Właśnie odebrałem paczuszkę z Melonkote 850. Dziękuje Bardzo koledze Melonmelon. Czy mogę się jakoś odwdzięczyć?
Ładny kolega ma zbiór książek. Czy jest jakaś możliwość skorzystania z nich?
Mam w sumie Bibliotekę Jagiellońską całkiem niedaleko ale nie jestem już studentem więc mogę skorzystać tylko z czytelni - jako student też miałem tylko katę do czytelni bo byłem na AGH. W Jagiellonce powinno być wszystko. Myślałem o pożyczeniu kilku wybranych pozycji i zdigitalizowaniu w rozsądnym czasie, i oddaniu w stanie nie zmienionym.
Spotkać się ... no tak Częstochowa, Poznań i Olkusz to przecież tak blisko. Chyba że będziemy pić piwo i cydr przez skype.
NC4 - nie wszędzie sprzedają, NC6 przyniósł klient. Ja jeszcze nie mam składu ze stalą bo nie wiem jaką wybrać na magazyn. Mam zdobyczną fi50 1mb NMV.
Izolacja w środku wiem że chłonie wodę ale to byłby kompromis jakiś.
Teraz chciałbym sformować problem czyli cel jaki chcę osiągnąć (choćby tylko w teorii).
Hartowanie stali narzędziowych węglowych i stopowych może szybkotnących bez odwęglenia (innych uszkodzeń) o jakości gotowego wyrobu co najmniej dobrej . W warunkach nieprzemysłowych, półprofesjonalnych w ilościach jednostkowych. Wydawało mi się że piec próżniowy może być dobrym rozwiązaniem do realizacji takiego zadania. Prawdopodobnie zasugerowane zostało to przez materiały reklamowe jakie można znaleźć w internecie na temat hartowania. Może lepsza będzie inna technologia niepróżniowa? Czyli zacząłbym teraz od przeglądu istniejących rozwiązań. Może mniejszym nakładem sprzętu i pieniędzy można osiągnąć cel.
Znaleziono 4 wyniki
Wróć do „Piec próżniowy budowa, hartowanie.”
- 06 kwie 2017, 11:13
- Forum: Spawalnictwo i obróbka cieplna
- Temat: Piec próżniowy budowa, hartowanie.
- Odpowiedzi: 12
- Odsłony: 4669
- 01 kwie 2017, 02:34
- Forum: Spawalnictwo i obróbka cieplna
- Temat: Piec próżniowy budowa, hartowanie.
- Odpowiedzi: 12
- Odsłony: 4669
W końcu znalazłem chwilkę na przeczytanie zadanych lektur.
Z wykresu poniżej widzę że musimy zejść z temperatury austenityzowania poniżej 550st C w najwyżej 48 sekund.
. Wydawało mi się że jak hartujemy to chłodzimy na maksa i tyle bez filozofii na przystanki i takie tam - teraz wiem że to nie do końca takie proste i oczywiste.
Zimnych końców termopary nie trzyma się w 0 st.C tylko stosuje układy kompensacyjne są gotowe specjalizowane układy scalone i problem z głowy. Tylko ten układ musi się znajdować tam gdzie te zimne końce i mieć taką samą jak one temperaturę.
Na podstawie wyników hartowania przedstawionych w artykule "Obróbka cieplna stali przeznaczonych na części maszyn i narzędzia do obróbki plastycznej w zmodernizowanym piecu próżniowym RVFOQ-224" wnioskuję że nie ma sensu bawić się w chłodzenie gazowe. Wystarczy "wsadzić" wannę z olejem do komory próżniowej (dodatkowej komory nie koniecznie próżniowej ale aby zachować ciągłość gazu ochronnego). Jakby to było takie proste
. Mniejsza komplikacja pewniejszy efekt - prędkość chłodzenia dostępna w szerszym zakresie.
Mamy już konkretne dane z jednostkami na temat chłodzenia w gazie:
heat transfer coefficient α up to 800 [W/m2K])
prędkość chłodzenia (nie wiadomo przy jakich parametrach ale prawdopodobnie poniższych) 120st C/ min
Zwiększanie prędkości chłodzenia poprzez zwiększenie ciśnienia z 6 do 12 - 15 atmosfer (610 x610 x 915 mm)-komora , zmiana silnika dmuchawy obiegowej chłodzenia z 135 do 160 kW
Czyli oprócz chorych mocy grzałek mamy chore moce silnika dmuchawy zapewniającej obieg gazu chłodzącego.
W artykule o piecu RVFOQ-224 razi mnie posługiwanie się przez trzech magistrów inżynierów określeniem błąd pomiaru, bardziej by mi pasowało określenie dokładność pomiaru.
Czyli szkic pieca do amatorskiej obróbki byłby taki: izolacja termiczna z włókien ceramicznych, grzałki na całej powierzchni wewnętrznej pieca, pompa próżniowa rotacyjna bez dyfuzyjnej, azot 5.0, prowadzenie procesu w zmniejszonym ciśnieniu a nie w wysokiej próżni - próżnia do łatwiejszego przepłukania azotem - chłodzenie przy ciśnieniu atmosferycznym w kąpieli olejowej o regulowanej temperaturze. Pomiar temperatury "pieca" oraz 2 sondy do wkładania w hartowane przedmioty lub "manekiny" o podobnych parametrach.
Chyba brzmi realnie.
To teraz pytanie o austenityzowanie i podgrzewanie wstępne.
Mamy np. stal NC6 przedmiot fi 55mm podgrzewanie wstępne w 550st C przez 1,7min.mm czyli 93 minuty, temperatura austenityzacji 820 st.C ale temperatura pieca o 10 st. C większa czyli 830st. C czas grzania 1,2min/mm czyli 66 min i teraz doliczyć 20 minut na austenityzację? Do oleju. Jeśli używam jednego pieca to czas nagrzewania powinienem chyba liczyć od osiągnięcia przez piec 830 st.C czyli jeszcze ok 10 do 15 minut więcej?
Hartowałem wczoraj gwintownik M55x2 z NC6 i zrobiłem tak 550 ok 90 min 830 66 min + 10 minut i do oleju, zabezpieczenie przed odwęgleniem pasta boraks z wodą owinięte drutem wiązałkowym żeby nie odpadło - i nawet było ok - w niektórych miejscach są plamy to chyba odwęglenie. Odpuszczanie 200 st. 4-5 godzin. Czasy podgrzewania z "Małego poradnika hartownika" Narzędzie już swoje zadanie wykonało - kalibracja gwintu odkształconego po spawaniu przez klienta gwintowanej tulei do blachy.
Ewentualnie mogę wywiercić w takim elemencie otwór i mierzyć temperaturę rdzenia i rozumiem że liczę 20 minut od momentu osiągnięcia 820 sto. C - NC6
Tak opieram się na źródłach głównie internetowych bo nie mam innych pod rękom. Znalazłem skan Małego poradnika hartownika trochę poczytałem. Macie może do zaproponowania jakąś literaturę papierową?
