autonomiczny sterownik osi Z
-
- Specjalista poziom 1 (min. 100)
- Posty w temacie: 3
- Posty: 158
- Rejestracja: 26 sty 2010, 21:15
- Lokalizacja: Kielce
- Kontakt:
Dołączę się do tematu. Robiłem kiedyś maszyny na sterowniku USBCNC tam jest na ekranie wyprowadzone okienko PWM gdzie zmieniając wartość można zmienić prędkość wrzeciona. Ja wykożystałem to wyjście PWM jako napięcie referencyjne dla THC. Natomiast THC które stosuje mają wejście ENABLE. wyłączam THC na łukach i ok 3 mm przed końcem linii. Kiedyś stosowałem silniki DC ale miałem problemy z ustawieniem wolnych prędkości. Zapytam jeszcze czy ktoś z Was wie jaka powinna być prędkość THC/ Na logikę powinna się zmieniać wraz ze zmianą prędkości cięcia.
Tagi:
-
- Lider FORUM (min. 2000)
- Posty w temacie: 7
- Posty: 3576
- Rejestracja: 24 gru 2006, 11:54
- Lokalizacja: już tylko Mysłowice
- Kontakt:
Przy profesjonalnym układzie pomiarowym jest brane głównie napięcie i prąd z łuku a są układy gdzie jak np. w maszynach z ALW jest i brana również szybkość z serw po osiągnięciu komendy M114 która odpowiada za złagodzenie łuku przy zakańczaniu by zminimalizować zużycie elektrody oraz wygładzić ścianki zakończenia cięcia.
Ale to są bardzo skomplikowane układy i nie warto tego stosować w Twoim urządzeniu , jeżeli to ma być tanie i uniwersalne , bo zakładam że takie ma być.
Wiec z PWM , można sobie odpuścić. Jak ktoś chce zawsze może sobie zrobić układ na sterowniku "logo" i w nim wykorzystać PWM.
