Maszyna z syntetycznego granitu
-
Autor tematu - Specjalista poziom 1 (min. 100)
- Posty w temacie: 53
- Posty: 141
- Rejestracja: 22 sie 2007, 04:52
- Lokalizacja: USA
Dziekuje za zainteresowanie oraz komentarze!
Powazna praca tak naprawde dopiero sie zacznie. Material trzeba doprowadzic do uzywalnosci w scisle profesjonalnych aplikacjach- trzeba to zoptymalizowac termicznie, pod katem wibracji oraz sztywnosci- a to wymaga wielomiesiecznej pracy laboratoryjnej i napewno doprowadzi do wymiany calego obecnego skladu- wlacznie z zywica.
Artur,
Bardzo dobre pytanie.
Jesli chodzi o powierzchnie bazowe to wszystko zalezy od skali projektu, doswiadczenia oraz budzetu.
Ludzie nie zwiazani z branza metalowa nie maja zbyt wygorowanych wymagan wzgledem precyzji, wiec nie bedzie problemu.
Ci z kolei ktorzy operuja w setnych mm i wymagaja wysokiej precyzji zazwyczaj spedzaja duzo czasu przy maszynach i sa obeznani z budowaniem wszelkiego rodzaju przyrzadow i mocowan- bo na tym polega ich praca. Czyli pozostaje tylko kwestia inwencji i wyobrazni. To odnosnie doswiadczenia.
Teraz skala projektu. Czy bedzie to urzadzenie amatorskie do zabawy czy tez zawodowa maszyna do biznesu? W drugim przypadku wymagania beda duzo wieksze i uzasadnione bedzie uzycie zawodowych technik.
Po trzecie budzet. Inne beda rozwiazania przy budzecie 300pln a inne przy 300 tys pln.
W moim przypadku budzet jest ograniczony i dlatego wybralem metody amatorskie- bez obrobki skrawaniem- polegajac jedynie na precyzji ktora oferuje aluminum Mic6. Do belki prezentowanej na pierwszej stronie zostala skrecona konstrukcja- jest ona fabrycznie szlifowana i ma trzymac oryginalny ksztalt.
Na belki stolu zostanie uzyte to samo aluminum,tylko tym razem 25mm listwy. Nie beda one w stanie utrzymac ksztaltu wiec zostala ulozone na powierzchni wylanej z epoxy- poziom powstanie za pomoca grawitacji, listwy przyjda na wierzch i beda powtornie zalane.
To tyle jesli chodzi o moje amatorstwo. Gdybym robil powazna maszyne do stali to zdecydowanie wybralbym to co proponowales- wpuszczenie stalowych listew i zawiezienie calosci do obrobki po fakcie. Mozna tez obrobic listwy przed, do odlewu przykrecic je do wzorca katowego i zalatwic sprawe w ten sposob. Oczywiscie plyty wzorcowe musza miec wysoka precyzje. To raczej sprawdzi sie w mini maszynach bo duze wzorce kosztuja majatek i malo kto sie odwazy w nich wiercic.
Czyli jest tylko kwestia ujecia calej sprawy w budzecie, zrobienia kosztorysu co bardziej sie oplaca- czy maszyna ma 20cm czy 200cm i czy da sie ja zawiezc do obrobki.
Mozna tez zrobic maszyne modulowa, z osobnym stolem itp. Osobiscie jednak bym tego nie robil, konstrukcja jest bardziej zwarta gdy odlana w calosci i nie posiada wielu powierzchni laczacych. Tym bardziej ze musialyby one byc stalowe co przyczyni sie do wiekszych wibracji.
Mam kilka swoich pomyslow na precyzyjna frezarke do stali, choc nie mysle zebym jej kiedykolwiek potrzebowal czy mial na nia budzet. Gdyby to sie jednak zmienilo to plan bylby taki:
powierzchnie bazowe pod dwie osie skrecone z listew zeliwnych w formie klatki, zalane zywica z piaskiem i w postaci 300kg bryly zawiezione do obrobki w warstacie. Potem bryla delikatnie zawieszona w formie i zalana 1000kg materialu do koncowego ksztaltu na solidnych fundamentach w garazu.
W sumie to mam ochote zrobic 30cm miniaturke takiej maszyny i sprawdzic czy zda to egzamin. Hmm..
Powazna praca tak naprawde dopiero sie zacznie. Material trzeba doprowadzic do uzywalnosci w scisle profesjonalnych aplikacjach- trzeba to zoptymalizowac termicznie, pod katem wibracji oraz sztywnosci- a to wymaga wielomiesiecznej pracy laboratoryjnej i napewno doprowadzi do wymiany calego obecnego skladu- wlacznie z zywica.
Artur,
Bardzo dobre pytanie.
Jesli chodzi o powierzchnie bazowe to wszystko zalezy od skali projektu, doswiadczenia oraz budzetu.
Ludzie nie zwiazani z branza metalowa nie maja zbyt wygorowanych wymagan wzgledem precyzji, wiec nie bedzie problemu.
Ci z kolei ktorzy operuja w setnych mm i wymagaja wysokiej precyzji zazwyczaj spedzaja duzo czasu przy maszynach i sa obeznani z budowaniem wszelkiego rodzaju przyrzadow i mocowan- bo na tym polega ich praca. Czyli pozostaje tylko kwestia inwencji i wyobrazni. To odnosnie doswiadczenia.
Teraz skala projektu. Czy bedzie to urzadzenie amatorskie do zabawy czy tez zawodowa maszyna do biznesu? W drugim przypadku wymagania beda duzo wieksze i uzasadnione bedzie uzycie zawodowych technik.
