Chciałem przedstawić moją konstrukcję w trochę innej formie niż robią to koledzy na forum a mianowicie dodać od siebie coś więcej niż tylko fotki maszyny - rysunki. Pewnie niektóre osoby będą złe, ale po przemyśleniu zauważą iż w żaden sposób im to nie zaszkodzi.
Można to potraktować jako open source/open hardware. Zamieszczę tyle, ile uważam za stosowne, mam nadzieje że komuś się przydadzą materiały oraz moje uwagi, wskazówki i nie popełni błędów początkującego. Na prośbę mogę zamieścić coś wiecej jesli ktoś będzie zainteresowany a o tym zapomnę. Będe sukcesywnie dopisywał conieco, co nie oznacz iż nagle nie przestanę z takiego bądź innego powodu.
Odrazu zaznaczam iż nie jest to wersja jakaś super ekonomiczna, zastosowane elementy mogą być w innym rozmiarze, niektóre elementy nawet powinny być inne.
Mój wywód jest raczej skierowany do osób które chcą zbudować coś w podobnym stylu samemu ale mają problemy typu np. mają rysunek ale nikt im nie chce tego wykonać. Można się powzorować na niektórych rysunkach i wyciągnąć wnioski. Zaznaczm jednak iż bez podstawowej wiedzy z mechaniki i/lub doświadczenia będzie tak czy tak ciężko - jak każdemu. No chyba że ktoś chce kopiować na żywca...

Założenia
Konstrukcja metalowa, wyżarzana, powierzchnie bazowe frezowane
Pole pracy ok 580x500, w osi Z w zależności od zastosowanego wrzeciona - ok. 180mm
Prowadnice szynowe, rozmiar 20
Śruby kulowe, w osi X i Y - 20x05, w osi Z 16x05
Bloki łożyskujące BK12 oraz BF12
Kolejne części będę dopisywał nie w kolejnych postach, ale w tym jednym, pierwszym.
Z góry przepraszam za błędy, brak interpunkcji, a także merytoryczne powtórzenia lub jakieś braki.
Jeśli są (a pewnie są) jakieś merytoryczne błędy to proszę o zwrócenie uwagi- poprawię.
[ Dodano: 2012-10-23, 19:00 ]
Rama
Element moim zdaniem najbardziej nietrafiony w rezultacie. (Ale negatywnie się zaczyna, co?

Założeniem było wykonać ramę o sprawdzonej konstrukcji, czyli opartą o profile 250x150 lub w bardzo podobnym rozmiarze. Założeniami była ścianka w okolicach 12mm jednak zdobycie takowych profili w Polskich realiach graniczy z cudem. Owszem, zdarzają się, ale jednak do tego trzeba mieć dojście/mieszkać w bardziej przyjaznej okolicy/mieć kontakty albo poprostu kupić całe 12m profila jak już mamy gdzie. Jak dla mnie do najbliższego profilu o ściance 8mm miałem 130km w jedną stronę przy czym musiał bym wziąć właśnie całe 12m.
Już bliżej po cenie złomowej trafił się taki profil o, rzekomo, ściance w okolicach 6 lub 7mm. Jak się okazało - 5mm. Cóż, 100km przejechane z przyczepą to bierzemy, docięte niemal na wymiar, 3,5 stówki, ja niezadowolony z tych 5mm ale cóż.
Elementy:
-profil 250x150x5, ścianka 5mm, im więcej tym lepiej
-profil 140x60x4
-płaskownik 70x10
-ceownik 100x50x6
-blacha 16mm
Wymiary jak na rysunku, stopek (czerwone) w rezultacie wystarczyło po 4 z każdej strony elementu 12.00.01
W elemencie 12.00.02 blachy pod stopki polecam grubsze, chyba że mamy dobrego spawacza (prostopadłości + ściąganie po spawaniu)
Plik “wyżarzanie” jak sama nazwa wskazuje to rysunki do zapytania o wyżarzanie. Tylko najważniejsze informacje - gabaryty oraz najgrubszy element - co jest najczęściej wymagane.
Plik “frezowanie_1” to jak sama nazwa wskazuje rysunki do frezowania. Najważniejsze wymiary niezbędne, oczywiście w granicach rozsądku, na 12.00.01 rowek na głębokość 3mm jako wymiar główny. Nie ma podanego wymiaru miedzy blachą pod stopkę a rowkiem pod prowadnice - w zakładzie frezującym powinni ustawić tak żeby jak najmniej zebrać (zabielić) a żeby było dobrze.
Otwory - tylko niezbędne do ustawienia geometri
Plik “frezowanie_2” to to samo tylko z otworami które po wycenie stwierdziłem że lepiej jak na maszynie to wykonają niż ja na wiertarce ręcznej. Te same rysunki które powinny pozostać takie same żeby była jasność ile dopłacamy jeśli robimy taki manewr. Rysunki odpowiednio 01->05 i 02->06. Polecam robić od razu otwory pod prowadnice, aczkolwiek to kosztuje. Jak kto woli, ja się swoje namęczyłem.
Jedna sprawa.
Otrzymanie wyceny zajmuje czas, sporo czasu, pare telefonów, czas na zrobienie rysunku.
W opisywanym przypadku jest to rysunek elementu, który nie obrobi byle zakład mechaniczny.
Projektując ramę takich gabarytów musimy się zorientować gdzie w okolicy (lub nie okolicy a dalej) obrobią to, najlepiej żeby mieć na oku kilka zakładów. W moim przypadku podczas projektowania orientowałem się gdzie mogę wyżarzyć i ofrezować. Jak wiedziałem na czym stoje to wtedy wziąłem się za wykonanie.
Rama wyżarzana gdzie indziej, frezowana gdzie indziej, warunek to dobry rysunek. Nie będe tu się rozwodził co trzeba a co nie, sam popełniłem pewnie wiele błędów rysunkowych ale skoro udało się zlecić, i to w fabryce, to znaczy że rysunki były wystarczające. Oczywiście jako osoba prywatna trzeba ponudzić - wysłać zapytanie, odczekać 2, 3 dni i dzwonić. Oczywiście w większym zakładzie nasze zapytanie zostanie olane/zapomniane w dziale handlowym/obsługi klienta dlatego dzwonimy do wybranego zakładu/fabryki i prosimy numer do technologa. On twierdzi że nic nie dostał a my twierdzimy że zostało wysłane i prosimy także mail do niego i wysyłamy. Albo poprostu on sam sobie “wyciąga” z działu handlowego. Najlepiej wysyłać do technologa i również do działu handlowego (czasem jest to niezbędne) w tym samym mailu i mamy spokój. Oczywiście są lepsze sposoby na jeszcze szybsze i sprawniejsze załatwianie sprawy...ale czas to pieniądz i to powinno wystarczyć amatorom budowy cnc

Odrazu zaznaczam, powtarzam, co niezbędne. Niezbędne jak materiał na maszyne tak niezbędne to: dobry rysunek. Taki, aby wystarczył na bezproblemowe wykonanie zlecenia.
Rysunek zgodny z rzeczywistością, a nie gdzieś, coś dospawane, czego nie było na rysunku a uniemożliwia obróbkę.
