rc36 Jak mawiają zaplanuj sobie coś, a rozbawisz Boga.
Masz dobre wyczucie czasu bo właśnie przygotowywałem nowego posta z kolejną modyfikacją. Przerwa wynikała z moich problemów budżetowych i konieczności zamrożenia wszelkich wydatków, w tym też warsztatowych :/ Na szczęście to już przeszłość i można działać dalej.
Tematem tej modyfikacji będzie podłączenie falownika do tokarki w możliwie bezpieczny, estetyczny i praktyczny sposób.
Komponenty składowe
Silnik trójfazowy 1.1kW MS 80 3-4
Falownik (chińczyk) 1.5kW HY01D523B
- optoizolator 2xPC817 (DIP4) lub 1xPC827 (DIP8)
Panel
- włącznik zasilania - 1x - MK621 podświetlany (lub podobny)
- przełącznik JOG - 1x - ASW-01 DC12V 20A
- kontrolki - 4x - NXD-212 (do modyfikacji z 12V na 5V)
- diody białe fi 3mm - 12x - (brak danych - jakieś miałem)
- rezystory - 12x - 100Ohm 0,25W
- potencjometr - 1x - 10k liniowy 2W
- gałka potencjometru - 1x - GBC 30
- przekaźnik 24V - 2x - NEC EC2-24NB
- przekaźnik 5V - 1x - NEC EC2-5NB
- złącze główne płytki - 1x - LPH-20
- złącze główne kabla - 1x - FHY-20 kątowe
- złącza kontrolek - 4x - GW-02S + GH-02 (gniazdo-wtyczka 2pin)
- złącze potencjometru,przełączników i przekaźników - 6x GW-03S + GH-03 (gniazdo-wtyczka 3pin)
- złącze "Enable" - 1x - ARK 2 (raster 5.08mm)
- płytka uniwersalna 20x35 pól (moja pochodzi z zestawu uruchomieniowego STM)
Okablowanie główne:
kabel silnika 4x2,5mm2
kabel stycznika E-stop 4x1.5mm2 (lub cieńszy)
Przewód sygnałowy telefoniczny ekranowany 32 żyły (wystarczy 16żył = dwie skrętki)
+trochę kabelków i koszulek termokurczliwych.
Zacznijmy od końca, jaki jest nasz cel:
1. Włącznik zasilania - załącza zasilanie na falownik i sygnalizuje włączenie podświetleniem
2. Przycisk JOG dwukierunkowy - umożliwia uruchomienie silnika na wolnych obrotach w obu kierunkach