Prawie gotowce robi np. SIEMENS i są często układy te stosowane w maszynach.
Ale jest też i odpowiednia cena za to logo.
I dlatego PWM kolego LEO dużo tu wzbogaci ale czy warto iść w tym kierunku
Rozpoczęcie procesu cięcia , sam proces i zakończenie się bardzo zmienią.
Owszem , dla osoby która nie dostrzega tego nie zrobi tu żadnego to wrażenia ale coraz więcej maszyn profesjonalnych tak działa.
a tak wygląda cięcie z układem PWM i zakończenie.
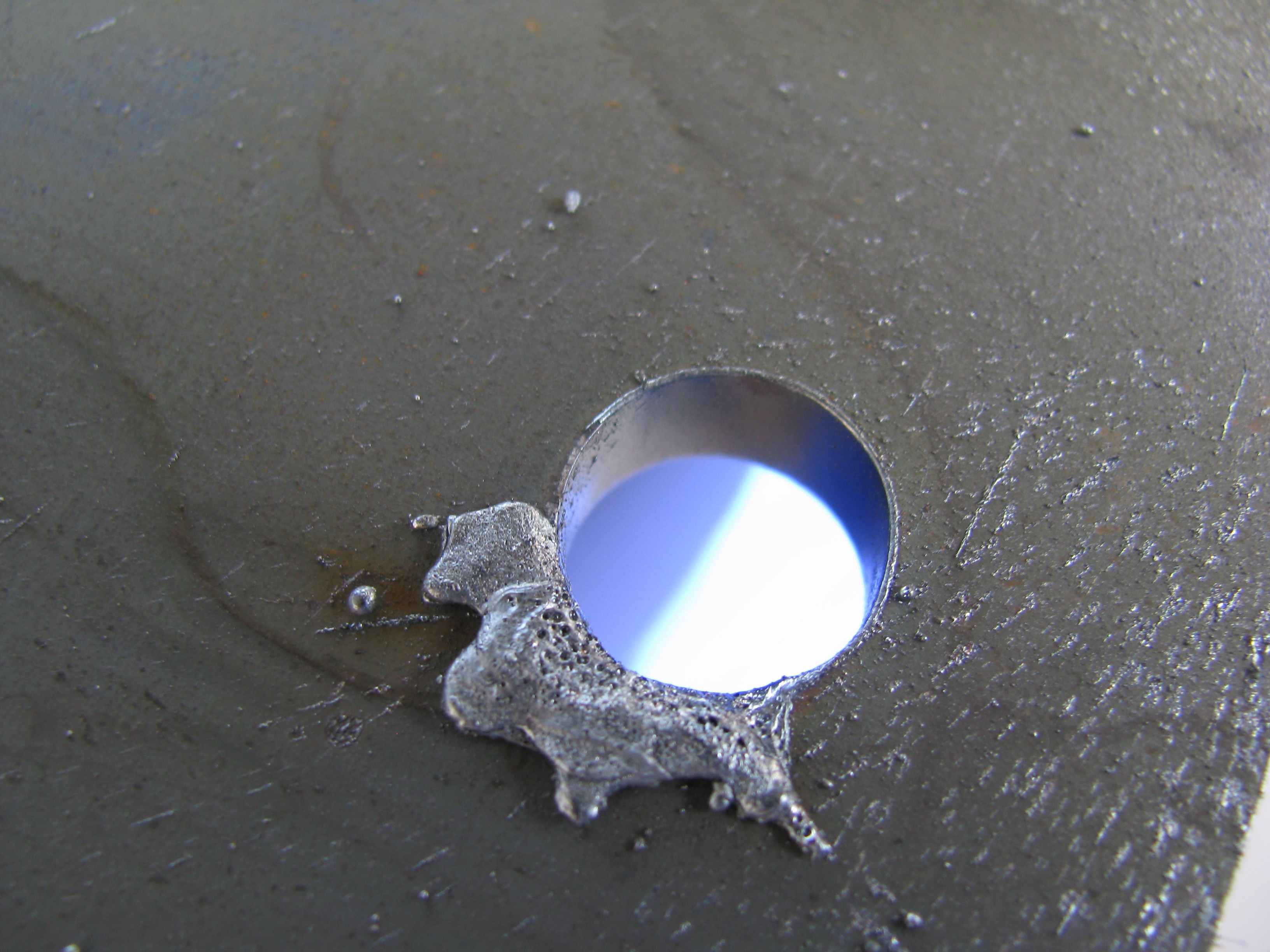
nie jest to laser co prawda ale nierówność jest naprawdę mała w porównaniu to zwykłego sterowania.
Ten otwór był robiony jak miałem odbiór maszyny w Czechach i warunkiem było to że ma być to otwór pod gwint.
Ale to są bardzo skomplikowane układy i nie warto tego stosować w Twoim urządzeniu , jeżeli to ma być tanie i uniwersalne , bo zakładam że takie ma być.
Wiec z PWM , można sobie odpuścić. Jak ktoś chce zawsze może sobie zrobić układ na sterowniku "logo" i w nim wykorzystać PWM.
Prawie gotowce robi np. SIEMENS i są często układy te stosowane w maszynach.
Ale jest też i odpowiednia cena za to logo.
I dlatego PWM kolego LEO dużo tu wzbogaci ale czy warto iść w tym kierunku

Rozpoczęcie procesu cięcia , sam proces i zakończenie się bardzo zmienią.
Owszem , dla osoby która nie dostrzega tego nie zrobi tu żadnego to wrażenia ale coraz więcej maszyn profesjonalnych tak działa.
a tak wygląda cięcie z układem PWM i zakończenie.
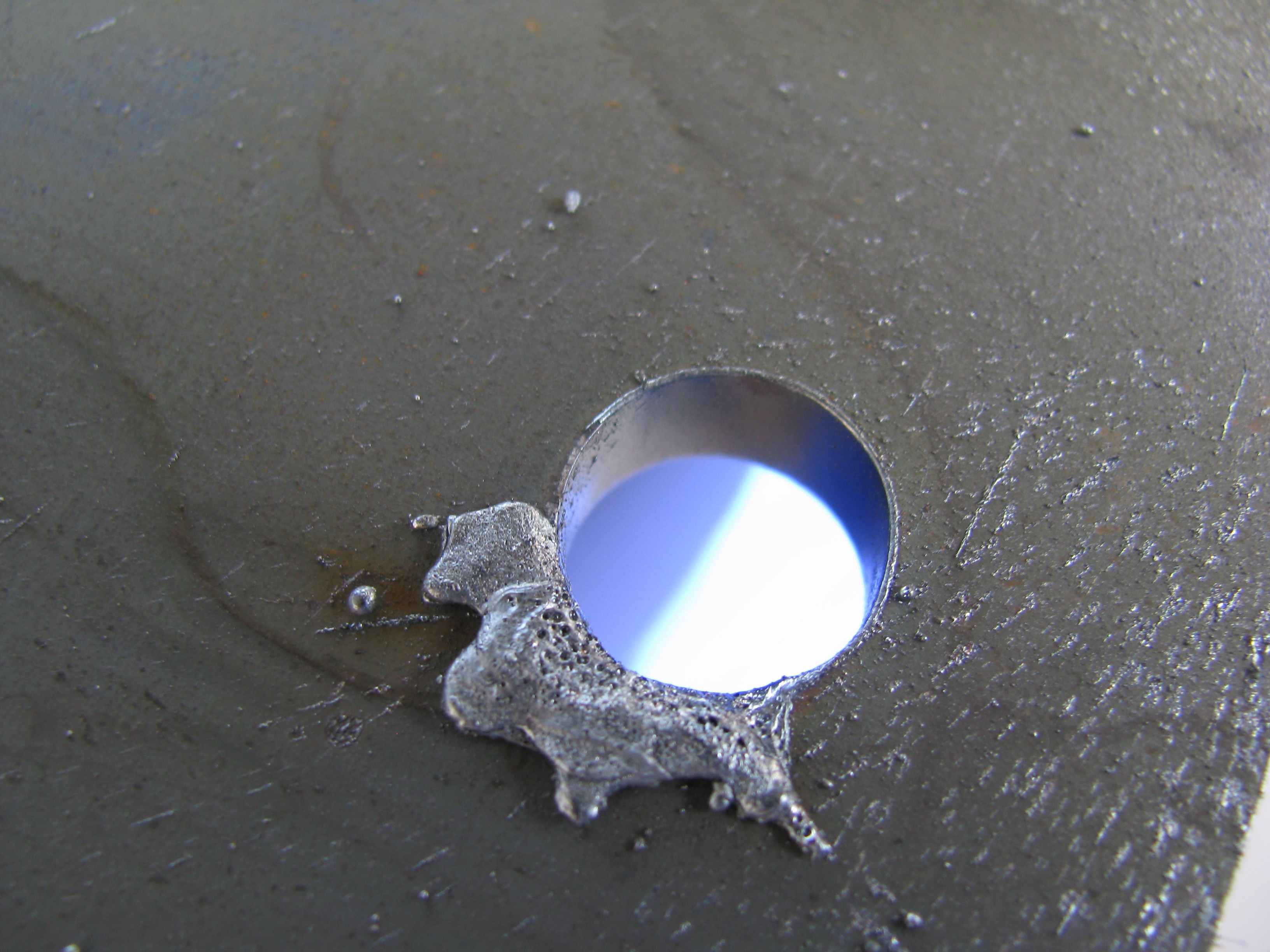
