w płycie osi Z.
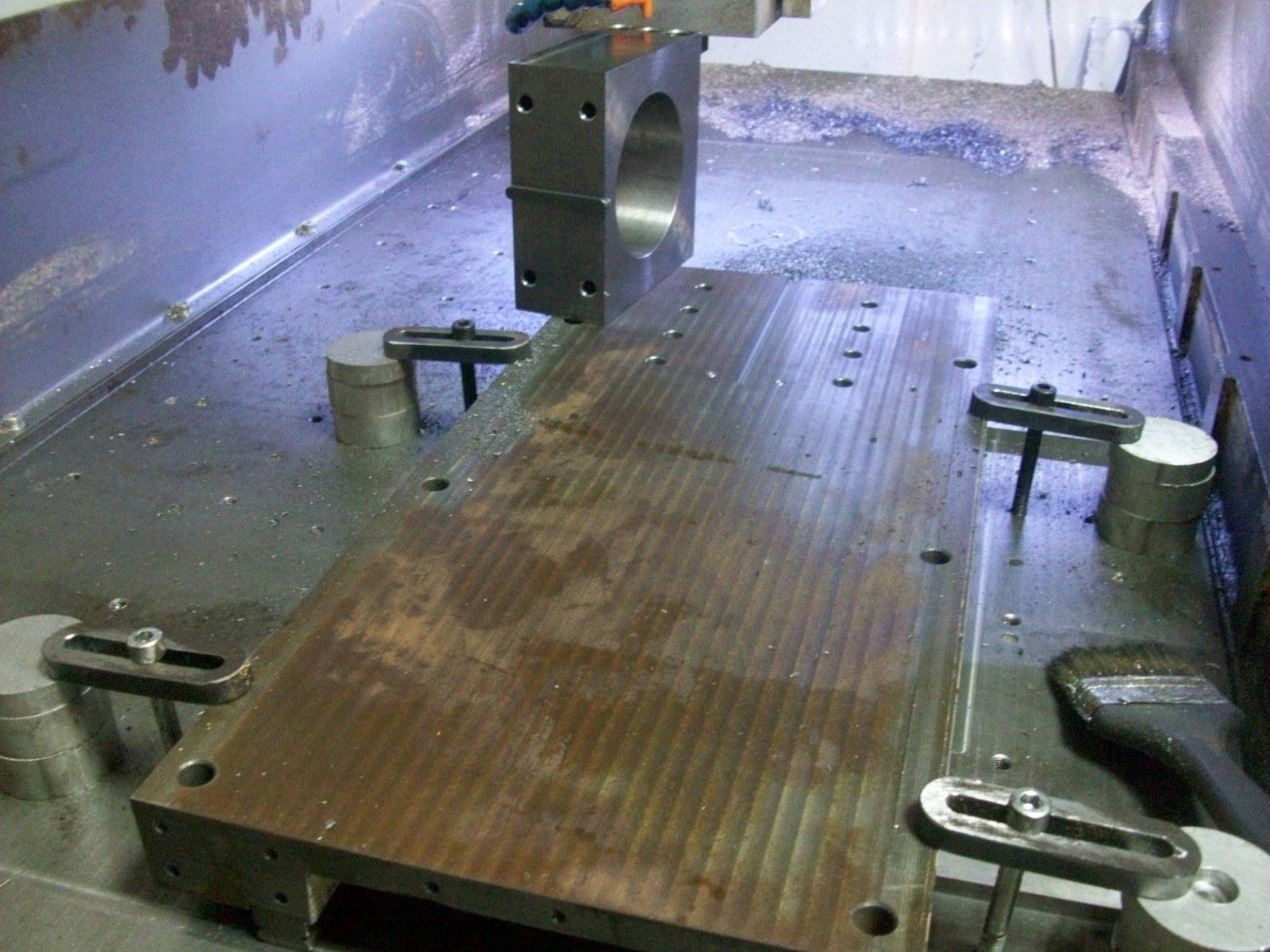
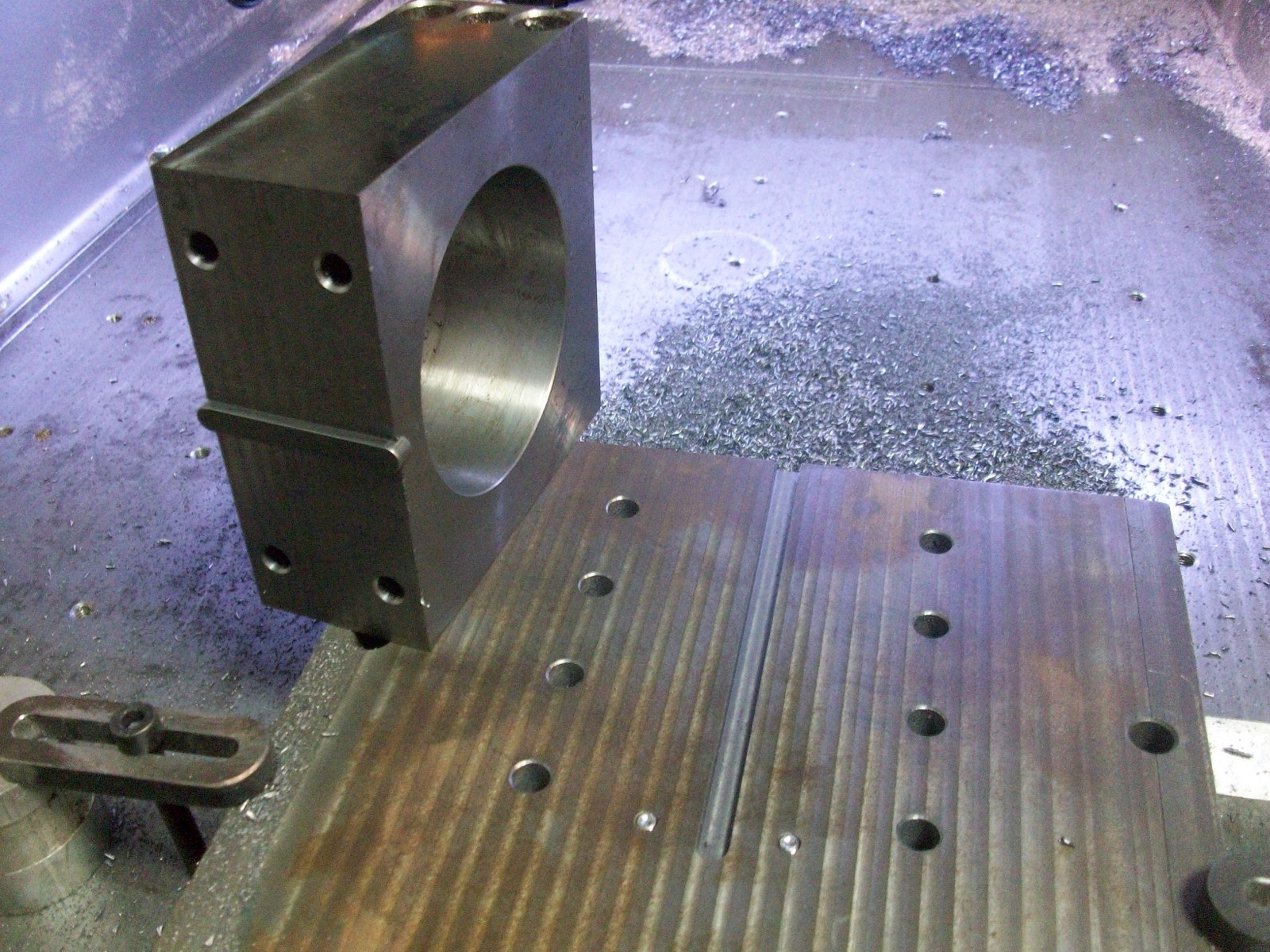
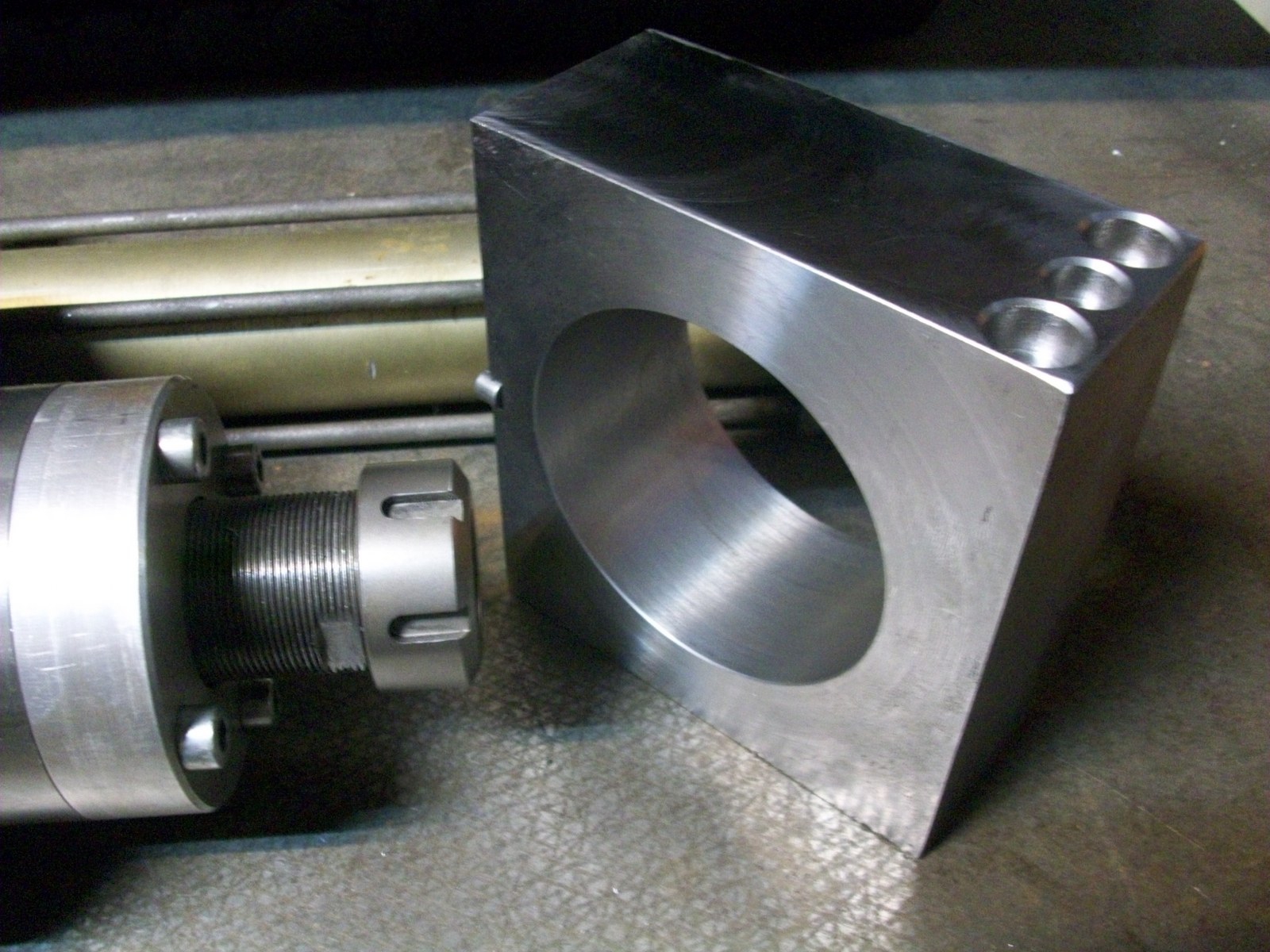
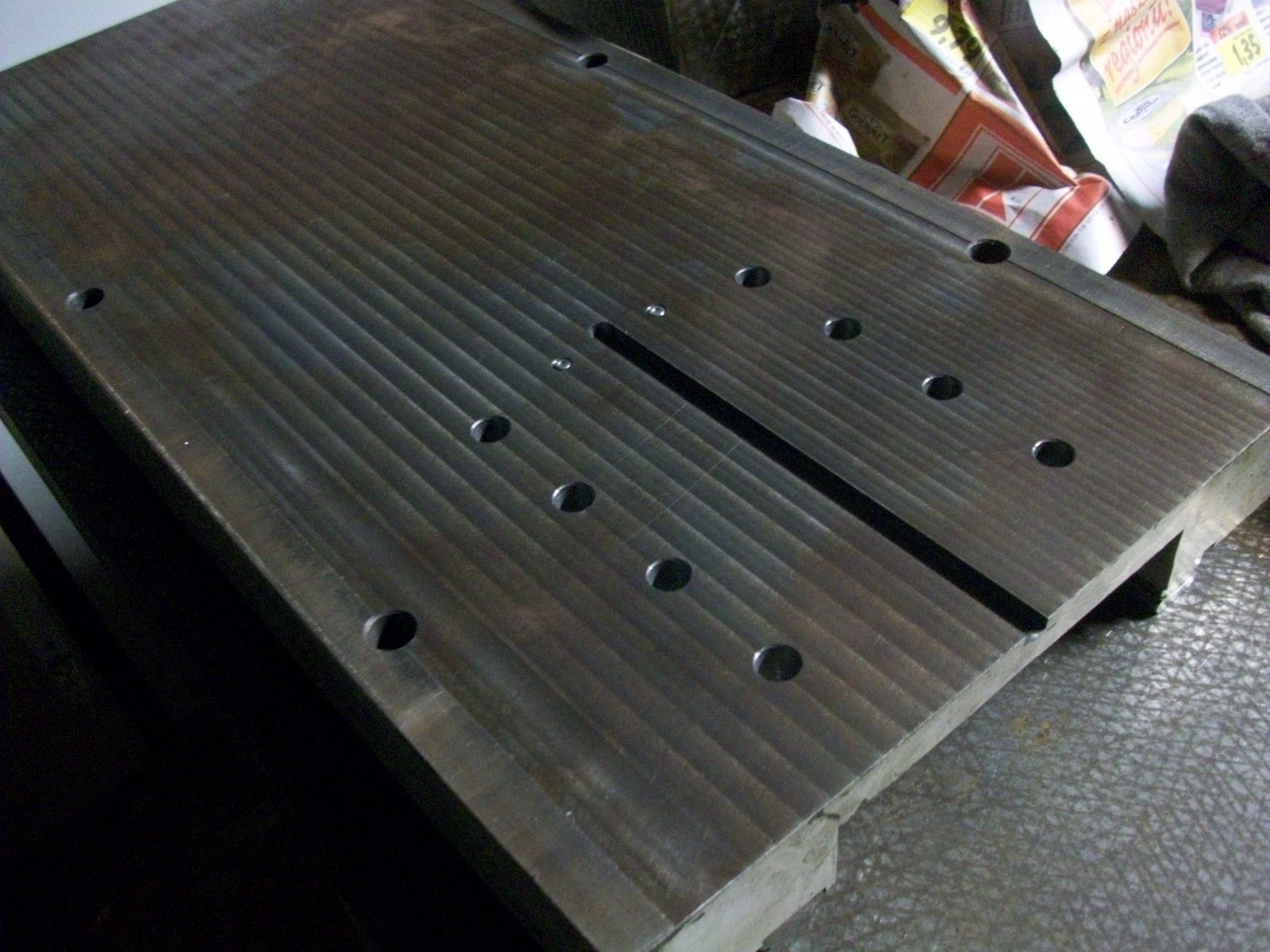
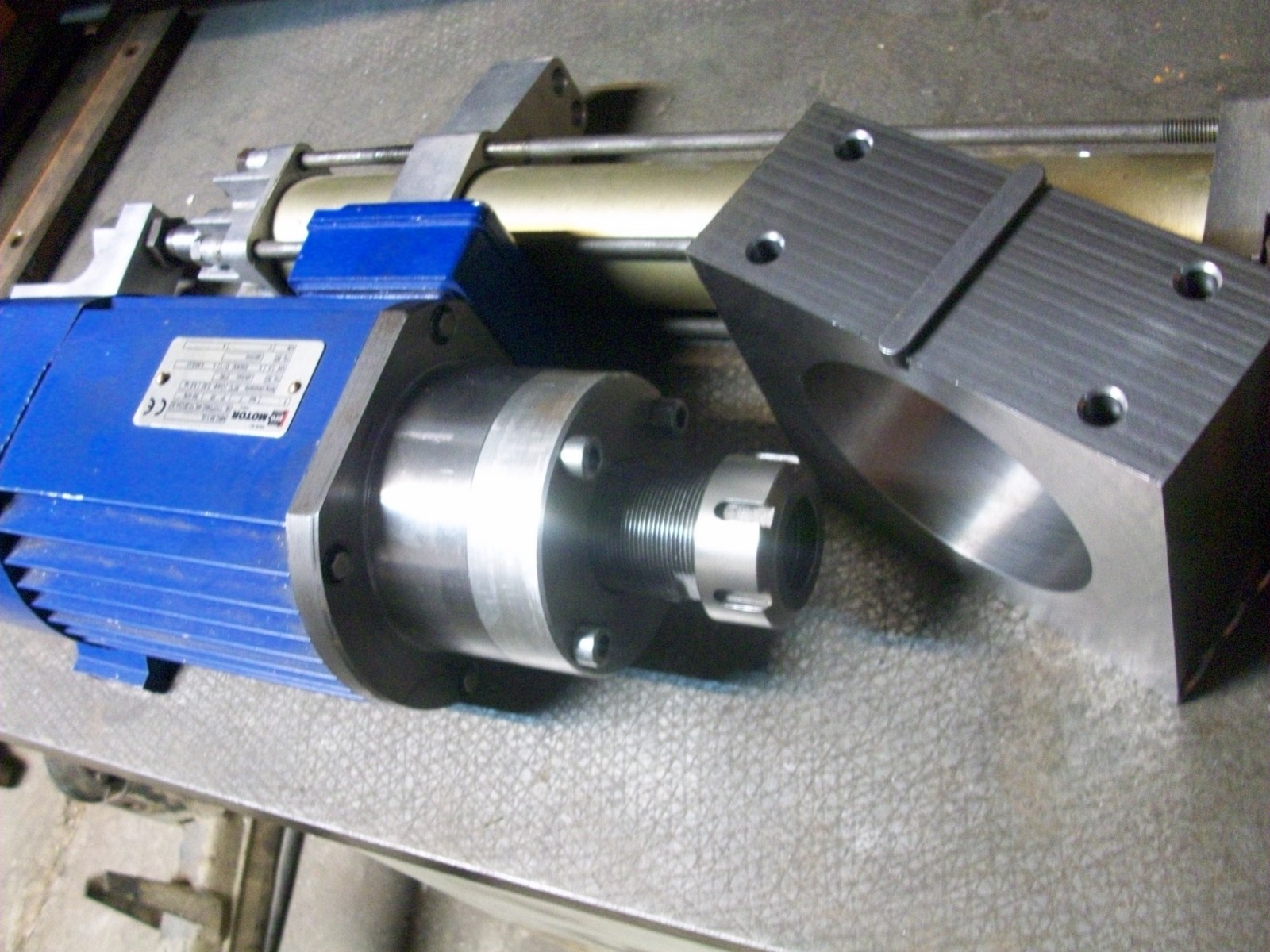
Od Dudiego odkupiłem jego pierwsze wrzeciono z ER32 więc jestem cały w skowronkach bo tego urządzenia brakowało mi najbardziej.
Jutro czeka mnie powiercanie otworów do zaciskania wrzeciona, przecięcie uchwytu, gwintowanie, gratowanie, fazowanie, malowanie i inne przyjemne prace

Długo nie miałem czasu na dłubanie przy maszynie bo zawsze coś ważniejszego wypadało.
Ale coś drgnęło. Przycisnąłem trochę i są postępy.
Tak więc pokazuję co się ostatnio działo.
Wykombinowałem sobie ładne prowadniki przewodów firmy Tsubaki (wykopałem ze śmieci w Extremtechu). Nie miały one zakończeń do montażu więc sobie je pomierzyłem i wyfrezowałem w aluminium. Pasują bardzo ładnie. Teraz będzie je można zamontować bez druciarstwa.
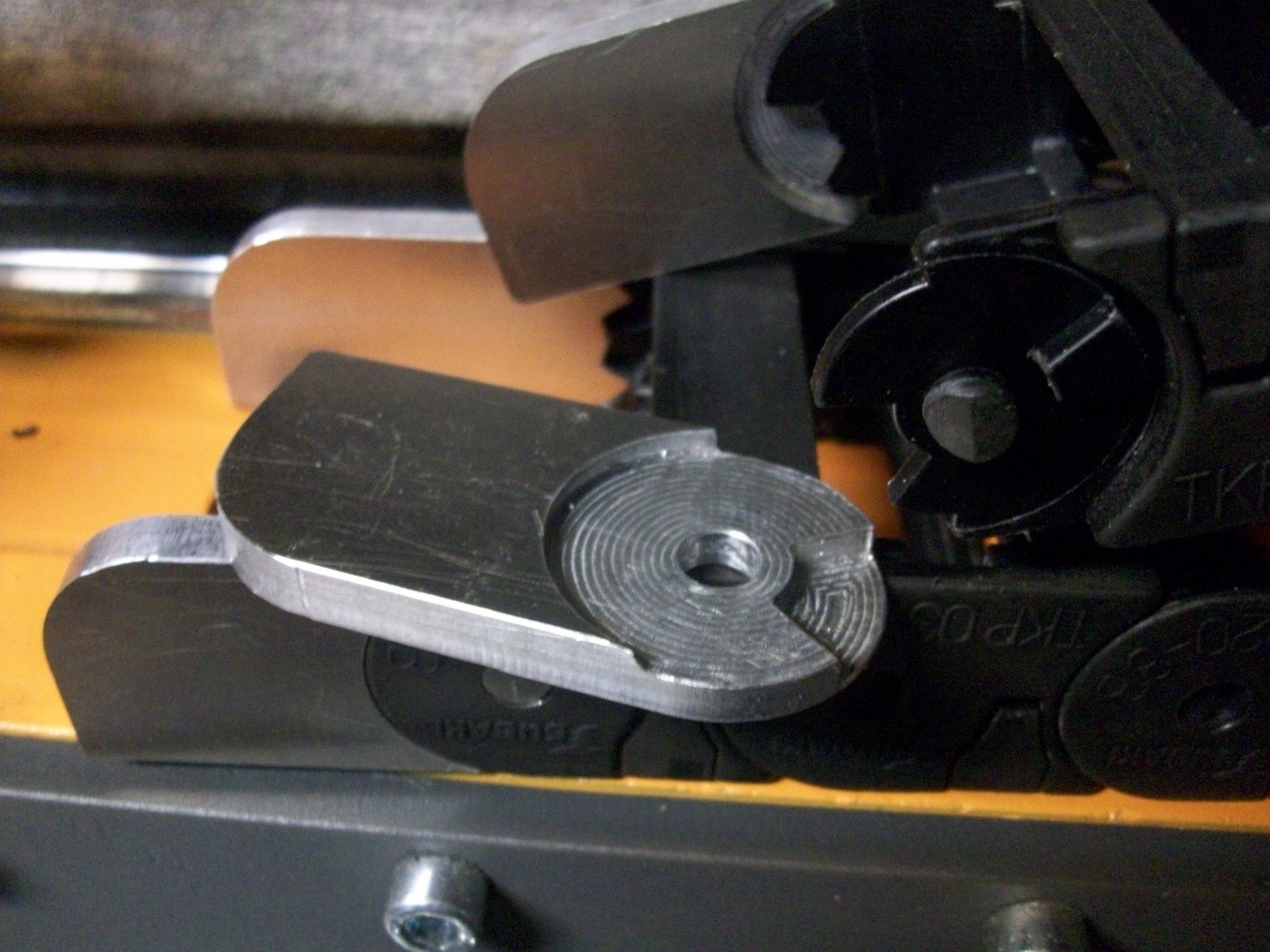
Zleciłem wypalenie 8-ki blachy na laserze abym mógł nią zamknąć ten żeliwny ceownik na bramie.
