Desktopowa Frezarka CNC
-
- Lider FORUM (min. 2000)
- Posty w temacie: 3
- Posty: 7739
- Rejestracja: 23 lis 2004, 22:41
- Lokalizacja: kraków
witam.
jeżeli ma to być naprawdę precyzyjnie zrobione to albo tokarka i wytoczyć - albo frezarka i wytaczadło.
lub na frezarce cnc - tylko frez musi być dość długi ( 50mm głębokości ) .
zakładając że w ogóle da się to precyzyjnie zrobić - w plastiku ( co to jest precyzyjnie ? )
pozdrawiam
pozdrawiam.
jeżeli ma to być naprawdę precyzyjnie zrobione to albo tokarka i wytoczyć - albo frezarka i wytaczadło.
lub na frezarce cnc - tylko frez musi być dość długi ( 50mm głębokości ) .
zakładając że w ogóle da się to precyzyjnie zrobić - w plastiku ( co to jest precyzyjnie ? )
pozdrawiam
pozdrawiam.
Mane Tekel Fares
Tagi:
-
- Znawca tematu (min. 80)
- Posty w temacie: 1
- Posty: 90
- Rejestracja: 08 sty 2008, 22:39
- Lokalizacja: Poznań
Silniki absolutnie za słabe, zabraknie mocy na pokonanie oporów wynikających z nieuniknionych niedoskonałości konstrukcyjnych maszyny.napęd: silniki 0,6Nm + śruby trapezowe 14x4,
Ja mam w podobnej maszynie (MDF22mm) silniki 1,26Nm i będę je wymieniał na 1,96Nm.
Na więcej nie pozwoli sterownik.
Zrób wiekszy, bo przy takim małym zabraknie Ci miejsca na mocowanie większych przedmiotów.w projekcie konstrukcja umożliwia wyjazd stołu poza obrys całej maszyny - nie jestem pewien, czy zależy mi na takim powiększeniu pola roboczego (i czy będzie dość stabilny)
Nie wiem jakie mocowanie planujesz, ale ostrzegam i odradzam używania takich śmiesznych gniazd z wewnętrznym gwintem,
które wciska się w stół od dołu:

Są za miękkie i po którymś użyciu po prostu wyrabiają się na tyle, że nie utrzymają już żadnej śruby.
Idź od razu w stronę jakiegoś stołu teowego albo czegoś alternatywnego.
BTW:
1. Nie widziałem nigdzie projektu mocowania wrzeciona i jego wysokości nad stołem?
2. Ciekawi mnie w jaki sposób chcesz jednocześnie zamocować silnik, zacisnąć sprzęgło na śrubach i przymocować silnik do skrzynki? Z tego co widzę na projekcie to niewykonalne.
3. Nie widzę też w jaki sposób śrubą będzie blokowana przed swobodą w swojej osi podłużnej. Nie widze na niej żadnego przetoczenia pod gwint, nie widze miejsca na nakrętkę, która zablokuje śrubę w łożysku.
4. W osi Z: te wstawki poliamidowe robią za łożyska? Jeżeli tak, to są za wąsko, a zastanawiam się czy wogle to będzie chciało jeździć na wałkach.
-
Autor tematu - Sympatyk forum poziom 1 (min. 40)
- Posty w temacie: 35
- Posty: 48
- Rejestracja: 20 mar 2012, 20:16
- Lokalizacja: Wrocław
- Kontakt:
pukury pisze:plastiku ( co to jest precyzyjnie ? )
Miałem na myśli dokładność między 1 a 1/4 milimetra. Coś czuję, że takie otworowanie może być drogie, chyba zrezygnuję z pomysłu wózka w jednym kawałku.
Szukając wymiarowania wspomnianych wcześniej tulei, natknąłem się na tą stronę. Może komuś się to przyda - wszystkie wymiary są od razu na rysunku.
Poprawki związane z wałkami (16mm -> 20mm) i wymiana wstawek poliamidowych na łożyska ślizgowe; dodałem też dodatkowe wzmocnienie w skrzynce Ztki.