nie jest to laser co prawda ale nierówność jest naprawdę mała w porównaniu to zwykłego sterowania.
Ten otwór był robiony jak miałem odbiór maszyny w Czechach i warunkiem było to że ma być to otwór pod gwint.
Pozdrawiam robaczki kolorowe :)
-
Autor tematu - ELITA FORUM (min. 1000)
- Posty w temacie: 8
- Posty: 1126
- Rejestracja: 11 sty 2005, 13:03
- Lokalizacja: Grodków
- Kontakt:
chwilka, czegoś nie rozumiem chyba... w jaki sposób PWM wpływa na jakość cięcia bo piszemy o utrzymaniu wysokości palnika nad materiałem więc chyba tylko chodzi o "płynność ruchu" przy zastosowaniu zwykłego silnika DC. Przy pięknym otworze którym się pochwaliłeś (nie wiedziałem, że można taką jakość uzyskać przy cięciu plazmowym) przecież THC raczej mało się napracuje.
-
- Lider FORUM (min. 2000)
- Posty w temacie: 7
- Posty: 3576
- Rejestracja: 24 gru 2006, 11:54
- Lokalizacja: już tylko Mysłowice
- Kontakt:
właśnie ...
dla stałej wysokości wystarczą przekaźniki ale zakańczanie otworu to już nie tylko wyłączenie palnika ale płynne zmniejszenie jego parametrów oraz odpowiednie płynne podniesienie palnika proporcjonalnie do zamykanych parametrów cięcia.
Są jeszcze inne uwarunkowania jak spadek ciśnień gazów , wzrost lub spadek szybkości etc.
Ale to nie dotyczy Twojego projektu.
dla stałej wysokości wystarczą przekaźniki ale zakańczanie otworu to już nie tylko wyłączenie palnika ale płynne zmniejszenie jego parametrów oraz odpowiednie płynne podniesienie palnika proporcjonalnie do zamykanych parametrów cięcia.
