Mini wrzeciono BLDC
-
- Lider FORUM (min. 2000)
- Posty w temacie: 10
- Posty: 2692
- Rejestracja: 08 gru 2009, 22:33
- Lokalizacja: Elbląg
- Kontakt:
-
- Lider FORUM (min. 2000)
- Posty w temacie: 10
- Posty: 2692
- Rejestracja: 08 gru 2009, 22:33
- Lokalizacja: Elbląg
- Kontakt:
Trzymany w imadle był silnik?smouki pisze:wybijakiem się udało
Generalnie trochę się zmartwiłem po obejrzeniu takich poradników.
-
- ELITA FORUM (min. 1000)
- Posty w temacie: 8
- Posty: 1744
- Rejestracja: 03 sty 2007, 14:27
- Lokalizacja: Wiedeń
tak dla obudzenia tematu
Zacząłem pracę nad drugą wersją swojego wrzeciona - "myśl przewodnia" taka sama jak poprzednio ale z lepszymi łożyskami, silnikiem i poprawione błędy konstrukcyjne które wyszły przy budowie pierwszego modelu.
Na początek projekt:
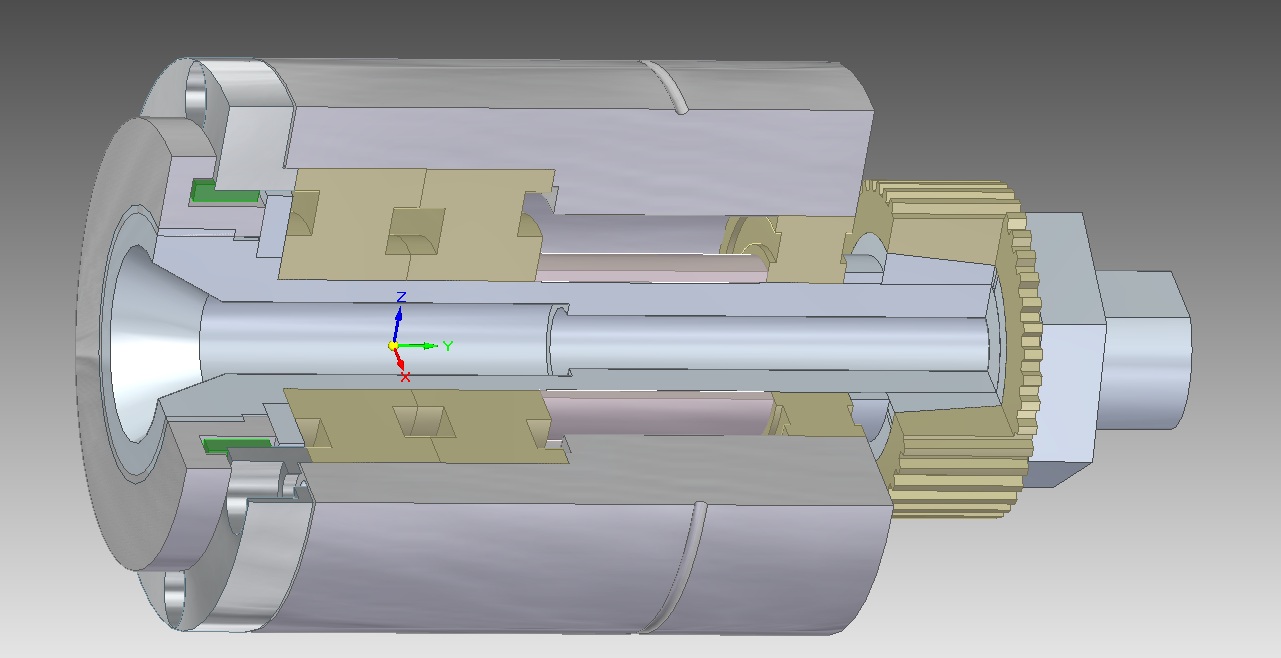
łożyska główne to SKF7201BEP (nie jest to klasa polecana do wrzecion ale do zabawy powinny wystarczyć) tylne 6901Z.
