Generalnie frezarka miałaby w 80% służyć do wycinania w laminacie szklanym, w 15% w sklejkach, 4% w piankach, a dopiero później ewentualnie w alu [tego raczej nie biorę w założeniach pod uwagę].
Tak na prawdę to Z mogło by równie dobrze wynosić 100mm.
Chodzi o to że obrabiane elementy mają zazwyczaj wysokość około 200mm i są stożkami/walcami, na boku których trzeba wycinać otwory, więc założyłem, że tak będzie po prostu wygodniej i nieco bardziej uniwersalnie przy obróbce pianki.
Otwory te są rozstawione do około 1500mm, więc albo musiałbym zrobić maszynkę 500x500 i każdy obrabiany element przesuwać do robienia każdego otworu, albo zrobić maszynkę o Y lub X w okolicach tych 1500mm.
Brama musi być ruchoma, bo obrabiane elementy mają w okolicach 6-10metrów długości [oczywiście obrabiany jest jedynie odcinek ~1500].
Jako że Z i Y mam narzucone z góry to stoję przed wyborem jaki X wybrać...
Jedna opcja to dość krótki X - około 500-600 mm by mi w zupełności wystarczyło,
Druga to 2,5 metra tak żeby mieć możliwość wrzucenia kilku obrabianych elementów na raz i jazda jednym programem, albo całej sklejki 125x250.
Przy pierwszej opcji myślałem nad ramą podobną do tej:
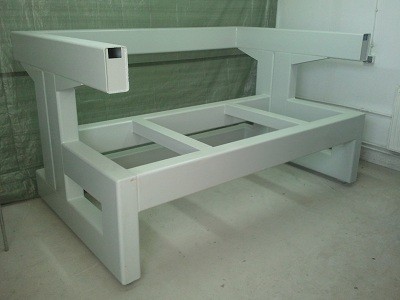
Nie ukrywam że taka konstrukcja bardzo by mi ułatwiła pracę z długimi elementami i mocowanie obrabianych elementów do stołu, które mógłbym po prostu wsunąć pod belki prowadnic X'a.