Są jeszcze inne uwarunkowania jak spadek ciśnień gazów , wzrost lub spadek szybkości etc.
Ale to nie dotyczy Twojego projektu.
Pozdrawiam robaczki kolorowe :)
-
- Specjalista poziom 1 (min. 100)
- Posty w temacie: 3
- Posty: 158
- Rejestracja: 26 sty 2010, 21:15
- Lokalizacja: Kielce
- Kontakt:
Chodziło mi bardziej o to czy dla prędkości cięcia przykładowo 1m/min, prędkość osi Z nie powinna być inna niż dla prędkości cięcia 6m/min a jeśli tak to jaka. Zawsze przy gazie z regulatorem THC i czujnikiem pojemnościowym uzyskiwałem lepsze efekty gdy na THC zmniejszałem znacznie dynamikę działania. Odpowiedź THC na zmianę napięcia ma znaczenie ale czy nie trzeba tego rozróżniać względem prędkości cięcia.
-
- Lider FORUM (min. 2000)
- Posty w temacie: 7
- Posty: 3576
- Rejestracja: 24 gru 2006, 11:54
- Lokalizacja: już tylko Mysłowice
- Kontakt:
kol. centro ...
Rozwiązań jest dużo. I masz rację że przy czujniku pojemnościowym uzyskałeś leprze wyniki niż przy zwykłym THC pomijając fakt że pojemnościowy czujnik przy plazmie nie jest dobrym rozwiązaniem.
Ale jeżeli cykle pracy będą na tyle dobrze zrobione by minimalizować narażanie dyszy na uszkodzenia to zwykłe THC jakie kol. prokopcio zbudował zda również egzamin dobrej jakości cięcia.
A reszta to palnik i CNC.
mam mało czasu bo ciągle serwisy i projekty.
Ale jak wygospodaruję go trochę i nie zapomnę to opiszę i wkleję zdjęcia jak działa maszyna z bardzo za awansowanymi kontrolami cyklu.
Mam na swoim serwerze całkowite oprogramowanie dla sterownika HPC a szczegóły jak zbudowany jest ten sterownik można znaleźć na stronie
http://www.powerautomation.com/
Rozwiązań jest dużo. I masz rację że przy czujniku pojemnościowym uzyskałeś leprze wyniki niż przy zwykłym THC pomijając fakt że pojemnościowy czujnik przy plazmie nie jest dobrym rozwiązaniem.
Ale jeżeli cykle pracy będą na tyle dobrze zrobione by minimalizować narażanie dyszy na uszkodzenia to zwykłe THC jakie kol. prokopcio zbudował zda również egzamin dobrej jakości cięcia.
A reszta to palnik i CNC.
mam mało czasu bo ciągle serwisy i projekty.
Ale jak wygospodaruję go trochę i nie zapomnę to opiszę i wkleję zdjęcia jak działa maszyna z bardzo za awansowanymi kontrolami cyklu.
Mam na swoim serwerze całkowite oprogramowanie dla sterownika HPC a szczegóły jak zbudowany jest ten sterownik można znaleźć na stronie
http://www.powerautomation.com/
Pozdrawiam robaczki kolorowe :)
-
- Specjalista poziom 1 (min. 100)
- Posty w temacie: 3
- Posty: 158
- Rejestracja: 26 sty 2010, 21:15
- Lokalizacja: Kielce
- Kontakt:
Ja chcę zintegrować sterowanie wraz oprogramowaniem podobnie do ProNest Hypertherma z funkcją TrueHole tak aby program przesyłał do sterownika oraz THC parametry w zależności od rodzaju i grubości ciętego materiału. Dlatego w THC które stosuje chcę dopisać funkcje które poprawią parametry cięcia w szczególności skos. Pytam więc na co należy zwrócić uwagę. Ja w swoich THC mam dwa wejścia oddzielnie programowalne jedno dla gazu i czujnika pojemnościowego, drugie do pomiaru napięcia łuku.
-
- Lider FORUM (min. 2000)
- Posty w temacie: 7
- Posty: 3576
- Rejestracja: 24 gru 2006, 11:54
- Lokalizacja: już tylko Mysłowice
- Kontakt:
Hypertherm skopiował "swoje" urządzenie z wzorów już istniejących.
Jeżeli chcesz zrobić coś podobnego to musisz mieć komunikację po między wszystkimi urządzeniami by jak korzystają z bazy parametrycznej mogły się wymieniać zmiennymi.
