
Tytułem wstępu, jestem hobbysta amator który liznął trochę elektryki i mechaniki w ten czy inny sposób, 32 lata.
Historia zaczęła się tak...
Mam znajomego który robi fajne rzeczy z drewna, ręcznie [kopiarką ręczną] , tak kiedyś rozmawiamy sobie, i po stwierdzeniu, że się męczy robić 10x to samo, mówi - są fajne maszyny do tego. Ale wiesz, strasznie drogie, samemu nie zrobię bo to skomplikowane, kabelki to czarna magia, itp. Od słowa do słowa wyszło, ze zechciałem coś takiego zrobić... nie koniecznie dla niego i do produkcji, bardziej dla sprawdzenia czy/jak się da.
Było to ze 3 lata temu...
Poczytałem o CNC w internetach, trafiając min. na to forum - wielce pomocne się okazało

Pierwsza wersja planowana i zrobiona była na sterowniku po LPT, płytkach MB-02 z forumowego sklepiku, jakiś pierwszych z brzegu silniczkach krokowych z allegro, mechanicznie pręty gwintowane a posuw liniowy na kątownikach z przykręconymi do nich łożyskami... prowizorka straszna, ale co ciekawe, ruszało się po poskładaniu i wpisaniu kilku komend do macha

Fajnie, ale zdałoby się coś porządniejszego... tu zacząłem czytanie o ramach, śrubach, prowadnicach, sztywnościach, spawaniu, wyżarzaniu, i całej reszcie. Z braku budżetu na hobby na czytaniu się kończyło.
Kilka razy na allegro wypływały profile aluminiowe w okazyjnych cenach, padło na zbudowanie maszyny z tego - spawać mam czym i gdzie, obrobić i odprężyć - już nie. Równolegle liczyłem ile i jakich trzeba wałków podpartych, łożysk z oprawami, śrub trapezowych, nakrętek, itd. Kwota się zrobiła czterocyfrowa i to nie z jedynką z przodu... z braku budżetu temat stał w miejscu. Raz na kilka tygodni przeglądałem allegro pod kątem podzespołów.
Któregoś razu trafiłem na firmę na 'e' z '1' na końcu, która miała tyle dobra na stanie, że szczęka opadła. Śruby kulowe w cenie trapezówek z kompletem nakrętek, prowadnice używki w cenie wałków, itd, wiecie to co będę mówił. Budżet też jakiś się udało zorganizować bo akurat praca była...
To zrobiłem zakupy, profile grubsze cieńsze, wpusty, kątowniki, śrubki, śruby kulowe, prowadnice, itd. Plan był na pole robocze ~800x500x200 z ruchomą bramą.
Z braku czasu [praca była... dużo pracy :], dobra leżały na półce kilka miesięcy i czekały na lepsze czasy:
W międzyczasie silniki kupiłem, 6Nm, o takie:
http://www.ebay.com/itm/4Axis-Dual-Shaf ... 1372842847
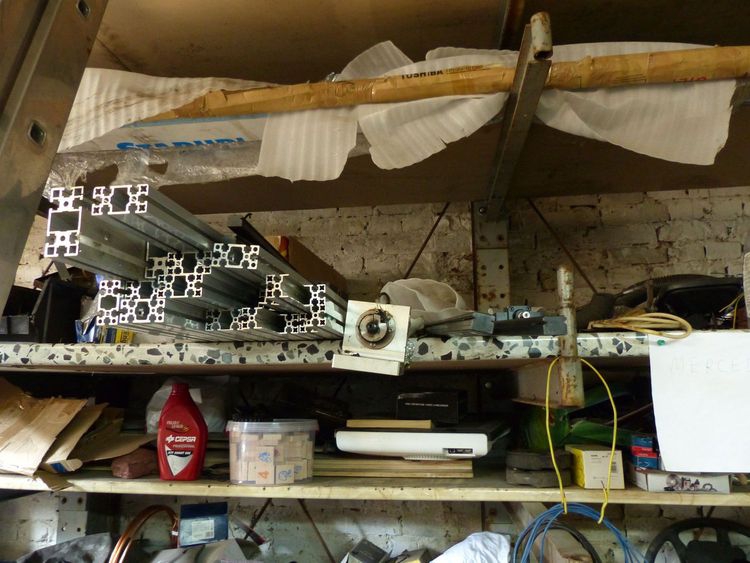
Ja tradycyjnie allegro raz kiedyś.
I ooo, sprzedający na e ma gotowe osie... używane, drogie, ale poskręcane na płycie, wszystko mające, z wyprowadzona równoległością i prostopadłością wszystkiego, zakołkowane tak że można rozłożyć i złożyć do kołków bez przyrządów... no cudo. Wykosztowałem się i kupiłem.
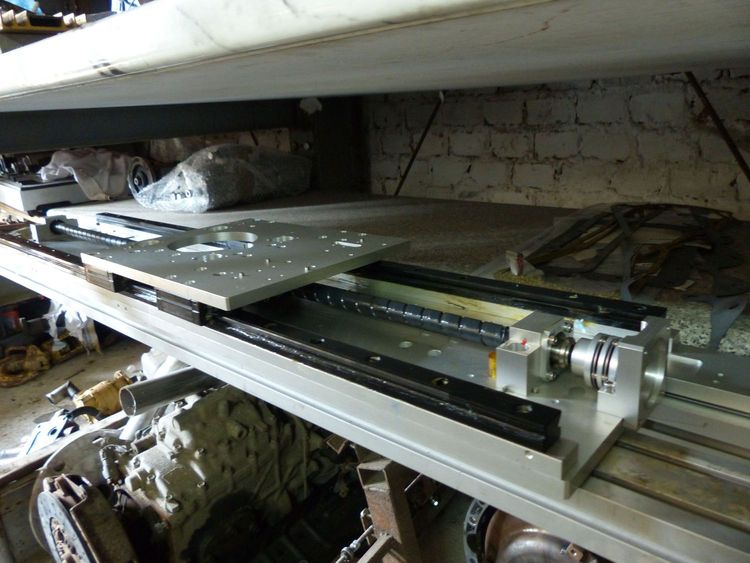
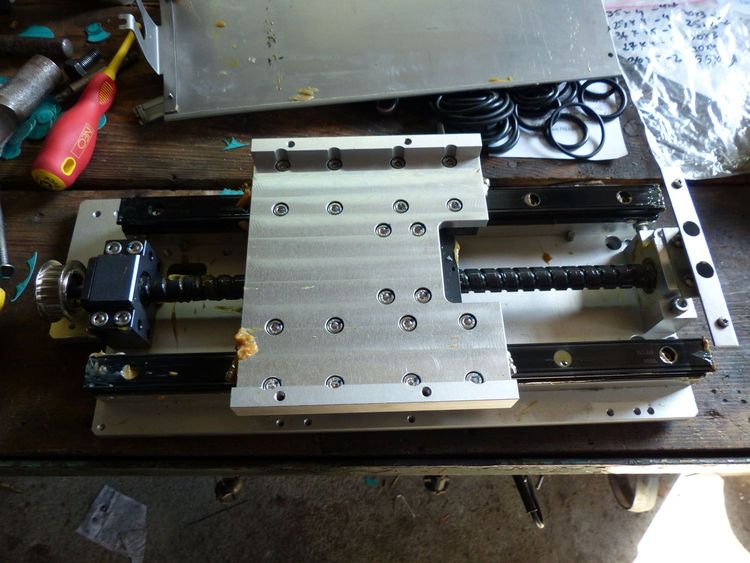
To było z rok temu. Praca dalej była, czasu nie było, wszystko leżało. Nie miałem też ogarniętej kwestii sterowania - zarówno wiedzy co z czym się je [doczytałem o wszystkim później], wybranych i kupionych sterowników, zasilaczy, komunikacji z PC [LPT czy Ethernet], itd. Wrzeciona też nie było, planowany chińczyk 2.2.
