CNC<Retro>BOT Frezarka modelarska 500x400x200 OHW
-
- Specjalista poziom 1 (min. 100)
- Posty w temacie: 1
- Posty: 129
- Rejestracja: 13 lut 2013, 23:17
- Lokalizacja: Plock
Witam, kolego wiem że sie namęczyłeś pokazałeś nie małą wiedzę o cad/cae ale musisz jedno wiedzieć że: przy projektowaniu obrabiarki sztywność to tylko 40% sukcesu zazwyczaj wszystko jest na tyle sztywne "że się nie połamie", ale tu nie chodzi o to symulacja dynamiczna którą przedstawiłeś też nie wiele wprowadza dlatego ze te siły sa ciut większe i ot tyle, najważniejsze niestety tu są drgania a to już wyższa szkoła jazdy oczywiście możesz zrobić analizę modalną poszczególnych częsci ale nie wiesz np jak sie zachowuje wózek z napreżeniem 0.02C a jak 0,08C, spytasz jaki rodzaj wymuszenia? to dobre pytanie nie musze chyba mówić ile jest czynników które potrafią modulować amplitud: obroty wrzeciona, bicie freza, ostrość freza, zamocowanie przedmiotu i pewnie wiele innych których nie da sie przewidzieć. Jeszcze a propo tych wszystkich symulacji to co komplikować życie to że mamy dostępność do fajnych programów to zaleta ale po co kombinować przecierz najwieksze obciażenia działaja gdy cału układ jest na środku i opuszczony wtedy mamy belkę "dźwignię" wystarczy kartka papieru i 5 min i znamy wszystkie siły i reakcje w podporach wtedy przenosimy to na belkę i liczymy ugięcie prostsze i szybsze a nie zastąpi tego żaden program... obciążenia dynamiczne? max waga detalu i zwykła zasada dynamiki newtona i juz mamy gotowy układ sił... Przyjąć max siłę osiową na śrubię od monentu jaki wygeneruje silniki doda jakis tam zapas i liczyć prosty układ belkowy a nie skomplikowany z jakimiś wiązaniami....
Tagi:
-
Autor tematu - Sympatyk forum poziom 1 (min. 40)
- Posty w temacie: 25
- Posty: 47
- Rejestracja: 29 sty 2014, 11:39
- Lokalizacja: Tomaszów Lubelski
Przedstawione obliczenia są jedynie odpowiedzią na sugestię kolegi 251mz, który podpowiedział że max siła która może pojawić się w naszym układzie jest siłą przy której złamie się frez podczas awarii wrzeciona - i taki właśnie zaprezentowałem scenariusz, uwzględniając w nim prędkość posuwu wzdłuż linii osi X. Chodziło mi o zbadanie sił pojawiających się na wózkach, chwilowo bez analizy samej ramy. Zapewne jeszcze większe siły powstaną np. przy zerwaniu detalu z mocowania podczas obróbki, ale jakie to już ciężko przewidzieć... Oczywiście jeżeli podane wartości nie odpowiadają rzeczywistości, bardzo proszę o informację.
Zaznaczam, że wszystkie sugestie kolegów traktuje jak wyrocznie i zamierzam się sumiennie do nich stosować
Przy wymiarowaniu detali zostawiłem sobie możliwość prostej modyfikacji głównych wymiarów brył - po zmianie dosłownie kilku parametrów możemy mieć zupełnie inne proporcje ramy z zachowaniem wszystkich płaszczyzn odniesienia / kieszeni itd.
W wolnym czasie przedstawię "okrojony" model, ale ponownie bardzo proszę o opinię n/t możliwości technicznych wykonania tych detali
Zaznaczam, że wszystkie sugestie kolegów traktuje jak wyrocznie i zamierzam się sumiennie do nich stosować

Przy wymiarowaniu detali zostawiłem sobie możliwość prostej modyfikacji głównych wymiarów brył - po zmianie dosłownie kilku parametrów możemy mieć zupełnie inne proporcje ramy z zachowaniem wszystkich płaszczyzn odniesienia / kieszeni itd.
W wolnym czasie przedstawię "okrojony" model, ale ponownie bardzo proszę o opinię n/t możliwości technicznych wykonania tych detali

-
Autor tematu - Sympatyk forum poziom 1 (min. 40)
- Posty w temacie: 25
- Posty: 47
- Rejestracja: 29 sty 2014, 11:39
- Lokalizacja: Tomaszów Lubelski
Jeszcze raz przejrzałem frezarki dostępne w sprzedaży - oczywiście większość powstało z profili stalowych.
Weźmy np. dedykowaną do obróbki metali kolorowych konstrukcję ONRED KMP45 (450x600x200).
Producent podaje z jakich profili zostały wykonane kolumny bramy: 100x100x8mm
Wątpię żeby profile były wypełnione epoxy-granitem
, więc upraszczając dla porównania "złożę" kolumnę w jedną bryłę stali i otrzymam przekrój formatki o wymiarze około 200x16mm.
Biorąc pod uwagę że stal posiada trzykrotnie lepszą sztywność od alu, można przyjąć że musimy zastosować w podobnej aluminiowej kolumnie formatkę o przekroju 200x48mm...
Zapewne w przypadku zastosowania profili stalowych mamy szersze podparcie dla belki osi X, ale za to wartość tłumienia drgań dla aluminium jest 1,8 razy większa niż dla stali
Na stronie producenta wymienionego modelu widać także klasyczny krzyżak i wydaje mi się że rozstaw prowadnic osi X nie jest wcale większy niż u nas...