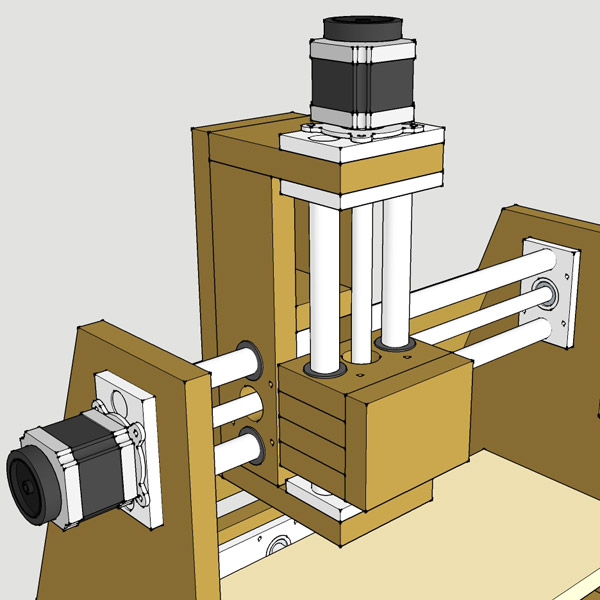
Takie już niestety mam i na nowe pieniędzy nie znajdę.mefiu pisze:Silniki absolutnie za słabe, zabraknie mocy na pokonanie oporów wynikających z nieuniknionych niedoskonałości konstrukcyjnych maszyny.

Nie przemyślałem jeszcze odpowiedniego mocowania, ale na pierwszy ogień idą małe elementy - wykorzystam małe imadło maszynowe. W każdym razie dzięki za ostrzeżenie!mefiu pisze:Nie wiem jakie mocowanie planujesz, ale ostrzegam i odradzam używania takich śmiesznych gniazd z wewnętrznym gwintem które wciska się w stół od dołu

Ad. 1: Nie mam dokładnych wymiarów wrzeciona, więc nie mogę zaprojektować uchwytu. Wysokości też jeszcze nie ustaliłem, ale mam wrażenie, że lepiej nieco za wysoko niż za nisko.mefiu pisze:BTW:
1. Nie widziałem nigdzie projektu mocowania wrzeciona i jego wysokości nad stołem?
2. Ciekawi mnie w jaki sposób chcesz jednocześnie zamocować silnik, zacisnąć sprzęgło na wałkach i przymocować silnik do skrzynki? Z tego co widzę na projekcie to niewykonalne.
3. Nie widzę też w jaki sposób śrubą będzie blokowana przed swobodą w swojej osi podłużnej. Nie widze na niej żadnego przetoczenia pod gwint, nie widze miejsca na nakrętkę, która zablokuje śrubę w łożysku.
4. W osi Z: te wstawki poliamidowe robią za łożyska? Jeżeli tak, to są za wąsko, a zastanawiam się czy wogle to będzie chciało jeździć na wałkach.
Ad. 2 i 3: Jeszcze nie wymodelowałem detali śruby pociągowej, ale pamiętam o nich

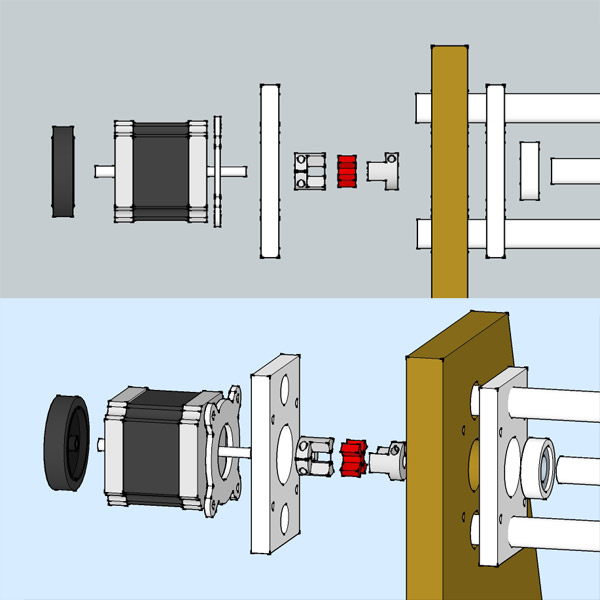
Śruba pociągowa przechodzi przez łożysko (stoczona do 10mm), następnie zaciskam na niej pierwszą piastę (10mm). Montuję śrubę na dwie obręcze zaciskowe (od środka, w takiej odległości, że blokują się o łożyska). Później montuję drugą piastę na oś silnika, a jego samego przykręcam do obudowy wpasowując obie piasty i wkładkę. Dzięki temu silnik montuję na sztywno do obudowy, a sprzęgło działa w zamkniętej przestrzeni.