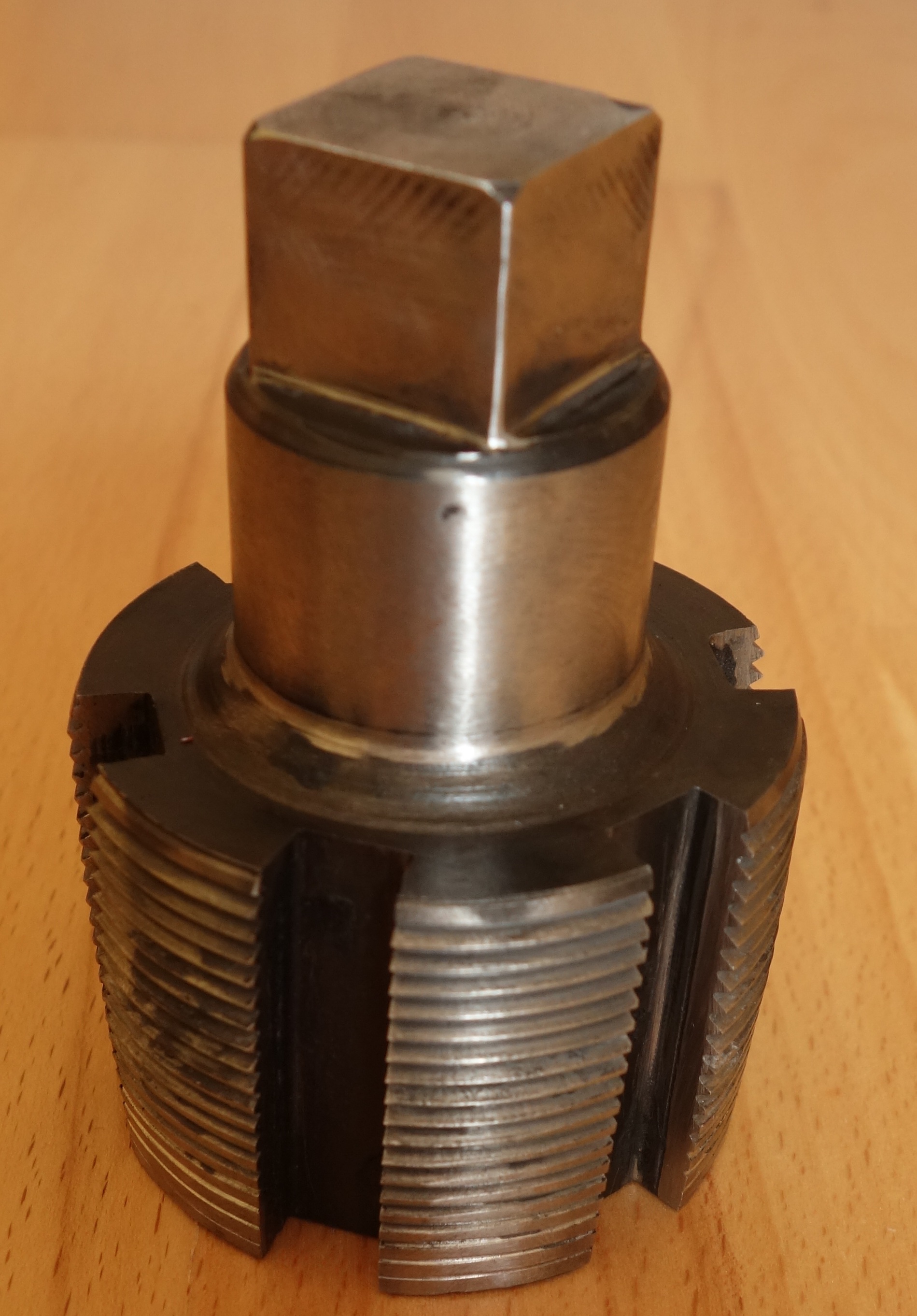
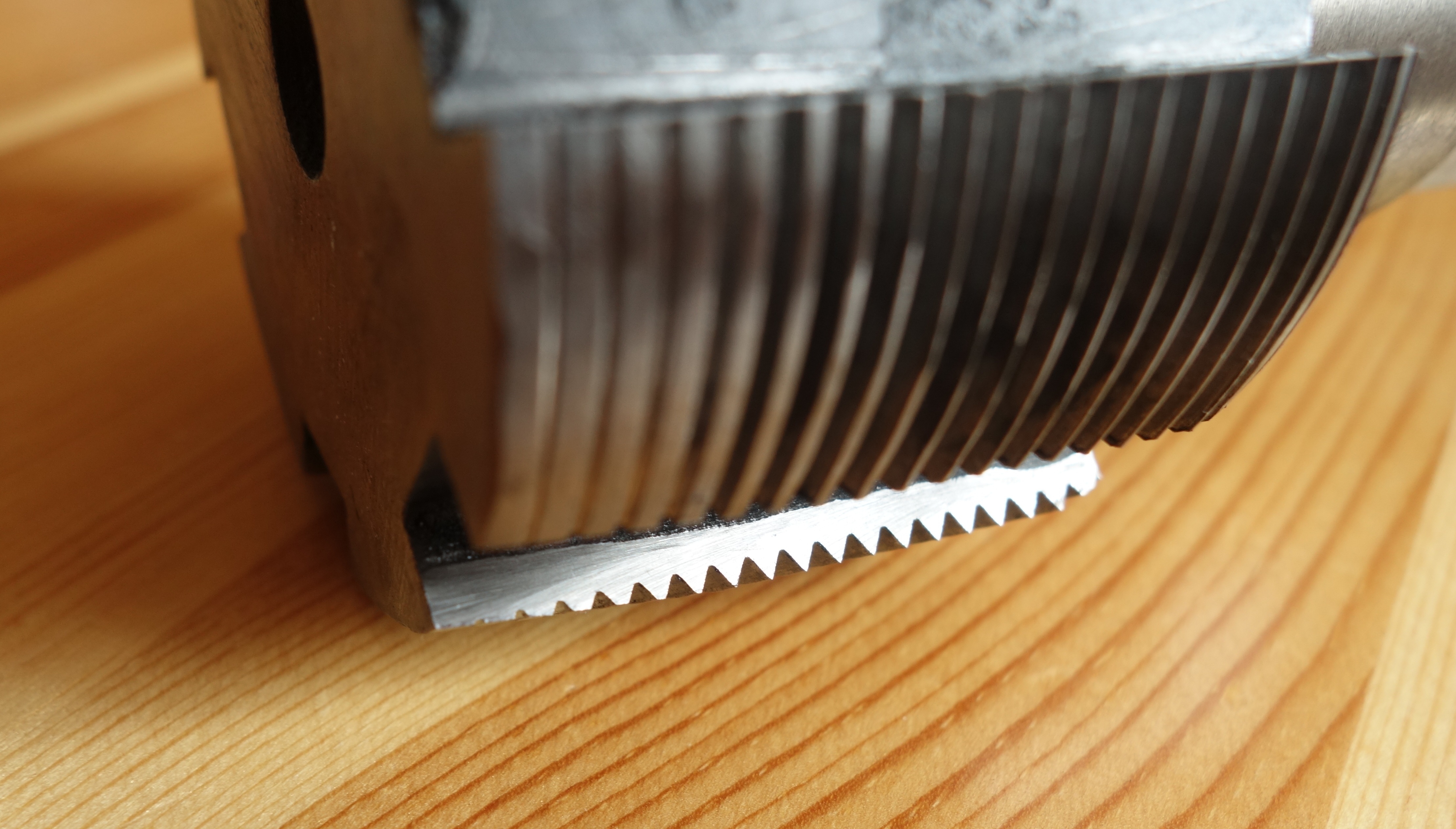
Z wykresu poniżej widzę że musimy zejść z temperatury austenityzowania poniżej 550st C w najwyżej 48 sekund.