Po trzecie budzet. Inne beda rozwiazania przy budzecie 300pln a inne przy 300 tys pln.
W moim przypadku budzet jest ograniczony i dlatego wybralem metody amatorskie- bez obrobki skrawaniem- polegajac jedynie na precyzji ktora oferuje aluminum Mic6. Do belki prezentowanej na pierwszej stronie zostala skrecona konstrukcja- jest ona fabrycznie szlifowana i ma trzymac oryginalny ksztalt.
Na belki stolu zostanie uzyte to samo aluminum,tylko tym razem 25mm listwy. Nie beda one w stanie utrzymac ksztaltu wiec zostala ulozone na powierzchni wylanej z epoxy- poziom powstanie za pomoca grawitacji, listwy przyjda na wierzch i beda powtornie zalane.
To tyle jesli chodzi o moje amatorstwo. Gdybym robil powazna maszyne do stali to zdecydowanie wybralbym to co proponowales- wpuszczenie stalowych listew i zawiezienie calosci do obrobki po fakcie. Mozna tez obrobic listwy przed, do odlewu przykrecic je do wzorca katowego i zalatwic sprawe w ten sposob. Oczywiscie plyty wzorcowe musza miec wysoka precyzje. To raczej sprawdzi sie w mini maszynach bo duze wzorce kosztuja majatek i malo kto sie odwazy w nich wiercic.
Czyli jest tylko kwestia ujecia calej sprawy w budzecie, zrobienia kosztorysu co bardziej sie oplaca- czy maszyna ma 20cm czy 200cm i czy da sie ja zawiezc do obrobki.
Mozna tez zrobic maszyne modulowa, z osobnym stolem itp. Osobiscie jednak bym tego nie robil, konstrukcja jest bardziej zwarta gdy odlana w calosci i nie posiada wielu powierzchni laczacych. Tym bardziej ze musialyby one byc stalowe co przyczyni sie do wiekszych wibracji.
Mam kilka swoich pomyslow na precyzyjna frezarke do stali, choc nie mysle zebym jej kiedykolwiek potrzebowal czy mial na nia budzet. Gdyby to sie jednak zmienilo to plan bylby taki:
powierzchnie bazowe pod dwie osie skrecone z listew zeliwnych w formie klatki, zalane zywica z piaskiem i w postaci 300kg bryly zawiezione do obrobki w warstacie. Potem bryla delikatnie zawieszona w formie i zalana 1000kg materialu do koncowego ksztaltu na solidnych fundamentach w garazu.
W sumie to mam ochote zrobic 30cm miniaturke takiej maszyny i sprawdzic czy zda to egzamin. Hmm..
Tagi:
-
- Sympatyk forum poziom 2 (min. 50)
- Posty w temacie: 9
- Posty: 61
- Rejestracja: 19 kwie 2007, 16:20
- Lokalizacja: Jaworzno
Tak właśnie myślałem. Odlew taki powinno się jednak traktować jak odlew żeliwny i obrabiać po odlaniu.
Druga kwestia.
Przeprowadziłem próby, 1-piasek bardzo drobny (kupiony w zoologicznym dla szynszyli), 2-zwykły piasek kwarcowy (jako średnie ziarno), 3-piasek gruby ( przesiany ze żwiru). Do tego klej epoksydowy jak na fotkach ( niestety nie znam dokładnie parametrów ani kleju ani utwardzacza wiem tylko że jest niemiecki).
Wszystko wymieszane i rzeczywiście robi się skała (przekrój odlany posiada przekrój 10mmx10mm) i nie potrafię go złamać w rękach. Za to po lekkim podgrzaniu do ok 60-80 C, zaczyna robić się miekki jak guma, po ponownym ostudzeniu znów jest skała.
Moje wnioski:
Epoksyd będzie prawdopodobnie "pływał" podobnie jak szkło (szkło po paru latach w oknie podobno na dole jest grubsze niż na górze), z tym że wg mnie zjawisko to w epoksy zachodzić będzie szybciej. Jak szybko? Tego nie jestem w stanie powiedzieć, ale podejrzewam że nawet gdy odlejemy i obrobimy wypuszczone części metalowe to dokładność konstrukcji z dnia na dzień może być coraz gorsza i tylko kwestia czasu aż będzie niedopuszczalna. Oczywiście jak napisałem wcześniej nie wiem ile to potrwa (jeżeli parenaście lat to spoko, ale jeżeli parę miesięcy?).
Druga kwestia.
Przeprowadziłem próby, 1-piasek bardzo drobny (kupiony w zoologicznym dla szynszyli), 2-zwykły piasek kwarcowy (jako średnie ziarno), 3-piasek gruby ( przesiany ze żwiru). Do tego klej epoksydowy jak na fotkach ( niestety nie znam dokładnie parametrów ani kleju ani utwardzacza wiem tylko że jest niemiecki).
Wszystko wymieszane i rzeczywiście robi się skała (przekrój odlany posiada przekrój 10mmx10mm) i nie potrafię go złamać w rękach. Za to po lekkim podgrzaniu do ok 60-80 C, zaczyna robić się miekki jak guma, po ponownym ostudzeniu znów jest skała.
Moje wnioski:
Epoksyd będzie prawdopodobnie "pływał" podobnie jak szkło (szkło po paru latach w oknie podobno na dole jest grubsze niż na górze), z tym że wg mnie zjawisko to w epoksy zachodzić będzie szybciej. Jak szybko? Tego nie jestem w stanie powiedzieć, ale podejrzewam że nawet gdy odlejemy i obrobimy wypuszczone części metalowe to dokładność konstrukcji z dnia na dzień może być coraz gorsza i tylko kwestia czasu aż będzie niedopuszczalna. Oczywiście jak napisałem wcześniej nie wiem ile to potrwa (jeżeli parenaście lat to spoko, ale jeżeli parę miesięcy?).