Blaszkę pomalowałem i przykręciłem. Pomalowałem tez krzyżak bo mi ktoś coś o rdzy wypominał ostatnio


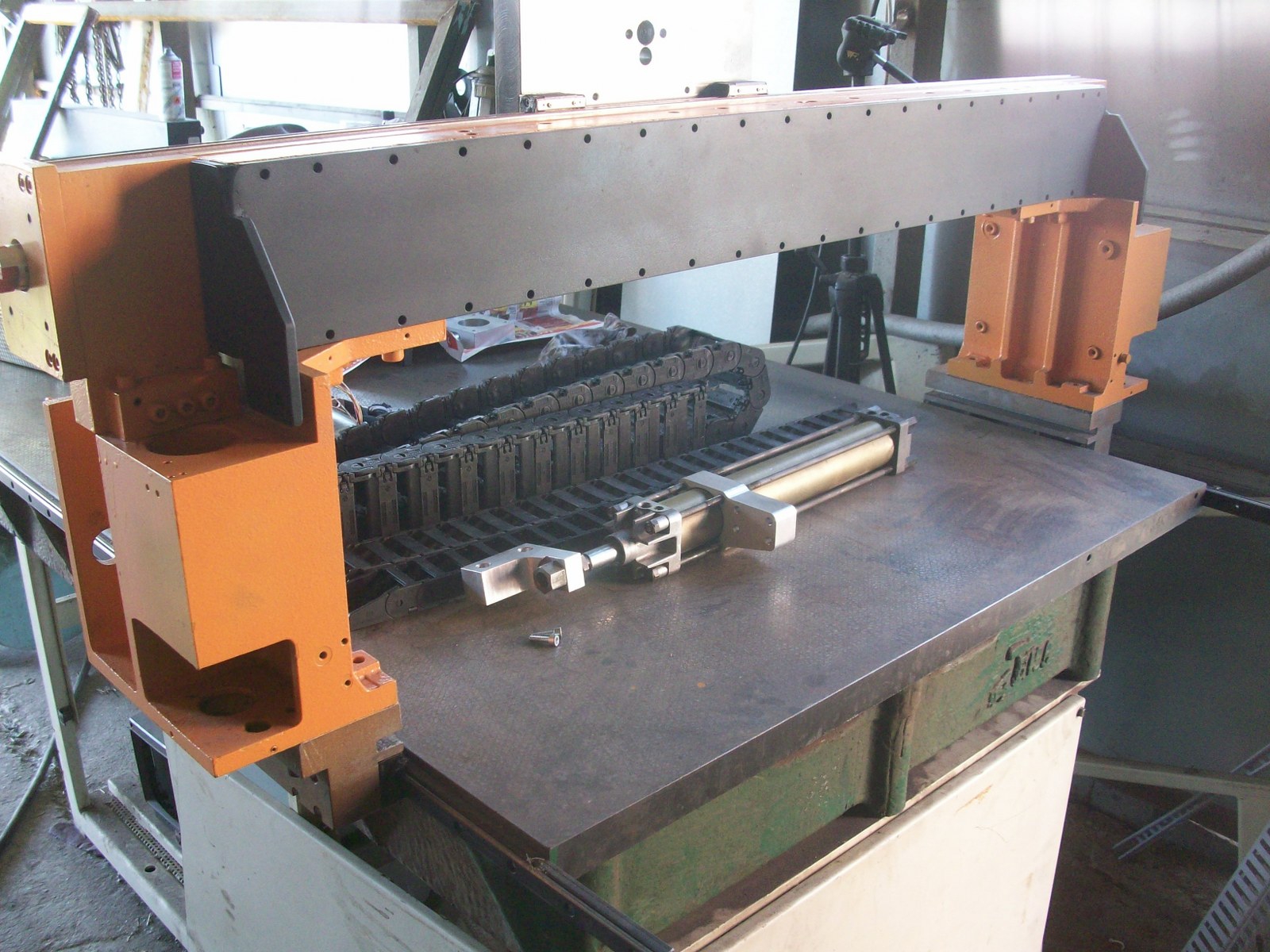
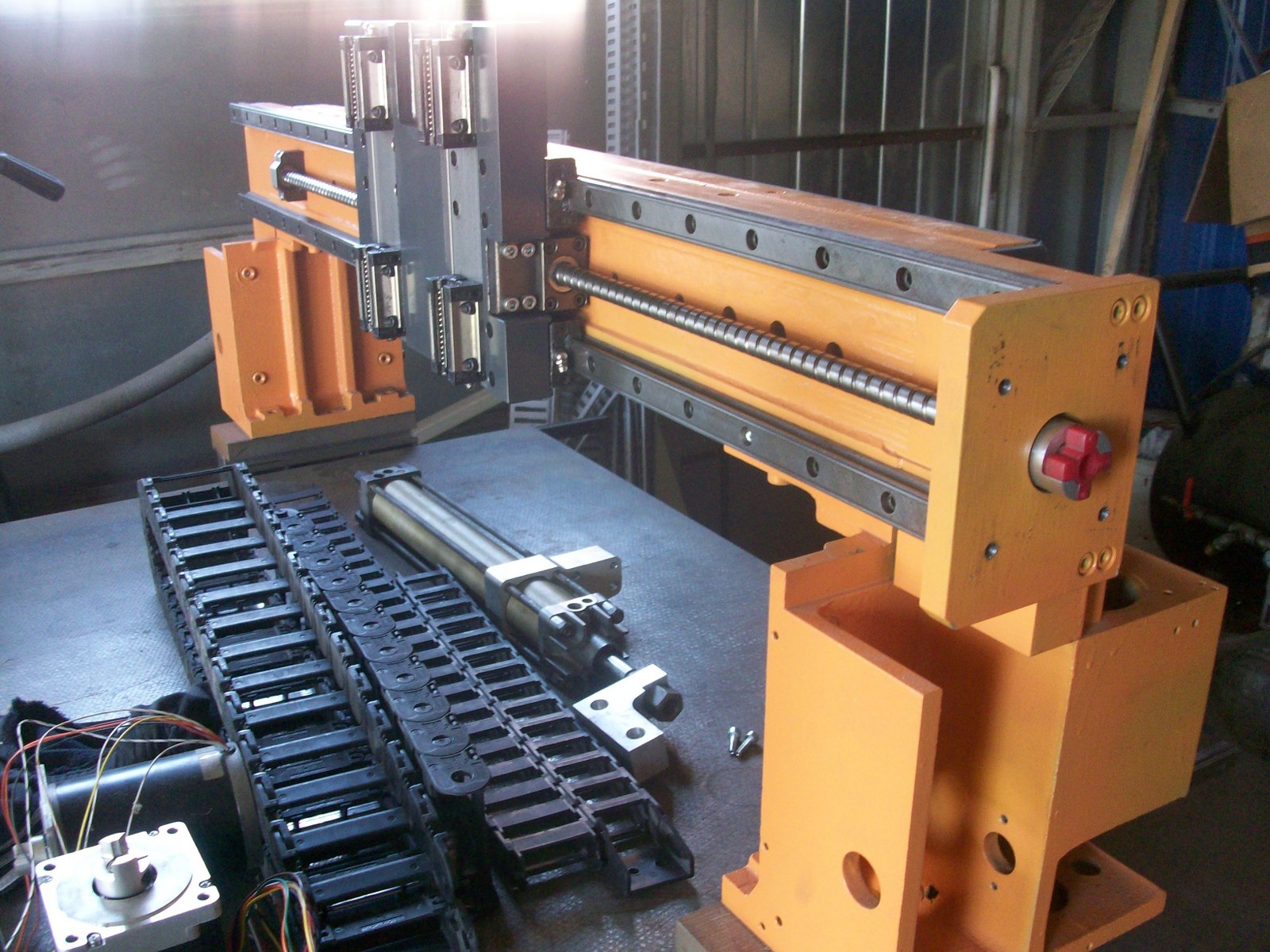
Kupiłem też kawał stali 145x145x60 (koszt 40 zł) z którego miał powstać uchwyt wrzeciona.
Zgrubne toczenie i frezowanie tego nie było łatwe i trwało kupę czasu.
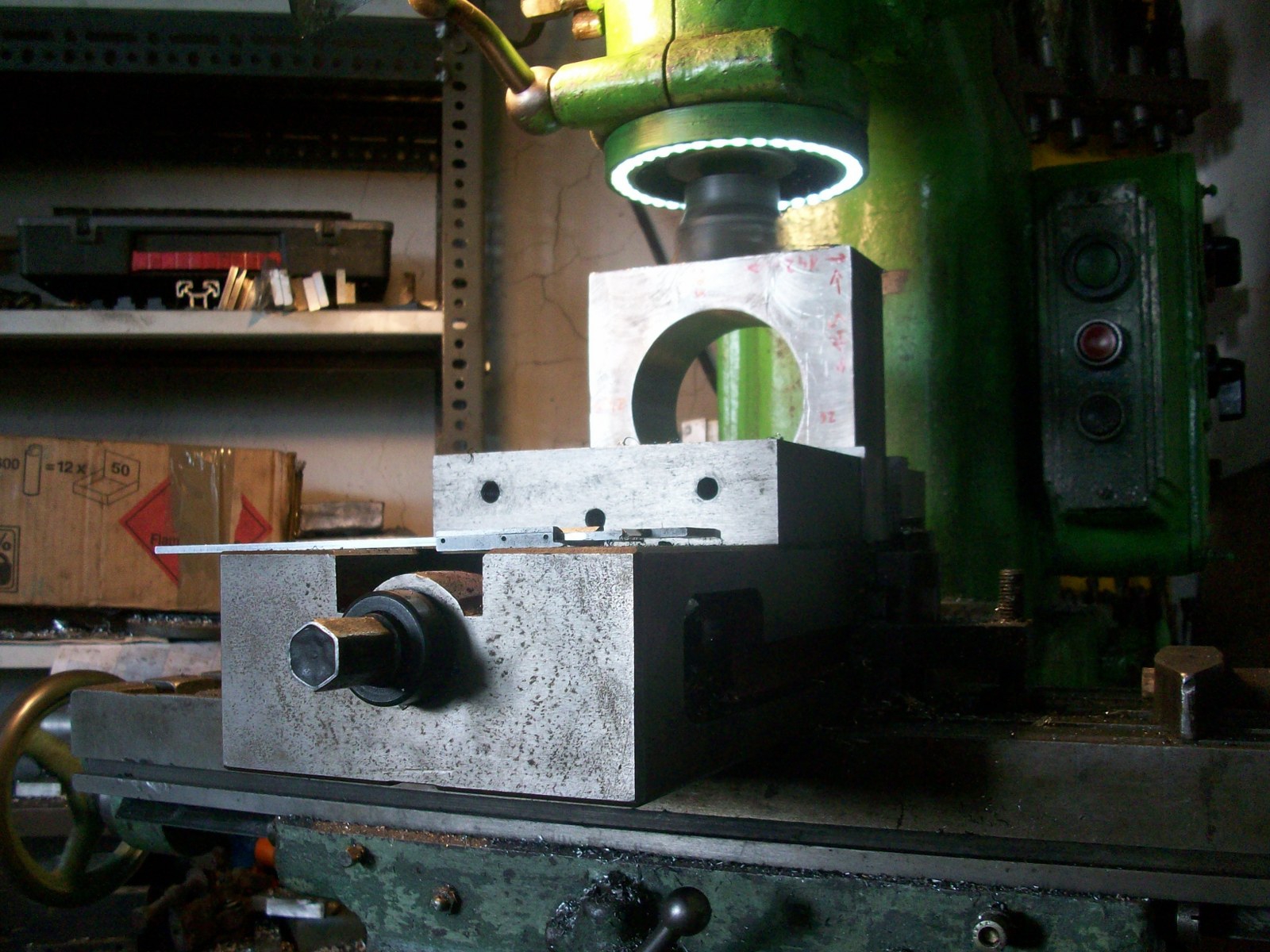
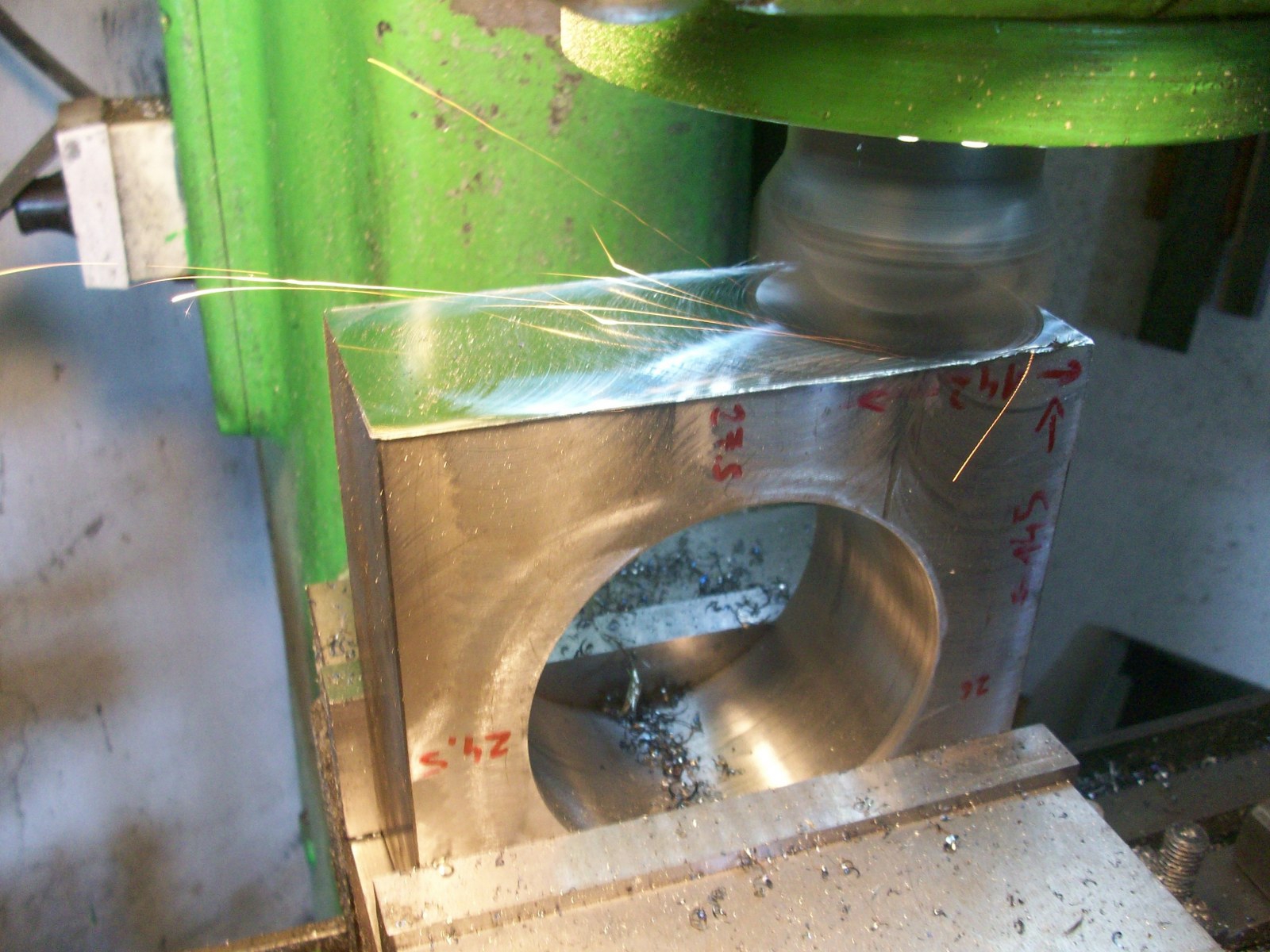
Wykończenie na wymiar otworu i czoła zostawiłem naszemu forumowemu koledze - Dudi1203.
Ma starszą ale dokładniejszą tokarkę niż moja i dużo precyzyjnych narzędzi pomiarowych więc zrobił mi to perfekcyjnie jak zawsze

Zawsze wszystko cierpliwie tłumaczy i na każde pytanie odpowiada. Nie wiem skąd On ma tą całą wiedzę i umiejętności...

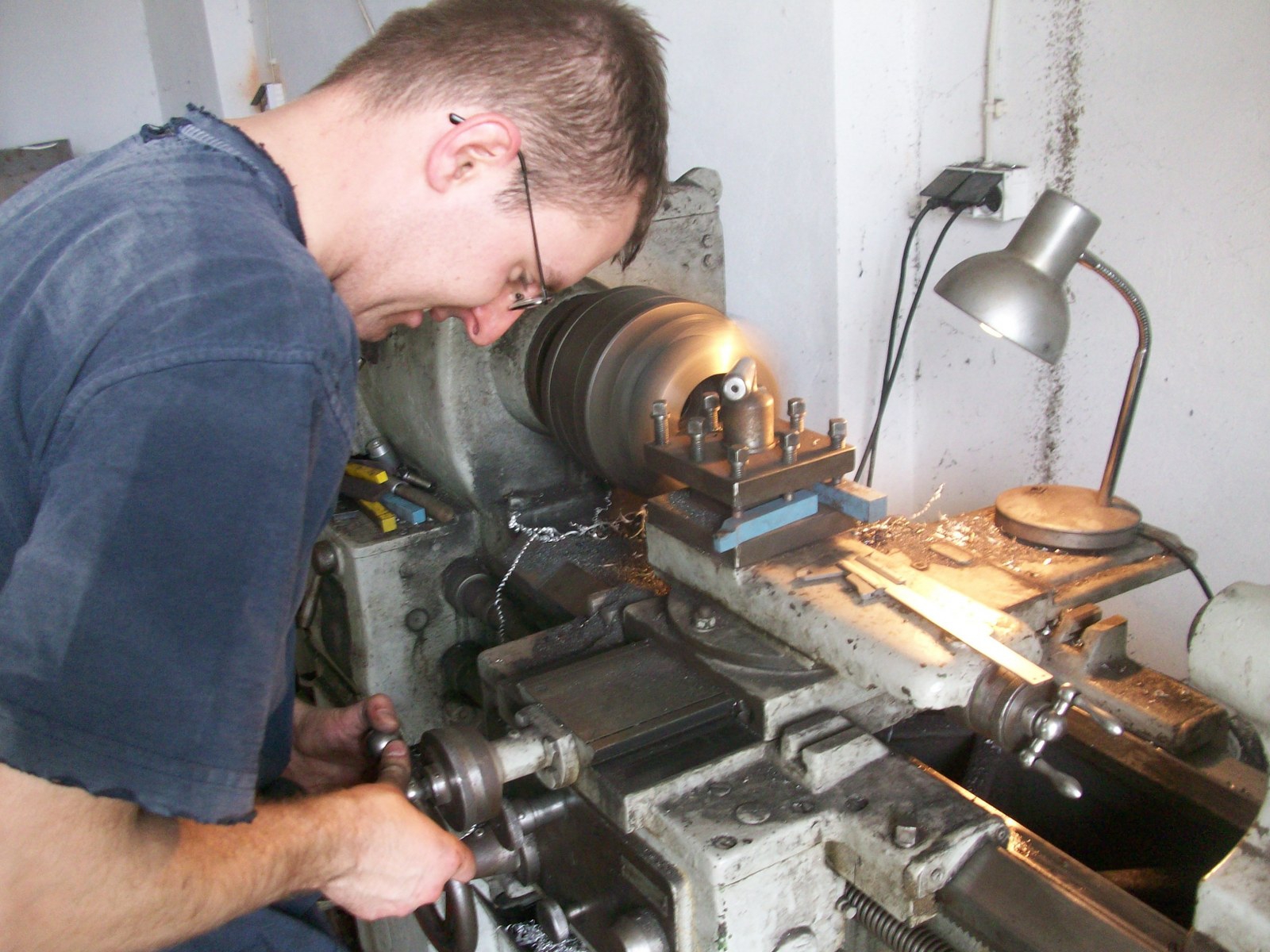
Na frezarkę powędrowała tez płyta osi Z w której zostały wykonane otwory do przykręcenia mocowania wrzeciona. Zażyczyłem sobie 8 otworów w rozstawie 38x100mm. Dzięki tylu otworom mam możliwość podnieść wrzeciono o oczko wyżej lub niżej co może się przydać w krytycznych sytuacjach jak na przykład wiercenie długim wiertłem w wysokim przedmiocie.
O precyzyjne prostopadłe ustawienie wrzeciona zadba rowek z klinem. Klin (8mm szerokości) jest ciasno osadzony w mocowaniu wrzeciona i spasowany suwliwie w rowku w płycie osi Z.