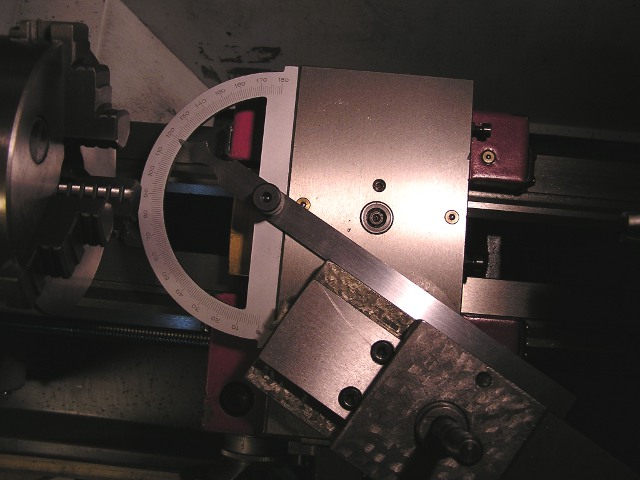
Pracę zacząłem od ustawienia kąta stożka (łatwiej to zrobić na czystej tokarce
)
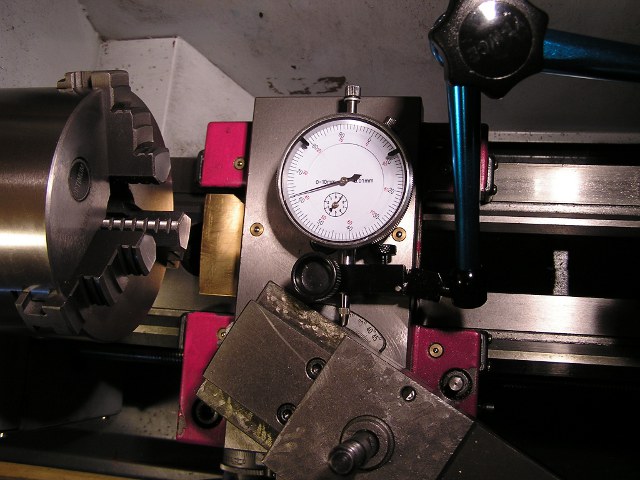
I skontrolowania go czujnikiem - dla kąta 30 stopni, po przesunięciu sanek czujnik powinien się odchylić o 8.66mm, jak widać (albo i nie) - pokazuje trochę mniej - 8.62. Jest to celowe - chodzi o to żeby tulejki były "łapane" za szeroki koniec
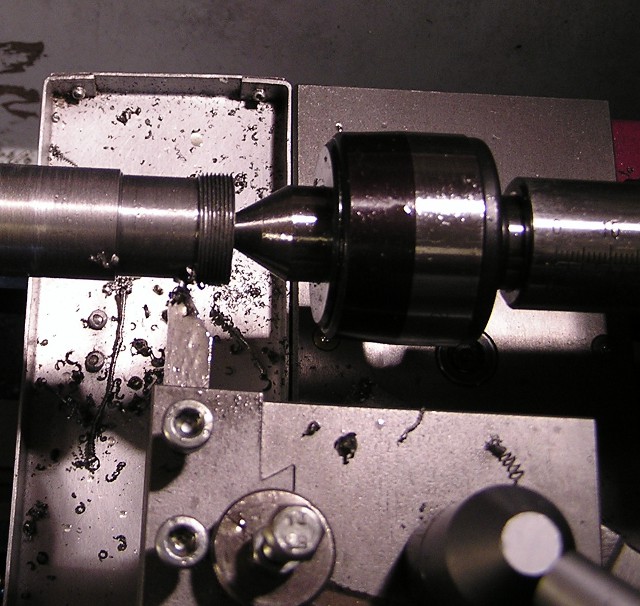
Gwint do mocowania kołnierza osłaniającego przed kurzem
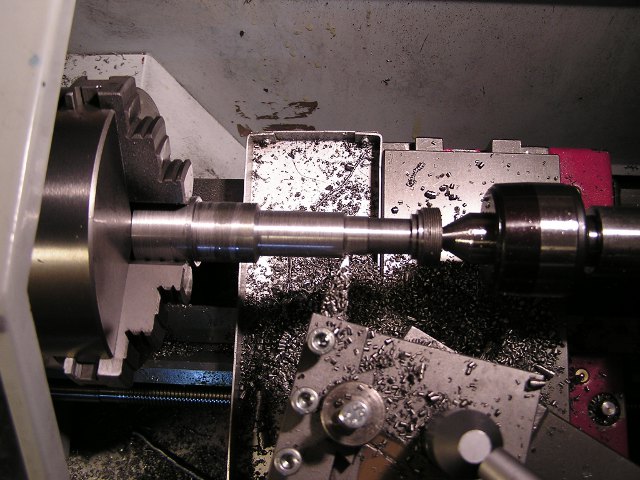