Ogólnie jeśli ktoś nie zna książki “Rysunek Techniczny Maszynowy” T. Dobrzańskiego to będzie mu cięzko... Nieraz w dziale “giełda” pojawia się zlecenie wykonania elementu gdzie otwór jest zwymiarowany do obwodu a nie środka, jakieś dziwne tolerancje, wymiary do osi która fizycznie nie istnieje i trzeba by się nagimnastykować żeby wyznaczyć od niej jakąś baze co kończy się często w rezultacie brakiem materiału, itp. dlatego z takimi rysunkami lepiej nie zawracać głowy poważniejszym zakładom. No chyba że się jest gotowym zapłacić 5x więcej niż przy normalnym rysunku.
Jeśli ktoś nie pracował jeszcze albo się po prostu w tym nie orientuje to dam bardzo prosty przykład: Rysunki oraz projekty dla studentów z mechaniki kosztują od 40zł (za prosty rysunek) w górę. Nietypowy projekt - za parę obliczeń i ze dwa rysunki wykonawcze i jakieś tam złożenie ceny idą od 100zł w górę. Projekty które są zgrubne, nie dokładne, nie ma co się przejmować kolizjami albo że coś nie gra.
Tak więc trzeba się zastanowić czy czasem nie lepiej zlecić komuś, choćby z forum, wykonanie rysunku. Wiedza kosztuje i jeśli nie umiemy rysować, nie znamy podstaw a chcemy wykonać coś solidnego to do kosztów trzeba doliczyć te “dodatkowe sprawy”. Jak komuś ciężko zrozumieć to z tym jest np. jak ze spawaniem - jak nie umiemy spawać to musimy znaleźć spawacza i mu zapłacić. Chyba że wolimy jak to niektórym osobom na forum się zdarza - szukać zleceniobiorcy tego samego elementu przez pół roku. Ile miedzy czasie się odzwonił, ojeździł, pewnie też w niejednym zakładzie usłyszał conieco na temat swoich błędów rysunkowych i coś tam poprawił.....ten wie.
Czasem bardziej opłacalnym jest zlecenie komuś, kto jest zorientowany, załatwienie paru spraw za nas. Faktycznie, to kosztuje, ale ile czasu nas by to kosztowało? Często zapewne wiele więcej.
A przed nami przecież jeszcze daleka droga do ukończenia budowy...
Wracając do samej konstrukcji ramy- mogła by być wykonana z mniejszych profili lub zaprojektowana z blach wycinanych na laserze. Droższa (o wiele więcej niż cena złomu) opcja ale mniej problemu z docinaniem do spawania. Mogła by także być wykonana z dużo grubszych profili. Profil 250x150x5 jest zbyt cienki. Tak czy tak obydwa elementy ramy ważą ok 240kg.
Na poparcie dokumentacji że się udało, wprawdzie jest w innym temacie ale nikt skoro to ma pomóc to na pewno skakanie po tematach pomocne nie będzie.
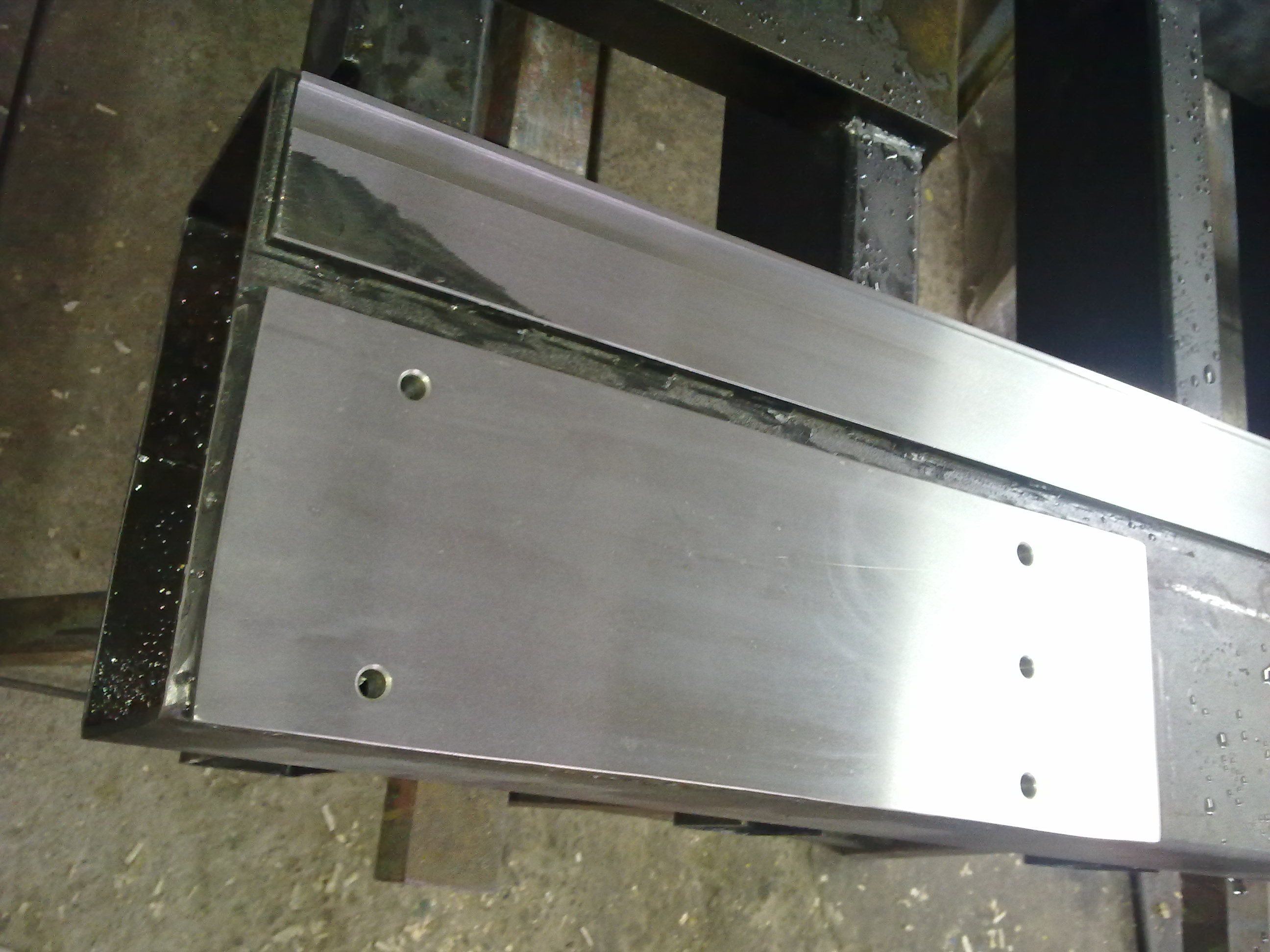
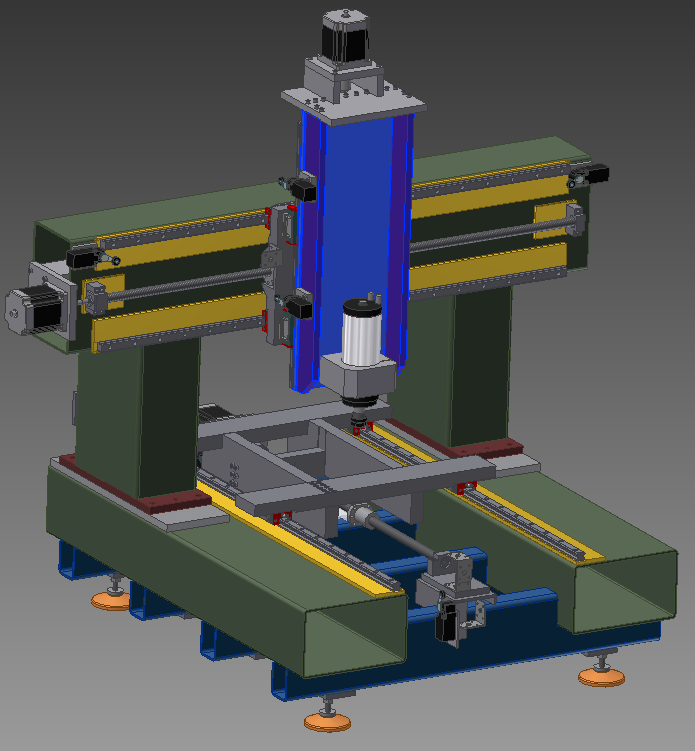
[ Dodano: 2012-10-24, 17:18 ]
Krzyżak
Element ten może być wykonany zarówno jako skręcany jak i z jednego, litego kawałka materiału. Zalety skręcanego to niewątpliwie łatwość (względna) wykonania i montażu. W przypadku jednolitego kawałka materiału musimy przede wszystkim MIEĆ ten materiał (po prostu mało który zakład ma coś takiego). U mnie docelowo miał być półfabrykat grubości 85mm. Skończyło się tym że miły Pan z jednej firmy której zależało znalazł mi najpierw taki 60mm - nie wystarczyło, a następnie 80mm - to już wystarczyło.