Potem dalej chłodzimy ale to już nie jest tak krytyczne chodzi o ominięcie obszaru P bo na to jest mało czasu na ominięcie obszaru B jest już sporo czasu. Nie wiedziałem że tak można z tą perlityzacjąkolec7 pisze:Nie wiem, co chcesz uzyskać, więc nie umiem wypowiedzieć się na temat Twojej "receptury" w kontekście zamiarów.

Zimnych końców termopary nie trzyma się w 0 st.C tylko stosuje układy kompensacyjne są gotowe specjalizowane układy scalone i problem z głowy. Tylko ten układ musi się znajdować tam gdzie te zimne końce i mieć taką samą jak one temperaturę.
- jak go wykonać - to znaczy jak przygotować próbkę to wiem ale jakich odczynników użyć do trawienia i czego szukać po trawieniu? Co ciekawe we wszystkich materiałach jakie do tej pory widziałem jest tylko mowa o uzyskanej twardości i koniec. Przy tym modyfikowanym piecu aż się prosi aby klient zadowolony z uzyskanej twardości był też zadowolony z uzyskanej struktury ... no chyba że to mogłoby klienta troszkę zmartwić to dla bezpieczeństwa udajemy że tego nie ma?kolec7 pisze:obejrzeć zgład metalograficzny
Na podstawie wyników hartowania przedstawionych w artykule "Obróbka cieplna stali przeznaczonych na części maszyn i narzędzia do obróbki plastycznej w zmodernizowanym piecu próżniowym RVFOQ-224" wnioskuję że nie ma sensu bawić się w chłodzenie gazowe. Wystarczy "wsadzić" wannę z olejem do komory próżniowej (dodatkowej komory nie koniecznie próżniowej ale aby zachować ciągłość gazu ochronnego). Jakby to było takie proste

Mamy już konkretne dane z jednostkami na temat chłodzenia w gazie:
heat transfer coefficient α up to 800 [W/m2K])
prędkość chłodzenia (nie wiadomo przy jakich parametrach ale prawdopodobnie poniższych) 120st C/ min
Zwiększanie prędkości chłodzenia poprzez zwiększenie ciśnienia z 6 do 12 - 15 atmosfer (610 x610 x 915 mm)-komora , zmiana silnika dmuchawy obiegowej chłodzenia z 135 do 160 kW
Czyli oprócz chorych mocy grzałek mamy chore moce silnika dmuchawy zapewniającej obieg gazu chłodzącego.
W artykule o piecu RVFOQ-224 razi mnie posługiwanie się przez trzech magistrów inżynierów określeniem błąd pomiaru, bardziej by mi pasowało określenie dokładność pomiaru.
Czyli szkic pieca do amatorskiej obróbki byłby taki: izolacja termiczna z włókien ceramicznych, grzałki na całej powierzchni wewnętrznej pieca, pompa próżniowa rotacyjna bez dyfuzyjnej, azot 5.0, prowadzenie procesu w zmniejszonym ciśnieniu a nie w wysokiej próżni - próżnia do łatwiejszego przepłukania azotem - chłodzenie przy ciśnieniu atmosferycznym w kąpieli olejowej o regulowanej temperaturze. Pomiar temperatury "pieca" oraz 2 sondy do wkładania w hartowane przedmioty lub "manekiny" o podobnych parametrach.
Chyba brzmi realnie.
To teraz pytanie o austenityzowanie i podgrzewanie wstępne.
Mamy np. stal NC6 przedmiot fi 55mm podgrzewanie wstępne w 550st C przez 1,7min.mm czyli 93 minuty, temperatura austenityzacji 820 st.C ale temperatura pieca o 10 st. C większa czyli 830st. C czas grzania 1,2min/mm czyli 66 min i teraz doliczyć 20 minut na austenityzację? Do oleju. Jeśli używam jednego pieca to czas nagrzewania powinienem chyba liczyć od osiągnięcia przez piec 830 st.C czyli jeszcze ok 10 do 15 minut więcej?
Hartowałem wczoraj gwintownik M55x2 z NC6 i zrobiłem tak 550 ok 90 min 830 66 min + 10 minut i do oleju, zabezpieczenie przed odwęgleniem pasta boraks z wodą owinięte drutem wiązałkowym żeby nie odpadło - i nawet było ok - w niektórych miejscach są plamy to chyba odwęglenie. Odpuszczanie 200 st. 4-5 godzin. Czasy podgrzewania z "Małego poradnika hartownika" Narzędzie już swoje zadanie wykonało - kalibracja gwintu odkształconego po spawaniu przez klienta gwintowanej tulei do blachy.
Ewentualnie mogę wywiercić w takim elemencie otwór i mierzyć temperaturę rdzenia i rozumiem że liczę 20 minut od momentu osiągnięcia 820 sto. C - NC6
Tak opieram się na źródłach głównie internetowych bo nie mam innych pod rękom. Znalazłem skan Małego poradnika hartownika trochę poczytałem. Macie może do zaproponowania jakąś literaturę papierową?