Któregoś dnia dzwoni znajomy z miejscowości gdzie była fabryka płyt meblowych.. która zbankrutowała i stała od kilku lat. I mówi, Grzesiek tną to wszystko to kontenerów... dzień później pojechałem, i faktycznie. Temat na inną historię, ale zdążyłem trochę dobra uratować przez hutą, niestety jak na złość budżetu nie było a dobra do wzięcia było mnóstwo... przytargałem min. taką ramę po 2/kg...
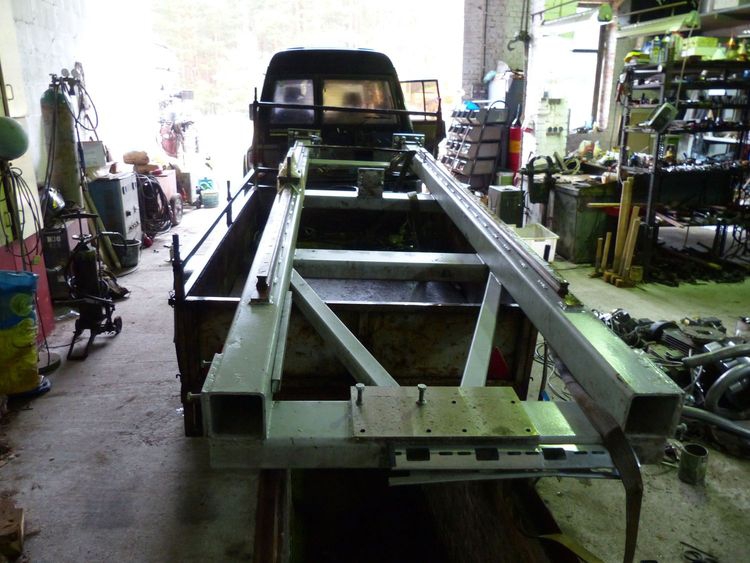
Niestety brak było jednego wózka [obłaziłem za nim wszystkie hale i nic], a prowadnice stara z nalotem rdzy - leżało to wszystko w warunkach w jakich się złom składuje

Prowadnice sprzedałem, miałem wcześniej kupione THK 30 z wózkami z wiadomej firmy, 2200 długie. Rama prawie 5 metrów... ze ślicznie wyprowadzonymi płaszczyznami pod prowadnice [nawet 4m długie by wlazły], śrubę też udało się zamontować [oryginalnie napęd na paskach zębatych].
Zmieniło mi to koncepcję z ruchomej bramy na ruchomy stolik... i nawet dobrze, prościej wykonać w amatorskich warunkach.
Zamontowałem śrubę, i przerwa przez zimę [praca + inne]
W międzyczasie kupiłem sterowniki 860, zasilacze 50V, 24V, CSMIO IP/M, chińczyka + falownik z ebaya, jakieś inne drobnostki.
Przez zimę planowałem i czytałem...
Całkiem nie dawno skończyła się praca i budżet, ale czasu jak i dobra nazbieranego było dużo i miałem do wyboru... czekać na resztę rzeczy [a sytuacja finansowa w firmie nie napawa optymizmem na przyszłość], albo składać prowizorycznie z tego co mam.