Ad. 4: Zrezygnowałem z łożyskowania w poliamidzie - z tego co się zorientowałem, to za duże koszta. Jednak według producentów, poliamid z domieszką oleju albo MoS2 świetnie nadaje się do takich zastosowań.
-
- Lider FORUM (min. 2000)
- Posty w temacie: 12
- Posty: 2083
- Rejestracja: 11 cze 2011, 18:29
- Lokalizacja: Warszawa / Lublin
Otwory pod prowadnice muszą być wywiercone z możliwie dokładnie takim samym rozstawem na obu końcach prowadnic. Różnica nie powinna przekraczać 0.1mm albo lepiej 0.05mm. Można to osiągnąć np. wiercąc otwory w 2 elementach na raz.
Najlepszym narzędziem do precyzyjnego wywiercenia takich otworów jest wytaczadło - trzeba najpierw zgrubnie otwór wywiercić (2-3mm mniejszy) a potem polecieć wytaczadłem. Można to zrobić na frezarce lub dobrej wiertarce kolumnowej (słowo-klucz: dobrej, znaczy nie takiej z marketu za 250zł).
Ja u siebie z braku narzędzi robiłem to za pomocą różnych sztuczek - nawet wyszło, chociaż założenia były takie, że np. nie ważne, w jakiej odległości od siebie będą wałki, byle były w równej na obu końcach, podobnie z odległością otworów od krawędzi deski. Przy stosowaniu tulej ślizgowych czy łożysk osadzanych w deskach takie podejście nie zadziała (ja odżałowałem na łożyska w obudowach).
Wykonanie takich otworów na CNC jest banalne i powinno być dość tanie (w skali usług CNC). Z tego, co mi wiadomo, w niektórych firmach obróbka wychodzi względnie tanio, jeżeli dasz im G-code - wrzucacją do maszyny, nikt nie musi wklepywać programu ani nic rysować. A może jakiś kolega z forum się zlituje?
Silniki 0.6Nm pociągną, jeżeli śruba będzie prosto zamontowana i centrycznie zatoczona na końcach. No chyba, że kolega chce robić partyzantkę bez zataczania końców.
Najlepszym narzędziem do precyzyjnego wywiercenia takich otworów jest wytaczadło - trzeba najpierw zgrubnie otwór wywiercić (2-3mm mniejszy) a potem polecieć wytaczadłem. Można to zrobić na frezarce lub dobrej wiertarce kolumnowej (słowo-klucz: dobrej, znaczy nie takiej z marketu za 250zł).
Ja u siebie z braku narzędzi robiłem to za pomocą różnych sztuczek - nawet wyszło, chociaż założenia były takie, że np. nie ważne, w jakiej odległości od siebie będą wałki, byle były w równej na obu końcach, podobnie z odległością otworów od krawędzi deski. Przy stosowaniu tulej ślizgowych czy łożysk osadzanych w deskach takie podejście nie zadziała (ja odżałowałem na łożyska w obudowach).
Wykonanie takich otworów na CNC jest banalne i powinno być dość tanie (w skali usług CNC). Z tego, co mi wiadomo, w niektórych firmach obróbka wychodzi względnie tanio, jeżeli dasz im G-code - wrzucacją do maszyny, nikt nie musi wklepywać programu ani nic rysować. A może jakiś kolega z forum się zlituje?
Silniki 0.6Nm pociągną, jeżeli śruba będzie prosto zamontowana i centrycznie zatoczona na końcach. No chyba, że kolega chce robić partyzantkę bez zataczania końców.
-
Autor tematu - Sympatyk forum poziom 1 (min. 40)
- Posty w temacie: 35
- Posty: 48
- Rejestracja: 20 mar 2012, 20:16
- Lokalizacja: Wrocław
- Kontakt:
Wygląda na to, że dzięki uprzejmości ludzi z tego forum, będę miał możliwość wyfrezowania elementów na CNCursus_arctos pisze:Otwory pod prowadnice muszą być wywiercone z możliwie dokładnie takim samym rozstawem na obu końcach prowadnic. Różnica nie powinna przekraczać 0.1mm albo lepiej 0.05mm. (...) Z tego, co mi wiadomo, w niektórych firmach obróbka wychodzi względnie tanio, jeżeli dasz im G-code - wrzucacją do maszyny, nikt nie musi wklepywać programu ani nic rysować. A może jakiś kolega z forum się zlituje?

