G0 Z10 - jadę na Z=10
G0 X0 Y0 - jadę na 0,0,10
M03 - włączam wrzeciono
G0 Z-10 - "dotykam materiału"

Ok dam tu G0 Z-9 - jestem milimetr nad materiałem i jadę potem do pierwszego otworu. Sprawdziłem w mach-u wygląda niby tak samo jak poprzednio, ale przy symulacji chyba rzeczywiście teraz zaczyna od Z1. Kiepsko to widać w tym Mach-u, wcześniej był zjazd na Z0 i potem na Z1 i G81 ... czyli fizycznie maszyna by dotknęła w poliamid. Rysunek na podglądzie się nie zmienił, ale przy starcie programu widać tę jedną zieloną kropkę mniej.
[ Dodano: 2012-09-03, 00:01 ]
qrde. Te G00 Z-9 to miało być po G91, czyli:
G00 Z10 - 10 do góry
G00 X0 Y0 - i na punkt 0,0 (który ustawiam przy pierwszej frezowanej formatce)
(tu włączę wrzeciono M coś tam - muszę sprawdzić)
G91 - teraz pozycjonowanie inkrementalne
G00 Z-9 - zjazd do materiału (byłem na 10 teraz jadę do 1)
[ Dodano: 2012-09-03, 00:28 ]
Po poprawkach program działa raczej dobrze, na symulacji nie widać zbędnych ruchów (nie wiedziałem że jak się w mach-u zmniejszy prędkość to i podgląd jest lepszy). W stół frez nie uderza:
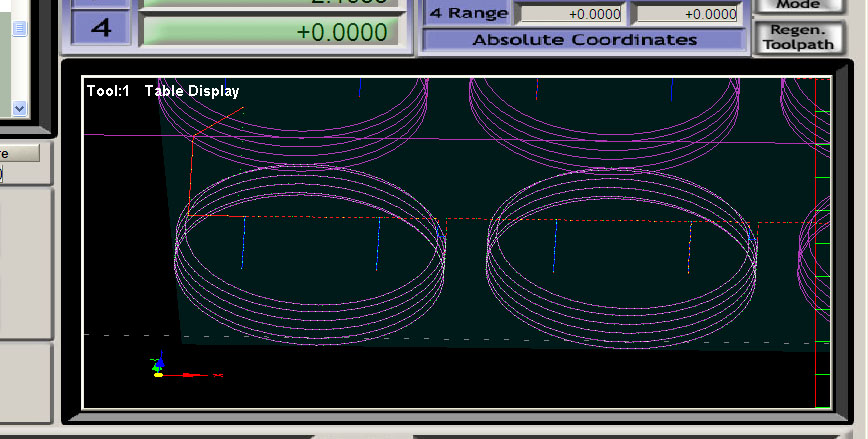
... i chyba już ostateczna poprawna wersja programu:
Kod: Zaznacz cały
%
G90
G54
G40
G80
G94
G17
G21
G64
T1 M6 (frez 2mm)
G97 S10000
F800
#100=10 (ilość w Y)
#101=12 (ilość w X)
#102=2 (odstep między elementami)
#103=2 (średnica freza)
#104=23.4 (średnica elementu)
#105=[#104+#102+2*#103] (obliczenie odstępu z uwzględnieniem średnicy freza)
G00 Z10
G00 X0 Y0
M3
G91
G00 Z-9
M98 P110L#100 (wycinanie #100 serii wzdłuż Y)
M30
o110 (wycinanie #101 serii wzdluz osi X)
(#101 - ilość elementów wzdluz osi X)
(#105 - odstęp między elementmi)
M98 P100l#101
G00 X[-1*#105*#101] Y#105
m99
O100 (wycinanie elementu właściwego z korekcją średnicy freza)
(2 x otwór 2 mm)
G81 x[5.35] y0 Z-5 R1
G81 x[12.7] y0 Z-5 R1
G80
(najazd nad pierwszy okrąg)
G00 X[5.35-0.8+#103/2] y0
(zjazd 0.2 na materiałem i wjazd roboczy 1mm w materiał)
G00 Z-0.8
G01 Z-1.2
(okrąg R10.9 Z0 z korekcją średnicy freza)
G02 I[-10.9-#103/2] J0 Z0
(przejazd nas drugi okrąg)
G01 X0.8
(Zejście po spirali R11.7 na 4mm)
G02 I[-11.7-#103/2] J0 Z-1
G02 I[-11.7-#103/2] J0 Z-1
G02 I[-11.7-#103/2] J0 Z-1
G02 I[-11.7-#103/2] J0 Z-1
(odcięcie końcówki)
G02 I[-11.7-#103/2] J0 Z0
(wyjazd 1mm nad materiał)
G00 Z6
G00 x[#105-#104-#103/2] (przesunięcie na pozycję następnego elementu)
M99
%