I stopniowe zgrubne wydobywanie średnicy zewnętrznej (zostawiłem 0.5mm na obróbkę końcową). Przypuszczam że lepiej by było najpierw zrobić wnętrze wrzeciona a potem, stopniowo, "odkopywać" kolejne fragmenty wrzeciona - zostawiając możliwie dużo materiału pomiędzy miejscem obróbki a uchwytem.
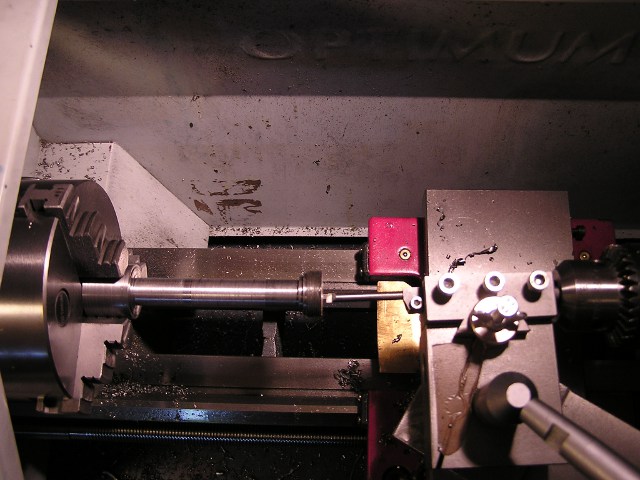
Rozwiercanie średnicy wewnętrznej - 8mm średnicy 33mm głębokości, narzędzie to stałka HSS 4mm średnicy. Od tego momentu cała obróbka jest robiona bez podparcia - mój konik jest o trochę zbyt wysoki i przy podparciu kłem nie ma co liczyć na dużą dokładność
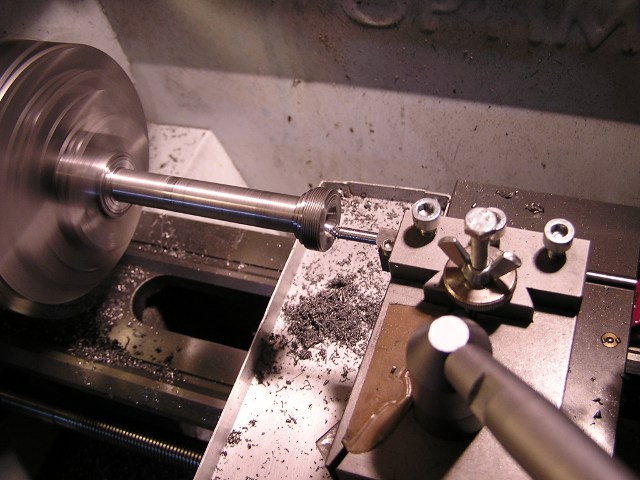
Stożek - bogu dzięki można już było schować większość noża