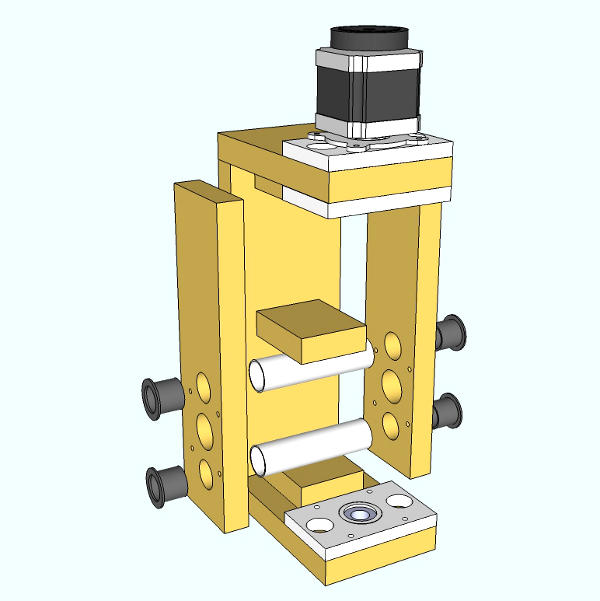
Zewnętrzne fi tulejek to 23mm, rurka o fi 25mm i grubości 1mm powinna być idealna.
Śruba oczywiście będzie zatoczana na 10mm pod łożysko i 6/8mm pod sprzęgło kłowe.ursus_arctos pisze:Silniki 0.6Nm pociągną, jeżeli śruba będzie prosto zamontowana i centrycznie zatoczona na końcach. No chyba, że kolega chce robić partyzantkę bez zataczania końców.
-
- Lider FORUM (min. 2000)
- Posty w temacie: 12
- Posty: 2083
- Rejestracja: 11 cze 2011, 18:29
- Lokalizacja: Warszawa / Lublin
Jak elementy będą wycinanie na CNC, to nie kombinuj, tylko wbijaj łożyska w materiał - ręcznie dokładniej nie zrobisz; kombinacje z rurkami też raczej na dobre nie wyjdą.
Jak będzie zatoczona śruba? Bo widziałem tutaj kiedyś - powiem szczerze - idiotyczny schemat zataczania aż di fi6 i nie chciałbym, by kol. go powielił.
Polecam zatoczyć tak (od gwintu do brzegu):
(opcjonalnie) kawałek fi12-fi14
fi10/h5 pod łożyska
gwint M10 do dokręcenia łożysk
fi8/h6 pod sprzęgło
Można też zrobić montaż osiowy od strony wolnej i podparcie od strony napędowej - wtedy zataczamy fi10/h5 pod łożyska i M10 z jednej strony oraz po prostu fi10 z drugiej (sprzęgło fi10).
Jak będzie zatoczona śruba? Bo widziałem tutaj kiedyś - powiem szczerze - idiotyczny schemat zataczania aż di fi6 i nie chciałbym, by kol. go powielił.
Polecam zatoczyć tak (od gwintu do brzegu):
(opcjonalnie) kawałek fi12-fi14
fi10/h5 pod łożyska
gwint M10 do dokręcenia łożysk
fi8/h6 pod sprzęgło
Można też zrobić montaż osiowy od strony wolnej i podparcie od strony napędowej - wtedy zataczamy fi10/h5 pod łożyska i M10 z jednej strony oraz po prostu fi10 z drugiej (sprzęgło fi10).
-
- Lider FORUM (min. 2000)
- Posty w temacie: 12
- Posty: 2083
- Rejestracja: 11 cze 2011, 18:29
- Lokalizacja: Warszawa / Lublin
-
Autor tematu - Sympatyk forum poziom 1 (min. 40)
- Posty w temacie: 35
- Posty: 48
- Rejestracja: 20 mar 2012, 20:16
- Lokalizacja: Wrocław
- Kontakt:
Sam już nie wiem, które rozwiązanie (tuleje w rurach, czy bezpośrednio w sklejce) zapewni lepszą osiowość. Chyba po prostu okaże się w praniu...
@pascalPL i @ursus_arctos - podziękowania za gotowe rozwiązanie
. Czy zwykłą narzynką dam radę nagwintować M8 na tokarce? Zastanawiam się czy rozwiązanie z pierścieniami Segera nie byłoby prostsze, chociaż wtedy będzie mi bardzo trudno uzyskać jak najmniejszy luz.
