w pierwszych słowach chciałbym podziękować Wszystkim, którzy przyczynili się do powstania mojej maszynki – zarówno tym, którzy fizycznie mi pomogli, jak i tym których prace mogłem podziwiać na tym forum - osobom które podzieliły się swoim doświadczeniem.
Niestety mój projekt nie wnosi nic nowego i nie jest wolny od wad. Zastanawiałem się nawet, czy jest sens przedstawiać wynik, ale stwierdziłem, że jestem winny temu forum chociaż opis i parę fotek - za to, że mam nowe hobby...

Z załażenia ploter jest dla własnego, hobbystycznego użytku (cieszy każda wycięta literka). Prędkości przejazdowe nie mają więc dużego priorytetu, a dokładność z przedziału 0,1 – 0,5 mm będzie na zadawalającym poziomie.
A teraz konkrety:
############# PART I - MECHANIKA #######################
Obszar roboczy: 670x670x100 [mm]
Materiał obrabiany to wszystko, co wpadnie w ręce typu: sklejka, płyta wiórowa, decha, pleksi, mdf. Chciałbym również obrabiać aluminium - jeśli się uda puścić konkretnego wióra to super, a jeśli będzie szło tylko dziergać to uzbroję się w cierpliwość i niech jeździ

Konstrukcja skręcana – miała dać możliwość rozwoju i poprawek. Plusem jest też brak spawania = brak ściągania oraz brak odpuszczania po spawaniu, bo tego obawiałem się najbardziej.
Chciałem się wzorować na:
https://www.cnc.info.pl/topics60/konstr ... 041,60.htm
W miarę rysowania i przybywania kolejnych części stwierdziłem jednak, że belka bramy z profili może okazać się za słaba/wiotka.
U kolegów Gaspara i Bartussa wyglądało to już znacznie solidniej:
https://www.cnc.info.pl/album_page.htm? ... e=previous
https://www.cnc.info.pl/album_page.htm? ... &mode=next
Wiedziałem mniej więcej co chcę osiągnąć. Pole robocze założyłem minimum 500x600 (for fun). Przyznaję, że całość zacząłem dokładnie projektować jak już przybyło kilka część.
Pierwsze przybyły boki bramy od Kol. Bartussa, który miał je na zbyciu – solidne kawałki alu (20 [mm]), były już pofrezowane kieszenie na belkę bramy, łatę pociągową i na wózki prowadnicy liniowej (ale nie pod wózki chińskich wałków). W miarę postępów prac zostały trochę zmodyfikowane.
Drugi trafił się prawie kompletny stół. Nie udało mi się znaleźć z jakiego systemu pochodzą profile (90x45), są jednak zaskakująco masywne i proste (co najważniejsze). Kupiłem je jako używki razem z kątownikami łączącymi oraz z wibroizolatorami pod nogi

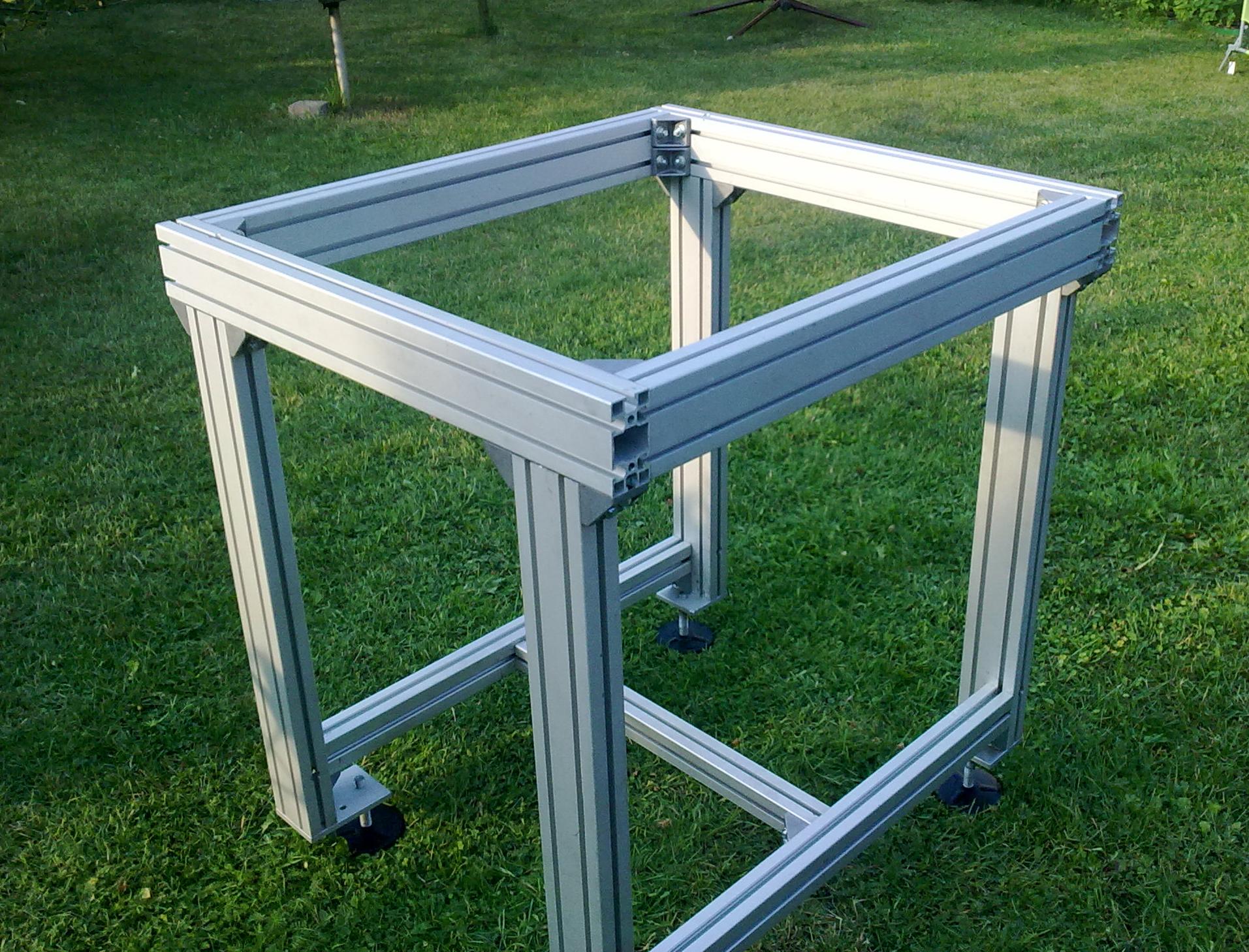
Stół po skręceniu tylko tymi kątownikami nie budził mojego zaufania. Po „uwieszeniu” się na części stołu niepodpartej nogą, słychać było… że wymiar ucieka. Zdecydowałem się na śruby M8 od czoła profilu, tym bardziej, że jest tam miejsce na nie (na powyższym zdjęciu jeszcze ich nie widać). Zdecydowanie poprawiło sytuację – teraz jest nie do ruszenia. Później dodałem jeszcze profil idący przez środek stołu – dodatkowo usztywnia całość i jest podporą blatu, co by się nie uwieszał.
Długie nogi, czyli to co misie lubią najbardziej – pozwoliły mi swobodnie zainstalować elektronikę i ułatwiają montaż obrabianych elementów (nie trzeba się tyle schylać, aby coś wymierzyć). Całość stołu jest o dziwo bardzo ciężka (niestety nie zważyłem), ale że brama też nie należy do najlżejszych (z elektrowrzecionem pewnie ponad 40 kg) to w początkowych fazach budowy czasem się zdarzało, że przy szybkich nawrotach stół próbował się pobujać. Przeszło mu, gdy zacząłem dokręcać/uwieszać coraz to więcej nowych części (szafa sterownicza, zbiornik chłodzenia wodnego, falownik itp.)
Dużym plusem tego rozwiązania jest to, że mogę nogi odkręcić bez ruszania ramy stołu i ułatwić sobie transport (nie oszukujmy się… komu by się chciało to wszystko odkręcać.. no chyba że zmuszony).
Nie chciałem ciąć profili ramy pod kątem 45 stopni i później ich składać (co by było super) ze względu na to, że nie zrobiłbym tego dokładnie, a jak wspomniałem profile z długości były już obrobione. Dodatkowo taki układ daje możliwość korekty w przypadku, gdyby brama wyszła np. 0,5-1 [mm] szersza od ramy i nie chciała wskoczyć na prowadnice (co jest ważne, gdyż nie miałem wszystkich części na raz, a czasem coś odstaje od rysunku technicznego..). Dzięki temu z geometrią stołu również nie było problemów.
Aby całość trzymała się kupy zabrałem się za zrobienie rysunków i rzutów. Warto trochę posiedzieć i coś nakreślić. Ślęcząc nad rysunkami można zauważyć co ma sens, a co nie, co jest proporcjonalne, co masywne, co się zmieści, co zawadza. Rysunki końcowe (oczywiście inspirowane zakupionymi już częściami, w tym osią Z):
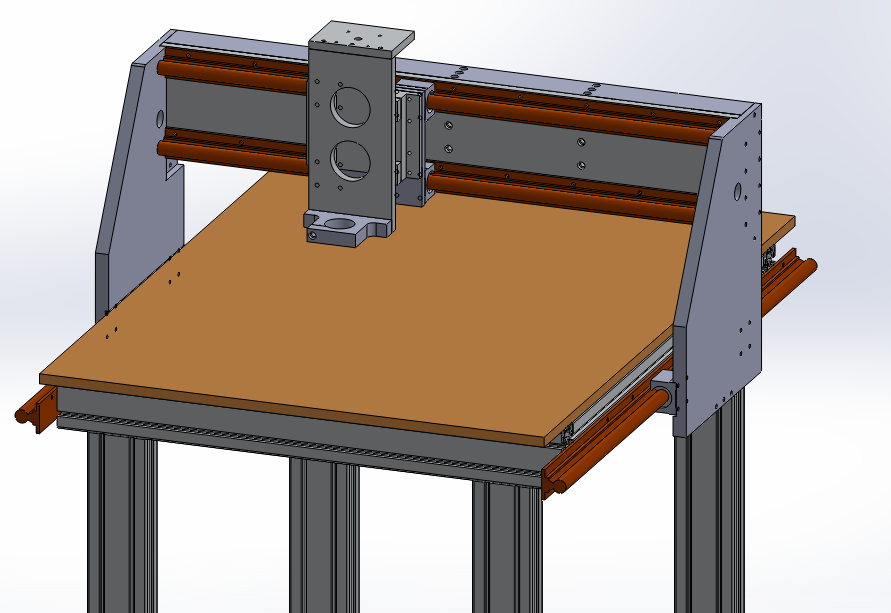
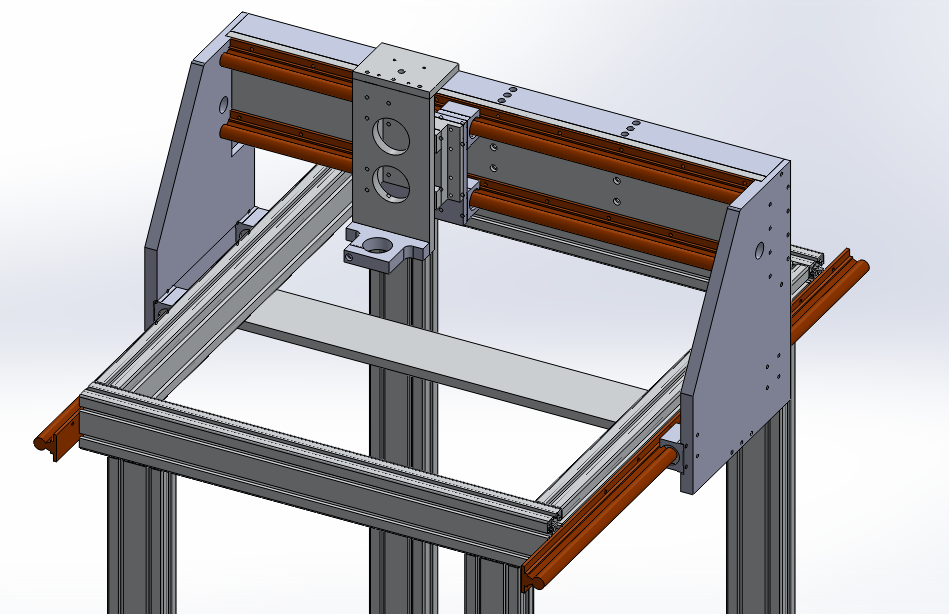
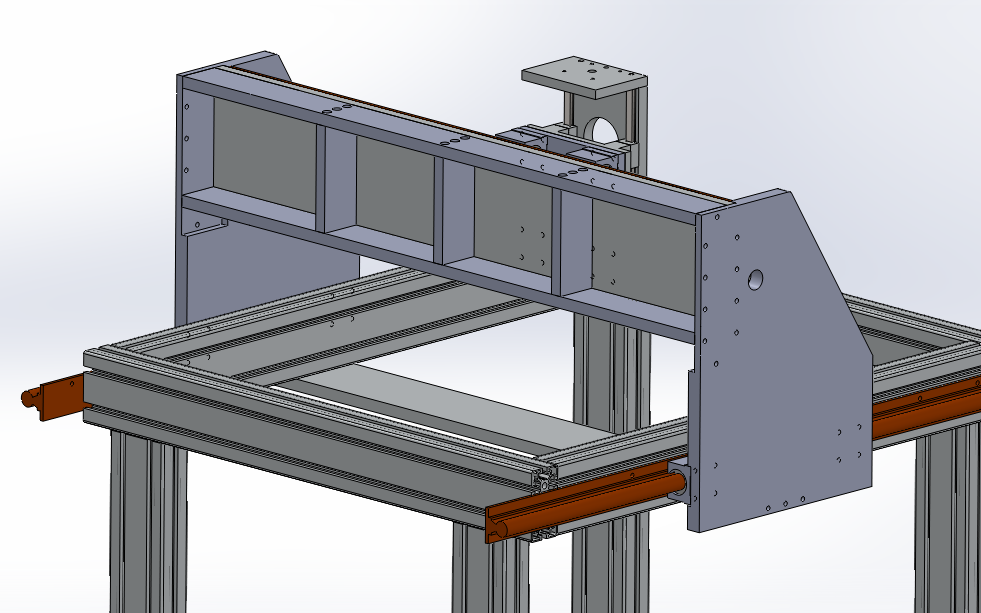
Rysunki z belką bramy zrobioną z profili 90x45 (chciałem jeszcze dodać rozpórkę pomiędzy dwoma profilami) – koncepcja odrzucona:
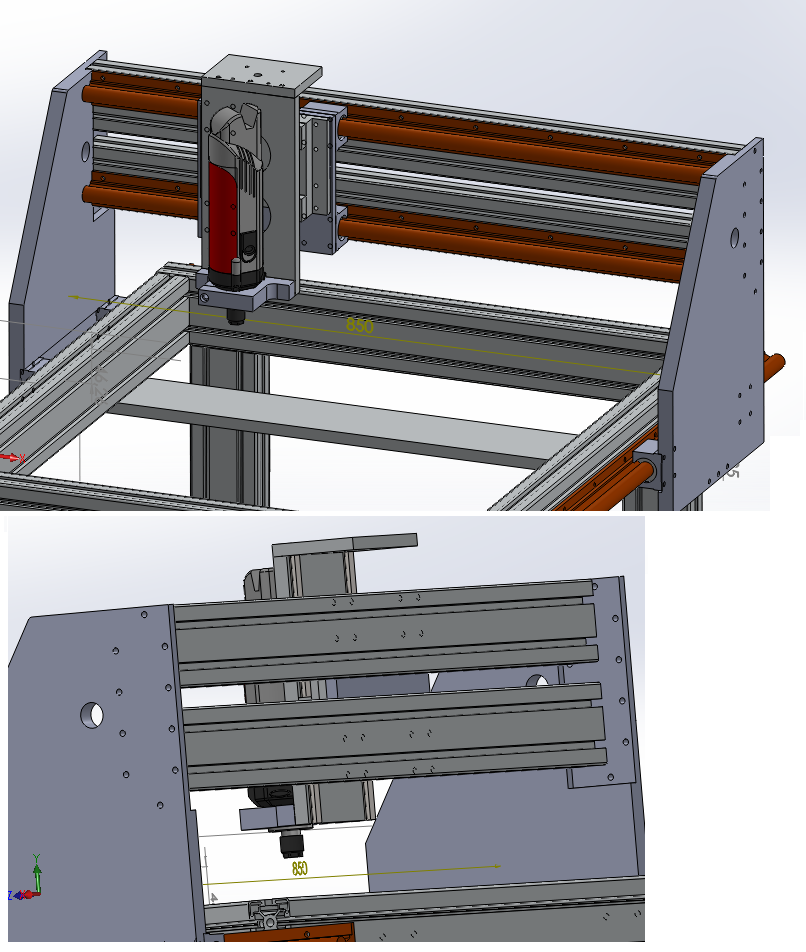
Zdecydowałem, że warto zainwestować w konkretniejszą belkę bramy i zrobić ją z formatek alu. W moim przypadku są to blachy 15 [mm] (bodajże Pa11).