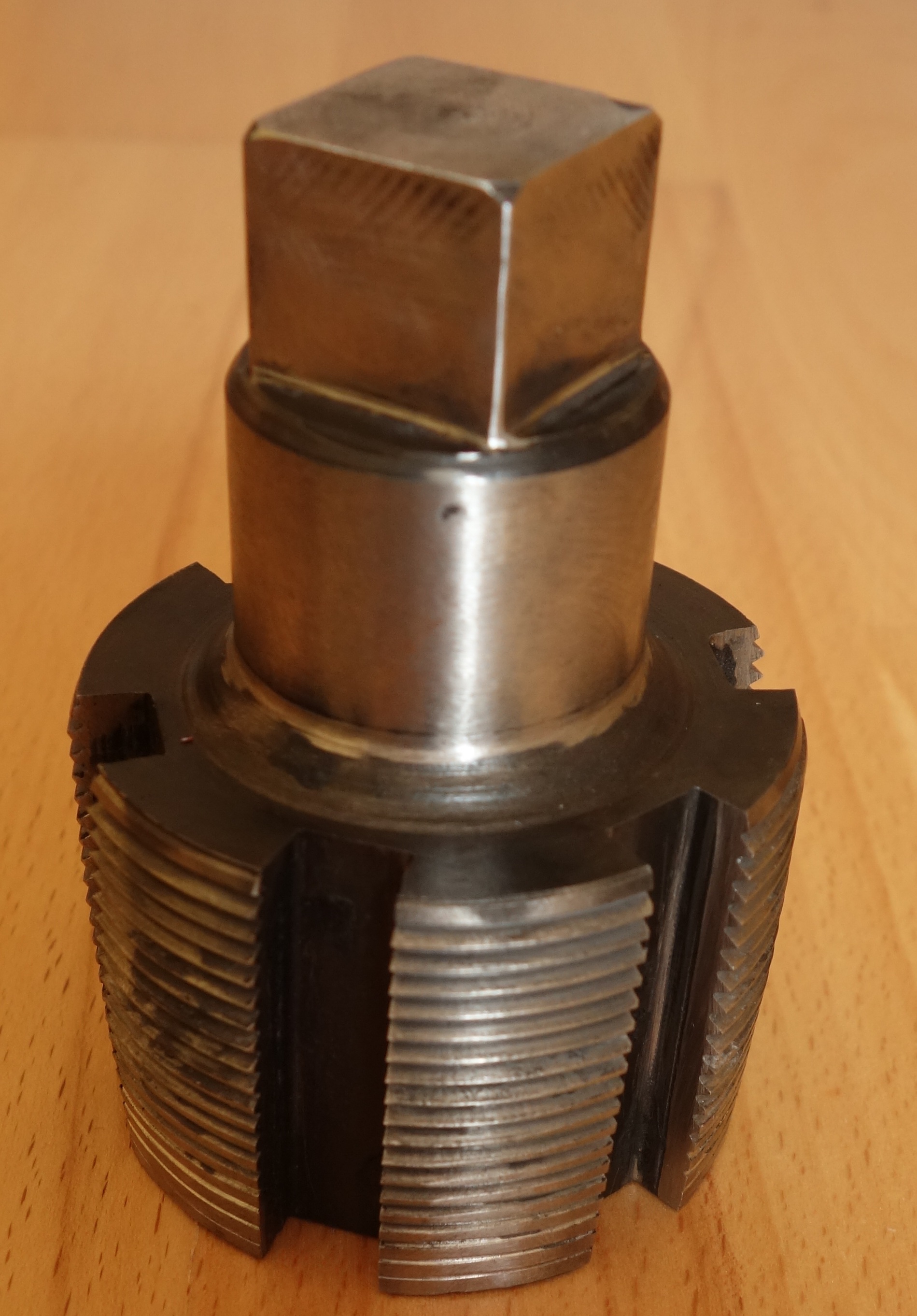
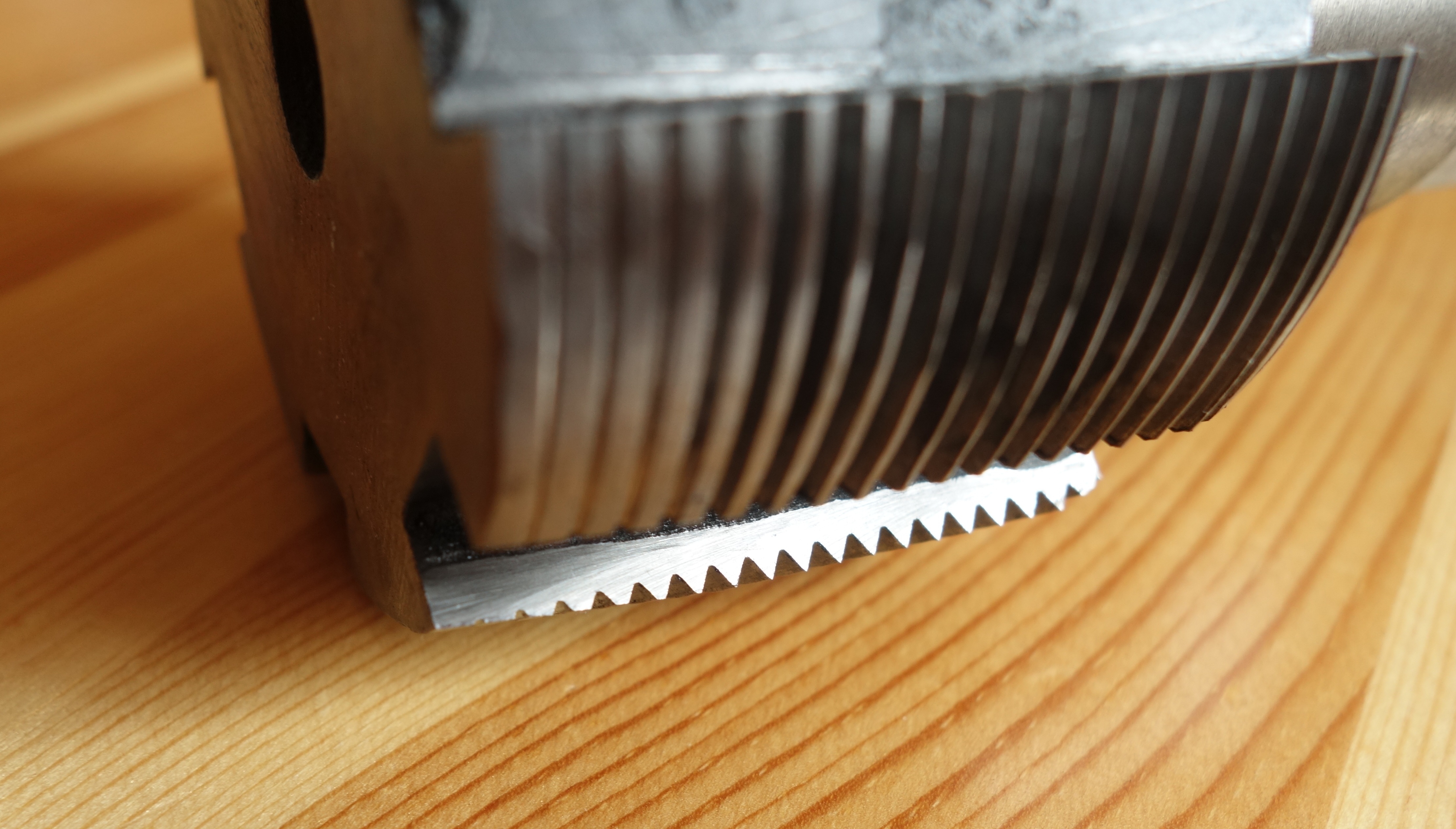
- 24 mar 2017, 18:52
- Forum: Spawalnictwo i obróbka cieplna
- Temat: Piec próżniowy budowa, hartowanie.
- Odpowiedzi: 12
- Odsłony: 4669
Żeby czytać wykres CTPc to muszę się podszkolić z tematu.
Z wykresu poniżej widzę że musimy zejść z temperatury austenityzowania poniżej 550st C w najwyżej 48 sekund.
Stal NMV - generalnie przeznaczona do hartowania w oleju.
