Konstrukcja "Mini Lathe"
: 08 cze 2011, 14:01
Witam kolegów. Do skonstruowania własnej tokarki przymierzam się już dość długo. W tytule dałem "mini lathe" bo takie były wstępne plany. Pomalutku coś zaczyna powstawać.
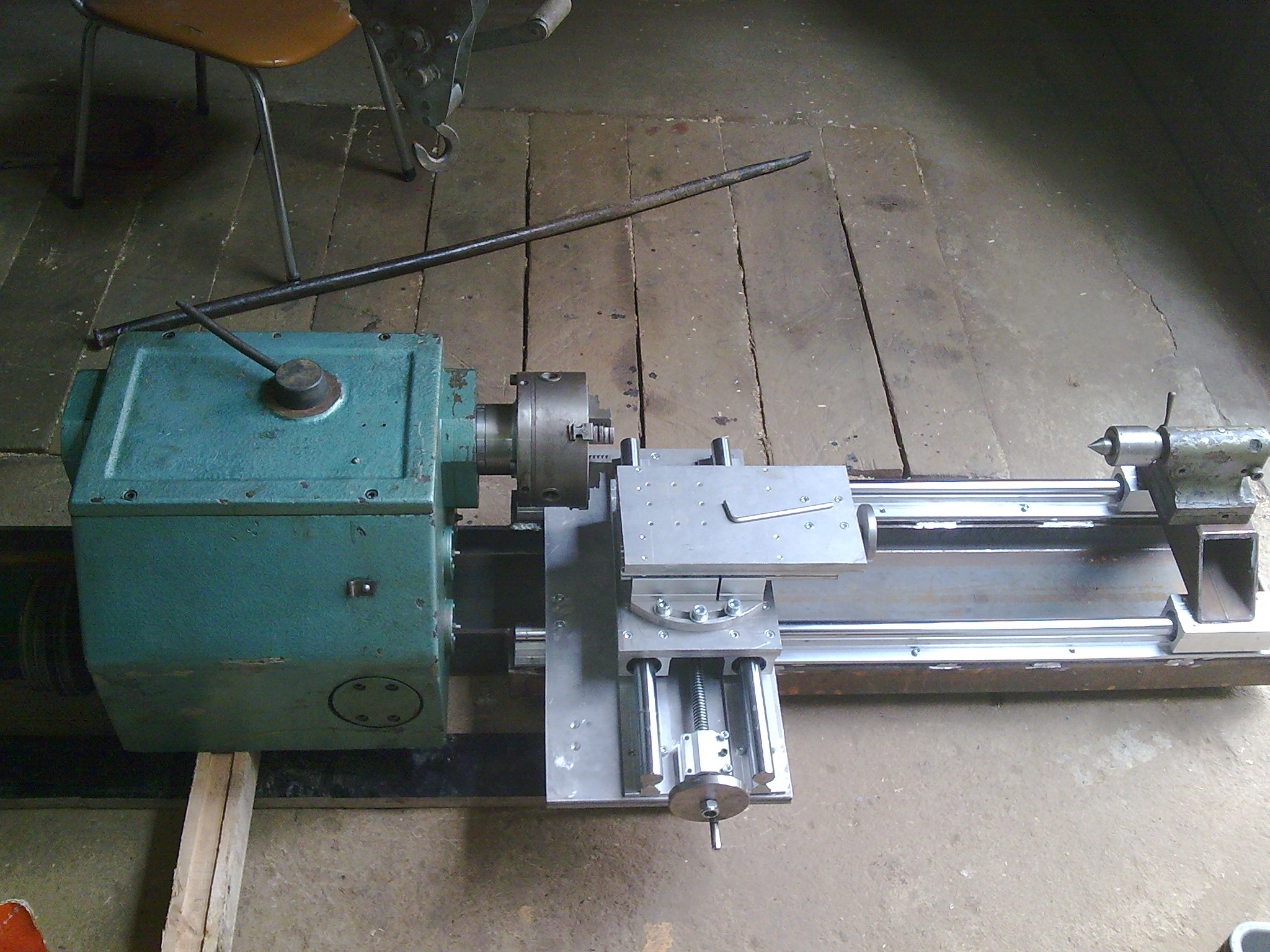
Podstawą jest dwuteownik 180 i dospawane po jego obu stronach profile zamknięte 60x60x4 oraz płaskownik, stanowi to podstawę (nagwintowaną) pod prowadnice.
Prowadnice to wałki fi-25 (podparte na całej długości) i łożyska otwarte w obudowach przedłużanych, czyli na każdą obudowę przypadają dwa łożyska (więcej w mojej galerii ).
Konik został "ustawiony" do zdjęcia
.