Elementy składowe belki wykonał dla mnie forumowy kolega Patryk (Nicku nie podaje – jak będzie chciał to się sam ujawni), od którego wcześniej zakupiłem oś Z. Dobrze wykonana praca.
Prowadnice osi X i Y to poltechowe chińczyki, czyli wałki podparte fi20 z dedykowanymi wózkami. Chwilę się zastanawiałem nad prowadnicami liniowymi z prawdziwego zdarzenia (np. hiwin), ale wałki miały jedną przewagę – krzyżak osi XZ zdecydowanie był łatwiejszy do wykonania – praktycznie całość poskręcana z formatek bez konieczności frezowania dodatkowych rowków/podebrań. Całość się idealnie mieści i daje łatwo poskręcać – w przypadku prowadnic liniowych nie udałoby mi się zmieścić oprawki nakrętki (oraz śruby) bez obróbki płyty krzyżaka albo przeróbki belki. Również różnica cenowa nie jest bez znaczenia. Ostatecznie stwierdziłem, że wałki nie będą odstawać jakościowo od pozostałych elementów plotera

Dobrym pomysłem było wpuszczenie prowadnic osi X w boki bramy. Prowadnice zostały też nawiercone i nagwintowane, przez co mogłem je solidnie połączyć z bokami. Po tym zabiegu właściwie miałem już dobre punkty odniesienia (warto się przyłożyć, aby te otwory w bokach bramy były wyfrezowane dokładnie) i belka dała się poskręcać bez oporów.
Z tego co czytałem (tu na forum), złym pomysłem jest ustawienie prowadnic osi Y bokiem. Ponoć pracują tylko dwa z czterech rzędów kulek w łożysku (to logiczne). Przeczytałem o tym jednak za późno.. ale jak do tej pory nie mam z wózkami żadnych problemów (pracują płynnie), a jak by przyszło nawet je wymienić to są dość tanie (przynajmniej te chińskie) i łatwo mogę je podmienić (mam dobry dostęp).