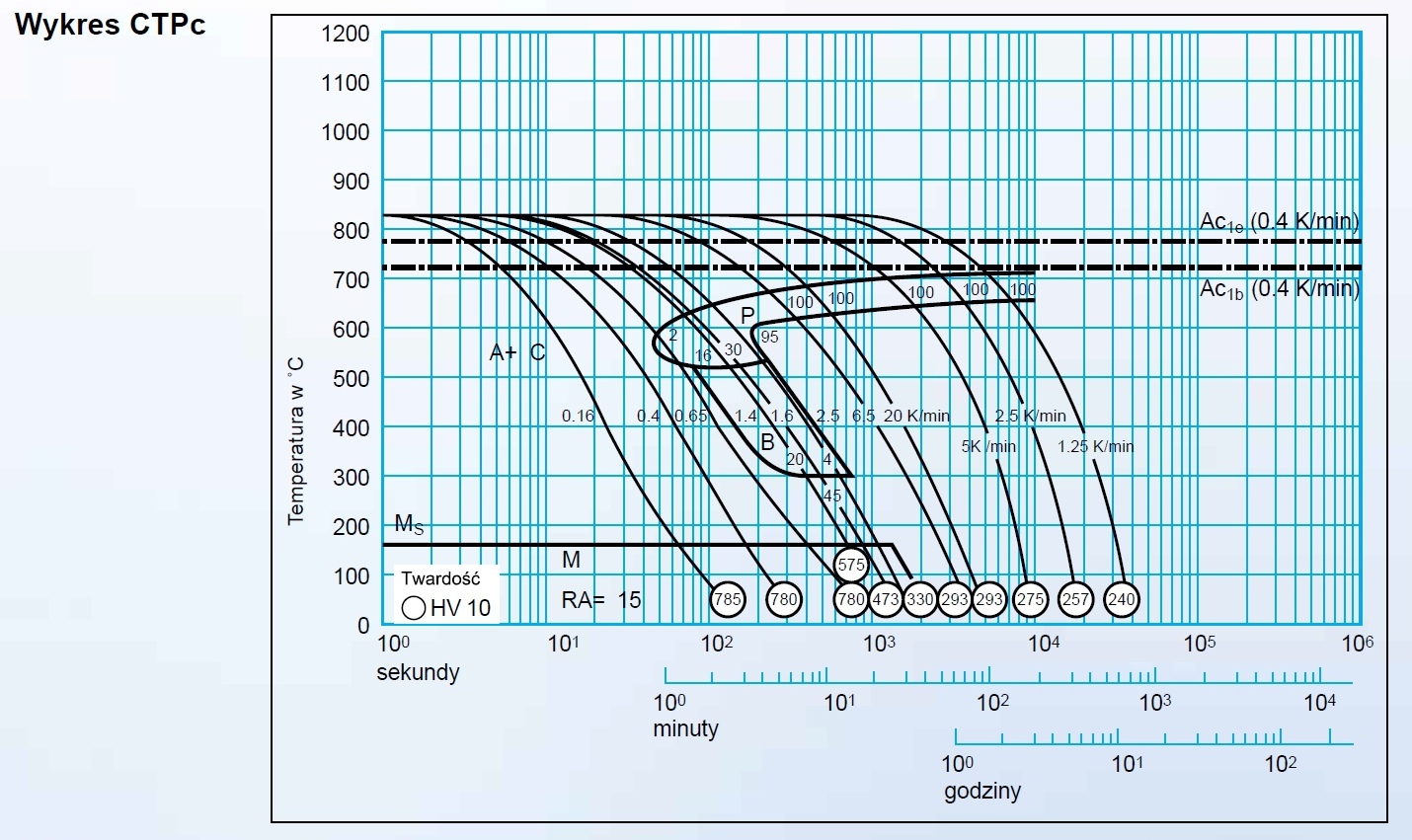
http://pbc.gda.pl/Content/4097/pbc_huci ... talozn.pdf
O chłodzeniu w nadciśnieniu danych które by zawierały jednostki nie znalazłem.
Ciekawe są informację jakie można znaleźć w internecie na temat pieców próżniowych. Są one jakby troszkę przesadnie gloryfikujące ich przydatność. Te obrazki z mojego poprzedniego posta też są "fajne" Ty zauważyłeś że jakby niedocenianą złoży fluidalnych ja widzę że nie pokazano rozkładu temperatury tego pręta chłodzonego gazem po jego stronie zawietrznej a będzie inny niż dla strony nawietrznej ale po co tym martwić widzów.
W sumie nie powinno to dziwić firmy wymyśliły technologie i chcą ją sprzedawać. Dla typowych zastosowań gdzie to ma ręce i nogi sprzedali to próbują wciskać w innych polach. Podają więc dane stawiające takie piece w dobrym świetle.
Już jakiś czas temu zauważyłem pewien problem z piecami próżniowymi. Z przyczyn podstawowych czyli sposobu nagrzewanie nie da się uzyskać detali o takich samych parametrach a później te detale leżą w jednym pudełku na półce i udają że są takie same.
Jak mamy całą komorę gwintowników to te ze środka nawet nie widzą grzałki (chyba że się mylę) no to jak one mają się nagrzać a no od sąsiadów jak się oni nagrzeją. Siedzi taki gwintownik w piecu patrzy na około gdzie jest grzałka nie widzę grzałki ojejku jak ja się nagrzeje dajcie mi trochę ciepła koledzy. Przy chłodzeniu podobnie.
Jakaś norma jest na to że ma być rozkład mniejszy niż +/- 5 st. C - ktoś to skomentuje?
No to dla którego detalu włączyć ten stoper czasu austenityzacji? Tego ze środka czy tego z zewnątrz?
Ja się akurat zapotrzebowaniem na moc przejmuje bo ma słabe przyłącze - 16kW więc nie poszaleje (nawet spawarki dobrze nie przehulam bo ma możliwość pobrać ok 24 kW). Według tego artykułu o stratach ciepła wychodzi mi komora sześcian 20cm licząc jeszcze izolację to zostaje sześcian 10 cm na 16 kW!!! Nie wiem jak oni liczą tą powierzchnie oddawania ciepła bo nijak mi nie wychodzi tyle co im z tych danych co podali.
Widzę że wiedza o hartowaniu jest jeszcze bardziej tajemna niż o spawaniu.
Z wykresu poniżej widzę że musimy zejść z temperatury austenityzowania poniżej 550st C w najwyżej 48 sekund.
Stal NMV - generalnie przeznaczona do hartowania w oleju.