W świetle podanego przykładu i uwag kolegów, zmodyfikowałem rozmiary elementów naszej ramy uproszczając przy okazji niektóre detale:
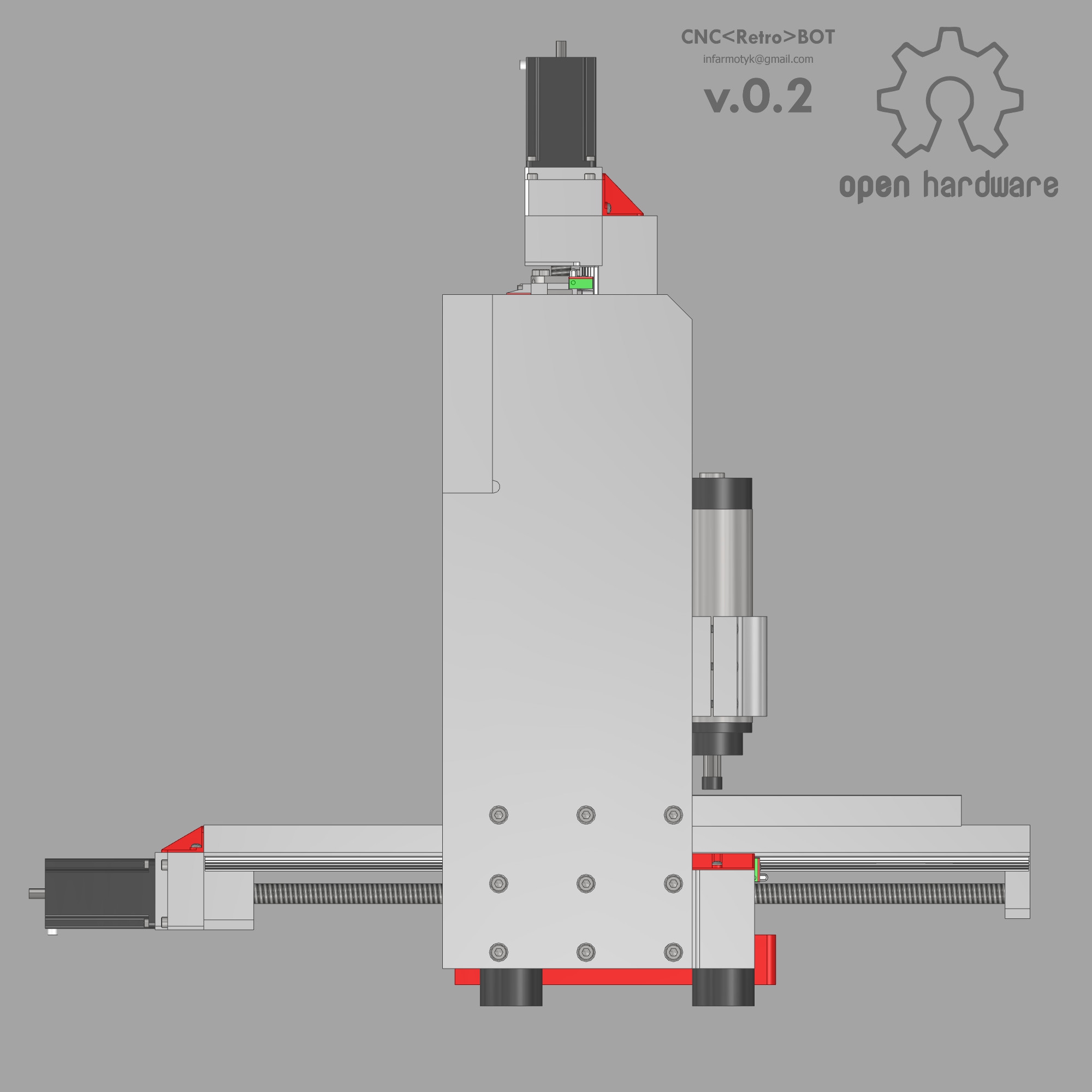
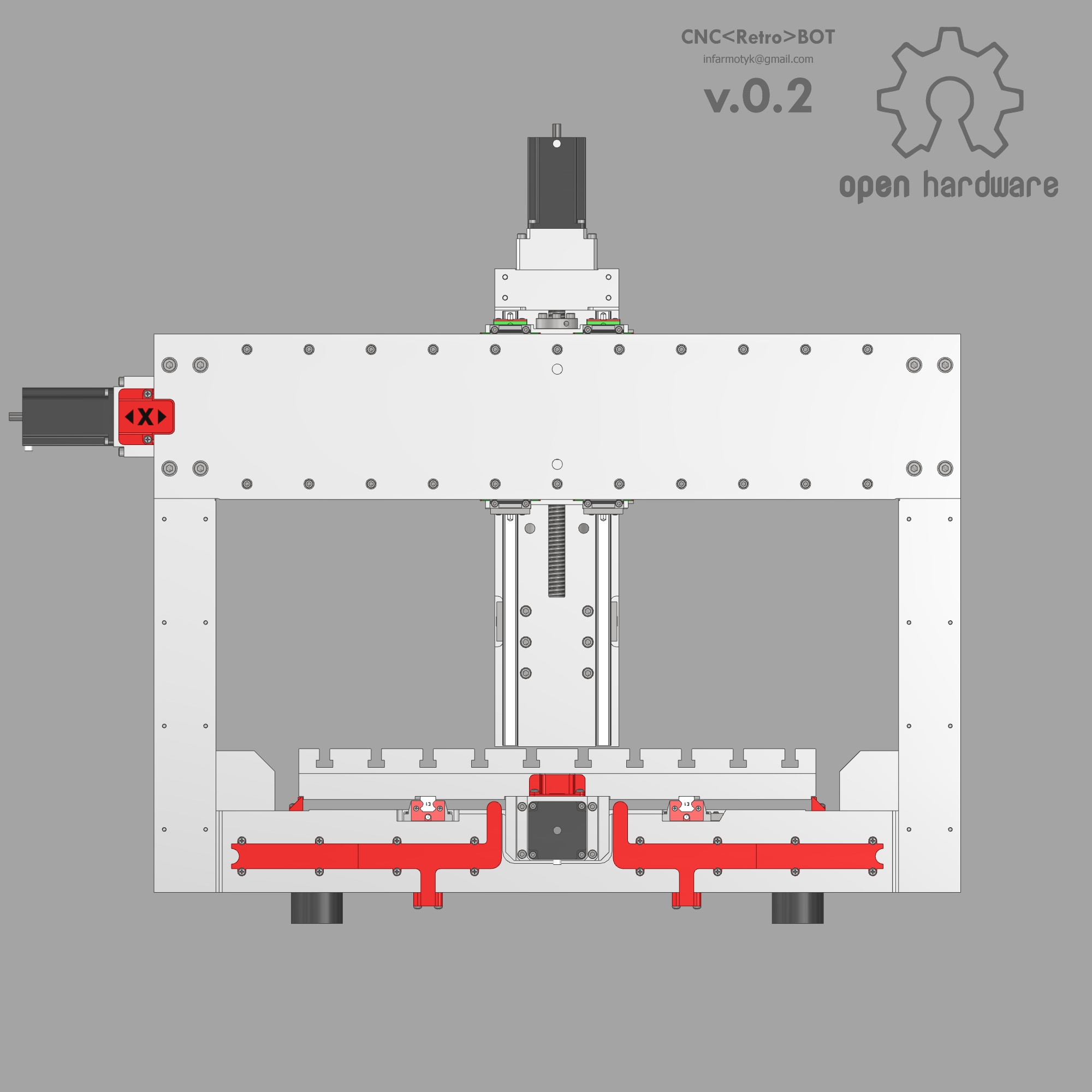
Co sądzicie o rezygnacji z podtrzymania śruby kulowej w osi Z przy długości "gwintu" 280mm?