- Załączniki
-
- piasek szynszyla
- ep1.jpg (20.54 KiB) Przejrzano 5476 razy
-
- Piasek kwarcowy
- ep2.jpg (29.48 KiB) Przejrzano 5476 razy
-
- Piasek gruby
- ep3.jpg (32.74 KiB) Przejrzano 5476 razy
-
- Przed odlaniem
- ep4.jpg (33.08 KiB) Przejrzano 5476 razy
-
- Efekt końcowy
- ep5.jpg (27.64 KiB) Przejrzano 5476 razy
-=Artur=-
-
Autor tematu - Specjalista poziom 1 (min. 100)
- Posty w temacie: 53
- Posty: 141
- Rejestracja: 22 sie 2007, 04:52
- Lokalizacja: USA
Aby zrozumiec opisane wyzej zjawisko nalezy siegnac do zrodel i przeanalizowac zywice: http://pl.wikipedia.org/wiki/%C5%BBywica_epoksydowaatu79 pisze:Epoksyd będzie prawdopodobnie "pływał" podobnie jak szkło (szkło po paru latach w oknie podobno na dole jest grubsze niż na górze), z tym że wg mnie zjawisko to w epoksy zachodzić będzie szybciej. Jak szybko? Tego nie jestem w stanie powiedzieć, ale podejrzewam że nawet gdy odlejemy i obrobimy wypuszczone części metalowe to dokładność konstrukcji z dnia na dzień może być coraz gorsza i tylko kwestia czasu aż będzie niedopuszczalna. Oczywiście jak napisałem wcześniej nie wiem ile to potrwa (jeżeli parenaście lat to spoko, ale jeżeli parę miesięcy?).
"Zywice epoksydowe to rodzaj żywic syntetycznych powstających w reakcji polifenoli, rzadziej glikoli z epichlorohydryną lub innymi związkami epoksydowymi lub dwuchlorohydrynowymi.
Żywice epoksydowe, zależnie od masy cząsteczkowej i struktury, są wysokolepkimi cieczami lub topliwymi ciałami stałymi, rozpuszczalnymi w ketonach i węglowodorach aromatycznych. Utwardzone, stają się nierozpuszczalne i nietopliwe, są bardzo przyczepne do prawie wszystkich materiałów oraz względnie chemoodporna [..]"
Inne zrodlo podaje:
"Żywice
Żywicami epoksydowymi nazywamy związki epoksydowe małocząsteczkowe, oligomeryczne i polimeryczne zawierające w swojej budowie co najmniej dwie grupy epoksydowe, a także utwardzone produkty tych związków. W Zakładzie Epoksydów otrzymuje się je głównie w wyniku syntezy epichlorochydryny (1,2-epoksy-3-chloropan) z dianem - bisfenol A (4,4'-dihydroksydifenylopropan) lub z bisfenolem F. W zależności od stosunków molowych substratów oraz parametrów kondensacji otrzymuje się różne typy żywic różniące się między sobą wielkością cząsteczki oraz ilością reaktywnych grup epoksydowych i hydroksylowych.
W postaci nieutwardzonej żywice epoksydowe są lepkimi cieczami lub termoplastycznymi ciałami stałymi. Utwardzenie czyli usieciowienie przestrzenne następuje w wyniku reakcji chemicznych zawartych z żywicy grup funkcyjnych z odpowiednio dobranym utwardzaczem. Wybierając typ utwardzacza można modyfikować własności utworzonego tworzywa.
Żywice epoksydowe to doskonałe tworzywo stanowiące bazę materiałów powłokowych, lakierniczych, laminatów, szpachlówek, klejów, kitów i spoiw stosowanych w wielu gałęziach przemysłu.
Utwardzacze
Utwardzacze do żywic epoksydowych są związkami chemicznymi, które w wyniku reakcji chemicznych powodują przestrzenne usieciowanie żywic, nadając im cechy kleju, syciwa fub tworzywa chemoutwardzalnego. Utwardzacze typu: pierwszorzędowe i drugorzędowe dwuaminy, wieloaminy alifatyczne i aromatyczne, polimerkaptany zawierające aktywne atomy wodoru reagują tylko z grupami epoksydowymi, natomiast bezwodniki kwasowe reagują także z grupami wodorotlenowymi, dzięki czemu gęstość usieciowania utwardzonej żywicy jest znacznie większa. Do utwardzania żywic epoksydowych stosuje się także utwardzacze nie zawierające czynnych atomów wodorur które powodują polimeryzację jonową. Są to kwasy i zasady typu Lewisa, np. fluorek boru i aminy trzeciorzędowe. Utwardzacze stosowane do utwardzania żywic epoksydowych można podzielić na następujące grupy:
1. Utwardzacze aminowe:
* aminy alifatyczne
* aminy cykloalifatyczne
* aminy aromatyczne
* addukty amin aromatycznych i alifatycznych oraz ich modyfikcje
* zasady typu Mannicha
2. Utwardzacze poliamidowe
3. Utwardzacze amidowe
4. Utwardzacze bezwodnikowe
5. Utwardzacze typu kwasów i zasad Lewisa
Wybór odpowiedniego utwardzacza zależy od typu żywicy, warunków utwardzania i wymaganych właściwości gotowego wyrobu. W przypadku utwardzania kompozycji zawierających środki modyfikujące bez grup epoksydowych ilość utwardzacza należy odnosić do żywicy wchodzącej w skład kompozycji. Przed użyciem żywicę należy dokładnie wymieszać z określoną ilością utwardzacza, Proces utwardzania aminami prowadzi się w temperaturze pokojowej, podwyższonej, ewentualnie w systemie dwuetapowym tj. utwardzanie wstępne w temp. pokojowej i dogrzewanie w temp. średniej (do 100°C). Utwardzanie bezwodnikami kwasowymi prowadzi się w temperaturze wyższej niż 100°C.