Ogółem -> nie ma dramatu z tego powodu, ale warto to wziąć pod uwagę.
Czas na wytłumaczenie się z brzydko wystających prowadnic osi Y. Wystające prowadnice (na 70 [mm]) to efekt wyciągnięcia maksimum pola roboczego z dostępnego stołu. Taki z pozoru dziwny układ pozwolił na wykorzystanie wałków i śruby o długości handlowej 1000 [mm]. Właściwie mogę prawie dojechać bramą do końca prowadnicy zanim łata pociągowa uderzy w nogę stołu.
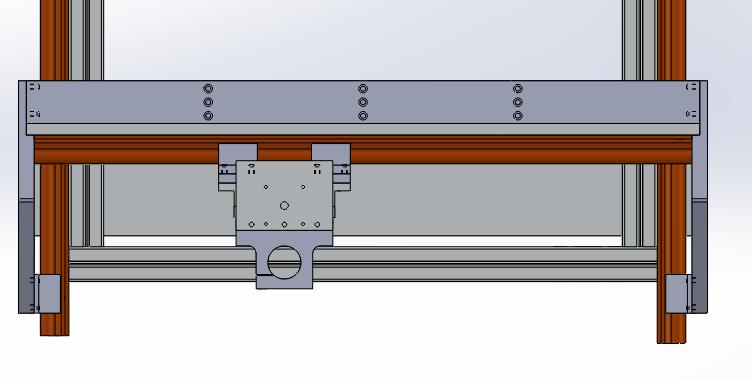
Oczywiście tak tych prowadnic nie zostawię. Mam już przygotowane cztery mocne kątowniki z nierdzewki (70x70, ucięte na szerokość profilu – 90 [mm]), które zamontuję pomiędzy profilami, a wystającymi podporami prowadnicy. To powinno skutecznie zwiększyć sztywność.
Część formatek wiercona ręcznie, a część na cnc. Dużo zabawy z gwintowaniem, tysiące śrubek, a każda pomyłka kosztuje kolejne rozkręcenie całości

(Łyk kawy, przymiarka -> dwa łyki kawy, skręcenie na „dwie” śrubki -> łyk kawy, pomiar dokładności, jest ok -> dwa łyki kawy, @##%& zapomniałeś skręcić czegoś wcześniej -> łyk kawy, rozkręcasz >>> wniosek = idź zaparzyć kolejną kawę)
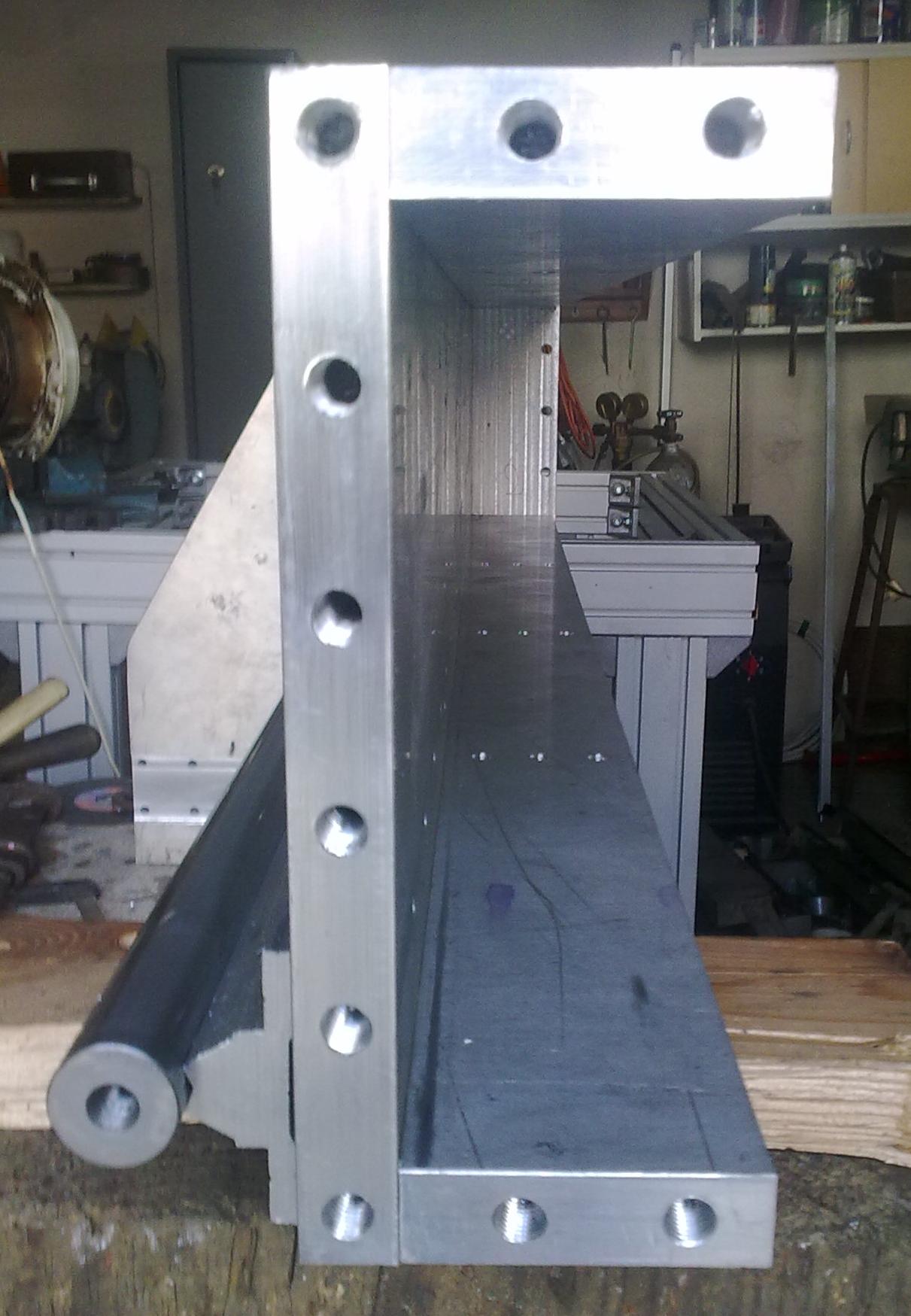
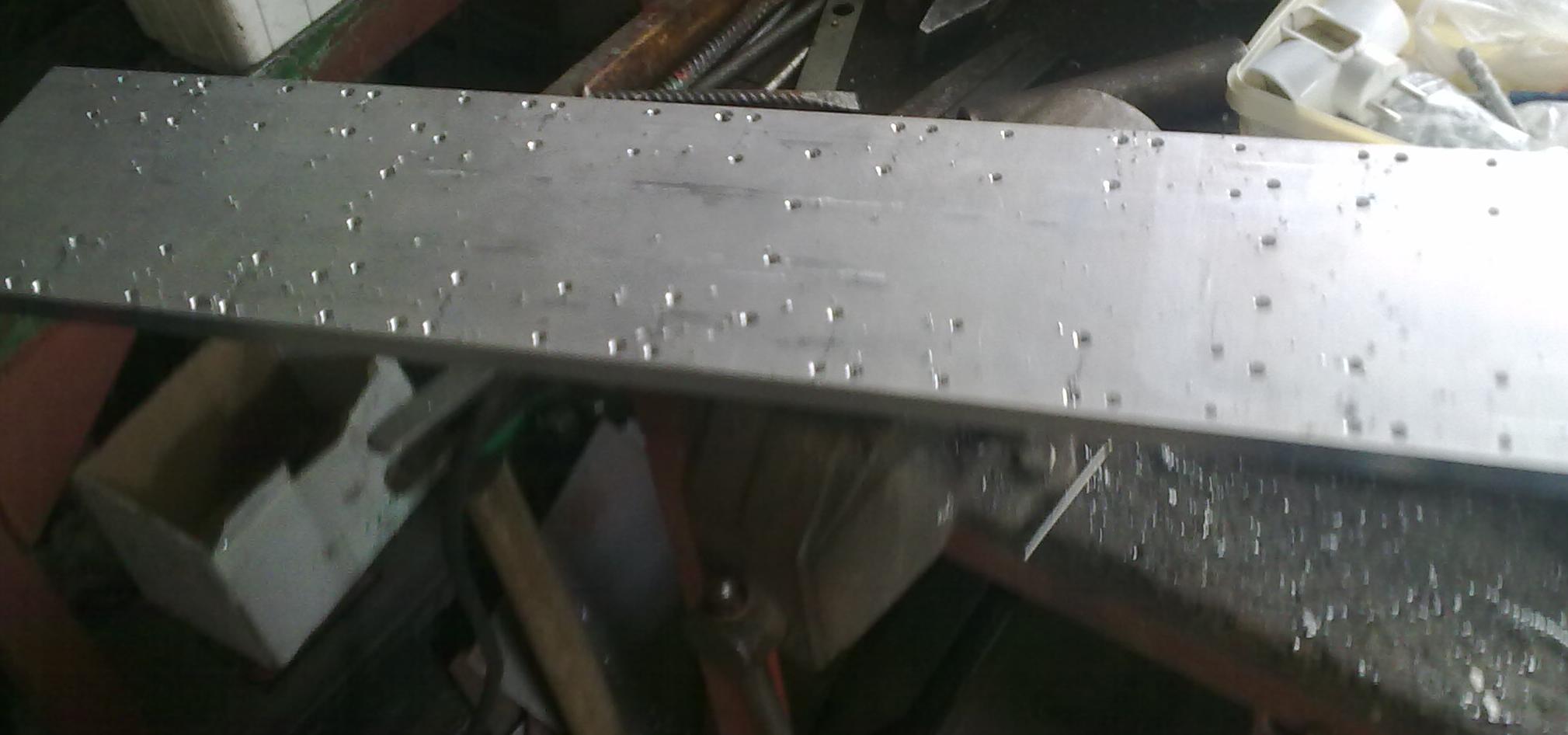
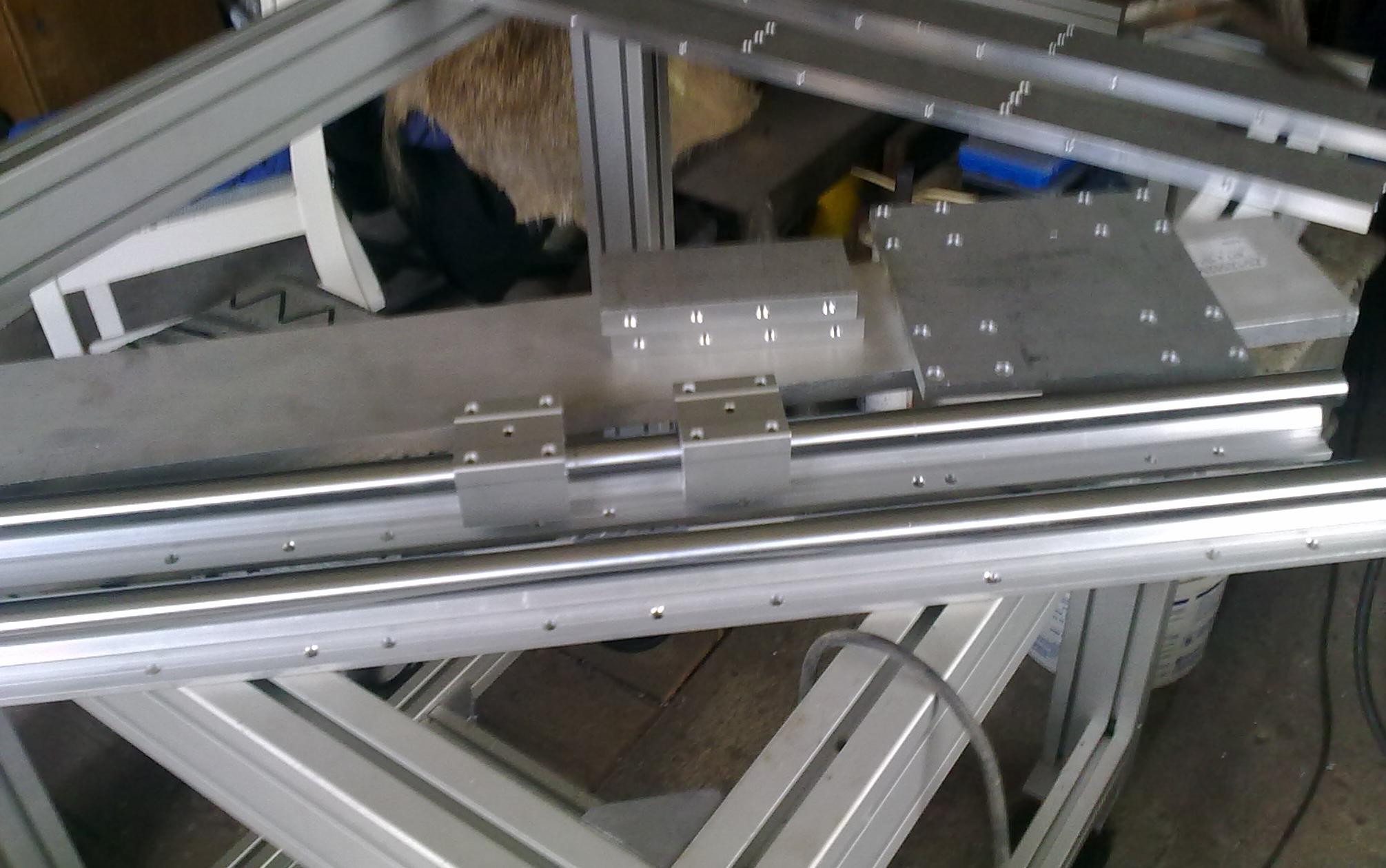
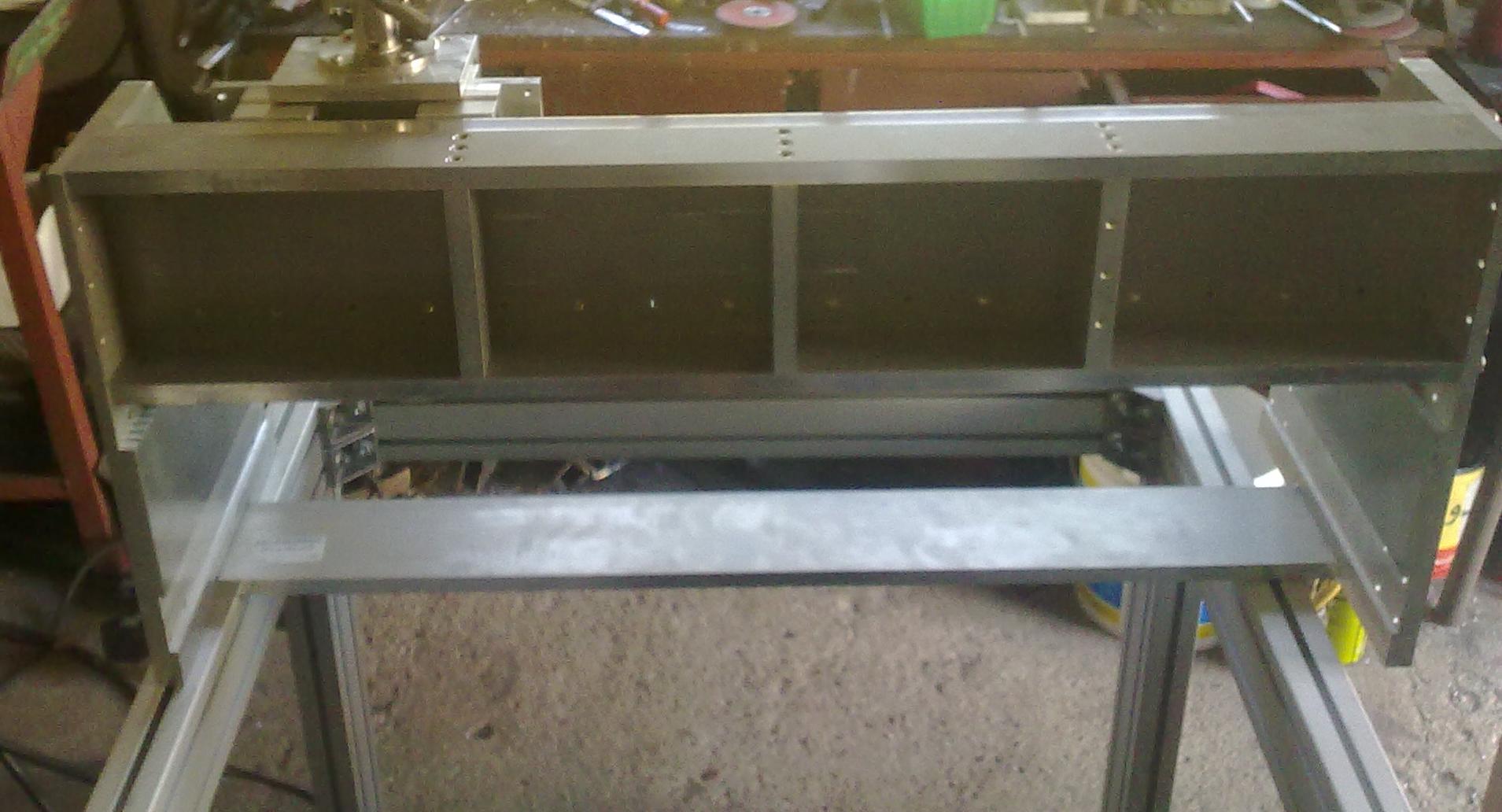
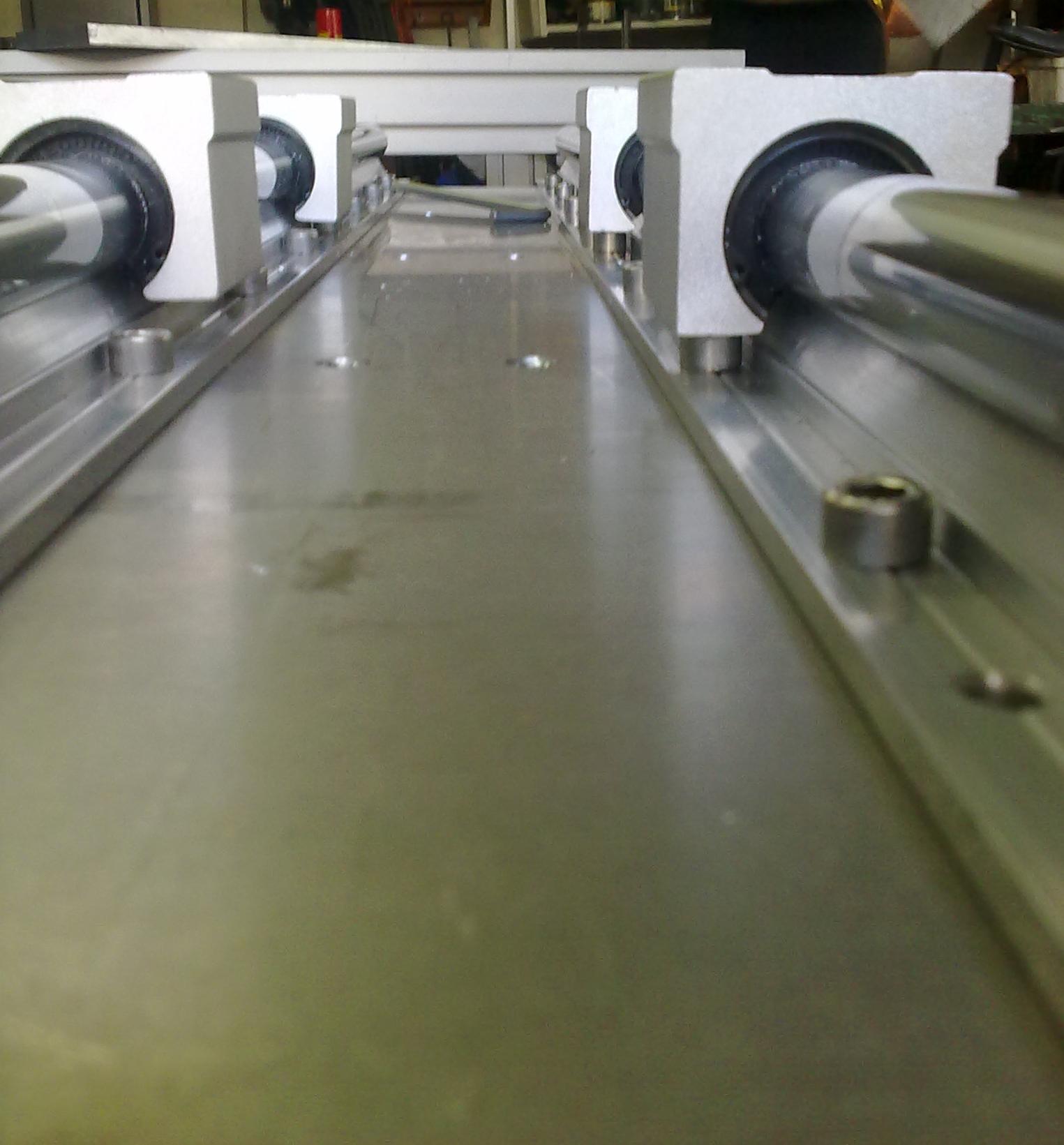
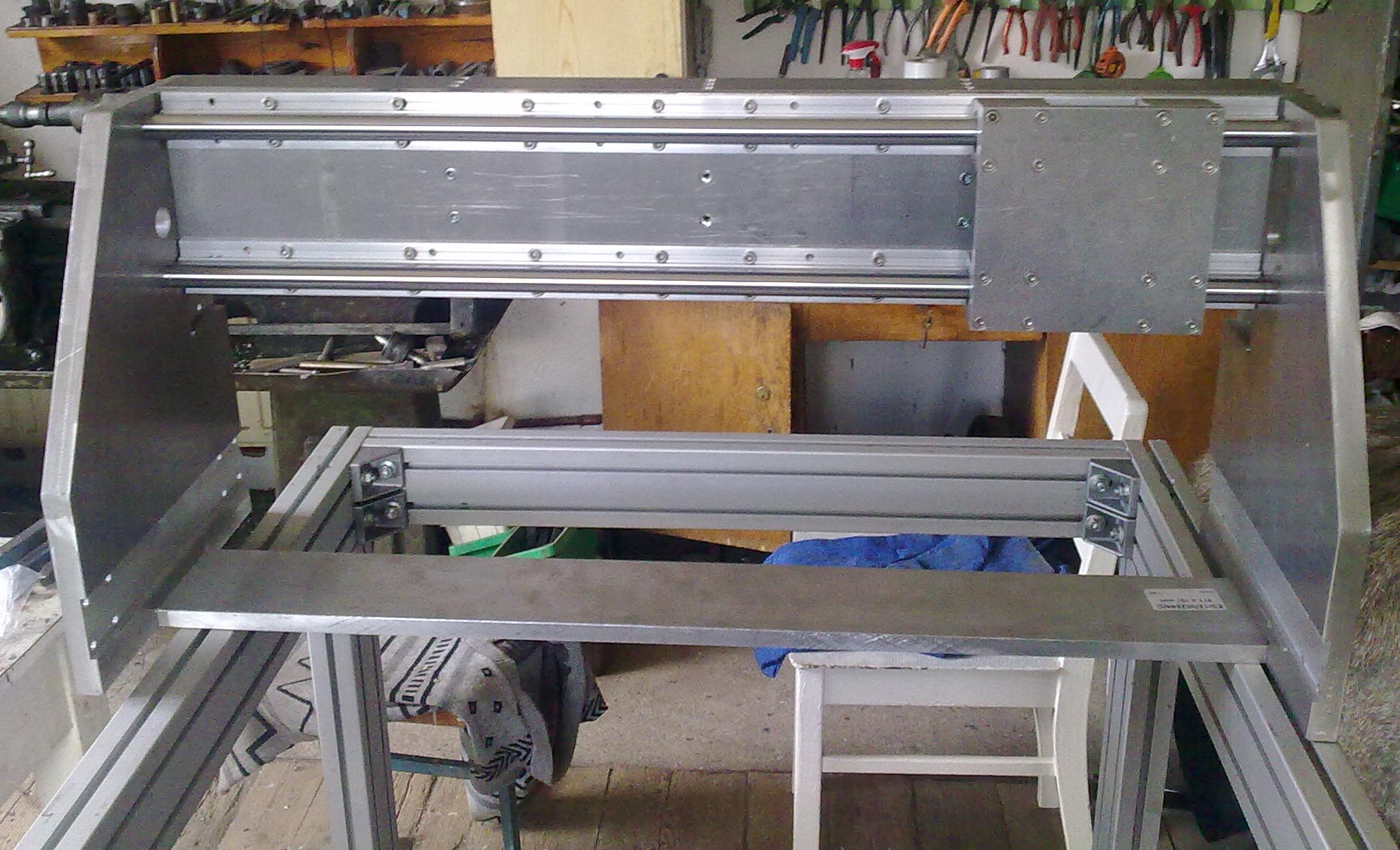
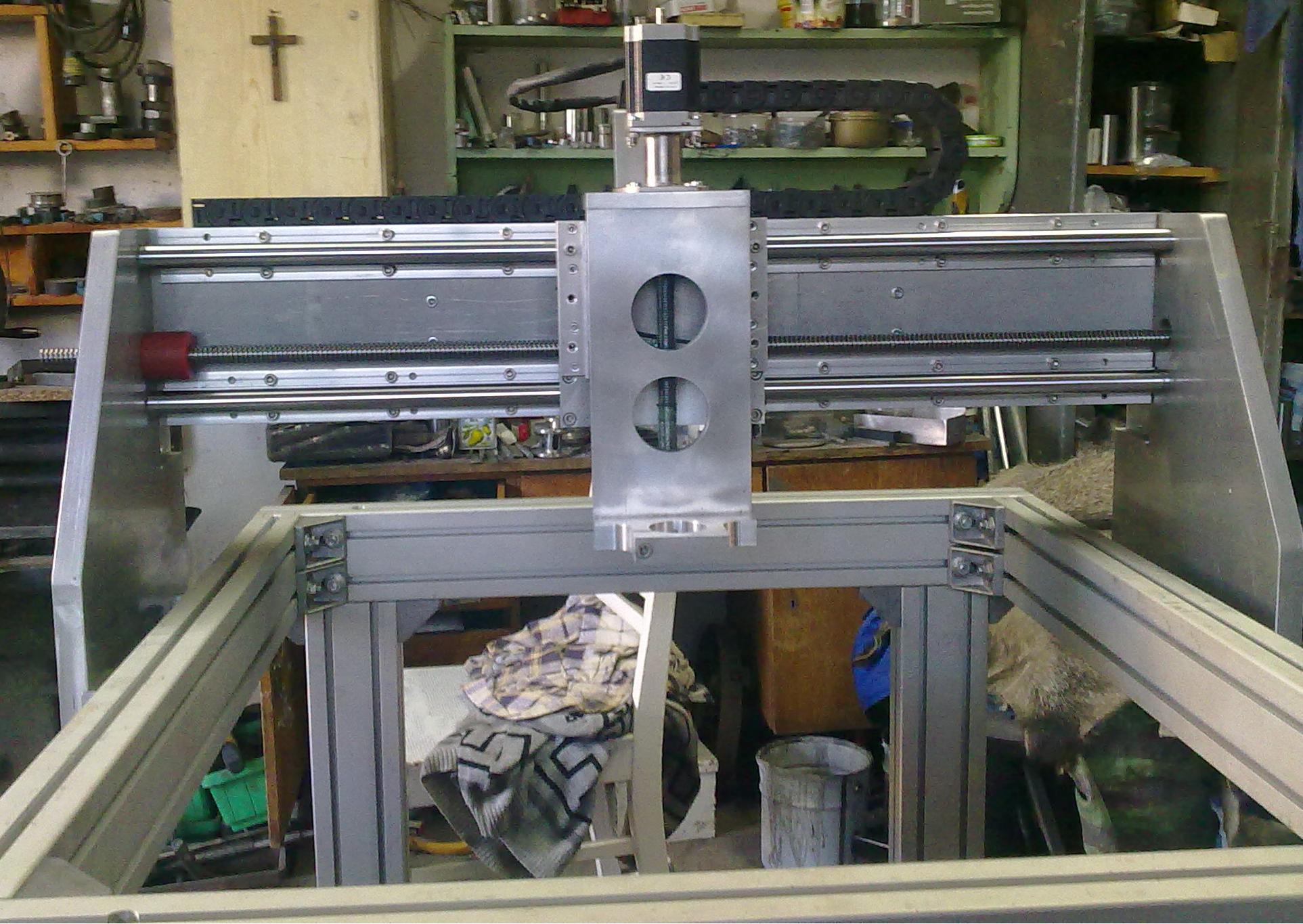
Kiedy całość ruszyła już we wszystkich osiach napędem białkowym, przyszła kolej na śruby. Zdecydowałem się na śruby trapezowe tr16x4 i nakrętki z kasowaniem luzu. O ile bezpośredniego dostępu do frezarki nie mam, to z tokarką jest już pełen wypas – jest w warsztacie i włada nią bardzo dobry tokarz – mój Tata