A nie każde urządzenie się do tego nadaje.
I tak ... jak wspominałem o sterowniku HPC
On ma bazę parametryczna i wybierasz rodzaj stali ... okienko poniżej
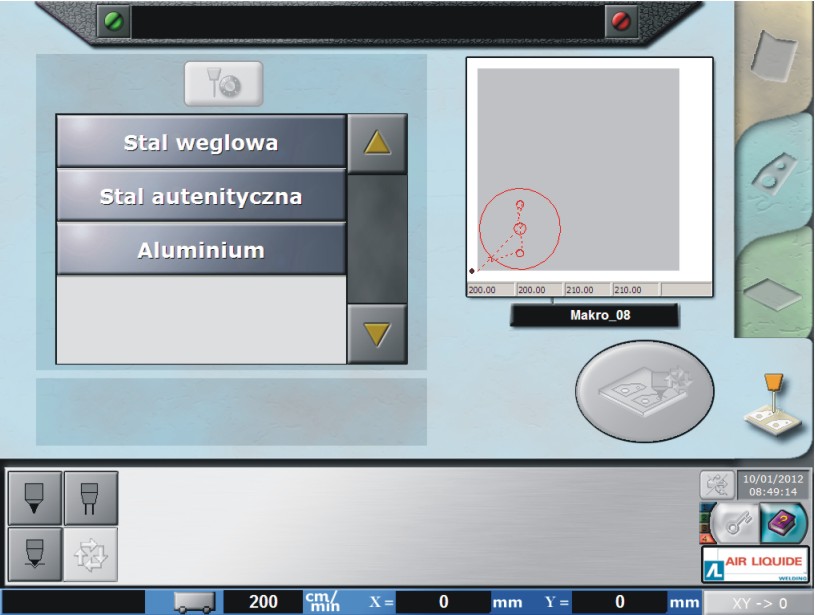
następnie grubość i
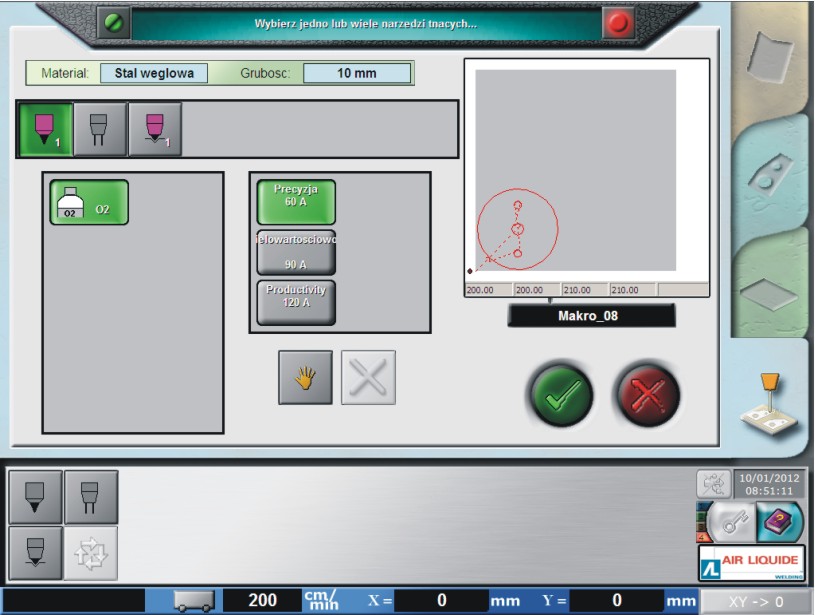
na samym końcu sterownik Ci proponuje jaka ma być jakośc cięcia.
I teraz sterownik po wybraniu najlepszej opcji ładuje odpowiednie parametry do urządzeń.
Czy dasz radę to zrobić u siebie , takie ładowanie
Ja zbudowałem urządzenie do spawania o podobnych własciwościach ale te właśnie właściwości są jako opcja.
A nie każde urządzenie i palnik się do tego nadają.
Jeżeli chcesz zrobić coś podobnego to musisz mieć komunikację po między wszystkimi urządzeniami by jak korzystają z bazy parametrycznej mogły się wymieniać zmiennymi.
A nie każde urządzenie się do tego nadaje.
