To będzie mój pierwszy post, chociaż z zasobów forum korzystam od dawna.
Po prostu wychodzę z założenia że lepiej wypowiadać się dopiero wtedy, gdy zgromadzimy minimalny zasób wiedzy na dany temat (co by nie narzucać się głupimi pytaniami).
Zaznaczam że nigdy nie miałem osobiście do czynienia z "poważnymi" maszynami, których projekty przewijają się przez to forum.
Jestem jedynie skromnym entuzjastą tematyki "cnc", a jeżeli chodzi o frezarki opieram się w większości na informacjach zdobytych właśnie tutaj.
Wielu hobbystów-amatorów zaczyna przygodę od jakiegoś drewniaka lub pająka z profili, który daje na początku dużo frajdy i pozwala poznać podstawy zagadnienia.
Bardzo szybko jednak dochodzimy do wniosku, że taka konstrukcja posłuży nam tylko i wyłącznie do zabawy...
Otóż właśnie części z mojego pierwszego "maleństwa" wylądowały w rep-rapie (grzanie-24V/RUMBA/DRV8825/0,8Nm

Teraz kolej na następny krok - trzeba zdecydować się na projekt maszynki, która znajdzie praktyczne zastosowanie.
W związku z tym, mam propozycję skierowaną do kolegów, którzy (podobnie jak ja) doszli do wniosku że profile konstrukcyjne i płyty meblowe już ich nie satysfakcjonują

Dotyczy to także osób, które (podobnie jak ja) nie posiadają odpowiednich narzędzi/umiejętności i warsztatu do zabawy ze stalą/żeliwem/(epoxy)granitem/itp.
A na pewno tych, którzy zebrali w skarpecie sporą ilość gotówki

Teraz pewnie wszyscy zastanawiają się o jaką niedwuznaczną propozycję chodzi...

Zasadniczy problem polega na tym, że żaden inżynier pracujący w oprogramowaniu CAD/CAM, a przy tym dobrze znający zagadnienie budowy maszyn, nie będzie miał czasu ani chęci żeby zająć się tzw. "otwartym" projektem i udostępnić nam efekty swojej pracy.
A gdyby tak zajął się tym jakiś entuzjasta-amator (ja

Jednym słowem, proponuję coś w rodzaju FabLab-a (którym to forum w pewnym sensie już się stało).
Efektem pracy będzie dokumentacja i modele elementów ramy frezarki, opublikowane jako tzw."Open-Hardware" (w jakimś popularnym formacie - do uzgodnienia).
Generowanie gotowych ścieżek w CAM-ie uważam za niezasadne, ze względu na ewentualne różnice w użytych narzędziach, funkcjach specjalnych i charakterystykach różnych maszyn.
Skupił bym się tu jedynie na opisie sposobu zamocowania danego detalu, kolejności obrabiania płaszczyzn, oraz sugestiach dotyczących rodzaju i średnicy narzędzia stosowanego przy obróbce danej płaszczyzny - zaś sam gcode zostawiając wykonawcy.
Koledzy, którzy pomogą w realizacji zapewne zyskają bardzo wiele: wieczną sławę i szacunek


Pojawia się tu okazja dla operatorów maszyn z szanownego forum na zwiększenie ilości zleceń, jeżeli tylko wyjdzie nam taki "gotowiec"...
Oczywiście marzenia, marzeniami, a rzeczywistość wszystko zweryfikuje...
Być może proponowany model frezarki już w założeniach posiada poważne błędy konstrukcyjne i na zawsze pozostanie jedynie wytworem mojej chorej wyobraźni

Być może koszty realizacji zniechęcą na starcie, albo po prostu wszyscy wyśmieją taki pomysł (chociaż idea raczej szlachetna).
Teraz do meritum...