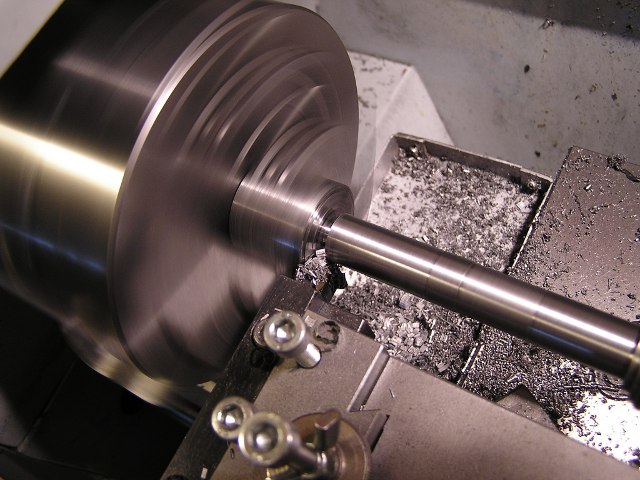
obcianie
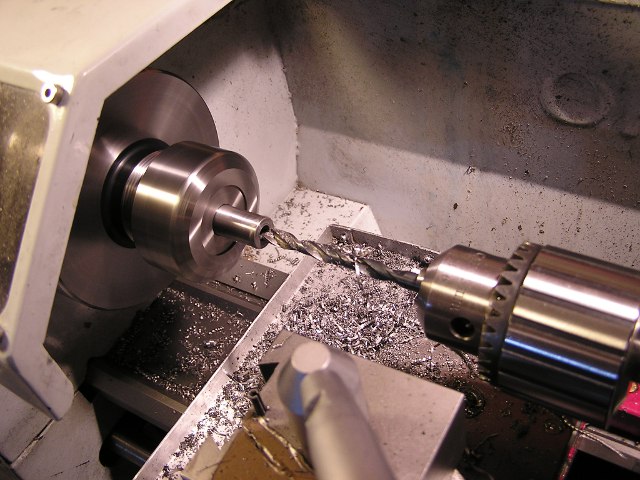
i wiercenie "od tyłu" - w tulejce zaciskowej. Między innymi ze względu na tą operacją kołnierz o który opierają się łożyska jest zrealizowany jako oddzielna część - inaczej główka wrzeciona nie zmieściłaby się się w uchwycie
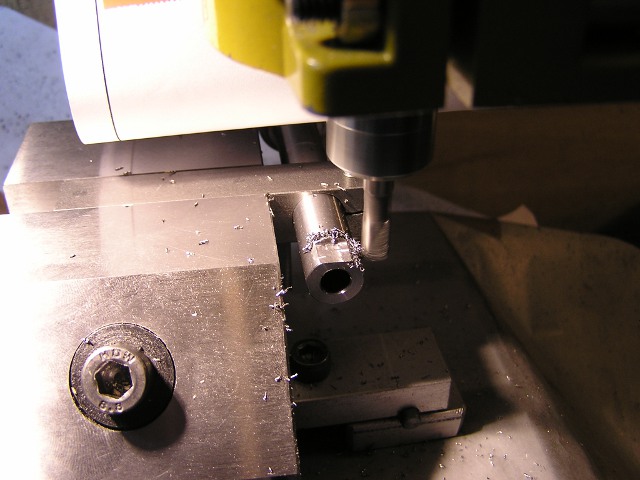
płaszczyzny pod klucz
No i wrzeciono z zamontowanymi łożyskami - próba oszacowania bicia (pomiarowcy proszeni są zażycie waleriany przed obejrzeniem zdjęcia
)
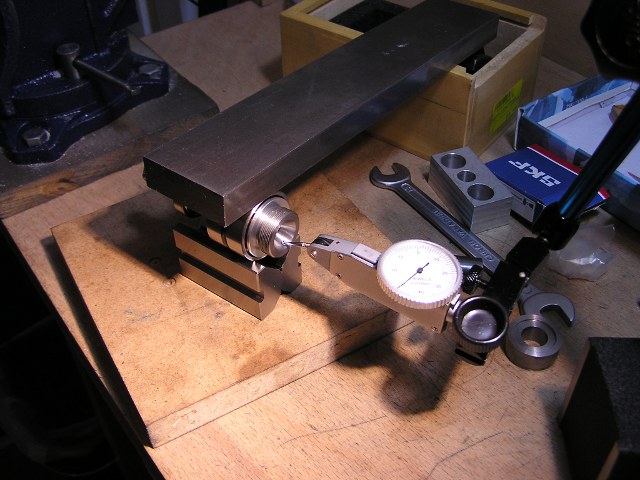
Wynik "pomiaru" - dużo poniżej 0.01mm, chyba nieźle...