Pozostałą kwestia materiału - aluminium czy stal.
Stal:
-lepiej tłumi drgania
-tańsza od aluminium
-cieższe od aluminium
Aluminium:
-gorzej tłumi drgania
-droższe
-lżejsze
-prawdopodobnie obróbka była by tańsza (nie wiem, poprawcie jeśli się mylę)
Dlaczego wybór pał na aluminium? Ze względów praktycznych czyli przede wszystkim lepsze tłumienie drgań. Do tego tańsze. Nie znam dokładnie ceny materiału ale razem z materiałem na ten prowizoryczny stolik wyszło mnie 615zł (ok. 110kg, z czego blacha 305x295x80 - ok 56,5kg.). Do tego mogę napisać iż większa, prawie trzykrotnie, masa stali ma większą bezwładność (nie wiem czy to nie jest powód sam w sobie lepszego tłumienia drgań)a co za tym idzie dodatkowo ciężej jest wymusić na większej masie drgania.
Ze dwie foty materiału:
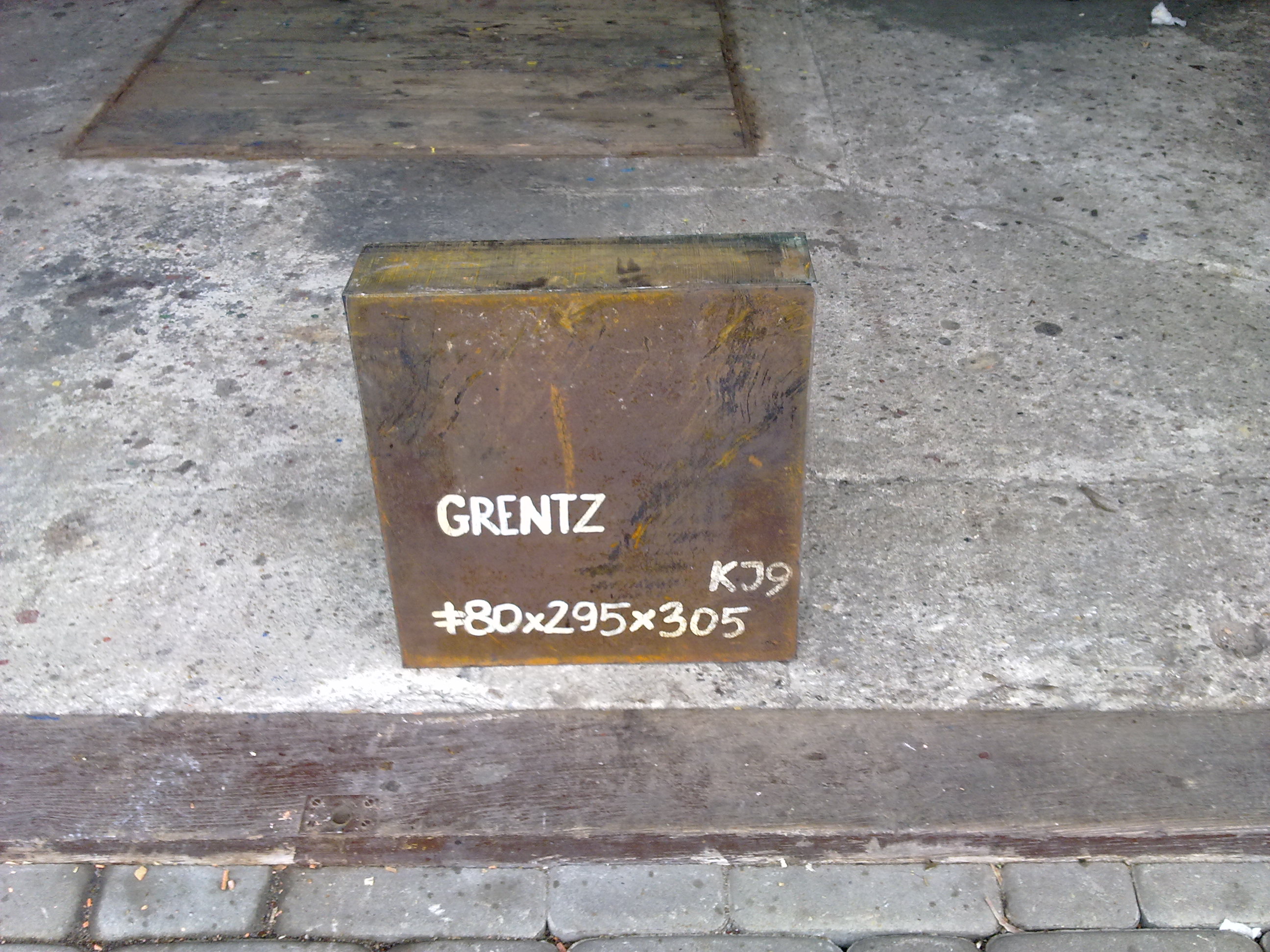
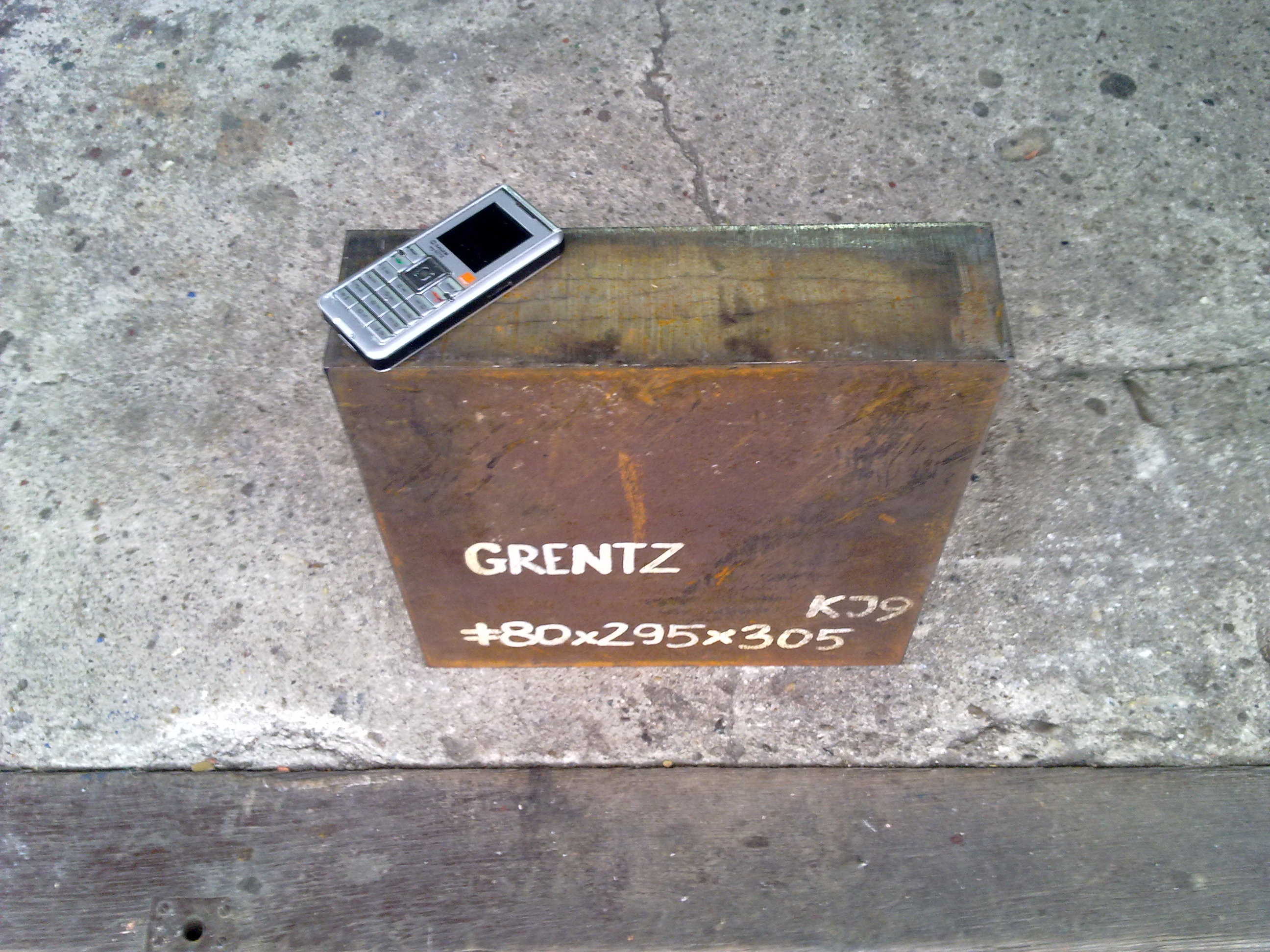