3. Potencjometr - umożliwia zmianę obrotów silnik
4. Kontrolki
- Czerwona - sygnalizuje włączenie się falownika (jest spore opóźnienie pomiędzy załączeniem zasilania i uruchomieniem się falownika)
- Zielona - sygnalizuje kiedy wszystkie "krańcówki" w tym E-Stop są włączone są w pozycji pracy.
- Niebieska - sygnalizuje kiedy falownik wysterowuje silnik (w czasie hamowania też)
- Żółta - sygnalizuje błąd falownika - np przeciążenie i konieczność restartu przyciskiem na panelu falownika
To tyle jeśli chodzi o wstęp. Teraz pytanie jak to osiągnąć?
Zacznijmy od kontrolek. Nie udało mi się znaleźć fajnych kontrolek na 5V (kwestia gustu) wiec postanowiłem przerobić kontrolki 12V, które pasowały mi rozmiarem i wyglądem.
W fabrycznej postaci mają one w sobie małą żarówkę która nie daje za dużo światła przy niższym niż 12v zasilaniu. W falowniku mamy dostępne zasilanie 24V i 5V (nie liczę zasilania referencyjnego 10V do potencjometru bo ono ma za małą wydajność).
Fabryczną żarówkę zamieniam na 3 diody z szeregowo podłączonymi rezystorami 100Ohm:
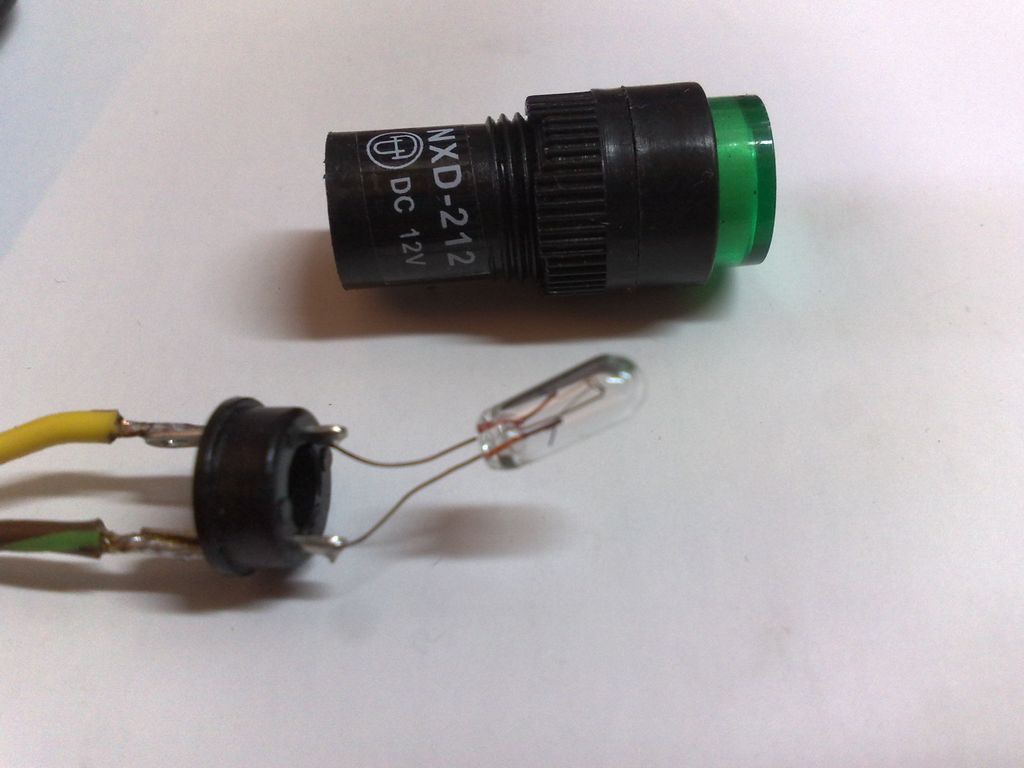
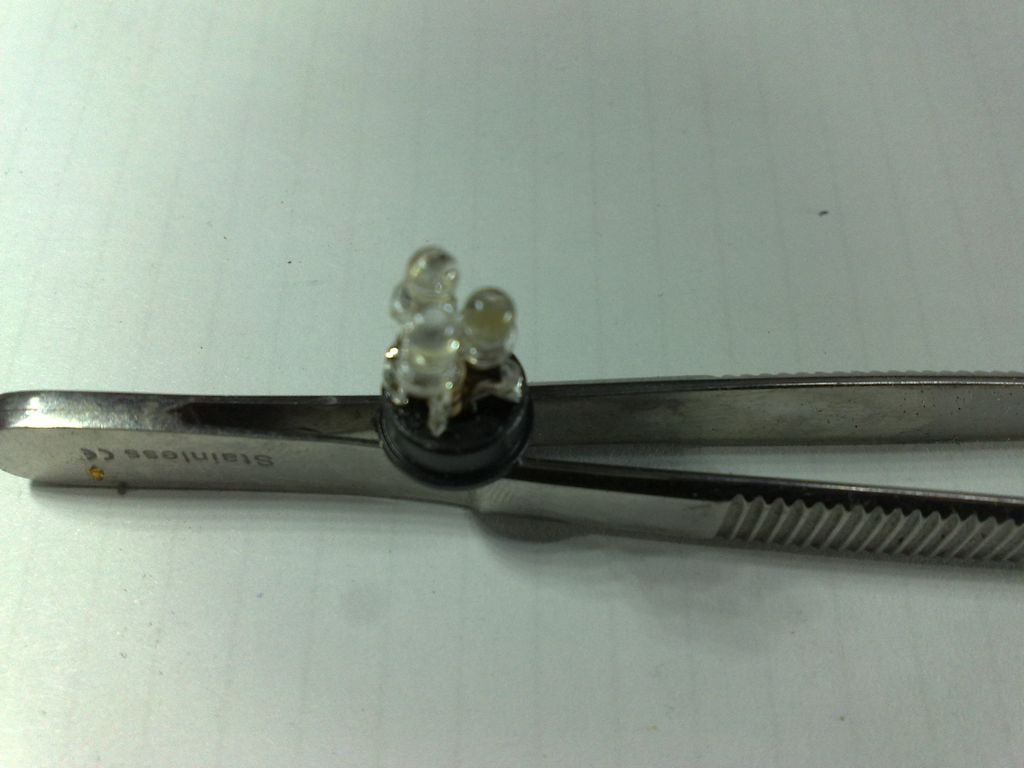
Po przerobieniu kontrolek przystępuje do przymiarki pasowania poszczególnych elementów na skrzynce:
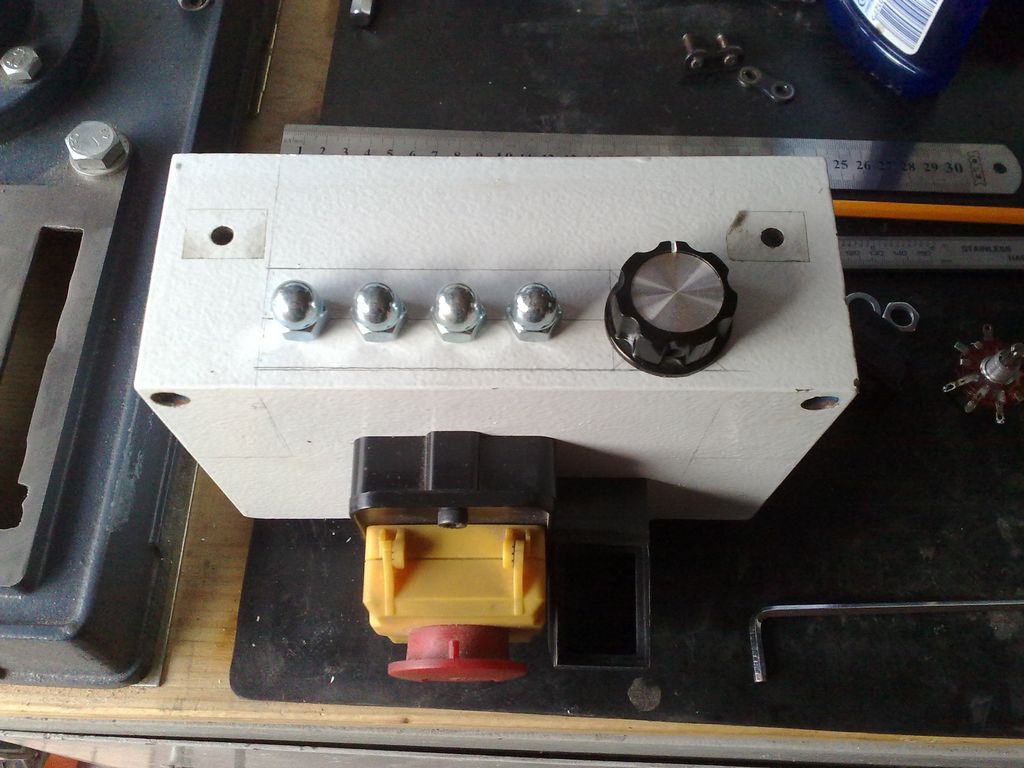
Dla bezpieczeństwa i zachowania czystości maskowanie elementów przed obróbką
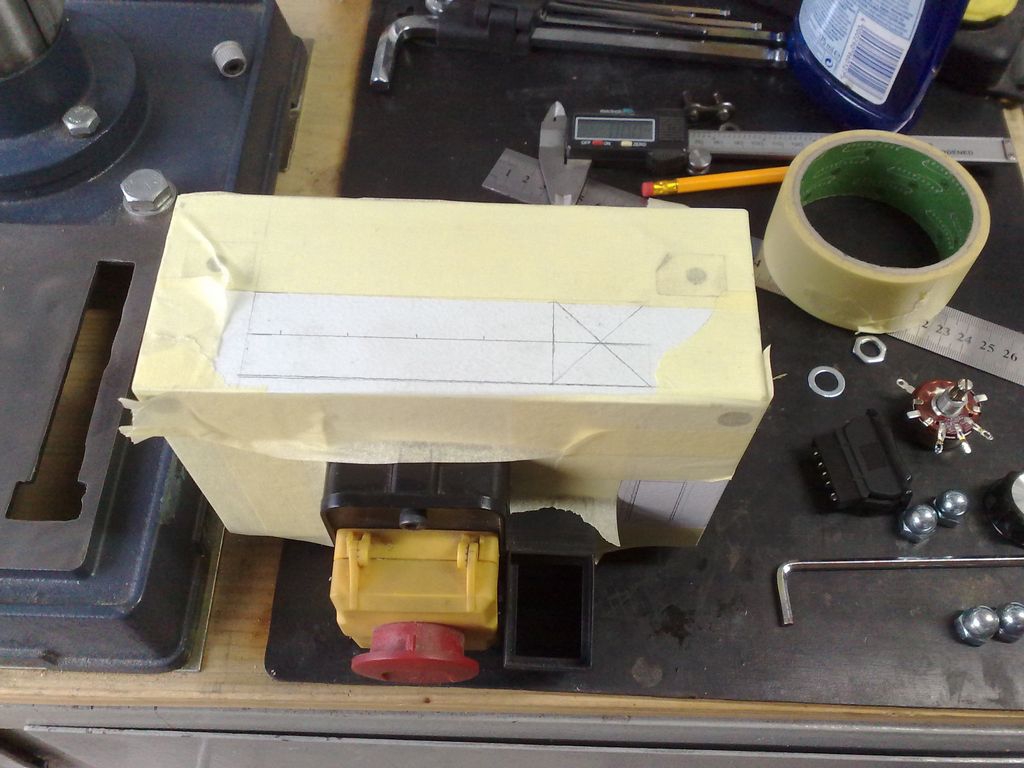
Trzeba bardzo dokładnie wyznaczyć punkt mocowania potencjometru żeby wszedł do środka odlewu. Jest tu ciasno szczególnie dla 2W wersji potencjometru. Wybrałem taką sądząc, że może dłużej wytrzyma, zobaczymy.
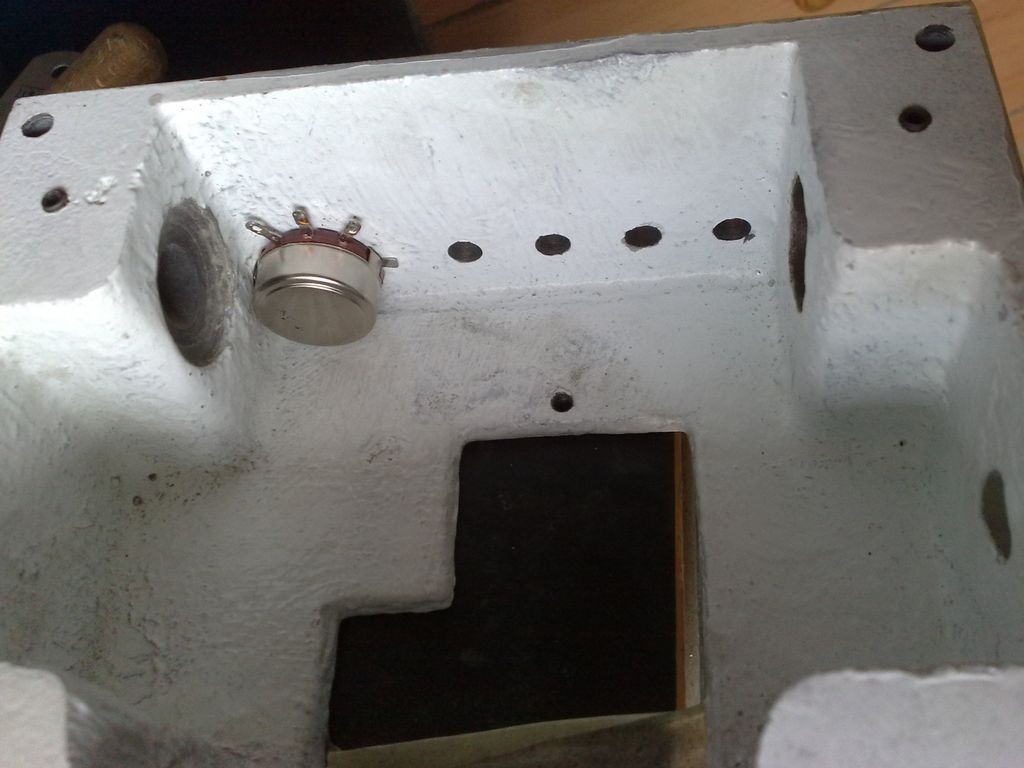
Wycięcie pod przełącznik było trochę trudniejsze, zużyłem całą tarczę z "dremela" żeby się udało. Chyba lepiej by było wywiercić masę małych dziur i dopiero ciąć. Ten odlew jest naprawdę gruby.