Jako wrzeciennik myślę wykorzystać górną część wytaczarki do bębnów. Wytaczarka pochodziła z "powodzi" więc była zalana, skorodowana i wymagała remontu, ale nic mnie nie kosztowała.
Wstępnie zakładałem, że napęd sań odbywać się będzie za pośrednictwem obrotowej nakrętki, czyli posuw ręczny bądź z małego silnika dla szybkich przejazdów.
Wspomniana wcześniej wytaczarka wyposażona jest w "skrzynkę posuwów" (dwa biegi i luz).
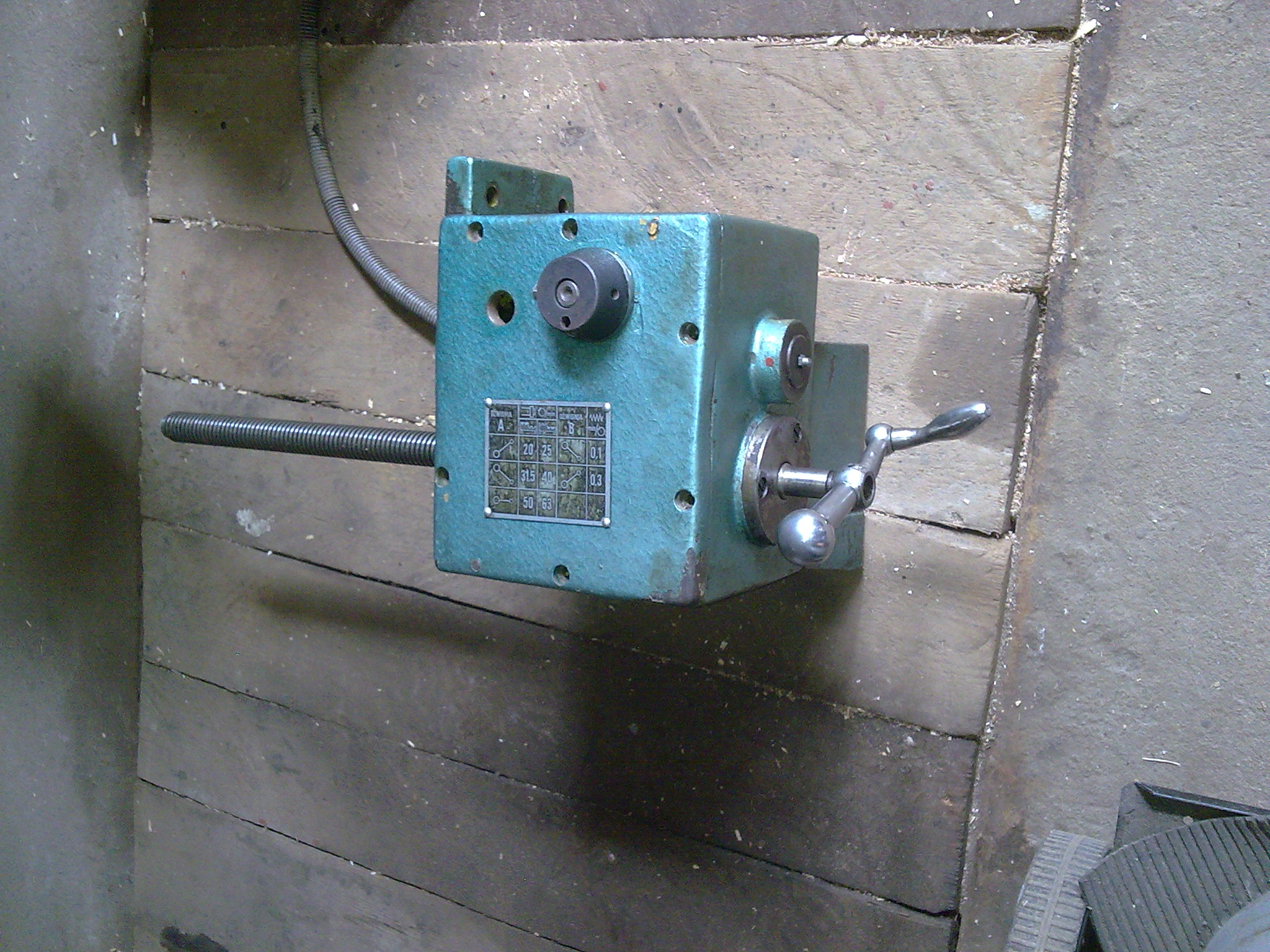
Więc chyba ją wykorzystam o ile nie będzie za wolna.
Zastanawiam się jeszcze nad faktem, że jako materiał do budowy wykorzystałem aluminium.
