Najpierw cele:
-maszyna ma się mieścić na warsztatowym granitowym blacie, i być przenośna siłami dwóch-trzech osób.
-ma pracować w drewnie, kompozytach drewna typu mdf, osb, hdf etc. i przede wszystkim musi nadawać się do frezowania 3d w różnych gatunkach aluminium.
-pole robocze musi mieścić kartkę A4 plus kilka cm na ewentualne mocowania detali. Oś Z 150mm posuwu.
-powtarzalność przy grawerce w alu musi zamknąć się w 0,05mm.
-ma być możliwie tania, ale musi nadawać się do dłuższych sesji pracy. Mam nadzieję że zarobi na siebie.
I teraz środki:
Posuw liniowy oparty chcę oprzeć na wynalazku zwanym MakerSlide.
http://makerslide.com/
http://store.makerslide.com/index.php?m ... ucts_id=50
I teraz pytania. Po pierwsze, czy to w ogóle ma sens przy planowanej eksploatacji maszyny? Zastosowałbym rolki stalowe, kupione mam nadzieję za mniej niż $10 za sztukę(każdy wózek wymaga minimum trzech), zaś same profile starałbym się wykończyć twardym anodowaniem(na razie nie udało mi się uzyskać ceny takiej usługi).
Ewentualnie samodzielnie toczone kółka z łożysk i 'oponą' z delrinu.
Wg. tego co policzyłem to wyjdzie mnie to zauważalnie taniej niż wiszące wałki o dużej średnicy. Nie wspominając o prostocie uzyskania prawidłowej geometrii prostopadłości osi(powierzchnie pod wałki podparte musiałbym mieć splanowane, co kosztuje krocie)
Dalej, napęd też chcę zrobić po głupiemu, nie śrubą, a paskiem zębatym. Ale żeby ograniczyć rozciągliwość paska, chcę w pewien sposób odwrócić montaż. Mianowicie podpatrzyłem tutaj ciekawy patent, jeden pasek jest przyklejony do maszyny, zębami do góry, tworząc listwę zębatą(na rysunku niebieski), i drugi jest położony zębami do dołu(czerwony), wpasowując się w listwę zębatą, dociskają go dwa kółka napinające dając nacisk w dół.
Przepraszam za jakość rysunku, ale 'oryginalny' z forum gdzieś zapodziałem.
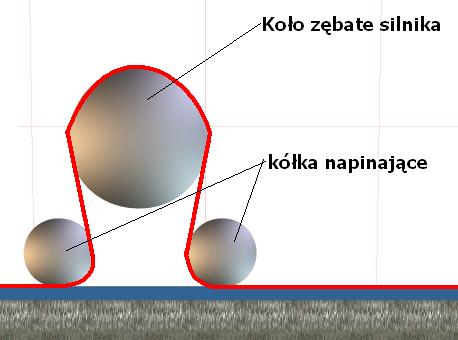
Dalej sama konstrukcja. Będzie to połączenie nietypowego materiału z klasyką, profile aluminiowe wzmacniane i podparte odlewem z polimerobetonu.
Planuję stałą bramę z osiami y z i ruchomy stół z osią x. Korpus stanowić będą dwa odlewy w kształcie odwróconej litery T, które będą tworzyć boki maszyny i kolumny bramy. Do zatopionej w odlewie płycie aluminiowej dokręcę profile(lub zwykłe płaskowniki i kątowniki) które zepną odlewy i połączą to w jedną sensowną całość.
Nie wiem czy w takiej konfiguracji maszyna odczuje najważniejszą zaletę polimerobetonu, czyli wytłumianie drgań, ale trudno.
To tyle koncepcji, jutro dodam wizualizacje maszyny.