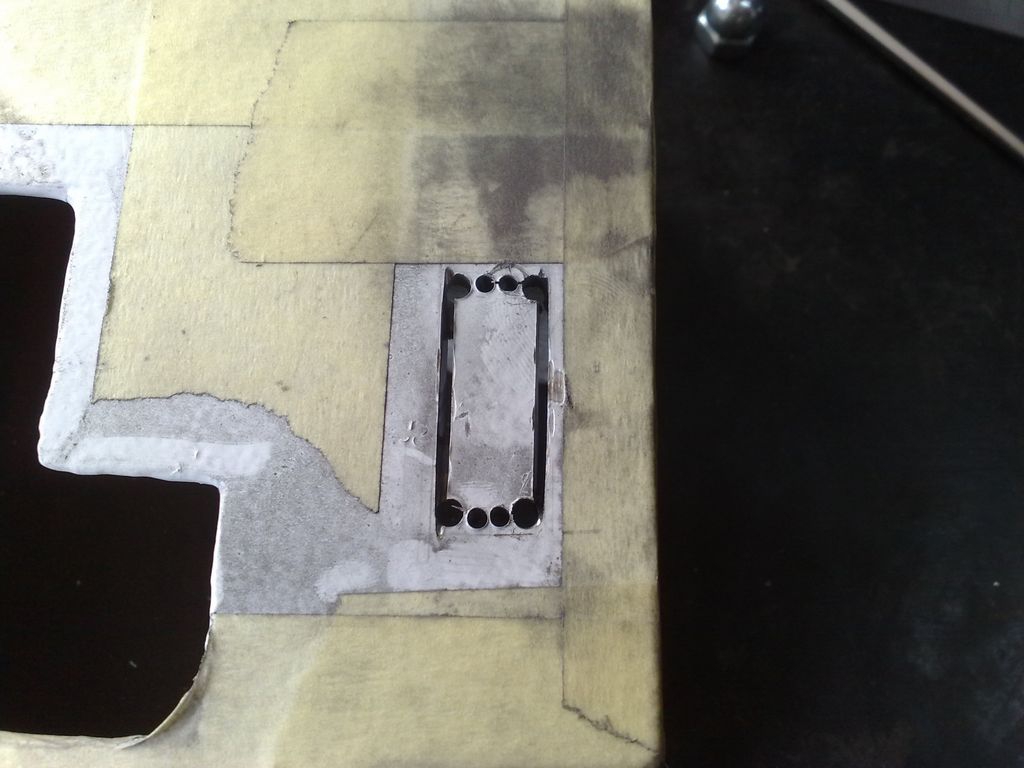
Ostatecznie mniej więcej takie wymiary wyszły umieszczonych elementów, licząc od prawego przedniego narożnika skrzynki:
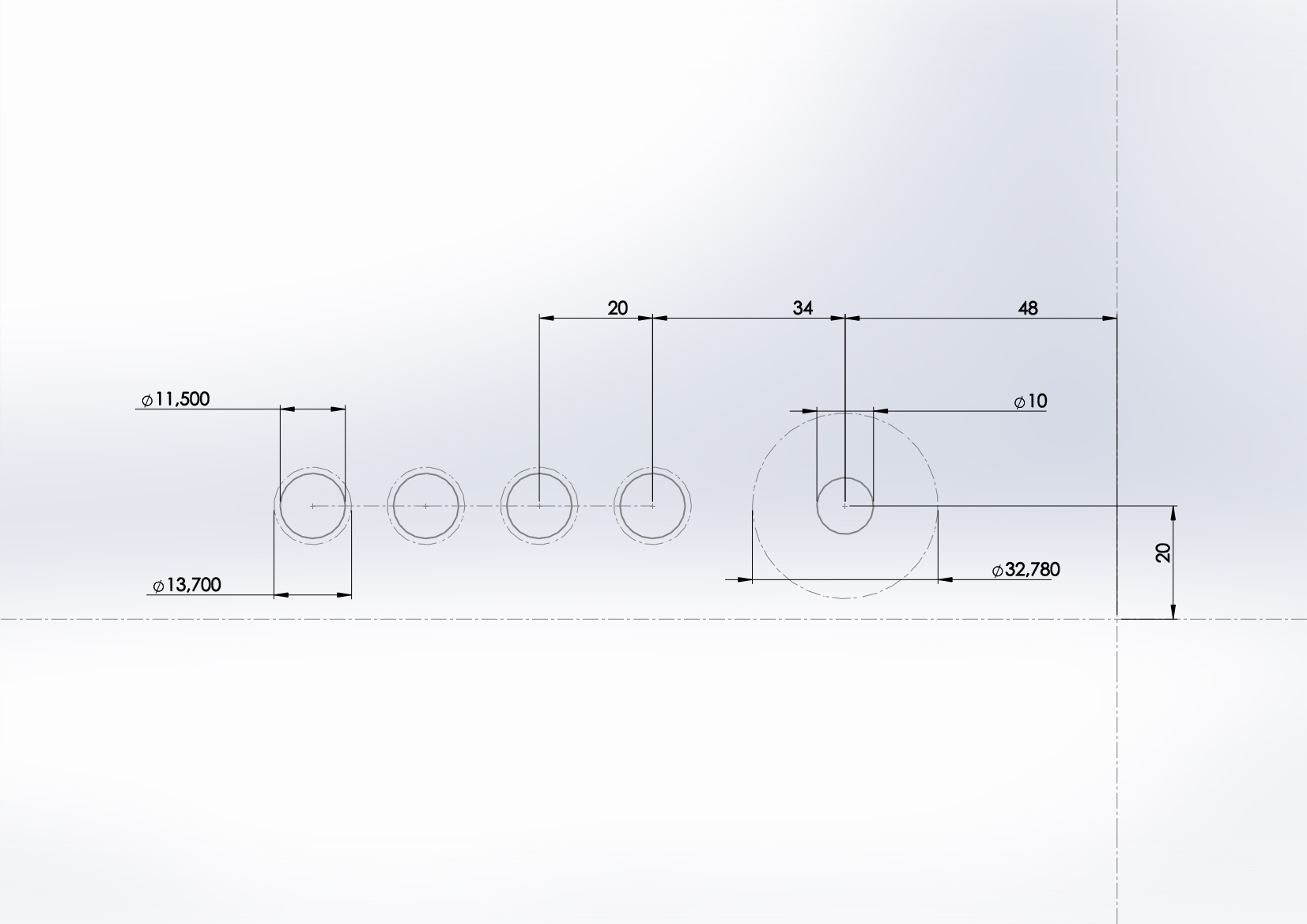
Teraz to całe ustrojstwo trzeba podłączyć do falownika w przystępny dla niego sposób.
Dysponuje on (strona 12 instrukcji - schemat)
1. dwoma wyjściami przekaźnikowymi FA,FC które postanowiłem pozostawić na "czarną godzinę" do sterowania innymi urządzeniami.
2. dwoma wyjściami tranzystorowymi DRV i UPF, wybrałem je do sterowania kontrolkami żółtą (błędu) oraz niebieską (praca silnika).
3. wejście potencjometru VR,VI,ACM
4 wejścia cyfrowe:
- FWD (wybrane do pracy - silnik do przodu),
- REV (wybrane do pracy - silnik do tyłu),
- RST (wybrane do pracy - JOG do przodu),
- SPH (wybrane do pracy - JOG do tyłu),
- SPM (wybrane do pracy - Maszyny STOP - podłączone pod zanegowane ENABLE),
Na podstawie instrukcji powstały następujące schematy:
Podłączenie potencjometru jest banalne bo to tylko kable podłączone pod odpowiednie WE/WY w falowniku:
Sterowanie kontrolkami żółtą i niebieską przy użyciu wyjść cyfrowych 24V (UPF i DRV) . Konieczne było użyć przekaźników aby wykonać separację 24V -> 5V, przy okazji zyskujemy dodatkowe wyjścia z przekaźników, które będą sygnalizowały to samo co diody. Przykładem użycia może być załączanie chłodziwa dopiero jak startuje silnik albo coś w tym rodzaju.
Przybliżony schemat:
Trzeci układ jaki jest potrzebny zaświeca czerwoną diodę kiedy pojawia się zasilanie na falowniku, zieloną kiedy włączona jest GOTOWOŚĆ=ENABLE, czyli grzybek wyciągnięty oraz zasila przyciski sterujące kiedy jest GOTOWOŚĆ. W tym układzie też konieczna jest separacja 24V -> 5V ponieważ kontrolki chodzą na 5V a przyciski sterujące na 24V.
Na schemacie stycznik grzybka oraz inne styki z osłon itd są reprezentowane przez przycisk ENABLE. Będą one połączone szeregowo i wszystkie będą musiały być zwarte aby silnik mógł być uruchomiony. Domyślnie przekaźnik jest wyłączony i zwiera do masy DCM wejście cyfrowe SPM, które będzie skonfigurowane jako STOP lub EMERGENCY STOP w zależności od upodobań. Dodatkowo przyciski JOG i RUN nie zadziałają póki przekaźnik się nie przełączy i nie zaświeci się zielona kontrolka.