Czekam na sugestie i podpowiedzi doświadczonych konstruktorów.
Na pytania postaram się odpowiedzieć.
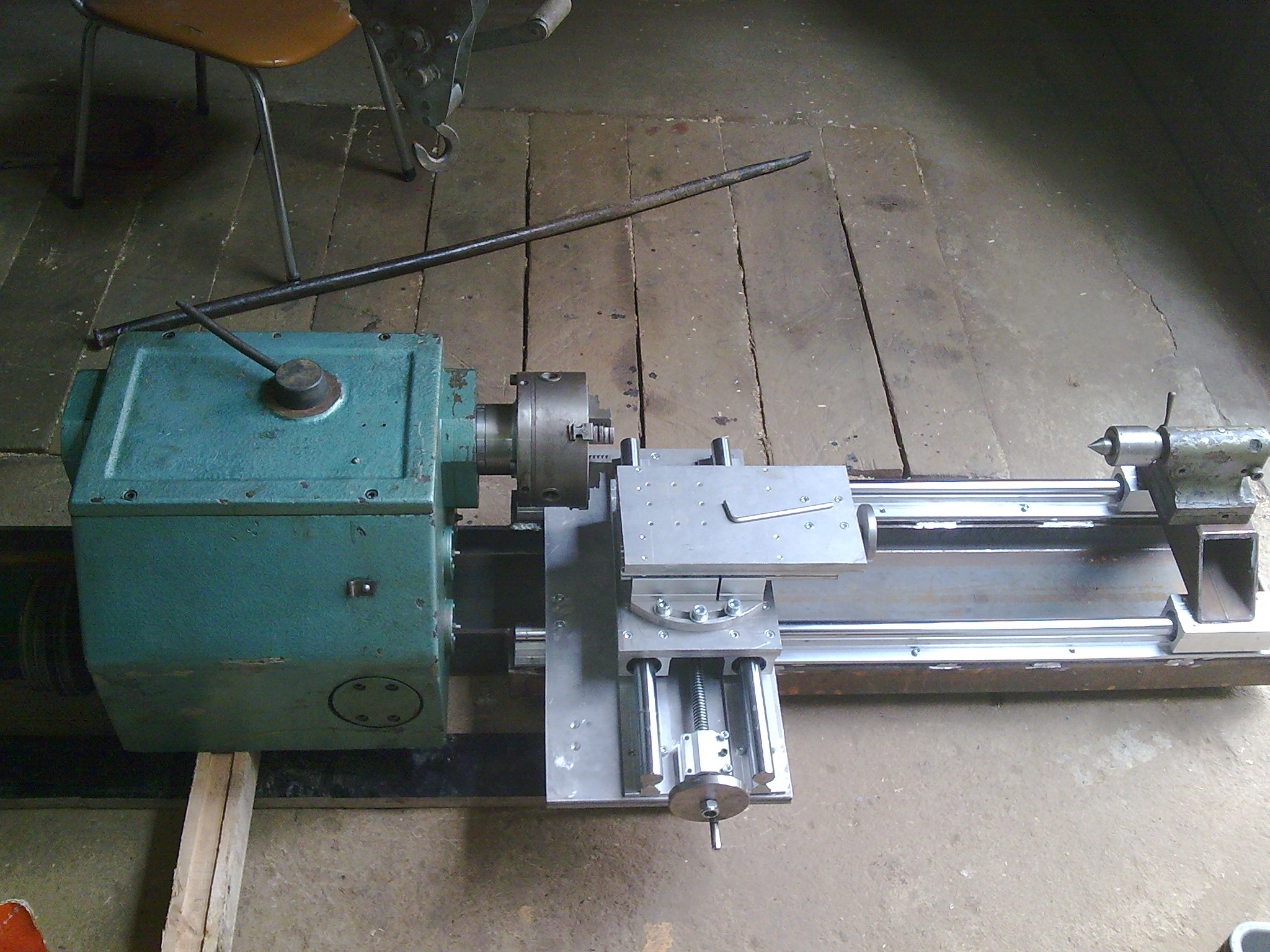
Podstawą jest dwuteownik 180 i dospawane po jego obu stronach profile zamknięte 60x60x4 oraz płaskownik, stanowi to podstawę (nagwintowaną) pod prowadnice.
Prowadnice to wałki fi-25 (podparte na całej długości) i łożyska otwarte w obudowach przedłużanych, czyli na każdą obudowę przypadają dwa łożyska (więcej w mojej galerii ).
Konik został "ustawiony" do zdjęcia

Jako wrzeciennik myślę wykorzystać górną część wytaczarki do bębnów. Wytaczarka pochodziła z "powodzi" więc była zalana, skorodowana i wymagała remontu, ale nic mnie nie kosztowała.