Teraz trochę danych d/t zmian i rozmiarów detali:
nazwa detalu (wymiary) waga przed - po obróbce
podstawa-frezarki (682x220x80) 32,4kg - 30,6kg
kolumna-lewa (540x200x60) 17,5kg - 15,8kg
kolumna-prawa (540x200x60) 17,5kg - 15,6kg
wzmocnienie-kolumn (170x58x58) 1,6kg - 1,4kg
plyta-X (780x160x50) 16,8kg - 15,6kg
plyta-Z (462x120x50) 7,5kg - 6,9kg
krzyzak-X-Z (178x138x66) 4,6kg - 2,3kg
sanie-Y (662x500x25) 22,3kg - 21,2kg
teowy (500x400x25) 13,5kg - 11kg
blok-FK12-Y (100x62x40) 0,7kg - 0,4kg
blok-FK12-Z (120x62x40) 0,8kg - 0,5kg
podtrzymanie-Y (53x44x20) 0,3kg - 0,1kg
blok-silnika x3szt (78x62x40) 0,5kg - 0,3kg
uchwyt-wrzeciona (110x90x80) 2,1kg - 1kg
RAZEM: 139,1kg przed - 123,3kg po obróbce
Usunięte 15,8kg (około 5861cm^3 aluminium)
Stop EN 5083 (PA13) lany, odprężony można zakupić pocięty na żądane formatki już w cenie 20zł brutto za kg.
Daje nam to cenę za materiał na ramę około 2,8k zł brutto, plus transport.
Bardzo proszę o komentarze i może wstępne kosztorysy dotyczące obróbki...
CNC-Retro-BOT_v.0.2_STEP.zip
Weźmy np. dedykowaną do obróbki metali kolorowych konstrukcję ONRED KMP45 (450x600x200).
Producent podaje z jakich profili zostały wykonane kolumny bramy: 100x100x8mm
Wątpię żeby profile były wypełnione epoxy-granitem

Biorąc pod uwagę że stal posiada trzykrotnie lepszą sztywność od alu, można przyjąć że musimy zastosować w podobnej aluminiowej kolumnie formatkę o przekroju 200x48mm...
Zapewne w przypadku zastosowania profili stalowych mamy szersze podparcie dla belki osi X, ale za to wartość tłumienia drgań dla aluminium jest 1,8 razy większa niż dla stali

Na stronie producenta wymienionego modelu widać także klasyczny krzyżak i wydaje mi się że rozstaw prowadnic osi X nie jest wcale większy niż u nas...