Dobra, teraz czas to wszystko zmontować. Mając na stanie kilka płytek uruchomieniowych postanowiłem, że nie będę robił dedykowanej płytki drukowanej na ten cel. Montaż odbył się na zasadzie "druciarstwa":
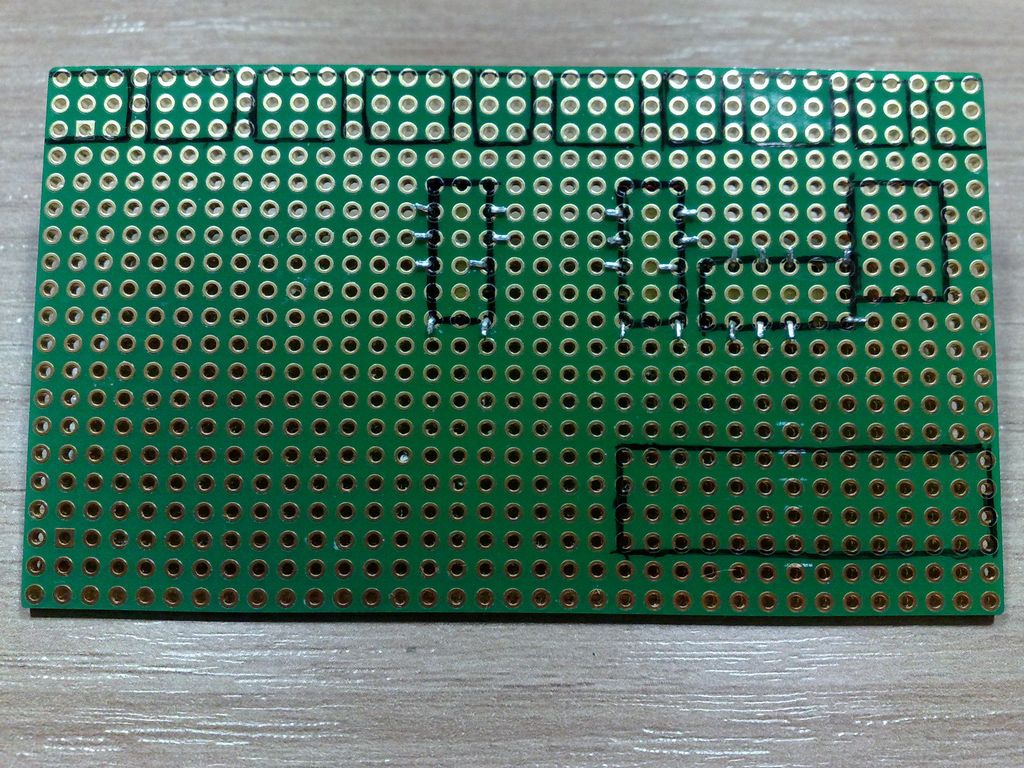
Na zdjęciu widać drobną poprawkę (Linia koloru szarego), w wersji na zdjęciu do potencjometru była podłączona masa DCM a nie jak powinna ACM
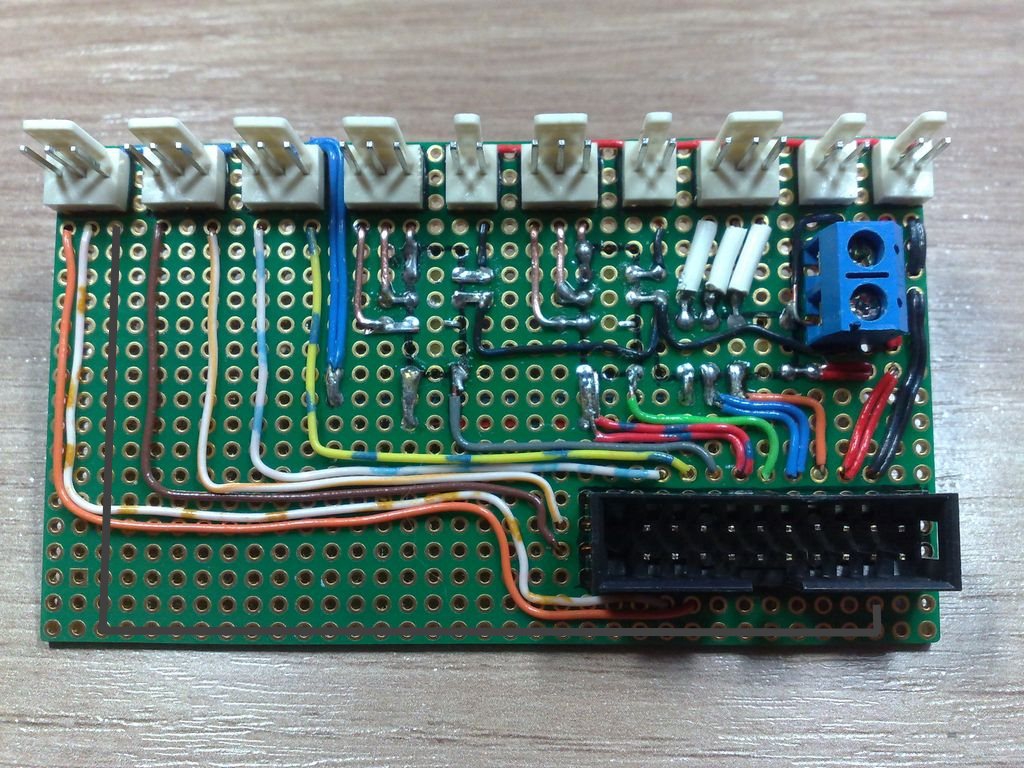
Diagram przedstawia sposób połączeń na płytce bo na zdjęciach nie widać wszystkiego.
Jakby ktoś pytał to na fioletowo są zwory od spodu płytki. Poniżej diagramu tabela z opisem wtyczki (zgodnie z układem na diagramie).
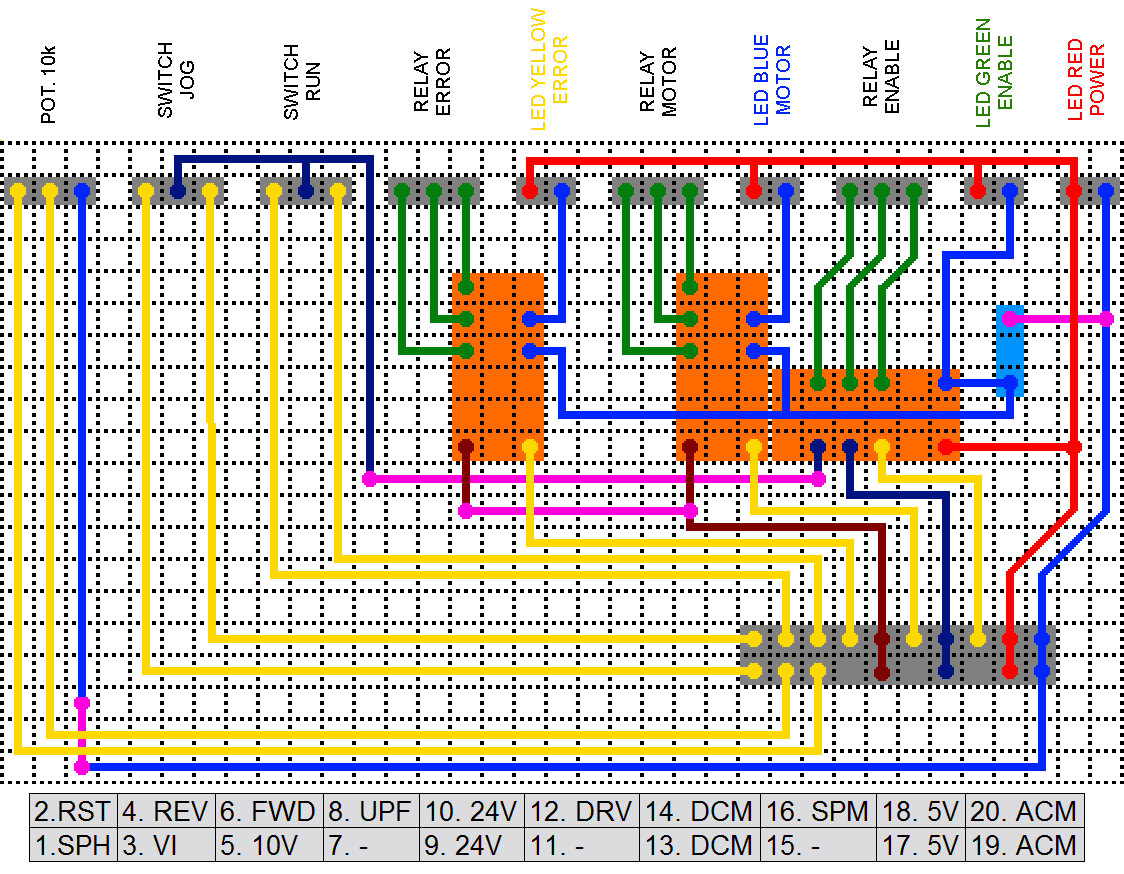
I teraz kiedy to wszystko podłączymy czeka nas niespodzianka bo mimo poprawnej konfiguracji nie działają diody żółta i niebieska.... a dlaczego?