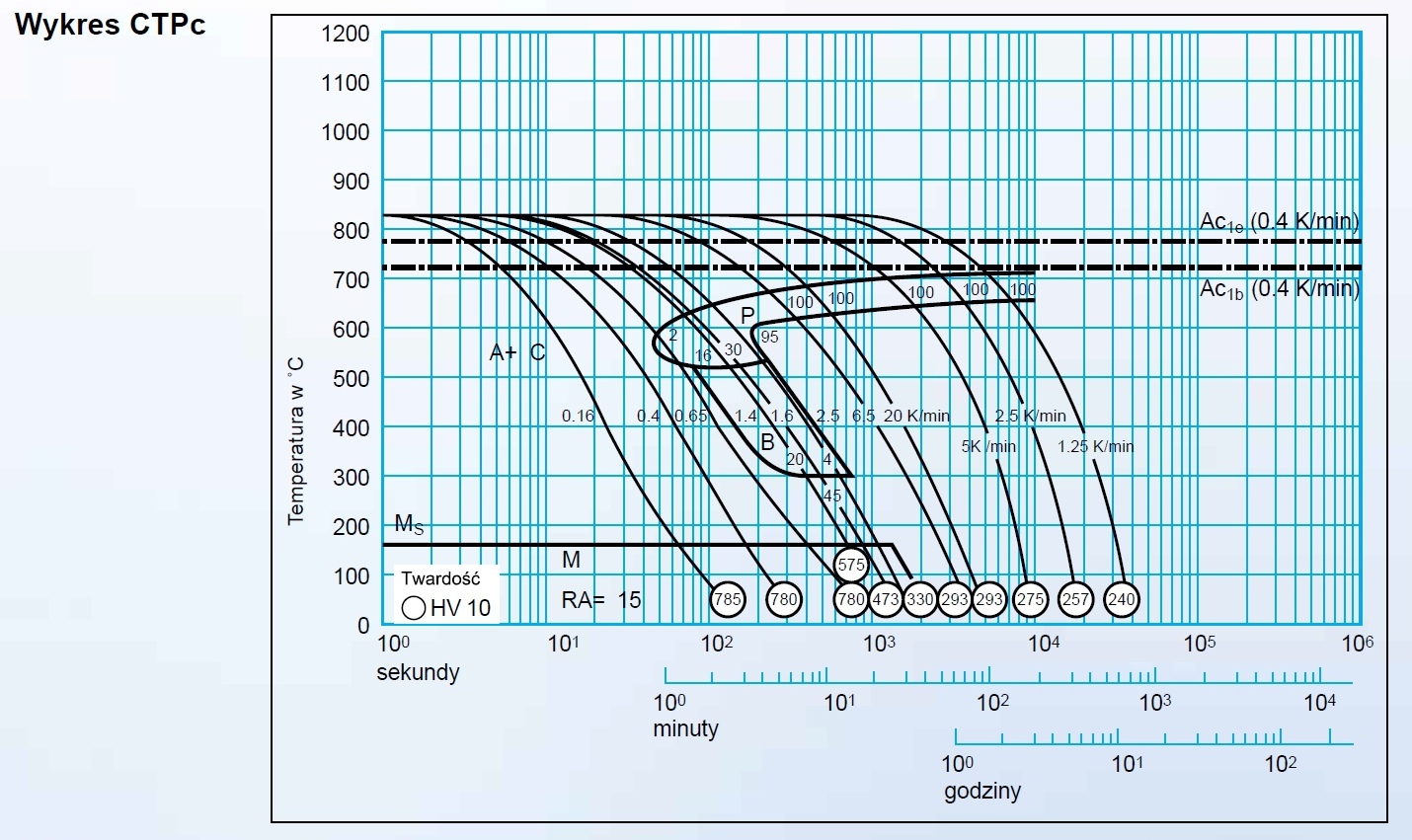
http://pbc.gda.pl/Content/4097/pbc_huci ... talozn.pdf
O chłodzeniu w nadciśnieniu danych które by zawierały jednostki nie znalazłem.
Ciekawe są informację jakie można znaleźć w internecie na temat pieców próżniowych. Są one jakby troszkę przesadnie gloryfikujące ich przydatność. Te obrazki z mojego poprzedniego posta też są "fajne" Ty zauważyłeś że jakby niedocenianą złoży fluidalnych ja widzę że nie pokazano rozkładu temperatury tego pręta chłodzonego gazem po jego stronie zawietrznej a będzie inny niż dla strony nawietrznej ale po co tym martwić widzów.
W sumie nie powinno to dziwić firmy wymyśliły technologie i chcą ją sprzedawać. Dla typowych zastosowań gdzie to ma ręce i nogi sprzedali to próbują wciskać w innych polach. Podają więc dane stawiające takie piece w dobrym świetle.
Już jakiś czas temu zauważyłem pewien problem z piecami próżniowymi. Z przyczyn podstawowych czyli sposobu nagrzewanie nie da się uzyskać detali o takich samych parametrach a później te detale leżą w jednym pudełku na półce i udają że są takie same.
Jak mamy całą komorę gwintowników to te ze środka nawet nie widzą grzałki (chyba że się mylę) no to jak one mają się nagrzać a no od sąsiadów jak się oni nagrzeją. Siedzi taki gwintownik w piecu patrzy na około gdzie jest grzałka nie widzę grzałki ojejku jak ja się nagrzeje dajcie mi trochę ciepła koledzy. Przy chłodzeniu podobnie.
Jakaś norma jest na to że ma być rozkład mniejszy niż +/- 5 st. C - ktoś to skomentuje?
No to dla którego detalu włączyć ten stoper czasu austenityzacji? Tego ze środka czy tego z zewnątrz?
Ja się akurat zapotrzebowaniem na moc przejmuje bo ma słabe przyłącze - 16kW więc nie poszaleje (nawet spawarki dobrze nie przehulam bo ma możliwość pobrać ok 24 kW). Według tego artykułu o stratach ciepła wychodzi mi komora sześcian 20cm licząc jeszcze izolację to zostaje sześcian 10 cm na 16 kW!!! Nie wiem jak oni liczą tą powierzchnie oddawania ciepła bo nijak mi nie wychodzi tyle co im z tych danych co podali.
Napisz coś o możliwości uzyskania różnych własności NC11LV w zależności od obróbki. Szukałem wykresu CTPc dla NC6 i nie znalazłem może masz gdzieś przypadkiem.kolec7 pisze:NC11LV jest dlatego ciekawą/fajną stalą narzędziową, ponieważ pozwala kreować własności mechaniczne wykonanego z niej detalu, właśnie poprzez sterowanie parametrami OC. Jest to gatunek, na który nie ma jednej właściwej receptury, tak jak jest to na przykład dla NC6. Dlatego uważam, że oddawanie do hartowni z poleceniem - chcę na 60HRC - to zmarnowanie tego utajonego potencjału.
Widzę że wiedza o hartowaniu jest jeszcze bardziej tajemna niż o spawaniu.
- 23 mar 2017, 11:00
- Forum: Spawalnictwo i obróbka cieplna
- Temat: Piec próżniowy budowa, hartowanie.
- Odpowiedzi: 12
- Odsłony: 4669
Piec próżniowy budowa, hartowanie.
Ponieważ temat w innym wątku zaczął się rozrastać dla porządku i większej przejrzystości zakładam nowy temat.
Tutaj jest porównania chłodzenia w różnych ośrodkach - link.