Uwaga: Po dodaniu utwardzacza do żywicy, rozpoczyna się proces utwardzania, któremu towarzyszy wydzielanie się ciepła. Im większa jest masa przygotowanej kompozycji, tym szybciej przebiega proces utwardzania i większa jest ilość wydzielanego ciepła."
http://www.laminexbb.pl/zywice_epoksydowe.php
* * *
Z definicji wynika ze zywica epoksydowa jest nierozpuszczalna i nietopliwa. Skutki uboczne prezentowane przez Artura wskazuja wiec ze nie byla to prawdziwa zywica. I nie jest to wcale dziwne- producenci klejow modyfikuja zywice do swoich celow, a takze rozcienczaja aby na nich zarobic. Takie zywice mozna najszybciej rozpoznac po zapachu- czyste zywice sa bezzapachowe- jesli cos brzydko pachnie to nalezy to omijac z daleka. Wiekszosc srodkow do rozcienczania jest toksyczna.
Niestety nie ma latwego sposobu na przestudiowanie zawartosci zywicy. Nazwa na opakowaniu ma niewiele wspolnego z tym co jest w srodku i dopiero ostre telefony do firmy powoduja ujawnienie oryginalnego producenta zywicy/utwardzacza. Po zdobyciu tej informacji dzwoni sie do oryginalnego producenta, zdobywa 10 stronicowy pdf zywicy i utwardzacza oraz rozmawia z inzynierem technologiem. Wtedy i tylko wtedy mozemy sie dowiedziec jakie sa oryginalne formulacje, czy nadaja sie one do naszej aplikacji i na ile mozemy to rozcienczyc- i czym- zanim zaczniemy degradowac wlasnosci mechaniczne.
Pisalem wielokrotnie ze uzywam najtanszej zywicy, byla ona jednak dokladnie przeswietlona i odbyly sie rozmowy z technologami oryginalnego producenta. Jest to prosta formulacja bisphenol-A z utwardzaczem aminowym o niskiej lepkosci i minimalnej ilosci domieszek. Nie jest idealna (chocby ze wzgledu na skurcz czy rozszerzalnosc termiczna) ale spelnia przynajmniej podstawowe warunki. Nie nadaje sie ona jednak do ultra profesjonalnych zastosowan- w przyszlosci bedzie modyfikowana albo wymieniona na inny gatunek.
Dodam jeszcze ze nalezy przestudiowac instrukcje obslugi zywicy. Odlewy uzyskuja pelne wlasciwosci dopiero po tygodniu, podgrzewanie odlewu po kilku godzinach moze spowodowac wlasnie efekt opisywany przez Artura. Niektore zywice sa tez np. nagrzewane po 24 godzinach w celu utwardzenia powierzchni oraz polepszenia wlasnosci mechanicznych. Wszystko zalezy od typu utwardzacza.
* * *
Historycznie rzecz biorac, przypadki z zywicami sa rozne. Szwajcarzy posiedli jeden z pierwszych patentow na zywice epoksydowe (koncern Ciba Geigy), Szwajcarski Studer (rowniez przypadkowo) wynalazl system odlewow mineralnych w latach 70 tych. Ciba Geigy wyprodukowal specjalna mieszanke na potrzeby Studera i calosc byla trzymana w tajemnicy ponad 30 lat. Dopiero 4 lata temu otwarli oni sejfy i zaczeli sprzedawac licencje.
Faktem jest tez ze w latach 80 tych wielu producentow wzielo sie za odlewy mineralne- i po jakims czasie zostaly one zarzucone. Okazalo sie ze po latach niektore korpusy maszyn zaczynalo krzywic pod wplywem temperatury, niektore nasiakaly tez chlodziwem.
Zrodlem defektow byly niewatpliwie slabe zywice. Dzisiejsze zywice sa nieporownywalnie lepsze, nie znaczy to jednak ze nie bedzie wpadki.
Dlatego proponuje nie lekcewazyc tematu i sprawdzic zywice pod katem przydatnosci. Albo- jesli ktos ma powazny projekt i wiele do stracenia- przyjrzec sie blizej ofercie warszawskiego AMODu ktory ma w ofercie zywice przeznaczona dokladnie do tego celu.
W ramach ciekawostki dodam ze niektore korpusy urzadzen odlewane sa na gotowy precyzyjny wymiar. Jeden z producentow podaje dokladnosc komponentow po wyjeciu z formy do 0.01mm, dokladnosc otworow 0.0025mm.
Pozdrowienia!
-
- Lider FORUM (min. 2000)
- Posty w temacie: 24
- Posty: 4017
- Rejestracja: 15 lis 2006, 22:01
- Lokalizacja: Tarnobrzeg
Kolega zrobi tak trzykrotnie a za czwartym razem nie powinno "pływać" mimo podgrzania. Niektóre żywice odporne na wysoką temperaturę wymagają takiego hartowania.atu79 pisze:Wszystko wymieszane i rzeczywiście robi się skała (przekrój odlany posiada przekrój 10mmx10mm) i nie potrafię go złamać w rękach. Za to po lekkim podgrzaniu do ok 60-80 C, zaczyna robić się miekki jak guma, po ponownym ostudzeniu znów jest skała.