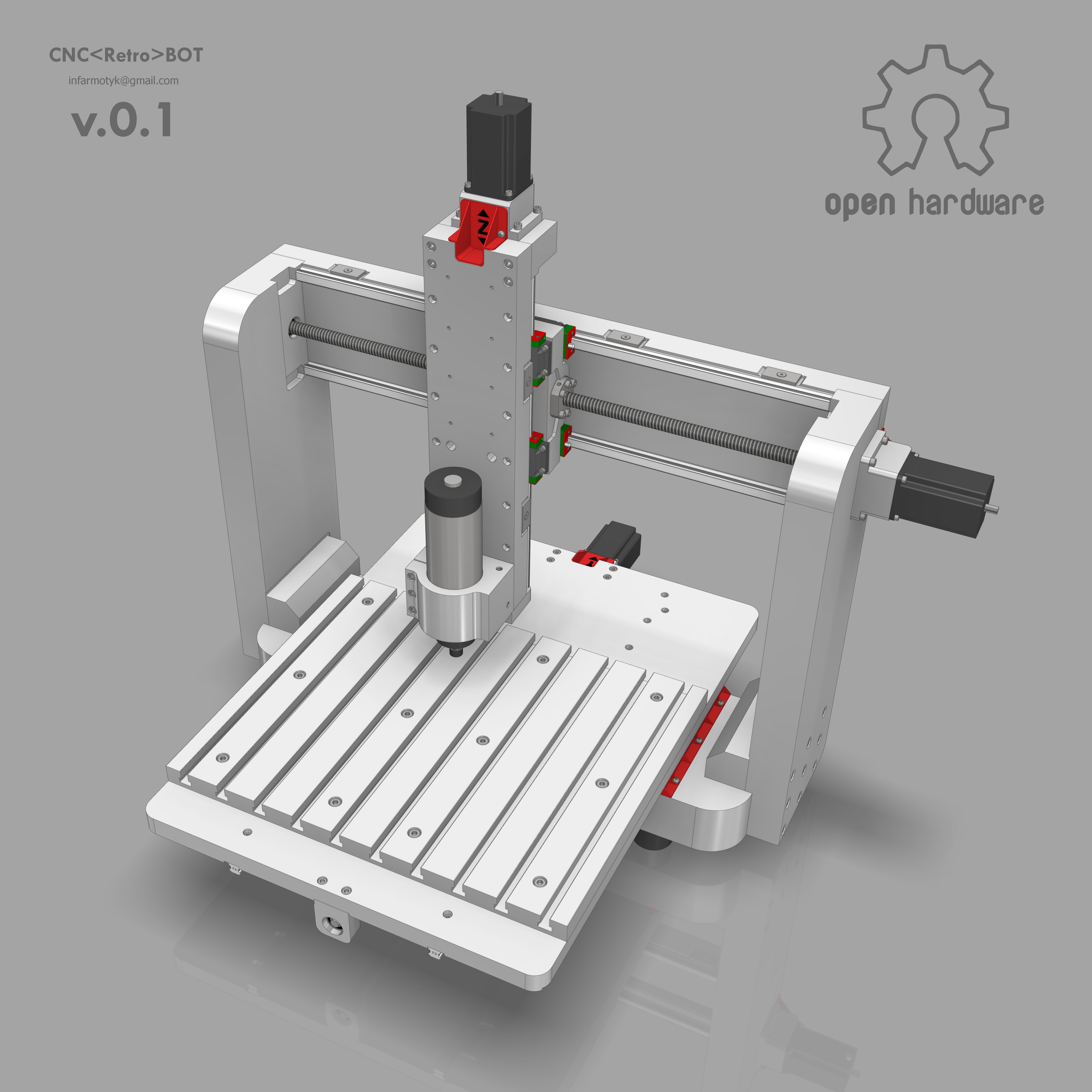
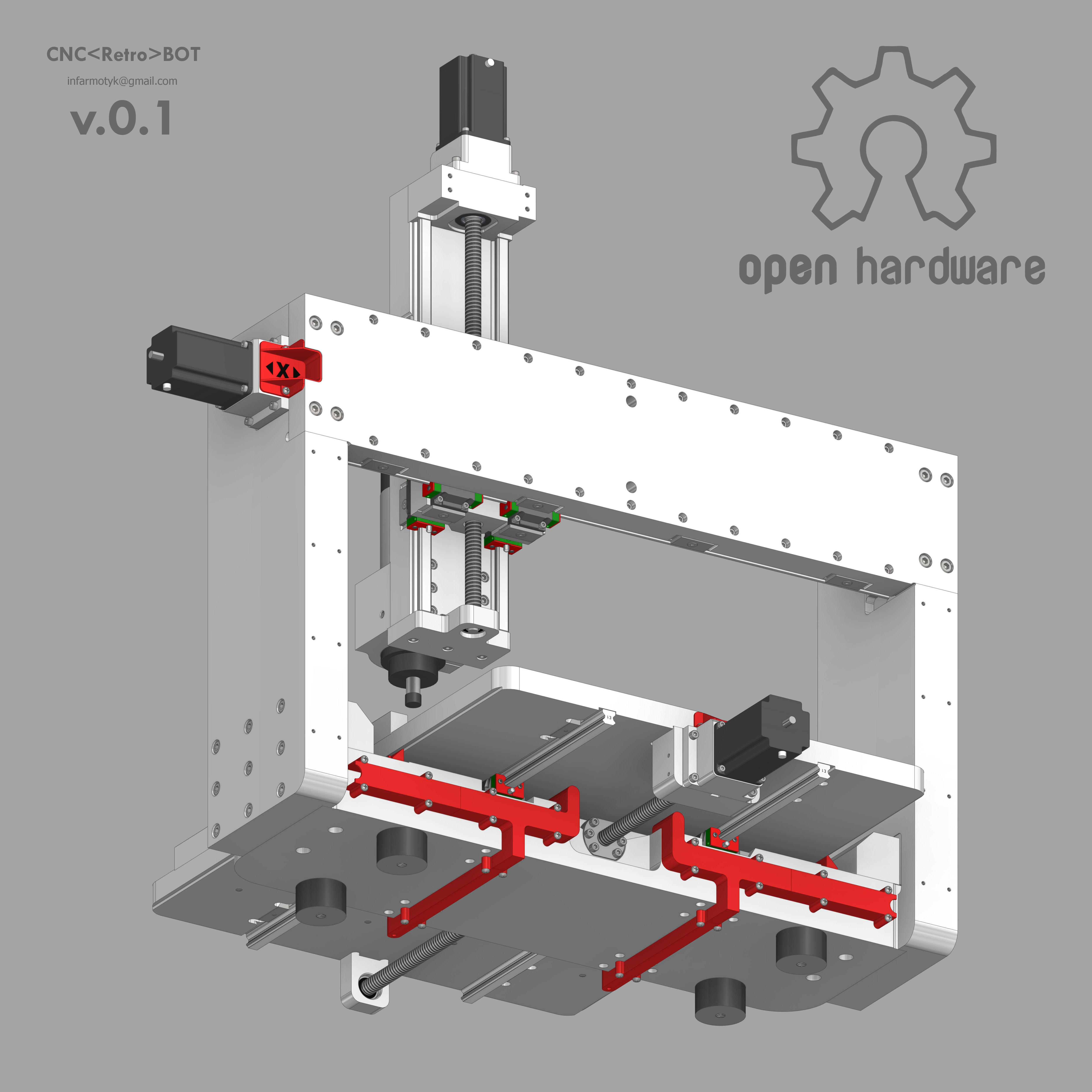
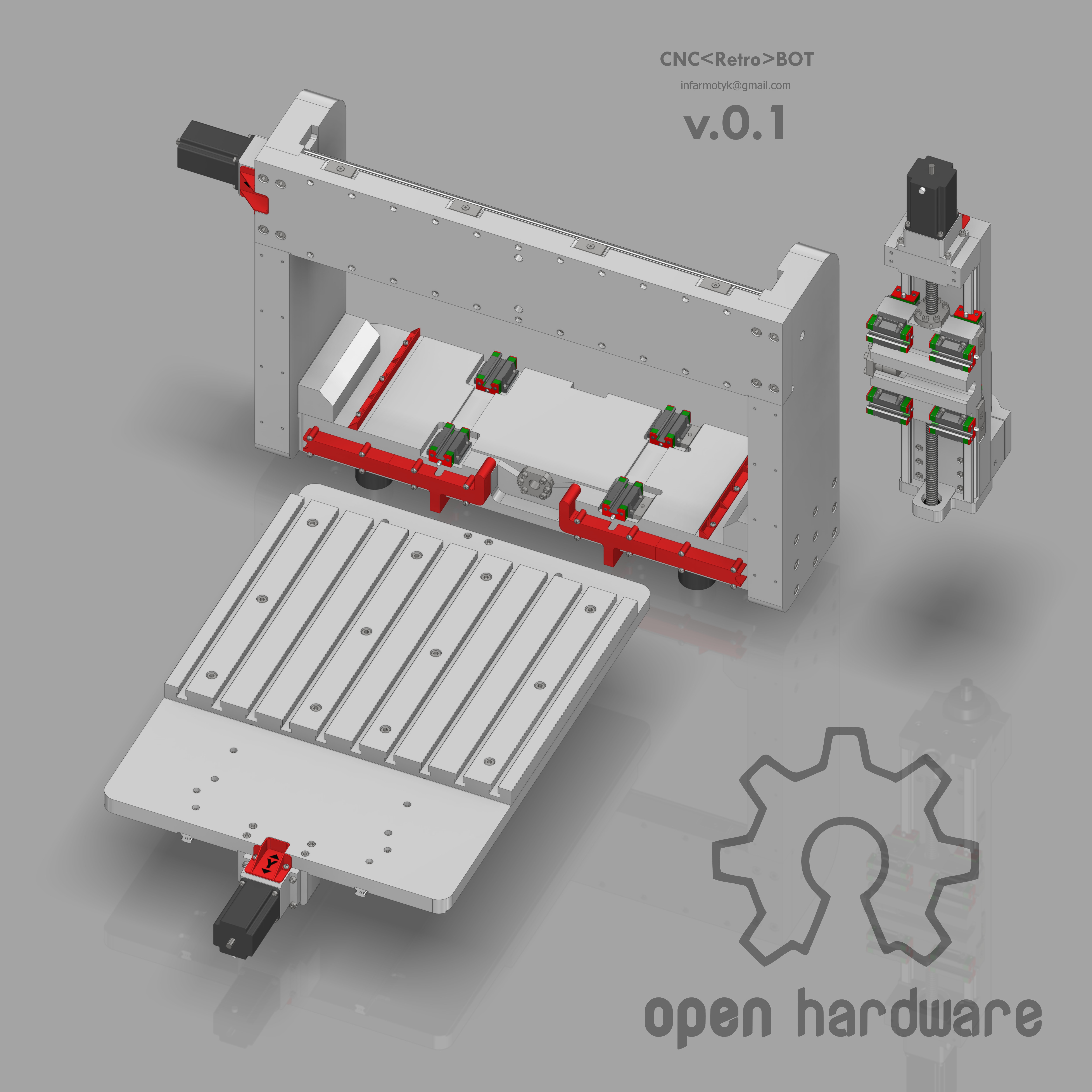