Otóż w falowniku brakuje optoizolatorów na wyjściach UPF i DRV:
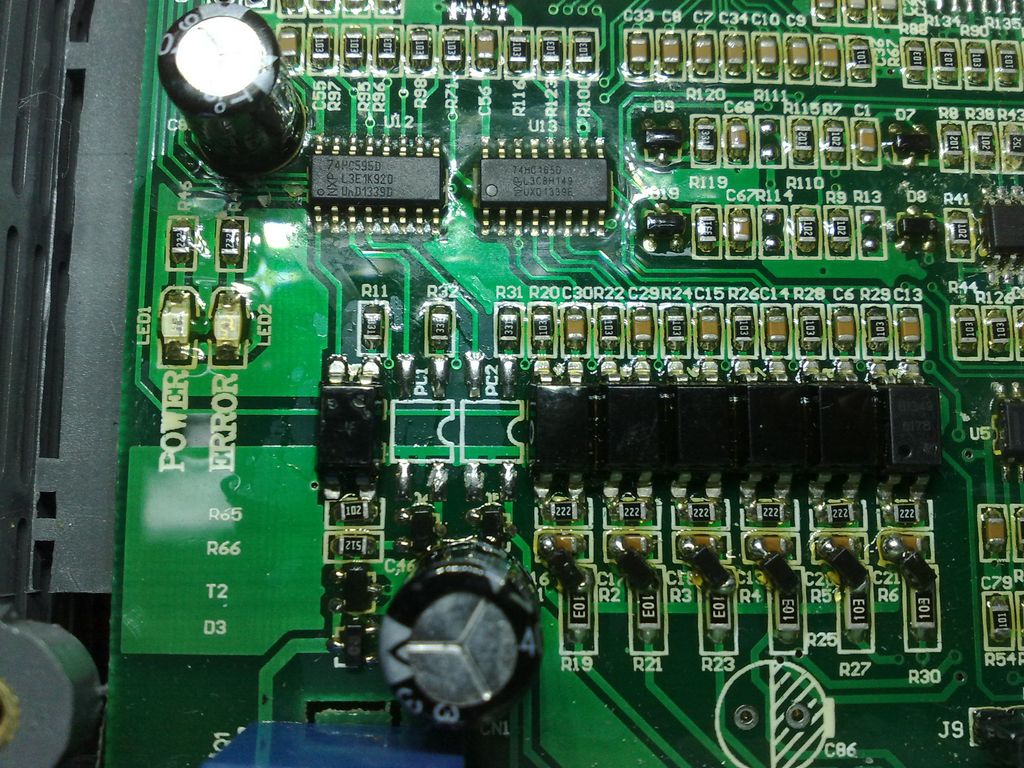
I teraz przychodzi czas na zamontowanie elementu 817/827
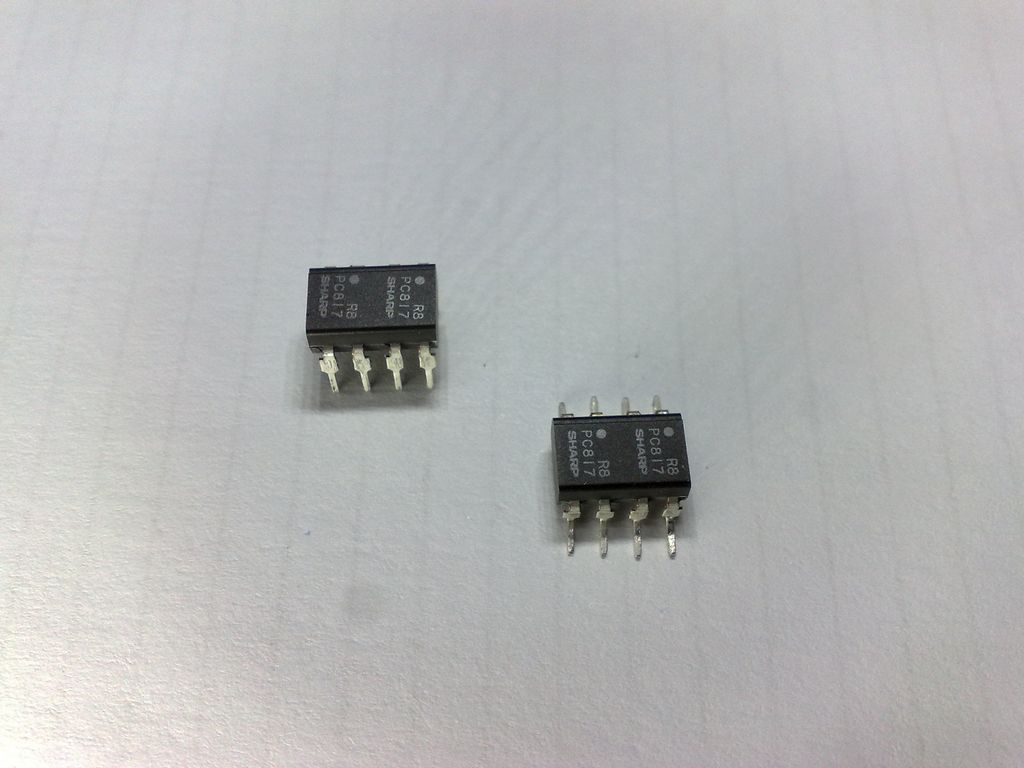
Przy montażu należy pamiętać że przeciwnie do wszystkich pozostałych optoizolatorów w falowniku PC1 i PC2 pracuję jako wyjścia, a nie wejścia wiec należy je wlutować odwrotnie niż pozostałe (Patrz na kropki).
Do panelu potrzebny jest jeszcze grzybek z przełącznikiem zasilania.
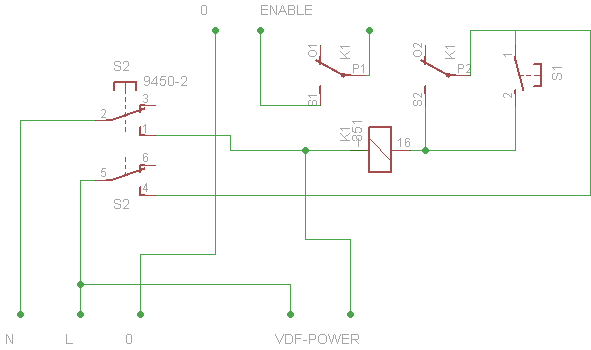
Tu mamy lekkie zamieszanie:
- żółto zielony wiadomo uziemienie które pójdzie na obudowę tokarki
- niebieski N też wiadomo podłączamy na styki wejściowe przełącznika - te bez żarówki
- brązowy L faza też podłączamy na wejściowe styki przełącznika
- drugi brązowy krótki przewód ma za zadanie doprowadzić zasilanie do cewki podtrzymującej stycznik grzybka
- Czarny przewód ma wrócić zasilanie do falownika. Tak, że przełącznik zasilania ma dwie funkcje: 1. zasilanie falownika, 2. zasilanie grzybka. Dlatego właśnie potrzebne są 4 przewody w kablu zasilania.
To już wszystkie komponenty, które składają się na panel sterujący. Wszystko ładnie trzeba upchnąć w odlewie.
Teraz trzeba przygotować kabel sygnałowy, ja użyłem odpadu z kabla telekomunikacyjnego 4x(4 pary)=32żyłu. Minimalna ilość przewodów potrzebnych do działania to 16, czyli dwie skrętki. Ja miałem taki tabel na moim złomie więc taki użyłem. Podwójny ekran nikomu nie zawadzi.
Kable telefoniczne niestety mają PARY kabli o tych samych kolorach, więc najpierw trzeba przedzwonić każdy i rozdzielić z każdej pary (żółtymi koszulkami). Przed lutowanie koniecznie trzeba umieścić odpowiedniej wielkości koszulki izolacyjne.