-
Autor tematu - Specjalista poziom 1 (min. 100)
- Posty w temacie: 53
- Posty: 141
- Rejestracja: 22 sie 2007, 04:52
- Lokalizacja: USA
Koledzy ostro posuwaja sie do przodu. Gratuluje postepow!
Zachecam do dalszej pracy i testowania tej wyjatkowej technologii.
* * *
Przyznam ze przejscie z 0.5kg probek do 75kg odlewow zajelo mi dosyc duzo czasu. Chocby ze wzgledu na logistyke calego przedsiewziecia, ale nie tylko. Szczegolny problem zdaje sie sprawiac osiagniecie odpowiedniej gestosci odlewu- gestosci w ktorej klej staje sie matryca utrzymujaca ziarna i sam nie pracuje pod obciazeniem. Diablel tkwi w szczegolach czyli dokladnym obliczeniu proporcji kleju i wypelniacza. Jesli uzyjemy za duzo kleju to ziarna nie zejda sie ze soba, zbyt mala ilosc kleju natomiast moze spowodowac luki.
Swego czasu robilem testy z miksturami o absolutnie minimalnej zawartosci kleju. Probki byly bardzo suche, nie byly wibrowane tylko ubijane i charakteryzowaly sie wyjatkowo duza gestoscia. Eksperymenty zostaly jednak zarzucone bo probki byly bardzo slabe i rozpadaly sie jak kruche ciasto. Kilka miesiecy pozniej koledzy znalezli informacje ze jednak ugniatanie materialu z gory nie jest wcale zlym pomyslem i jest nawet wymagane w celu osiagniecia najwyzszej gestosci odlewu- pod warunkiem ze odbywa sie podczas wibrowania materialu.
Idea "maksymalnej gestosci" zaklada rowniez ze znamy % przestrzeni jaka zajmuje wypelniacz i ze jestesmy w stanie dobrac odpowiednia ilosc kleju- zadanie wbrew pozorom dosyc trudne. Nawet jesli mamy idealnie granulowany wypelniacz to obliczenia te przysparzaja klopotu- inaczej sie je liczy dla okraglych ziaren, inne dla kanciastych. Jeszcze inaczej dla mieszanki jednych i drugich. Gdy uzyjemy 2% za malo kleju to ryzykujemy efekt kruchego ciasta. Gdy uzyjemy 2% za duzo to nie bedziemy w stanie tego scisnac (chyba zeby przycisnac tak zeby nadmiar wyplynal na wierzch i wtedy to zebrac?).
Borykalem sie z tym przez jakis czas i w koncu zdecydowalem sie uzyc tego co mam- nawet jesli jest tam za duzo kleju- i zajac sie budowa maszyny zanim strace cierpliwosc i zainteresowanie calym tematem. Nie przyciskalem tez mikstury podczs odlewania- nie bylo za bardzo czasu oraz nie bylo to praktyczne. Dwie z moich form byly calkiem zamkniete, mialy tylko 10cm otwor na material.
I choc powierzchnia odlewow wyglada dosyc solidnie (oraz brzmi jak prawdziwy kamien)
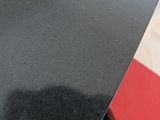
to uwazam ze mozna to zrobic duzo lepiej, zmniejszyc ilosc epoxy co najmniej o kolejne 2-5% (objetosciowo). Byc moze bedzie to wymagalo uzycia pompy prozniowej. Moze nawet ktos zbuduje wibracyjny mixer prozniowy, i dopiero wtedy bedzie to osiagalne- trudno powiedziec. Wiem ze predzej czy pozniej ktos to osiagnie i ludzie zaczna domowymi metodami robic maszynerie ktora nie sni sie nawet niektorym komercyjnym producentom. Pamietajmy ze wiekszosc komercyjnych producentow jest ograniczona do uzycia odlewow zeliwnych, gdzie najbardziej podstawowy korpus to nie lada wysilek.
Odlewy mineralne natomiast mozna robic w najbardziej wymyslnych ksztaltach, i bez ograniczen wzgledem grubosci elementow korpusu typowych dla zeliwa.
U nas problem moze wystapic np z ograniczeniem skurczu (ktory obecnie jest nieznany), czy tez rozszerzalnosci termicznej. Jednak te rzeczy sa do przeskoczenia za pomoca odpowniednich zywic i kilku testow. W kazym razie nie jestesmy tak daleko.
Dla porownania zdjecie komercyjnego $$ odlewu jednej z niemieckich firm:
(przy okazji widac sposob umieszczania insertow pod sruby)
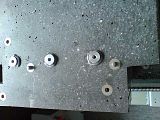
Z poczatku studiowalem technologie kwarcowych blatow kuchennych
ktore uzywaja podobnych wypelniaczy oraz charakteryzuja sie fenomenalna gestoscia. Te technologie wystepuja pod nazwa np. Slilestone i mozna je obejrzec z bliska w specjalistycznych sklepach budowlanych. Jesli ktos ma mozliwosc to proponuje sie przyjrzec z bliska powierzchni blatu- oni stosuja jeszcze mniej kleju- ok 5-8% wagowo.