Dodatkową trudnością jest zachowanie poprawnej geometrii detalu. W moim przypadku po obróbce zmierzona prostopadłość jednej strony względem drugiej to 0,02.
(
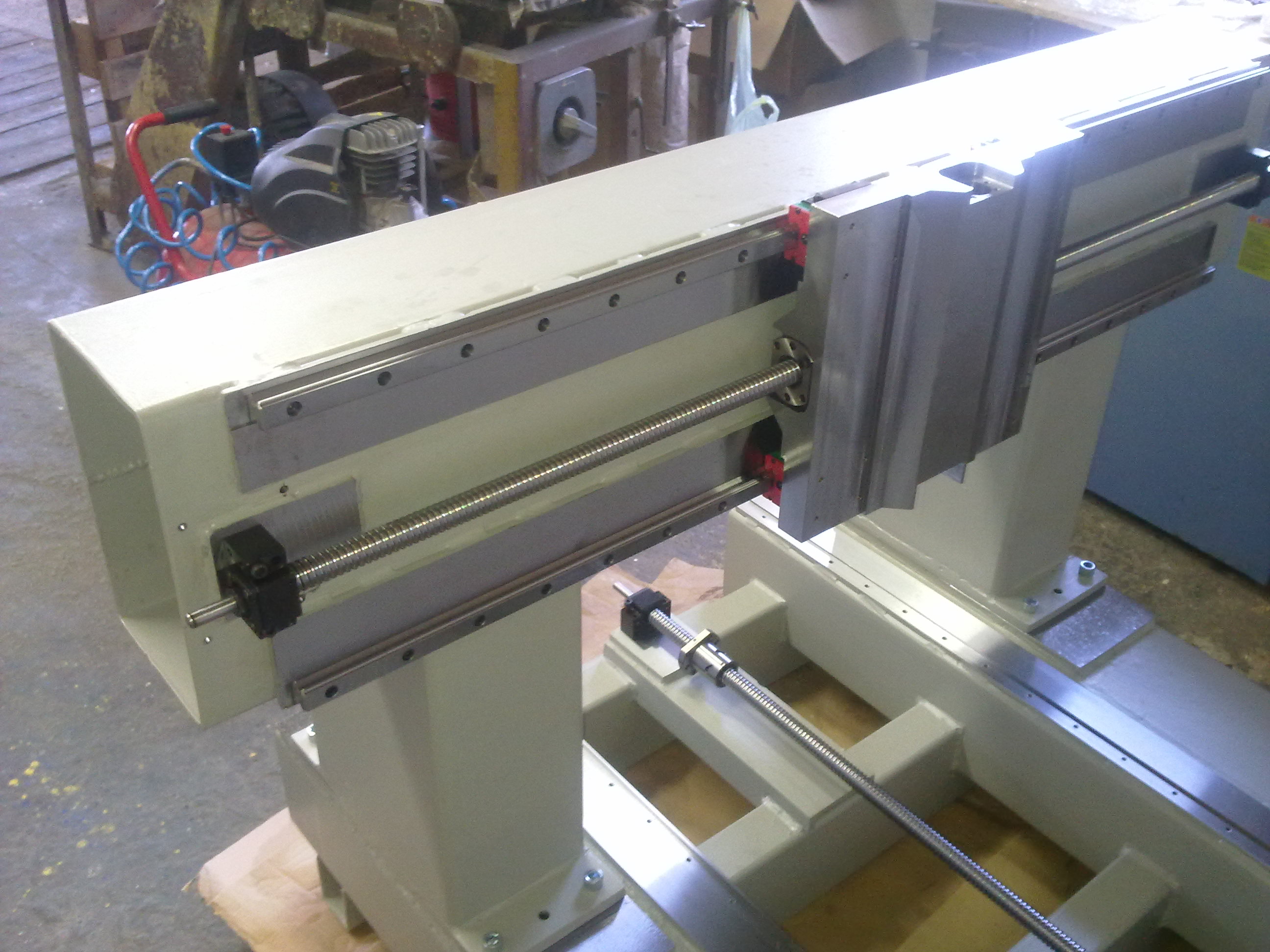
Nie wiem czy to dużo, czy to mało ale myślę że powinienem być zadowolony. Wiem jedno - byle jaki zakład na byle jakiej maszynie tego nie zrobi. Dlatego przestrzegam przed udaniem się do pobliskiego zakładu mechanicznego co to ma jedną frezarkę i jedną tokarkę. Ja się do takiego udałem żeby mi wykonali stolik i to był błąd. Ale o tym w następnej części.
Projekt krzyżaka wykonany oczywiście w 3D, przerzucony na 2D. Dwa arkusze A3 ze względu na praktyczność. W rysunkach jest pewna nieścisłość, można powiedzieć że nawet błąd - wybranie z idealnymi krawedziami. To wynikało z ustnego umówienia się z frezerem jak i czym to zrobi. Po prostu nie wiedziałem jakim narzędziem będzie robił. Jak już miałem rysunek mówił coś o głowiczce fi63 ale w rezultacie zrobił frezem coś około fi10.