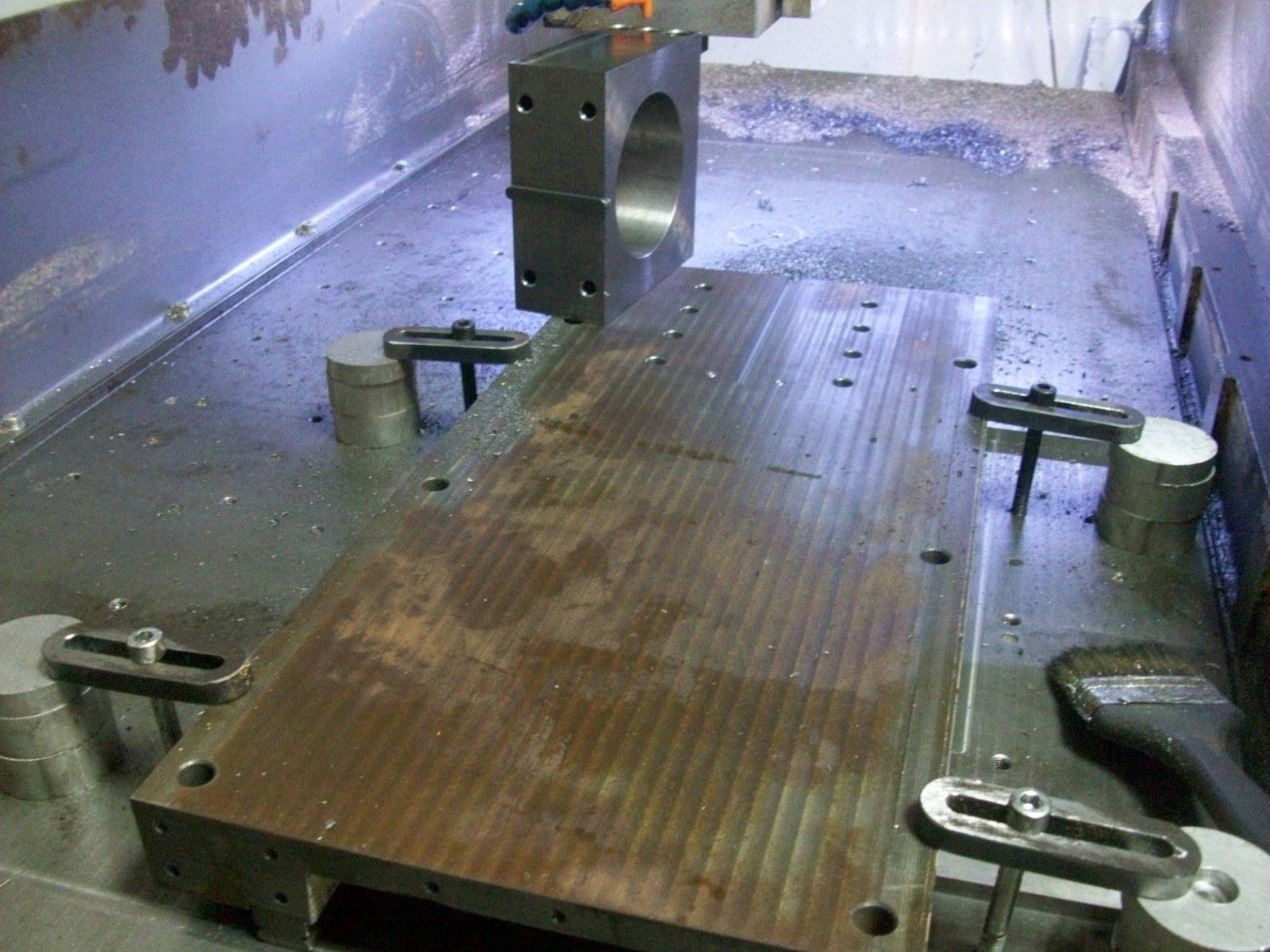
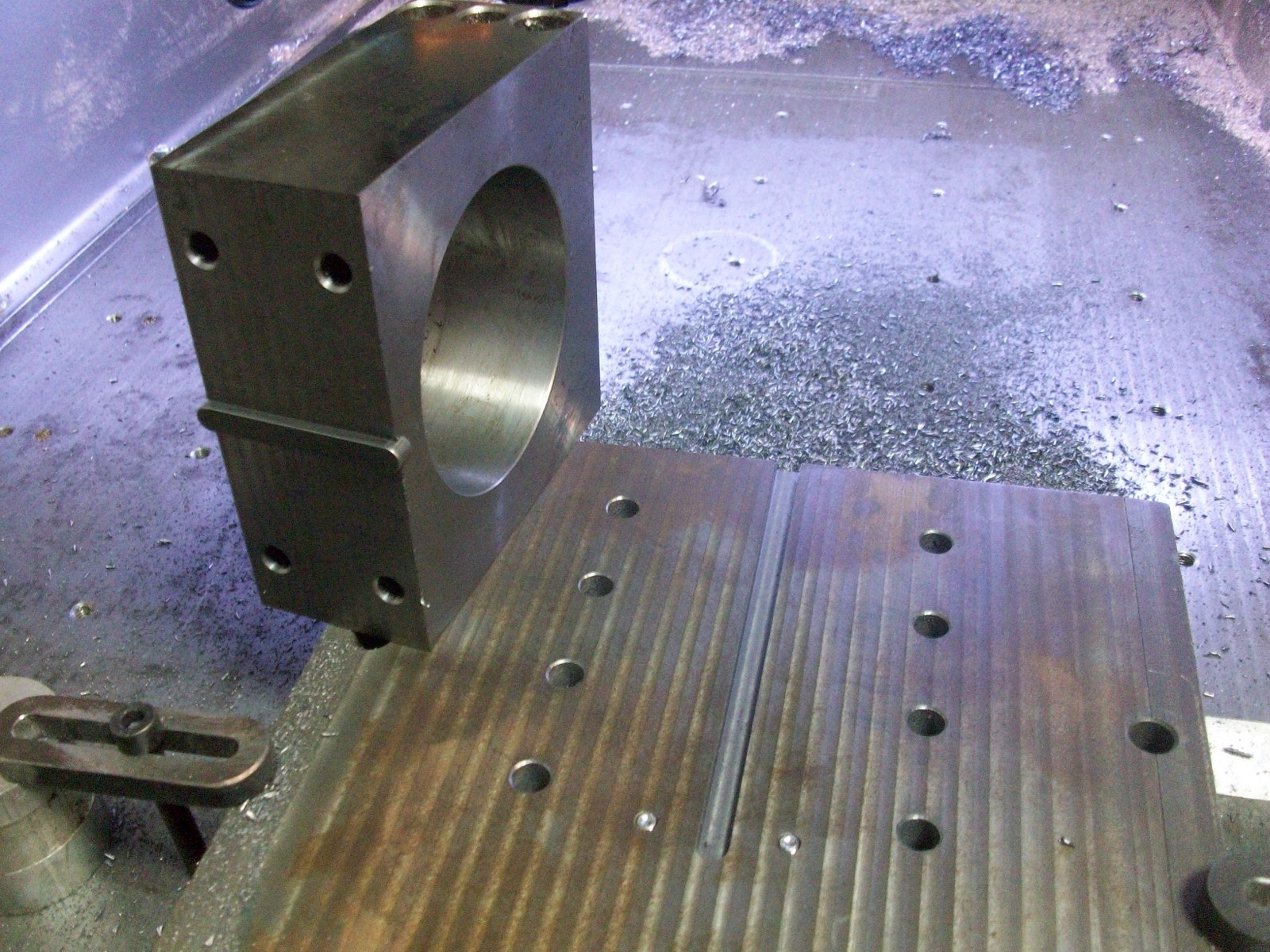
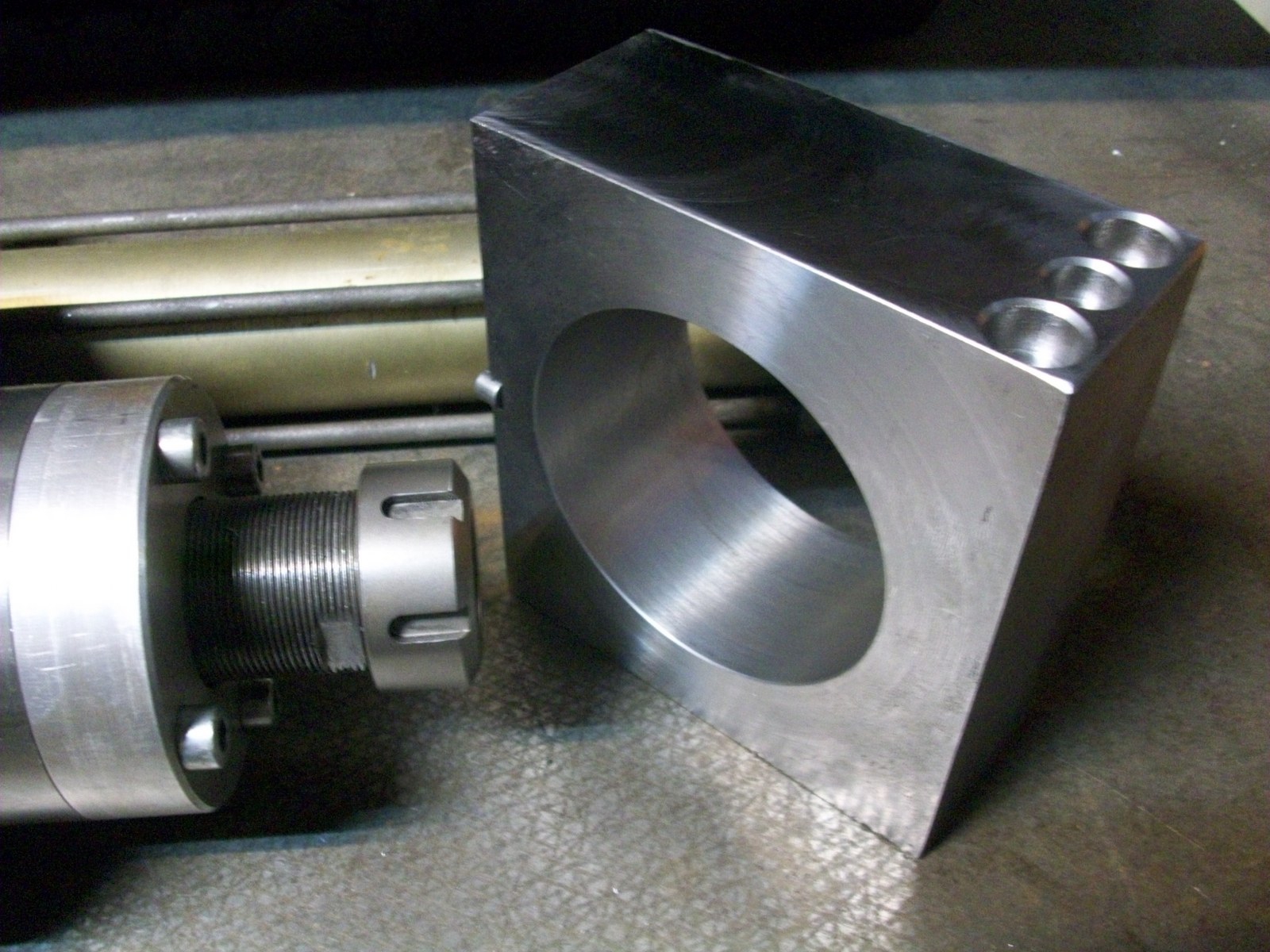
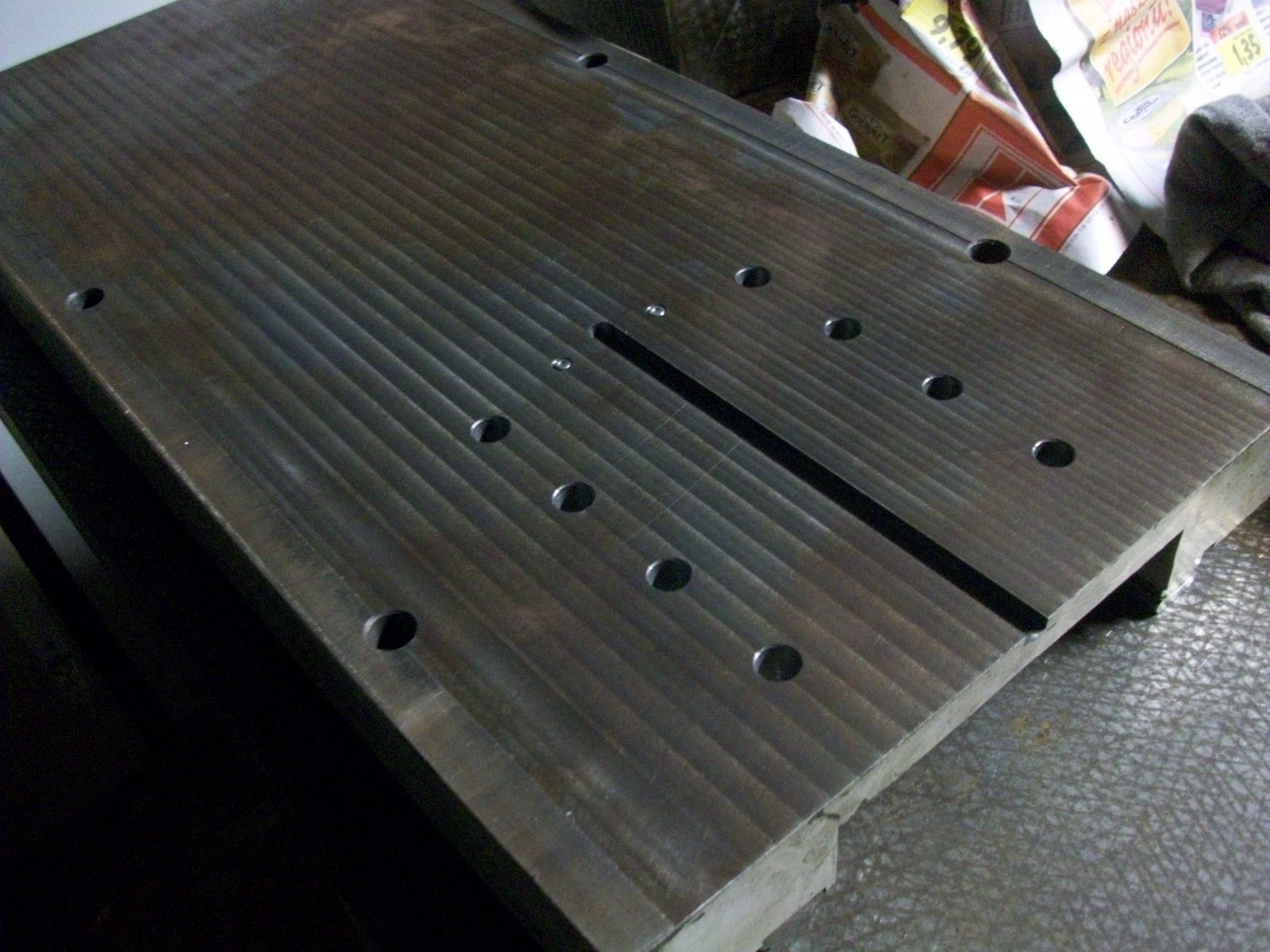
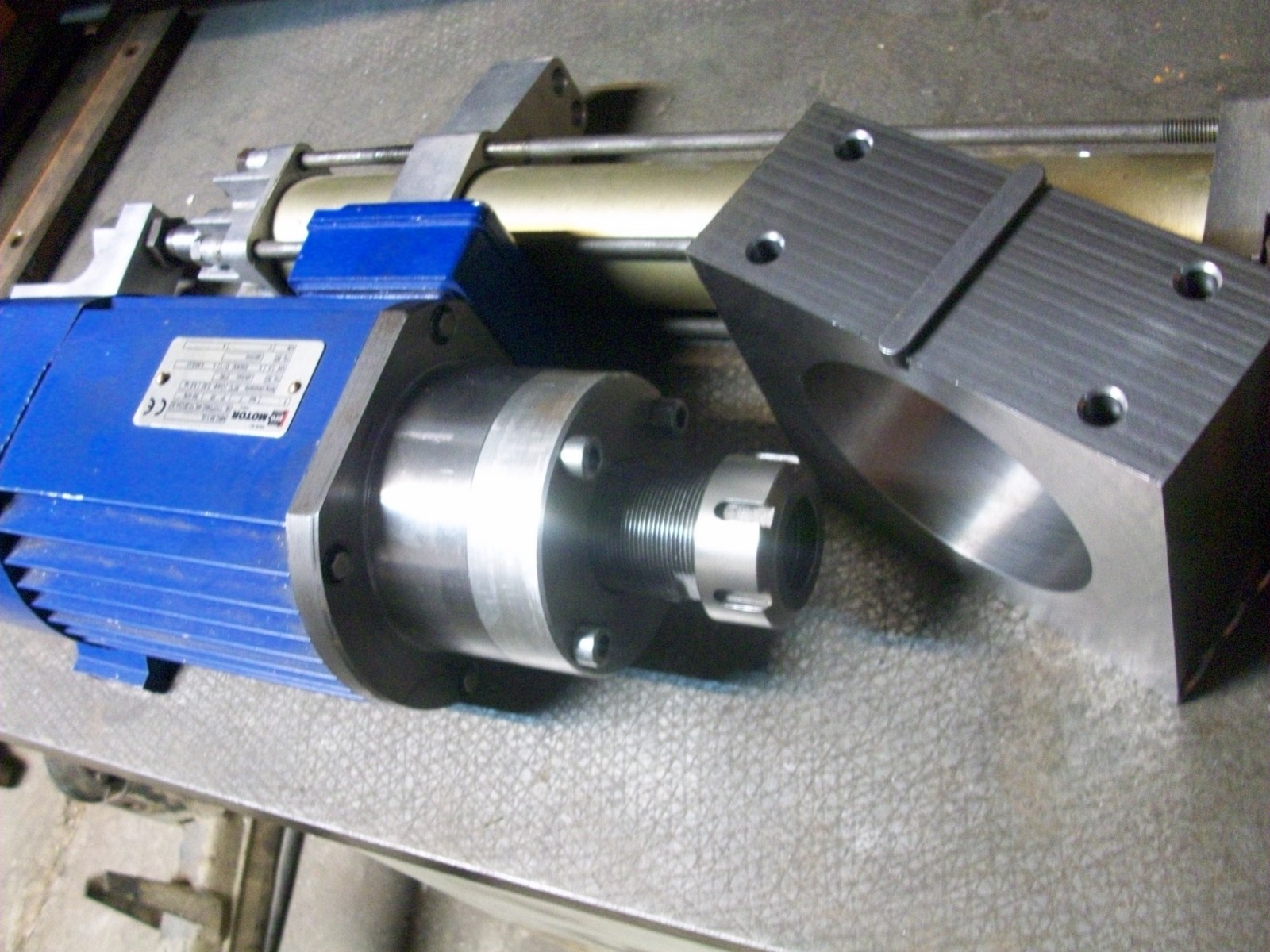
Od Dudiego odkupiłem jego pierwsze wrzeciono z ER32 więc jestem cały w skowronkach bo tego urządzenia brakowało mi najbardziej.
Jutro czeka mnie powiercanie otworów do zaciskania wrzeciona, przecięcie uchwytu, gwintowanie, gratowanie, fazowanie, malowanie i inne przyjemne prace


-
- Specjalista poziom 2 (min. 300)
- Posty w temacie: 4
- Posty: 309
- Rejestracja: 19 sty 2014, 18:56
- Lokalizacja: Elbląg
-
Autor tematu - ELITA FORUM (min. 1000)
- Posty w temacie: 38
- Posty: 1361
- Rejestracja: 18 sie 2010, 10:58
- Lokalizacja: Okolice Łodzi
I kolejna porcja fotek. Praca przy najtrudniejszej osi Y wzdłuż stołu:
.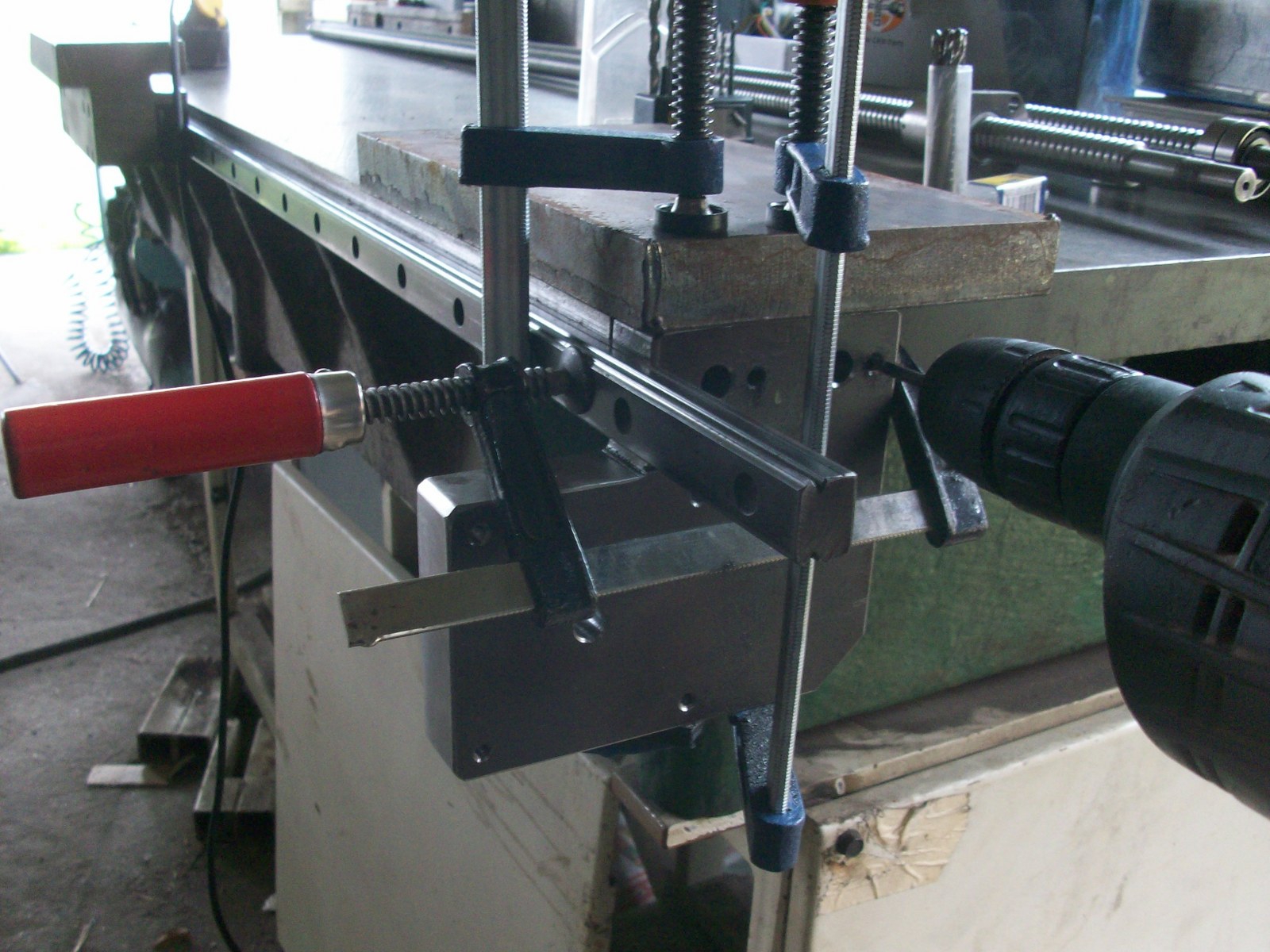
.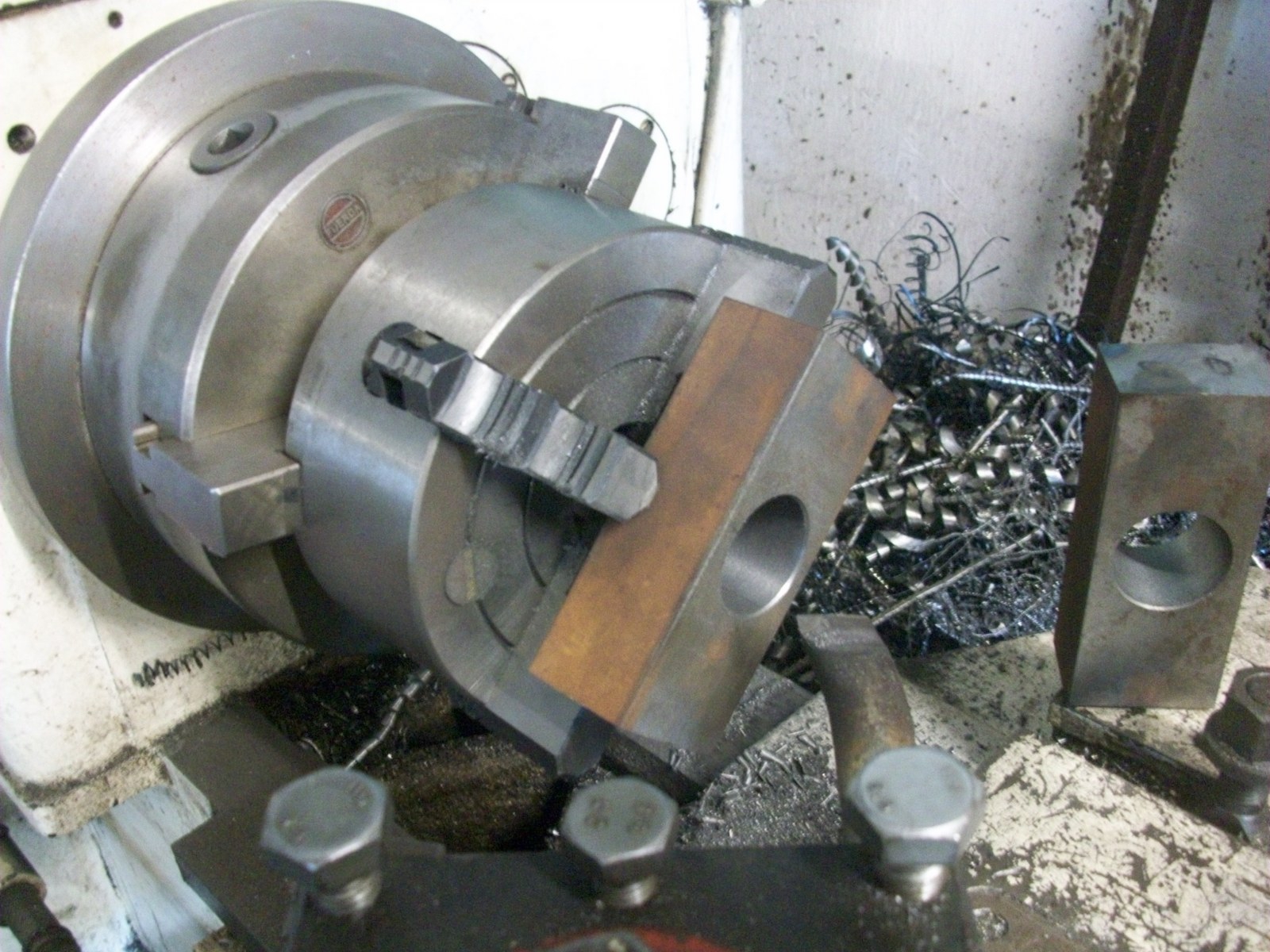
.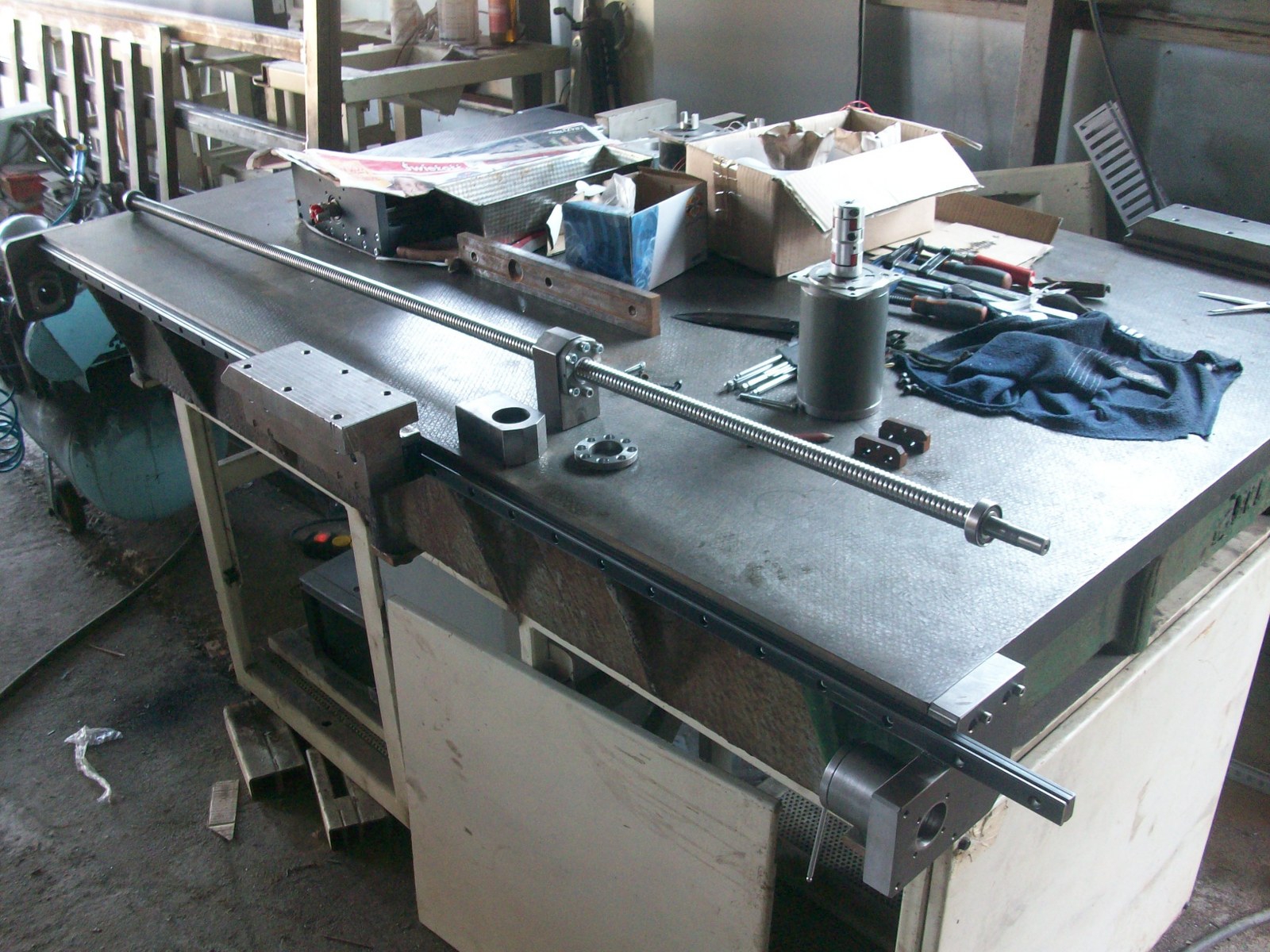
Pozazdrościłem wujowi Kamarowi Flycuttera i w końcu zrobiłem i dla siebie. Stara oprawka na tulejki z przyspawanym kawałkiem nawierconej i nagwintowanej stali, stare koło zamachowe z malucha i 3 godzinki pracy i oto jest. W stali robi to średnio ale aluminium gładzi aż miło.