Sześcian stanowiący oprawkę nakrętek, został na tokarce „wytoczony” z wałka. W środku są dwie nakrętki z kołnierzem (jedna poliamidowa ze smarem stałym – od Kol. Pascala, a druga z brązu), jedna oczywiście na stałe, a druga przesuwna - dodatkowo jest jeszcze klin przez całość , aby się nie obracały (choć i tak nie powinny). Z wierzchu kołnierze nakrętek dostały „opakowanie” z kwasówki.
Na zdjęciu oprawka nakrętek osi X:
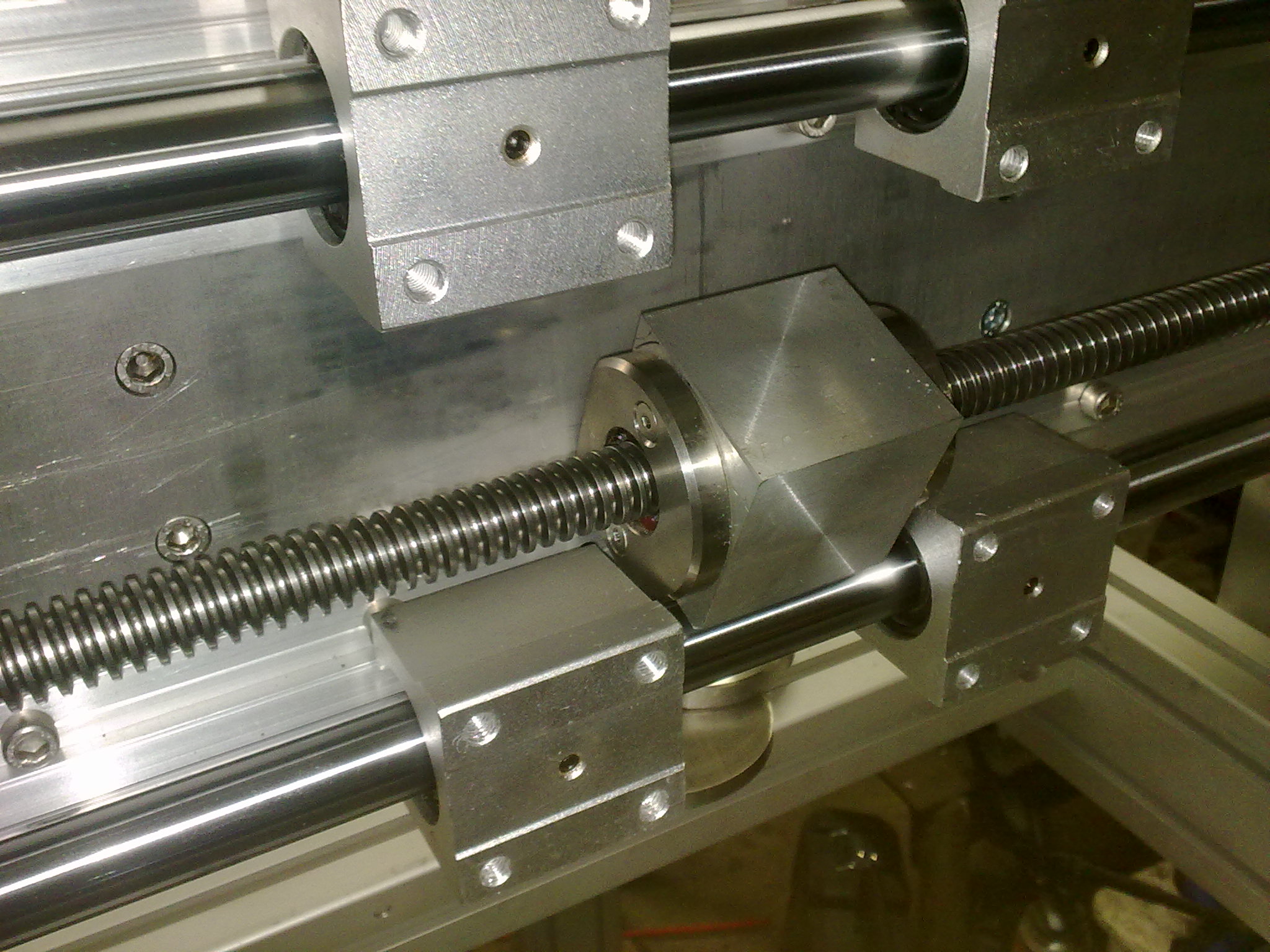
Śruba osi X nie jest umieszczona centralnie pomiędzy wałkami. Wynika to z faktu, że boki bramy były projektowane pod szerszą belkę. Otwory na śrubę w bokach bramy byłyby na środku, gdybym miał belkę o szerokości 200 [mm], a ja mam belkę 165 [mm]. Stwierdziłem, że nie jest duży błąd przy tak małym rozstawie prowadnic.
Wiem, że najlepsze byłby śruby kulowe (przez większość uważane za jedyny sensowny wybór), jednak nie chciałem już zwiększać kosztów. Budowa trwała bardzo długo i chciałem już zobaczyć, czy ma ona w ogóle sens.. czy całość ruszy i czy warto było się za to zabierać. Z czasem planuję wymianę na kulówki 16x5, może maszyna coś sama dołoży do tego interesu.
Boki bramy są na tyle szerokie, że w osi Y postanowiłem dać tylko jedną, umieszczoną centralnie śrubę. Jak na razie nie zauważyłem, aby były jakieś tendencje do przekaszania.
Łata pociągowa bramy ma szerokość 100 [mm] i trafiła na nią identyczna oprawka nakrętek jak w osi X.
Łożyska śrub to: 3200 2RS kulkowe skośne dwurzędowe – od strony silnika, a 6200 2RS - jako podparcie. Oprawki łożysk zostały wykonane również z nierdzewki.