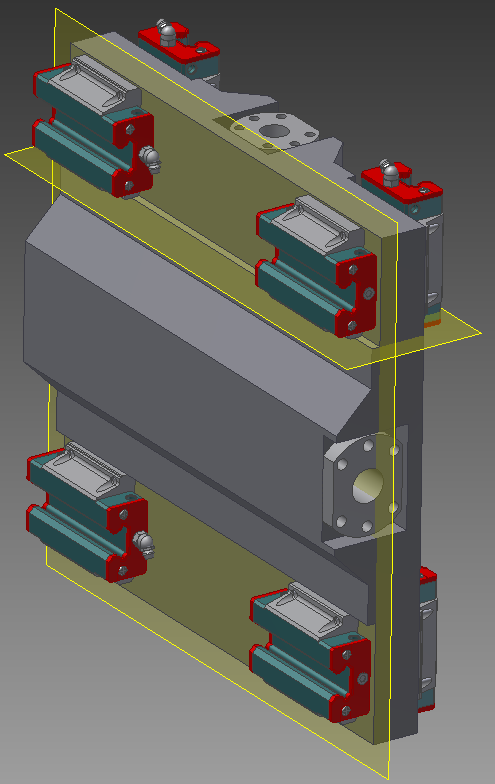
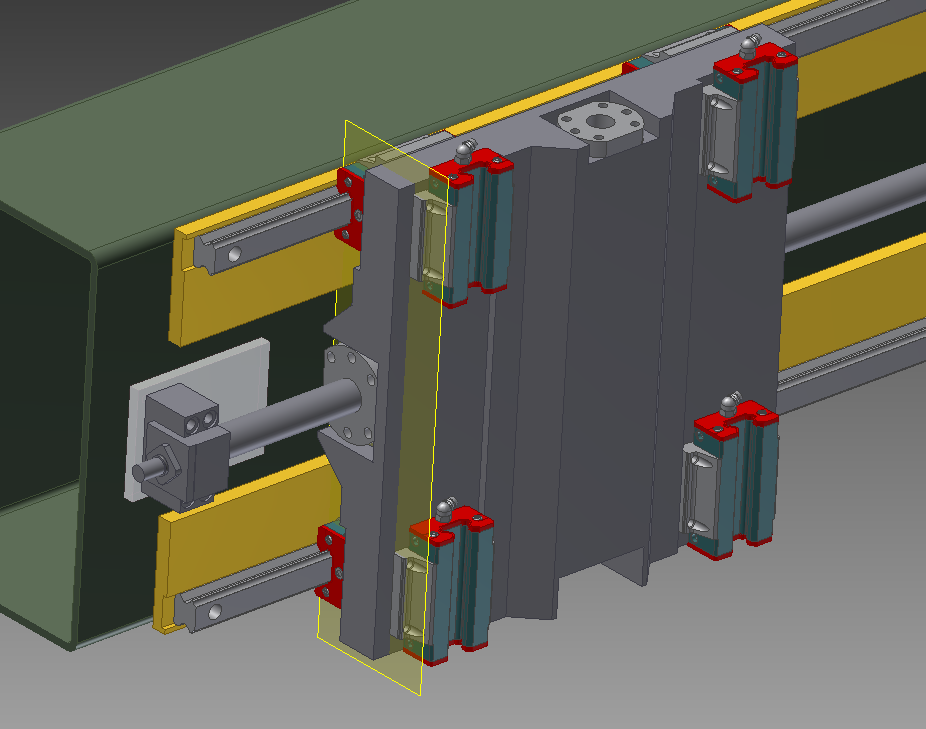
Wykonanie całości trwało stosunkowo długo, nie potrafię powiedzieć ile ale coś o obróbce. Najpierw splanowanie całości z każdej strony + chyba szlifowanie. Potem wiercenie dwóch otworów przez całą długość czyli 305 oraz 295. (Z tego co wiem to z dwóch stron) Na porządnej wiertarce pionowej. Następnie wykonanie wszystkich płaszczyzn, odsadzeń itd. Na koniec napunktowanie pod otwory pod śruby. Otwory pod śruby pod wózki robił frezer, sam robiłem otwory (pod wózki) oraz trasowanie +otwory pod śruby mocujące nakrętki. Jak coniektórzy już wyczytali zdarzyło mi się złamać gwintownik w jednym z otworów mocujących wózek (wg. prawa Murphy’ego - spieprzy się w najważniejszym momencie). Usunięcie elektrodrążarką. Na marginesie dodam iż drugi gwintownik (z dwóch) jaki złamałem to także w rzeczonym krzyżaku, ale na szczęście w mniej znaczącym otworze - otworze mocującym materiał współpracujący z krańcówką.
Co więcej mogę napisać o tym elemencie... grubość w najcieńszym punkcie(punktach) miedzy obydwoma stronami to 28mm bez paru dych, grubość całości to 80mm bez jednej czy tam dwóch dych (na szczęście grubość tej blachy 80mm była ponad 80mm). Zamontowanie na bramie nie należało do przyjemności - najpierw wózki do krzyżaka, potem szyny w wózki i na koniec całość we dwie osoby przykładały do rowków na bramie. Trzecia osoba mimo oporów płci pięknej do wszelkich mechanicznych rzeczy oraz smaru przykręcała śrubki do szyn. Na szczęście wszystko było na tyle dobrze spasowane (rowki w tolerancji jakoś takiej, jak na rysunkach) że weszło od kopa i spasowało.
Z drugiej współpracującej strony czyli osi Z także nie ma większych problemów - płyta osi Z frezowana i szlifowana wraz z zastrzałami - porusza się bez żadnych problemów. Powieszona oś Z ważąca ok 25kg na większości długości zjeżdrza bez większego problemu w dół, tylko na samym końcu żeby zjechałą trzeba odrobiny siły, czemu się nie dziwie skoro odsadzenie pod blok było tylko frezowane, dodatkowo bazowanie każdej osi jest nie do otworu tylko do płaszczyzn.
Bazowanie do płaszczyzny a nie osi - mam na myśli że blok łożyskujący dociśnięty jest mimo wszystko do płaszczyzny prostopadłej do płaszczyzny mocowania nakrętki co nie pozwala na samoistne ustawienie bloku łożyskującego względem nakrętki w pozycji wykazującej jak najmniejsze opory. Nie ma to jakiegoś większego znaczenia gdyż odkształcenia jakie pojawiają się są nadal w zakresie spreżystości więc nie wpływa to zasadniczo na pracę układu. Jeśli się mylę proszę profesjonalistów o poprawienie. Przykładowo w konstrukcji Piotrajub sprzed lat można zauważyć iż bloki łożyskujące w osiach są bazowane nie do płaszczyzny prostopadłej do płaszczyzny mocowania nakrętki ale do osi (blok dokręcany po ustaleniu pozycji). Nakrętka natomiast nie wiem (nie pamietam albo się nie wpatrzyłem) jak jest bazowana - czy do otworu w supporcie/stole czy do płaszczyzny na kołnierzu - chyba to nie robi większego znaczenia skoro blok łożyskujący ma te minimum ruchu poprzecznego przed dokręceniem.