.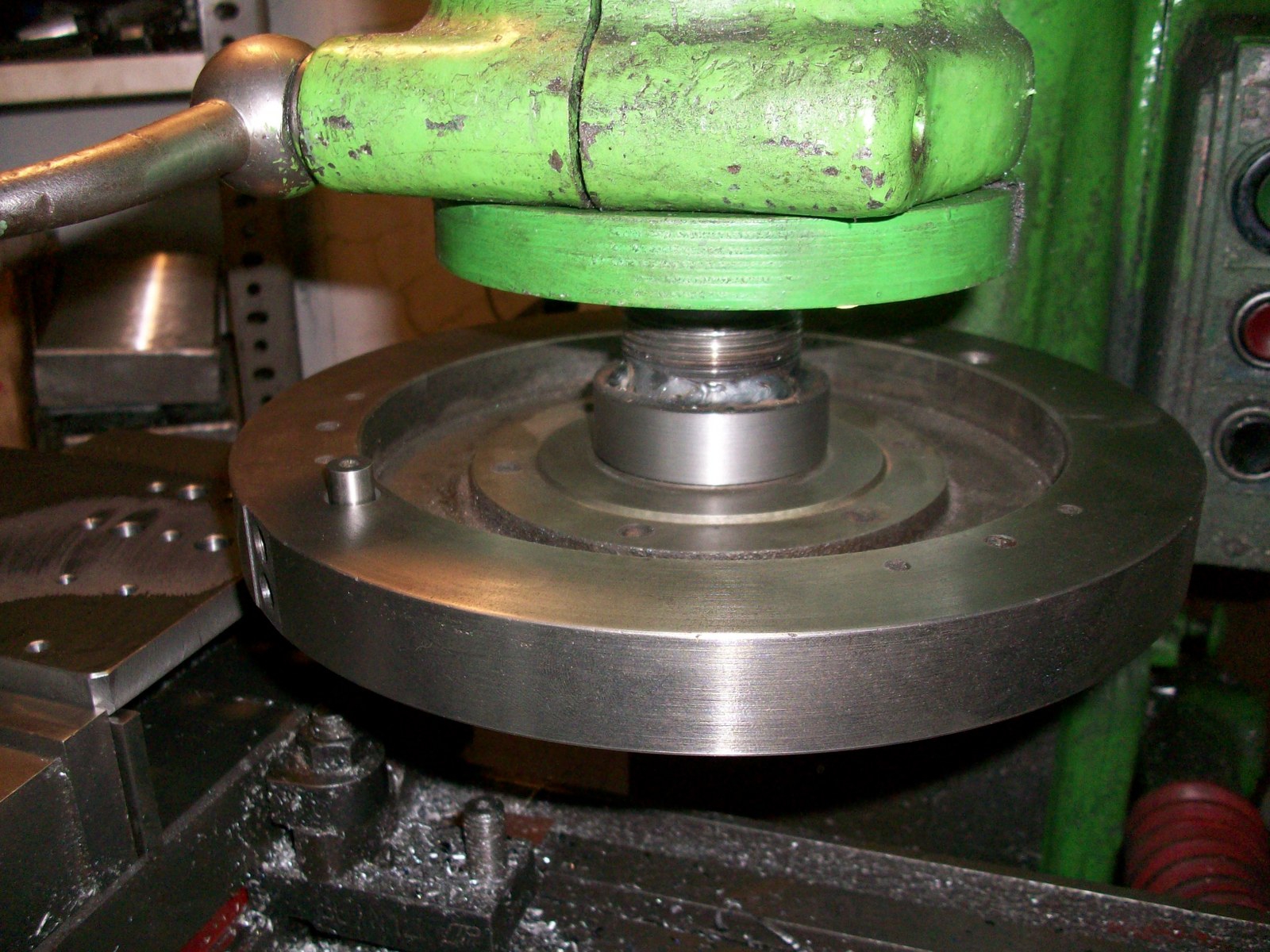
.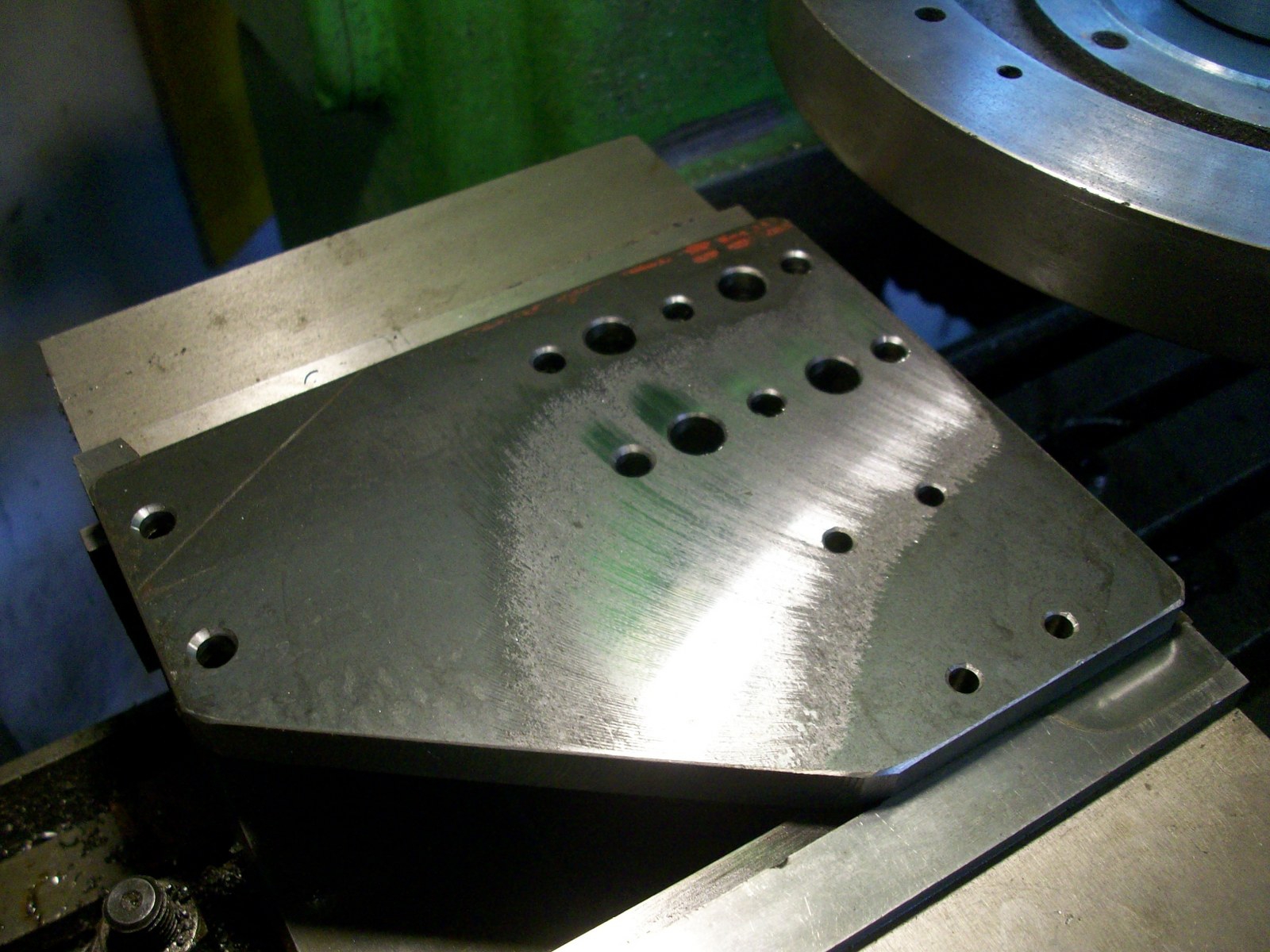
.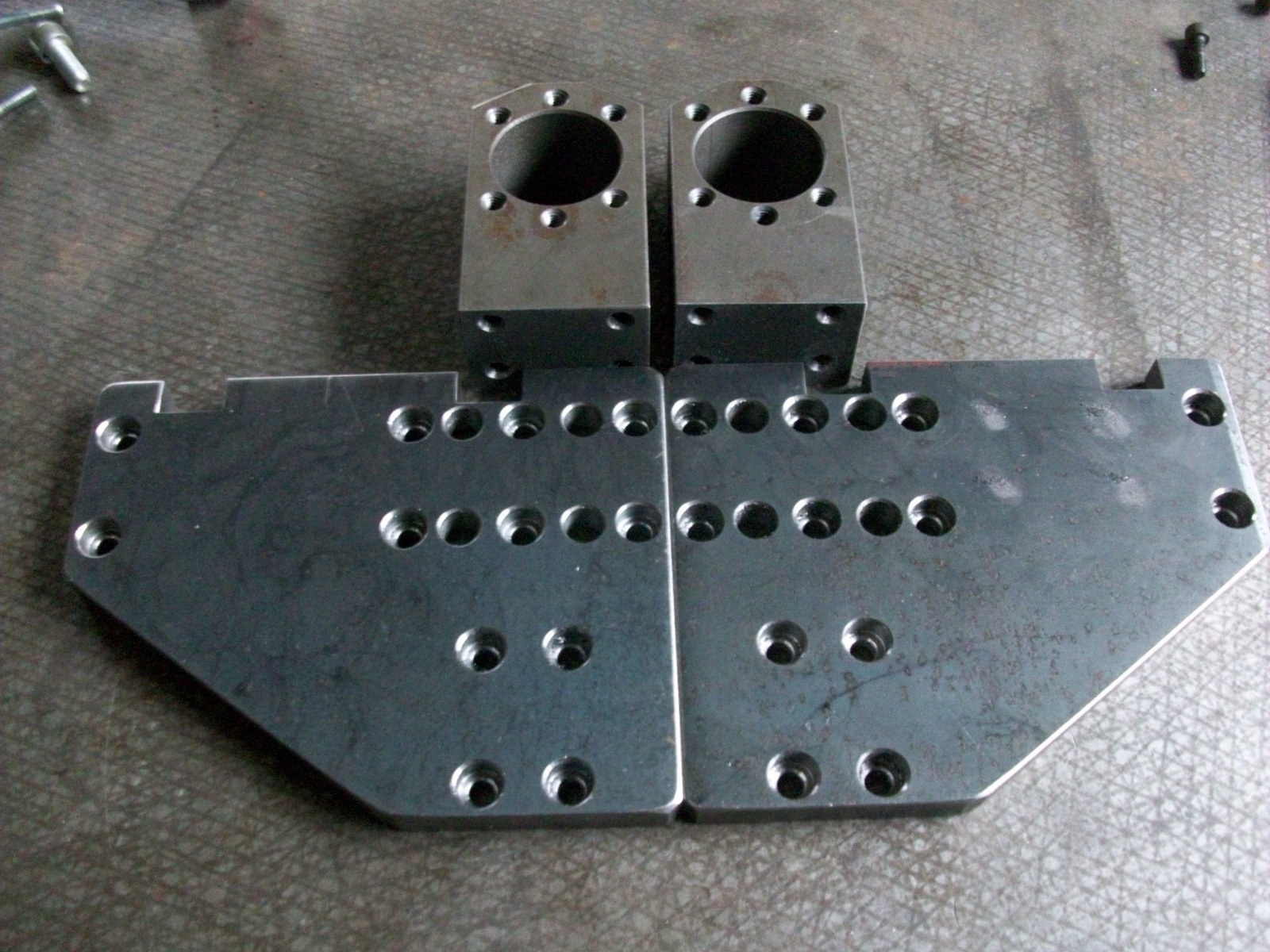
.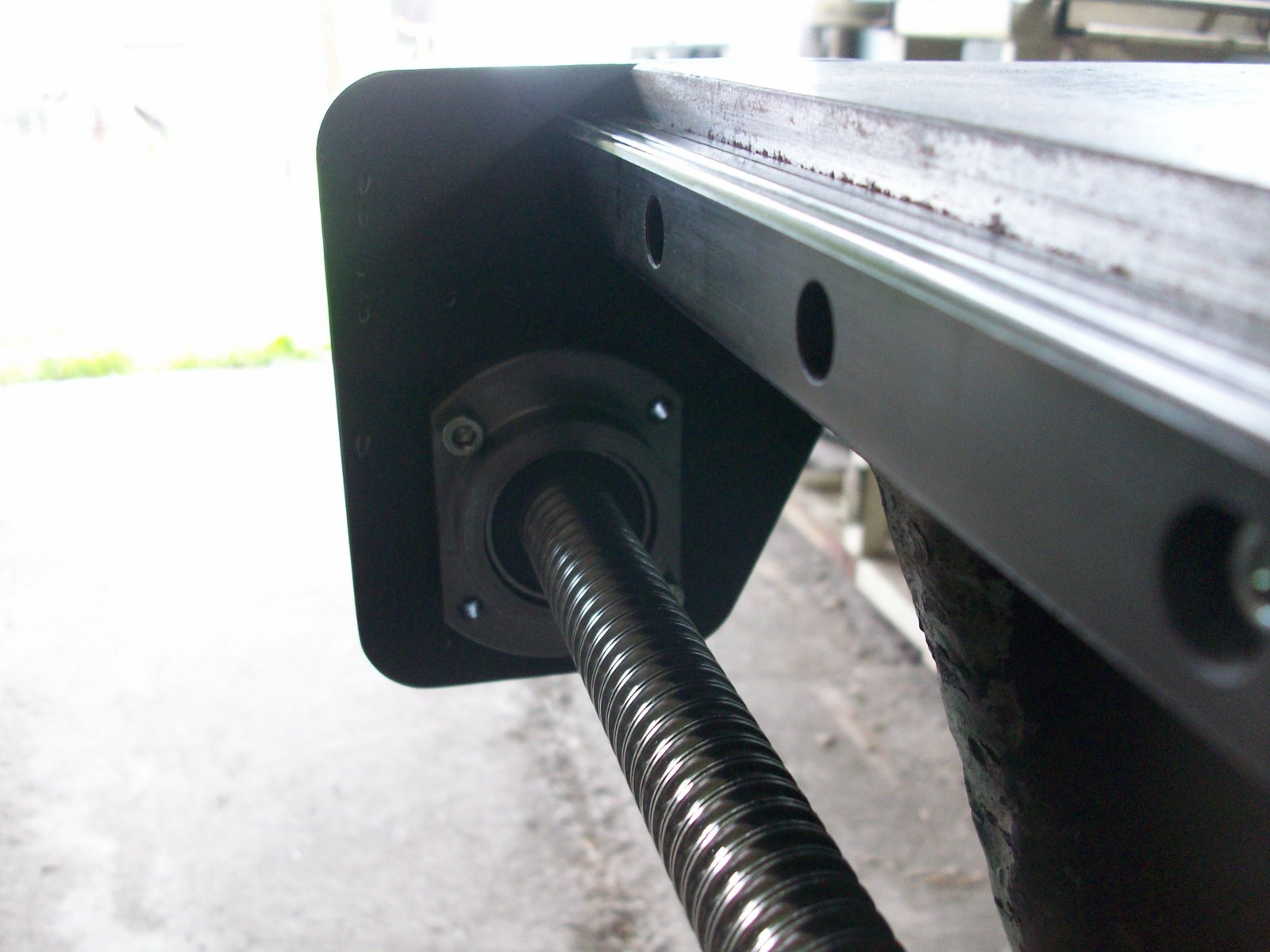
.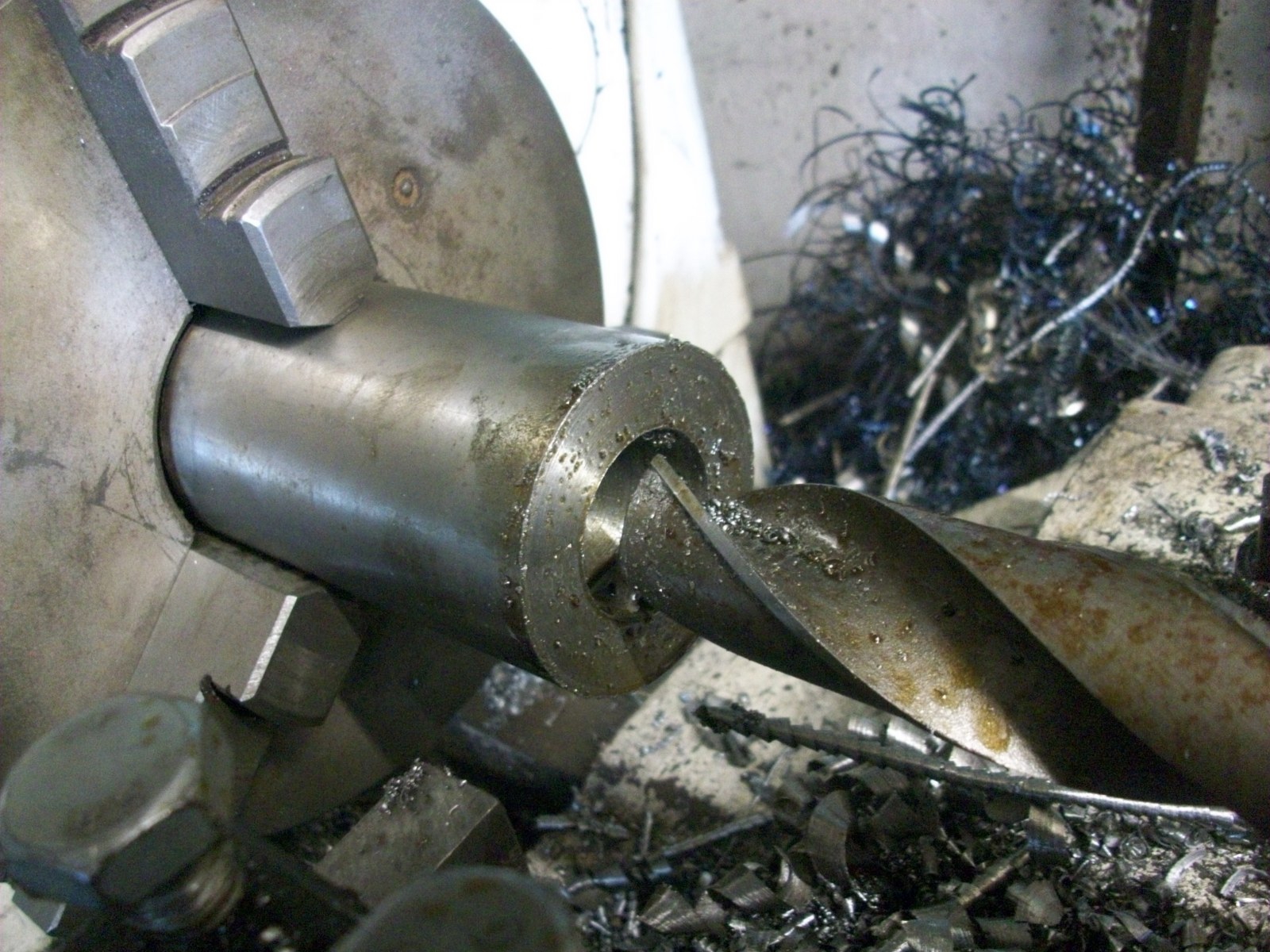
.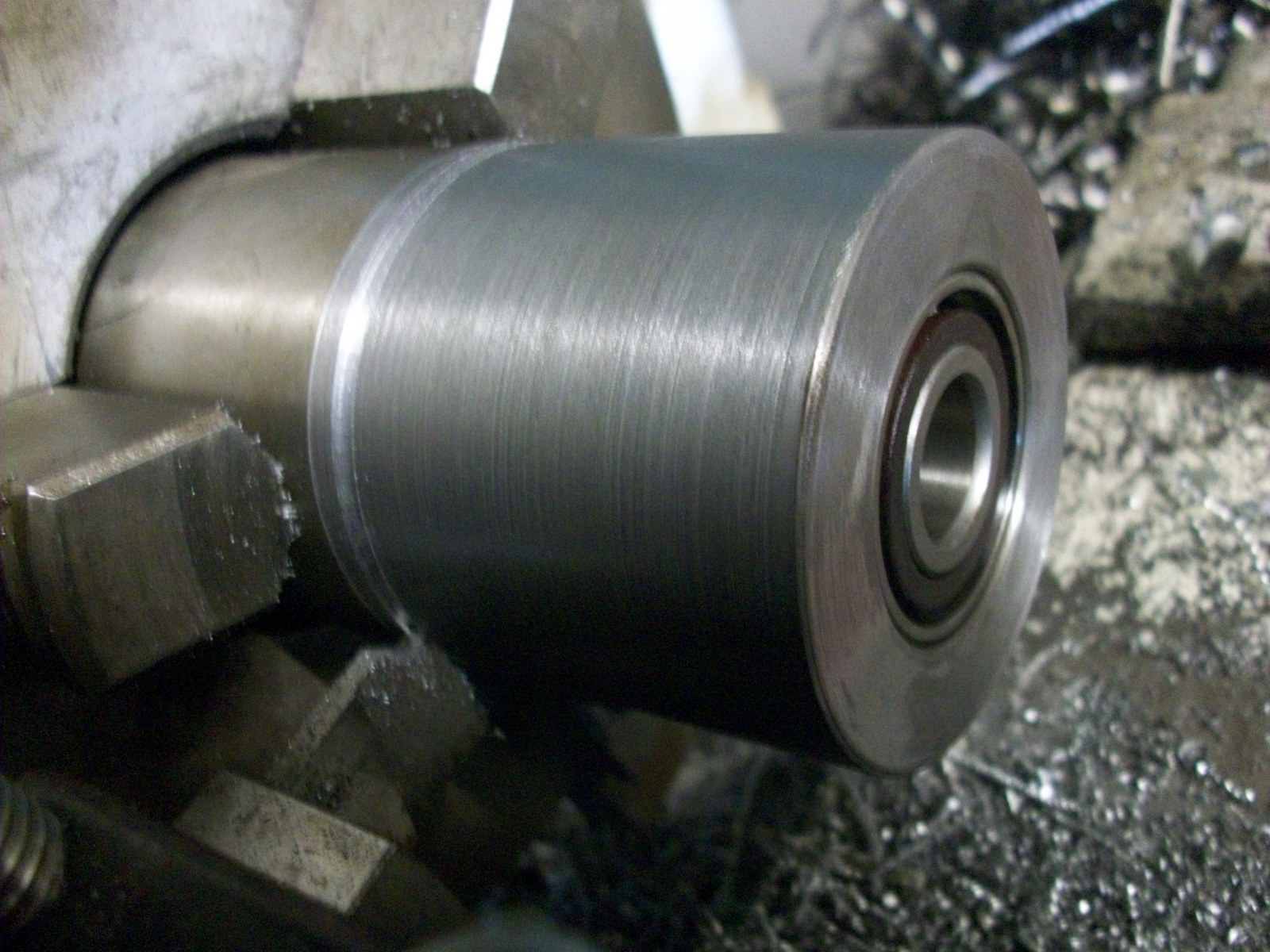
.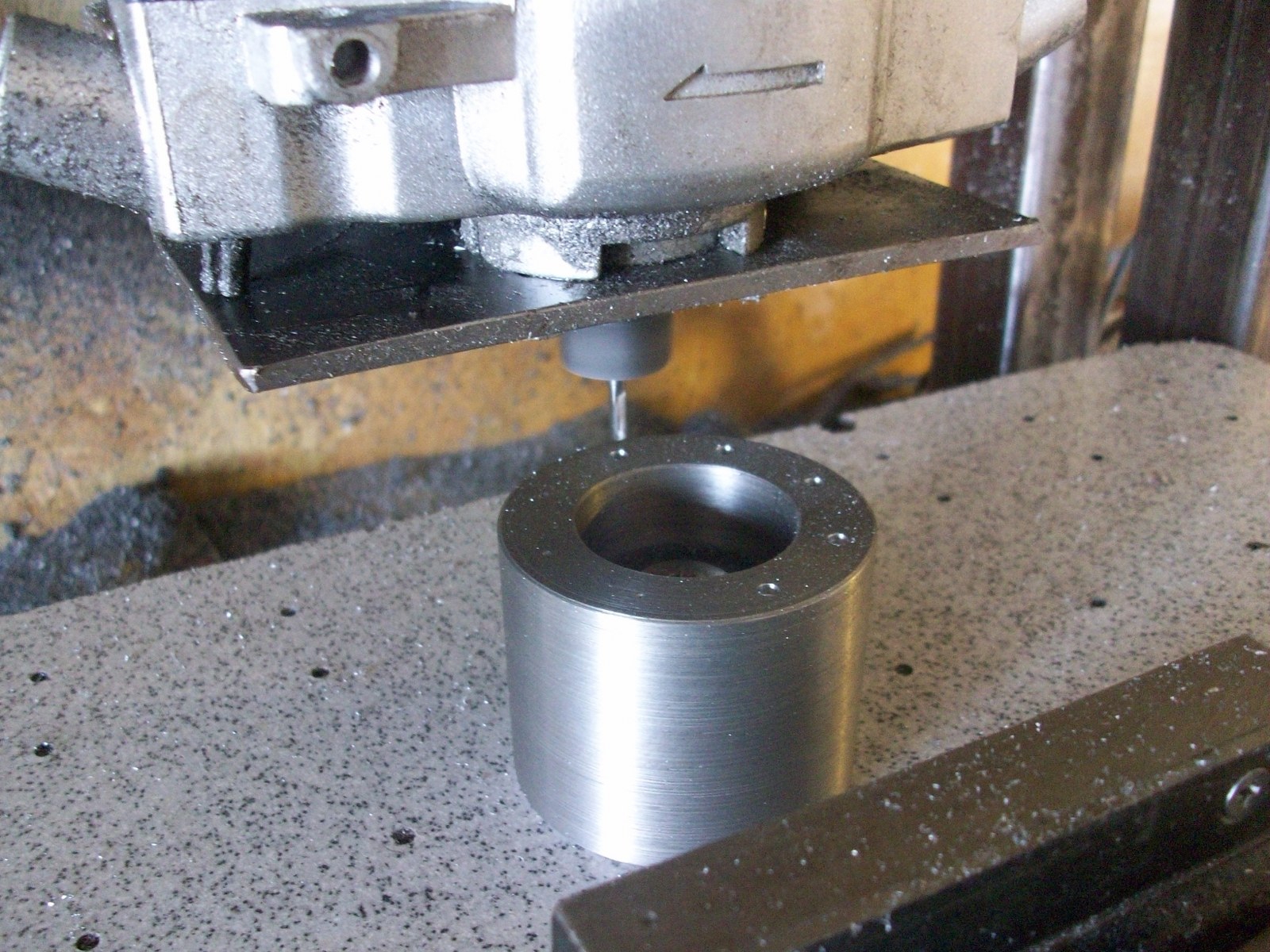
.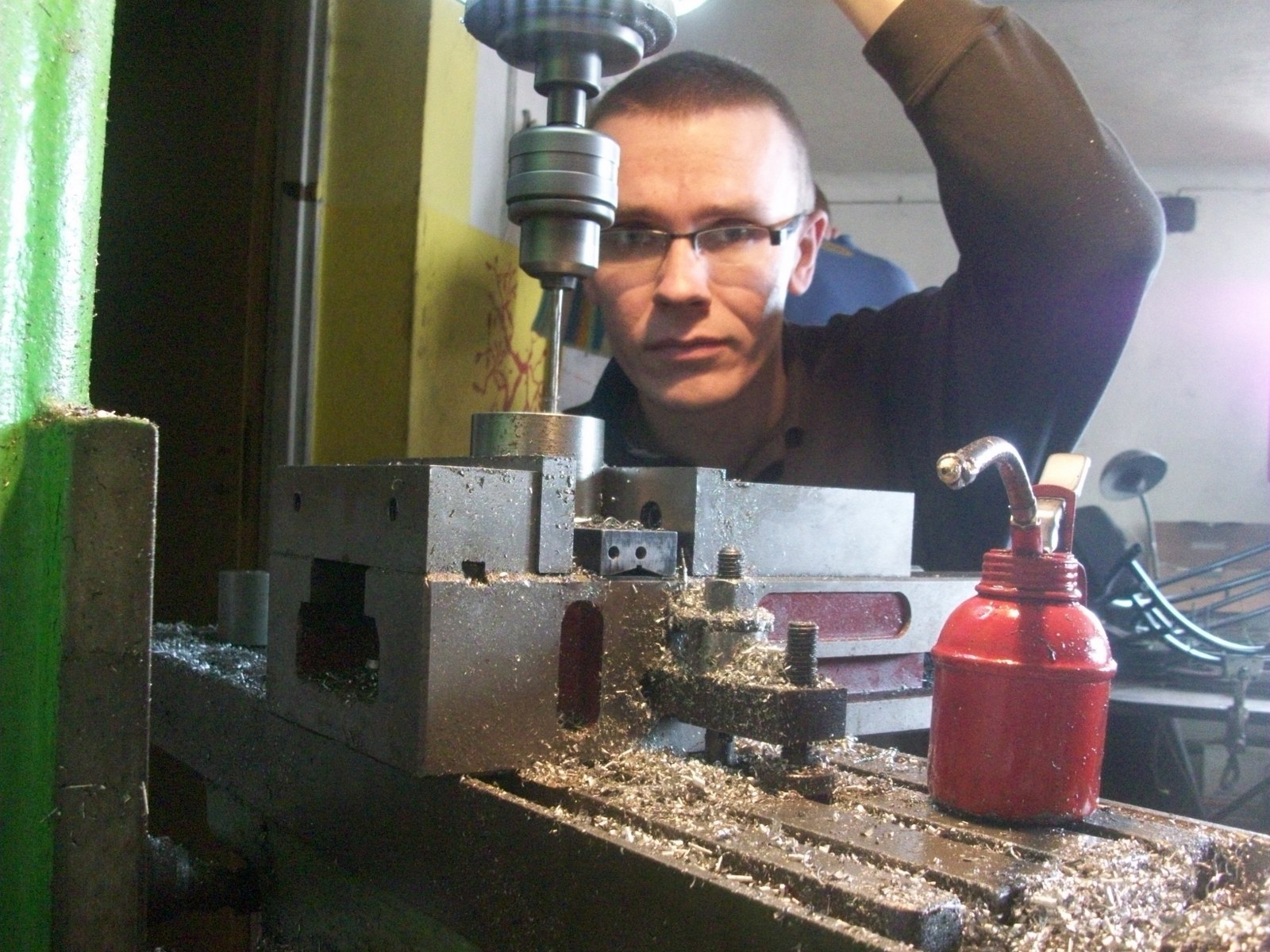
.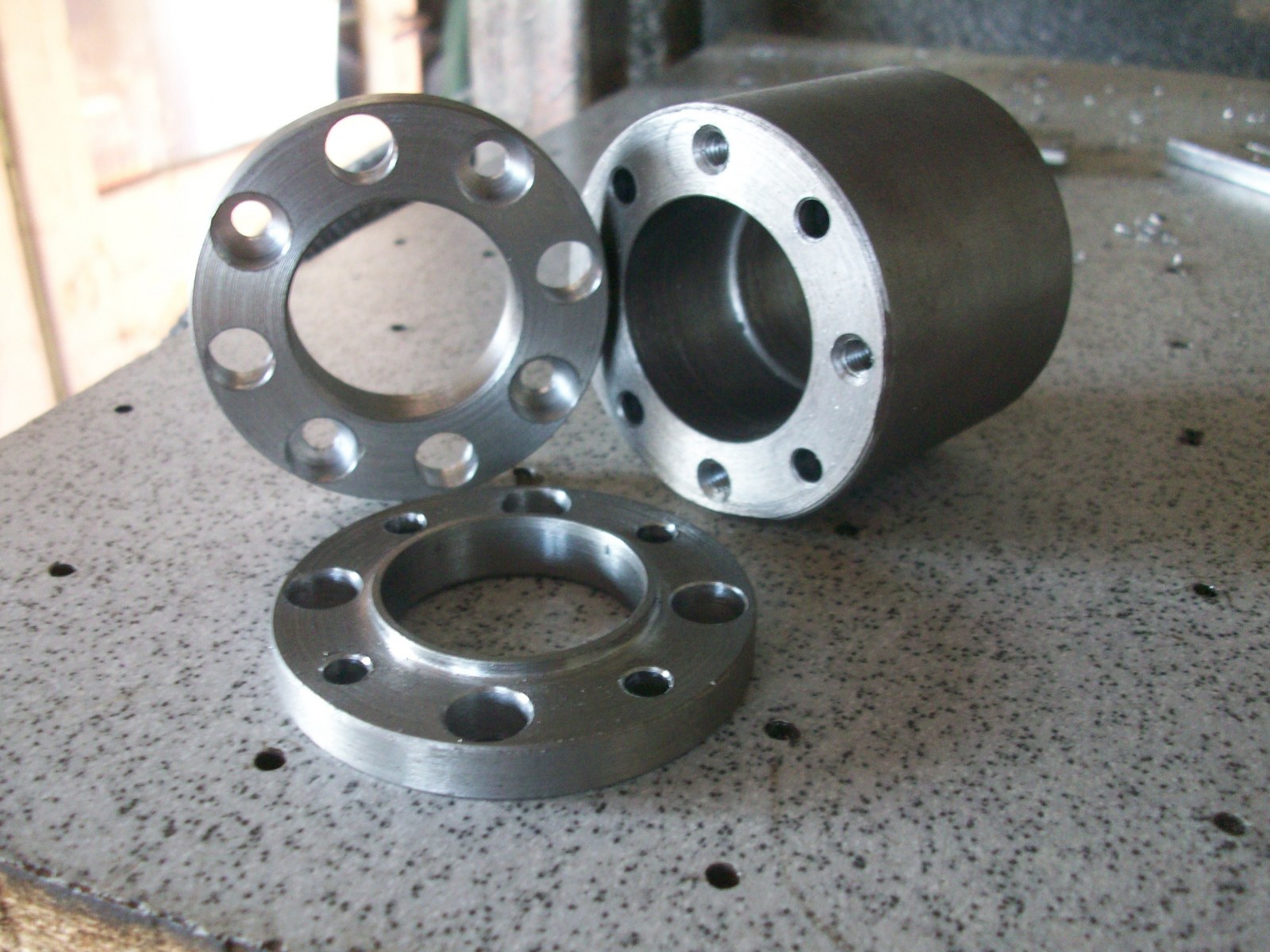
Siedzę w warsztacie po 12 godzin i co z niego wychodzę to wydaje mi się że stoję w miejscu i że w sumie nic nie zrobiłem. Każda pierdoła wymaga tyle czasu, uwagi, wymyślenia i spasowania.... jestem już zmęczony tą budową..... masakra.... żebym wiedział że tyle czasu to będzie trwać to bym se zbudował jakiegoś aluminiaka a nie żeliwnego potwora.
Rzucił się szczerbaty na suchary...
Ale etap ciężkiej budowy mechaniki w sumie zakończony.