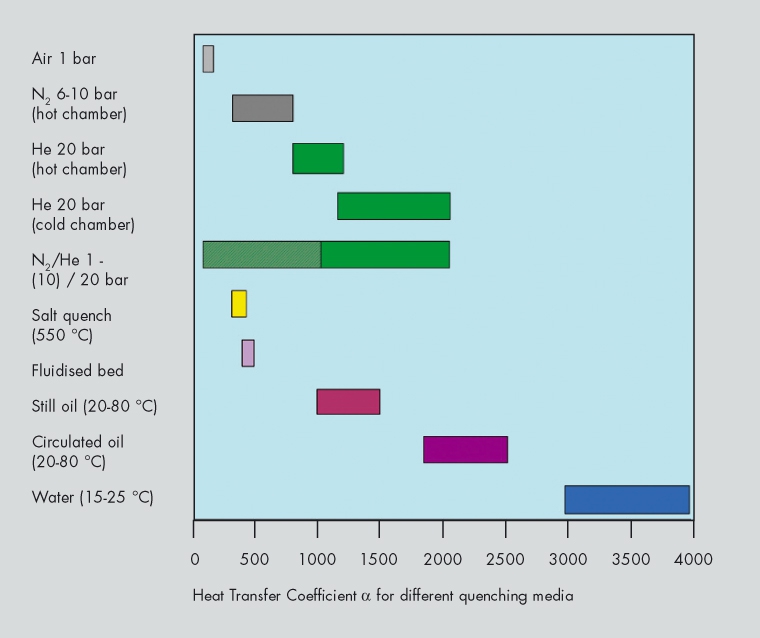
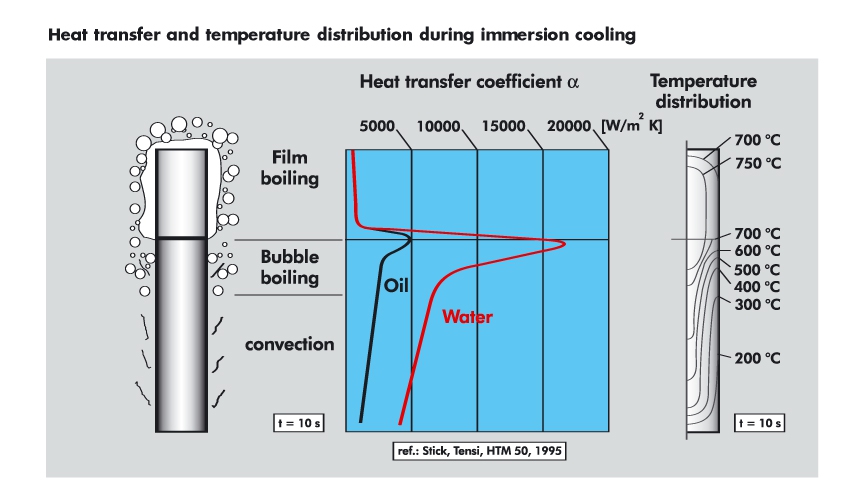
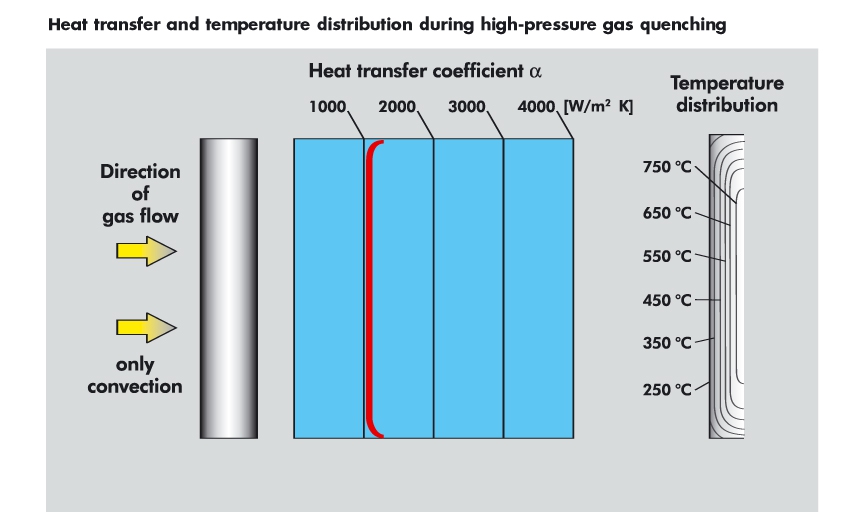
Widać na podstawie tych danych że prędkości chłodzenia powinny być porównywalne a i odkształcenia mniejsze.
O NC11LV się troszkę naczytałem, o jej prawie nierdzewności, o tym jak to właśnie trudno zepsuć bo twardość jest a inne parametry ... jakie parametry twardość jest się pan ciesz. Jak to się oszczędza na homogenizacji i kuciu, i jak w zasadzie ją zepsuć.
Teraz o budowie pieca przemysłowego to co znalazłem.
Po pobieżnym przeglądnięciu parametrów pieców próżniowych zobaczyłem że nawet te najmniejsze mają moc ok 70 kW!!! Pomyślałem sobie zaraz po co taka moc no rozumiem szybko nagrzać wsad ale tyle. Potem pojawia się pytanie no ok ale ja tu nie widzę żadnej izolacji tylko jakieś blachy "nierdzewne" to przecież to ciepło ucieka aż miło na zewnątrz nawet w póżni. Teraz jak jest grzany wsad ... tak samo jak obudowa pieca przez promieniowanie bo przecież mamy próżnie. Pomyślałem więc że w sumie to wsad jest grzany pewnie podobną mocą co straty pieca. Znalazłem ciekawy artykuł i wszystko się wyjaśniło.
Ta "nierdzewna" blacha to może być molibden, tantal lub wolfram i ostatnie warstwy są z blachy nierdzewnej.
Zacznę od początku.
Generalnie są trzy typy izolacji termicznej pieców
-metalowa izolacja czyli ekranowanie odbijanie ciepła z powrotem do wsadu -najmniej efektywna ale najczystsza i wytrzymała
-włókna ceramiczne - chłoną wodę i wydłużają czas pompowania (woda ma bardzo dużą objętość par) ale są najlepiej izolującym materiałem, stosowanym w niższych temperaturach i przy słabej próżni,
-filc grafitowy, płyty grafitowe, w miarę czysty i przyzwoicie izolujący, po wyłożeniu filcu płytą wystarczająco mocny do tego aby włączyć huraganowy wiatr azotu przy nadciśnieniu.
Artykuł omawia koszty związane ze stratami ciepła i rodzajem izolacji kosztami prądu i kosztami szczytowego zapotrzebowania na moc oraz kosztami w zależności od położenia w strefach cenowych prądu.
Tu przykład (str.5):
2000F (ok 1100st C) moc strat ciepła w zależności od materiału na izolację termiczną
2 cale filcu grafitowego -104 KW
1.5 cala filcu grafitowego - 139 KW
metalowa - 192 KW
C.D.N
Też nie miałem danych teraz mam czy są wiarygodne to inna sprawa.kolec7 pisze: Niestety nie posiadam wiarygodnych danych na temat chłodzenia azotem w warunkach nadciśnienia. Mogę jedynie domniemywać, że zabieg ten jest podyktowany zwiększeniem współczynnika przejmowania ciepła przez ogólnie słabo chłodzący ośrodek, aby - jak to nawet w przytoczonym przez Ciebie artykule napisano - zbliżyć się z parametrami, do charakterystyki chłodzenia oleju hartowniczego, kompandowanego, uszlachetnionego, emulsji wodno-olejowej, polimerów.........