W świetle podanego przykładu i uwag kolegów, zmodyfikowałem rozmiary elementów naszej ramy uproszczając przy okazji niektóre detale:
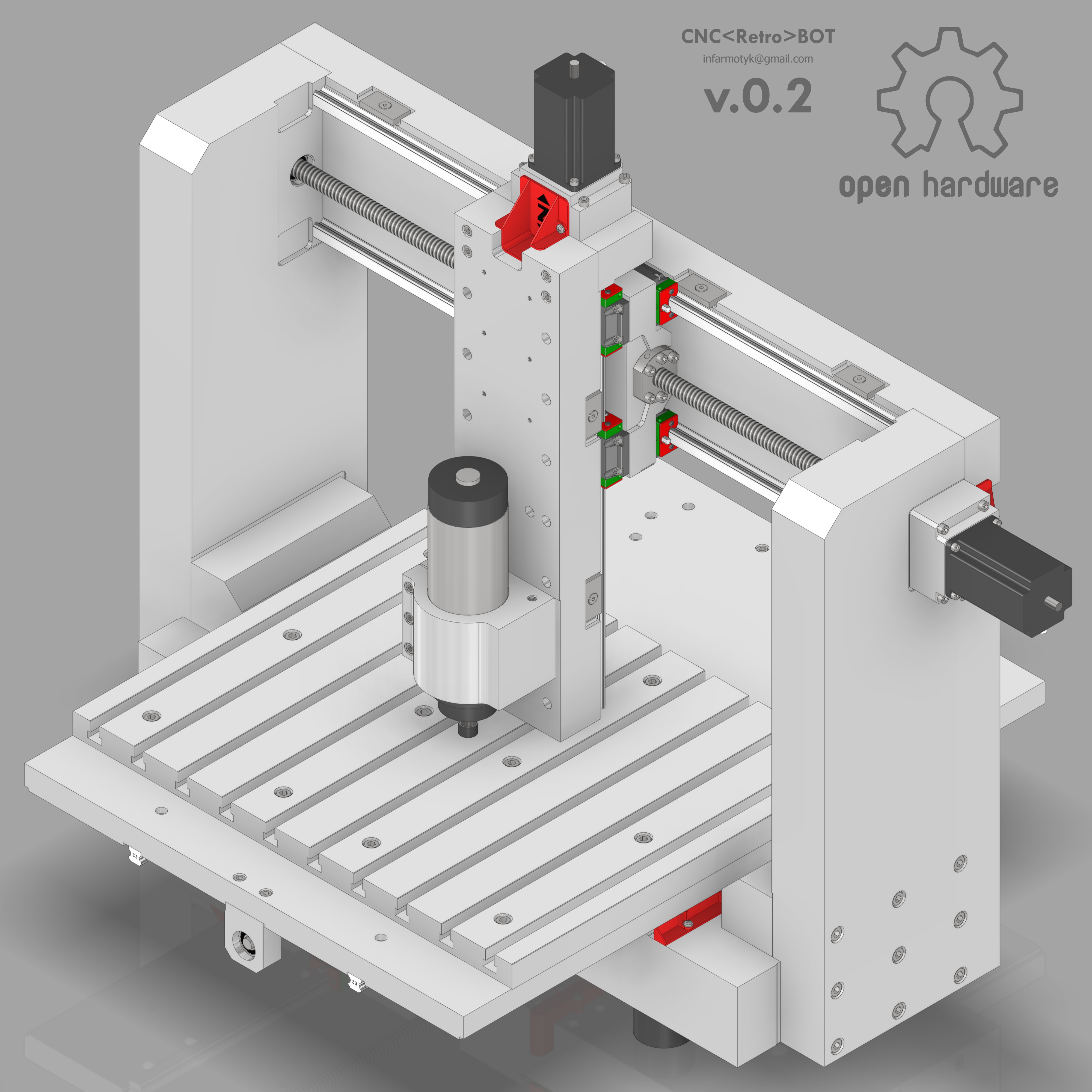
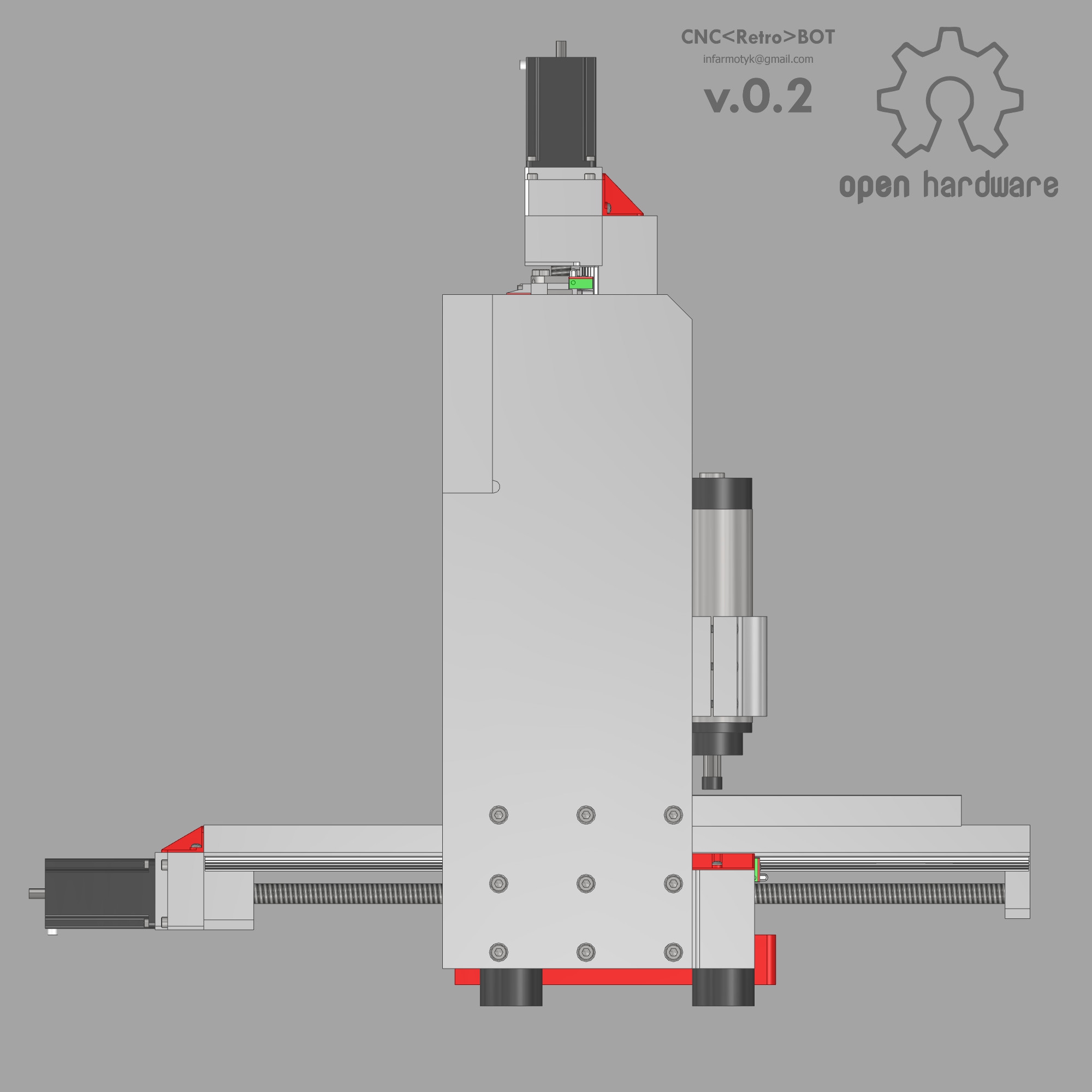
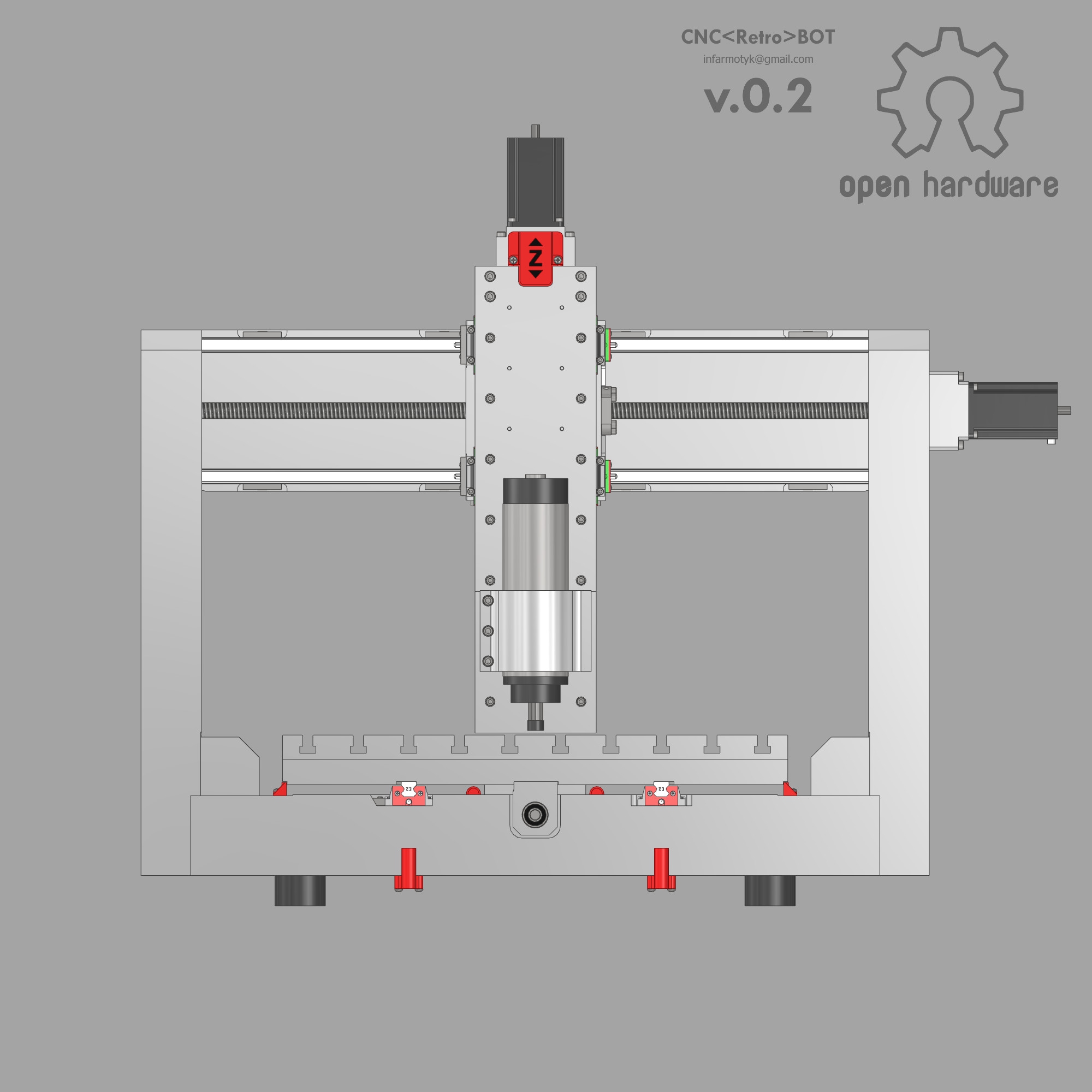
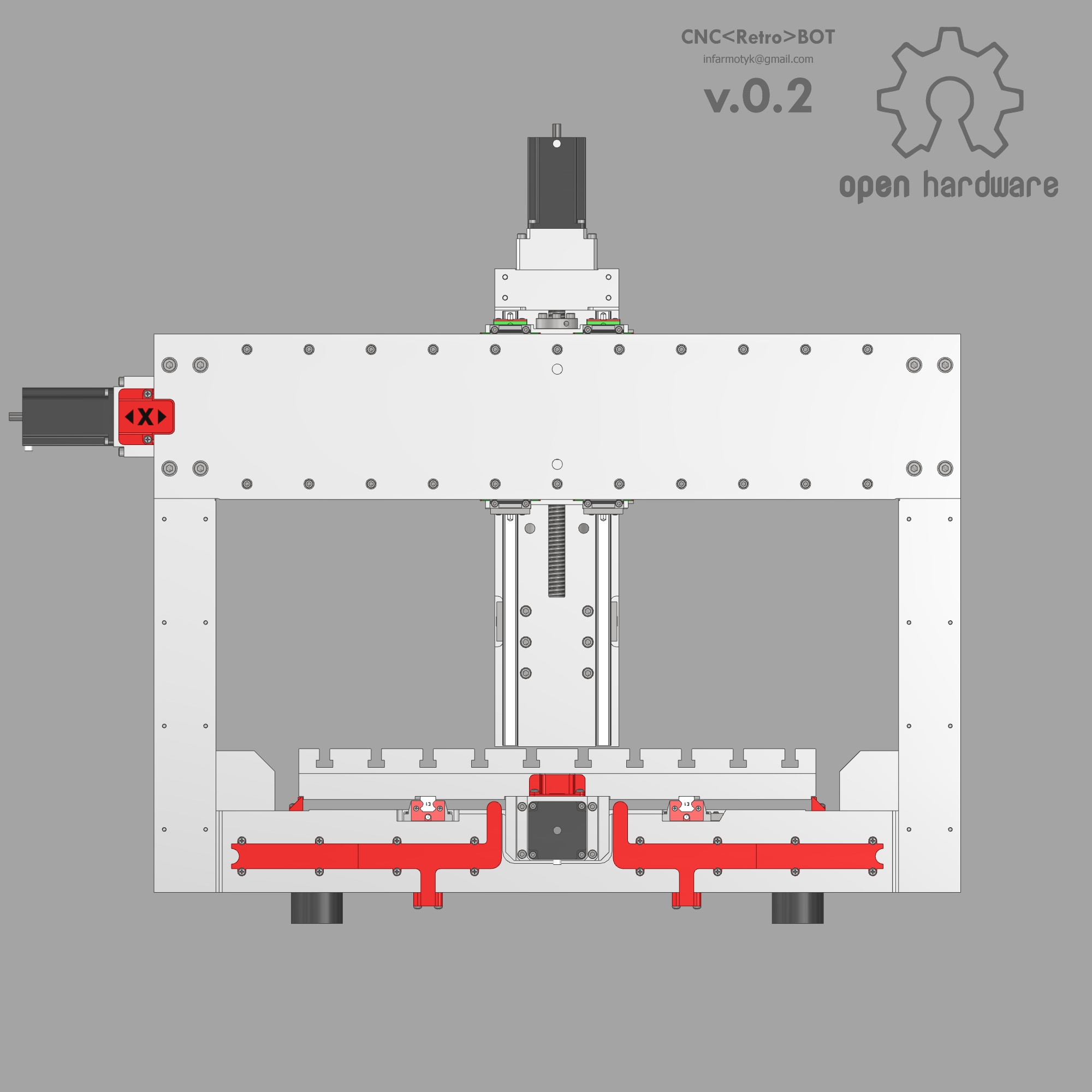
Co sądzicie o rezygnacji z podtrzymania śruby kulowej w osi Z przy długości "gwintu" 280mm?
Teraz trochę danych d/t zmian i rozmiarów detali:
nazwa detalu (wymiary) waga przed - po obróbce
podstawa-frezarki (682x220x80) 32,4kg - 30,6kg
kolumna-lewa (540x200x60) 17,5kg - 15,8kg
kolumna-prawa (540x200x60) 17,5kg - 15,6kg
wzmocnienie-kolumn (170x58x58) 1,6kg - 1,4kg