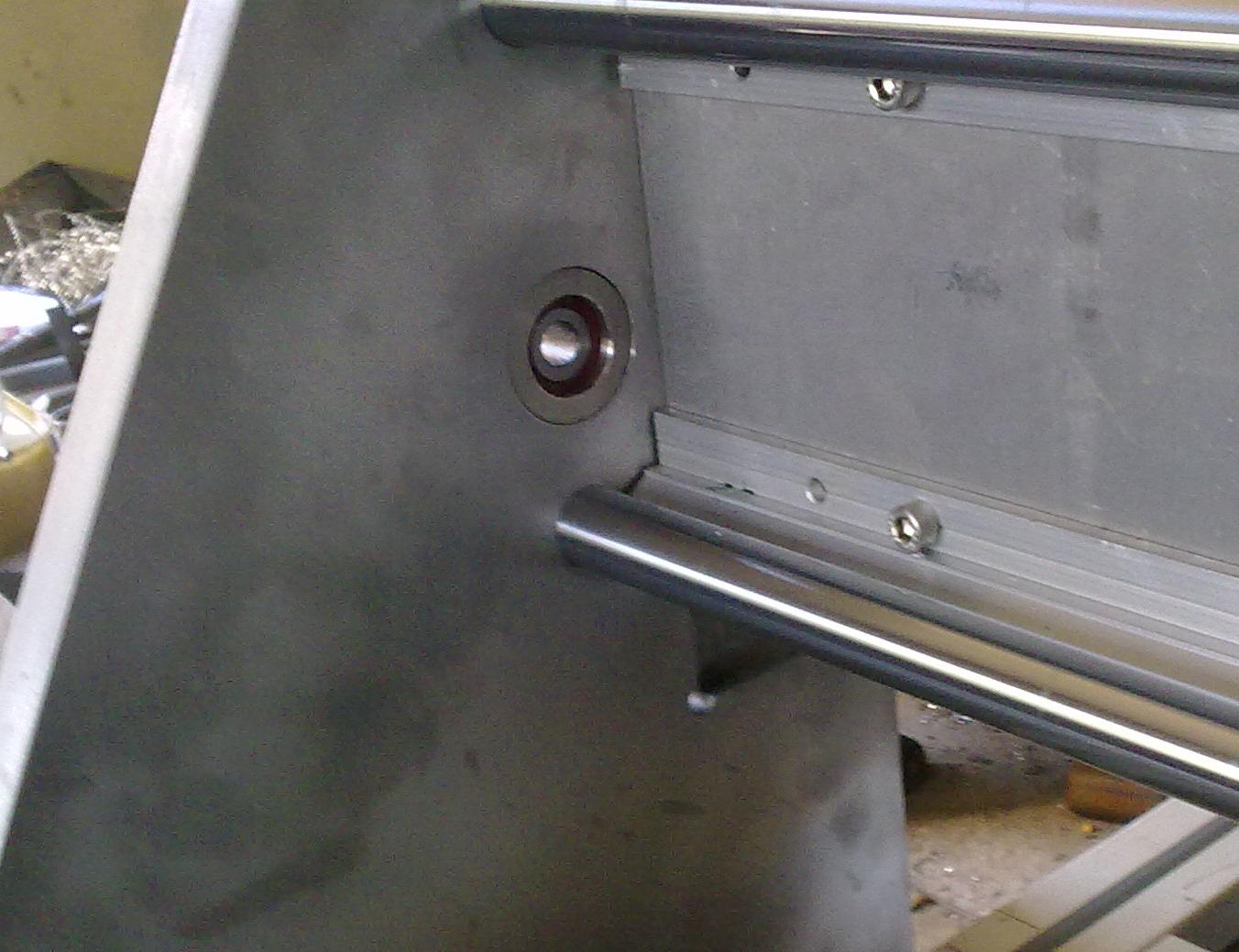
Oś Z została wykonana z formatek 12 i 15 [mm]. Kupiłem ją gotową, była projektowana pod kressa, ja jednak z czasem zmieniłem koncepcję. Napęd jest przenoszony poprzez śrubę metryczną (18x2) oraz nakrętkę z tworzywa (bez kasowania luzu). Zastosowane są dość wąskie prowadnice liniowe, ale za to dobrej jakości (Rexroth 9 mm). Śruba jest oczywiście do wymiany (miałem to zrobić od razu, ale póki działa to wolałem poświęcić czas na skręcenie reszty). Nie obliczałem możliwości prowadnic, są i tak zadziwiająco sztywne, połączenie wózków z krzyżakiem za pomocą śrubek M4 (albo M3?) to już słabo... Po kilku testach z obciążeniem ponad 10 kg, stwierdziłem, że tego teraz nie ruszam. Jak ploter da radę w alu to sam sobie części dorobi. Maszyna ma takie ograniczenia jakie ma jej najsłabsze ogniwo (to tak jak z kompem, a właściwie to chyba ze wszystkim).
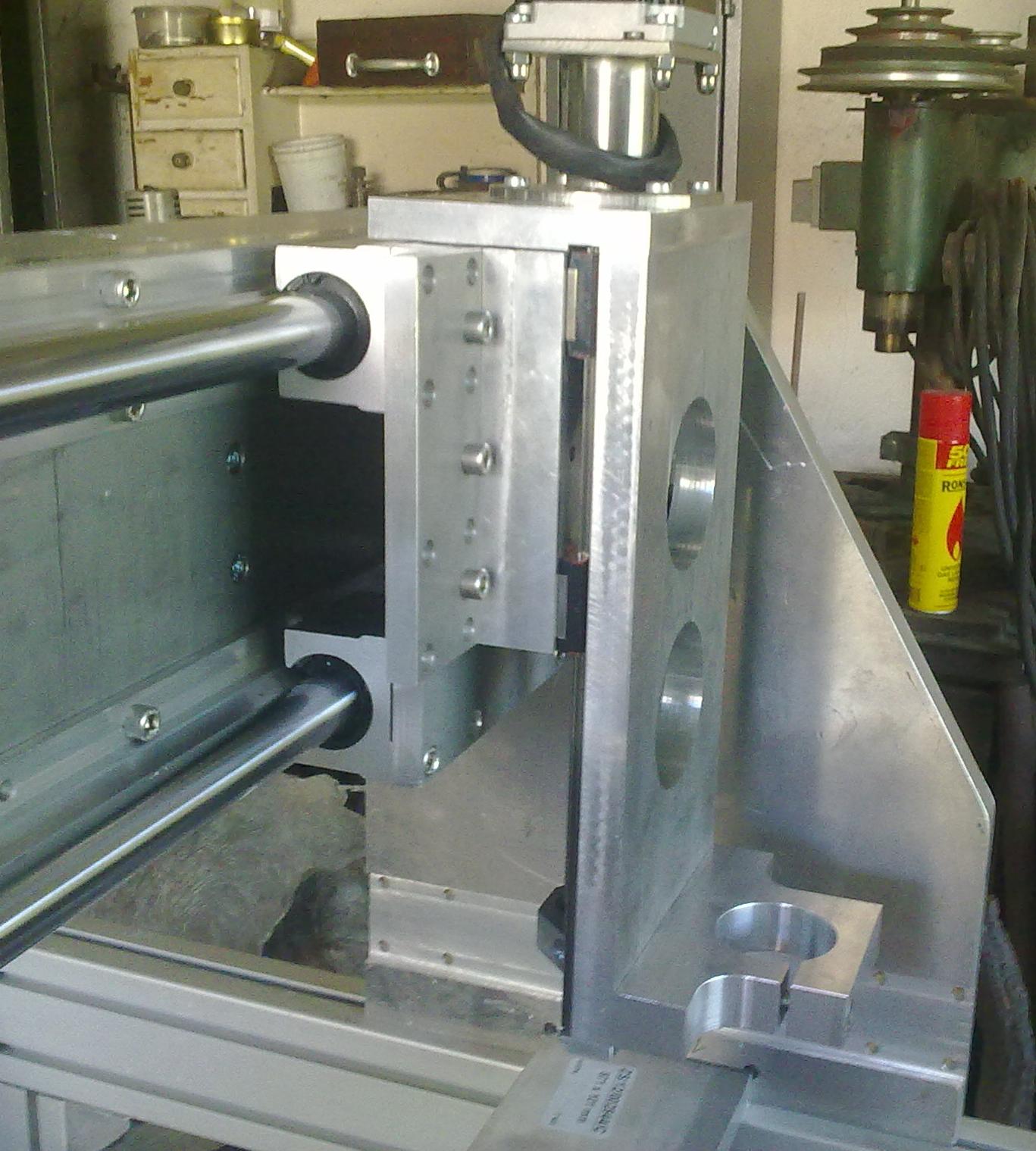
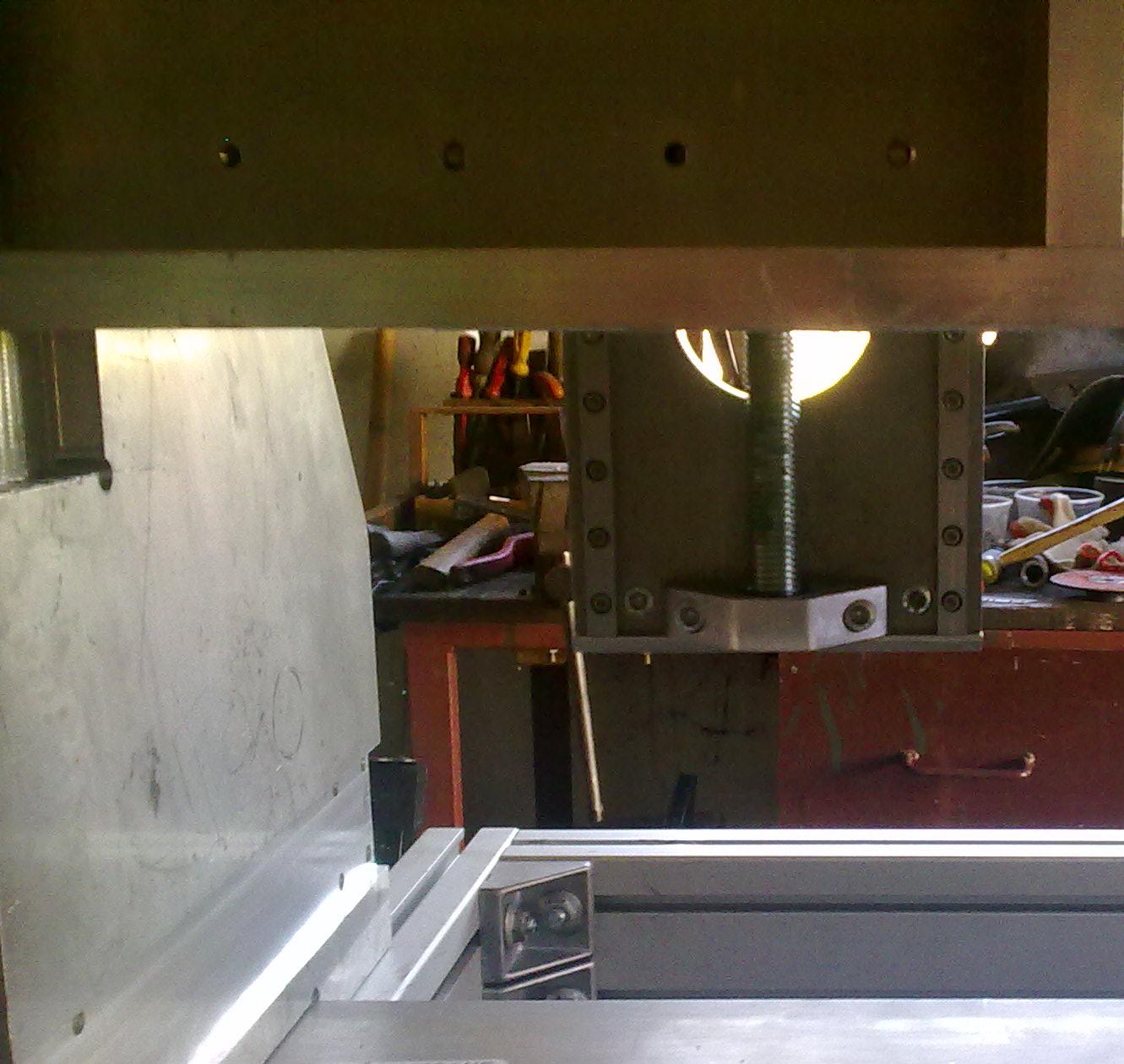
Od początku śledzenia forum dużo dobrego naczytałem się o elektrowrzecionie Kress i nawet dużo frezarek powstało właśnie z tym wrzecionem. Sam chciałem zastosować FME-1 1050. Pojawił się jednak konkurent znad morza żółtego - mokry chińczyk

Kupiłem chyba najczęściej kupowanego chińczyka z chłodzeniem wodnym, o mocy 2.2 [kW] i standardzie ER20. W moim przypadku o wyborze zadecydował niższy poziom hałasu niż w kressie – zależało mi, abym mógł sobie spokojnie doglądać jak ploter wycina – w końcu to hobby – ma cieszyć

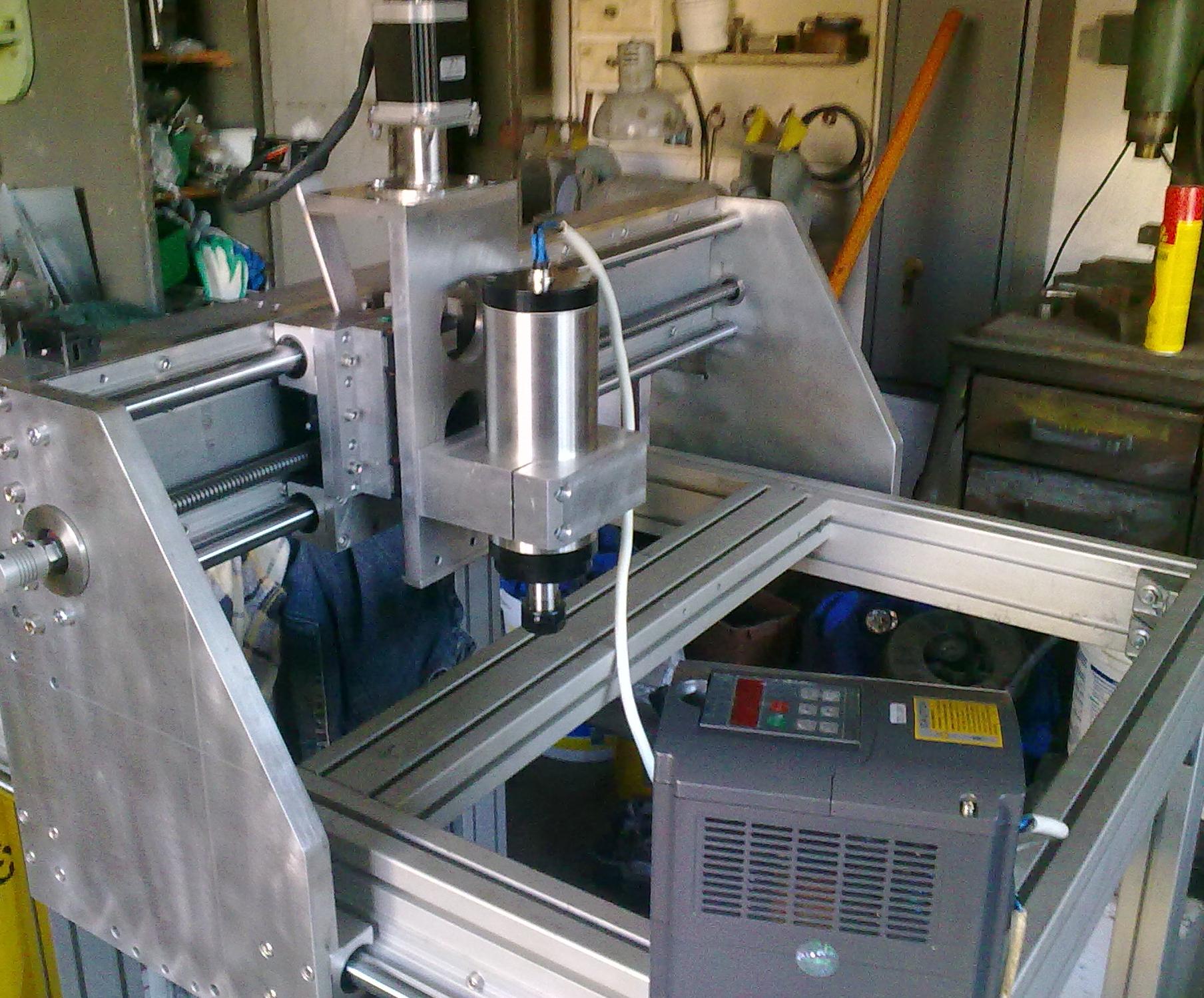
Zbiornik, pompka. Jeśli mokry chińczyk to trza dorobić chłodzenie. Na początku chciałem zastosować chłodzenie wodne z komputerów. Fajnie to wygląda, chłodnica z wiatrakami (np. 3 szt. 12 mm) + mała pompka + rezerwuar. Pewnie całość udałoby mi się umieścić na belce bramy. Niestety taki zestawik jest dość delikatny, a jego cena wygórowana. Postanowiłem nie iść na łatwiznę i zrobić coś z prawdziwego zdarzenia.