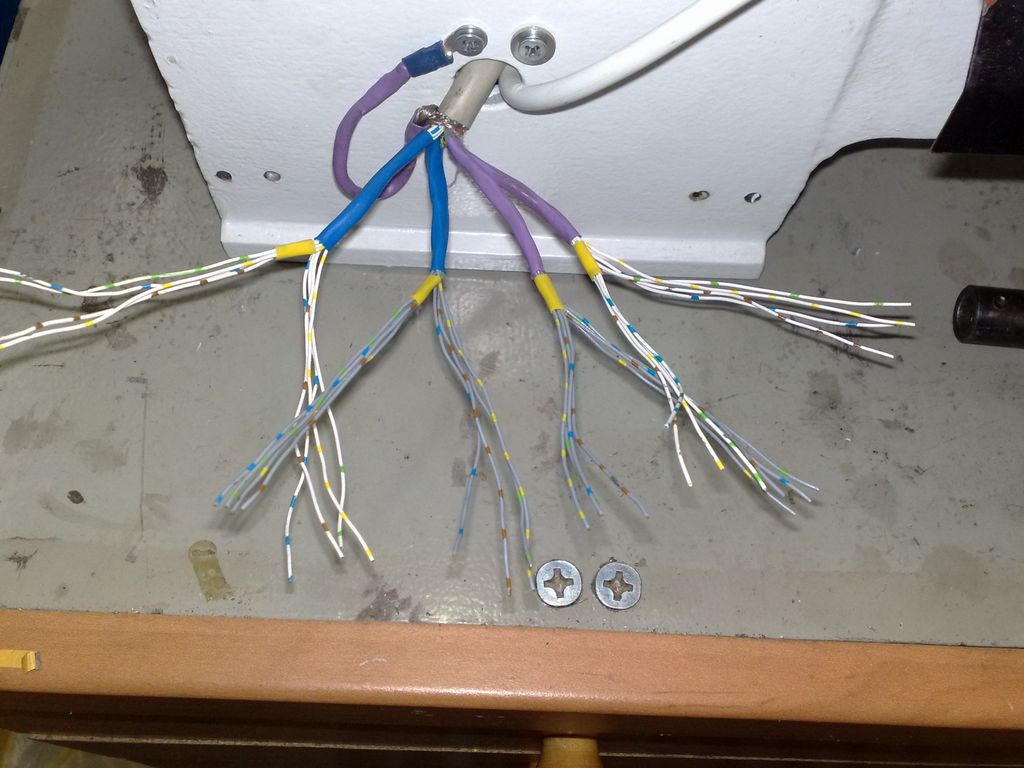
Wiem, że lutowanie kątowego wtyku na pająka to lekka fuszerka, ale w pierwotnym planie miał tu być wtyk z grzebieniem na taśmę ale okazało się, że kable telefoniczne są stanowczo za grube żeby weszły w ten grzebień, tak ratowałem sytuację.
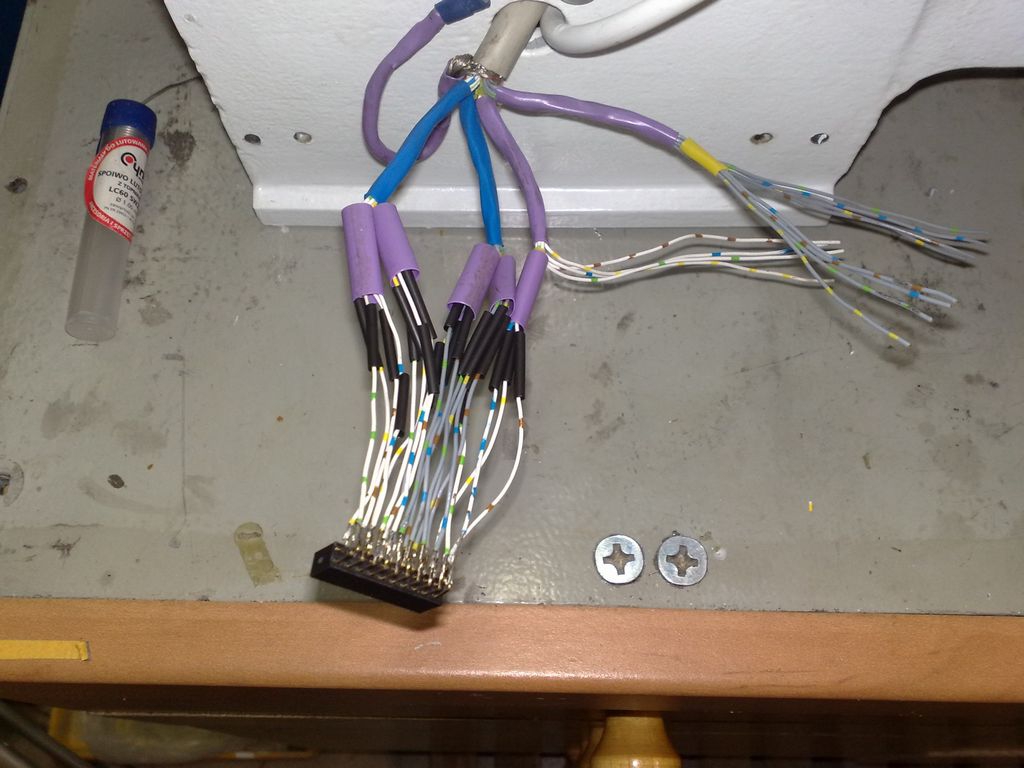
Tu jeszcze jedna globalna koszulka termokurczliwa żeby trzymała wszystko i przymiarka wszystkiego razem.
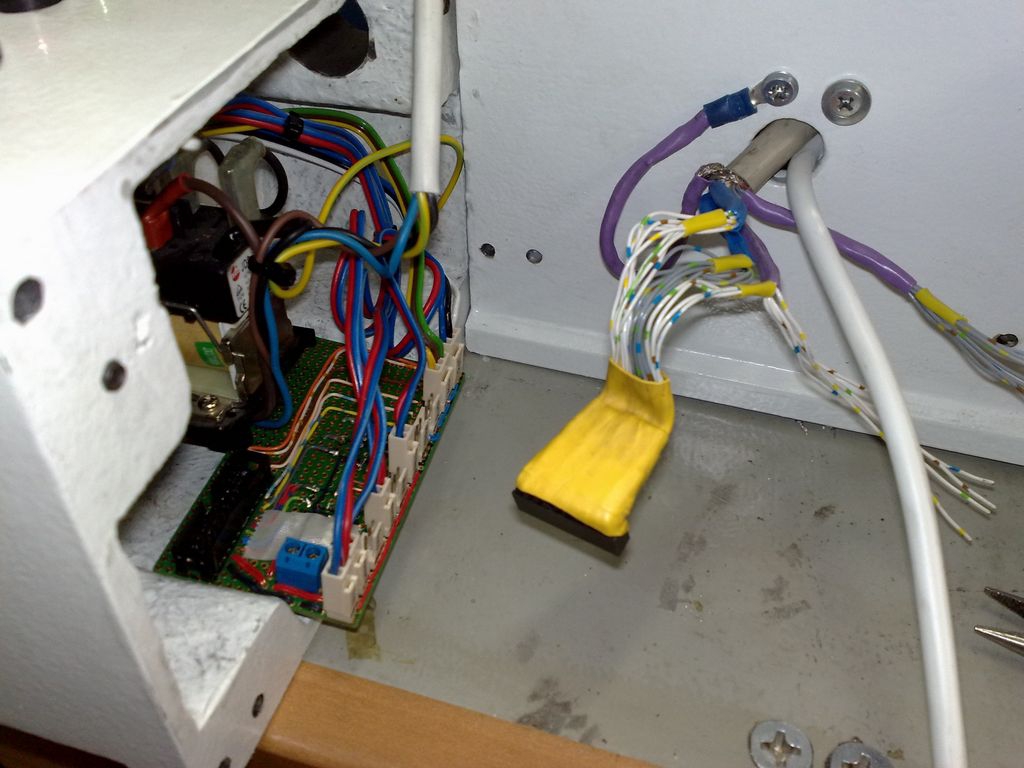
Sygnał a ENABLE na styczniki osłony uchwytu i obudowy gitary został wpięty szeregowo w sygnał grzybka i wyprowadzony na zewnątrz (przeźroczysty przewód). Na razie nie mam zamocowanej osłony ani fabrycznej obudowy gitary, ale w przyszłości ten kabel może się przydać.