plyta-X (780x160x50) 16,8kg - 15,6kg
plyta-Z (462x120x50) 7,5kg - 6,9kg
krzyzak-X-Z (178x138x66) 4,6kg - 2,3kg
sanie-Y (662x500x25) 22,3kg - 21,2kg
teowy (500x400x25) 13,5kg - 11kg
blok-FK12-Y (100x62x40) 0,7kg - 0,4kg
blok-FK12-Z (120x62x40) 0,8kg - 0,5kg
podtrzymanie-Y (53x44x20) 0,3kg - 0,1kg
blok-silnika x3szt (78x62x40) 0,5kg - 0,3kg
uchwyt-wrzeciona (110x90x80) 2,1kg - 1kg
RAZEM: 139,1kg przed - 123,3kg po obróbce
Usunięte 15,8kg (około 5861cm^3 aluminium)
Stop EN 5083 (PA13) lany, odprężony można zakupić pocięty na żądane formatki już w cenie 20zł brutto za kg.
Daje nam to cenę za materiał na ramę około 2,8k zł brutto, plus transport.
Bardzo proszę o komentarze i może wstępne kosztorysy dotyczące obróbki...
CNC-Retro-BOT_v.0.2_STEP.zip
-
Autor tematu - Sympatyk forum poziom 1 (min. 40)
- Posty w temacie: 25
- Posty: 47
- Rejestracja: 29 sty 2014, 11:39
- Lokalizacja: Tomaszów Lubelski
Faktycznie, wyjechałem z wrzecionem za bardzo do przodu...
Nie brałem nawet pod uwagę powyższego rozwiązania w Z-tce, nie chcąc dodatkowo komplikować konstrukcji.
Temat pojawił się w idealnym momencie, ponieważ przy okazji zauważyłem że w swoich maszynach OnRed bardzo "płasko" podchodzi także do krzyżaka, zostawiając tylko tyle miejsca, żeby solidnie zamocować wózki.