Tak powstał zbiornik z blachy kwasoodpornej, która walała się od dłuższego czasu po warsztacie. Wyszedł genialnie – znajomy pospawał całość. Po przejściu prób szczelności został jeszcze dopieszczony i przejechany satyniarką. Tata wykonał kroćce wężyków oraz kolanka do wskaźnika poziomu cieczy


I tym sposobem w żyłach jego płynie błękitna krew

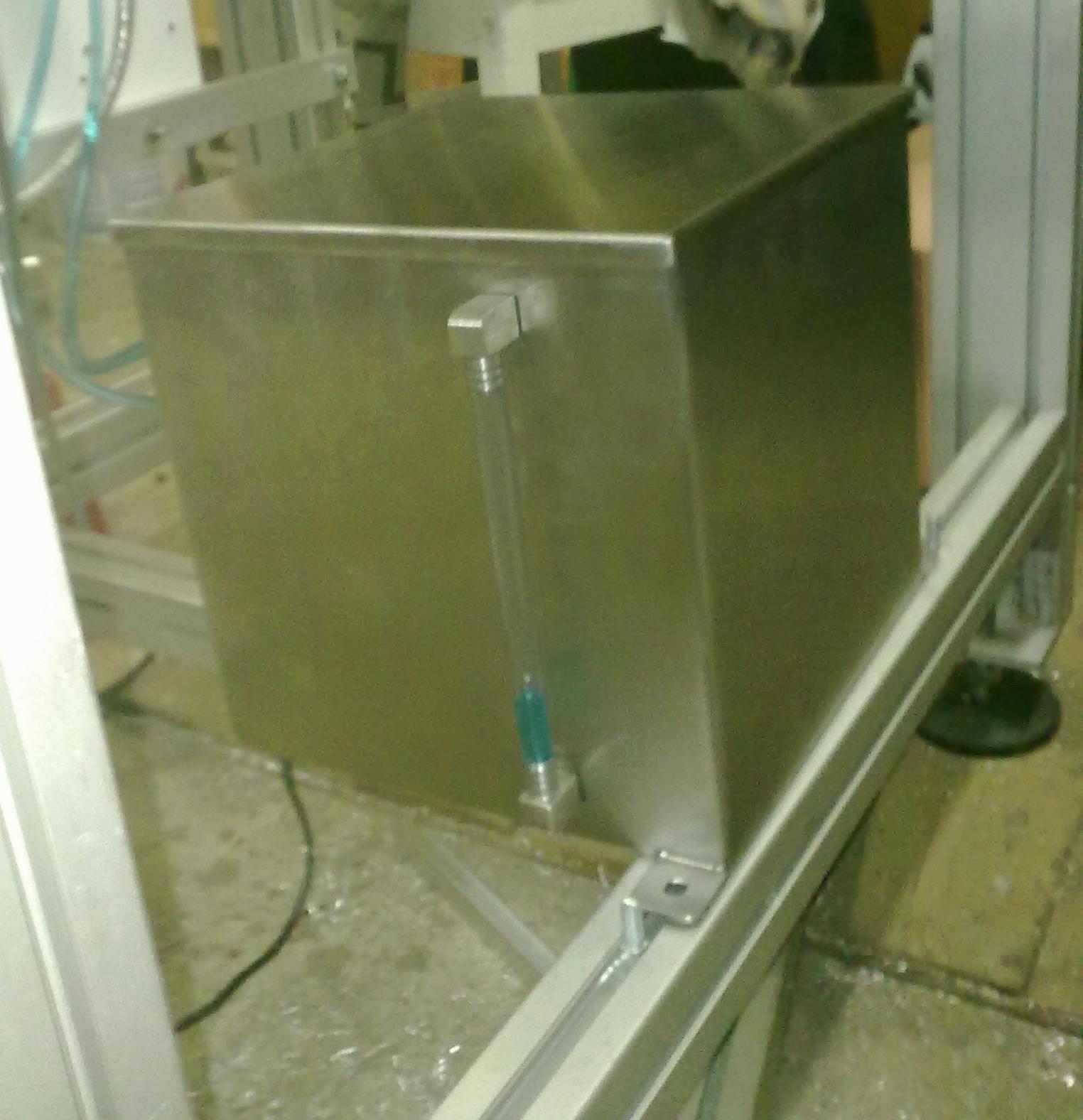
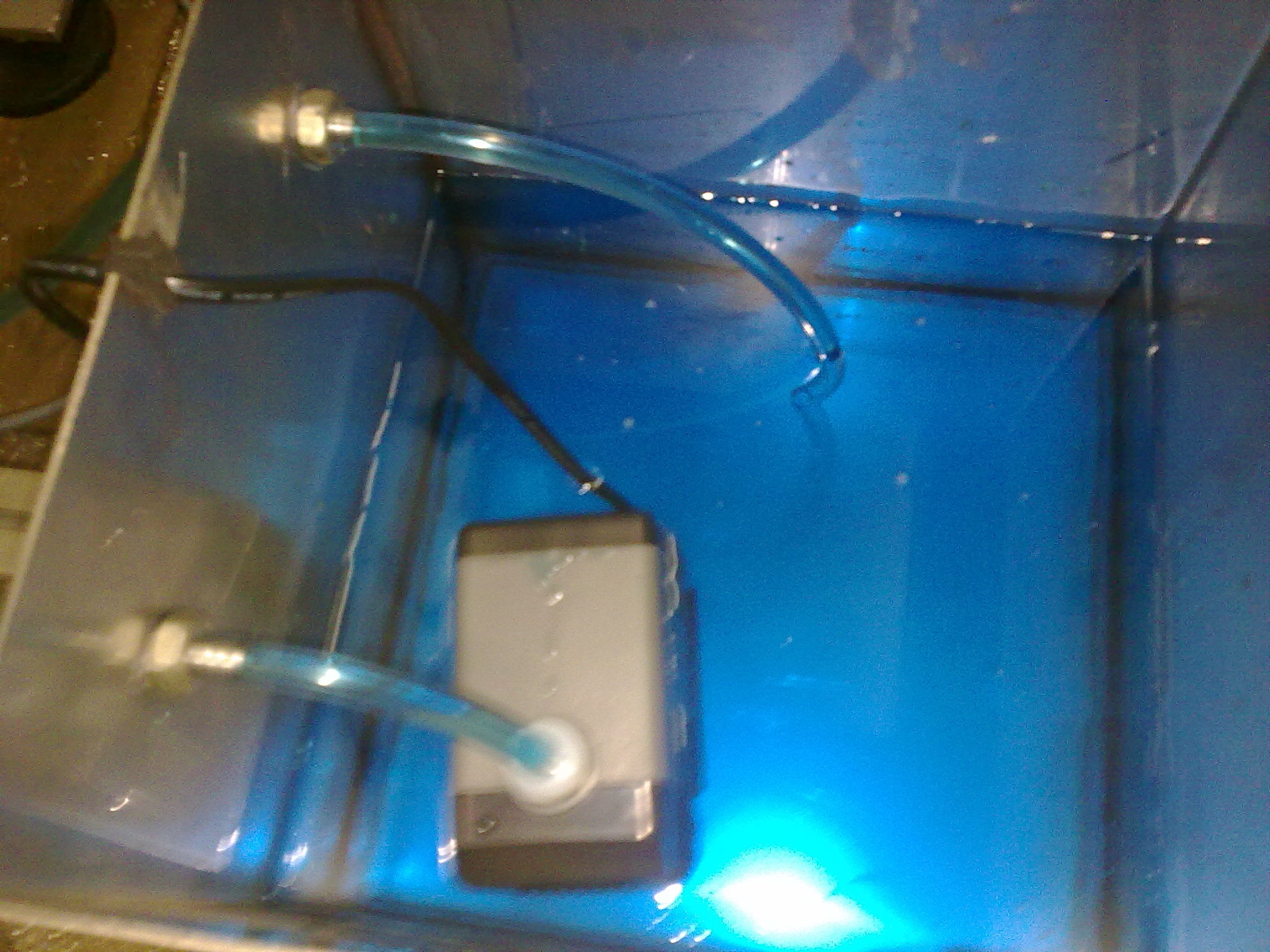
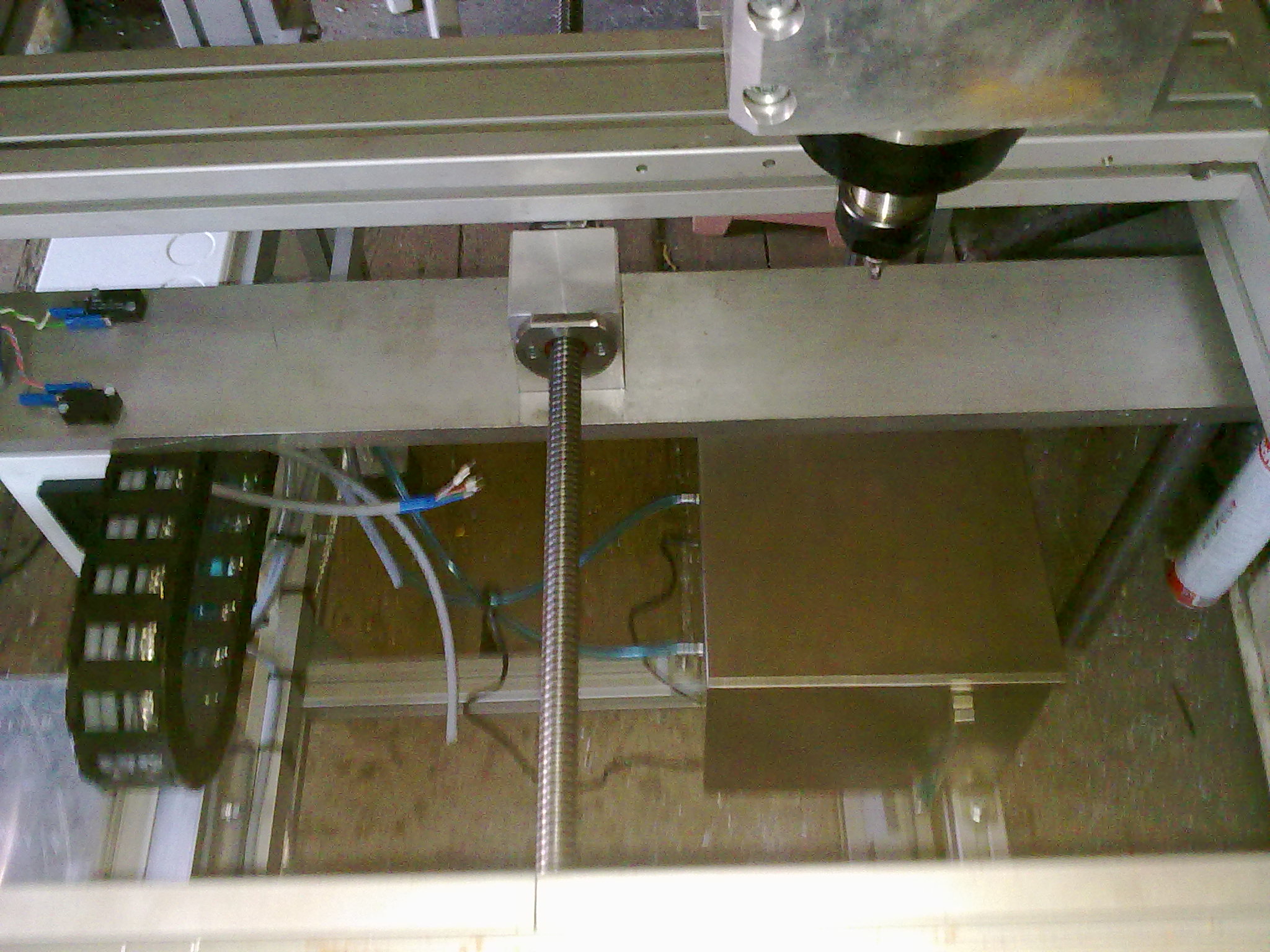
Maszyna już ruszyła, ale nie jest jeszcze ukończona. Wiszą wszędzie kable od krańcówek, a same krańcówki to zabawki za parę złotych (z czasem wymienię chociaż Home na indukcyjne).