Cała druciarska płytka została zaizolowana ze wszystkich stron taśmą, a wszystkie kable zostały zasłonięte przez dorobioną plastikową osłonę, na wszelki wypadek żeby wałek nie wciągnął czegoś co leży luzem. Klej na gorąco przyjacielem każdego
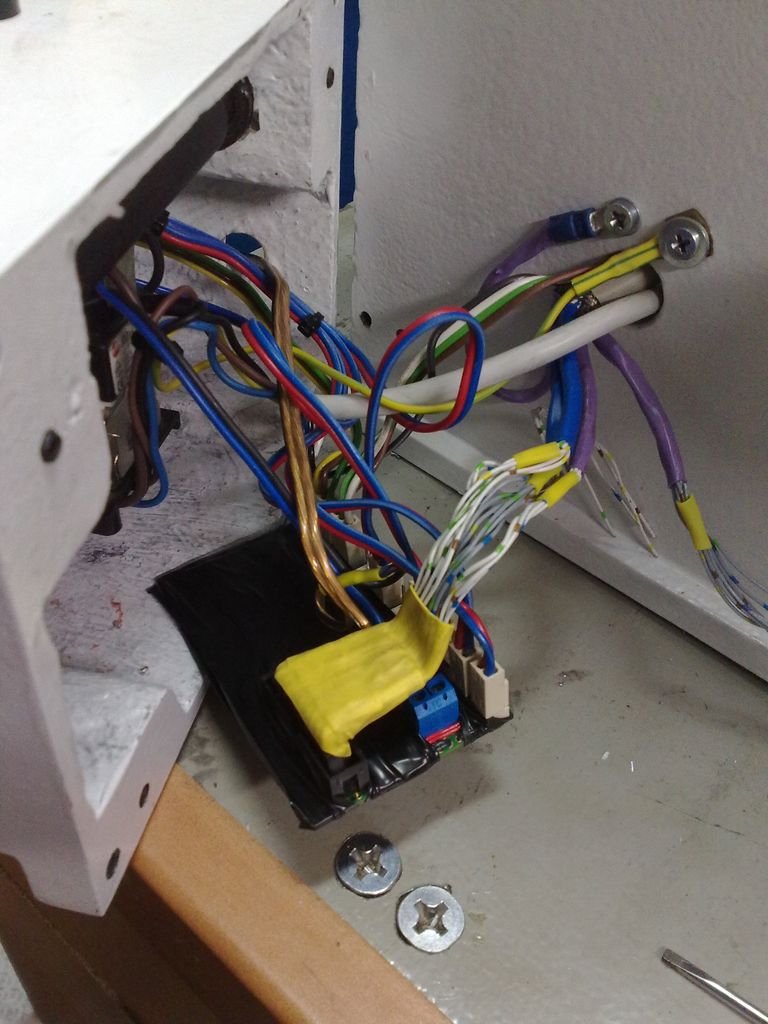
Przełącznik kierunku obrotów został wyprowadzony na zewnątrz i tymczasowo podpięty pod stary przełącznik obrotów, zostanie on jednak zmieniony na trójpozycyjny ponieważ uniemożliwia on wykorzystanie przycisku JOG (tokarka od razu startuje po włączeniu ENABLE). Docelowo będzie to obrotowy przełącznik na suporcie z dźwignią jak w dużych tokarkach. Wtedy w pozycji środkowej STOP będzie można użyć JOG.
Falownik został umieszczony na płycie wiórowej zawieszonej na linie gumowej do stołu tokarki
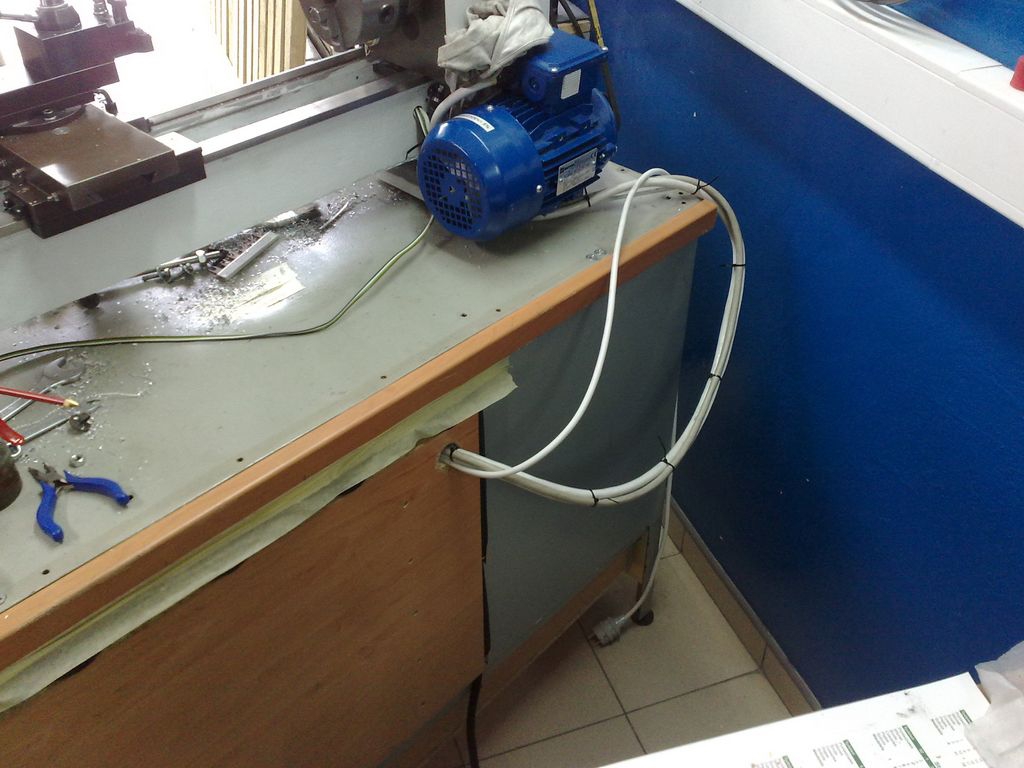
Z odrzutów mebli,czyli materiał za free, wykonałem sobie szufladki (stolarza ze mnie nie będzie

), tak aby trzy górne szufladki były krótsze i chowały za sobą "skrzynkę" sterowniczą.
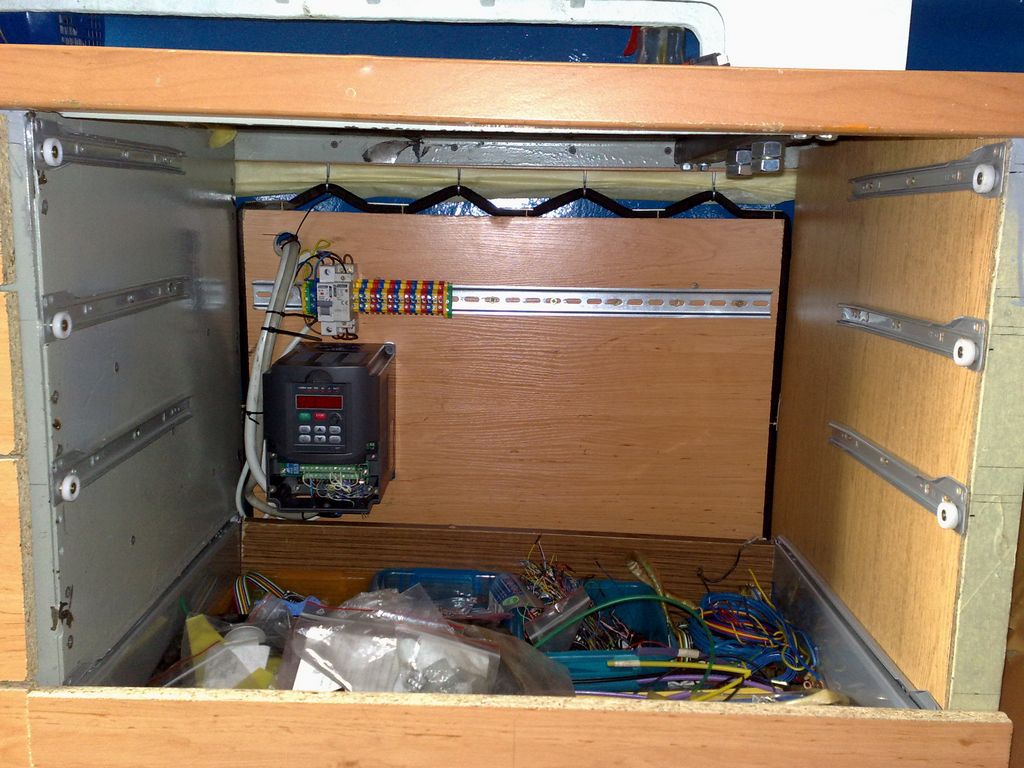
Teraz pozostaje tylko jedna sprawa:
Konfiguracja Falownika
Zawsze należy zacząć od resetu do ustawień fabrycznych:
PD013 = 1 (SET)
Ustawić parametry silnika ściągnięte z tabliczki znamionowej:
PD141 = 220 (Napięcie zasilania silnika)
PD142 = 4.6 (Prąd uzwojenia - w moim przypadku 4.62A)
PD143 = 4 (Ilość biegunów silnika - w moim przypadku 4)
PD144 = 1390 (Obroty znamionowe przy 60 Hz)
Należy uruchomić możliwość sterowania z panelu zewnętrznego
PD001 = 1 (1 czyli zewnętrzny panel) - dodatkowo trzeba pamiętać aby przestawić zworkę na falowniku aby działał zewnętrzny potencjometr a nie ten z panelu, jest ona umieszczona po prawej stronie wejść/wyjść falownika (str 10 w instrukcji) zworka po lewej stronie oznacza zewnętrzny potencjometr.
Określić maksymalną częstotliwość falownika
PD005 = 100 (100Hz aby zabezpieczyć się przed zbyt dużymi obrotami na wyższym biegu tokarki)
Określić środkową częstotliwość falownika:
PD006 = 8 (od tego parametru zależy nachylenie krzywej prędkości - można go potem regulować w przedziale PD007-PD005)
Określić minimalną częstotliwość falownika:
PD007 = 4
Trzy powyższe parametry pewnie ulegną zmianie podczas tuningu tokarki wiec nie ma co przykładać do nich większej wagi. Należy tylko pamiętać, żeby nie przekraczać górnej częstotliwości bo uchwyty tokarskie mają maksymalne obroty 3000/min i łatwo będzie przekroczyć tą wartość na wyższych biegach.