Teraz oddam pierdółki do czernienia, zdejmę płytę z ramy, przykryję ją blachami, pospawam i pomaluję ją w jakiś tam kolor. Potem połączę ramę ze stołem i składam maszynę na gotowo.
Zacznie się puszczanie kabelków, światełek i innych dzwoneczków.....
.....tylko czy ja dożyję ......
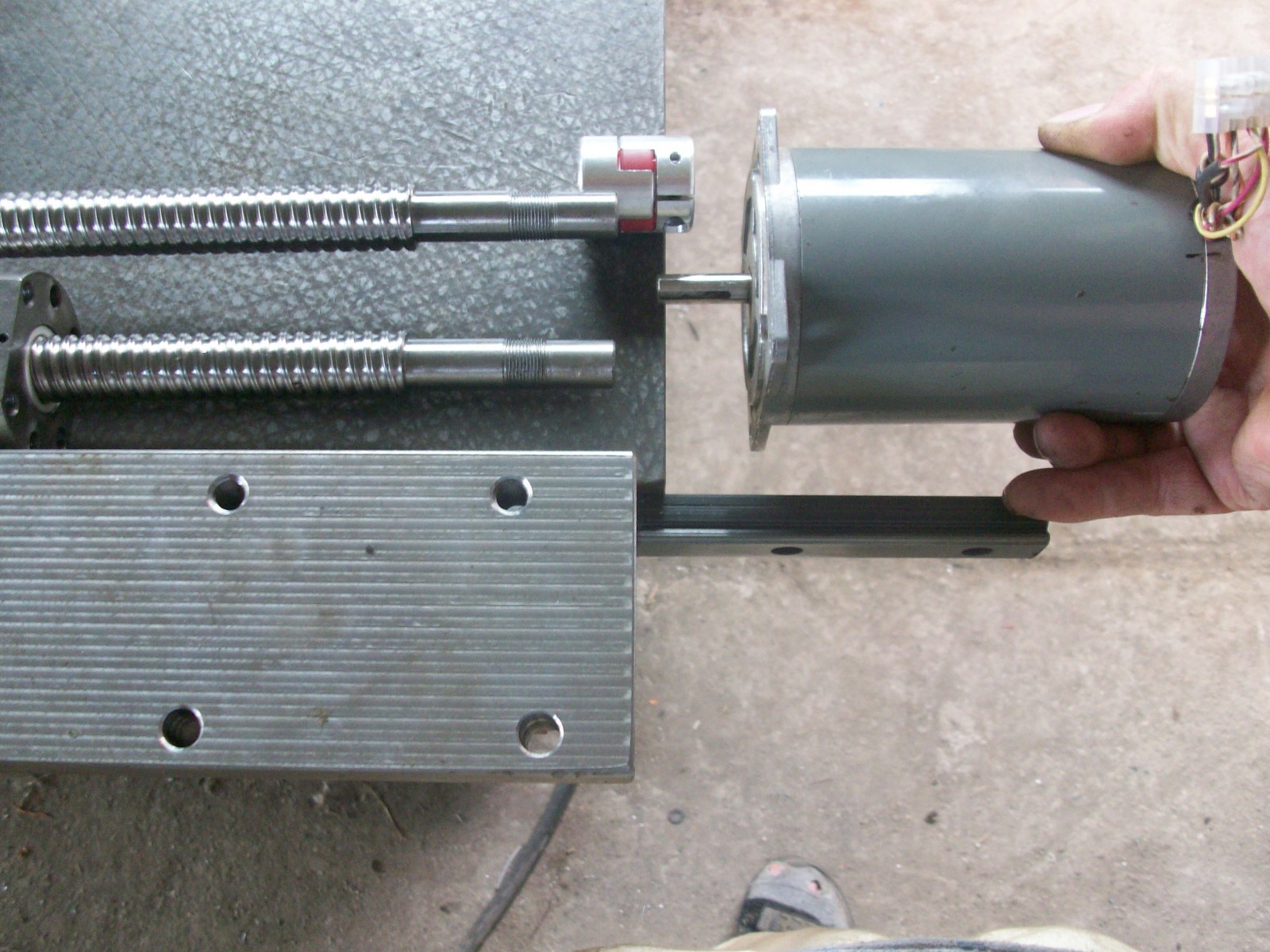
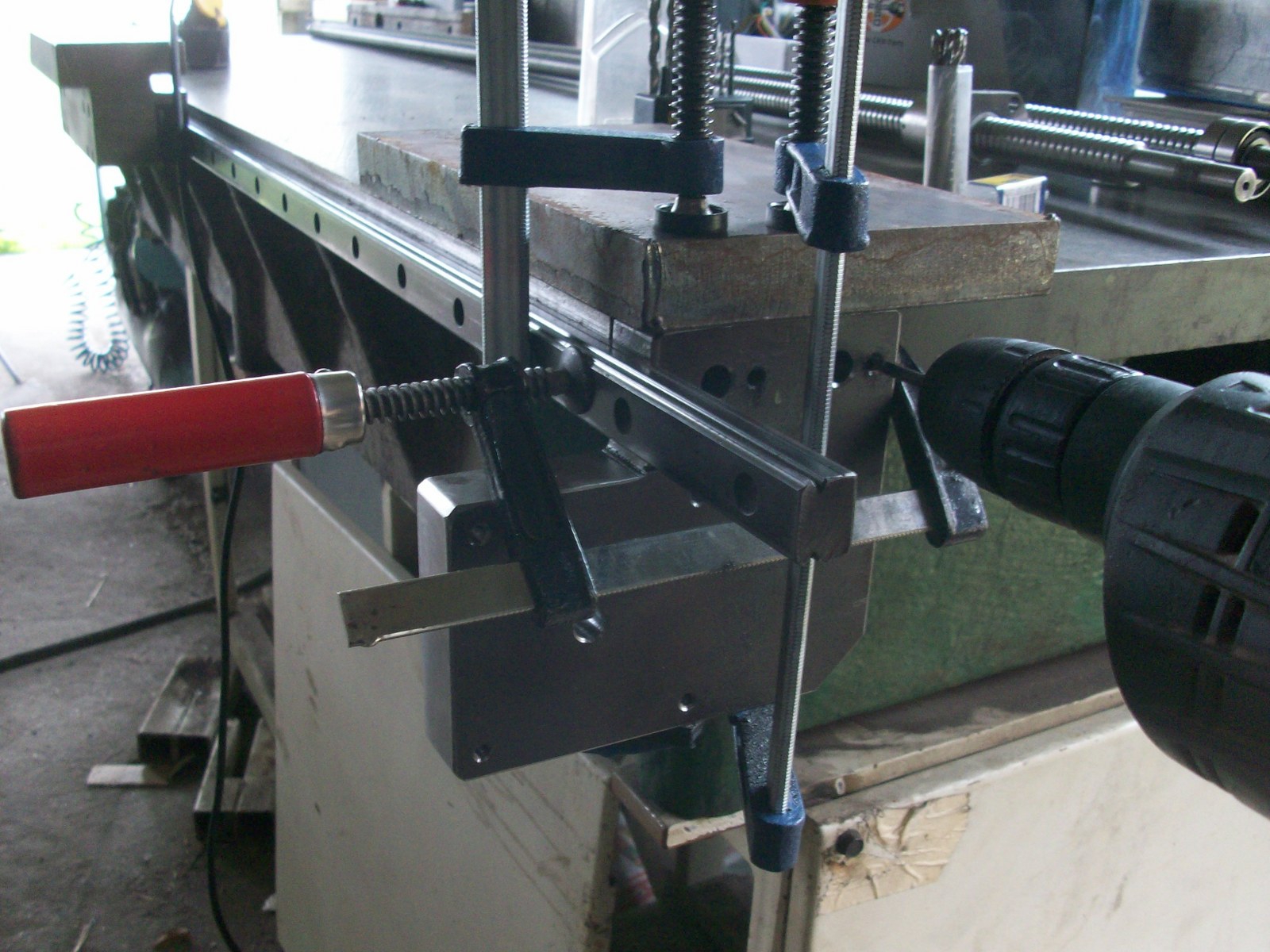
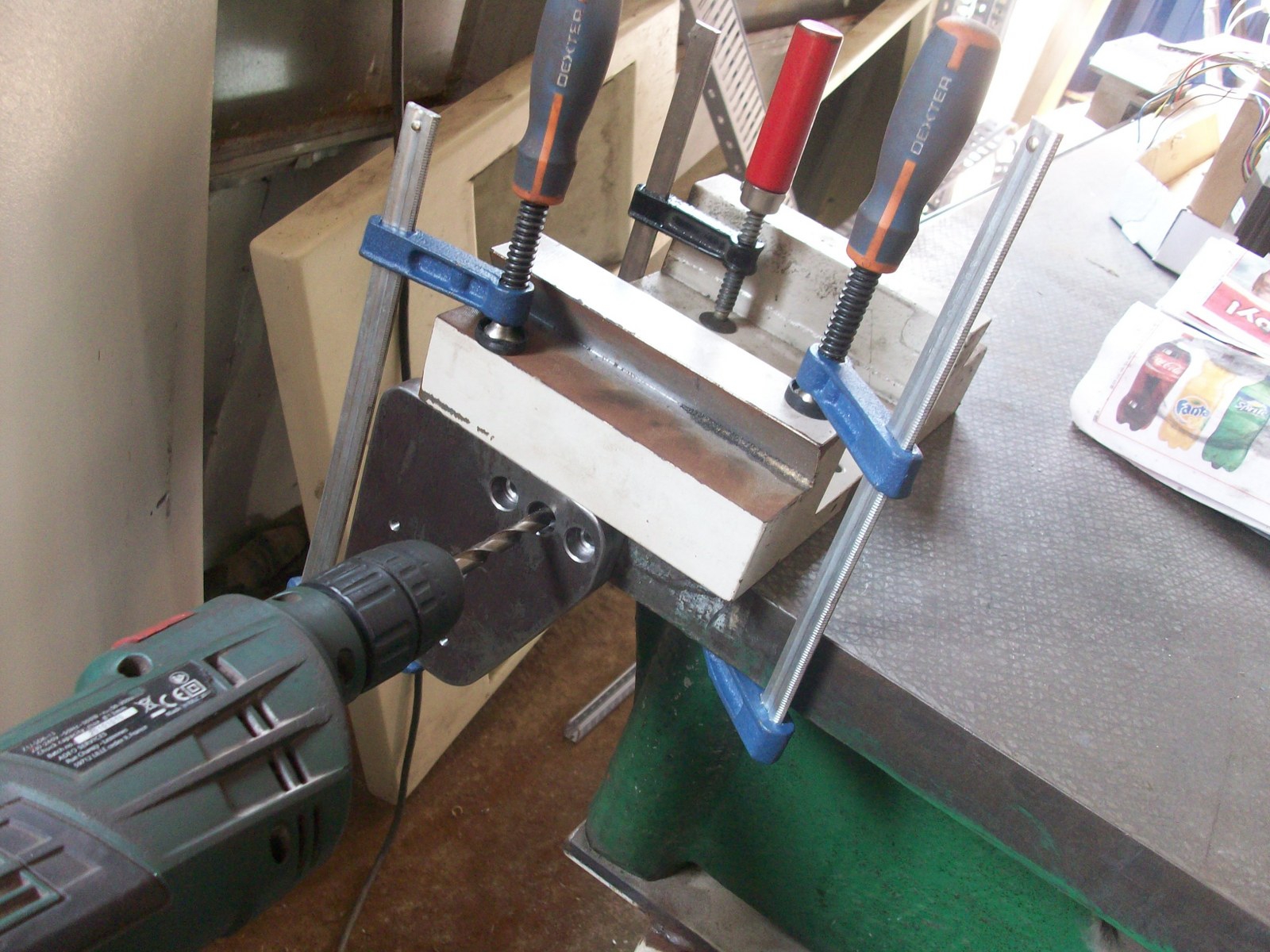
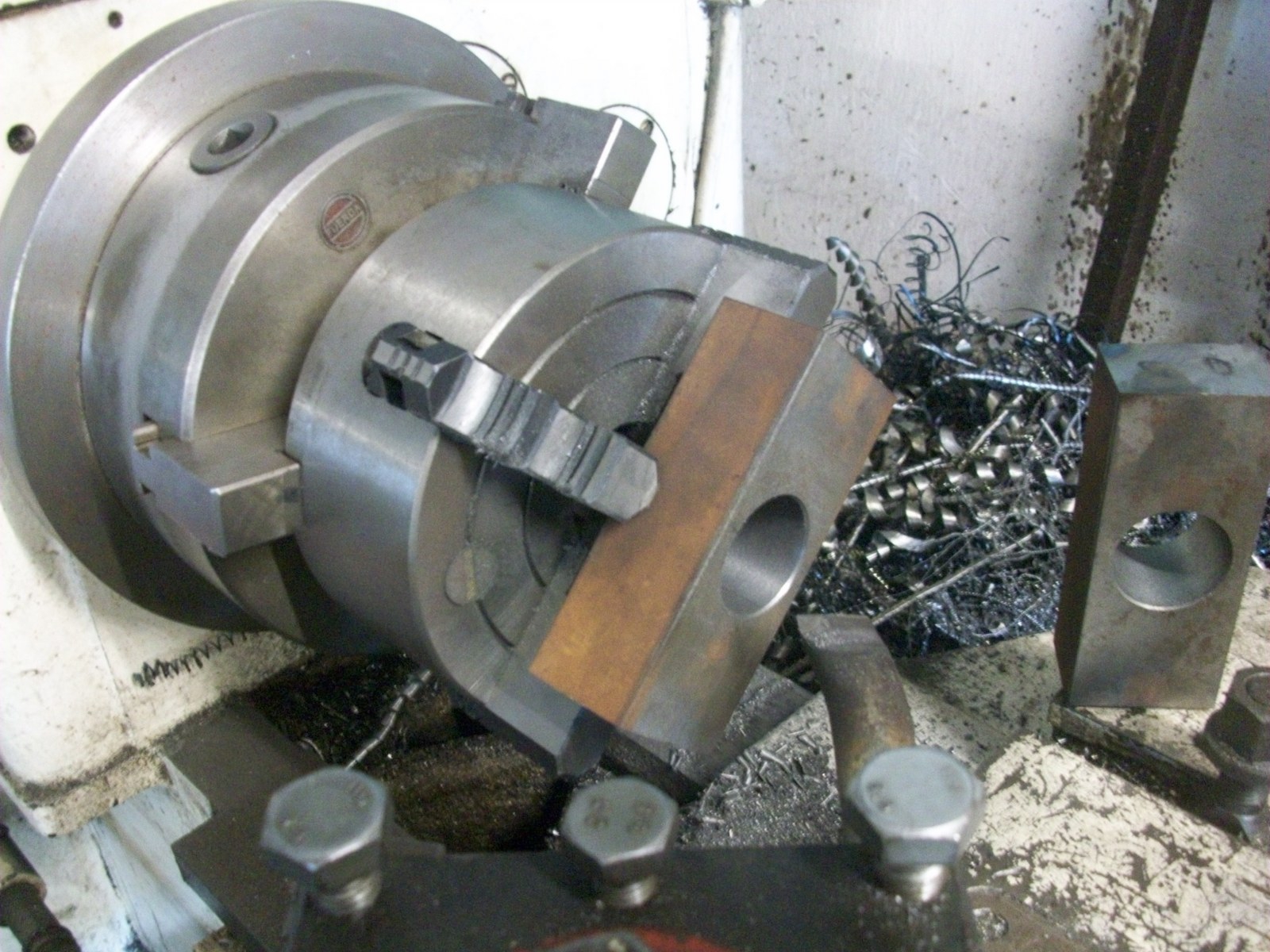
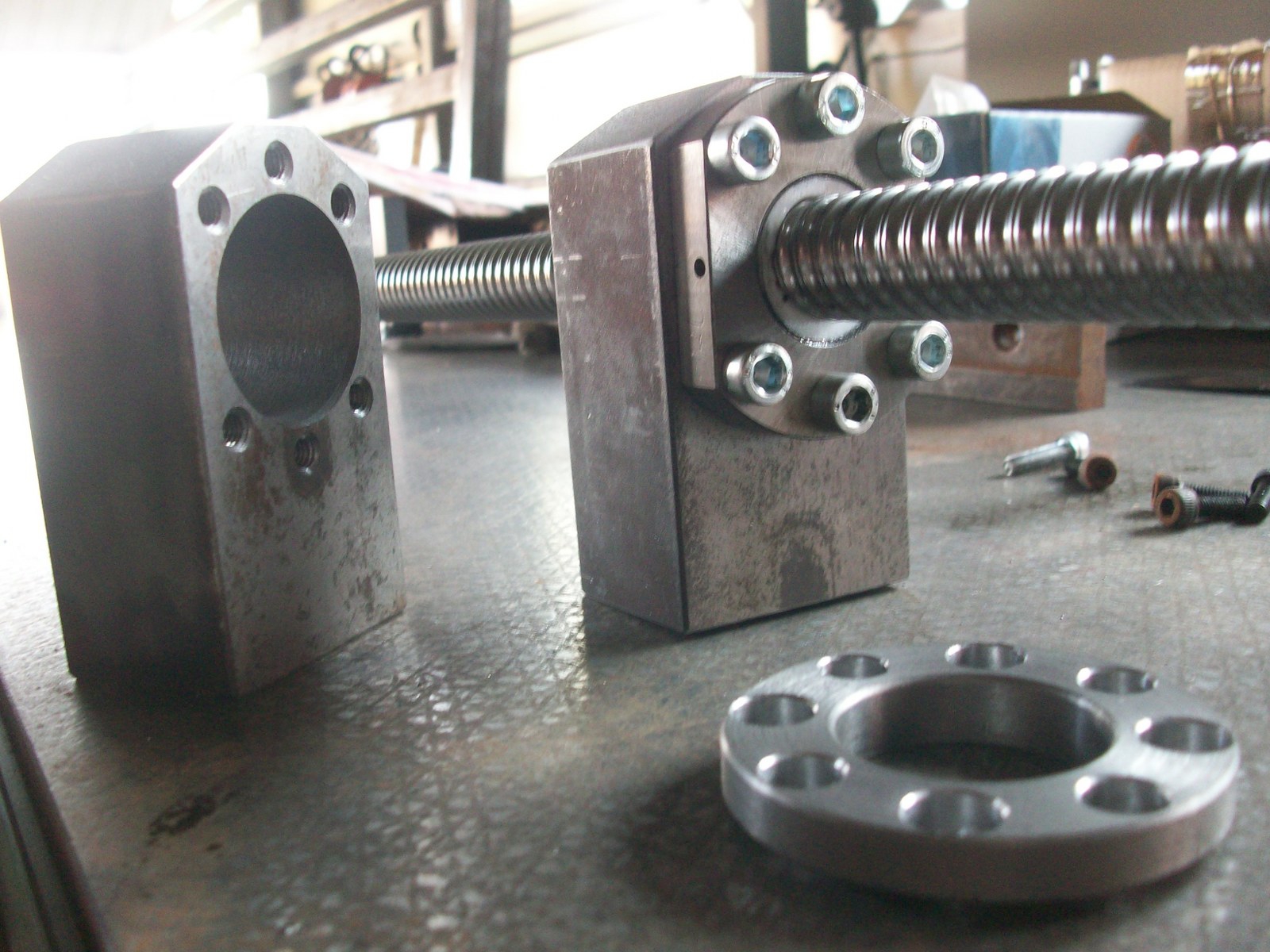
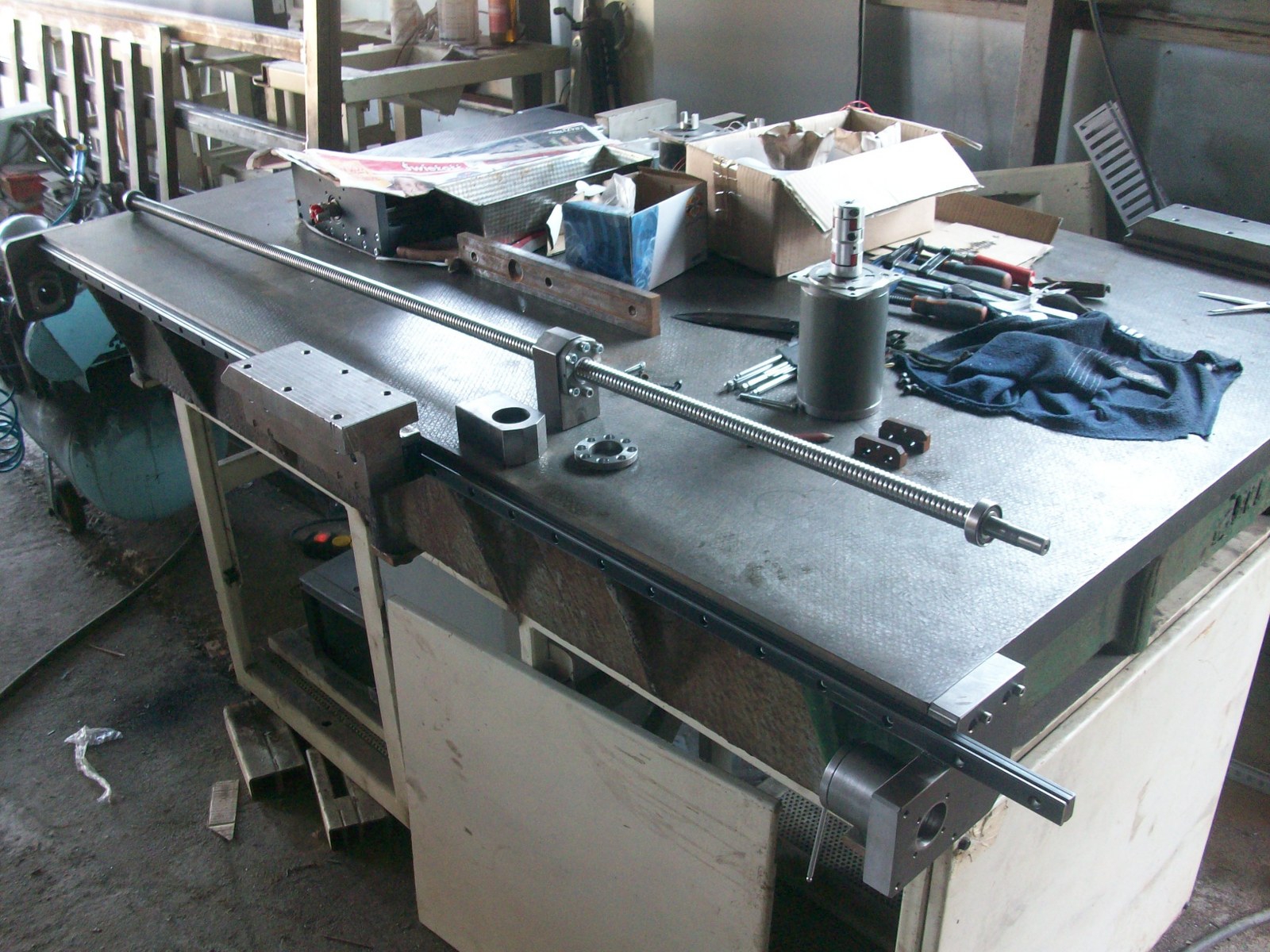
Pozazdrościłem wujowi Kamarowi Flycuttera i w końcu zrobiłem i dla siebie. Stara oprawka na tulejki z przyspawanym kawałkiem nawierconej i nagwintowanej stali, stare koło zamachowe z malucha i 3 godzinki pracy i oto jest. W stali robi to średnio ale aluminium gładzi aż miło.