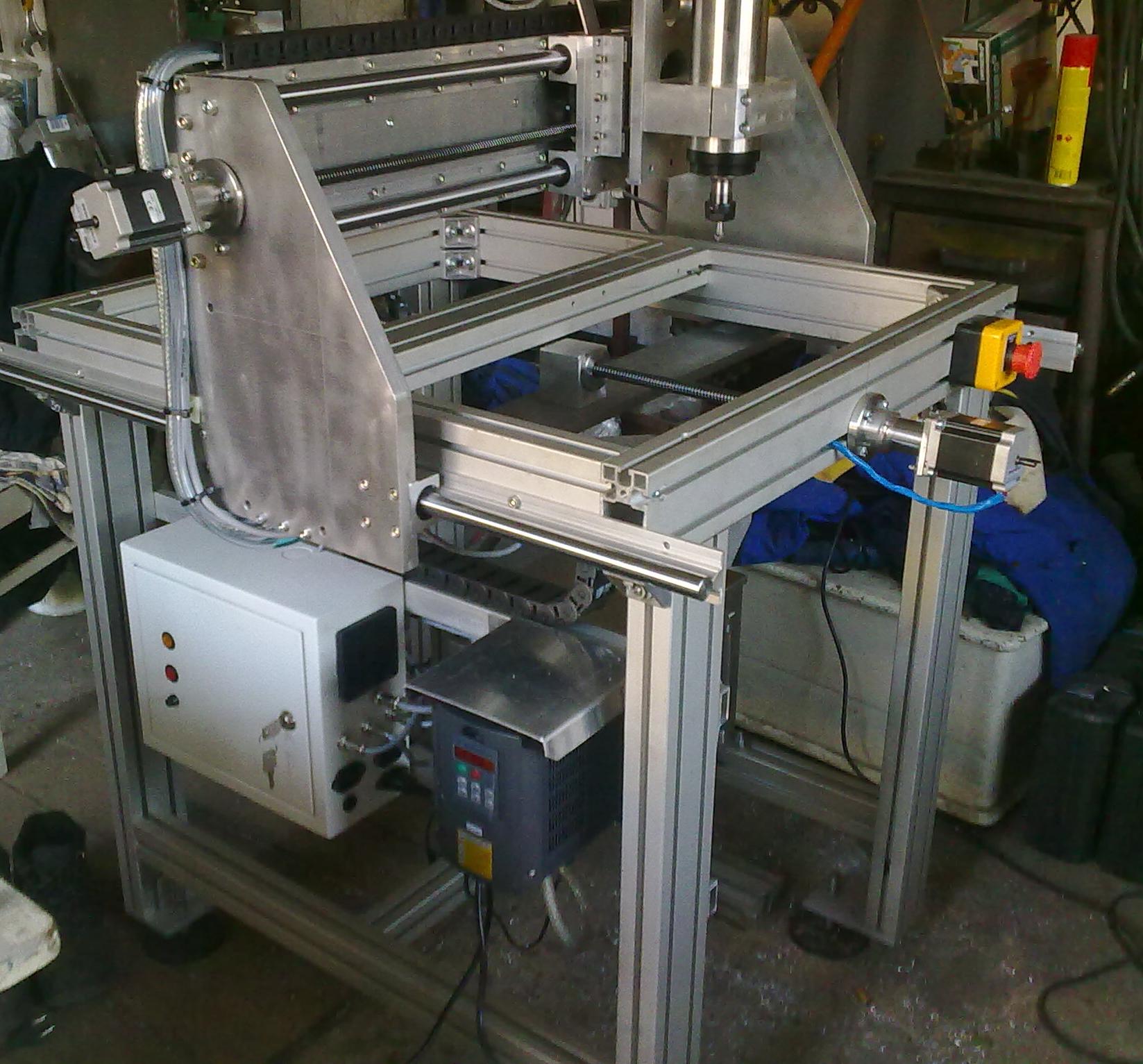
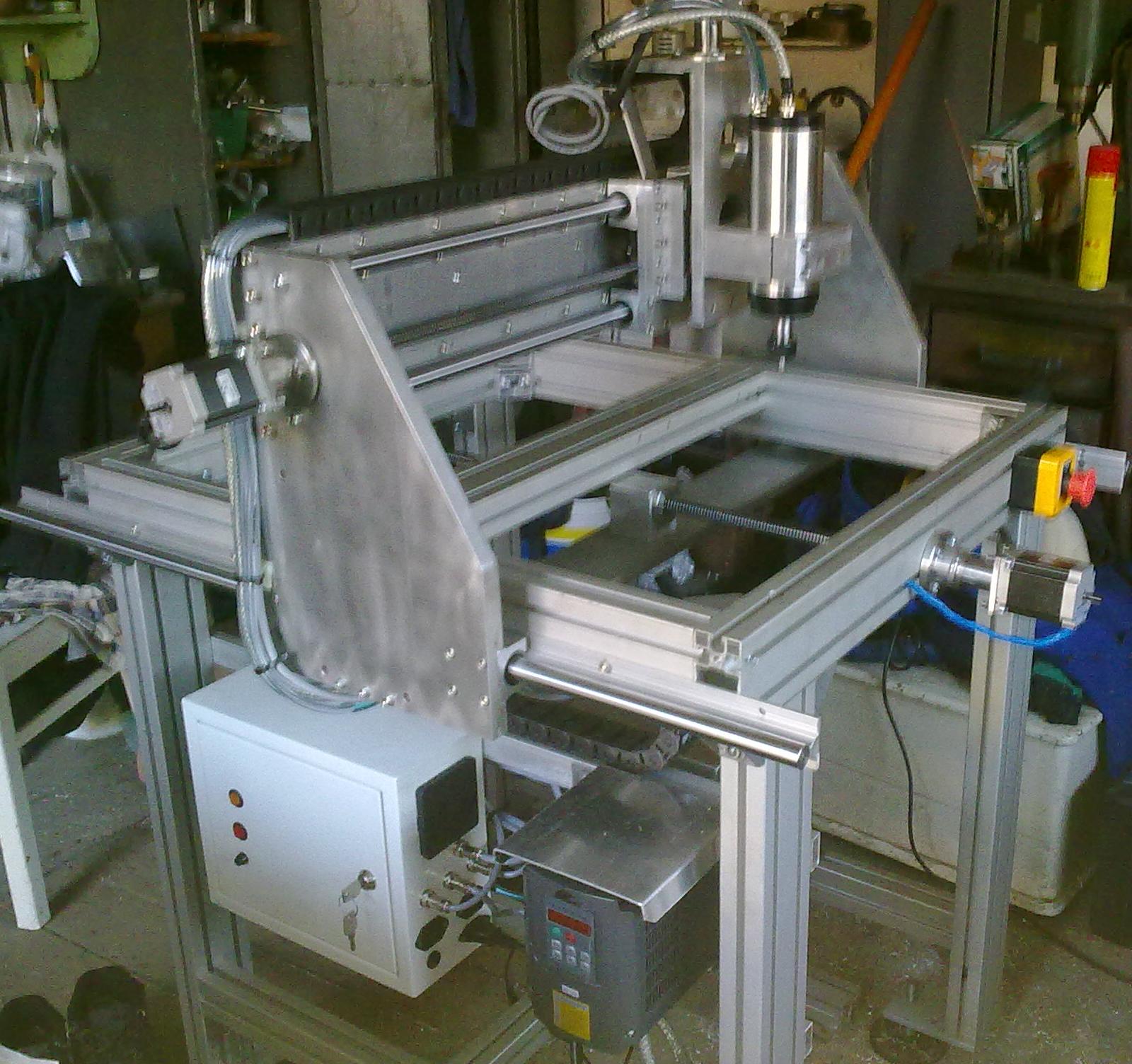
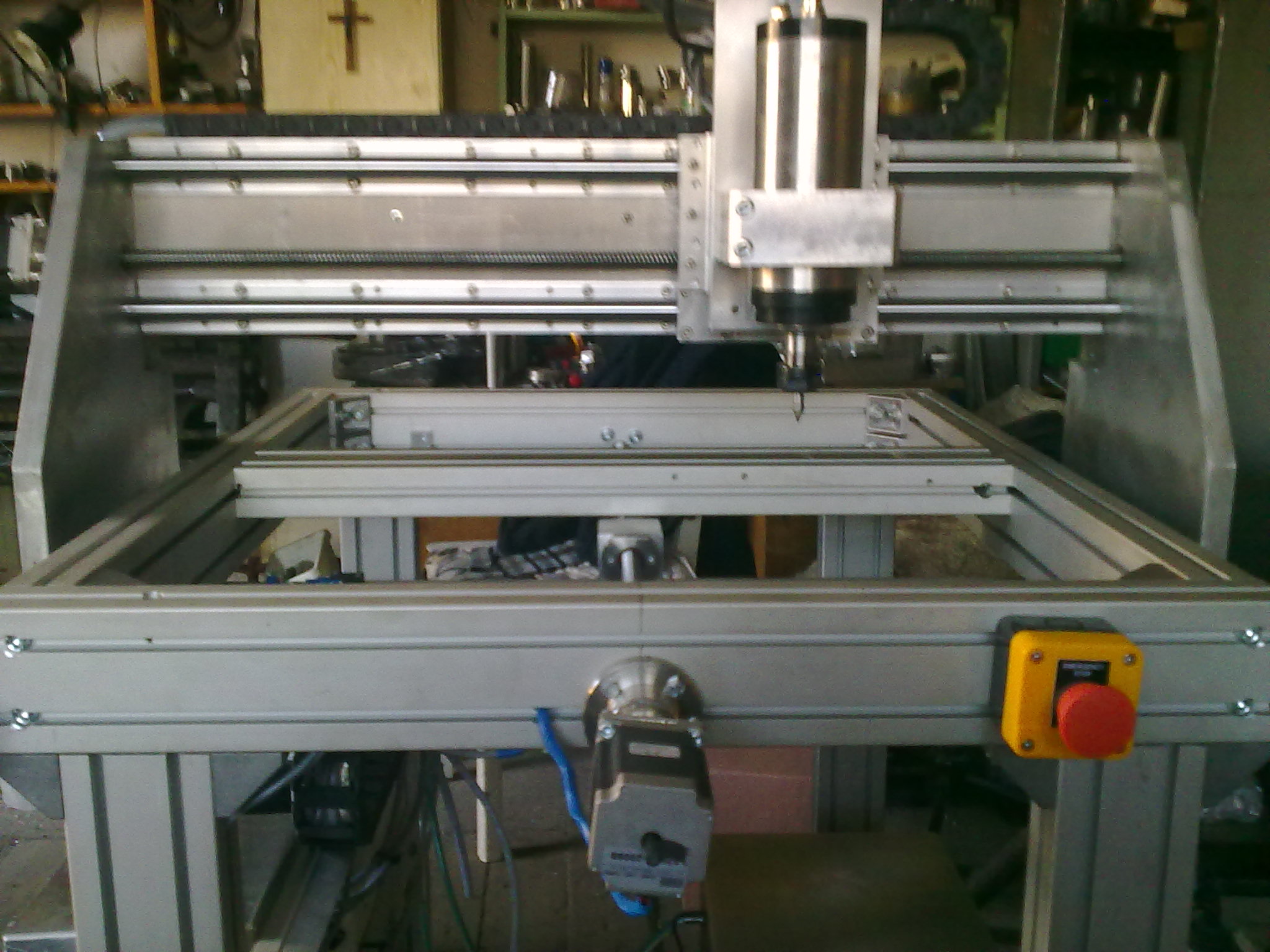
Blat – wodoodporna sklejka 12 [mm] powlekana filmem fenylowym. Z jednej strony gładka, a z drugiej porowata – wykorzystywana w produkcji bodajże podług w naczepach. Jest naprawdę solidna. Jeszcze nie udało mi się jej zamocować – jak na razie prowizorka. Wykorzystuję tę porowatą stronę (teoretycznie antypoślizgowa nawet po oblaniu wodą). Identyczna jak: http://www.fhsmetek.pl/sklejka-antyposlizgowa.html
Nie pomoże to w uzyskaniu dokładności, ale elementy nie ślizgają mi się po całym blacie. Ploter sam sobie odwierci jakąś siatkę otworów do montażu elementów obrabianych. Nastrój poprawił mi temat o XMD 32 i jego krzywym blacie. W zasadzie można powiedzieć, że mój ploter to taka wariacja na temat XMD32

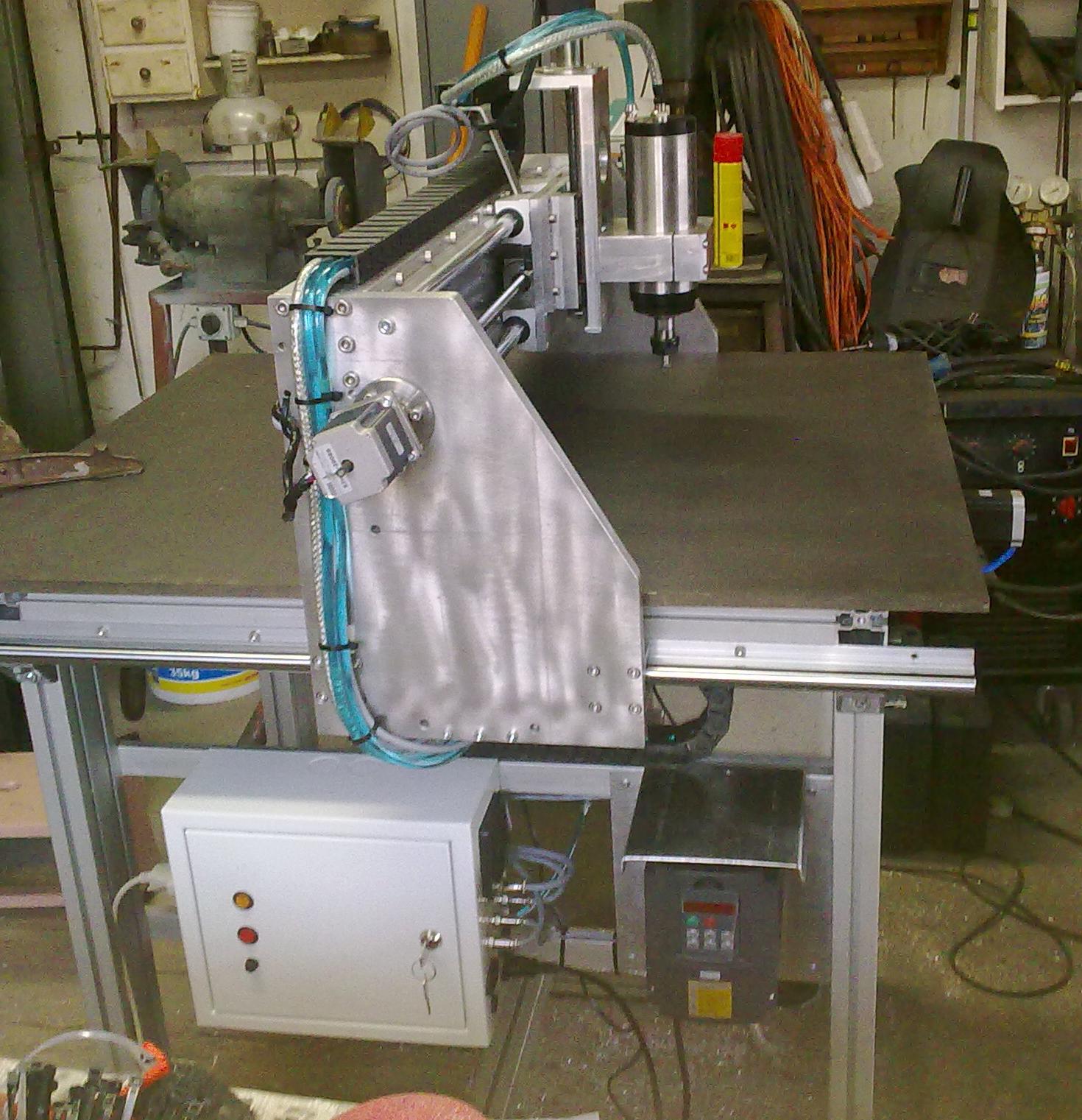
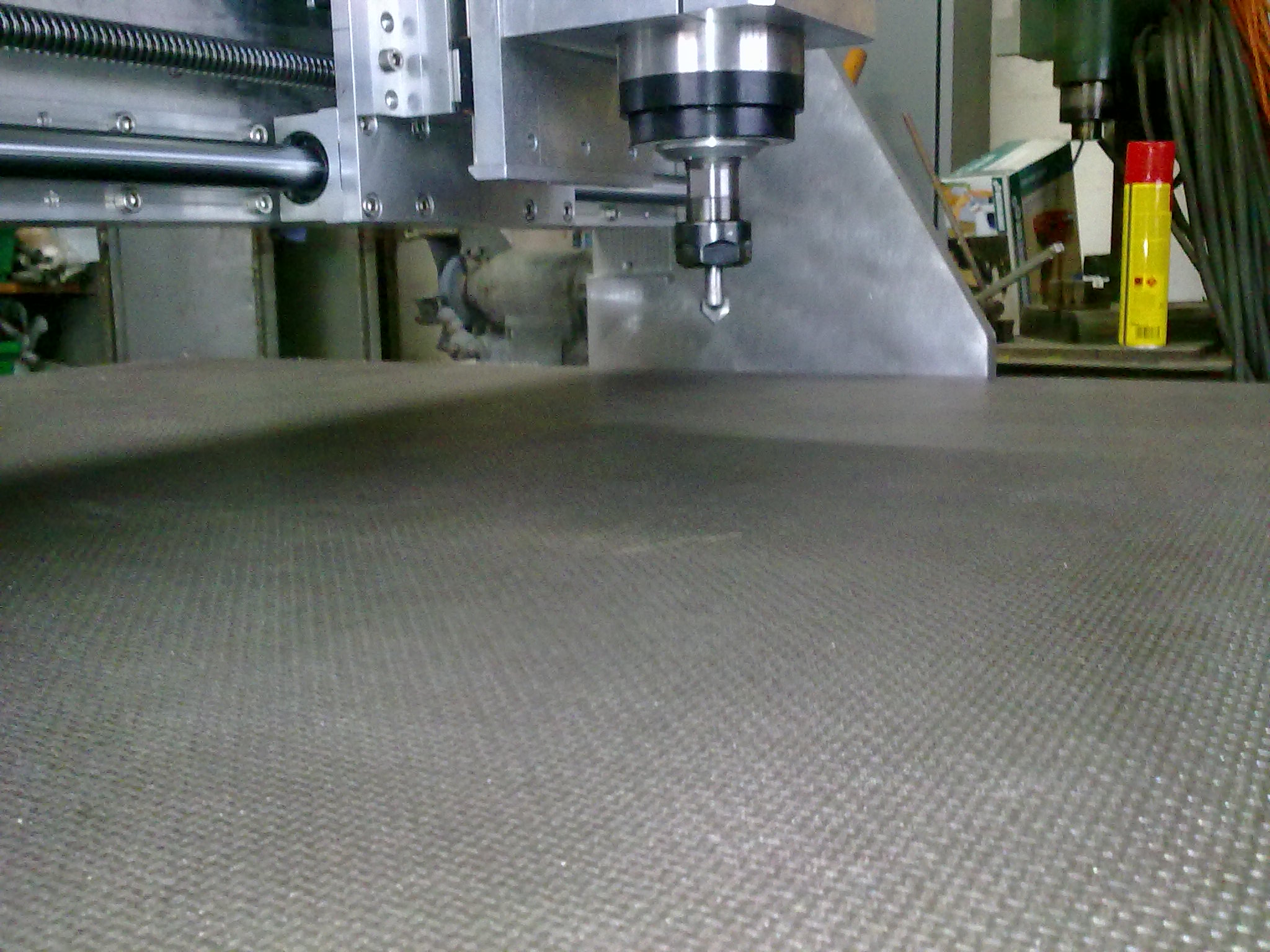
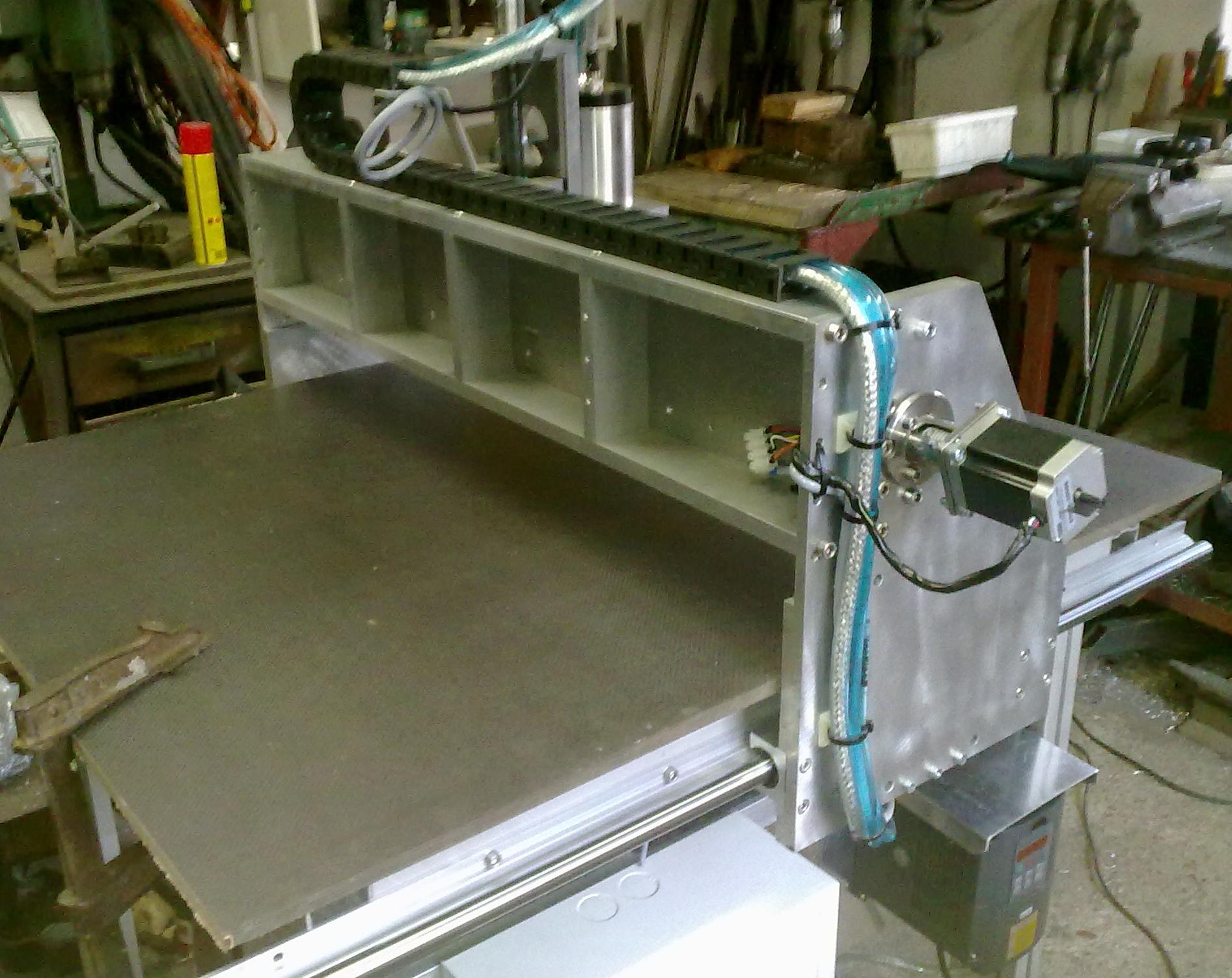