Wyszło coś takiego:
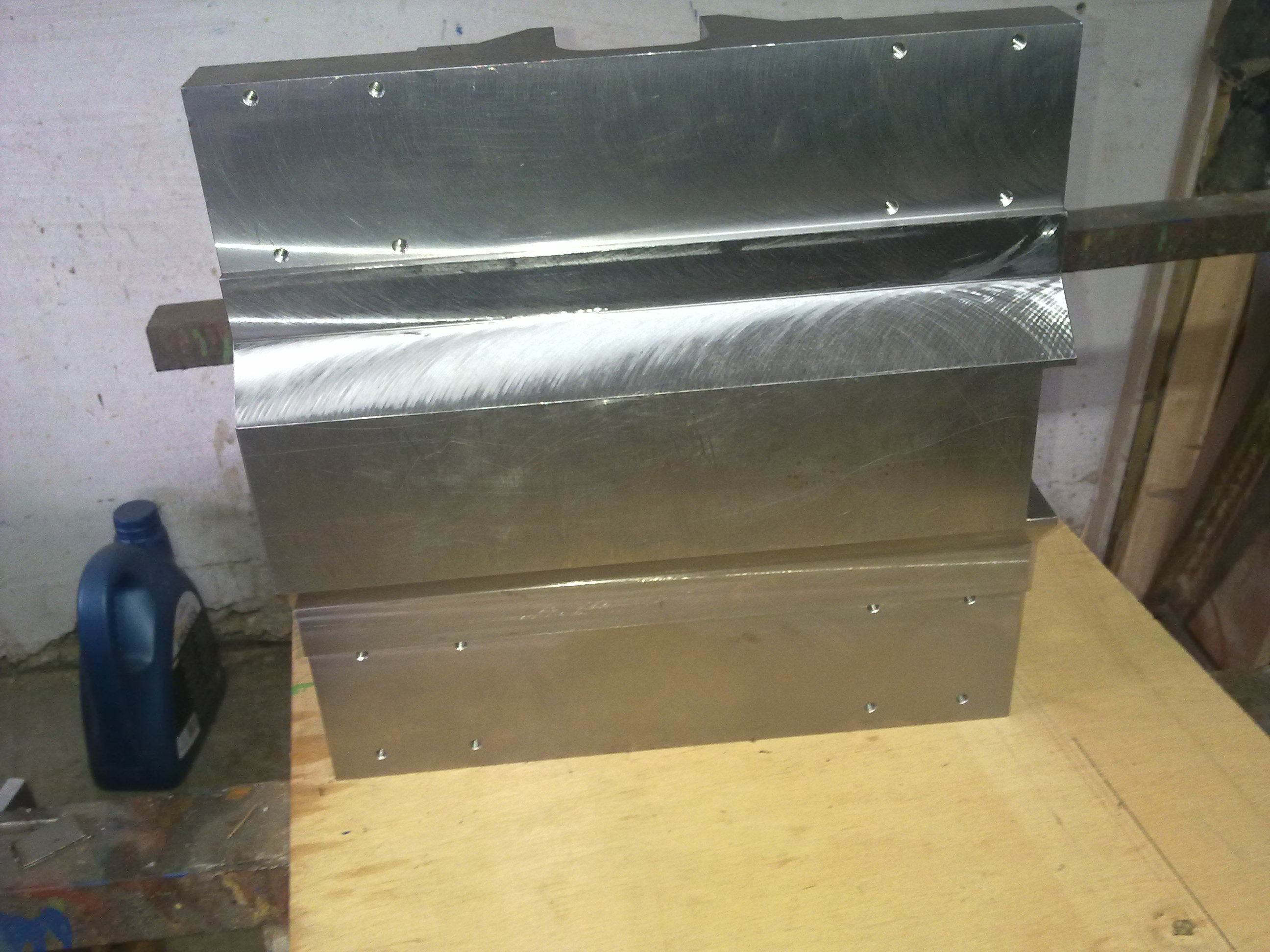
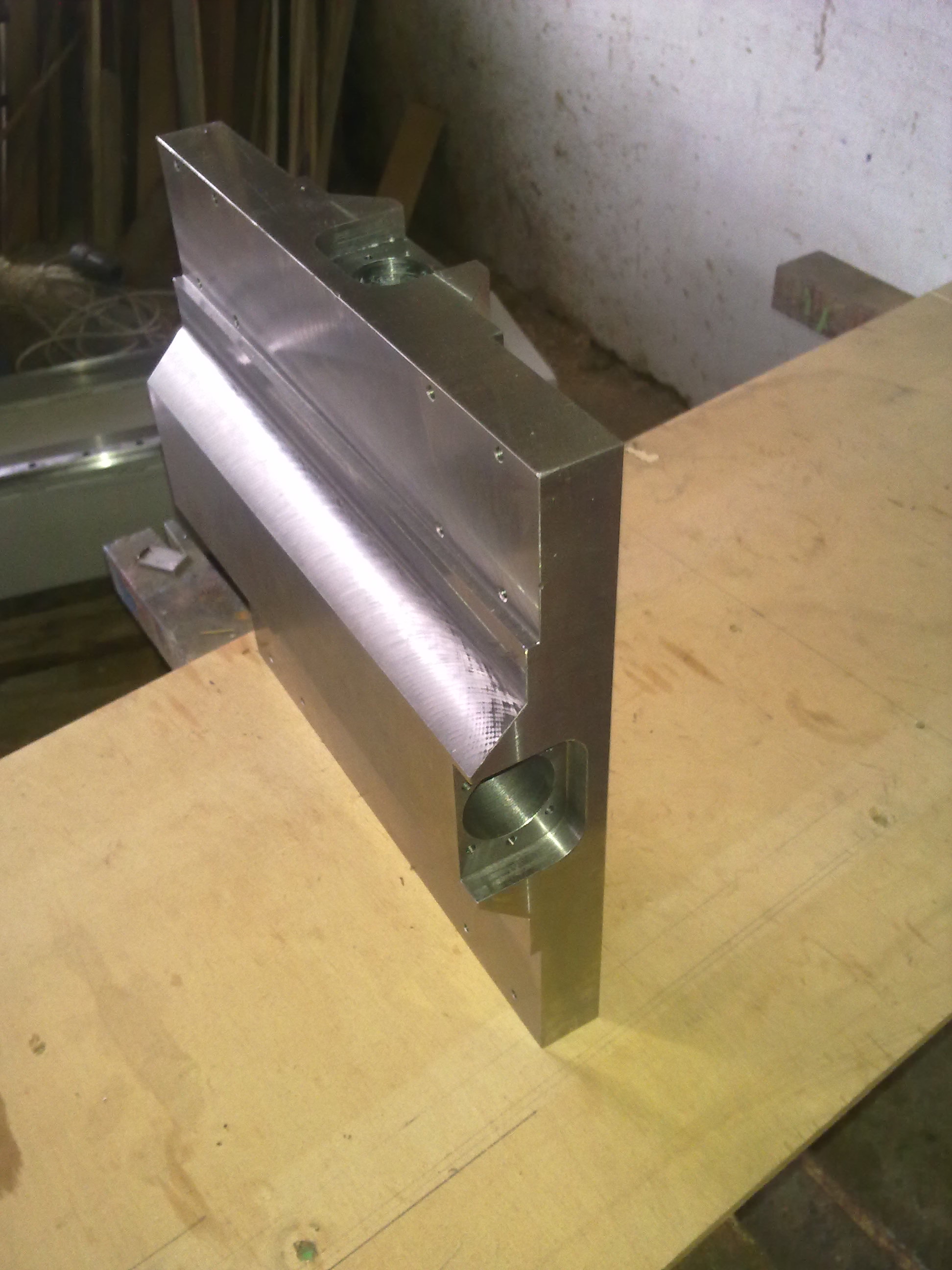
Rysunki w załącznikach:
Krzyżak_v2_wykonawczy_1
Krzyżak_v2_wykonawczy_2
[ Dodano: 2012-11-13, 18:49 ]
Oś Z
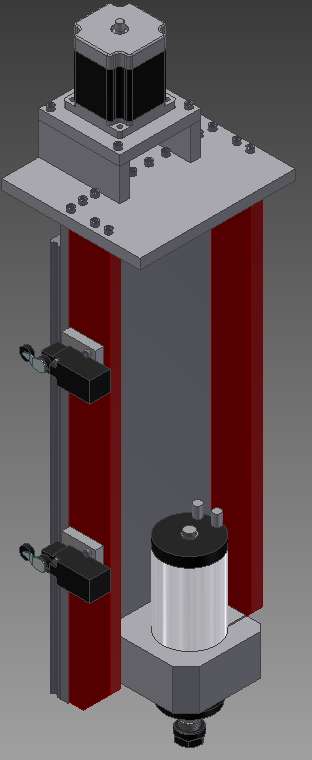
Element w mojej konstrukcji który pierwotnie miał być z czegokolwiek czyli blachy 15mm. Skończyło się tym, iż z blachy 15mm pozostały tylko zastrzały. Blacha miała mieć docelowo coś ok 13-14mm ale to 15mm wyszło z blachy 20mm specjalnie zakupionej. Mam na myśli tutaj o lekkiego bananka do tego spore wżery. Dobrze się stało że zakupiłem specjalnie blachę 20mm. Uwagi praktyczne. Pojechałem od razu po odrzuceniu starej blachy do jakiegoś zakładu, wycieli mi blaszkę 20mm na wymiar. Żeby było szybciej wpadliśmy na pomysł z Panami pachołkami żeby wrzucić ją do kałuży. Nie pomyśleliśmy że może ją rzucić. Dobrze że spawacz nas odwiódł od tego. Niby się wie, niby zwraca uwagę, niby pamięta o takich szczegółach a tu takie pomysły przychodzą człowiekowi do głowy

Finalnie blacha frezowana, szlifowana, pogłębienia pod bloki łożyskujące tylko frezowane.