Pozdrawiam
Grzesiek
Na początek projekt:
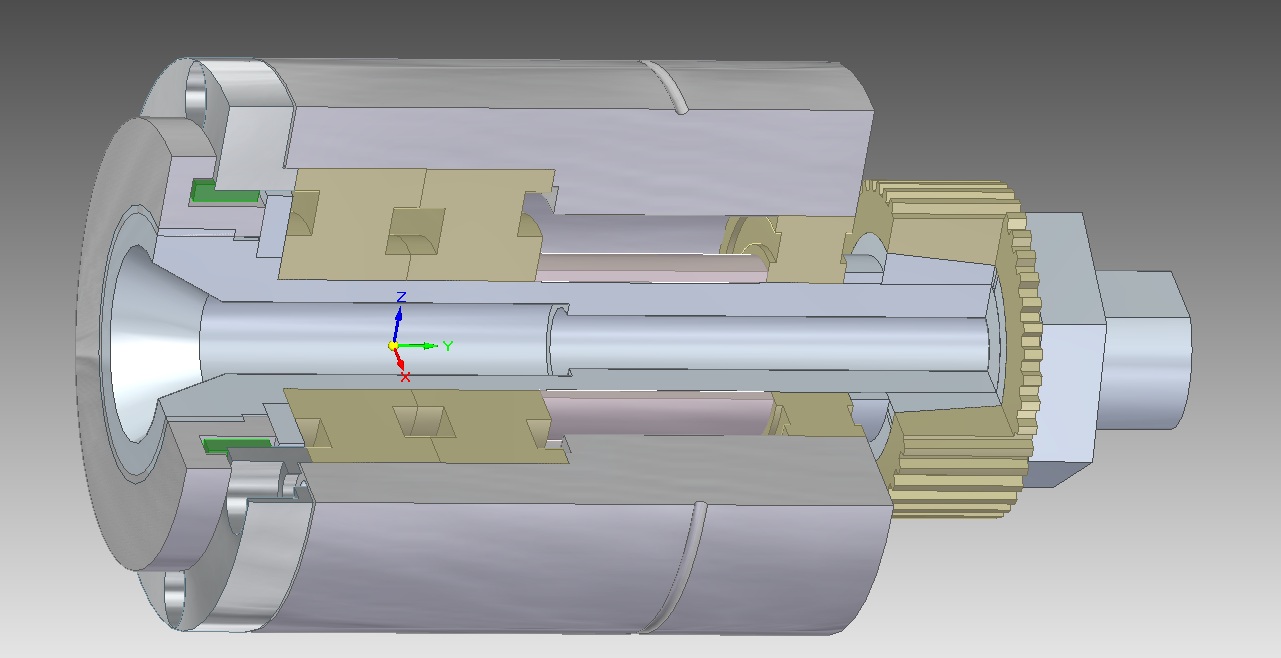
łożyska główne to SKF7201BEP (nie jest to klasa polecana do wrzecion ale do zabawy powinny wystarczyć) tylne 6901Z.