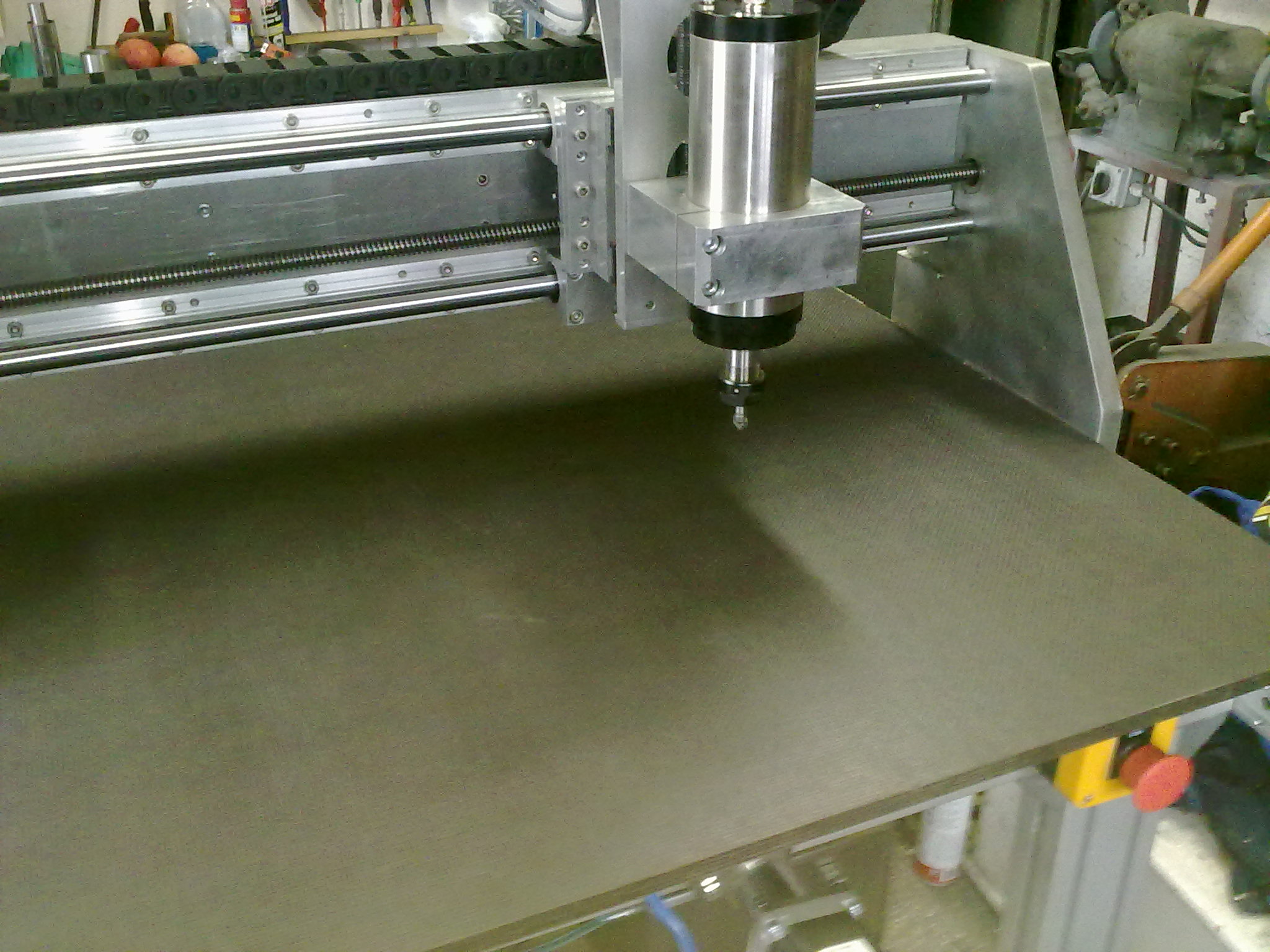
Maszyna nierdzewna

Ploter nie przepracował jeszcze nawet godziny. Prędkości nie są jeszcze dobrane optymalnie, ani też prądy sterowników. Nie udało mi się jeszcze pomierzyć dokładności. Niestety ploter stoi w warsztacie jakieś 120 km od obecnego miejsca zamieszkania. Zima i zimny warsztat również nie sprzyjają dalszym pracom.
Filmiki z pracy (Plusy - kolejny polski film. Minusy - gra aktorska jakaś taka drewniana, scenariusz sztampowy, praca kamery to już w ogóle nieporozumienie - operator był chyba nietrzeźwy, przemiana głównego bohatera nie została uprawdopodobniona psychologicznie).
Youtube zrobił z filmików sieczkę, ale coś tam zawsze widać.
- manualnie:
- grawerowania liter frezem typu V-bit 90* (litery o wysokości 40 [mm]):
Już niebawem druga część pt. „elektronika”, bo ten post jest już za długi. C.d.n.
Jeśli ktoś przeczyta cały post, to chylę przed nim czoła

Pozdrawiam Wszystkich
Jacek