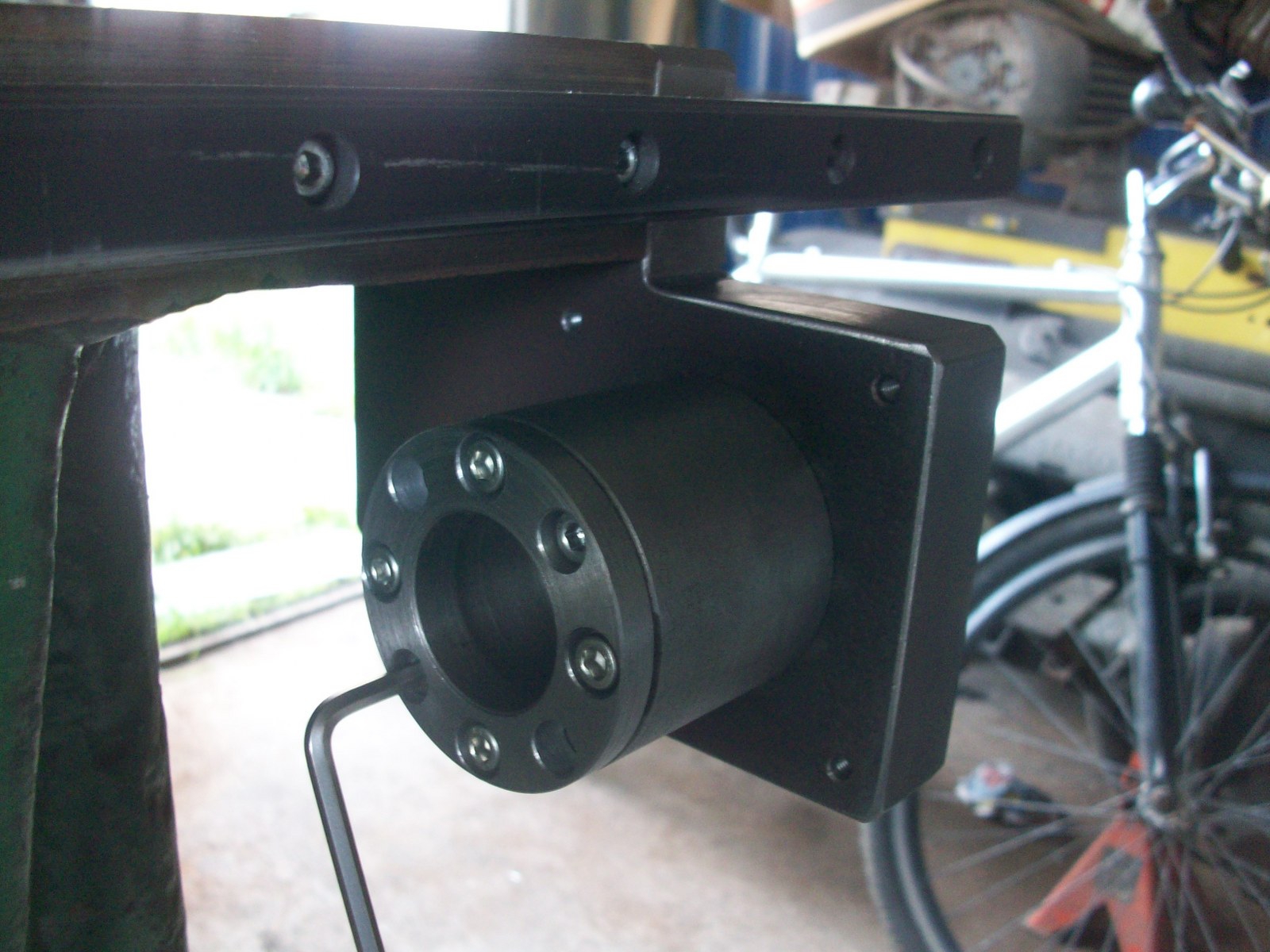
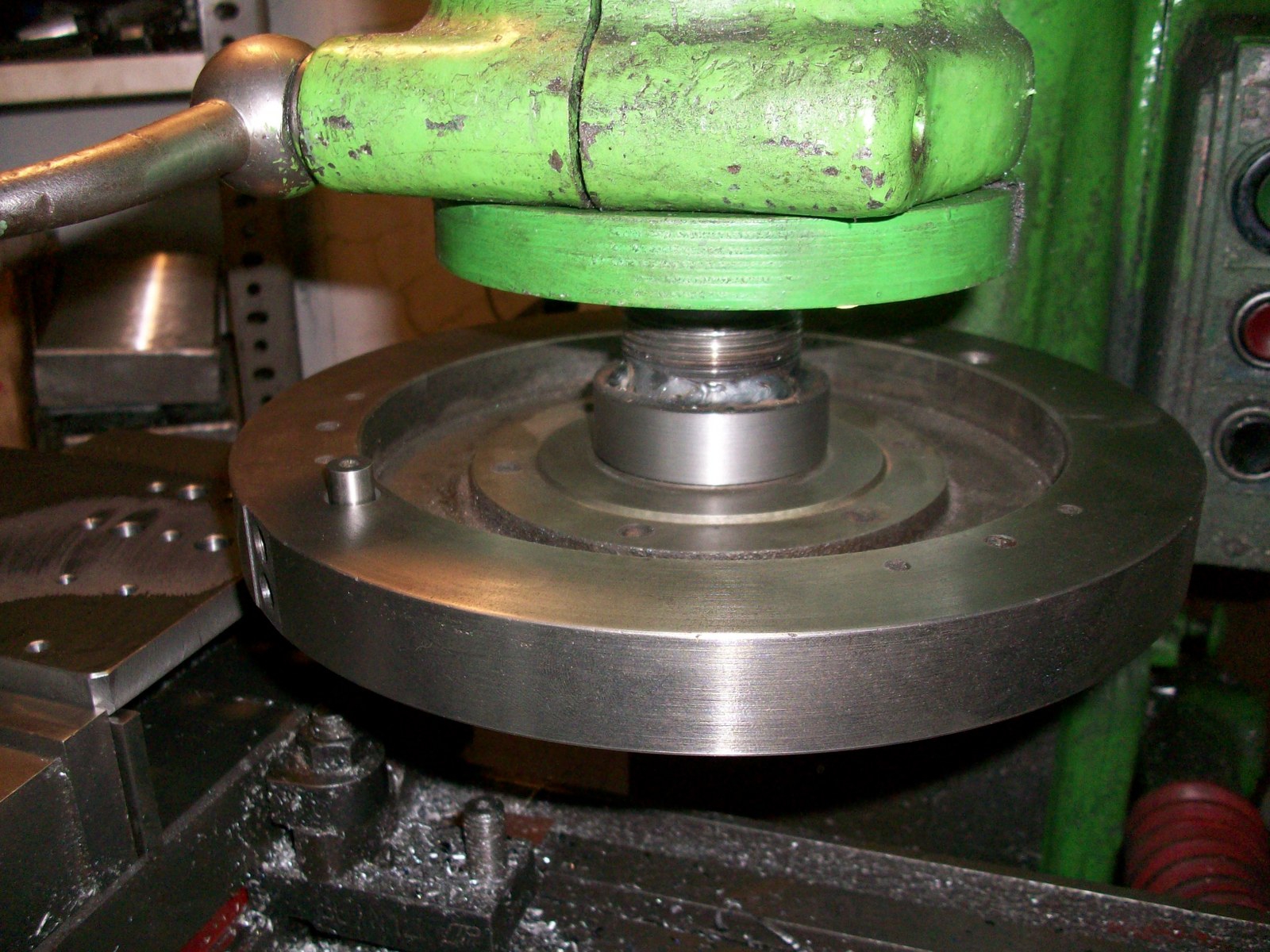
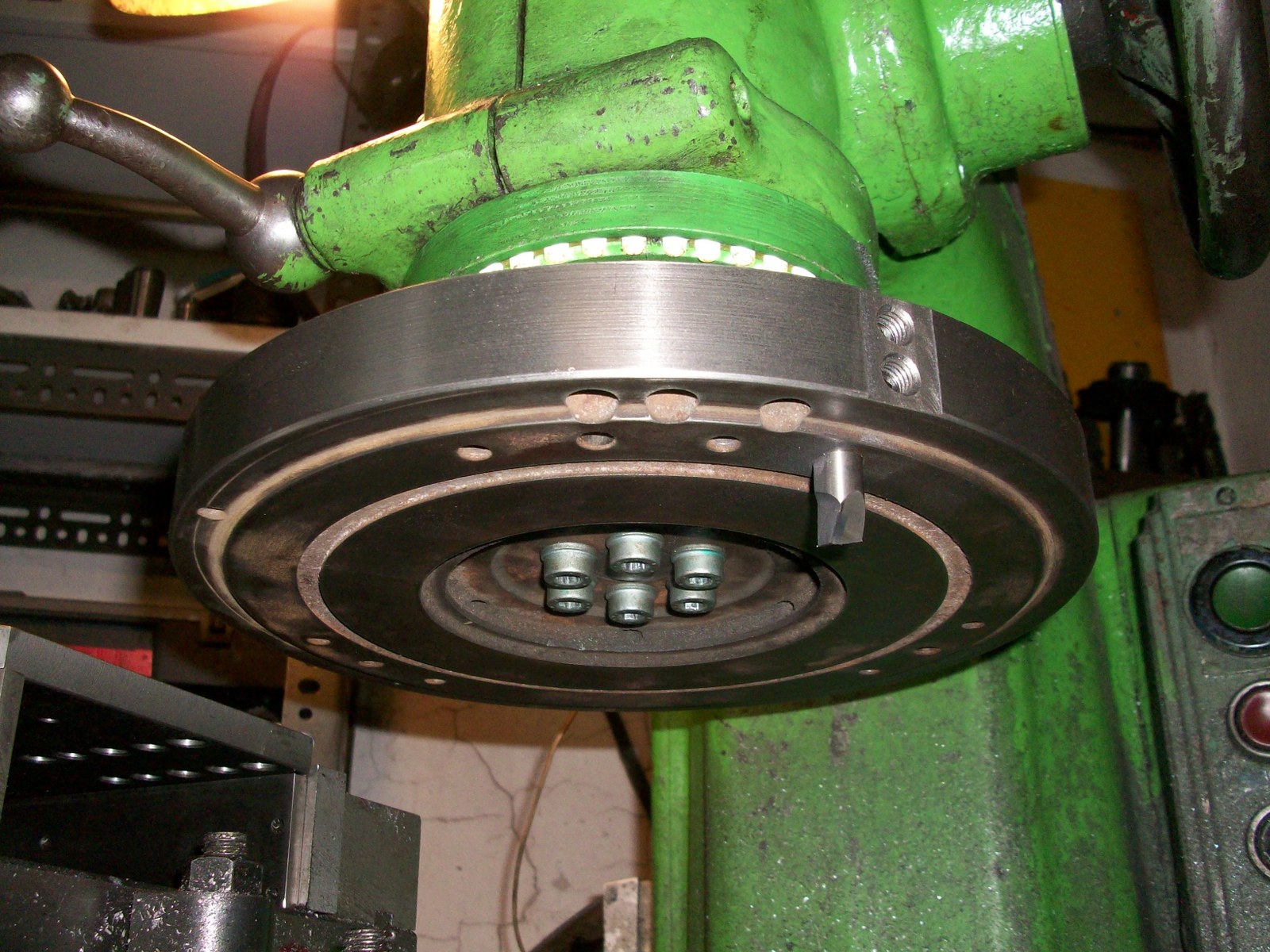
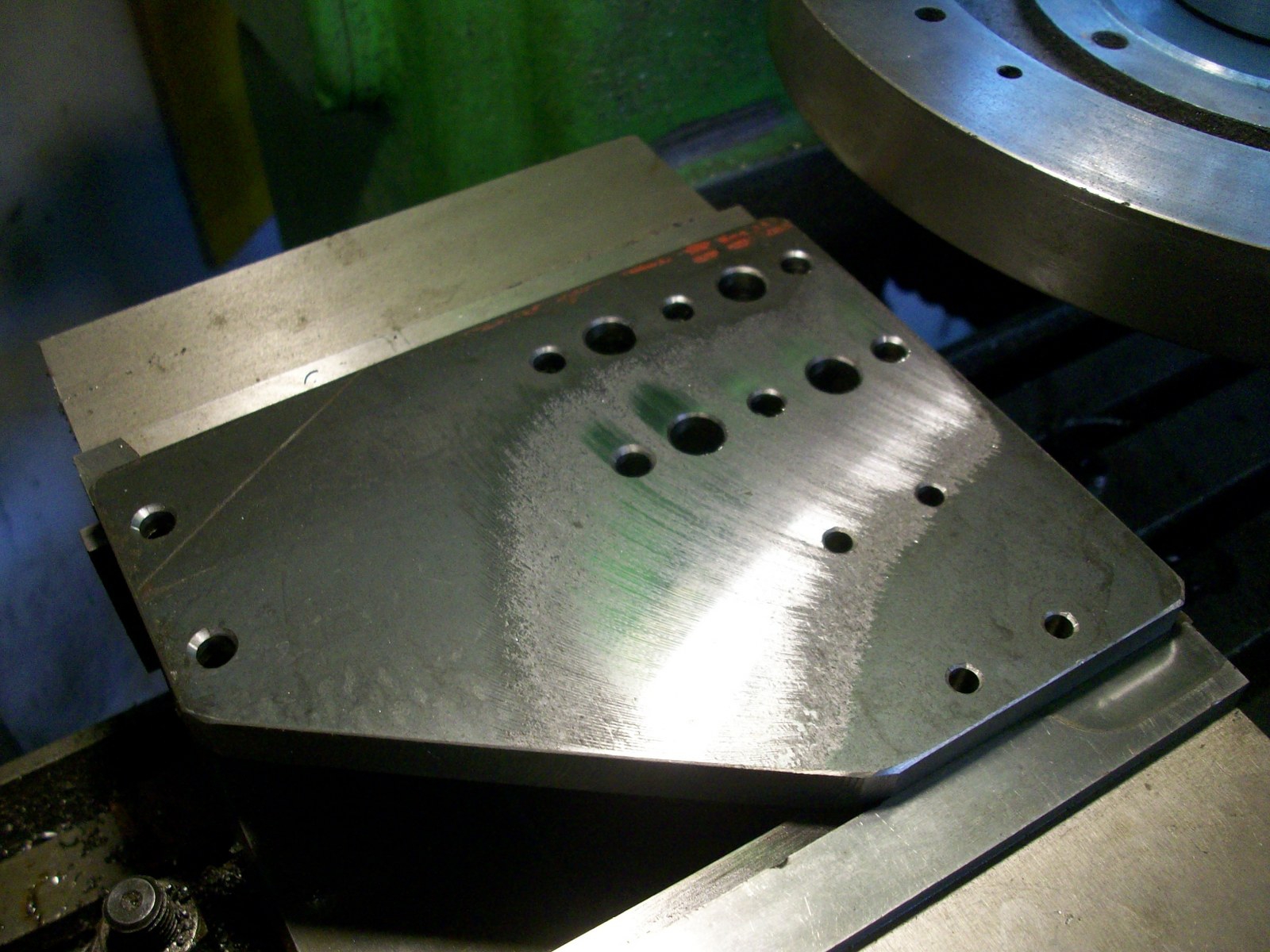
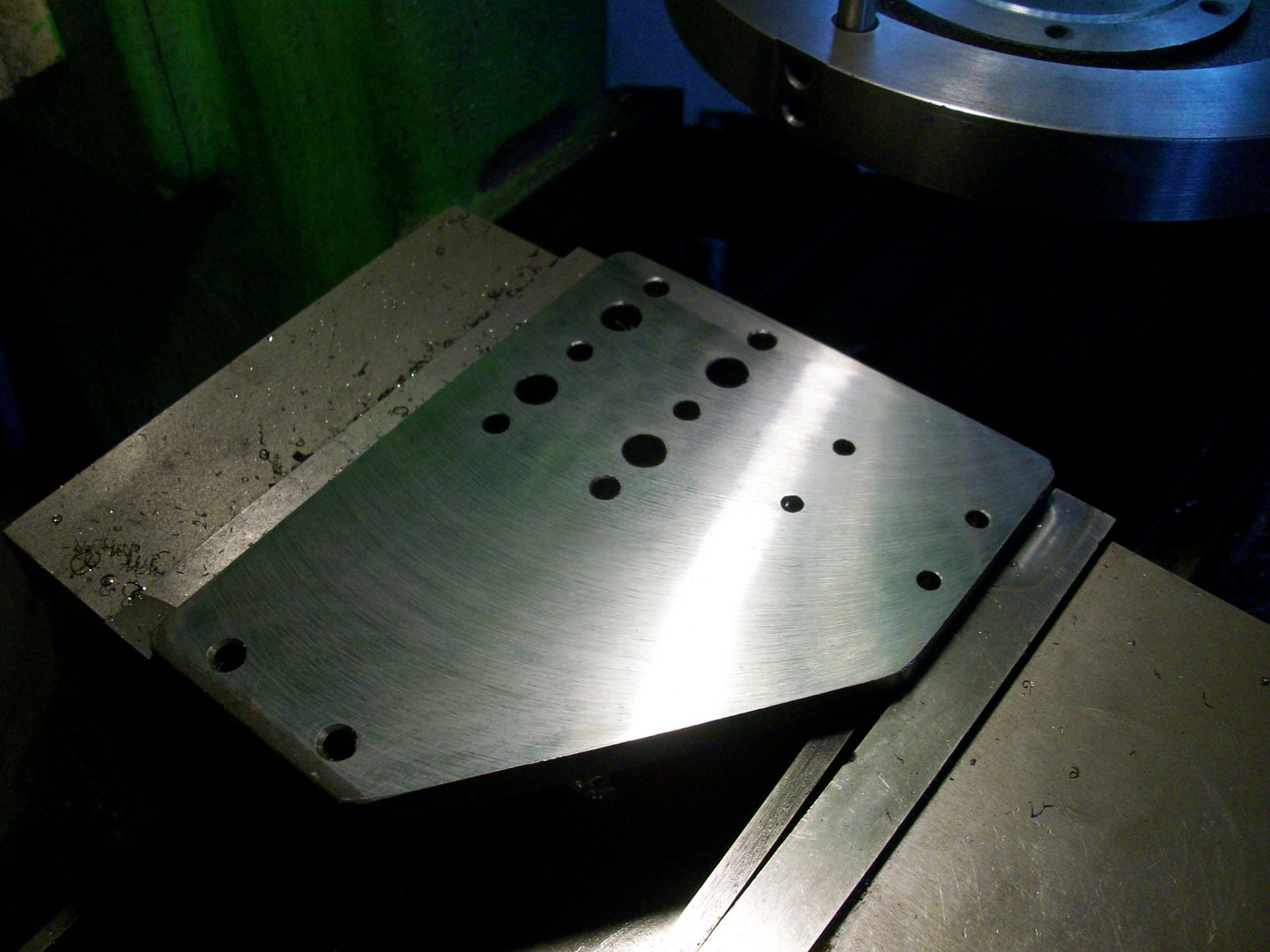
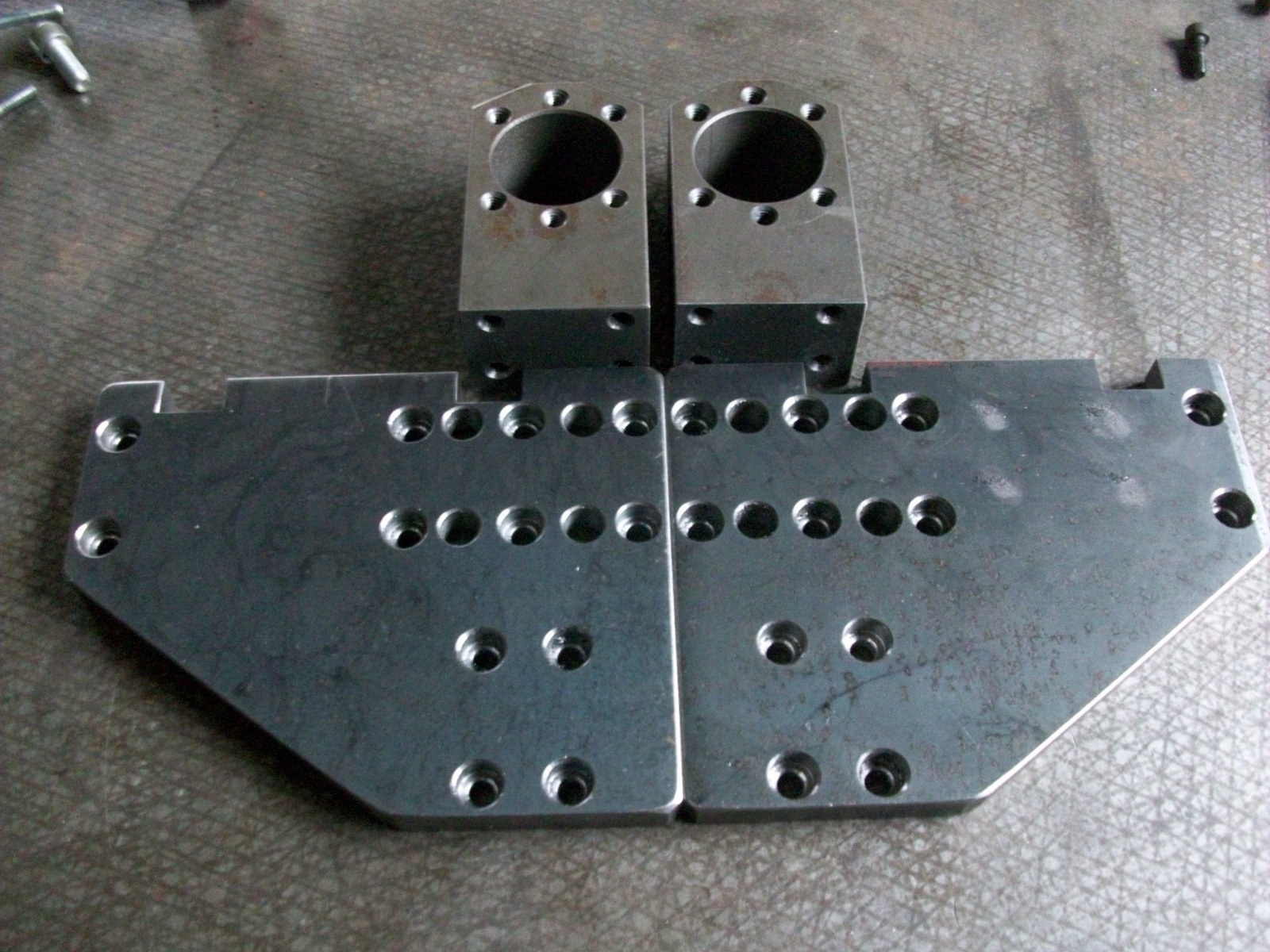
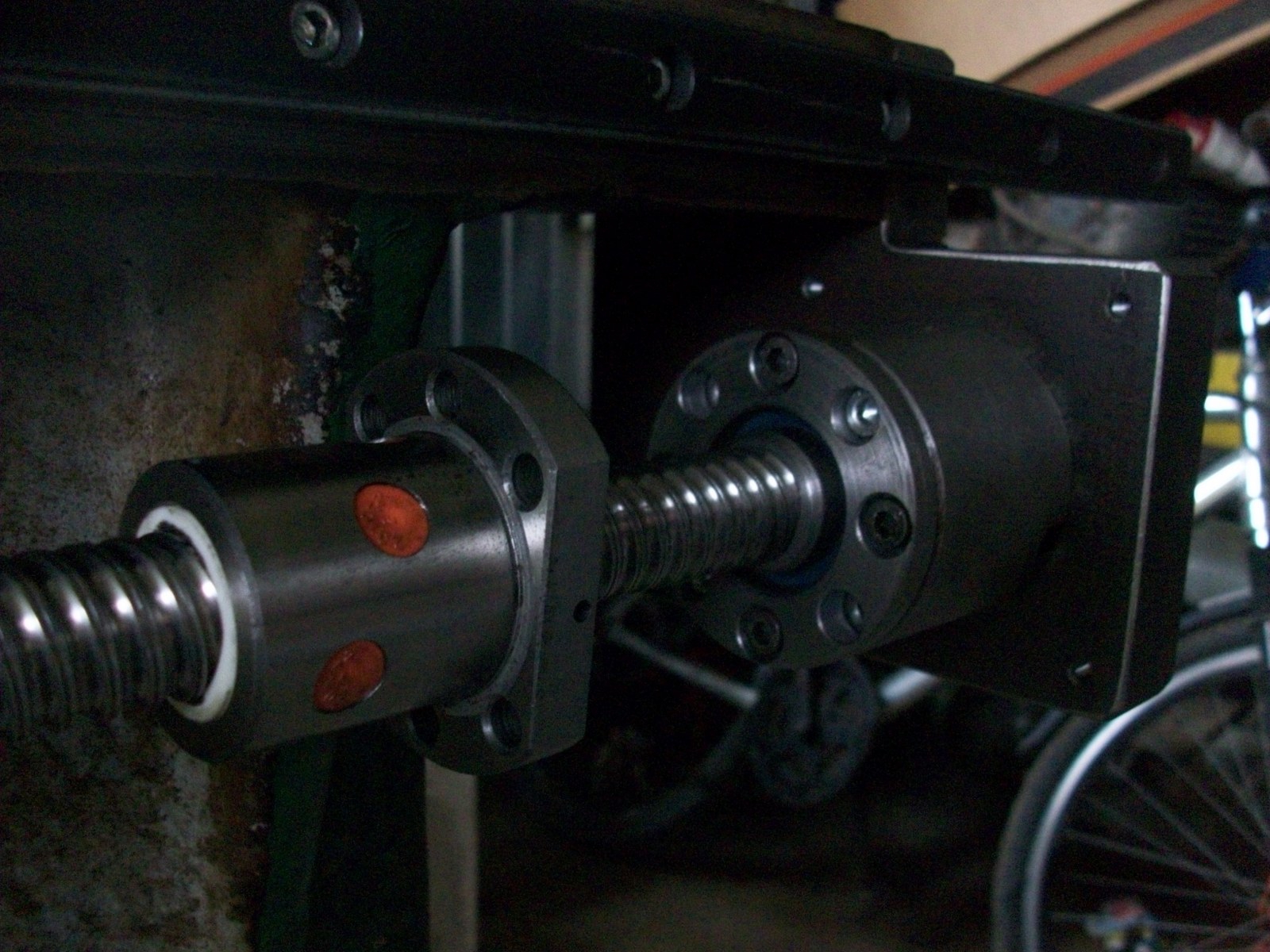
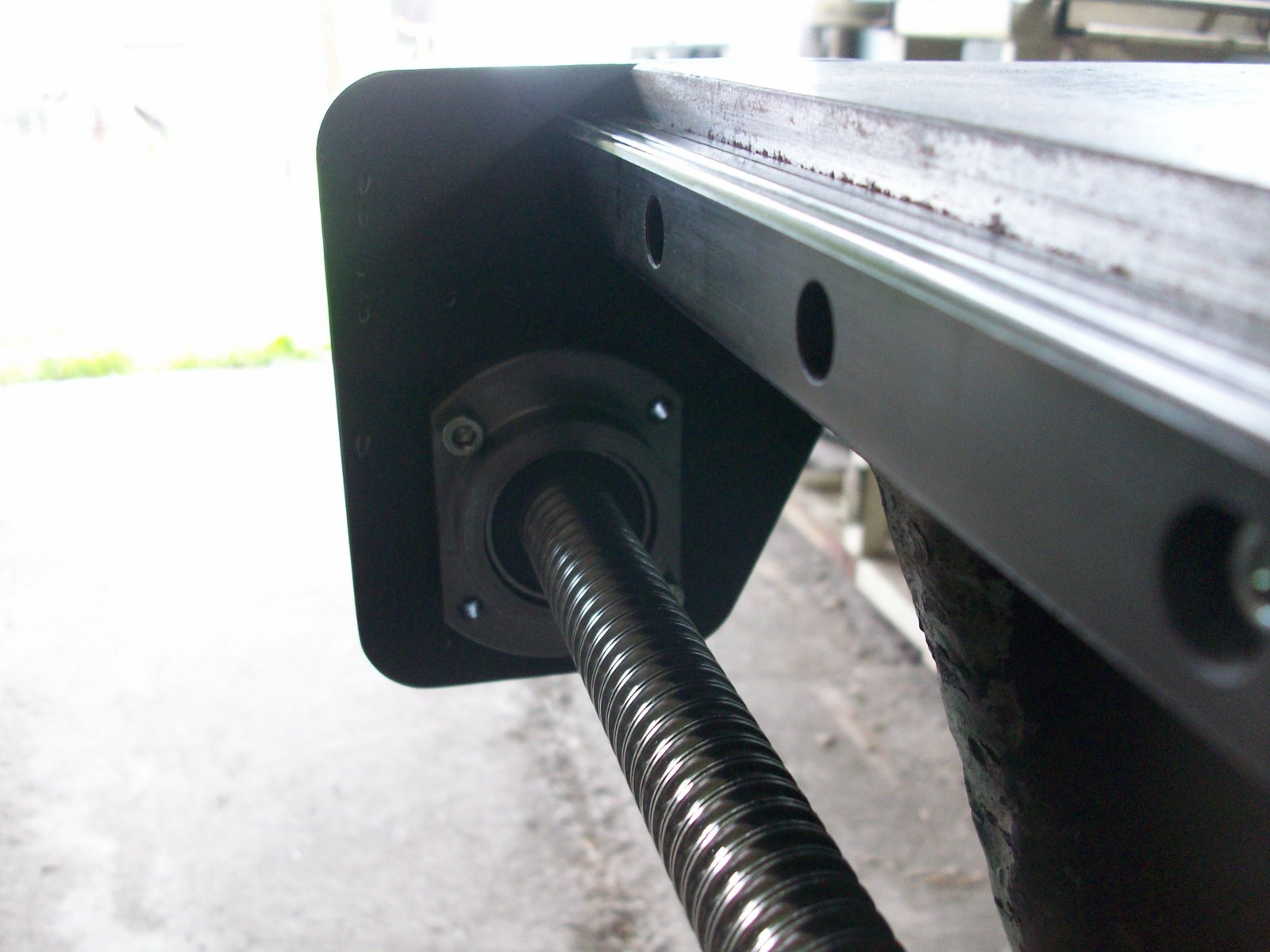
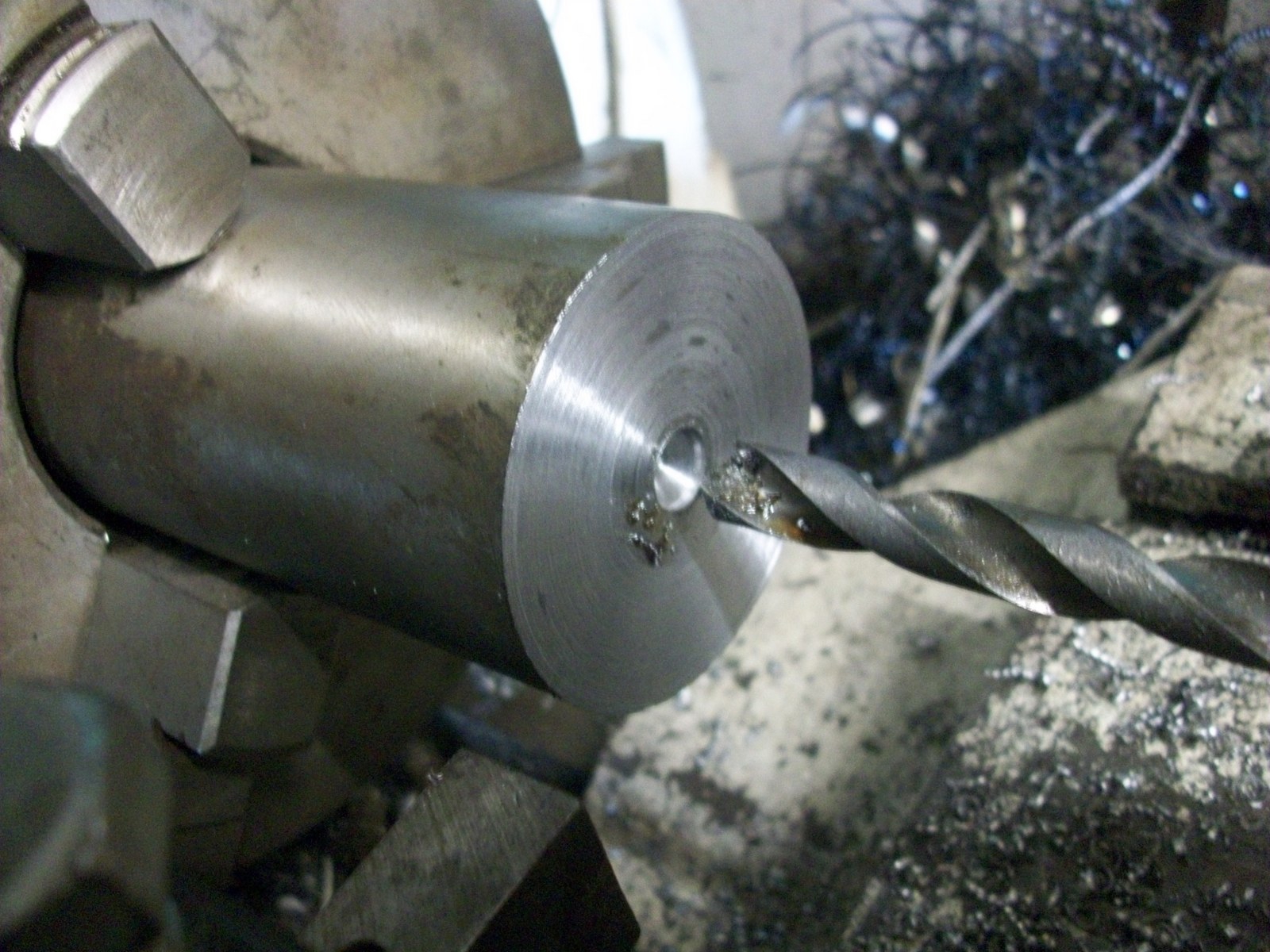
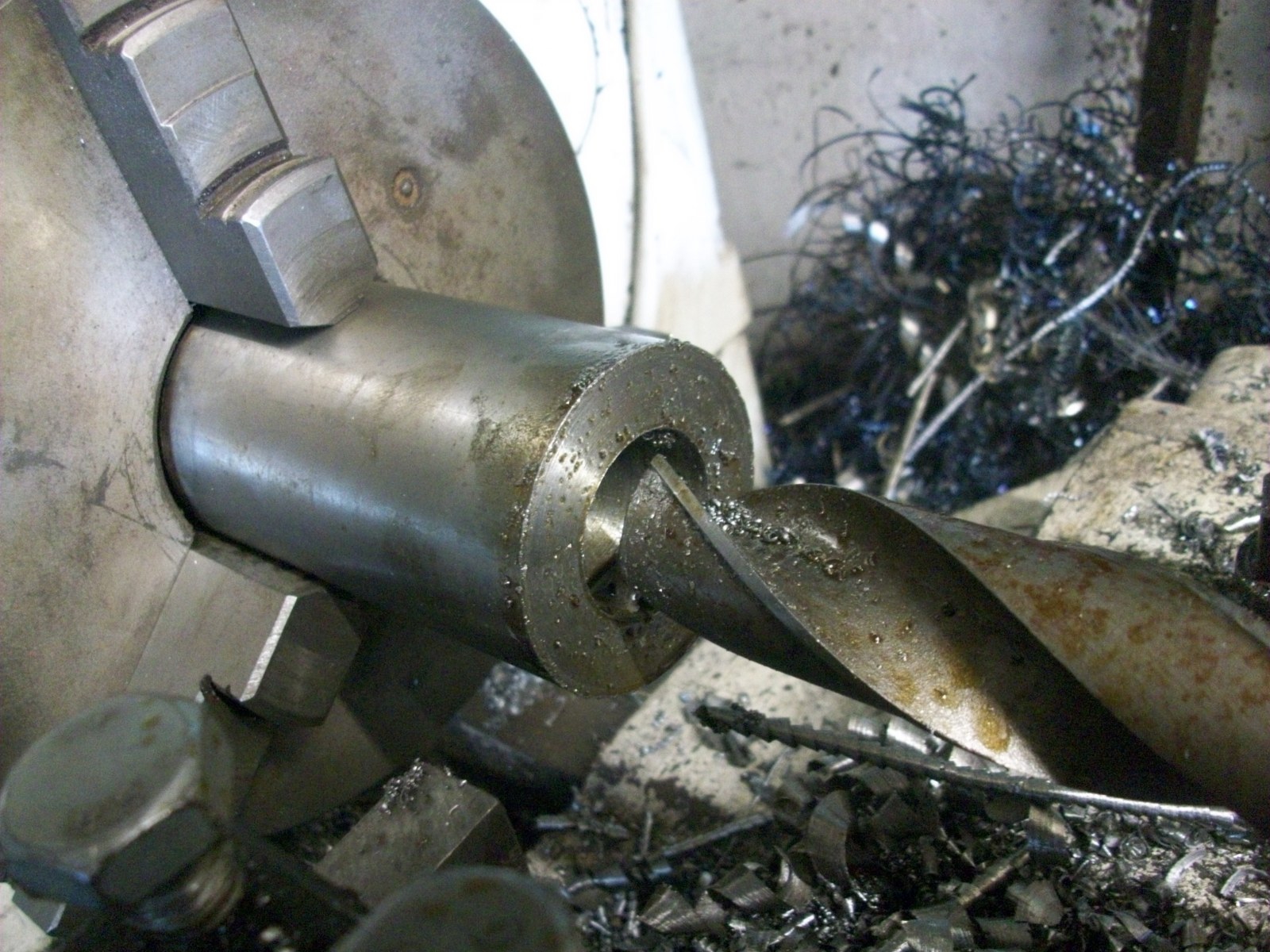
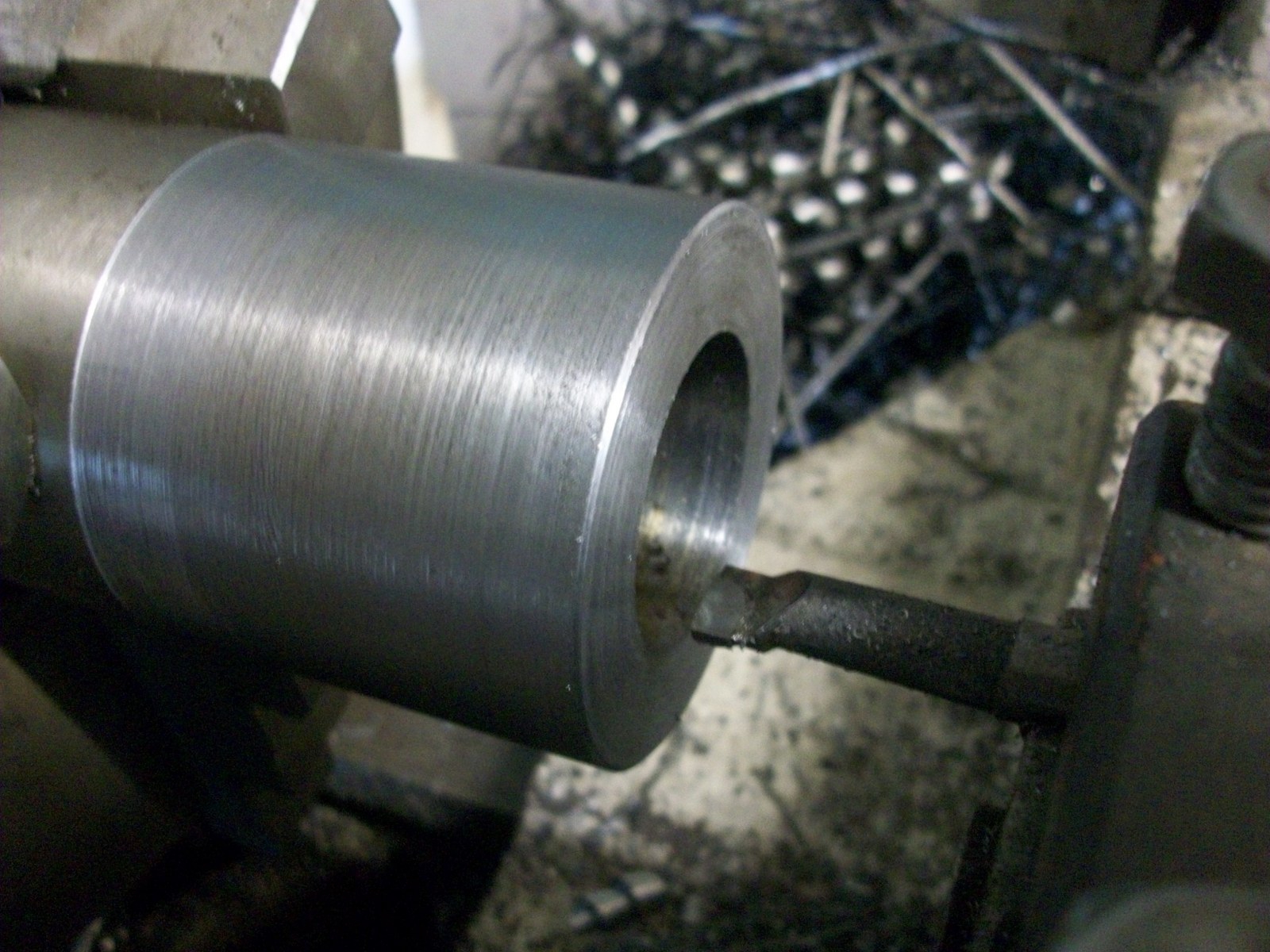
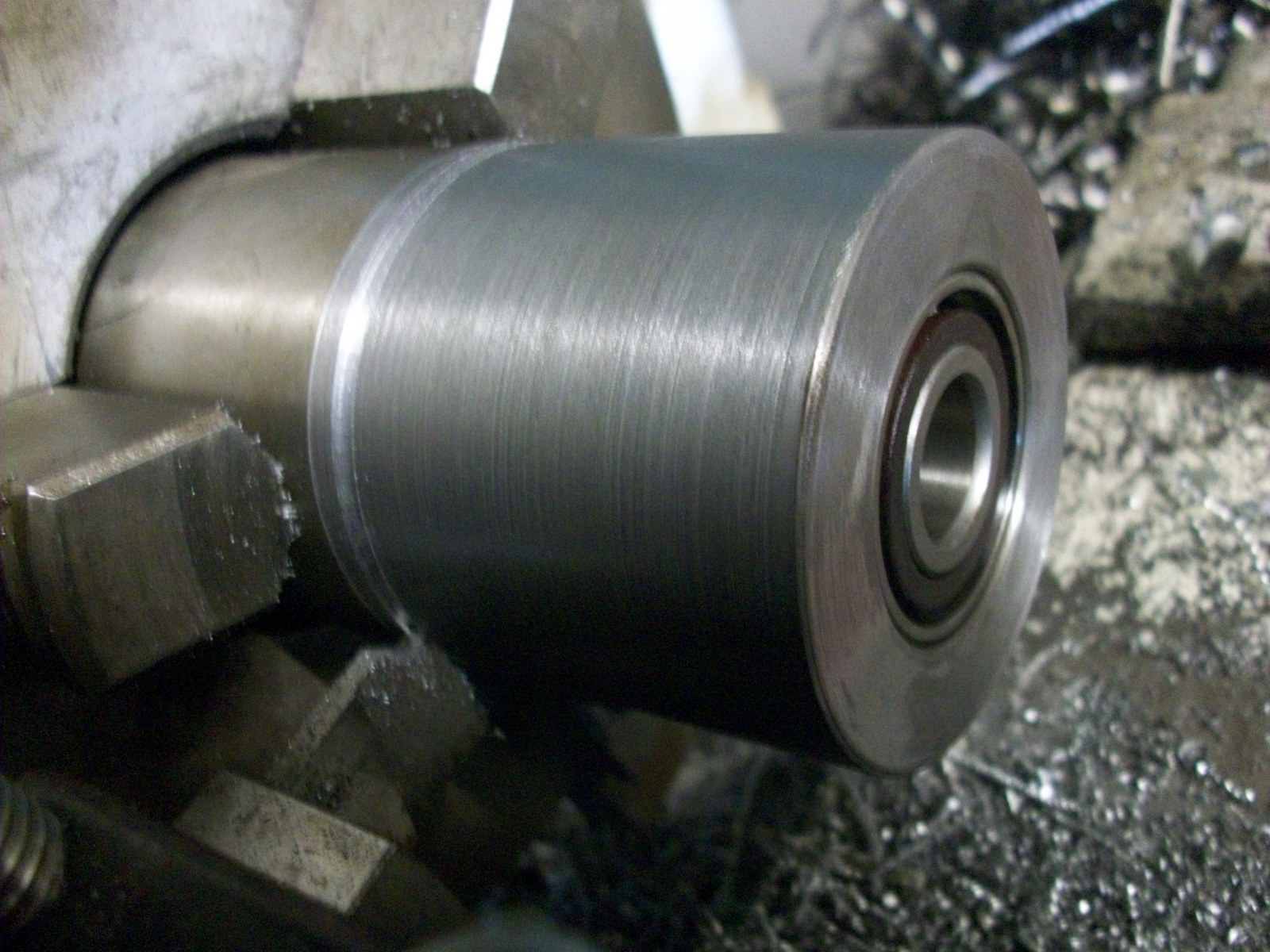