I tak ... jak wspominałem o sterowniku HPC
On ma bazę parametryczna i wybierasz rodzaj stali ... okienko poniżej
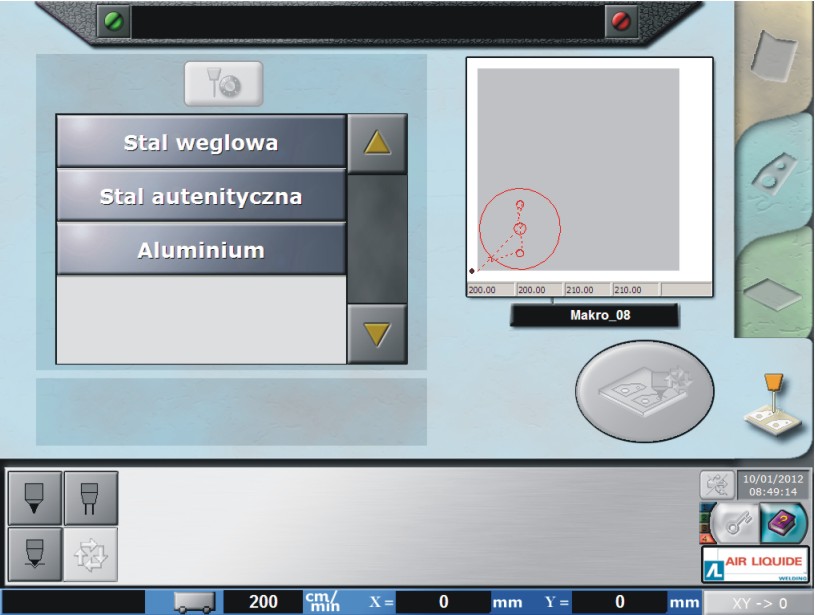
następnie grubość i
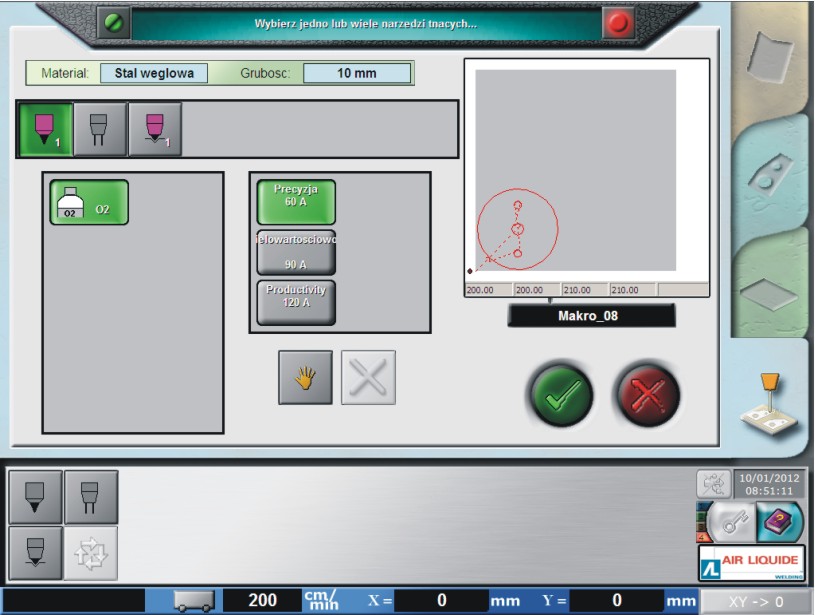
na samym końcu sterownik Ci proponuje jaka ma być jakośc cięcia.
I teraz sterownik po wybraniu najlepszej opcji ładuje odpowiednie parametry do urządzeń.
Czy dasz radę to zrobić u siebie , takie ładowanie

Ja zbudowałem urządzenie do spawania o podobnych własciwościach ale te właśnie właściwości są jako opcja.
A nie każde urządzenie i palnik się do tego nadają.
Pozdrawiam robaczki kolorowe :)
-
Autor tematu - ELITA FORUM (min. 1000)
- Posty w temacie: 8
- Posty: 1126
- Rejestracja: 11 sty 2005, 13:03
- Lokalizacja: Grodków
- Kontakt:
o nie wiem czemu nie dostałem info, że tu coś odpowiedziałeś
, tak właśnie planuję zrobić taką "mini bazę" parametrów tyle, że ustawień mojego kontrolera i ewentualnie notatkę jaki prąd i prędkość cięcia należy ustawić, nie zamierzam sterować źródłem poza włącz/wyłącz ponieważ bardzo mocno uzależniło by to urządzenie od typu posiadanego sprzętu a z założenia ma to być mocno uniwersalne urządzenie.