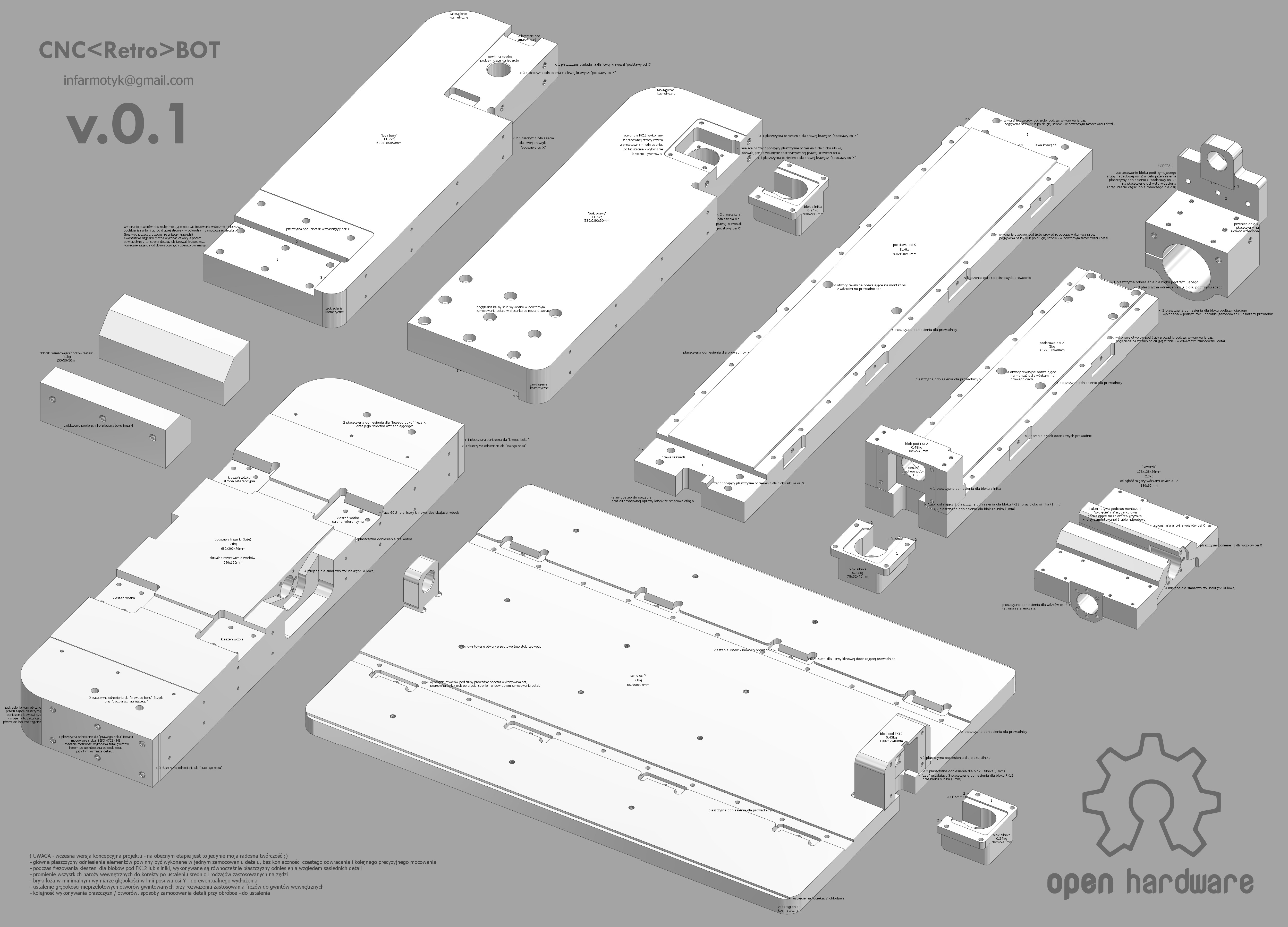
Założenia konstrukcyjne:
01. Z przeznaczeniem do wymagających precyzji prac modelarskich (przede wszystkim obróbka aluminium, przy maksymalnej średnicy frezu 6mm).