Jednak przy produkcji stosuja wielkie $20mil prasy ktore podgrzewaja, wibruja i odpowietrzaja w tym samym czasie. Sa to wielotonowe prasy, w gre wchodza tez powazne temperatury i generalnie uzywaja oni innych zywic, glownie poliestrowych; utwardzacze uruchamiane sa za pomoca temperatury. Z informacji wynika ze sa w stanie scisnac material do 1/4- 1/2 oryginalnej grubosci. Caly proces zostal wynaleziony ponad 40 lat temu przez Wlochow i o ile wiem jest uzywany przez wszystkich producentow blatow kuchennych- roznia sie tylko kolory wypelniaczy i niektore skladniki. Znaczyloby to ze jest tylko jeden sposob na tego typu odlewy.
* * *
Ok, powrot do mojej maszyny.
Gorna belka wyszla bardzo solidnie- nie pozostawalo nic innego jak tylko powtorzyc wysilek przy nogach portalu- te 3 elementy w sumie stanowia najbardziej krytyczna czesc calej maszyny. Wymiary nog to 14cm grubosc, calosc w kwardracie 48x48cm.
Belka wazy niecale 75kg i bez zbednych ceregieli bedzie osadzona na 2 prostokatnych blokach aluminium o grubosci 38mm. Normalnie tego typu maszyna bylaby odlana w calosci- niestety konstrukcja musi byc przenosna i stad cala masa niepotrzebnych powierzchni laczacych, komplikacji oraz co za tym idzie wibracji. Jest to moja pierwsza konstrukcja wiec mam nadzieje ze ujdzie mi to na sucho
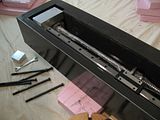
Aluminiowe bloki zostaly nawiercone i beda osadzone na pionowo ustawionych stalowych podporach. Z drugiej strony beda wystawaly sruby sluzace do przykrecenia belki. Tego typu stalowe podpory zauwazylem u jednego z producentow maszyn CMM. Mimo ze te maszyny nie pracuja pod zadnym obciazeniem, w obu scianach portalu byly grube stalowe prety podparte dwuteownikiem. Stal byla specjalnie dobrana i zdaje sie przyczyniala sie do stabilnosci termicznej calej konstrukcji.
Material na podpory:
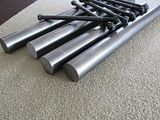
Calosc przypomina raczej budowe pomnika niz maszyny i musze przyznac ze sprawia mi niezla frajde- nie musze martwic sie rysunkami, tolerancjami, pasowaniami i cala reszta rzeczy ktora spedza sen z powiek innych budowniczych maszyn.
Po dosyc czasochlonnym ustawianiu wszystkiego za pomoca poziomnicy calosc zostala skrecona srubami i zalana zywica w celu uzyskania precyzyjnego odcisku powierzchni laczacych. Srodek belki zostal wylozony 0.01mm folia do kanapek, niektore czesci zostaly tez zaslepione. Zbyt ciasne zalanie wszystkich fragmentow spowodowaloby trudnosci przy pozniejszym pasowaniu elementow.
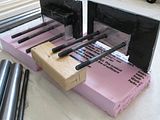
Powyzsze elementy zostaly wmontowane do formy i uzyte do zrobienia finalnego odlewu. Tak mialo to wygladac po osadzeniu belki:
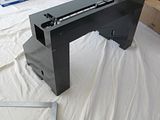
Obie nogi maja na spodzie nawiercone listwy aluminiowe ktore posluza mocowaniu nastepnych elementow.
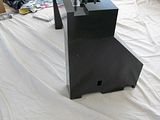
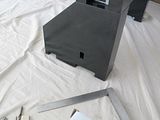
Odlewy zostaly wyjete z formy po ok tygodniu. Bylo tez kilka niedorobek, szczegolnie w poblizu otworow na spodzie- poprawki zostaly wokonane za pomoca dluta i grubego papieru sciernego i wykonczone za pomoca zywicy/drobnego wypelniacza.
* * *
Po skonczeniu obu odlewow przyszedl czas na test ugiecia belki. Do odlewu uzywalem najprostszych drewanianych form i jak pamiatamy byly podejrzenia co do pozniejszej dokladnosci/stabilnosci.
Prostolinijnosc powierzchni bazowych belki zostala sprawdzona za pomoca precyzyjnego linialu stalowego (dokladnosc linialu 0.07mm na dlugosci 1800mm). Przy uzyciu mocnego swiatla bez problemu mozna zauwazyc szczeliny rzedu 0.02mm- badalem calosc przed i po zalaniu zywica i nie stwierdzilem zadnych widocznych odksztalcen. Uwazam wiec ze pierwotny ksztalt zostal zachowany. Jesli byly jakies znieksztalcenia to sa one w granicach bledu pomiarowego.
Drugi wazny test to obciazenie belki i sprawdzenie ugiecia. Zgodnie z zalozeniami, konstrukcja miala uniesc wlasna mase plus sily skrawania plus wage doroslego mezczyzny stajacego na maszyne podczas obrobki.

Do testu cala konstrukcja zostala skrecona i ustawiona na stabilnym podlozu. Belka zostala obciazona na srodku. Dwa widoczne powyzej stalowe bloki zostaly przykryte gruba plyta na ktorej byly ukladane obciazniki (pudla z piaskiem).
Test odbyl sie dwukrotnie- z pomoca wyzej wspomnianego linialu oraz czujnika. Czujnik zostal oparty o dolna powierzchnie bazowa belki:
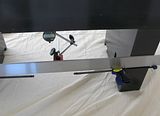
W calosci udalo mi sie polozyc na belke 255kg. Przy takim obciazeniu dolna powierzchnia bazowa belki odksztalcila sie 0.0025mm.