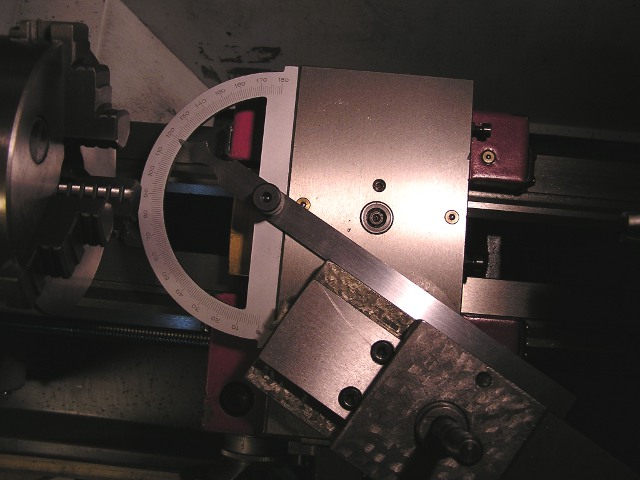
Pracę zacząłem od ustawienia kąta stożka (łatwiej to zrobić na czystej tokarce

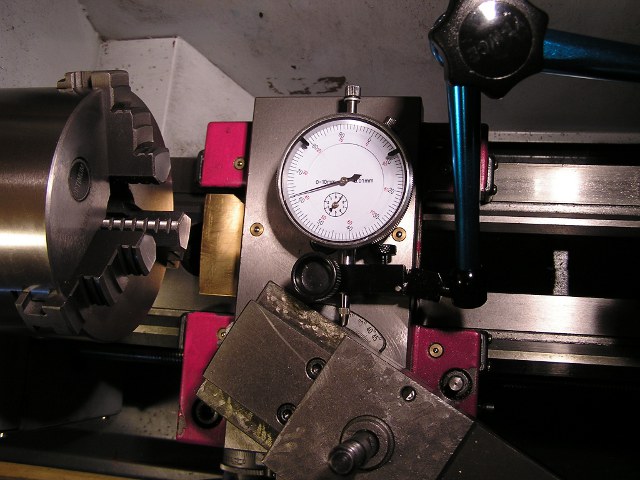
I skontrolowania go czujnikiem - dla kąta 30 stopni, po przesunięciu sanek czujnik powinien się odchylić o 8.66mm, jak widać (albo i nie) - pokazuje trochę mniej - 8.62. Jest to celowe - chodzi o to żeby tulejki były "łapane" za szeroki koniec
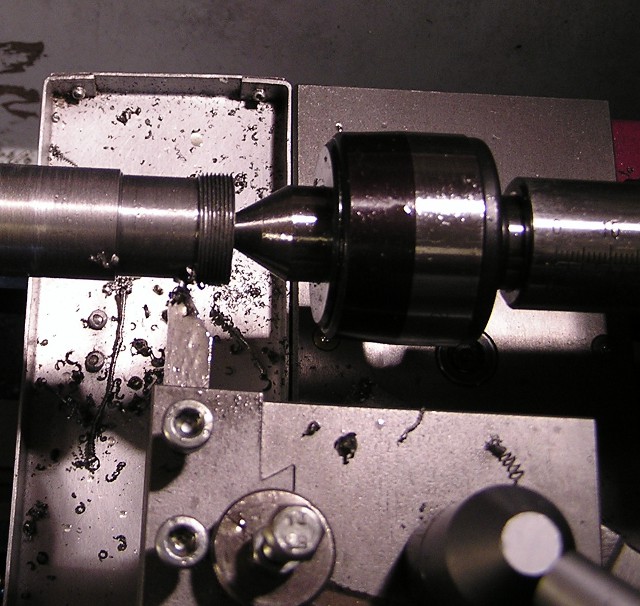
Gwint do mocowania kołnierza osłaniającego przed kurzem
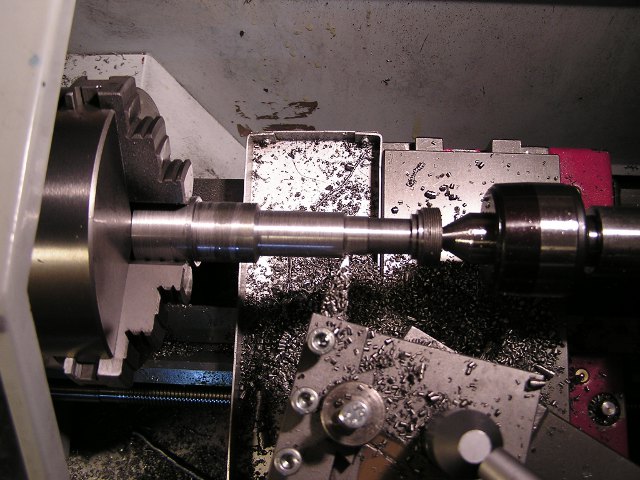
I stopniowe zgrubne wydobywanie średnicy zewnętrznej (zostawiłem 0.5mm na obróbkę końcową). Przypuszczam że lepiej by było najpierw zrobić wnętrze wrzeciona a potem, stopniowo, "odkopywać" kolejne fragmenty wrzeciona - zostawiając możliwie dużo materiału pomiędzy miejscem obróbki a uchwytem.