Padło na składankę... raz, że leżało na półce i korciło, dwa, że i tak potrzeba miesięcy jak nie lat żeby się nauczyć sprawnie posługiwać machem, i jakimś camem/cadem - o ile ogólnie komputery nie są mi obce, to akurat programy CAD, CAM i Mach3 to nowość. Tak samo jak ogólnie pojęta obróbka skrawaniem różnych materiałów - wcześniej to jedynie wierciłem na WS-16 i kątówką/pilnikiem szlifowałem, tyle ze skrawania

To zaczynamy, proszę brać poprawkę na to, że jest to w wielu kwestiach zamierzona prowizorka i druciarstwo i wiele rzeczy mam zamiar zmienić. Po zdjęciach opis co i jak.
Rama z tymczasowym stolikiem
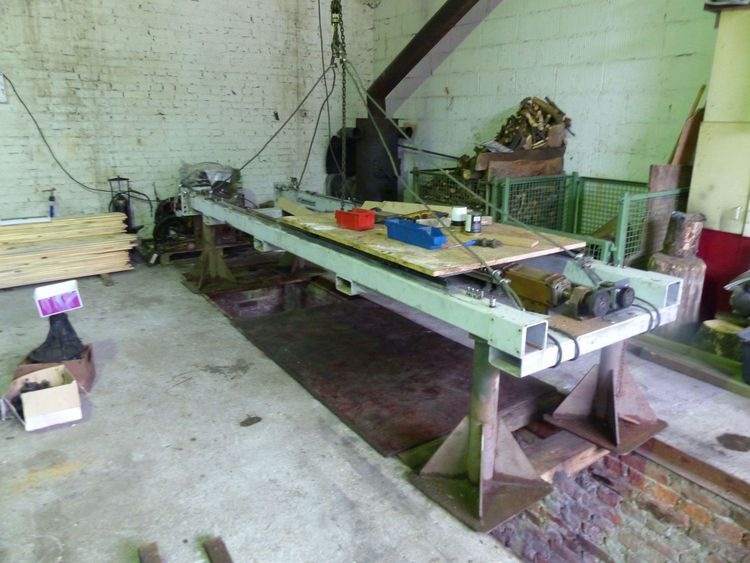
Osie
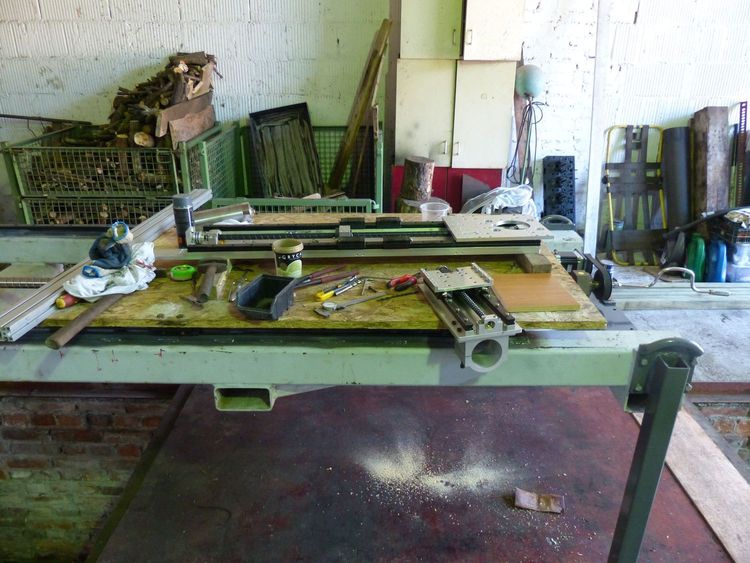
Oryginalna płyta osi X, po nawierceniu jej i płyty osi Z skręcone ze sobą:
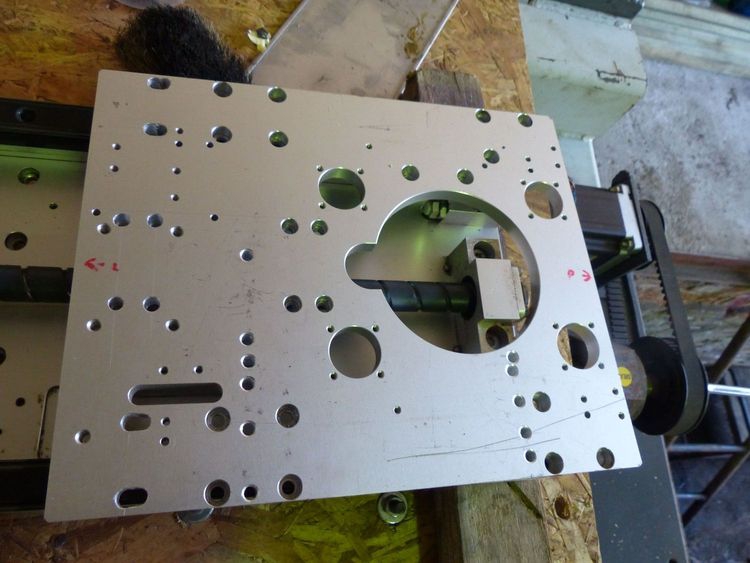
O tak:
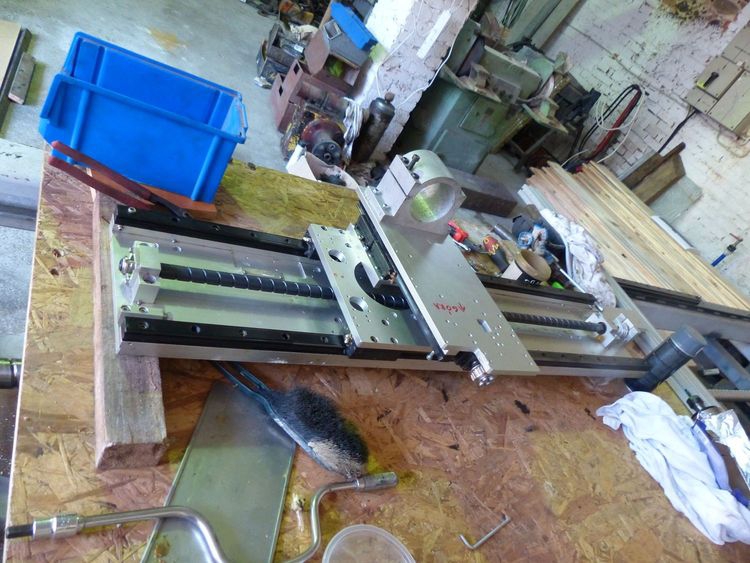
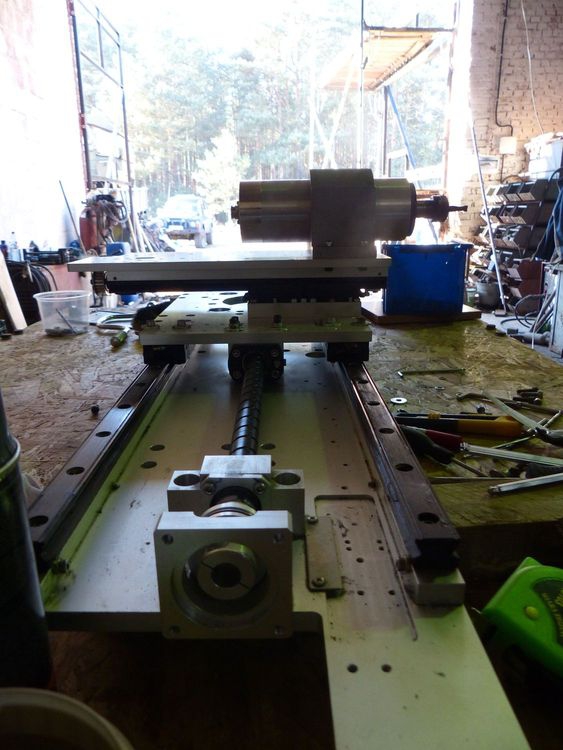
Konstrukcja bramy na razie z profili... żeby płytę z profilami skręcić trzeba wszystko ponawiercać, czyli rozkręcić oś w drobny mak... przy skręcaniu bardzo się przydały kołki ustalające.
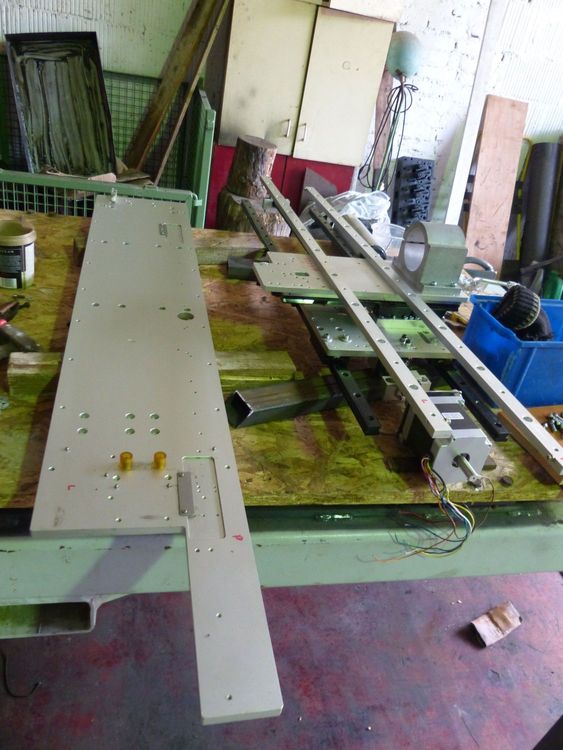
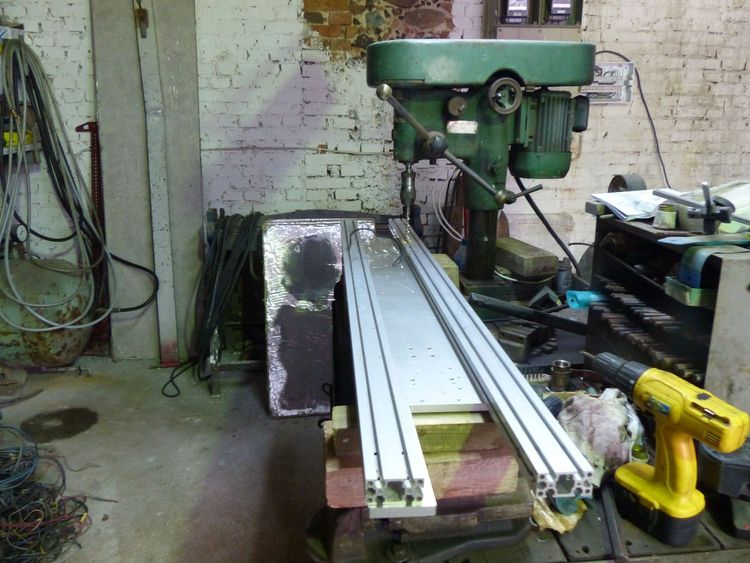
Jak już wszystko było powiercone zaczęło się skręcanie bramy i ustawianie jej równolegle... pierwsze przymiarki:
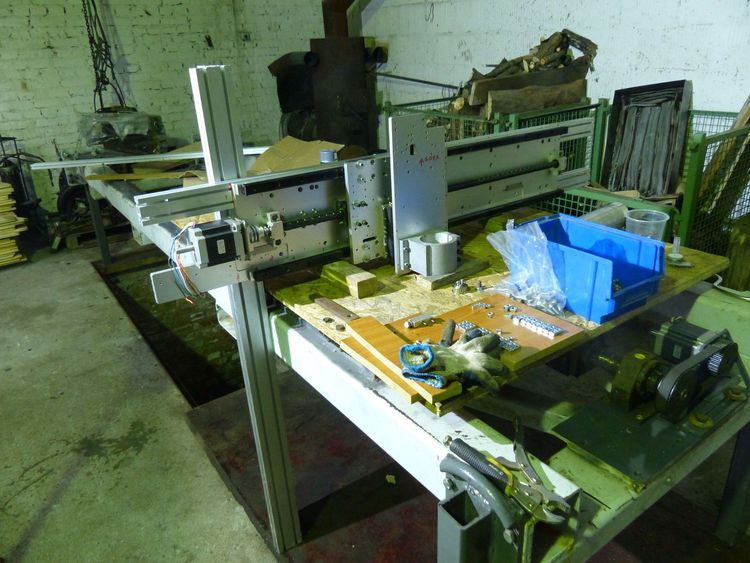
Kilka kilo śrubek poszło...