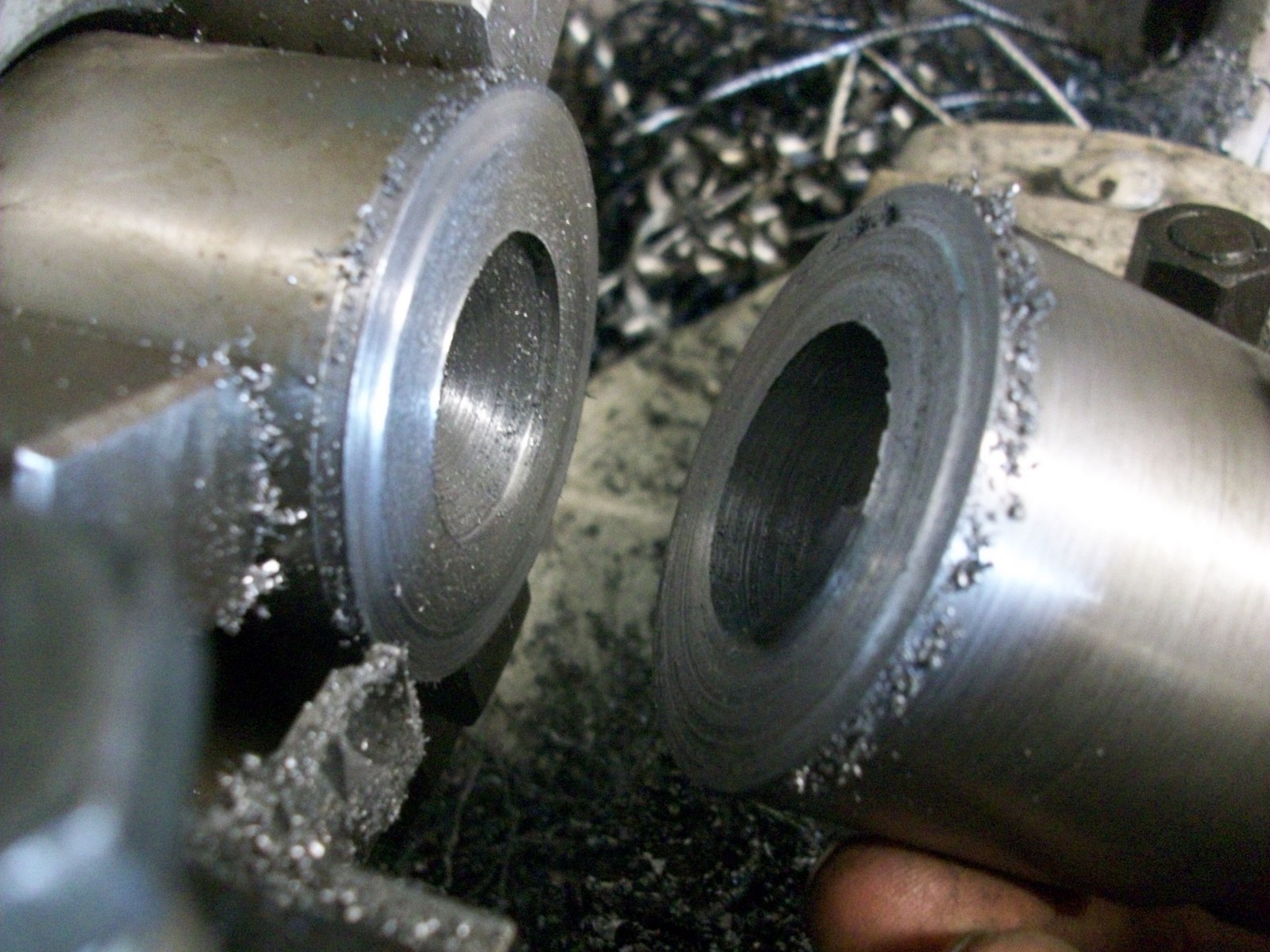
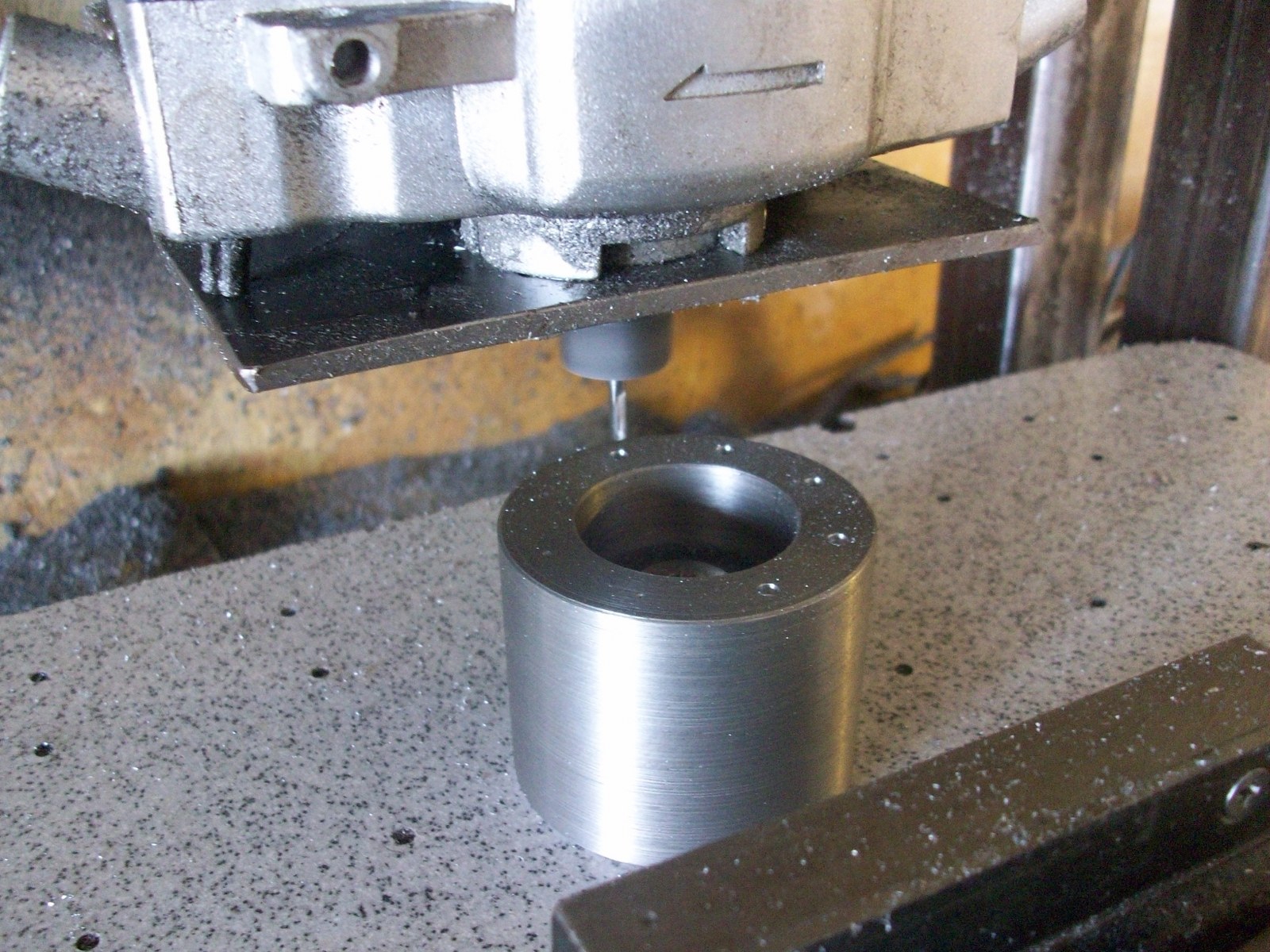
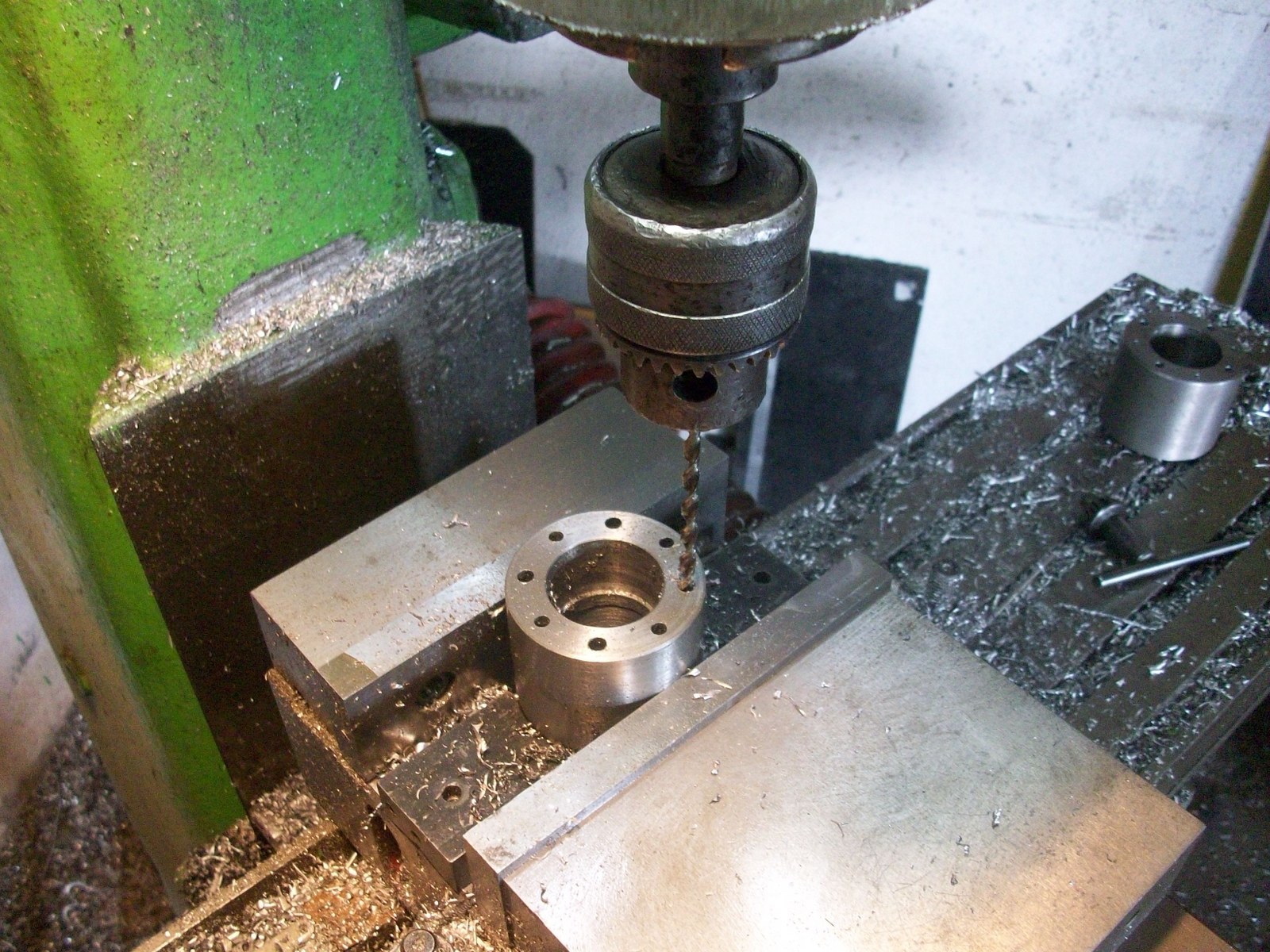
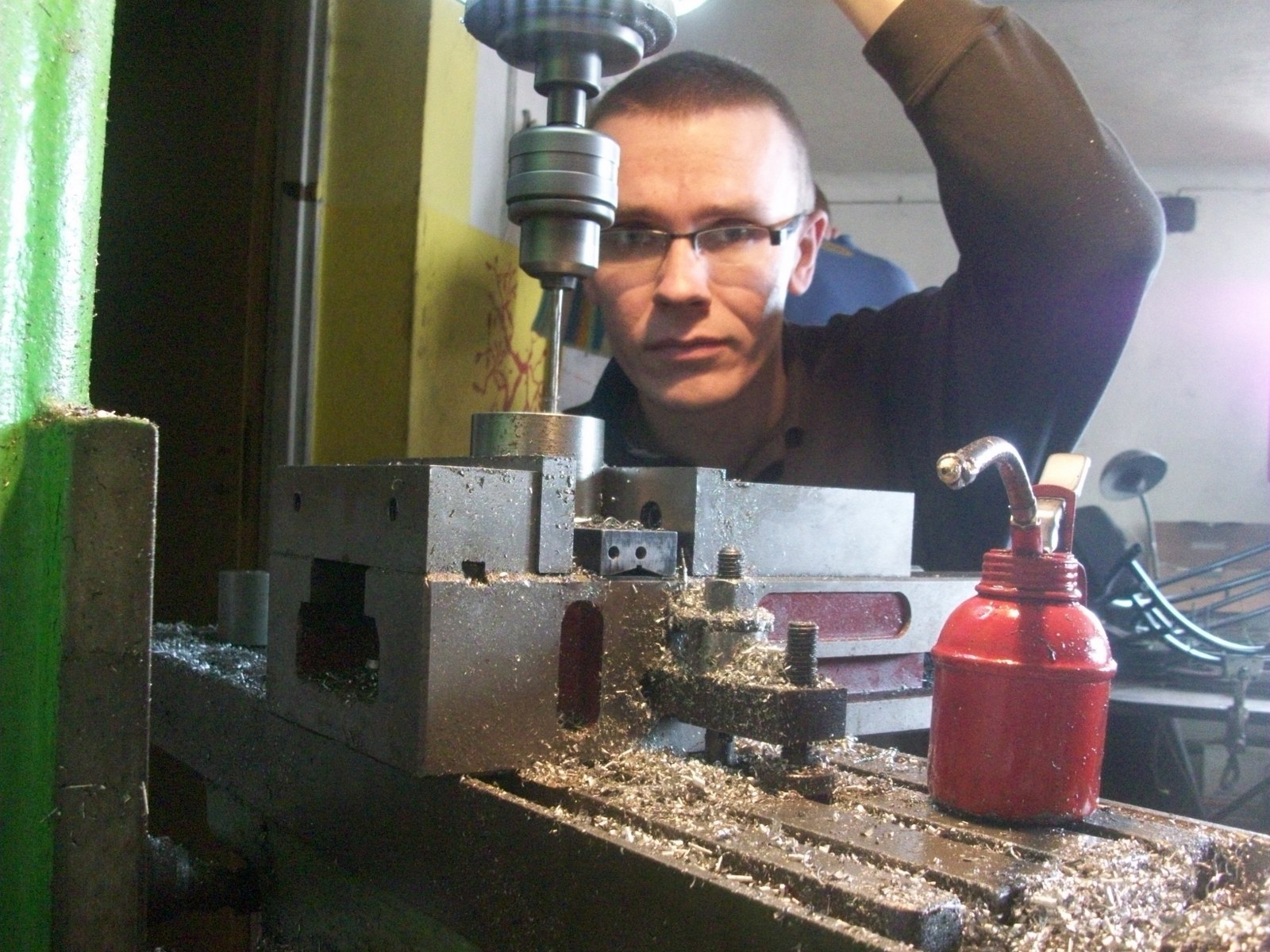
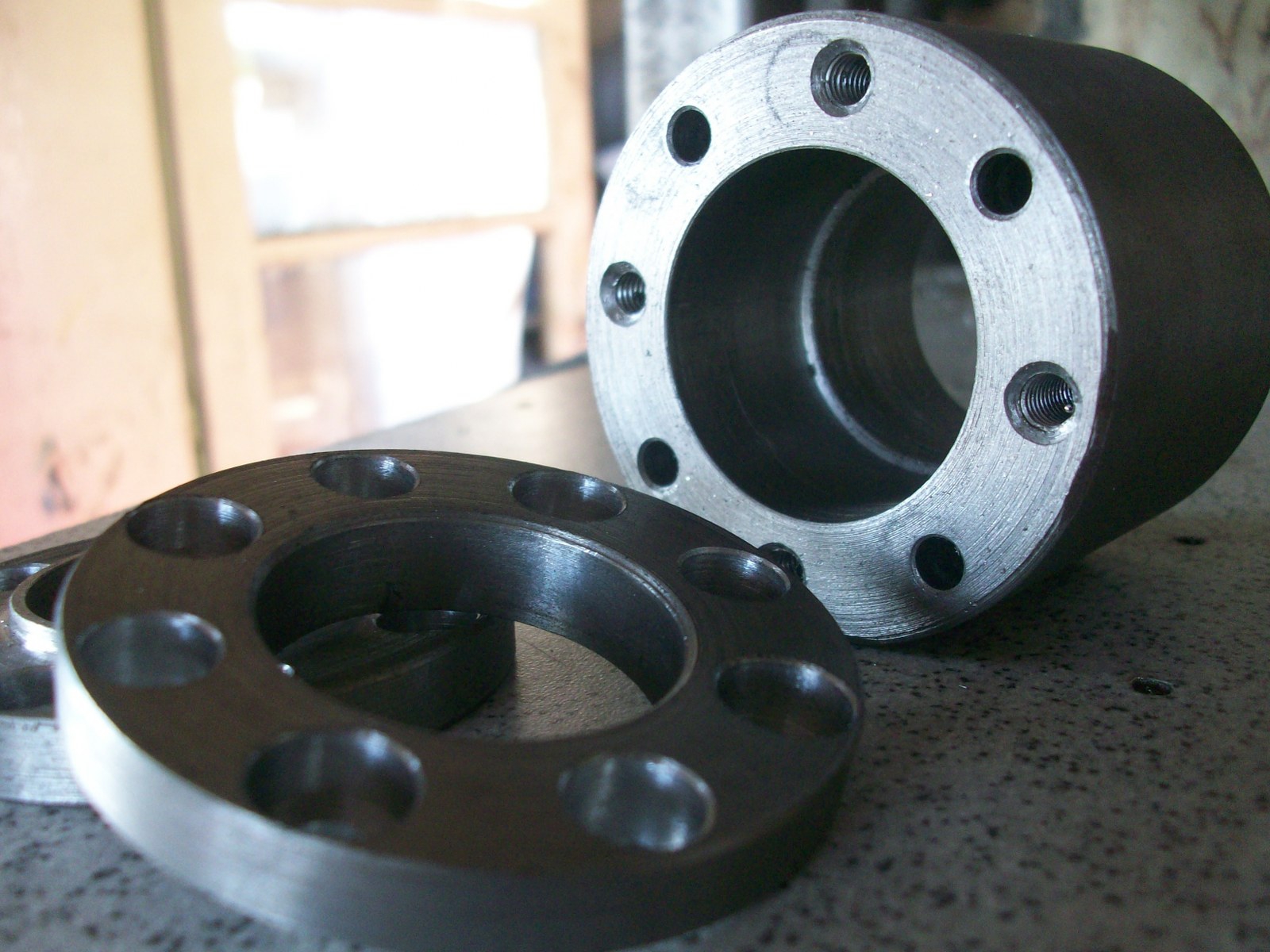
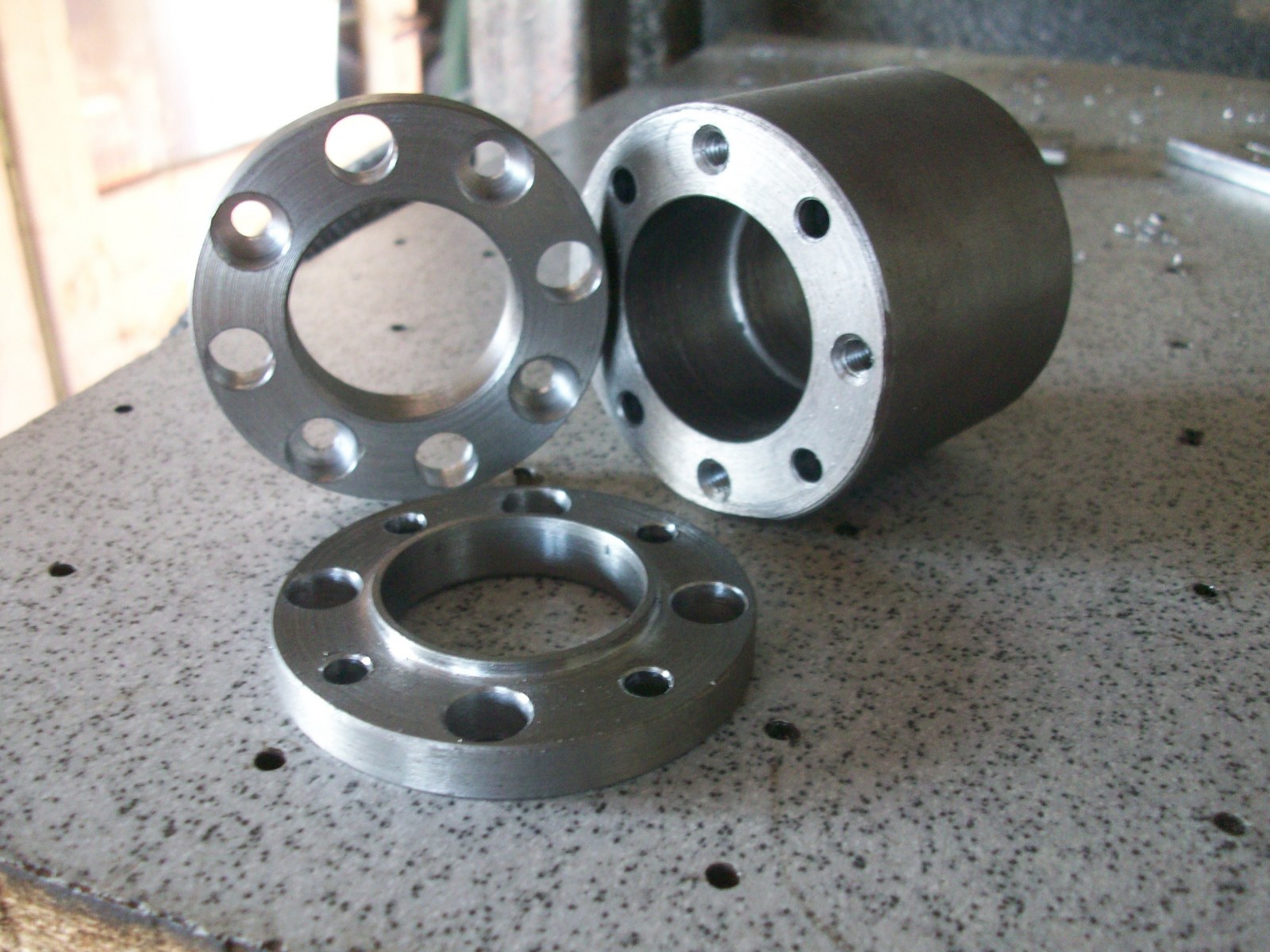
Siedzę w warsztacie po 12 godzin i co z niego wychodzę to wydaje mi się że stoję w miejscu i że w sumie nic nie zrobiłem. Każda pierdoła wymaga tyle czasu, uwagi, wymyślenia i spasowania.... jestem już zmęczony tą budową..... masakra.... żebym wiedział że tyle czasu to będzie trwać to bym se zbudował jakiegoś aluminiaka a nie żeliwnego potwora.
Rzucił się szczerbaty na suchary...

Ale etap ciężkiej budowy mechaniki w sumie zakończony.
Teraz oddam pierdółki do czernienia, zdejmę płytę z ramy, przykryję ją blachami, pospawam i pomaluję ją w jakiś tam kolor. Potem połączę ramę ze stołem i składam maszynę na gotowo.
Zacznie się puszczanie kabelków, światełek i innych dzwoneczków.....
.....tylko czy ja dożyję ......