02. Wózki liniowe HIWIN HGW15CC i prowadnice HGR15T we wszystkich osiach (nabyłem okazyjnie na forumowej giełdzie).
03. Śruby kulowe HIWIN i nakrętki R16 05T3 FSIDIN we wszystkich osiach (ostatecznie chińskie odpowiedniki).
04. Łożyskowanie strony napędowej - FK12 we wszystkich osiach (ewentualnie jakaś alternatywa ze smarowniczką łożysk).
05. Bezpośrednie przeniesienie napędu - krokowce z dużym zapasem mocy.
06. Materiał ramy: Aluminium PA13, odlewane - formatki dodatkowo odprężane przed obróbką (jeżeli to konieczne).
07. Materiał osłon, prowadników kabli, drobnych detali, itp.: ABS (druk 3D - służę pomocą jak wszystko wypali).
08. Prosta w montażu, skręcana konstrukcja ramy pozwalająca na redukcję koszów materiałowych, przy zachowaniu rozsądnej masy.
09. Każdy element ramy posiadający 3 płaszczyzny odniesienia, względem sąsiedniego/sąsiednich elementów (tam gdzie będzie to możliwe/potrzebne).
10. Płaszczyzny odniesienia elementów ramy wykonane w jednym zamocowaniu detalu (frezowanie walcowo-czołowe).
11. Brak zabawy z ustawianiem geometrii - po prawidłowym skręceniu ramy, geometria wszystkich osi względem siebie powinna być zachowana (no chyba że będzie krzywo pofrezowane).
12. Dociski prowadnic i wózków jako stałe elementy konstrukcji (dodatkowe wzmocnienie boczne, szczególnie dla wózków po stronach referencyjnych).
13. Uchwyty 65mm dla mokrego chińczyka i 43mm dla Kress-a.
14. Możliwość obróbki "własnego" (wymiennego) stołu teowego.
15. Duży prześwit między bokami frezarki (aktualnie 660mm).
16. Miejsce pod Z-tką dla czwartej osi.
17. Centralne smarowane dla wózków i nakrętek kulowych (alternatywa dla drogich, komercyjnych rozwiązań - w dalszym etapie).
18. Mobilna, poziomowana obudowa/wózek frezarki ze zbiornikiem chłodziwa (w dalszym etapie).
19. Kwestie elektroniki pozostawiam do indywidualnego rozważenia (miejsce na sterowniki i zasilanie za osią X, falownik na lewym boku frezarki).
Minusy konstrukcji:
- Koszt aluminium i obróbki

- Konieczność przykręcenia podstawy frezarki do podłoża, w celu uniknięcia przechyłów całej konstrukcji przy skrajnych pozycjach sanek osi Y.
- Zbyt bliskie rozmieszczenie wózków osi Y w linii posuwu (oszczędność na rozmiarach podstawy frezarki - do korekty).
- Użycie wózków HGW15 w osi Y (ze względu na niski profil wózka z prowadnicą, ale nie wykluczam zmiany na HGW20).
- Problematyczny montaż osi X, oraz śruby kulowej dla tej osi.
- Brzydkie "bloczki wzmacniające" przy bokach frezarki (opierające się naprężeniom ramy i pozwalające oszczędzić na wysokości łoża, zwiększając powierzchnię przylegania boków).
Projekt CAD:
Przypominam, że projekt ten będziemy traktować jako "edukacyjny" oraz "otwarty", a ja nie ponoszę żadnej odpowiedzialności za jakiekolwiek szkody powstałe w wyniku jego ewentualnej realizacji

Wiem że podobne pomysły pojawiały się już na forum, ale chyba żaden nie doszedł do skutku (może będzie tak i tym razem

Żeby wprowadzić jasne zasady, proponuję wykorzystanie w przyszłości licencji CERN OHL 1.2 http://www.ohwr.org/licenses (oczywiście dopiero gdy prototyp będzie trzymał się kupy...)