Obydwa rozwiązania pozwalają na spore cofnięcie wrzeciona, dlatego chyba warto było by z nich skorzystać
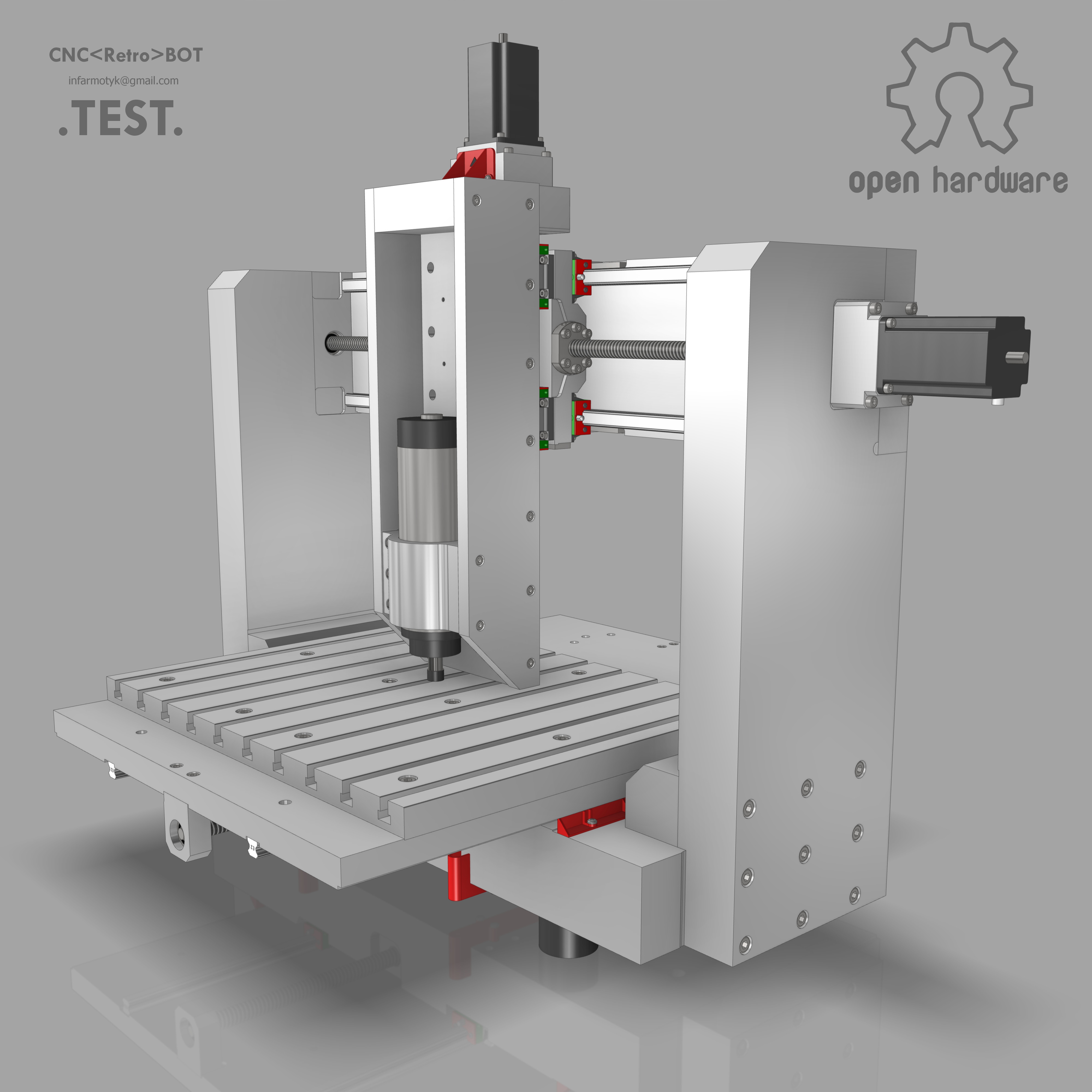
To na razie wstępna przymiarka, ale wygląda na to że w ten sposób możemy cofnąć się wrzecionem w stosunku do osi Z o 24mm, a dodatkowo "spłaszczając" krzyżak - do osi X o 34mm.
Oś wrzeciona (freza) będzie oddalona od płaszczyzny podstawy prowadnic Z-tki o 67mm / dla X - 137mm.
W miejscu mocowania uchwytu wrzeciona płyta Z ma 25mm grubości, dalej już 35mm. Usztywnienia mają 15mm, żeby nie ograniczać pola roboczego, ale za to dokręcone są także do uchwytu wrzeciona, który staje się stałym elementem konstrukcji
W naszym przypadku usztywnienia mocujemy na samym końcu, żeby wcześniej nie zasłaniały śrub mocujących wózki i docisków prowadnic podczas montażu ramy.
Będę musiał niestety solidnie przerobić całą Z-tkę, żeby wszystko się ładnie kupy trzymało

Nie brałem nawet pod uwagę powyższego rozwiązania w Z-tce, nie chcąc dodatkowo komplikować konstrukcji.
Temat pojawił się w idealnym momencie, ponieważ przy okazji zauważyłem że w swoich maszynach OnRed bardzo "płasko" podchodzi także do krzyżaka, zostawiając tylko tyle miejsca, żeby solidnie zamocować wózki.
Obydwa rozwiązania pozwalają na spore cofnięcie wrzeciona, dlatego chyba warto było by z nich skorzystać

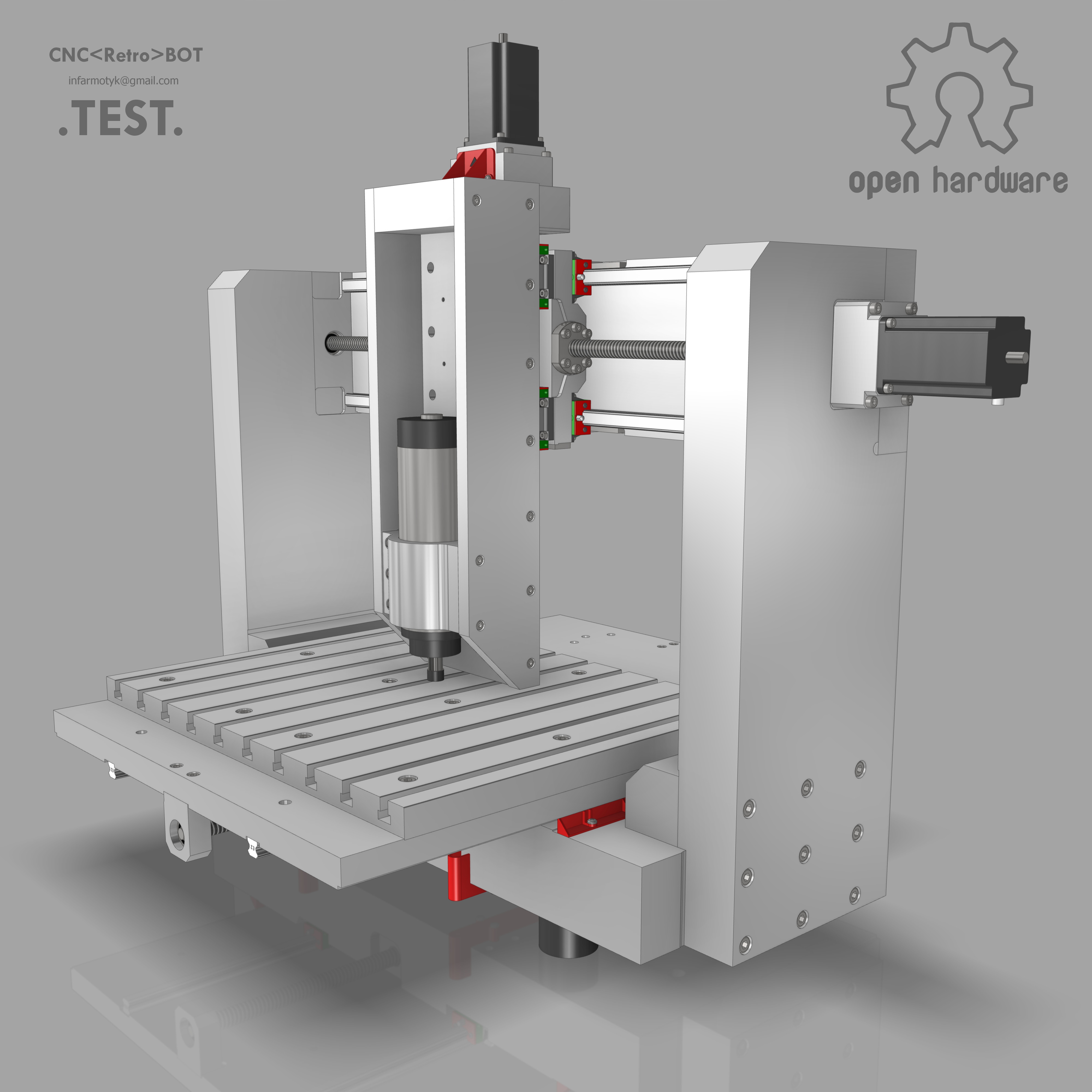
To na razie wstępna przymiarka, ale wygląda na to że w ten sposób możemy cofnąć się wrzecionem w stosunku do osi Z o 24mm, a dodatkowo "spłaszczając" krzyżak - do osi X o 34mm.
Oś wrzeciona (freza) będzie oddalona od płaszczyzny podstawy prowadnic Z-tki o 67mm / dla X - 137mm.
W miejscu mocowania uchwytu wrzeciona płyta Z ma 25mm grubości, dalej już 35mm. Usztywnienia mają 15mm, żeby nie ograniczać pola roboczego, ale za to dokręcone są także do uchwytu wrzeciona, który staje się stałym elementem konstrukcji

W naszym przypadku usztywnienia mocujemy na samym końcu, żeby wcześniej nie zasłaniały śrub mocujących wózki i docisków prowadnic podczas montażu ramy.
Będę musiał niestety solidnie przerobić całą Z-tkę, żeby wszystko się ładnie kupy trzymało