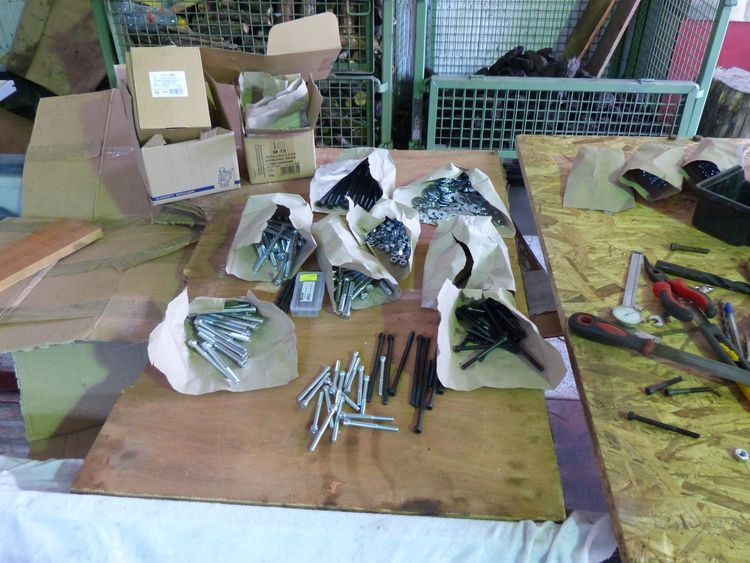
Nogi bramy, powzmacniane trochę kątownikami zwykłymi
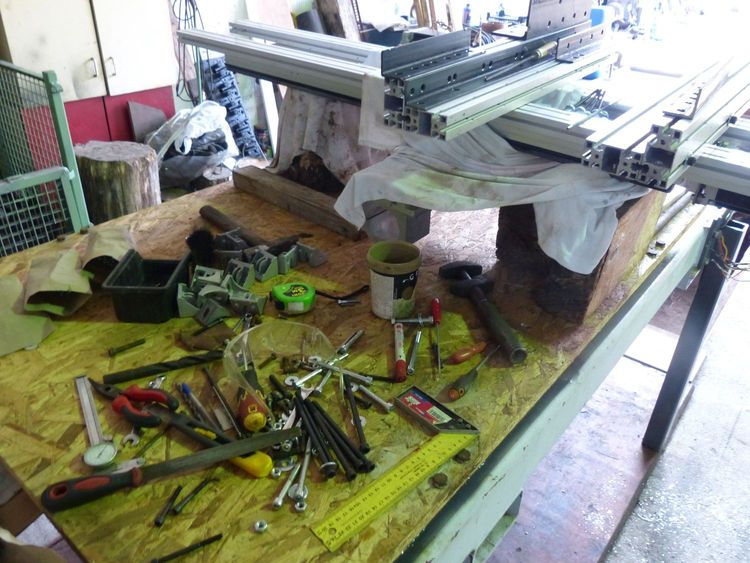
W tym momencie brama z osiami jest taka ciężka, że nie ma szans jej ręcznie podnieść, nie mówiąc o precyzyjnych przymiarkach
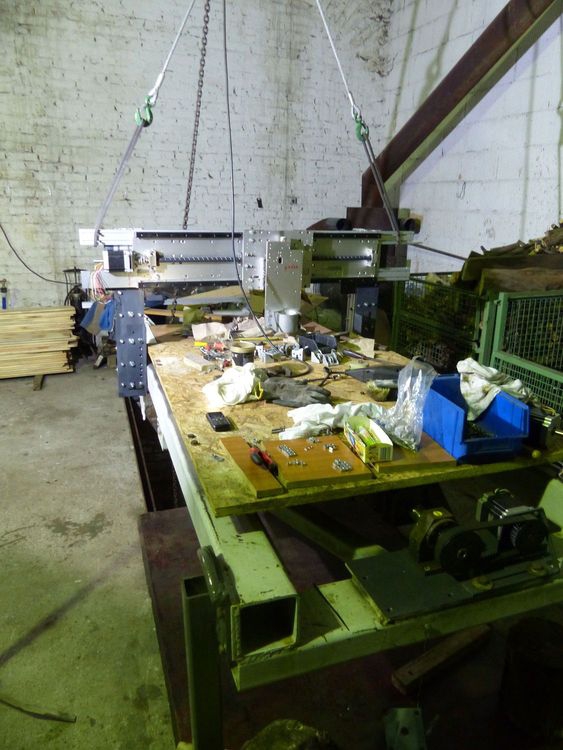
Po przykręceniu:
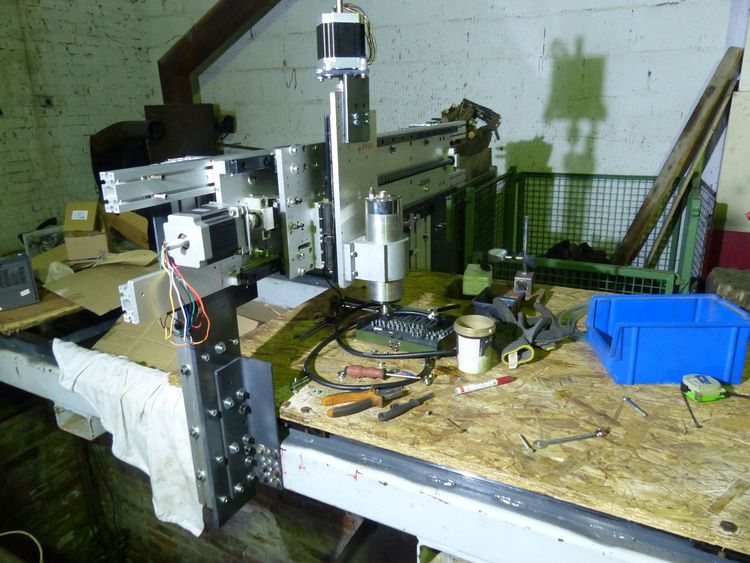
Napęd... z oczywiście prowizorką do mocowania silnika.