Wstępny szkic frezarki złożyłem w "wersji próbnej" Inventora. Mam nadzieję że Autodesk się nie obrazi, tym bardziej że dopuszcza do bezpłatnego wykorzystania swojego oprogramowania w celach edukacyjnych.
Docelowo trzeba będzie się przesiąść na "Fusion 360" albo "Free-CADa". Chcę uniknąć łamania jakichkolwiek licencji czy praw autorskich (proszę o zwrócenie uwagi, jeżeli takie zagrożenie wystąpi).
Na obecnym etapie nie uwzględniałem krańcówek, odbojów, przebiegów kabli i elektroniki.
Wszystkie detale traktujemy jako poglądowe, do czasu ustalenia rodzajów i średnic narzędzi zastosowanych do obróbki (wtedy skoryguje np. promienie dla naroży wewnętrznych).
Proszę o pomoc w dobraniu głębokości nieprzelotowych otworów gwintowanych i długości śrub, we wszystkich łączeniach.
Żeby wykonać gwinty na pełnej głębokości otworów i nie martwić się o jakość krawędzi, chciałbym wykorzystać frezy do gwintowania obwodowego (dzięki prowadnicom HGR15T odejdzie tu sporo roboty).
W osi Z zastosowałem blok łożyska wspierającego koniec śruby napędowej. Przenosi on płaszczyznę odniesienia na uchwyt wrzeciona - należy to obecnie traktować tylko jako ciekawostkę, ponieważ tracimy na takim zabiegu sporo pola w Z-tce.
Generalnie starałem się zawsze brać pod uwagę wygodę operatora podczas wykonywania detalu - jak najmniej przekładania i ponownego mocowania.
Pomyślałem też, że przy frezowaniu kieszeni w blokach pod FK12 czy silniki, można wykorzystać wykonane powierzchnie jako płaszczyzny odniesienia dla sąsiednich elementów.
Najwięcej krytyki wywoła pewnie oś Y (łoże i stół), więc skupie się szczególnie na niej...
Całkowita waga stołu (wraz z prowadnicami, płytą teową, silnikiem, itd.) wyniesie około 37kg.
Na maksymalne obciążenie stołu przyjąłem 20kg (dla ewentualnej 4-osi i obrabianego detalu).
Dla siły działającej podczas skrawania ustaliłem z nadmiarem F=800N (na podstawie napotkanych na forum obliczeń dla aluminium, gdzie przy frezie fi10 wyszło około 650N).
Niestety w naszej konstrukcji pozycja środka ciężkości stołu w odniesieniu do wózków będzie zmienna i czasem znajdzie się za nimi.
Wrzeciono znajduje się bezpośrednio nad linią "przedniej pary" wózków, które dodatkowo przy maksymalnym wychyleniu stołu muszą przyjąć większość jego masy z obrabianym detalem (sytuacja skrajna).
W celu przeprowadzenia symulacji dynamicznej użyłem przerobionego modelu wózka - tak by prowadnice przylegały tylko w punktach stycznych dla 4 kulek (po jednej na każdej "bieżni" prowadnicy).
Grapher wypluł następujące wyniki dla obciążenia ("-" przy wartości oznacza przeciwny zwrot siły):
Obciążenie: W=57kg=560N
Rozstaw wózków: 250x150mm
P1,P3: przednia para wózków
P2,P4: tylna para wózków
Gdy środek ciężkości stołu znajduje się dokładnie pomiędzy wózkami:
P=140 N (na każdy wózek)
Gdy środek pola roboczego znajduje się pomiędzy wózkami:
P1= 178 N
P2= 92 N
P3= 176 N
P4= 93 N
Maksymalne wychylenie sanek w tył:
P1= -192 N
P2= 467 N
P3= -194 N
P4= 465 N
Maksymalne wychylenie sanek w tył + dodatkowa siła F działająca z góry nad rogiem pola roboczego:
P1= -90 N
P2= -27 N
P3= 527 N
P4= 973 N
Maksymalne wychylenie sanek do przodu:
P1= 551 N
P2= -284 N
P3= 556 N
P4= -284 N
Maksymalne wychylenie sanek do przodu + dodatkowa siła F działająca z góry nad rogiem pola roboczego:
P1= 376 N
P2= -468 N
P3= 1597 N
P4= -66 N
Podane wartości nie obejmują oczywiście przyśpieszeń/hamowania i prędkości przejazdów; są to siły działające przy nieruchomym stole.
Chwilowo muszę rozwiązać problem w Inventorze z przeniesieniem wartości sił działających na wózki przy uwzględnieniu pracy śruby napędowej.
W symulacji przejazdów powinny zostać wzięte pod uwagę takie parametry jak odległość osi śruby od płaszczyzny ruchu, czy siły poprzeczne działające podczas obróbki detalu w najwyższym położeniu wrzeciona.