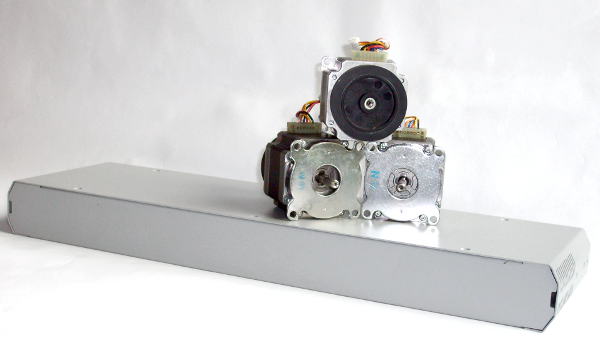
Silniki z "tłumikami-pokrętłami" już czekają, podobnie jak obudowa na sterownik i zasilacz. W drodze trochę stalowego złomu w postaci niewiarygodnie grubych wałków
. Nominalny prąd silników to 2,2A (napięcie 1,2V), sterowniki zrobię na L297 i L298. Czy taki transformator wystarczy?
@pascalPL i @ursus_arctos - podziękowania za gotowe rozwiązanie

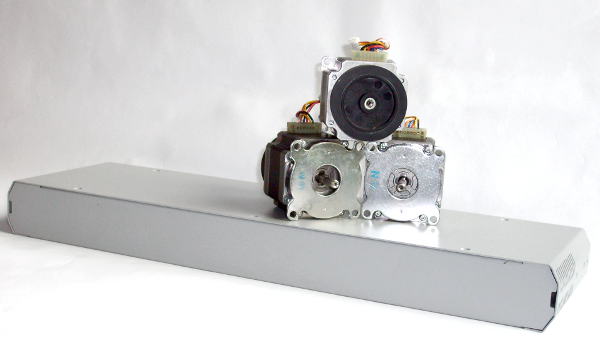
Silniki z "tłumikami-pokrętłami" już czekają, podobnie jak obudowa na sterownik i zasilacz. W drodze trochę stalowego złomu w postaci niewiarygodnie grubych wałków

-
- Lider FORUM (min. 2000)
- Posty w temacie: 12
- Posty: 2083
- Rejestracja: 11 cze 2011, 18:29
- Lokalizacja: Warszawa / Lublin
Nie rób sterowników na L297/L298! To przestarzałe dziadostwo!!!! Polecam układy A3977 - mikrokrok do 1/8 kroku, działa bardzo elegancko. Użyłem ich w swojej maszynce i sobie bardzo chwalę.
Co do zasilacza - aby zmaksymalizować osiągi trzeba zmaksymalizować napięcie. Na zasilaczu transformatorowym, którego napięcie zależy od obciążenia i humoru elektrowni, nie wyżyłujesz napięcia. Warto się zainteresować zasilaczami przemysłowymi - można za 130zł kupić zasilacz 36V (z regulacją +/- 10%; w praktyce zakres jest większy) i mocy 250W. Są też 120W - można je kupić za 79zł na alledrogo. To 3 złote więcej, niż ten transformator.
Co do narzynania narzynką na tokarce - da się, aczkolwiek nie wiem, czy akurat na śrubie walcowanej... jest jednak dosyć twarda. Można zrobić sztuczkę i trochę stoczyć fragment pod gwint, aby miał średnicę zewn. mniejszą od nominalnej dla danego gwintu - powinien nadal trzymać, a narzynanie będzie prostsze.
Co do zasilacza - aby zmaksymalizować osiągi trzeba zmaksymalizować napięcie. Na zasilaczu transformatorowym, którego napięcie zależy od obciążenia i humoru elektrowni, nie wyżyłujesz napięcia. Warto się zainteresować zasilaczami przemysłowymi - można za 130zł kupić zasilacz 36V (z regulacją +/- 10%; w praktyce zakres jest większy) i mocy 250W. Są też 120W - można je kupić za 79zł na alledrogo. To 3 złote więcej, niż ten transformator.
Co do narzynania narzynką na tokarce - da się, aczkolwiek nie wiem, czy akurat na śrubie walcowanej... jest jednak dosyć twarda. Można zrobić sztuczkę i trochę stoczyć fragment pod gwint, aby miał średnicę zewn. mniejszą od nominalnej dla danego gwintu - powinien nadal trzymać, a narzynanie będzie prostsze.