Tutaj jest porównania chłodzenia w różnych ośrodkach - link.
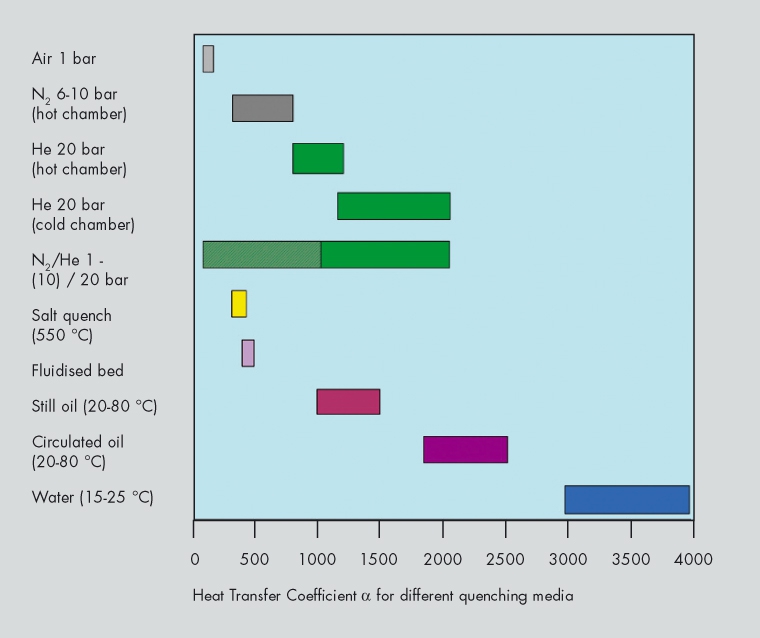
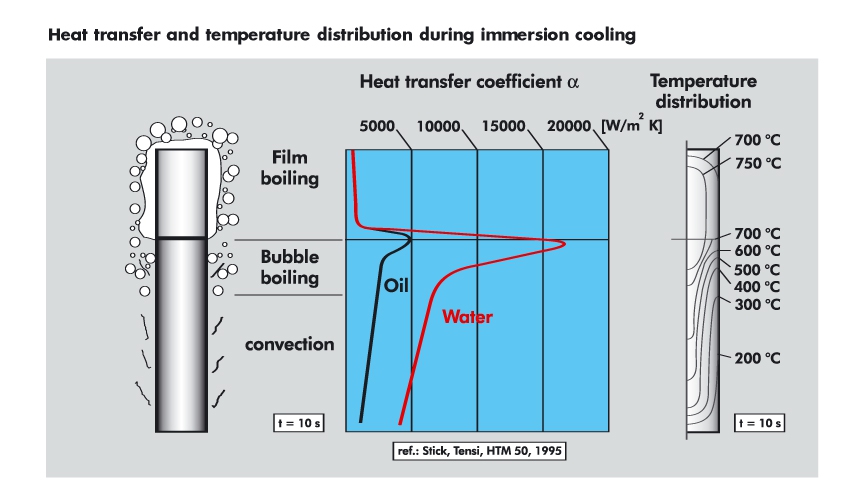
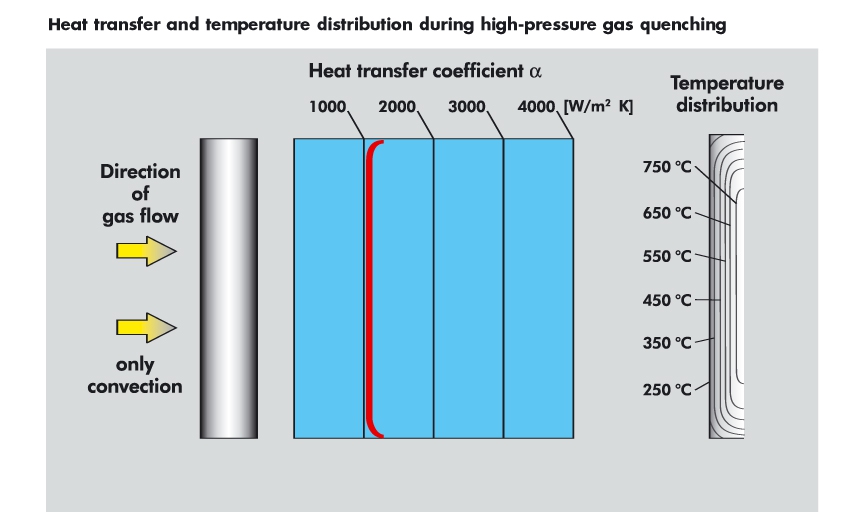
Widać na podstawie tych danych że prędkości chłodzenia powinny być porównywalne a i odkształcenia mniejsze.
O NC11LV się troszkę naczytałem, o jej prawie nierdzewności, o tym jak to właśnie trudno zepsuć bo twardość jest a inne parametry ... jakie parametry twardość jest się pan ciesz. Jak to się oszczędza na homogenizacji i kuciu, i jak w zasadzie ją zepsuć.
Teraz o budowie pieca przemysłowego to co znalazłem.
Po pobieżnym przeglądnięciu parametrów pieców próżniowych zobaczyłem że nawet te najmniejsze mają moc ok 70 kW!!! Pomyślałem sobie zaraz po co taka moc no rozumiem szybko nagrzać wsad ale tyle. Potem pojawia się pytanie no ok ale ja tu nie widzę żadnej izolacji tylko jakieś blachy "nierdzewne" to przecież to ciepło ucieka aż miło na zewnątrz nawet w póżni. Teraz jak jest grzany wsad ... tak samo jak obudowa pieca przez promieniowanie bo przecież mamy próżnie. Pomyślałem więc że w sumie to wsad jest grzany pewnie podobną mocą co straty pieca. Znalazłem ciekawy artykuł i wszystko się wyjaśniło.
Ta "nierdzewna" blacha to może być molibden, tantal lub wolfram i ostatnie warstwy są z blachy nierdzewnej.
Zacznę od początku.
Generalnie są trzy typy izolacji termicznej pieców
-metalowa izolacja czyli ekranowanie odbijanie ciepła z powrotem do wsadu -najmniej efektywna ale najczystsza i wytrzymała
-włókna ceramiczne - chłoną wodę i wydłużają czas pompowania (woda ma bardzo dużą objętość par) ale są najlepiej izolującym materiałem, stosowanym w niższych temperaturach i przy słabej próżni,
-filc grafitowy, płyty grafitowe, w miarę czysty i przyzwoicie izolujący, po wyłożeniu filcu płytą wystarczająco mocny do tego aby włączyć huraganowy wiatr azotu przy nadciśnieniu.
Artykuł omawia koszty związane ze stratami ciepła i rodzajem izolacji kosztami prądu i kosztami szczytowego zapotrzebowania na moc oraz kosztami w zależności od położenia w strefach cenowych prądu.
Tu przykład (str.5):
2000F (ok 1100st C) moc strat ciepła w zależności od materiału na izolację termiczną
2 cale filcu grafitowego -104 KW
1.5 cala filcu grafitowego - 139 KW
metalowa - 192 KW
C.D.N