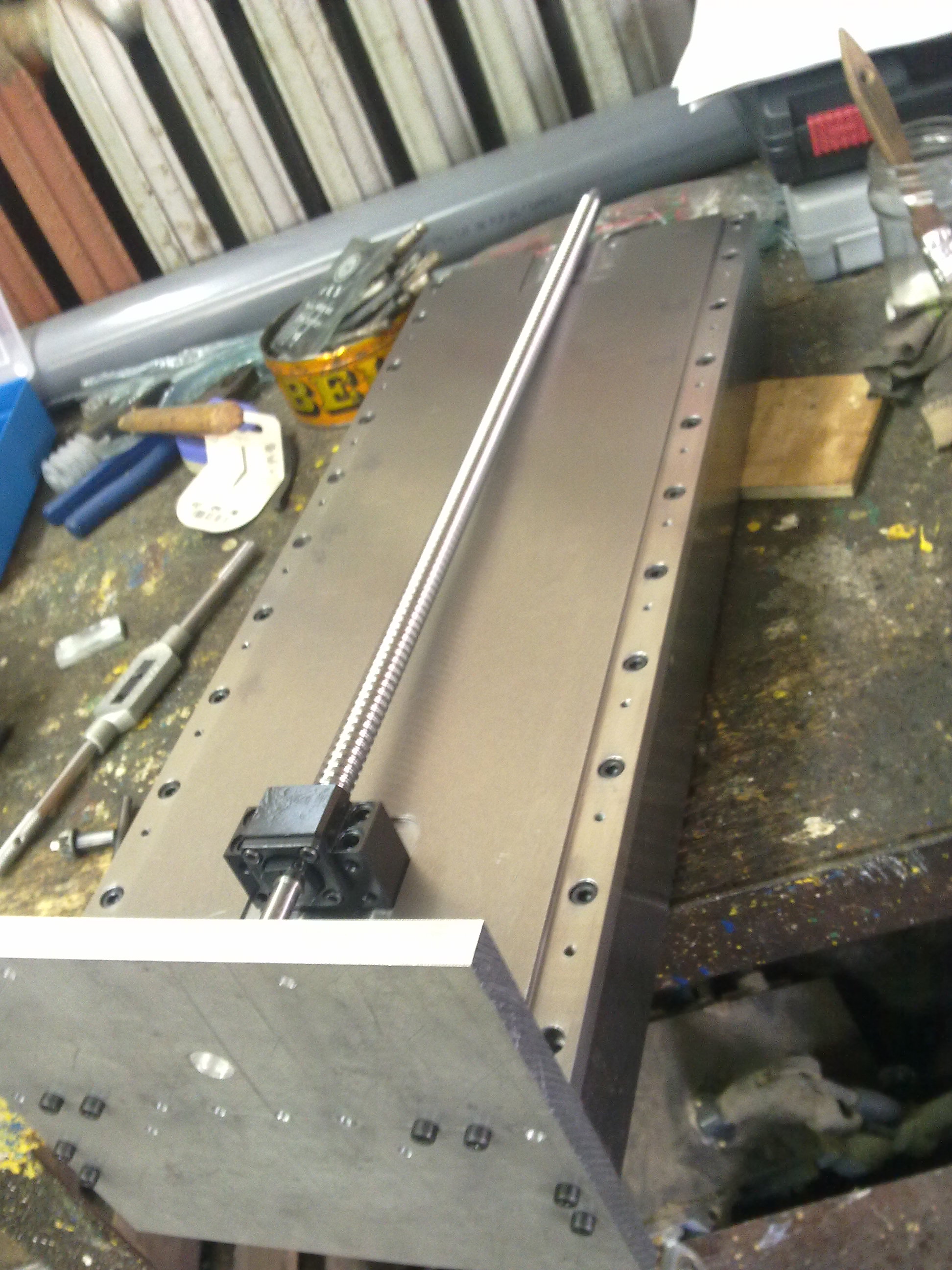
Po przyłożeniu szyn - minimalna, ledwie zauważalna kołyska. Nie wiem czemu. Po przykręceniu zastrzałów od strony frontowej - kołyska niewyczuwalna. Wnioskuję że krzywe zarówno szyny jak i blacha osi Z. Wnioskuję też iż dokręcenie do szlifowanych zastrzałów czołowo sprawiło że minimalna krzywizna blachy (mimo szlifowania) się przeprostowała, do tego przykręcenie szyn sprawiło iż ten element jest najbardziej prostym i sztywnym z całej konstrukcji (no, może łącznie z krzyżakiem).