Ostatnio zmieniony 10 lut 2016, 09:21 przez infarmotyk, łącznie zmieniany 1 raz.
-
Autor tematu - Sympatyk forum poziom 1 (min. 40)
- Posty w temacie: 25
- Posty: 47
- Rejestracja: 29 sty 2014, 11:39
- Lokalizacja: Tomaszów Lubelski
Wiem o co chodzi, ale niestety będę musiał chyba rozwiązać to dokładnie jak OnRed.
Nie pomieszczę usztywnień w ten sposób, bez poszerzania płyty - która zasłoniła by wtedy śruby mocujące wózki utrudniając montaż osi z wózkami na prowadnicach (opis we wstępie).
Oczywiście jeszcze dokładnie to przemyślę, ale wydaje mi się że stanie na wybraniu w usztywnieniach "pasa" materiału na głębokość powiedzmy 2mm, który stworzy dwie płaszczyzny odniesienia dla płyty...
Nie pomieszczę usztywnień w ten sposób, bez poszerzania płyty - która zasłoniła by wtedy śruby mocujące wózki utrudniając montaż osi z wózkami na prowadnicach (opis we wstępie).
Oczywiście jeszcze dokładnie to przemyślę, ale wydaje mi się że stanie na wybraniu w usztywnieniach "pasa" materiału na głębokość powiedzmy 2mm, który stworzy dwie płaszczyzny odniesienia dla płyty...

-
- Sympatyk forum poziom 2 (min. 50)
- Posty w temacie: 4
- Posty: 61
- Rejestracja: 11 kwie 2013, 13:04
- Lokalizacja: Zawadzkie
Coś kojarzę, że to po skręceniu jest jeszcze kołkowane, ale to sprawdzę jak wygląda oś Z u mnie na maszynce. Kołkowane, czyli wierci się otwory w obu elementach na raz, poprawia rozwiertakiem na dokładny wymiar i wbija szlifowany kołek/pręt. Wtedy nie ma luzu i nie przesunie się podczas pracy.
Wadą jest to, że nie da się tego zrobić przed złożeniem, podczas frezowania elementów osobno.
Wadą jest to, że nie da się tego zrobić przed złożeniem, podczas frezowania elementów osobno.
-
- Sympatyk forum poziom 2 (min. 50)
- Posty w temacie: 4
- Posty: 61
- Rejestracja: 11 kwie 2013, 13:04
- Lokalizacja: Zawadzkie
I ja się z tobą w całości zgadzam. Twierdzę jedynie, że dwa elementy skręcone śrubami, poddane wibracjom i obciążeniom przez dłuższy czas, mogą się w granicach tego luzu względem siebie przesunąć.Aldeberan pisze:Darsis - poprawnie wykonane połączenie śrubowe nigdy nie obciąży śruby na ścinanie (no chyba że śruby pasowane ale to inna historia). Obciążenia styczne przenosi tarcie.