Duszczyk_K, oczywiście metoda dobra ale jeszcze moje dwie uwagi...
- lepiej stoczyć pręt 50-60mm... jest sztywniej "na główce", a masa takiego przyrządu robi trochę za koło zamachowe bo flycuttery lubią niskie obroty...
- rowek (otwór) na nóż trzeba wywiercić (wyfrezować) niecentrycznie, żeby płytka była zamocowana centralnie w osi narzędzia...
- rowek może być centralnie jeżeli zamocujemy w nim nóż typu wytaczak jak u mnie (ma centralnie umieszczoną płytkę) ale wytaczak 12x12 wg mnie jest ciut za miękki do stali, w alu robi robotę
- co najważniejsze wrzeciono IDEALNIE W PIONIE inaczej flycutter zrobi schodki... im większa średnica zataczania tym większy schodek pomiędzy przejściami

Właśnie z tym walczę u siebie...
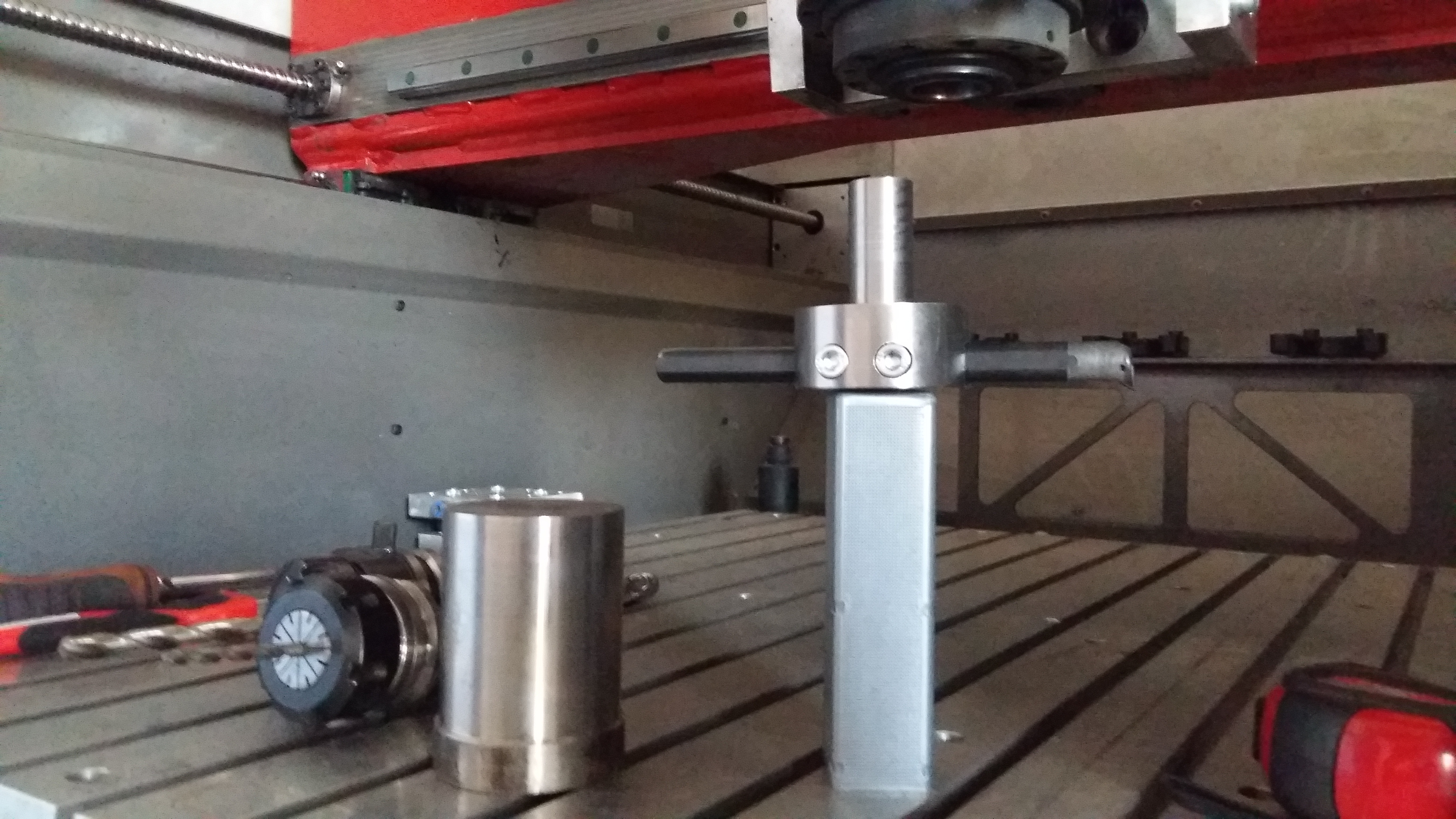
Na zdjęciu moja samoróbka. Fi główki około 52mm, mocowanie fi20x40 mm, dwie śruby M6 10.9 A2... Średnica zataczania maksymalna około 250mm, minimalna około 85mm...
Muszę jeszcze zrobić drugi na nóż kwadratowy lewy (obroty CW) - ta jest na prawy wytaczak (obroty CCW)...
A w drodze od skośnookich głowice fi50 na APKT1604 - będą szybsze niż flycutter, a powierzchnia wykończenia porównywalna