Wstępnie zakładałem, że napęd sań odbywać się będzie za pośrednictwem obrotowej nakrętki, czyli posuw ręczny bądź z małego silnika dla szybkich przejazdów.
Wspomniana wcześniej wytaczarka wyposażona jest w "skrzynkę posuwów" (dwa biegi i luz).
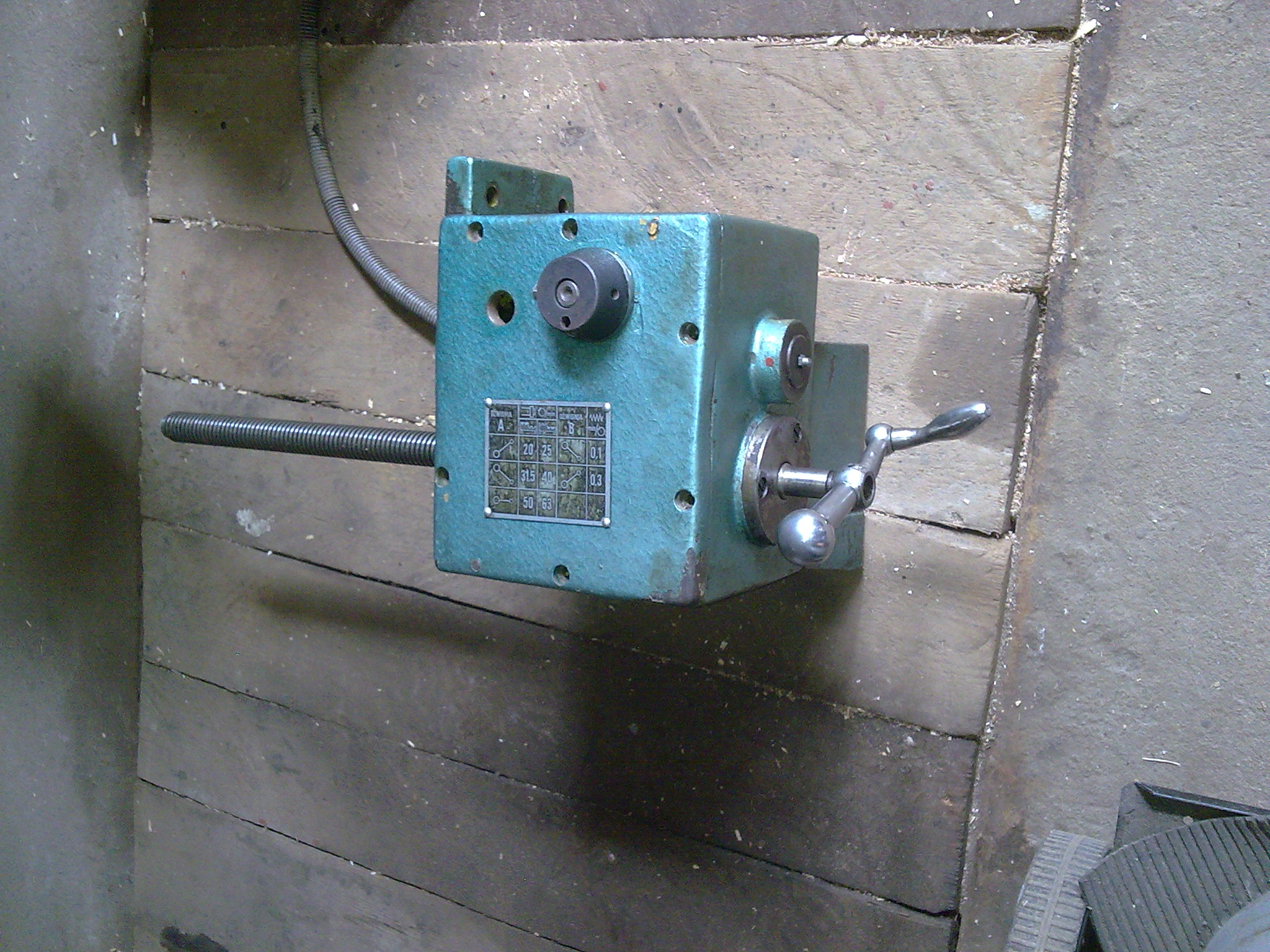
Więc chyba ją wykorzystam o ile nie będzie za wolna.
Zastanawiam się jeszcze nad faktem, że jako materiał do budowy wykorzystałem aluminium.
Czekam na sugestie i podpowiedzi doświadczonych konstruktorów.
Na pytania postaram się odpowiedzieć.