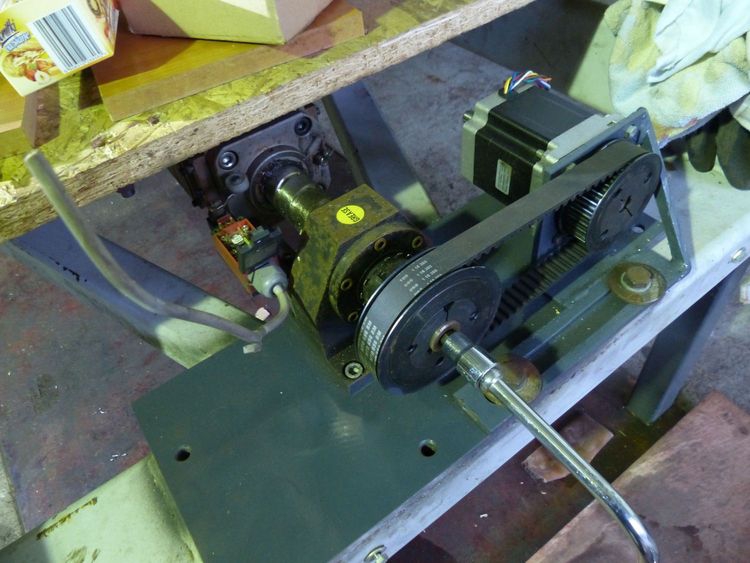
Chłodzenie z PC.
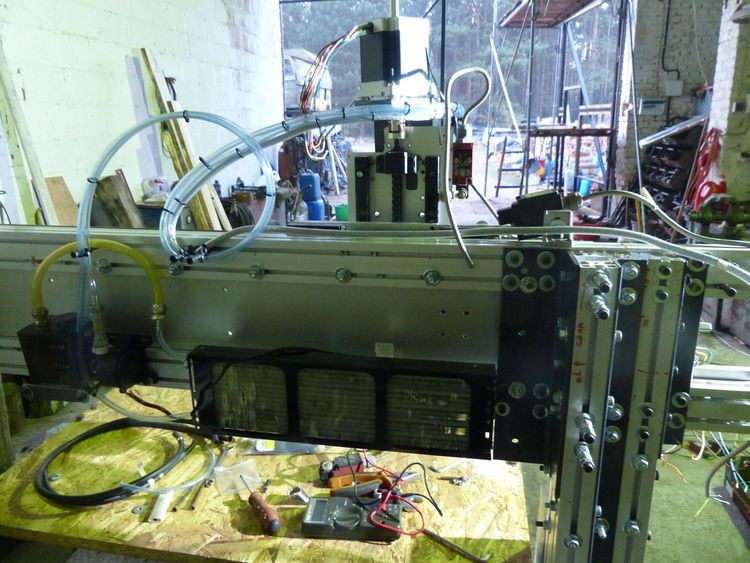
Tutaj uczę się czujników indukcyjnych
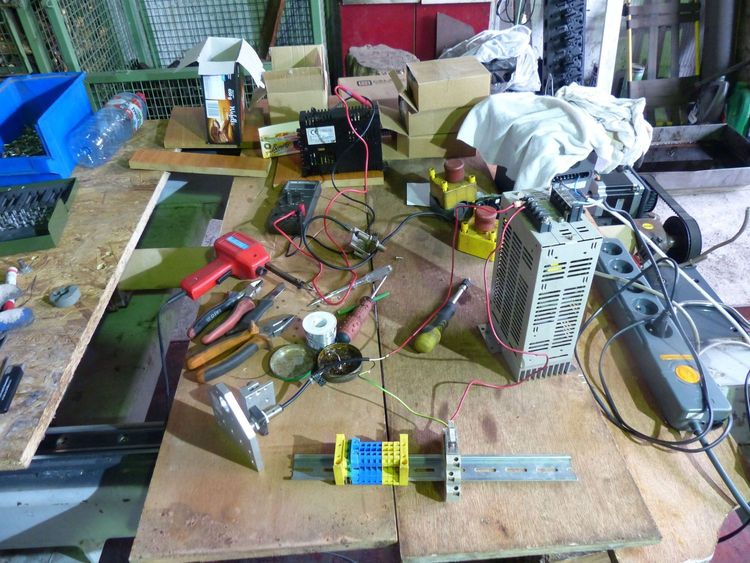
Po zamocowaniu na osiach
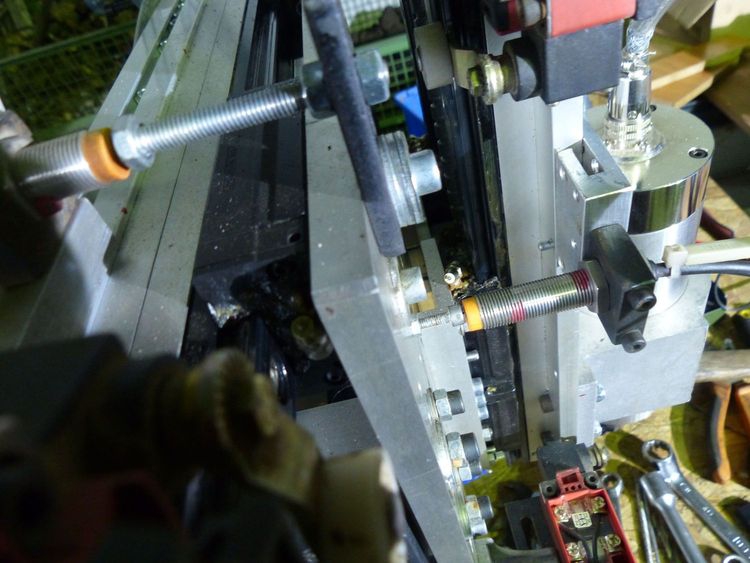
Przyszły przewody...