Być może aż takie zagłębianie się w obliczenia nie jest tutaj potrzebne i tracę tylko czas...
W dokumentacji prowadnic HIWIN-a spotkałem takie zdanie:
"Jeśli obciążenie odpowiada tylko 10% lub mniej nośności dynamicznej, większa część oporu tarcia powstaje poprzez zgarniacze oraz smar i tarcie między kulkami. Jeśli obciążenie robocze jest większe niż 10% nośności dynamicznej, obciążenie stanowi większą część oporu tarcia".
Jeżeli dla wózka HGW15 Cdyn=11380N to przekraczamy te magiczne 10% tylko w bardzo skrajnych sytuacjach.
Prosiłbym o fachową opinię na temat wytrzymałości/żywotności powyższego układu.
W przypadku "wydłużenia" bryły łoża i zwiększenia odstępu między wózkami w linii posuwu, rozłożymy obciążenia bardziej sprawiedliwie, ale kosztem pola roboczego i ceny użytego materiału.
Dobrze było by rozmieścić wózki na planie kwadratu, ale wtedy pole robocze w osi Y zmniejszy się o połowę. Myślę że trzeba wypracować tu jakiś kompromis...
Analiza naprężeń dla stołu, czy łoża przy maksymalnym obciążeniu (1360N) nie wykazała raczej istotnych przemieszczeń (w okolicach otworu na nakrętkę kulową wyszło około 0,002mm).
Montaż ramy:
Wszystkie elementy skręcamy kluczem dynamometrycznym - śrubami w klasie wytrzymałości minimum 8.8.
Siły i stopniowanie docisku poszczególnych śrub ramy, listew klinowych i płytek dociskowych wózków/prowadnic - do ustalenia.
Elementy ramy podczas skręcania dociskamy do wzajemnych płaszczyzn odniesienia np. dużymi zaciskami stolarskimi (można też zaimprowizować jakąś drewnianą ramę zaciskową).
Łby śrub po montażu trzeba będzie zabezpieczyć przed odkręcaniem jakimś dedykowanym środkiem (np. Loctite - do ustalenia).
A. Blok "podstawy frezarki" (łoże) przykręcamy przez wibroizolatory do wypoziomowanego stołu/wózka.
B.1. Przygotowujemy sanie osi Y, dociskając i przykręcając prowadnice liniowe w/g zaleceń producenta.
B.2. Zakładamy wózki na prowadnice, powierzchniami odniesienia do wnętrza osi Y - ustawiamy je po środku sań w odmierzonych pozycjach, aby mogły wpasować się w kieszenie na "podstawie frezarki" (wózki trzeba przykleić kawałkami taśmy, żeby się nie rozjechały).
B.3. Ostrożnie ustawiamy sanie osi Y na "podstawie frezarki", uważając żeby wózki nie zaczepiły o krawędzie swoich kieszeni (sanki ważą około 22kg i mamy tutaj tylko kilka milimetrów luzu, więc lepiej robić to przy czyjejś pomocy).
B.4. Dosuwamy wózki po stronie referencyjnej do powierzchni odniesienia (z nimi przesuwamy całe sanie) i upewniamy się, że gwintowane otwory we wszystkich wózkach są w jednej osi z otworami śrub w "podstawie frezarki".
B.5. Wkręcamy wstępnie śruby mocujące wózków i dokręcamy listwy klinowe po stronie referencyjnej - ostatecznie dokręcamy wszystkie wózki w/g zaleceń producenta.
C.1. Na "podstawę frezarki" zakładamy "prawy bok" ramy (strona napędowa osi X) - dociskamy go do płaszczyzn odniesienia, dokręcając po kolei śruby.
C.2. Przykręcamy "bloczek wzmacniający" boku, dokręcając go stopniowo - na zmianę - od strony boku i od spodu łoża.
C.3. Przygotowujemy oś X, dociskając i przykręcając prowadnice liniowe w/g zaleceń producenta.
C.4. Na prowadnice zakładamy wózki, powierzchniami odniesienia do wewnątrz osi X (możemy je okleić na czas montażu, żeby nie zjechały).
C.5. Ustawiamy "lewy bok" na podstawie i wkręcamy śruby mocujące, zostawiając kilku-milimetrowy "luz" (bok może się teraz przechylać, więc trzeba go czymś podeprzeć do czasu założenia osi X).
C.6. Zakładamy "podstawę osi X", wsuwając jej koniec na "prawy bok" (uważamy z tej strony na "ząb" podający płaszczyznę dla bloku silnika), następnie drugi koniec ustawiamy na "lewym boku", który musimy wcześniej delikatnie odsunąć na pozostawionym "luzie", żeby się wpasować.