Przednią furkę w takim wypadku dałbym raczej zaślepioną, żeby dodatkowo usztywnić ramkę.
Druga opcja to konstrukcja podobna do tej ze stajni Seemana:
Jak widać w obu ramach, podniesione są boki, a nie belka na podporach.
Od samego początku taka konstrukcja wydawała mi się sztywniejsza i tego założenia akurat nie mam zamiaru zmieniać.
Napęd X'a również miałem nadzieję rozwiązać, w podobny sposób jak u kolegi Seemana.
No i teraz pytanie dla doświadczonych użytkowników, czy nie licząc kosztów dłuższych prowadnic [na Z mam już wałki podparte 20mm, ale pozostałe osie jeszcze nie zostały zdefiniowane], wydłużenie maszyny o te przykładowe 2 metry bardzo komplikuje sprawę?
Czy faktycznie powinienem zrobić jak najmniejszą możliwą maszynkę, czy może jednak, zakładając napęd X'a na listwach zębatych, w obu wypadkach nie ma co się bać tylko rąbać ile wlezie po długości?
Dodam, że maszynka na 100% nie będzie spawana przezemnie, a przez doświadczony warsztat, a następnie sezonowana pewnie minimum pół roku, zanim dozbieram resztę szpeju.
W międzyczasie zacząłem rysować oś z i zacząłem rysować belkę Y - ceownik 180mm [mogę dać większy i jednak rozstawić wózki Y do 220-240mm, ale nie wiem czy nie będzie to bezsensowne dodawanie wagi na belce]:
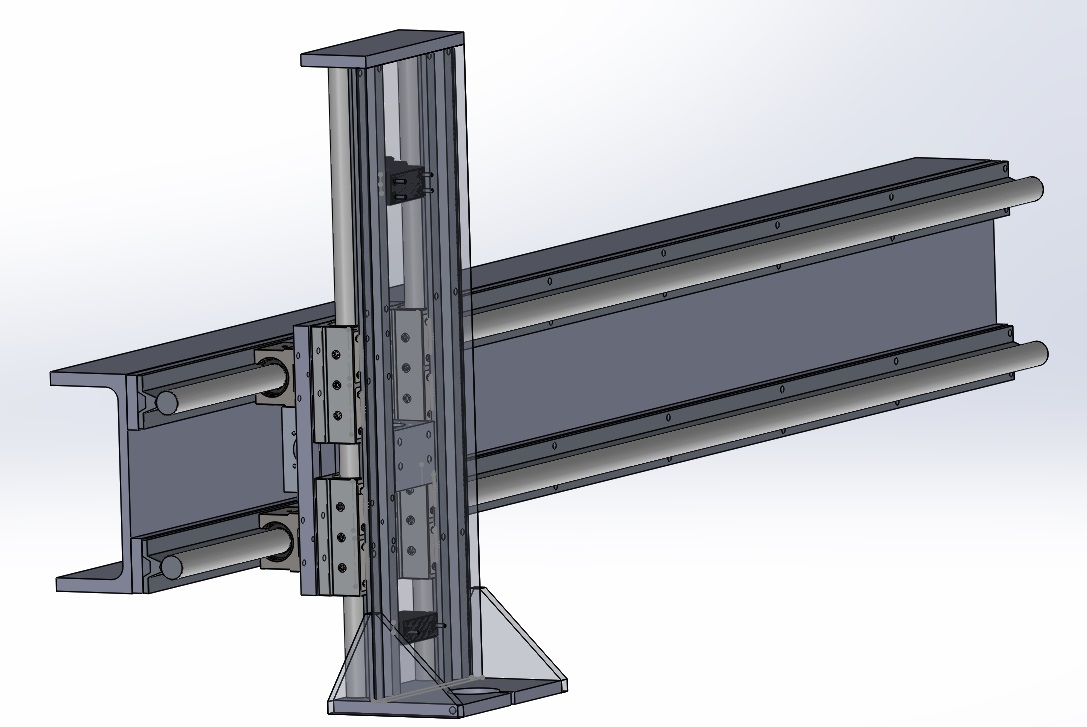
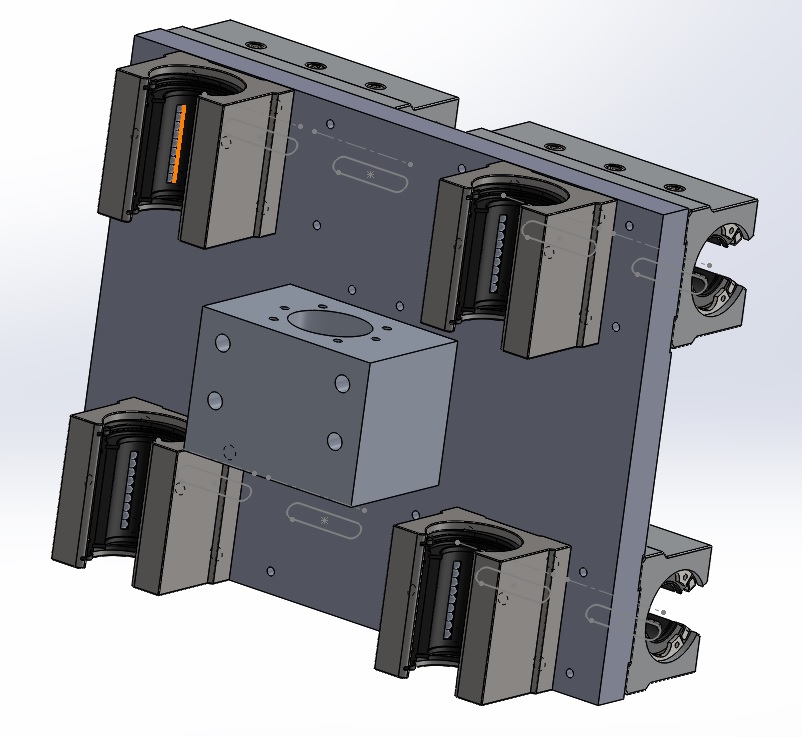
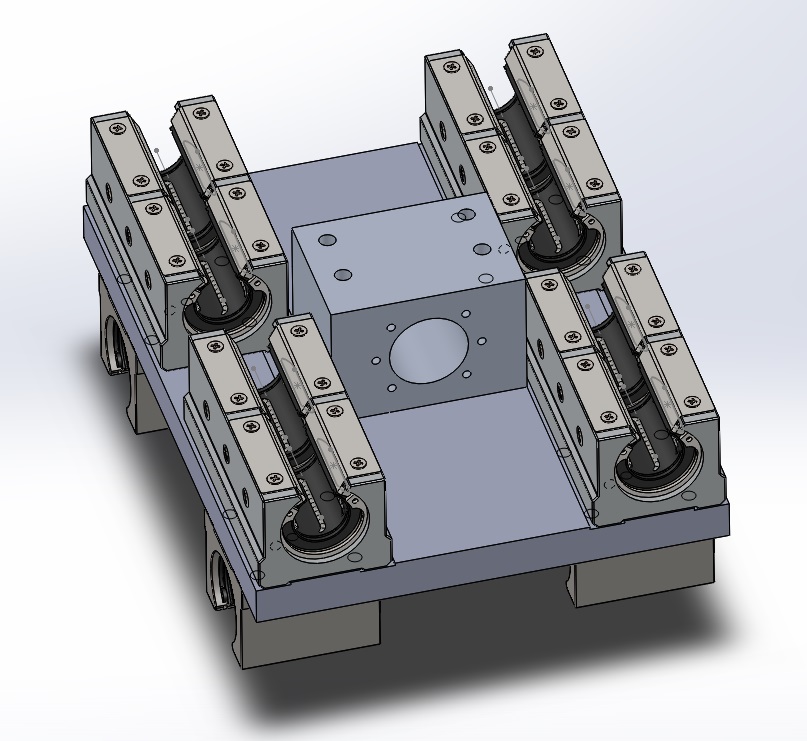