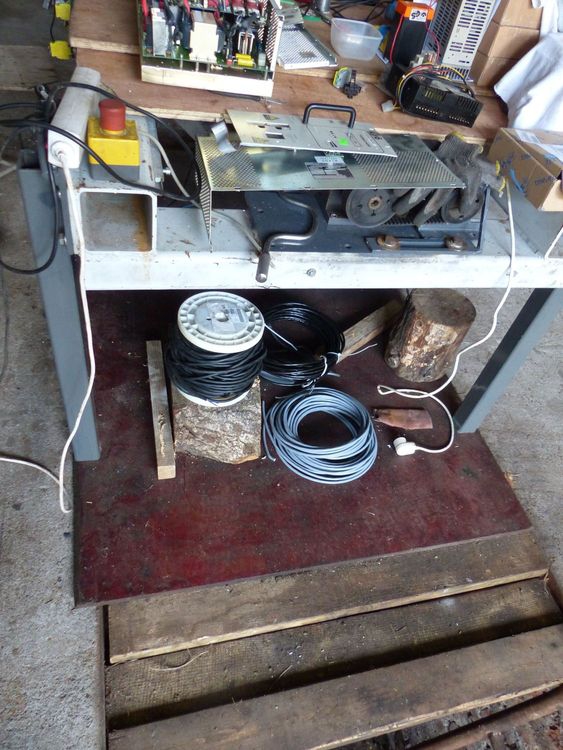
Rozpisujemy wyprowadzenia
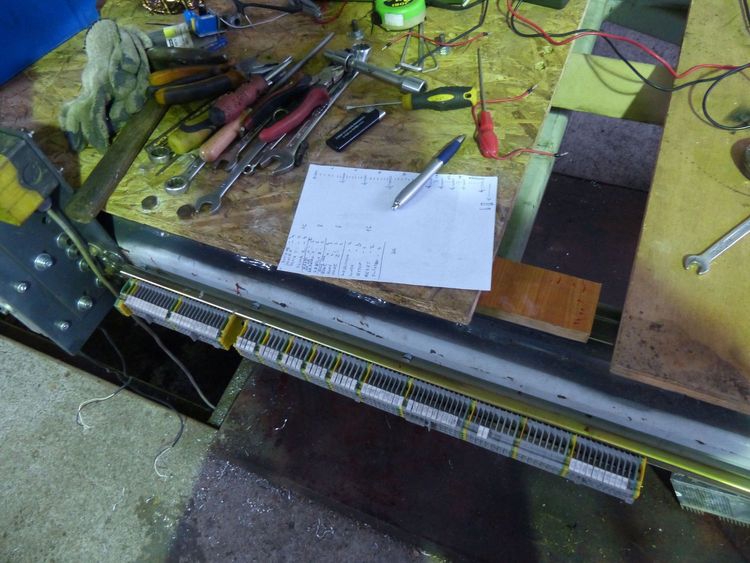
Łączymy do listwy...
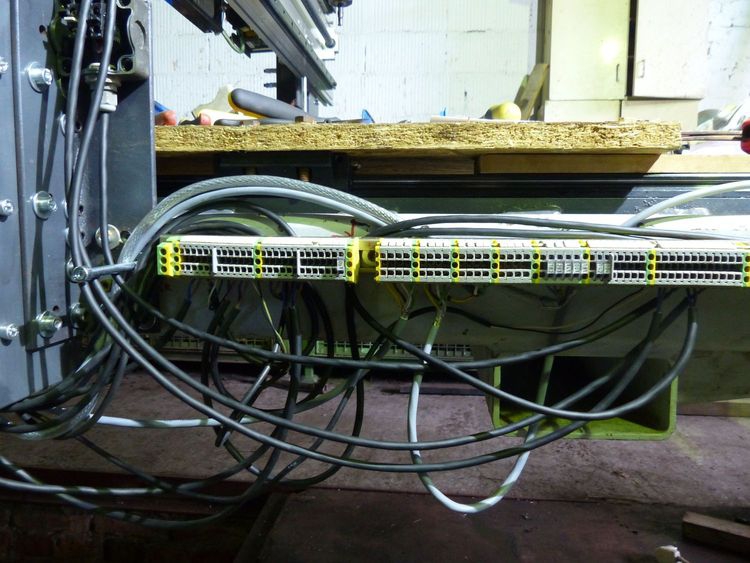
Przymierzamy, czy elektronika zmieści się na kawałku blachy który był na stanie
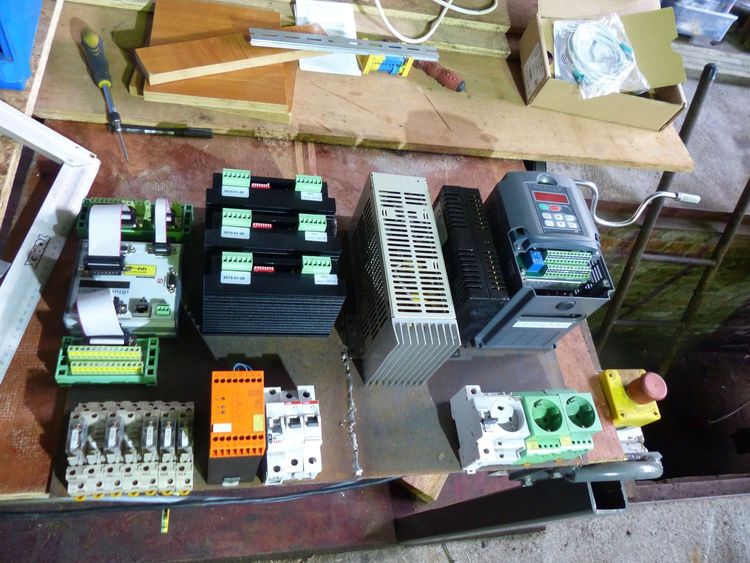
Zmieści!

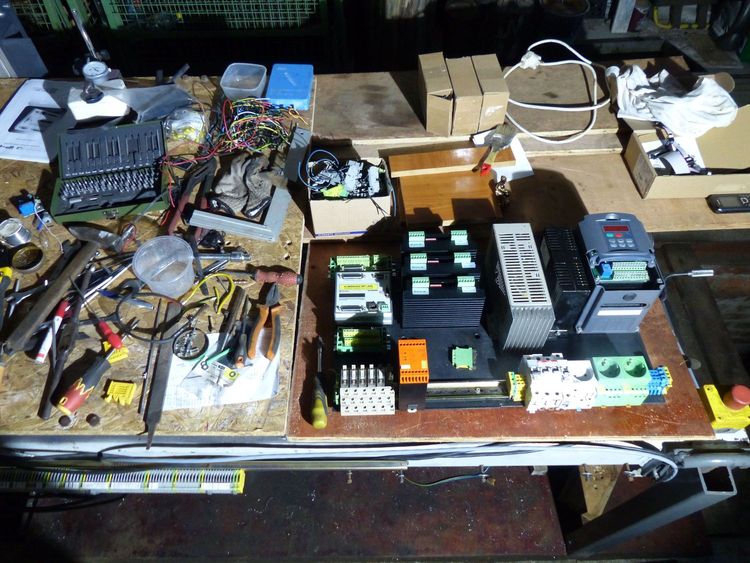
Klasyczny pająk... nie naśladować!