Faktem jest ze czujnik nie ma certyfikatu kalibracji a domowe metody pomiarowe pozostawiaja wiele do zyczenia. Nie spodziewalem sie jednak niczego w poblizu takiego wyniku i przyznam ze jest to mile zaskoczenie.
Tym bardziej ze cala konstrukcja jest raczej lekka (jak na epoxy-granitowe standardy) i nie byla planowana pod katem obrobki materialow twardych.
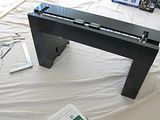
Pozdrowienia!
Zachecam do dalszej pracy i testowania tej wyjatkowej technologii.
* * *

Przyznam ze przejscie z 0.5kg probek do 75kg odlewow zajelo mi dosyc duzo czasu. Chocby ze wzgledu na logistyke calego przedsiewziecia, ale nie tylko. Szczegolny problem zdaje sie sprawiac osiagniecie odpowiedniej gestosci odlewu- gestosci w ktorej klej staje sie matryca utrzymujaca ziarna i sam nie pracuje pod obciazeniem. Diablel tkwi w szczegolach czyli dokladnym obliczeniu proporcji kleju i wypelniacza. Jesli uzyjemy za duzo kleju to ziarna nie zejda sie ze soba, zbyt mala ilosc kleju natomiast moze spowodowac luki.
Swego czasu robilem testy z miksturami o absolutnie minimalnej zawartosci kleju. Probki byly bardzo suche, nie byly wibrowane tylko ubijane i charakteryzowaly sie wyjatkowo duza gestoscia. Eksperymenty zostaly jednak zarzucone bo probki byly bardzo slabe i rozpadaly sie jak kruche ciasto. Kilka miesiecy pozniej koledzy znalezli informacje ze jednak ugniatanie materialu z gory nie jest wcale zlym pomyslem i jest nawet wymagane w celu osiagniecia najwyzszej gestosci odlewu- pod warunkiem ze odbywa sie podczas wibrowania materialu.
Idea "maksymalnej gestosci" zaklada rowniez ze znamy % przestrzeni jaka zajmuje wypelniacz i ze jestesmy w stanie dobrac odpowiednia ilosc kleju- zadanie wbrew pozorom dosyc trudne. Nawet jesli mamy idealnie granulowany wypelniacz to obliczenia te przysparzaja klopotu- inaczej sie je liczy dla okraglych ziaren, inne dla kanciastych. Jeszcze inaczej dla mieszanki jednych i drugich. Gdy uzyjemy 2% za malo kleju to ryzykujemy efekt kruchego ciasta. Gdy uzyjemy 2% za duzo to nie bedziemy w stanie tego scisnac (chyba zeby przycisnac tak zeby nadmiar wyplynal na wierzch i wtedy to zebrac?).
Borykalem sie z tym przez jakis czas i w koncu zdecydowalem sie uzyc tego co mam- nawet jesli jest tam za duzo kleju- i zajac sie budowa maszyny zanim strace cierpliwosc i zainteresowanie calym tematem. Nie przyciskalem tez mikstury podczs odlewania- nie bylo za bardzo czasu oraz nie bylo to praktyczne. Dwie z moich form byly calkiem zamkniete, mialy tylko 10cm otwor na material.
I choc powierzchnia odlewow wyglada dosyc solidnie (oraz brzmi jak prawdziwy kamien)
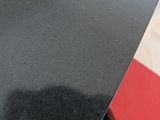
to uwazam ze mozna to zrobic duzo lepiej, zmniejszyc ilosc epoxy co najmniej o kolejne 2-5% (objetosciowo). Byc moze bedzie to wymagalo uzycia pompy prozniowej. Moze nawet ktos zbuduje wibracyjny mixer prozniowy, i dopiero wtedy bedzie to osiagalne- trudno powiedziec. Wiem ze predzej czy pozniej ktos to osiagnie i ludzie zaczna domowymi metodami robic maszynerie ktora nie sni sie nawet niektorym komercyjnym producentom. Pamietajmy ze wiekszosc komercyjnych producentow jest ograniczona do uzycia odlewow zeliwnych, gdzie najbardziej podstawowy korpus to nie lada wysilek.
Odlewy mineralne natomiast mozna robic w najbardziej wymyslnych ksztaltach, i bez ograniczen wzgledem grubosci elementow korpusu typowych dla zeliwa.
U nas problem moze wystapic np z ograniczeniem skurczu (ktory obecnie jest nieznany), czy tez rozszerzalnosci termicznej. Jednak te rzeczy sa do przeskoczenia za pomoca odpowniednich zywic i kilku testow. W kazym razie nie jestesmy tak daleko.
Dla porownania zdjecie komercyjnego $$ odlewu jednej z niemieckich firm:
(przy okazji widac sposob umieszczania insertow pod sruby)
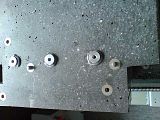
Z poczatku studiowalem technologie kwarcowych blatow kuchennych

Jednak przy produkcji stosuja wielkie $20mil prasy ktore podgrzewaja, wibruja i odpowietrzaja w tym samym czasie. Sa to wielotonowe prasy, w gre wchodza tez powazne temperatury i generalnie uzywaja oni innych zywic, glownie poliestrowych; utwardzacze uruchamiane sa za pomoca temperatury. Z informacji wynika ze sa w stanie scisnac material do 1/4- 1/2 oryginalnej grubosci. Caly proces zostal wynaleziony ponad 40 lat temu przez Wlochow i o ile wiem jest uzywany przez wszystkich producentow blatow kuchennych- roznia sie tylko kolory wypelniaczy i niektore skladniki. Znaczyloby to ze jest tylko jeden sposob na tego typu odlewy.