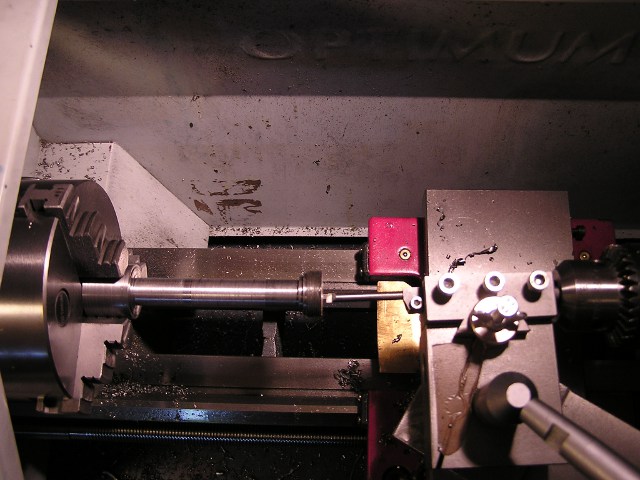
Rozwiercanie średnicy wewnętrznej - 8mm średnicy 33mm głębokości, narzędzie to stałka HSS 4mm średnicy. Od tego momentu cała obróbka jest robiona bez podparcia - mój konik jest o trochę zbyt wysoki i przy podparciu kłem nie ma co liczyć na dużą dokładność
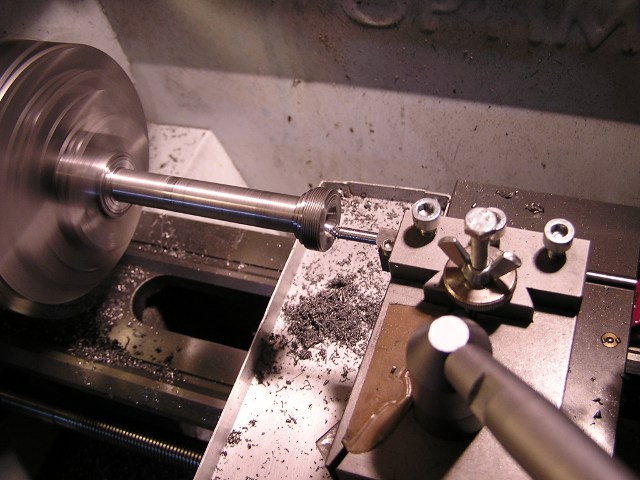
Stożek - bogu dzięki można już było schować większość noża
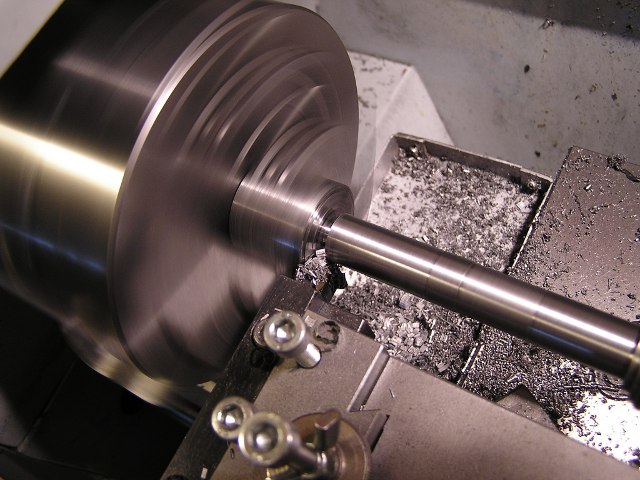
obcianie
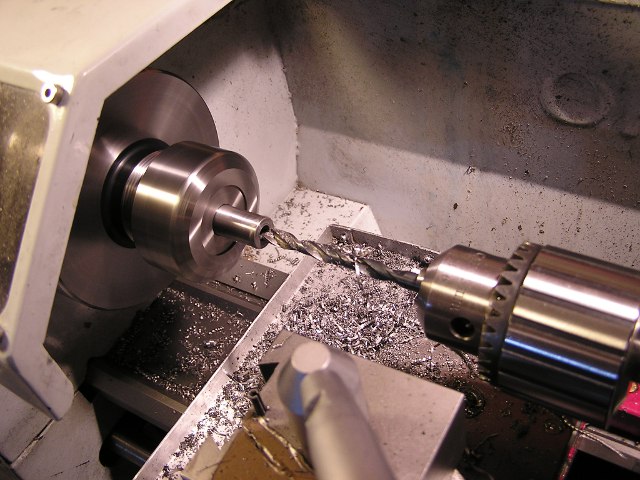