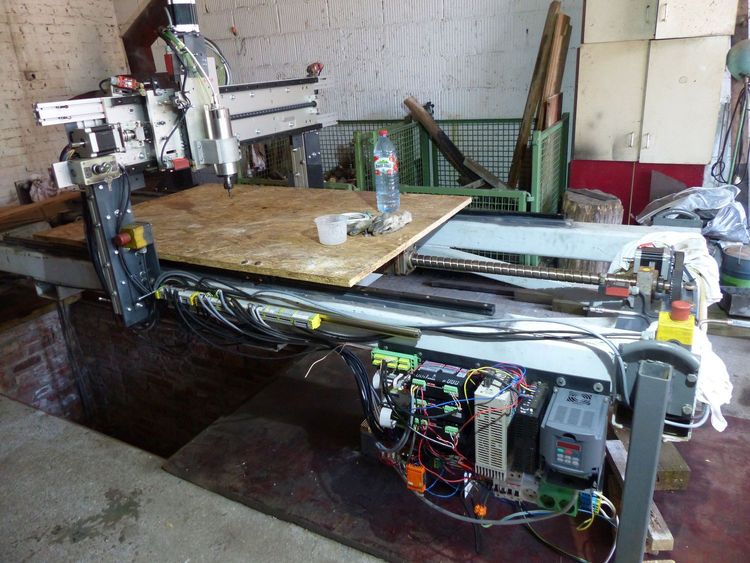
Równie prowizoryczny jak reszta stolik
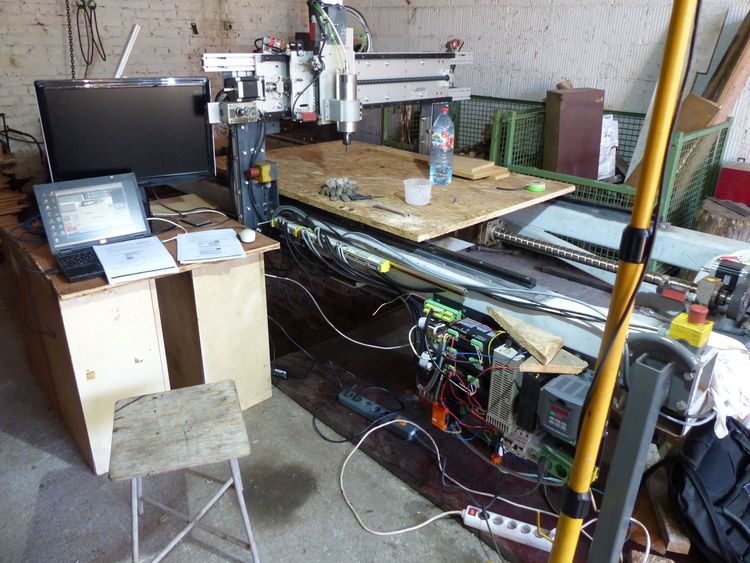
Uruchamianie i konfiguracja z manualem w ręce... oś Z dziwnie jeździ, raz dobrze, raz w inna stronę niż trzeba, raz tylko silnik terkocze

Przyczyna:
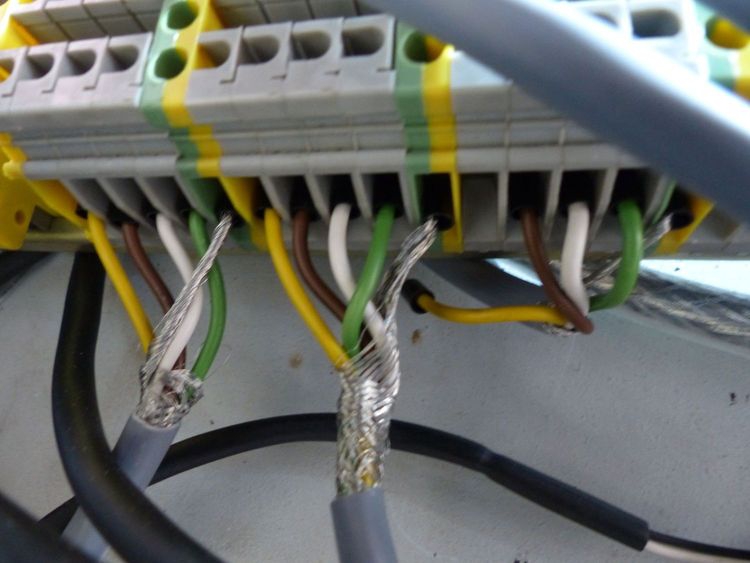
Pierwsze wiórki drewniane:
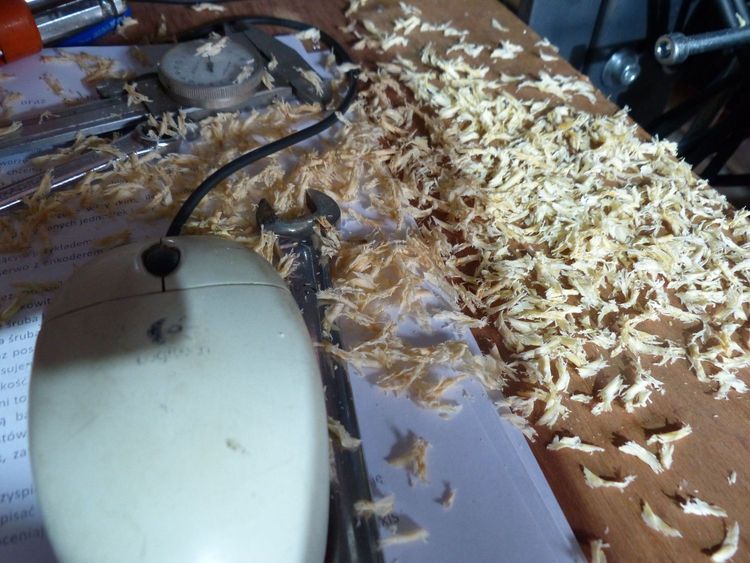
Pierwsze próby z aluminium:
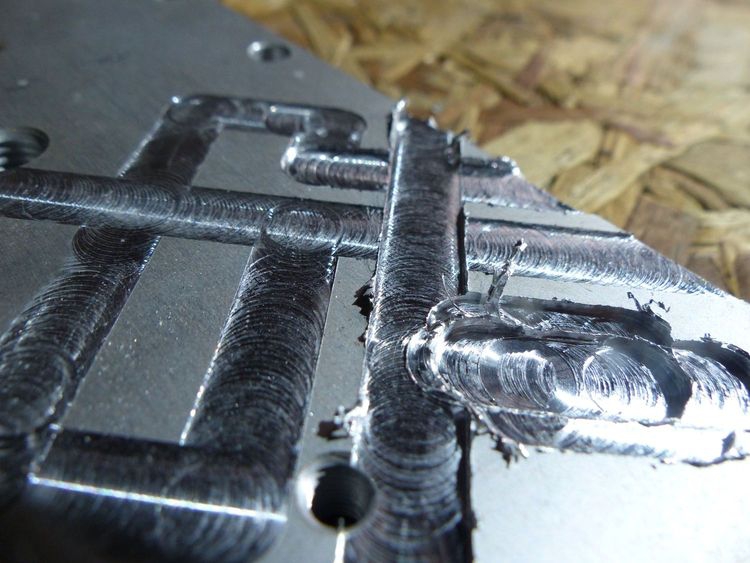
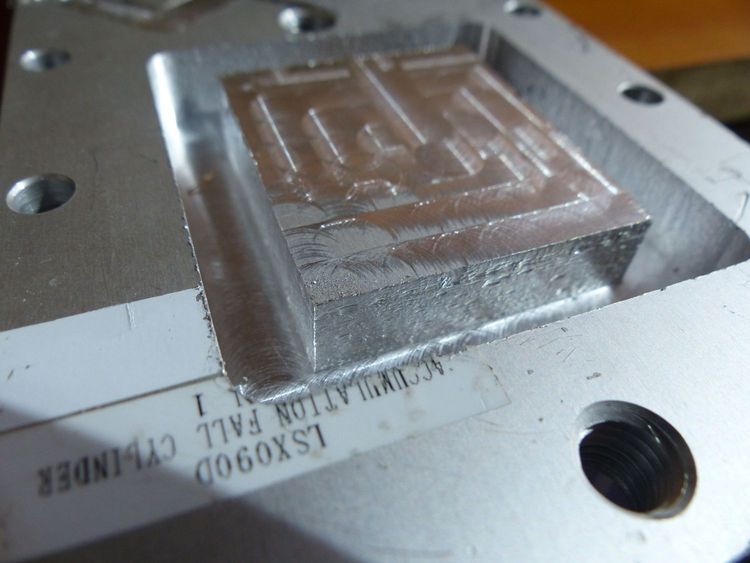
Hm, to tak.