C.7. Wkręcamy wstępnie śruby mocujące "podstawy osi X" oraz dosuwamy i dokręcamy bardziej "lewy bok" - pozostawiając nadal minimalny luz.
C.8. Teraz, dociskając wszystkie elementy do swoich płaszczyzn bazowych, możemy ostatecznie skręcić "lewy bok" i jego "bloczek wzmacniający" (analogicznie jak z prawej strony), następnie dokręcamy śruby mocujące "podstawę osi X" do boków.
D.1. Po środku osi X ustawiamy dolną parę wózków, zaś górną parę rozsuwamy na boki - na dolnych wózkach ustawiamy odpowiednią powierzchnią odniesienia "krzyżak osi XZ".
D.2. Teraz wjeżdżamy górną parą wózków "za krzyżak" (mamy tu 0,5mm odstępu, żeby się nimi zmieścić) i upewniamy się, że otwory montażowe we wszystkich wózkach są w jednej osi z gwintowanymi otworami w "krzyżaku".
D.3. Wkręcamy wstępnie śruby wózków nad i pod "podstawą osi X", następnie w miejscach zakrytych bryłą osi X korzystamy z "otworów rewizyjnych" pozwalających na montaż pozostałych śrub.
D.4. Przykręcamy płytki dociskowe wózków po stronie referencyjnej i ostatecznie dokręcamy wózki (w/g zaleceń producenta).
E.1. Jeżeli posiadamy śrubę kulową osi X zakupioną z założoną nakrętką, musimy odkręcić ją na tulejkę zabezpieczającą kulki (w/g instrukcji producenta - tylko co wtedy z naprężeniem wstępnym?).
E.2. Wkładamy nakrętkę kulową osi X do krzyżaka i wkręcamy wstępnie jej śruby mocujące, następnie dosuwamy krzyżak do "lewego boku" (strona podtrzymania śruby napędowej).
E.3. Na zakończeniu śruby kulowej montujemy blok łożyskujący FK12, po czym wprowadzamy jej drugi koniec przez otwór w boku od strony napędowej (śrubę możemy czymś owinąć, żeby nie zarysować gwintu kulowego i otworu).
E.4. Wkręcamy gwint kulowy w nakrętkę aż "zakończenie" śruby przejdzie przez cały "krzyżak" - tulejka zabezpieczająca kulki nakrętki powinna zostać wypchnięta otworem.
E.5. Zakładamy na śrubę po stronie podtrzymującej łożysko i wpasowujemy się nim w otwór w "lewym boku", teraz musimy wpasować się blokiem łożyskującym FK12 w otwór po stronie napędowej.
E.6. Przykręcamy blok łożyskujący i kręcimy śrubą kulową, ustawiając krzyżak na środku osi X - teraz możemy ostatecznie dokręcić nakrętkę kulową (w/g zaleceń producenta).
E.!. Alternatywa bez ściągania nakrętki kulowej (zachowujemy naprężenie wstępne): zastosowanie "wycięcia" wzdłuż krzyżaka, umożliwiającego jego założenie po zamontowaniu śruby - podczas zakładania śruby, jej koniec od strony napędu powinien przejść pod kątem przez otwór od wewnętrznej strony boku; potem montaż FK12 i wpasowanie nakrętki.
F.1. Przygotowujemy sanie osi Z, dociskając i przykręcając prowadnice liniowe w/g zaleceń producenta.
F.2. Zakładamy wózki na prowadnice, powierzchniami odniesienia do wnętrza osi Z, po czym ustawiamy Z-tkę na stole, zjeżdzając wózkami na dół.
F.3. Podsuwamy po kolei wózki od strony referencyjnej do "krzyżaka" i wkręcając wstępnie śruby mocujące w dostępnych otworach, dosuwamy sie do płaszczyzny odniesienia, następnie podsuwamy wózki z drugiej strony - mamy 0,5mm odstępu, żeby się nimi zmieścić (w miejscach zakrytych bryłą osi Z korzystamy z "otworów rewizyjnych" pozwalających na montaż wszystkich śrub).
...
Dalsze kroki pominę żeby nie przedłużać


Pole robocze traktujemy bardzo "elastycznie" - przy uwzględnieniu wszystkich uwag ustalimy jego realne wymiary po korekcie elementów ramy.
Proszę o komentarze czy istnieje zasadność kontynuowania tego projektu jeżeli chodzi o realną możliwość wykonania detali i rozsądne koszty...
Jeżeli ktoś zechce zerknąć na modele detali to będę zamieszczał na chomiku kolejne wersje w formacie STEP...
CNC-Retro-BOT_v.0.1_STEP.zip