Ustawić dolny limit częstotliwości, ja ustawiłem go na minimalną częstotliwość przy której mój silnik startuje, co nie znaczy, że jest do częstotliwość przy której będzie pracował.
PD011 = 7 (Przy 7Hz mój silnik się zaczyna kręcić)
Teraz ważne: Rampa przyspieszania i opóźniania pracy silnika przy start i stop. Jeśli te wartości będą źle ustawione to odbije się to na mechanice tokarki i może doprowadzać do przeciążania falownika przy rozruchu i hamowaniu. Ja ustawiłem na dolne granice przy których nie wyrzuca błędu na najwyższym biegu:
PD014 = 1.6 (Przyspieszenie przy starcie)
PD015 = 1.8 (Opóźnianie przy hamowaniu)
Umożliwienie pracy silnika na wstecznym
PD023 = 1
Częstotliwość nośna. Niektóre silniki wydają dziwne dźwięki jeśli ta wartość do nich nie pasuje, należy ja dobrać eksperymentalnie.
PD041 = 10 (u mnie najciszej jest przy wartości 10)
Prędkość silnika dla funkcji JOG
PD042 = 15 (ustawiłem na 1/4 pracy sieci) przy tej wartości silnik ma jeszcze trochę siły. Poniżej już jest bardzo słaby.
Określenie funkcji wejść cyfrowych - tabelka strona 20
PD044 = 02 (odpowiada za wejście FOR) ja użyłem tego wejścia pod przycisk Bieg do przodu
PD045 = 03 (odpowiada za wejście REV) użyte dla biegu w tył
PD046 = 07 (odpowiada za wejście RST) użyte jako JOG do przodu
PD047 = 08 (odpowiada za wejście SPH) użyte jako JOG do tyłu
PD048 = 13 (odpowiada za wejście SPM - na stronie 20 jest błąd w tabeli opisane jako SPL) użyte jako Emergency STOP
Wejście SPL pozostaje do wykorzystania
Określenie funkcji wyjść cyfrowych
PD050 = 1 (Odpowiada za wyjście DRV - w instrukcji Y1) użyte do sygnalizacji pracy silnika
PD051 = 3 (Odpowiada za wyjście UPF - w instrukcji Y2) użyte do sygnalizacji błędu falownika
Wyjścia przekaźnikowe FA FC pozostają do wykorzystania.
Określić przedziały częstotliwości dla maksymalnej i minimalnej wartości na potencjometrze prędkości:
PD072 = 107 (Przy tej wartości na wyświetlaczu pojawia się u mnie 100Hz - pewnie wina potencjometru )
PD073 = 20 (Minimalna wartość obrotów silnika przy regulacji potencjometrem - ustaliłem sobie na 1/3 obrotów znamionowych) przy niższej wartości silnik słabnie
Z tego co widzę pozostałe parametry pozostają bez zmian i nie trzeba ich dotykać jeśli zrobiło się reset ustawień.
Jeszcze na koniec kilka fotek
Panel podczas pracy:
Konfiguracja tymczasowa kół pasowych i paska klinowego:
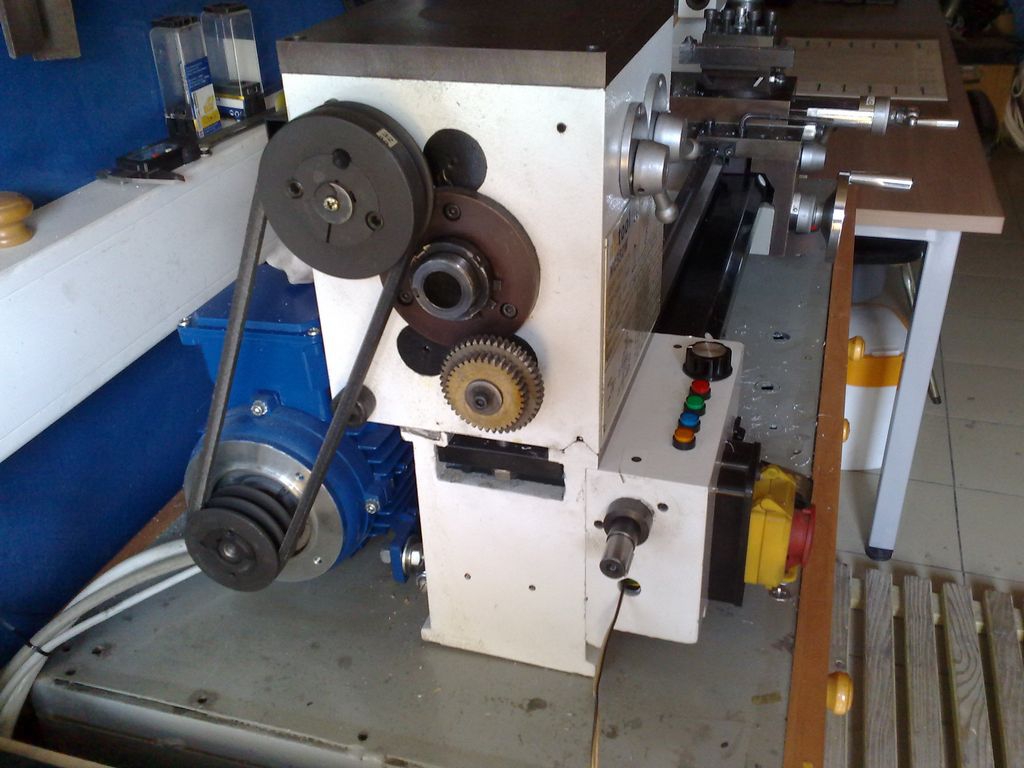
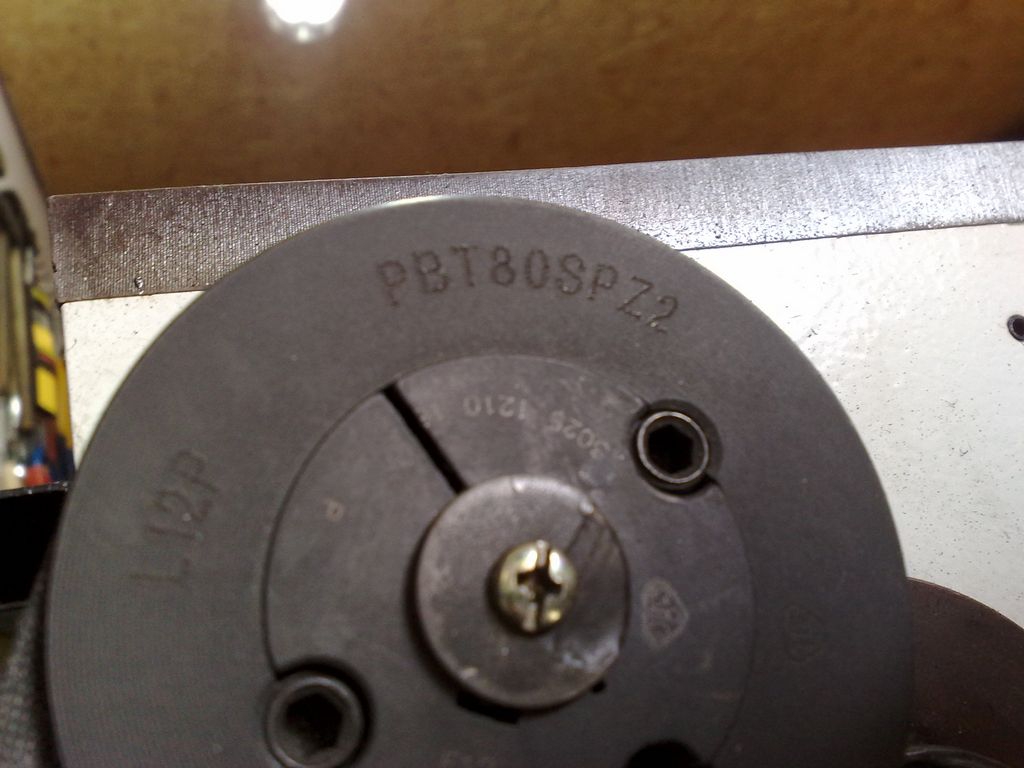
To powinno wystarczyć każdemu do realizacji zadania. Ostrzegam tylko, że można różnie podłączyć sobie przełączniki i potencjometr więc może okazać się, że konieczne będzie zamienienie żył we wtyczkach lub zmiana konfiguracji falownika.
Kolejne posty mogą się pojawić trochę późnij ponieważ teraz projektem głównym jest przystosowanie samochodu na wakacje. Obiecuje jednak, że mam jeszcze kilka fajnych rzeczy w zanadrzu do pokazania i prędzej czy później się tu pojawią.
Jeśli o czymś zapomniałem proszę o info na prv.
Pozdrawiam forumowiczów