i wiercenie "od tyłu" - w tulejce zaciskowej. Między innymi ze względu na tą operacją kołnierz o który opierają się łożyska jest zrealizowany jako oddzielna część - inaczej główka wrzeciona nie zmieściłaby się się w uchwycie
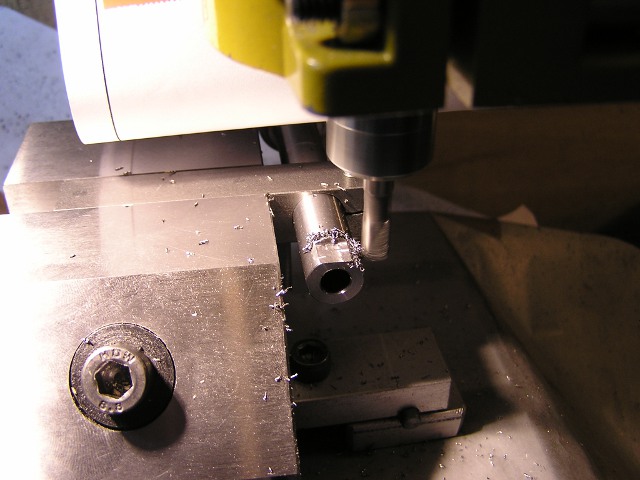
płaszczyzny pod klucz
No i wrzeciono z zamontowanymi łożyskami - próba oszacowania bicia (pomiarowcy proszeni są zażycie waleriany przed obejrzeniem zdjęcia

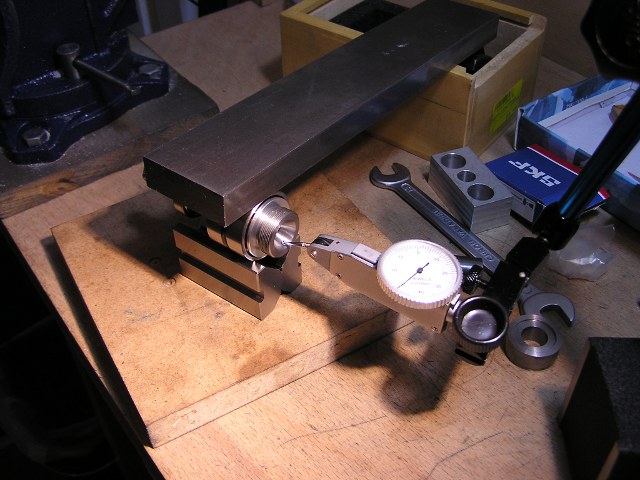
Wynik "pomiaru" - dużo poniżej 0.01mm, chyba nieźle...
Pozdrawiam
Grzesiek