Rama waży z 300, 400 kilo, gołej za jedną stronę nie mogłem podnieść. Profil ten główny długi - 120x120x8, poprzeczne ścianka 6, na to jeszcze dospawane żelastwo typu płaskowniki potem frezowane czy nogi na których stała. Brama z osiami i resztą - ze 100 kilo może?
Śruba stołu 40 skok 25, z przełożeniem na paskach 32/40 zębów, wychodzi taki sam posuw/obrót śruby jak w osi poprzecznej ze skokiem 20mm, napędzanej bezpośrednio. Zetka skok 10mm też napędzana bezpośrednio.
Celowo jest brama wykonana jak jest, żeby było szybko i bez kosztowo. Docelowo myślałem o takim czymś, tylko nie wiem czy myślę poprawnie... kątowniki np. 120x120x12, dwa kawałki po ~30cm, przykręcić po bokach do obecnej ramy [spawanie chyba nie jest dobrym pomysłem, może się zwichrować rama mimo solidnego profilu?]. Te kątowniki wyszlifować ile się da potem nauczyć się skrobać - wyprowadzając płaszczyznę względem frezowanych baz pod prowadnice. Na płaszczyzny kątowników klasyczne nogi i klasyczna belka ramy, odprężona i obrobiona.
Jest to dobry pomysł, czy można rozwiązać mocowanie bramy lepiej, bez spawania i frezowania baz na dużej ramie?
Po zjechaniu frezem na stół i ciągnięciu bramy za górę, ile mam sił, frez rusza się 0.1mm w każdą stronę.
Na krzyżaku lub osi Z [nie robiłem jeszcze pomiarów w kilku miejscach] jest dużo większy luz, wrzeciono do stołu i ciągnąc za mocowanie wrzeciona ile mam siły 0.5mm, to samo w drugą stronę pchając. Nie wiem czy to luz na wózkach, czy na skręceniu dwóch płyt aluminiowych śrubami 5, gdzie płyty nawet nie przylegają do siebie całą powierzchnią... ustawię czujnik w kilku miejscach i posprawdzam.
Tak czy siak, plan mam na wykonanie może nie krzyżaka, ale płyty łączącej obie osie, z płyty alu np. 20mm, powierconej i do niej skręcając wózki Y/Z. Przy okazji rozstawiając trochę od siebie wózki Z, w tej chwili przylegają do siebie [wózki 20]. Być może robiąc od razu całą Z na innych prowadnicach i śrubie - boki bramy zrobiłem z 50cm odcinków profila [szkoda mi było ciąć inne kawałki po 2m które mam], robiąc jakoś tą bramę stalową chciałbym ją wyższą... wtedy braknie pracy Z.
Stół. Tego co jest stołem nie można nazwać... po przyciśnięciu frezem ugina się kilka milimetrów, przy zagłębianiu freza w twardym materiale wpada w straszne wibracje. Tymczasowo chcę kupić kawałek sklejki, zrobić pod nią stelaż z kątowników, za kątowniki do wózków, żeby było choć trochę sztywniejsze. Docelowo płyta aluminiowa lub stalowa, tylko to wydatek na który obecnie mnie nie stać.
Hipotetycznie, przy szerokości podparcia 100cm jak u mnie, po brzegach płyty aluminiowej - jaka musi być gruba żeby się nie uginała przy frezowaniu materiału typu miękkie aluminium? 20, 30mm? Da się na pewno policzyć ale nie umiem... w pięknych maszynach tu prezentowanych są takie płyty 20-30, ale lepiej podparte, bardziej po środku.
Testy. Uruchomiłem wszystko kilka dni temu. Silniki na kroku 1/50, ustawione eksperymentalnie tak żebym zapierając się o oś nie był jej w stanie zablokować a silnik gubić kroki - nie mam pojęcia czy to dobra metoda

Frezowanie... frezować frezuje, ale tu wychodzi moja niewiedza o parametrach skrawania... w klocek sosnowy frezem 8mm o powierzchni roboczej 30mm wchodzi całą głębokością przy ruchu X/Y 3500mm - tylko nie wiem, czy to przyzwoity wynik czy beznadzieja. W zasadzie nie istotne, do nauki mi nie potrzebne wyśrubowane parametry.
Przy aluminium [nie wiem nawet jakim] i prędkościach 300/min idzie warstwą 0.3-0.4mm, powyżej wpada momentami w wibracje, i po frezowaniu zostaje wyraźnie gorsza powierzchnia. Tak samo przy zagłębianiu freza w alu, no ale to przez ten stół z gumy.
Geometria. Kwadrat 30x30cm na stole miał takie same przekątne +- 0.5mm mierzone metrówką. Nie pomyślałem, żeby zmierzyć ten klocek alu precyzyjnie suwmiarką... jutro to zrobię. Większego kawałka aluminium nie mam, żeby wyciąć np. 140x140 i sprawdzić.
Elektryka.
Na obu końcach osi krańcówki. Bazowanie na indukcyjnych. Powtarzalność bazowania wychodzi 0.02mm

Silniki gdzieś wyżej podałem, 6Nm. Sterowniki do nich M860, przewód ekranowany. Sterowniki spięte z CSMIO/IP-M.
Falownik + wrzeciono 2.2kW chiński komplet z ebaya [sprzedawca: wholesalermultifunction] Bicie na stożku 0.002

2 grzybki e-stop + reset z guzika na maszynie. To wpięte w przekaźnik bezpieczeństwa. Jeden kanał na te grzybki + kluczyk wpięte z wejściem CSMIO, drugi kanał odpina przez przekaźnik zasilacz od siników. Sterowniki mają wejścia enable, muszę później rozgryźć jak je też podłączyć i czy nie da się tego lepiej zrobić niż jest.
Zasilacz 24V do sterownika, czujników indukcyjnych i przekaźników, 12V do pompki wody.
Wykonanie elektryki... no mało profesjonalne. Będzie to docelowo wrzucone w porządną szafę i gdzieś z boku postawione. Do przewodów będą prowadnice zamiast puszczonych luzem jak teraz...
Komputer jak komputer, stary laptop z Machem3, póki co poustawiałem w nim osie, prędkości, jednostki, ustawiłem bazowanie i nauczyłem się bazować na home, ustawiłem limity programowe ruchu osi [fajna sprawa], pobawiłem się panelem MPG do ręcznego sterowania osiami i parametrami w nim... napisąłem g kod na całe 5 linijek który frezował ten prostokąt w aluminium. Właśnie, do nauki programów jeszcze by pasowało znać G-kody żeby wiedzieć z grubsza co program wypluwa - następny temat do nauki na tej prowizorce

Jak się powinno poprawnie nazywać osie? Są sprzeczne wersję, ta na bramie powinna być X czy Y?
Tu filmiki:
https://youtu.be/dVqAf7oqt6s
https://youtu.be/XU5qt0cGyA4