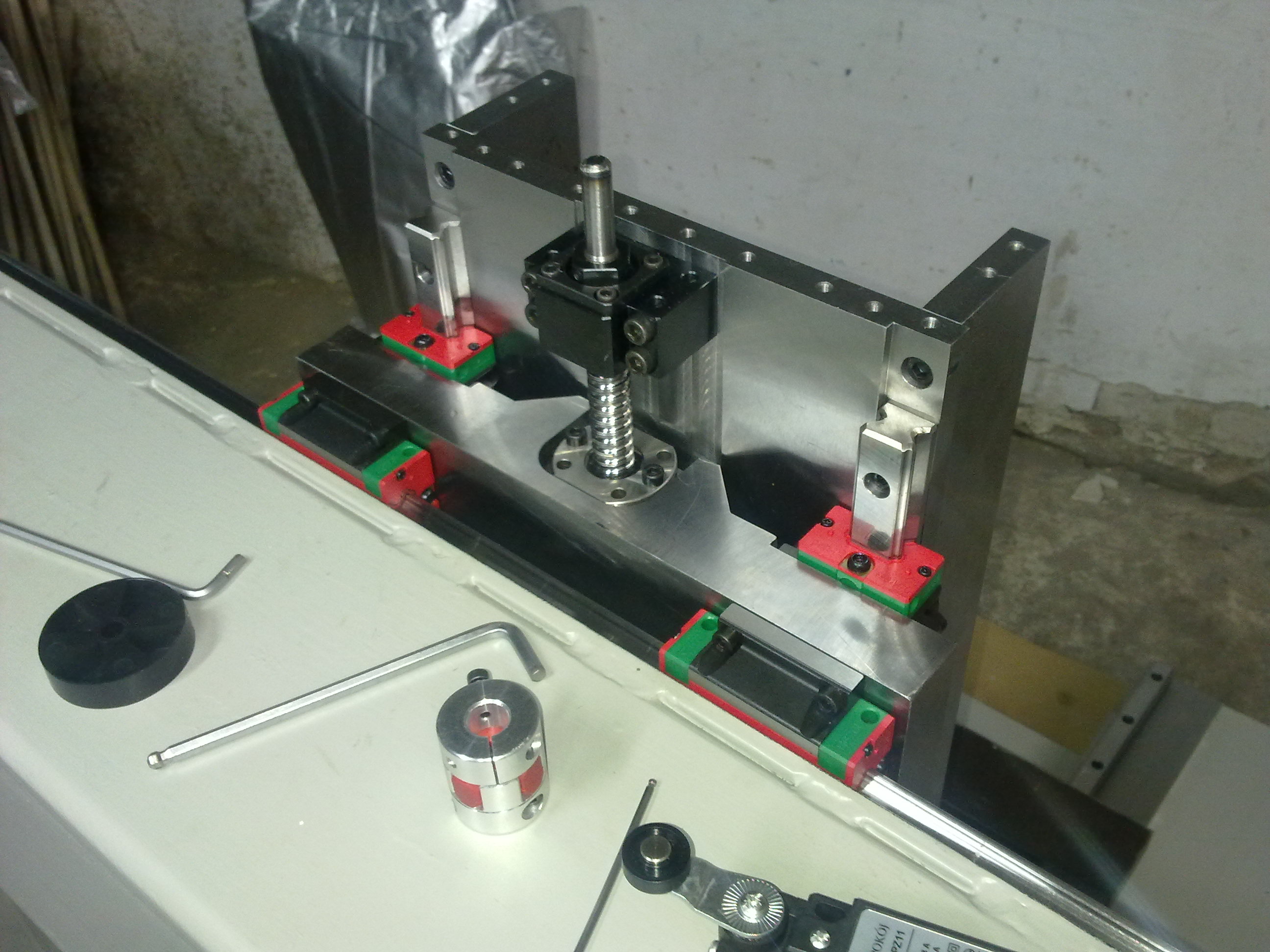
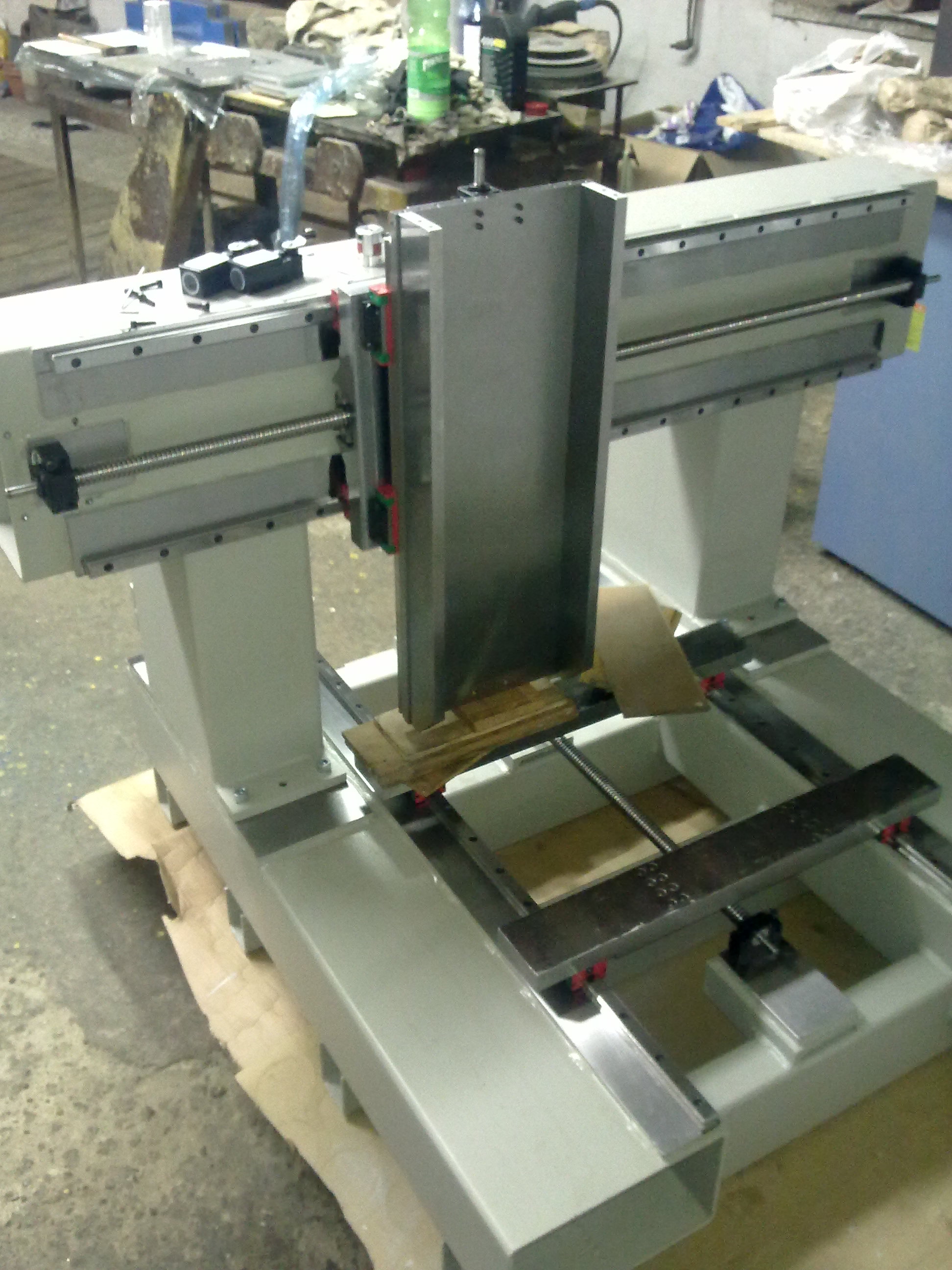
To chyba tyle o tym zespole, polecam nie tylko frezowanie ale i szlifowanie, oczywiście odpowiednio grube wymiarowo elementy. Można powiedzieć iż jeśli powierzchnia pod bloki łozyskujące nie była by poniżej powierzchni materiału to może i ona była by oszlifowana. Co oczywiście na plus dla konstrukcji. Ale kto to wiedział projektując krzyżak.... tzn. kto projektował wcześniej to wie....