* * *
Ok, powrot do mojej maszyny.
Gorna belka wyszla bardzo solidnie- nie pozostawalo nic innego jak tylko powtorzyc wysilek przy nogach portalu- te 3 elementy w sumie stanowia najbardziej krytyczna czesc calej maszyny. Wymiary nog to 14cm grubosc, calosc w kwardracie 48x48cm.
Belka wazy niecale 75kg i bez zbednych ceregieli bedzie osadzona na 2 prostokatnych blokach aluminium o grubosci 38mm. Normalnie tego typu maszyna bylaby odlana w calosci- niestety konstrukcja musi byc przenosna i stad cala masa niepotrzebnych powierzchni laczacych, komplikacji oraz co za tym idzie wibracji. Jest to moja pierwsza konstrukcja wiec mam nadzieje ze ujdzie mi to na sucho

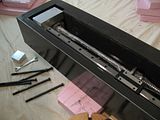
Aluminiowe bloki zostaly nawiercone i beda osadzone na pionowo ustawionych stalowych podporach. Z drugiej strony beda wystawaly sruby sluzace do przykrecenia belki. Tego typu stalowe podpory zauwazylem u jednego z producentow maszyn CMM. Mimo ze te maszyny nie pracuja pod zadnym obciazeniem, w obu scianach portalu byly grube stalowe prety podparte dwuteownikiem. Stal byla specjalnie dobrana i zdaje sie przyczyniala sie do stabilnosci termicznej calej konstrukcji.
Material na podpory:
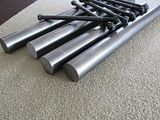
Calosc przypomina raczej budowe pomnika niz maszyny i musze przyznac ze sprawia mi niezla frajde- nie musze martwic sie rysunkami, tolerancjami, pasowaniami i cala reszta rzeczy ktora spedza sen z powiek innych budowniczych maszyn.
Po dosyc czasochlonnym ustawianiu wszystkiego za pomoca poziomnicy calosc zostala skrecona srubami i zalana zywica w celu uzyskania precyzyjnego odcisku powierzchni laczacych. Srodek belki zostal wylozony 0.01mm folia do kanapek, niektore czesci zostaly tez zaslepione. Zbyt ciasne zalanie wszystkich fragmentow spowodowaloby trudnosci przy pozniejszym pasowaniu elementow.
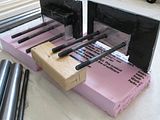
Powyzsze elementy zostaly wmontowane do formy i uzyte do zrobienia finalnego odlewu. Tak mialo to wygladac po osadzeniu belki:
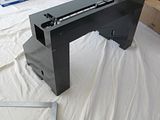
Obie nogi maja na spodzie nawiercone listwy aluminiowe ktore posluza mocowaniu nastepnych elementow.
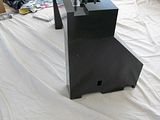
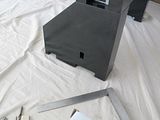
Odlewy zostaly wyjete z formy po ok tygodniu. Bylo tez kilka niedorobek, szczegolnie w poblizu otworow na spodzie- poprawki zostaly wokonane za pomoca dluta i grubego papieru sciernego i wykonczone za pomoca zywicy/drobnego wypelniacza.
* * *
Po skonczeniu obu odlewow przyszedl czas na test ugiecia belki. Do odlewu uzywalem najprostszych drewanianych form i jak pamiatamy byly podejrzenia co do pozniejszej dokladnosci/stabilnosci.
Prostolinijnosc powierzchni bazowych belki zostala sprawdzona za pomoca precyzyjnego linialu stalowego (dokladnosc linialu 0.07mm na dlugosci 1800mm). Przy uzyciu mocnego swiatla bez problemu mozna zauwazyc szczeliny rzedu 0.02mm- badalem calosc przed i po zalaniu zywica i nie stwierdzilem zadnych widocznych odksztalcen. Uwazam wiec ze pierwotny ksztalt zostal zachowany. Jesli byly jakies znieksztalcenia to sa one w granicach bledu pomiarowego.
Drugi wazny test to obciazenie belki i sprawdzenie ugiecia. Zgodnie z zalozeniami, konstrukcja miala uniesc wlasna mase plus sily skrawania plus wage doroslego mezczyzny stajacego na maszyne podczas obrobki.

Do testu cala konstrukcja zostala skrecona i ustawiona na stabilnym podlozu. Belka zostala obciazona na srodku. Dwa widoczne powyzej stalowe bloki zostaly przykryte gruba plyta na ktorej byly ukladane obciazniki (pudla z piaskiem).
Test odbyl sie dwukrotnie- z pomoca wyzej wspomnianego linialu oraz czujnika. Czujnik zostal oparty o dolna powierzchnie bazowa belki:
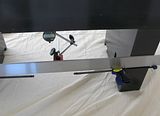
W calosci udalo mi sie polozyc na belke 255kg. Przy takim obciazeniu dolna powierzchnia bazowa belki odksztalcila sie 0.0025mm.
Faktem jest ze czujnik nie ma certyfikatu kalibracji a domowe metody pomiarowe pozostawiaja wiele do zyczenia. Nie spodziewalem sie jednak niczego w poblizu takiego wyniku i przyznam ze jest to mile zaskoczenie.
Tym bardziej ze cala konstrukcja jest raczej lekka (jak na epoxy-granitowe standardy) i nie byla planowana pod katem obrobki materialow twardych.
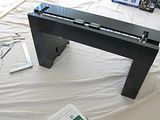
Pozdrowienia!